Реферат по теме выпускной работы
Содержание
- Обоснование темы и ее актуальность
- Цель и задачи исследования
- Предполагаемая научная новизна
- Практическая ценность работы
- Обзор данных, существующие исследования и разработки по теме
- Текущие и планируемые результаты по теме
- Заключение
- Список источников
Обоснование темы и ее актуальность
Среди многих жизненно важных проблем, волнующих современное человечество, одно из первых мест по своему значению принадлежит проблеме сохранения окружающей среды с ее сложным механизмом самовосстановления и саморегулирования, сложившимся за длительный период существования нашей планеты. Актуальность проблемы обусловливается тем, что по мере углубления научно-технического прогресса и расширения масштабов индустриализации возрастает степень совокупного воздействия промышленных производств на все элементы биосферы, вызывая их нежелательные качественные и количественные изменения. Все это создает экологическую напряженность в индустриально развитых регионах, заметно ухудшает условия обитания людей, животных и растений.
Так, экологическая несбалансированность окружающей среды в районах добычи и переработки угля вызывает необходимость проведения специальных природоохранных мероприятий практически на каждом промышленном предприятии [1].
Источников загрязнения на шахте, создаваемых непосредственно деятельностью предприятия, много (стволы, откаченные воды, отходы и др.). Но, на мой взгляд, особое внимание следует уделить породным отвалам при анализе опасных объектов загрязнения ОПС.
Известно, что такие углеотходы могут стать ценным ресурсом для извлечения из них редких и цветных металлов, для дорожного строительства, при производстве строительных материалов, закладки выработанного пространства, выращивания отдельных сортов растений и многое другое. Все это актуально в условиях удорожания исходного сырья для металлургии и производства стройматериалов, поддержания горных выработок и. т. д. Кроме того, актуальностью темы является не только поиск решений по применению породной массы, как ценного компонента, но и поиск наиболее рациональной технологии ее использования.
Цель и задачи исследования
Цель работы: выбрать и проанализировать рациональную технологию использования шахтной породы в условиях ГОАО ОП «Шахта им. М. И. Калинина» и уменьшение негативных воздействий террикона на окружающую среду.
Для поставленной цели необходимо выполнение следующих задач:
- По химическому и минералогическому составу и физическим свойствам шахтных пород определить направления их использования.
- Проанализировать существующие исследования и разработки в данных областях применения породы.
- Выбрать и обосновать наиболее рациональное направление использования породного отвала.
- Обосновать технологические решения применяемого направления.
Объект исследования: породный отвал и состояние ОПС в месте его размещения.
Предмет исследования: технологические решения по использованию породы в шахте.
Методы исследования: аналитический, методы технико-экономических расчетов, метод моделирования, прогнозирование, метод статистической обработки данных.
Предполагаемая научная новизнa
Научная новизна заключается в анализе статистических данных с экологической точки зрения, а также паспорта породного отвала и разработке рекомендаций по рациональному использованию породы в условиях конкретного предприятия, а именно ГОАО ОП «Шахта им. М. И. Калинина».
Научная новизна состоит из следующих аспектов:
- Прогнозирование количества породы, выдаваемой на поверхность, для определения наиболее рационального направления ее использования.
- Эколого-экономическое обоснование возможных методов использования шахтной породы.
- Техническое обоснование использования данной отвальной массы.
Практическая ценность работы
Применение породы в шахте для закладки выработанного пространства позволяет снизить деформацию массива земной поверхности; строительные материалы для внутришахтных сооружений получаются в несколько раз дешевле покупаемых материалов; высвобождение занятых породой земель при отсыпке ее для дорожного полотна.
Обзор данных, существующие исследования и разработки по теме
ГОАО ОП «Шахта имени М. И. Калинина» построена по проекту Донгипрошахт и сдана в эксплуатацию в 1962 году. Территориально шахта расположена в Калининском районе города Донецка вдоль проспекта Мира [2].
Определение направления утилизации конкретного отвала составлено согласно «Руководству по определению объема и номенклатуре исходных данных для составления мероприятий по утилизации вскрышных и вмещающих пород», выполненного по рекомендациям научно-исследовательского и проектно-конструкторского института охраны окружающей природной среды в угольной промышленности (ВНИИОСуголь) [3].
Согласно геологическим данным состав породы представлен в основном из алевролита, есть прослойки аргиллита и песчаника. Химический состав породного отвала шахты им. Калинина: SiO2 – 54,10 %, CaO – 0,93 %, Al2O3 – 17,65 %, Na2O – 0,50 %, Fe2O3 – 4,49 %, ППП – 15,73 %, MgO – 3,00 %, K2O – 2,00 %.
Другими показателями качества породы являются: зольность 12,7 – 13,5 %; влажность 1,2 – 2,0 %; сера 2,2 – 4,62 %; выход летучих составляет 18,3 – 23,0 %. Породы данного отвала рекомендуется применять для производства строительных материалов, для закладки выработанного пространства, а также в дорожном строительстве.
Шахтой порода отвала применяется в качестве закладки выработанного пространства во избежание оставления пустот под землей, что может привести к просадке грунта. На примере охраны группового вентиляционного ходка по собственному анализу и вычислениям было предложено возведение таких искусственных сооружений, как бутокостры. Следует размещать по 2 костра с восточной и западной стороны ходка. Породу для заполнения костров можно использовать от проведения данной выработки. Оставшуюся породу можно транспортировать к воздухоподающему ходку для поддержания его бутовой полосой, так как породы от его проведения не хватает для заполнения бутополосы.
Отходы предприятий угольной промышленности могут быть использованы в строительстве, что позволит получить следующие виды эффекта: экологический эффект (снижение антропогенной нагрузки на окружающую среду), экономический (уменьшение платежей за размещение отходов в окружающей среде, получение дополнительного дохода от реализации продукции, произведенной из отходов) и социальный (дополнительные рабочие места) [4].
Рассмотрим один из технологических вариантов производства продукции из породы.
Основные средства, необходимые для производства:
- дробилка,
- грохот,
- линия «Рифей-Варяг».
Технические характеристики комплекса производительность линии «Рифей-Варяг» при изготовлении [5]:
- стеновых блоков ......................................360 шт/час
- перегородочных блоков .......................500 шт/час
- тротуарной плитки .................................175шт/час
- зона формования изделий ...................500х1000 мм
- высота формируемых изделий ................50 – 240 мм
- установленная мощность .........................35,7 кВт
- масса ...............................................................8,7 тонн
- персонал .......................................................3 – 4 человека
- объем отходов............................................... 5 – 15 %
- стоимость....................................................около 376 000 грн.
В производстве строительных изделий используется три главных компонента: вяжущее, заполнитель и вода. В качестве вяжущего на комплексе «Рифей-Варяг» используется цемент, а в качестве заполнителя – пески отсевы щебеночного производства, керамзит, шлаки, золы, опилки или другие местные материалы, способные после смешивания с вяжущим и его схватывания создавать прочную композицию.
Для работы на комплексе цемент является наилучшим вяжущим. Цемент обладает достаточной скоростью твердения, обеспечивает высокую прочность и влагоустойчивость изделий. Это позволяет использовать изделия на основе цемента для строительства коттеджей, приусадебных строений, гаражей, малоэтажных зданий общественного и производственного назначения. Заполнители. В качестве заполнителей обычно используют песок, щебень, шлаки, золы, керамзит, опилки другие инертные материалы, а также их любые комбинации. В заполнителе должны отсутствовать чрезмерное количество пыли, мягкие глинистые включения, лед и смерзшиеся глыбы.
В воде, используемой для приготовления бетона, должны отсутствовать примеси масел, кислот, сильных щелочей органических веществ и производственных отходов. Удовлетворительной считается вода питьевого качества или вода из бытового водопровода. Вода обеспечивает гидратацию (схватывание) цемента. Любые примеси в воде могут значительно снизить прочность бетона и вызвать нежелательное преждевременное или замедленное схватывание цемента. Кроме того, загрязненная вода может привести к образованию пятен на поверхности готового изделия. Температура воды не должна быть ниже 150 °C, поскольку снижение температуры ведет к увеличению времени схватывания бетона.
В последние годы достигнут значительный прогресс в области разработки различных химических присадок к бетону. Они используются для снижения расхода цемента, увеличения скорости его схватывания, сокращения продолжительности тепловлажностной обработки изделий, придания бетону способности твердеть в зимнее время повышения его прочности и морозостойкости. Из добавок ускорителей твердения наиболее распространен хлористый кальций СаСI.
Производство строительных материалов на примере шлакоблока из пород отвала показано на рисунке 1.
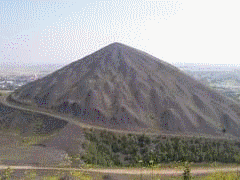
Рисунок 1 - Технологическая схема производства шлакоблока из пород отвалов шахт
Применяются шлакоблоки в соответствии со строительными нормами и правилами для несущих и ограждающих конструкций промышленных и сельскохозяйственных вспомогательных зданий, только для малоэтажного строительства. В угольной промышленности целесообразно использовать их для внутришахтных нужд, по себестоимости они в 2 – 4 раза дешевле; плюс – снижение транспортных расходов, потому что отвал располагается на шахте [6].
Шахтная порода одноковшовым погрузчиком доставляется в дробильное отделение и загружается в приемный бункер, оснащенный решеткой с ячейкой 15 мм, которая совершает колебательные движения под воздействием вибратора. Порода размером до 15 мм просыпается на ленточный конвейер, порода более 15 мм подается по наклонной решетке бункера в дробилку, оттуда – на инерционный грохот – 15 мм, а затем также на ленточный конвейер. Ленточный конвейером порода транспортируется на линию «Рифей-Варяг». В объемные дозаторы подается измельченная порода и цемент, вода из мерной емкости подается прямо в смеситель.
Бетоносмеситель устанавливается над бункером вибропресса. Съём готовых шлакоблоков с пресса и укладка в этажерку-накопитель осуществляется манипулятором-съемником. Транспортирование накопителей в пропарочные камеры осуществляется электропогрузчиком. Термообработка шлакоблоков осуществляется водяным паром в камерах периодического действия. Теплообработка камней в пропарочных камерах производится паром до температуры 80 °C. Цикл теплообработки – 15 часов, остывание камней – 2 часа. Из пропарочных камер накопители со шлакоблоками транспортируются электропогрузчиком на склад готовых шлакоблоков, где с помощью манипулятора шлакоблоки укладываются в штабели. Склад готовых шлакоблоков оснащен подвесным краном, с помощью которого производится погрузка шлакоблоков в автомобили.
Наиболее перспективным и экономически эффективным направлением утилизации данного плоского породного отвала является его использование в дорожном строительстве в качестве оснований полотна дорог.
Практический опыт применения углеотходов в дорожном строительстве имеют все угольные регионы. В Донецке технологию возведения дорожного полотна опробовали на дороге от проспекта Мира до улицы Байдукова рядом с «Донбасс Ареной» [7].
Отвальная масса должна применяться полностью, поэтому решается ряд вопросов, связанных с разным фракционным составом пород отвалов, повышенным содержанием в свежих отходах углерода, опасностью самовозгорания угля в насыпи, высоким содержанием соединений серы, которая агрессивно действует по отношению к некоторым дорожным материалам, повышенной влажностью отходов и др. Эти трудности преодолеваются, в основном, путем выбора рациональной конструкции насыпи. Кроме того, учитываются размещение отходов, перспектива развития дорожной сети в пределах данной территории, анализ об экономической выгоде замены обычного сырья отходами в каждом конкретном случае, данные о составе углеотходов и их свойствах как материала для сооружения земляного полотна [8].
Порода должна удовлетворять следующим главным условиям:
- необходимый зерновой состав. Допускается 5% глыб размером до 300 мм, а содержание пылевидных частиц – не более 3%;
- морозоустойчивость, в связи с сезонным промерзанием земляного полотна;
- оптимальная влажность;
- максимальная плотность отходов. Дает оценку уплотняемости и стабильности насыпи. Важным показателем считается и равнопрочность материала, учитывающая возможный разброс значений прочности и вероятность получения достаточно однородной конструкции.
Для устройства подстилающего слоя используется порода после первого дробления с размером зерен от 20 до 150 мм [9]. Технологический процесс сводится к разравниванию породы и уплотнению образующейся поверхности катками. Просадки выравниваются, рассыпая горелую породу меньшей крупности, и 15 – 18 раз по насыпи проходит тяжелый каток. Уплотнение заканчивается при прекращении деформации после прохода катка. Для повышения плотности слоя породу можно увлажнить.
Для нижних и средних слоев оснований применяют размеры фракций свыше 40 до 80 мм и свыше 80 до 150 мм, для верхних слоев оснований и покрытий – свыше 20 до 40 мм и свыше 40 до 80 мм. Расклинцовку слоя с перегоревшей породой следует производить мелкими фракциями с последовательно уменьшающимися размерами: 5 – 10, 10 – 20 и 20 – 40 мм.
Основания и покрытия из дробленных горелых пород укладывают аналогично основаниям из природного щебня и гравия – отсыпают, распределяют и уплотняют.
На рисунке 2 приведены варианты предлагаемых конструкций дорожной одежды из материалов горелых пород шахтных отвалов.
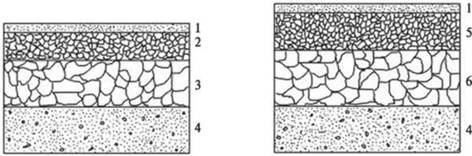
Рисунок 2 – Конструкции дорожных одежд усовершенствованного облегченного типа из материалов горелых пород (h – толщина слоя): 1 - поверхностная обработка, фракция 5 – 10 мм; 2 – щебень фракции 20 – 40 мм, обработанный битумом, h = 8 см; 3 – слой прочного щебня с расклинкой, h = 20 см; 4 – отсев дробления горелых пород, h = 16 см; 5 – щебеночная смесь фракций, обработанная битумом на дороге, h = 10 см; 6 - щебеночная смесь свыше 20 до 80 (150) мм, h = 30 см.
Текущие и планируемые результаты по теме
Результаты выполненной работы позволят:
- спрогнозировать количество используемой породы на шахте при ее максимальной добыче;
- обосновать направление рационального использования шахтной породы;
- предотвратить негативное воздействие горной промышленности на окружающую среду.
Результаты магистерской работы могут быть полезной основой для дальнейших исследований.
Заключение
Современное крупномасштабное развитие горнодобывающих отраслей промышленности оказывает существенное негативное воздействие на окружающую среду, выходящее за пределы ее самовосстановительных и саморегулирующих возможностей. Это является прямым следствием длительного экстенсивного развития горного производства, обусловливающего дестабилизацию природной среды многотонными отходами хозяйственной деятельности и обеспечивающего необходимые средства существования за счет разрушения естественных условий проживания людей [10].
К настоящему времени в угольной промышленности накоплен определенный опыт по восстановлению экологической сбалансированности окружающей среды в процессе производственной деятельности шахт, разрезов и обогатительных фабрик. Наиболее полное использование попутно добываемого сырья и отходов производства сможет удовлетворить собственные нужды предприятия в строительных материалах и поддержании горных выработок, а также снизить расходы, выплачиваемые предприятием вследствие нанесения отходами экологического ущерба.
Список источников
- В. С. Малышенко Совершенствование природоохранных работ в угольной промышленности / В. С. Малышенко,
Ю. В. Каплунов, А. П. Красавин, А. А. Харионовский // Обзор ЦНИЭИуголь.: М., – 1992. - Сведения о шахте Калинина. [Электронный ресурс]. – Режим доступа: http://duek.dn.ua/kln/index.html.
- Джунько П. М. Временное руководство по определению объема и номенклатуре исходных данных для составления мероприятий по утилизации вскрышных и вмещающих пород / П. М. Джунько, Т. А. Михалева, М. Я. Шпирт,
Ю. Н. Жаров // ВНИИСуголь.: М., – 1983. - Методические указания к выполнению курсовой работы по дисциплине «Экологический менеджмент» //
Беляева Е. Л., Костенко В. К., Матлак Е. С., Шафоростова М. Н. – Донецк, ДонНТУ, 2006. – 33 с. –
[Электронный ресурс]. – Режим доступа: http://feht.donntu.ru/strukt/pd/img/kurs_ecomenedgm.pdf> - Линия «Рифей-Варяг» [Электронный ресурс]. – Режим доступа: http://www.vpres.ru/?id=4
- Утилизация и рекуперация отходов. Учебное пособие (для студентов специальности 7. 070801 «Экология и охрана окружающей среды») / Краснянский М. Е., Донецк: ООО «Лебедь», – 2004. – 288с.
- Мишина Т. «При строительстве дорог к Евро-2012 будут использовать шахтные отходы». – МК Донбасс – 05.08.2011год. – [Электронный ресурс]. – Режим доступа: http://mk-donbass.com.ua/index.
- Мочков B.C. Опыт использования отходов добычи и обогащения угля в дорожном строительстве / B. C. Мочков,
Б. Е. Бронштейн // Обзор ННИЭИуголь.: М., – 1988. – 29с. - Буравчук Н. И., Гурьянова О. В., Окороков Е. П., Павлова Л. Н. «Материалы из техногенного сырья для дорожного строительства». – 8-я Международная конференция «Сотрудничество для решения проблемы отходов»,
23 – 24 февраля 2011 г., Харьков. – 168 с. [Электронный ресурс]. – Режим доступа: http://waste.ua/cooperation - Статья об угольной промышленности [Электронный ресурс]. – Режим доступа: http://www.tek.ua/article