Abstract
Содержание
- Itroduction
- 1 The technology of hot repair of masonry of coking chambers using ceramic welding
- 2 Description of technological process of preparing a mixture of ceramic
- 2.1 Fragmentation of silicon
- 2.2 Crushing and grinding of silicon
- 2.3 Drying of ceramic mixtures of initial components
- 2.4 Sieving of the initial components of ceramic mixtures
- 2.5 The dosage and mixing of the mixture components
- 2.6 Packing of the finished product
- Conclusions
- References
Introduction
Prolonged operation of coke oven batteries raises the question of durability of masonry of coking chambers, so the preservation of masonry, the maximum possible extension of its life – a very important task, the successful solution of which depends on the major technical and economic performance of the industry.
The last decade in the domestic coke, and in advanced coking industry wide front are working to improve methods and technologies for preventive maintenance of masonry of coking chambers, especially the hot repairs – to increase the resistance caused by the repair layer, reducing labor and material costs, and time-consuming to carry out repairs [1].
At present, there is a significant asset koksohimikov arsenal of methods of laying hot repair of coke ovens and equipment for its implementation. Traditional methods of repair of the hot – wet and semi-dry concrete spraying, and they are ubiquitous. Wet gunned a long time was the only industrially preventive maintenance masonry of coking chambers because of its cheapness, ease of implementation, unpretentious equipment. However, the lack of stability of the repair layer, thermal shocks that occur when applying a wet mixture on a hot ceramic surface of masonry, was forced to seek better ways to implement preventive repairs [2].
Numerous development (both abroad and in our country) the new modern way to hot repair, free from the above-mentioned drawbacks of semi-dry and wet shotcrete can be grouped as follows:
- Methods of deposition (
pripylivaniya
) refractory material on the clutch and then sintering it at the expense of laying accumulated heat or flame heat hot coke oven gas, acetylene, etc. - Methods of torch guniting, consisting in melting refractory powder by the heat of combustion of high-temperature flame of propane in oxygen and applying it to the repair area.
- Methods of ceramic welding (
Welding
), consisting of the fact that the dry refractory mortar mixed with metal powder is fed a stream of oxygen on the heated surface of the masonry, there is an exothermic reaction of oxidation of the metal component of a ceramic mixture of oxygen under the action of heat released refractory ceramic part of the mixture is melted and together with the products of the oxidation of metals melt, filling defects in the brickwork. - Methods of plasma shotcrete in which to melt the refractory material used heat the plasma of inert gases [1].
1 The technology of hot repair of masonry of coking chambers using ceramic welding
Method of hot repair of masonry of coking chambers using ceramic welding – is a complex physico-chemical process.
The essence of this method is as follows: dry spray powder in pure oxygen applied to the damaged area of masonry coke oven with a temperature of not lower than 700-800 ° C. Due to the heat of chemical exothermic reaction between oxygen and fuel component mixture of ceramic (aluminum powder, silicon crystal) is the melting of refractory components (Silica mortar and silica sand, ground diabase), followed by the filling of defects of masonry[3]. During the solidification of the melt, due to some combination of components of a mixture of ceramic, monolithic structure is formed, its properties are close to the masonry material with a ceramic bond between the fireclay brick masonry and repair layer, which provides a high resistance and durability of coatings deposited in this manner [4].
The process of coating deposition is shown in Figure 1[11].
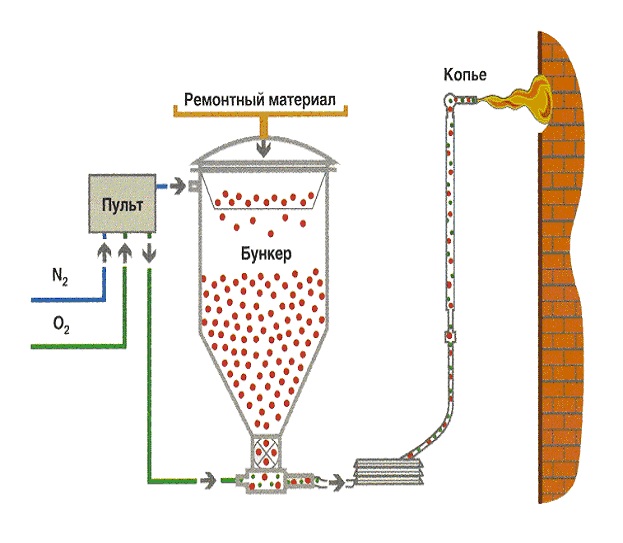
Figure 1 – The technological scheme of the application of ceramic mixtures
The quality of welding depends not only on the composition of the ceramic mixture, but also on parameters such as oxygen consumption, the speed of the ceramic coating deposited mixture, the temperature of the coking chambers of masonry, the surface state of the repaired area, as well as subjective factors such as staff expertise to the work of the new device (Figure 2)[5].
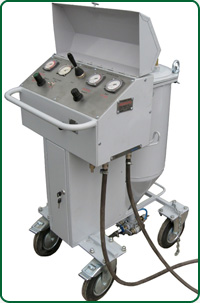
Figure 2 – Installation of ceramic welding MAX
Table 1 – The main technical characteristics of the facility MAX
Name | Unit | Value |
Fuel tank repair material: full / working | l | 37–30 |
Performance | kg / h | to 160 |
Gas pressure at the inlet, no more than: MPa (kgf/cm²) | oxygen | 0,60÷0,63 |
nitrogen | 0,70÷0,80 | |
Consumption of gas at a pressure of 0,6÷0,8 МPа (6÷8 kgf/сm²) | m³/min | 0,4÷0,7 |
Range of supply of repair materials | m | tо 20 |
Dimensions, В×L×H | mm td> | 510×780×1000 |
Low temperature carbonization chamber of masonry, as well as bad stripped from the graphite deposits repaired sections of masonry leads to poor adhesion with masonry cladding material, which reduces the adhesive strength of masonry. Increased oxygen consumption leads to a reduction in fire resistance, and high speed coating deposited mass to neproplavlennosti, friability and high porosity surfacing. It is therefore important to choose the optimal mode of ceramic welding [4].
A necessary condition for the normal flow of ceramic welding process is to match the stoichiometric ratio of expenditure weight of the mixture and oxygen at a temperature of masonry of coking chamber not below the onset temperature of exothermic reaction of combustion fuel component.
The temperature of the beginning of the exothermic reaction of combustion of aluminum is equal to its melting point, ie is 660 ° С.
Therefore, for successful and sustainable process of ceramic welding is necessary that the temperature of the coke oven repaired masonry was not lower 700-800 °С [6].
It is known that the flow of any gas, as well as fine granular materials transported by a gas depends on its pressure, and pressure increases with increasing flow rate. Transportation of a mixture of the system in this way is compressed air. Therefore, the main parameters of the process of ceramic welding is the pressure of oxygen and air pressure in the apparatus for coating.
The choice of the optimal values ??of the basic parameters of the ceramic welding was done after a series of experimental built-up layers on the experimental stand.
The appearance of chamotte lining of industrial furnaces is shown in Figure 3 [12].
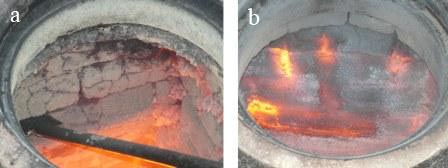
Figure 3 – The appearance of chamotte lining of industrial furnaces to (a) and after (b) the method of ceramic welding repair
Equally important in the conduct of a dispersion of ceramic welding of the components of a mixture of ceramic and the presence of impurities in it.
Empirically found that a mixture of ceramic particle size should not exceed 1.5 mm, and the moisture content of less than 1%.
The success of the hot repair by this method largely depends on the quality of the mixture, and it imposes certain conditions and requirements for the initial components, the process of preparation and equipment used [2].
The mixture is prepared by mechanical mixing of dry powders in certain proportions. The absence of complex physical and chemical transformations in the preparation of ceramic mixtures makes it accessible to the production of any coke plant. However, the initial assumption is that, without proper organization and preparation of the cooking process can be a mixture of qualitative, not justified. There was a need for a centralized its production with the selection of equipment and development of production schedules.
The main stages in the process of making ceramic mixtures are: crushing, grinding and grinding of lump silica, drying and sieving the original components, dosing and mixing of the initial components of the mixture. To perform these operations is mainly used, the standard model equipment: jaw and hammer mill, vibrating mill, a mixer [7].
2 Description of technological process of preparing a mixture of ceramic
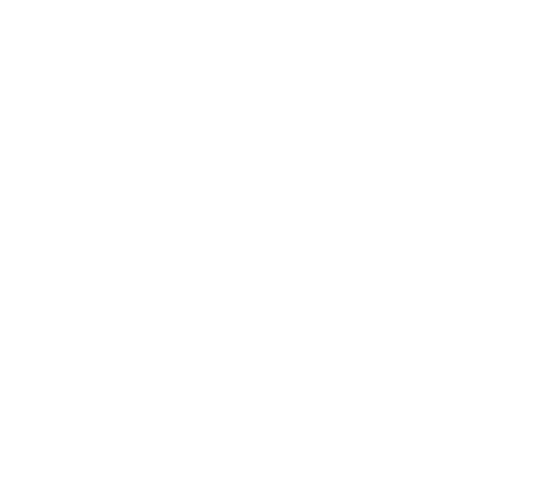
Figure 4 – Technological scheme of preparation of ceramic mixtures
The basic technological operations for the preparation of the mixture are:
2.1 Fragmentation of silicon
Lump crushing of silicon is carried out on a jaw crusher. Delivery of the Party of silicon from the warehouse to the crusher is done by truck. Download lump of silicon in a boot box crusher by hand. Crushed silicon from the exit slit of the crusher arrives in the receiving tank and then sent to the stage of grinding.
Mode crusher periodically. Number of crushed silicon in each case established a separate order of the head of the site, depending on the needs of the mixture. Possible time between crushed silica with a stock of the needs of [3].
The width of the output gap is set crusher adjustment mechanism so as to ensure that the minimum size (no more than 10 mm) of crushed pieces of silicon at the outlet of the crusher.
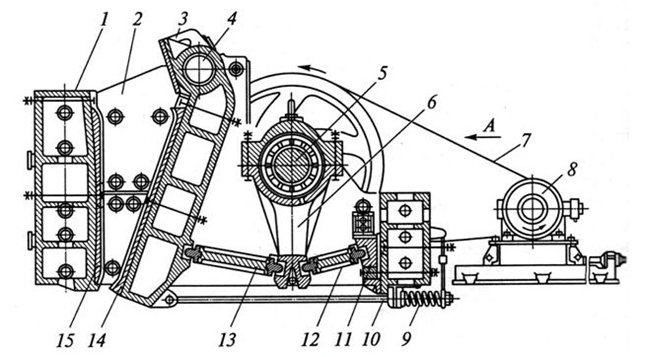
Figure 5 – Jaw crusher
1 – wall of the body, 2 – lateral cheek, 3 – movable jaw, 4 – axle, 5 – Val 6 – rod, 7 – Belt drive, 8 – electric, 9 – pring 10 – draft of 11 – blank, 12,13 – spacer plate, 14,15 – crushing plates
Grinder fitted with two locks, which disables the drive crusher in the following cases:
- if it enters the crusher material with high strength (greater than 250 MPa) or a piece of metal;
- when the door is opened, the existing fence to drive the crusher.
- Огнеупоры для промышленных агрегатов и топок: Справочное издание в двух книгах. Кн. 1 Производство огнеупоров / [И.Д. Кащеев, В.Г. Алфеева, М.Г. Ладыгичев и др.]. – М.: Интермет Инжииринг, 2000. – 663 с.
- Огнеупоры для промышленных агрегатов и топок: Справочное издание в двух книгах. Кн. 2 Служба огнеупоров / [И.Д. Кащеев, В.Г. Алфеева, М.Г. Ладыгичев и др.]. – М.: Интермет Инжииринг, 2002. – 656 с.
- Пак 3.П., Щепетьева Н.П. Экзотермический процесс горения порошкообразного материала – основа эффективного метода ремонта промышленных печей // Материаловедение. 1999. №5.
- Ухмылова Г.С. Продление срока службы коксовых батарей / По материалам IV Европейского конгресса по коксохимическому и доменному производствам // Кокс и химия. 2001. №4. С. 21-24.
- Новые возможности керамической сварки при горячих ремонтах огнеупорной кладки высокотемпературных промышленных агрегатов [электронный ресурс]. – Режим доступа: http://www.npomegatek.ru...
- Щепетьева Н.П., Кёниг А.А., Гришкин В.П., Ходарев Д.В., Кривошеин В.Т. Керамическая сварка – современная технология горячего ремонта футеровок высокотемпературных промышленных агрегатов // Кокс и химия. 2006. № 9. С. 42-46.
- Горячие ремонты коксовых печей керамической наплавкой и смесями СВС / А.Н. Патрушев, В.М. Неволин, В.В. Дябин, Ю.Л. Крутский и др. // Кокс и химия. 2000. №1. С. 16-19.
- Волков А.П., Пушкарев А.А., Хлопотов С.С. Ремонты кладки печных камер коксовых батарей с применением технологии фирмы
Fosbel
// Кокс и химия. 2005. №7. С. 18-20. - Щепетьева Н.П., Кёниг А.А., Гришкин В.П., Ходарев Д.В., Кривошеин В.Т. Новые возможности керамической сварки при горячих ремонтах огнеупорной кладки высокотемпературных промышленных агрегатов // Чёрная металлургия. 2006. № 6. С. 23-26.
- Ухмылова Г.С. Горячий ремонт кладки коксовых печей в сжатые сроки / По материалам IV Европейского конгресса по коксохимическому и доменному производствам // Кокс и химия. 2001. №7. С. 20.
- Технология керамической наплавки [электронный ресурс]. – Режим доступа: http://www.npomegatek.ru...
- Технология керамической наплавки как способ продления срока службы стекловаренных печей [электронный ресурс].– Режим доступа: http://www.npomegatek.ru...
2.2 Crushing and grinding of silicon
Crushing and grinding of silicon to the class of 1.5 mm made ??in a vibrating mill. Crushed silicon manually loaded into the chamber when the motor through the manhole, after removing the snap-on lid. At the same time the nearby outlet chamber lid closed flap. It is used in the case of liquid media. After loading a vibrating mill 1,0–1,2 m³ silicon and closing the hatch quick cover, including the engine for 3 hours[1].
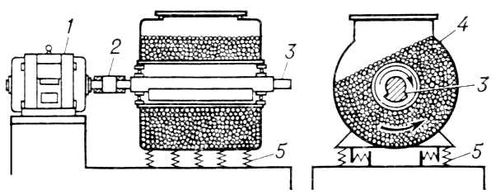
Figure 6 – Vibrating mill
1 – electric motor, 2 – coupling, 3 – shaft, 4 – drum, 5 – spring
At the end of the processing time turn off the engine, open bars unloading by removing the snap-cap grid. Connect the discharge pipe with a leak proof container sleeve, fixing his collar on the tube, after which the engine include the time required for unloading the silicon.
After unloading all the silicon engine turned off, and the product is sent to the drying stage [8].
It is possible that in the ground silicon will contain a significant amount (as determined visually, not large pieces of silicon promolotyh, whereas in this case a product is sent for re-grinding, pre-screenings for the past vibrating screen.
Re-grinding is carried out as described above and the operation of crushing and grinding of silicon.
2.3 Drying of ceramic mixtures of initial components
In the process of preparing a mixture of ceramic drying are the following: Silica, or quartz sand mortar, ground diabase, ground silica.
Drying in an oven, a periodic mode of operation.
Drying material to 120-150 kg is loaded into the oven.
In the oven served shirt or pair condensate. Drying of the components is carried out at a temperature of 120 ° C. The components are dried to a residual moisture content not exceeding 1% (wt). The drying in the oven, depending on the initial moisture content of the components of 2,5-4,5 hoursа [9].
Possible to carry out drying in natural conditions. Drying material disperses evenly on trays (smooth clean surface nekorroziruyuschaya) g for 2-3 days is dried in a dry and well heated room.
Each component – dried separately. Mixing of the components is not allowed at this stage. The dried product is sent to the stage of screening.
Number of drying material is determined depending on the degree of humidity of the initial components, the need for the ceramic mixture.
Initial moisture content of the initial components, especially silica sand or silica mortars delivered open, more than the required value. Therefore, these components always require drying. Ground silica, directed from the stage of grinding, as well as diabase, come to the stage of drying in closed containers and may have a moisture content within the normal range. Therefore, these components are subjected to laboratory analysis for moisture, and then concluded to hold dry milled silicon and diabase [6].
2.4 Sieving of the initial components of ceramic mixtures
Sieving are the following: Silica, or quartz sand mortar, diabase, ground silica.
Sieving of components produced in the vibrating screen, a periodic mode of operation. Each component is subjected to sieving to separate, not mixing nedopuskaetsya. Sieving is carried out on a grid of stainless steel mesh size of 1.5 mm. Class 1.5 mm collected in hermetically sealed containers and sent to the stage of dosing and mixing of the components, and the class of 1.5 mm in the receiving container and the accumulation of leaves to the dump. The exception to this is silicon, Class 1.5 mm which is sent for re-grinding.
Number of processed material at the stage of screening is determined in each case.
2.5 The dosage and mixing of the mixture components
Mix all the ingredients that make up the ceramic mixture is produced in the mixer, the periodic mode of operation.
Unloading is done manually, after a trough in front of this mixer is tilted relative to the horizontal plane at a certain angle.
Before mixing in the mixer weighed in the balances required number of each component of the mixture.
2. 6 Packing of the finished product
ПReceiving the above manner a mixture from the mixer is poured into the five-layer bituminous paper bags, which are stitched after the packing of. On each bag labeled as indicating the batch number, manufacturing date and weight, the names of packaged materials. Paper bag is placed in an outer plastic, which is brewed or stitch. In each bag are sending 35 kg mixture [10].
The bags with the mixture formed in the party, held laboratory analysis of the finished product from the warehouse and sent to the consumer.
Conclusions
Duration and effectiveness of high-temperature industrial units depending on their level of technical service, timely diagnosis of emerging defects and quality of preventive repairs. Timely implementation of the necessary volume and use the most efficient preventive maintenance, such as ceramic cladding, can significantly extend the service life of industrial furnaces [5].