Реферат за темою випускної роботи
Зміст
- Вступ
- 1 Технологія проведення горячого ремонту кладки камер коксовання методом керамічного наплавлення
- 2 Опис технологічного процеса приготування керамічної сумеші
- 2.1 Дроблення кремнію
- 2.2 Подрібнення і помел кремнію до класу
- 2.3 Сушка початкових компонентів керамічної сумеші
- 2.4 Розсівання початкових компонентів керамічної сумеші
- 2.5 Дозування і змішування компонентів керамічної сумеші
- 2.6 Затарювання готової продукції
- Висновки
- Список літератури
- Методи напилення (
припорошування
) вогнетривкого матеріалу на кладку з наступним спіканням його за рахунок закумульованого кладкою тепла або тепла полум'я гарячого коксового газу, ацетилену тощо. - Методи факельного торкретування, що полягають в розплавленні вогнетривкого порошку за рахунок тепла високотемпературного полум'я горіння пропана в кисні і нанесенні його на ремонтовану поверхню.
- Методи керамічного наплавлення (
зварювання
), що полягають в тому, що сухий вогнетривкий мертель в поєднанні з металевим порошком подається струменем кисню на розжарену поверхню кладки, відбувається екзотермічна реакція окислення металевої складової керамічної сумеші в кисні, під дією тепла, що виділяється, вогнетривка частина керамічної сумеші розплавляється і разом з продуктами реакції окислення металів складає розплав, який заповнює дефекти кладки. - методи плазмового торкретування, в яких для розплавлення вогнетривкого матеріалу використовується тепло плазми інертних газів. [1].
- при попаданні у дробарку матеріалу з великою міцністю (більш, ніж 250 МПа) або шматка металу;
- при відкритті дверець в обгороджуванні приводу дробарки.
- Огнеупоры для промышленных агрегатов и топок: Справочное издание в двух книгах. Кн. 1 Производство огнеупоров / [И.Д. Кащеев, В.Г. Алфеева, М.Г. Ладыгичев и др.]. – М.: Интермет Инжииринг, 2000. – 663 с.
- Огнеупоры для промышленных агрегатов и топок: Справочное издание в двух книгах. Кн. 2 Служба огнеупоров / [И.Д. Кащеев, В.Г. Алфеева, М.Г. Ладыгичев и др.]. – М.: Интермет Инжииринг, 2002. – 656 с.
- Пак 3.П., Щепетьева Н.П. Экзотермический процесс горения порошкообразного материала – основа эффективного метода ремонта промышленных печей // Материаловедение. 1999. №5.
- Ухмылова Г.С. Продление срока службы коксовых батарей / По материалам IV Европейского конгресса по коксохимическому и доменному производствам // Кокс и химия. 2001. №4. С. 21-24.
- Новые возможности керамической сварки при горячих ремонтах огнеупорной кладки высокотемпературных промышленных агрегатов [электронный ресурс]. – Режим доступа: http://www.npomegatek.ru...
- Щепетьева Н.П., Кёниг А.А., Гришкин В.П., Ходарев Д.В., Кривошеин В.Т. Керамическая сварка – современная технология горячего ремонта футеровок высокотемпературных промышленных агрегатов // Кокс и химия. 2006. № 9. С. 42-46.
- Горячие ремонты коксовых печей керамической наплавкой и смесями СВС / А.Н. Патрушев, В.М. Неволин, В.В. Дябин, Ю.Л. Крутский и др. // Кокс и химия. 2000. №1. С. 16-19.
- Волков А.П., Пушкарев А.А., Хлопотов С.С. Ремонты кладки печных камер коксовых батарей с применением технологии фирмы
Fosbel
// Кокс и химия. 2005. №7. С. 18-20. - Щепетьева Н.П., Кёниг А.А., Гришкин В.П., Ходарев Д.В., Кривошеин В.Т. Новые возможности керамической сварки при горячих ремонтах огнеупорной кладки высокотемпературных промышленных агрегатов // Чёрная металлургия. 2006. № 6. С. 23-26.
- Ухмылова Г.С. Горячий ремонт кладки коксовых печей в сжатые сроки / По материалам IV Европейского конгресса по коксохимическому и доменному производствам // Кокс и химия. 2001. №7. С. 20.
- Технология керамической наплавки [электронный ресурс]. – Режим доступа: http://www.npomegatek.ru...
- Технология керамической наплавки как способ продления срока службы стекловаренных печей [электронный ресурс].– Режим доступа: http://www.npomegatek.ru...
Содержание
Вступ
Тривала експлуатація коксових батарей породжує проблему стійкості кладки камер коксування, тому збереження кладки, максимально можливе подівження терміну її служби – дуже актуальне завдання, від успішного рішення якої залежать найважливіші техніко-економічні показники роботи галузі.
Останні десятиліття у вітчизняній коксохімії і в країнах з розвиненою коксохімічною промисловістю широким фронтом ведуться роботи з вдосконалення методів і технологій профілактичного ремонту кладки камер коксування, особливо гарячих ремонтів – з метою збільшення стійкості ремонтного шару, що наноситься, зниження трудових, матеріальних витрат, а також витрат часу на проведення ремонтів [1].
Нині в активі коксохіміків є значний арсенал методів гарячого ремонту кладки коксових печей і пристроїв для його здійснення. Традиційні способи гарячого ремонту – мокре і напівсухе торкретування; вони поширені скрізь. Мокре торкретування довгий час було єдиним промисловим способом профілактичного ремонту кладки камер коксування через дешевизну, простоту здійснення, невибагливого устаткування. Проте, недостатня стійкість ремонтного шару, термічні удари, що відбуваються при нанесенні мокрої керамічної сумеші на розжарену поверхню кладки, змусили шукати більш досконалі способи здійснення профілактичних ремонтів [2].
Численні розробки (як за кордоном, так і в нашій країні) нових сучасних способів гарячого ремонту, вільних від зазначених вище недоліків, властивих мокрому і напівсухому торкретуванню, можна згрупувати таким чином:
1 Технологія проведення горячого ремонту кладки камер коксовання методом керамічного наплавлення
Спосіб гарячого ремонту кладки камер коксування методом керамічного наплавлення – це складний фізико-хімічний процес.
Суть цього методу полягає в наступному: сухий торкрет-порошок в середовищі чистого кисню наноситься на пошкоджену ділянку кладки коксової печі з температурою не нижче 700-800 °С. За рахунок виділення тепла хімічних екзотермічних реакцій між киснем і паливної складової керамічної сумеші (алюмінієва пудра, кремній кристалічний) відбувається розплавлення її вогнетривких компонентів (динасовий мертель або кварцевий пісок, мелений діабаз) з наступним заповненням дефектів кладки [3]. При твердінні розплаву, завдяки певному поєднанню компонентів керамічної сумеші, утворюється монолітна структура, за своїми властивостями близька до матеріалу кладки з керамічним зв'язком між шамотною цеглиною кладки і ремонтним шаром, що дозволяє отримати високу стійкість і міцність нанесеного у такий спосіб покриття[4].
Процес нанесення керамічної сумеші представлен на рисунку 1 [11].
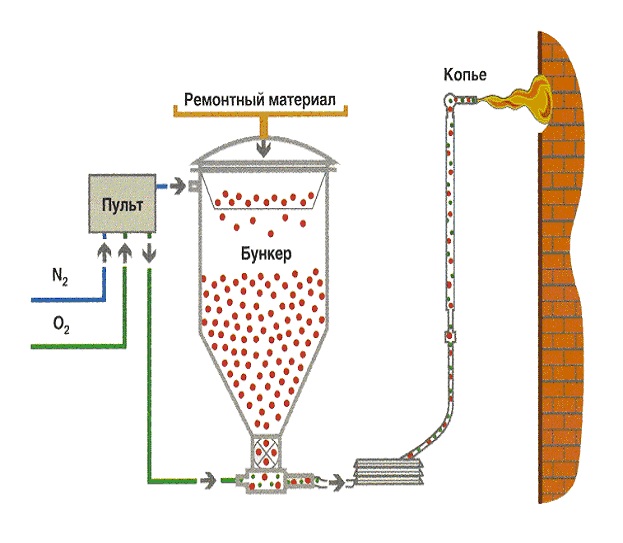
Рисунок 1 – Технологічна схема процесу нанесення керамічної суміші
Якість наплавлення залежить не лише від складу керамічної сумеші, але і від таких параметрів як витрата кисню, швидкість нанесення керамічної сумеші, що наплавляється, температура кладки камер коксування, стан поверхні ремонтованої зони, а також від суб'єктивних причин, таких як підготовленість персоналу до роботи новим апаратом (рис.2)[5].
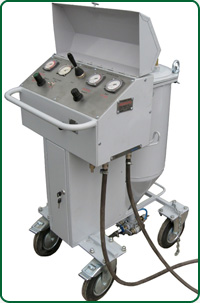
Рисунок 2 – Установка для керамічного зварювання МаКС
Таблиця 1 – Основні технічні характеристики установки МаКС
Найменування | Одиниця виміру | Значення |
Обсяг бака ремонтного матеріалу: повний / робочій | л | 37–30 |
Продуктивність | кг/год | до 160 |
Тиск газів на вході, не більше: МПа (кгс/см²) | кисень | 0,60÷0,63 |
азот | 0,70÷0,80 | |
Витрата газів при тиску 0,6÷0,8 МПа (6÷8 кгс/см²) | м³/хв | 0,4÷0,7 |
Дальність подачі ремонтного матеріалу | м | до 20 |
Габарити, В×L×H | мм | 510×780×1000 |
Низька температура кладки камер коксування, а також погано зачищені від графітових відкладень ремонтовані ділянки кладки призводять до поганого зчеплення матеріалу кладки з наплавленням, що знижує міцність зчеплення з кладкою. Підвищена витрата кисню призводить до зниження вогнетривкості, а велика швидкість нанесення маси, що наплавляється, до непроплавленості, рихлості і високої пористості наплавлення. Тому дуже важливий вибір оптимального режиму проведення керамічного наплавлення [4].
Необхідною умовою нормального протікання процесу керамічного наплавлення є відповідність стехіометричному співвідношенню вагових витрат сумеші і кисню при температурі кладки камери коксування не нижче температури початку екзотермічних реакцій горіння паливної складової.
Встановлено, що температура початку екзотермічної реакції горіння алюмінію співпадає з його температурою плавлення, тобто складає 660 °С.
Отже, для успішного і стабільного проведення процесу керамічного наплавлення необхідно, щоб температура ремонтованої кладки коксової печі була не нижча 700-800 °С [6].
Відомо, що витрата будь-якого газу, а також сипких дрібнодисперсних матеріалів, що транспортуються газом, залежить від його тиску, причому із збільшенням тиску збільшується витрата. Транспортування сумеші по системі в цьому способі здійснюється стислим повітрям. Тому основними параметрами процесу керамічного наплавлення є тиск кисню і тиск стислого повітря в апараті для нанесенн покриття.
ВВибір оптимальних значень основних параметрів процесу керамічного наплавлення був зроблений після проведення серії експериментальних наплавлень на досвлідницькому стенді.
Зовнішній вигляд шамотної футеровки промислової печі представлен на рисунку 3 [12].
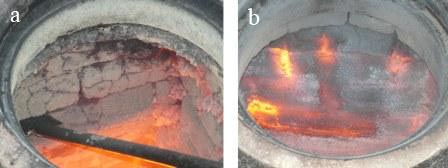
Рисунок 3 – Зовнішній вигляд шамотної футеровки промислової печі до (а) і після (b) ремонту методом керамічної наплавки
Важливе значення у проведенні керамічного наплавлення має дисперсність складових компонентів керамічної сумеші і наявність у ній сторонніх домішок.
Дослідницьким шляхом встановлено, що розмір часток керамічної сумеші повинна складати не більше 1,5 мм, а зміст вологи менше 1 %.
Успішне проведення гарячих ремонтів вказаним методом значною мірою залежить від якості сумеші, а це накладає певні умови і вимоги до вихідних компонентів, процесу приготування і використовуваного устаткування [2].
Суміш готується механічним змішенням сухих дрібнодисперсних порошків у певній пропорції. Відсутність складних фізико-хімічних перетворень в під час приготування керамічної сумеші робить її виробництво доступним на будь-якому коксохімічному заводі. Проте первинне припущення, що без належної організації і підготовки процесу приготування можна отримати якісну суміш, не виправдалося. Виникла необхідність у централізованому її виробництві з підбором необхідного устаткування і розробкою технологічного регламенту.
Основними стадіями процесу приготування керамічної сумеші є дроблення, подрібнення і помел кускового кремнію, сушка і розсівання початкових компонентів, дозування і змішення початкових компонентів керамічної сумеші. Для виконання вказаних операцій використовується, як правило, стандартне типове устаткування: щічна і молоткова дробарка, вібромлин, двороторний змішувач [7].
2 Опис технологічного процеса приготування керамічної сумеші
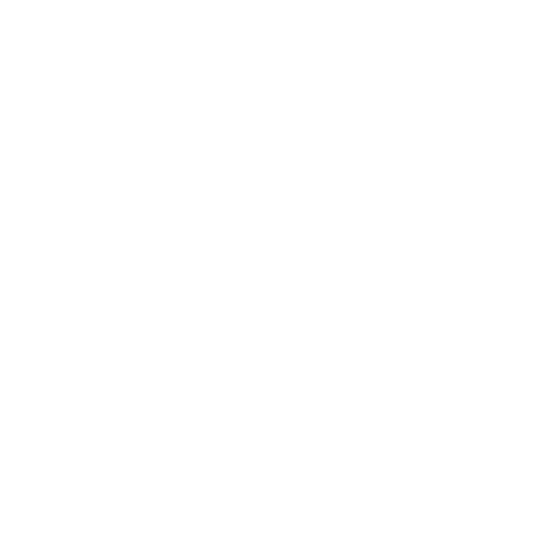
Рисунок 4 – Технологічна схема приготування керамическої сумеші
Основними технологічними операціями з приготування смесі є:
2.1 Дроблення кремнію
Дроблення кускового кремнію здійснюється на щічній дробарці. Доставка партії кремнію із складу до дробарки відбувається за допомогою навантажувача. Завантаження кускового кремнію в завантажувальне вікно дробарки відбувається вручну. Роздрібнюваний кремній з вихідної щілини дробарки поступає в приймальну ємність і потім прямує на стадію подрібнення і помелу.
Режим роботи дробарки періодичний. Кількість роздрібнюваного кремнію у кожному конкретному випадку встановлюється окремим розпорядженням начальника ділянки і залежить від потреби в смесі. Можливе напрацювання .роздрібнюваного кремнію із запасом за потребою [3].
Ширина вихідної щілини дробарки встановлюється механізмом регулювання так, щоб забезпечити мінімальний розмір (не більше 10 мм) шматків .роздрібнюваного кремнію на виході з дробарки.
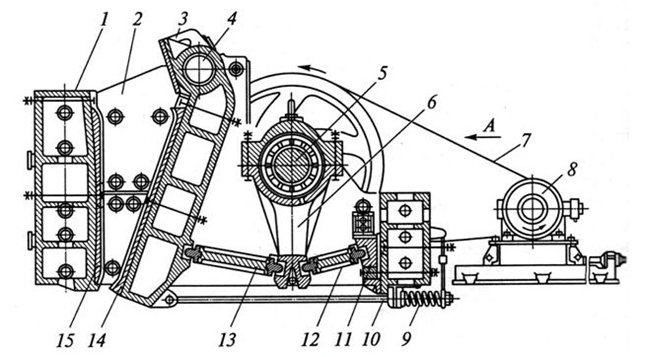
Рисунок 5 – Щічна дробарка
1 – стінка корпусу, 2 – бічна щока, 3 – рухлива щока, 4 – вісь, 5 – вал, 6 – шатун, 7 – ремінна передача, 8 – електродвигун, 9 – пружина, 10 – тяга, 11 – упор, 12,13 – плита розпору, 14,15 – плити, що дроблять.
Дробарка забезпечена двома блокуваннями, які відключають привід дробарки в наступних випадках:
2.2 Подрібнення і помел кремнію
Подрібнення і помел кремнію до класса -1,5 мм виробляється у вібромлині. Роздрібнюваний кремній вручну завантажують у камеру при зупиненому двигуні через оглядовий люк, заздалегідь знявши швидкоз’ємну кришку. При цьому сусідній патрубок кришки камери закритий заглушкою. Він використовується під час застосування рідких середовищ. Завантаживши у вібромлин 1,0–1,2 м³ кремнію і закривши люк швидкознімною кришкою, включають двигун на 3 години [1].
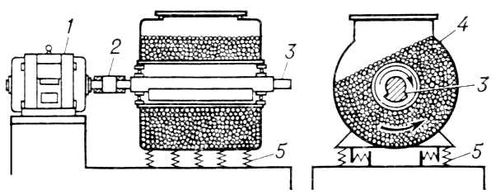
Рисунок 6 – Вібромлин
1 – електродвигун, 2 – муфта, 3 – вал, 4 – барабан, 5 – пружина
Після закінчення часу обробки вимикають двигун, відкривають вивантажувальні грати, знявши швидкознімну заглушку грат. Сполучають розвантажувальний патрубок з тарою герметичним рукавом, закріпивши його хомутом на патрубку, після чого включають двигун на період, необхідний для вивантаження кремнію.
Після вивантаження усього кремнію двигун відключають, а отриманий продукт прямує на стадію сушки [8].
Можливо, що в меленому кремнії знаходитиметься значна кількість (визначається візуально; великих неперемелених шматочків кремнію, тоді в цьому випадку такий продукт прямує на повторний помел, що попереднью пройшов відсів на віброситі.
Повторний помел здійснюється також як і вище описана операція подрібнення і помелу кремнію.
2.3 Сушка початкових компонентів керамічної сумеші
Під час приготування керамічної сумеші сушінню підлягають наступні компоненти: кварцевий пісок або динасовий мертель, мелений діабаз борошно, мелений кремній.
Сушка здійснюється в сушарній шафі, режим роботи періодичний.
Висушуваний матеріал вручну рівномірно розсипається на деках по 120-150 кг в кожному і завантажується в сушарну шафу.
У рубашку сушарної шафи подається пара або конденсат. Сушка компонентів ведеться при температурі 120 °С. Компоненти висушуються до залишкової вологості не більш 1 % (вага.). Тривалість сушки в сушарній шафі залежно від початкової вологості компонентів складає 2,5-4,5 години. [9].
Можливе проведення сушки у природних умовах. Матеріал, що сушиться, рівномірно розподіляється на піддонах (гладка чиста не піддатна корозії поверхня) протягом 2-3 діб висушується в сухому добре опалювальному приміщенні.
Кожен компонент висушується окремо. Змішування компонентів на цій стадії не допускається. Висушений продукт прямує на стадію розсівання.
Кількість висушуваного матеріалу визначається залежно від ступеню вологості початкових компонентів, потреби в керамічної суміші.
Початкова вологість початкових компонентів, особливо кварцевого піску або динасового мертеля, які доставляються відкритим способом, більше норми. Тому ці компоненти завжди вимагають сушки. Мелений кремній, що направляється із стадії помелу, а також діабазове борошно поступають на стадію сушки в закритій тарі і можуть мати вологість в межах норми. Тому ці компоненти піддаються лабораторному аналізу на вологість, після чого робиться висновок про проведення сушки меленого кремнію і діабазового борошна [6].
2.4 Розсівання початкових компонентів керамічної сумеші
Розсіванню піддаються наступні компоненти: кварцевий пісок або динасовый мертель, діабаз, мелений кремній.
Розсівання компонентів виробляється на віброситі, режим роботи періодичний. Кожен компонент піддається розсіванню окремо, змішування не неприпустимо. Завантаження компонентів у вібросито виробляється вручну. Розсівання здійснюється на сітці з нержавіючої сталі розміром осередка 1,5 мм. Клас -1,5 мм збирається в герметично закриту тару і прямує на стадію дозування і змішування компонентів, а клас +1,5 мм в приймальну ємність і при накопиченні вивозиться на звалище. Виняток становить кремній, клас +1,5 мм якого прямує на повторний помел.
Кількість оброблюваних матеріалів на стадії розсівання визначається у кожному конкретному випадку.
2.5 Дозування і змішування компонентів керамічної сумеші
Змішення усіх компонентів, що входять до складу керамічної сумеші, виробляється в двороторному змішувачі, режим роботи періодичний.
Вивантаження виробляється вручну, заздалегідь перед цим корито змішувача нахиляється по відношенню до горизонтальної площини на певний кут.
Перед змішуванням в змішувач зважується на вагах необхідна кількість кожного компонента керамічної сумеші.
2. 6 Затарювання готової продукції
Отримана вищезгаданим способом cуміш із змішувача совком засипається в паперові п'ятишарові бітуміровані мішки, які прошиваються після затарювання. На кожен мішок наклеюється ярлик з вказівкою номера партії, дати виготовлення, ваги, найменування упакованих матеріалів. Паперовий мішок поміщають у зовнішній поліетиленовий, який заварюють або прошивають. У кожен мішок засилають 35 кг керамічної сумеші [10].
Мішки з сумішью формуються в партії, проводиться лабораторний аналіз готового продукту і із складу вирушає до споживачів.
Висновки
Тривалість і ефективність роботи високотемпературних промислових агрегатів залежить від рівня їх технічної експлуатації, своєчасної діагностики виникаючих дефектів і якісного проведення профілактичних ремонтів. Своєчасне виконання необхідного об'єму і вживання найбільш раціональних профілактичних ремонтів, таких як керамічне наплавлення, дозволяють значно продовжити термін служби промислових печей [5].