Реферат по теме выпускной работы
- Введение
- 1. Способы переработки головной фракции сырого бензола
- 2. Физико–химические основы процесса переработки ГФСБ аммиачным способом
- 3. Экспериментальная часть
- 3.1 Методика выделения СS2 из ГФСБ
- 3.2 Методика анализа продуктов водной и органической фаз
- 3.3 Разделение продуктов органической фазы – бензола и дициклопентадиенa
- 3.3.1 Простая перегонка
- 3.3.2 Перегонка с водяным паром
- 3.3.3 Перегонка под вакуумом
- 4. Анализ экспериментальных данных
- 4.1 Процесс выделения СS2 из ГФСБ
- 4.2 Процесс разделения продуктов органической фазы – бензола и дициклопентадиена
- 4.2.1 Простая перегонка
- 4.2.2 Перегонка с водяным паром и под вакуумом
- 5. Пилотная установка для разделения продуктов органической фазы
- Выводы
- Список литературы
Введение
Сырой бензол, получаемый в процессе коксования каменного угля, в дальнейшем перерабатывается с целью получения чистых продуктов. Схема переработки имеет стадию предварительной ректификации, которая обеспечивает разделение низкокипящих и высококипящих соединений. Смесь низкокипящих компонентов, получаемая при этом, называется головной (ГФСБ), или сероуглеродной фракцией. Выход головной фракции составляет 2,0-3,5%. На предприятиях, перерабатывающих бензол, который получен из сернистого донецкого угля, головная фракция содержит 20-35% сероуглерода, 15-35% циклопентадиена, 20-50% бензола, 2-5% дициклопентадиен, до 10% ненасыщенных (олефины C5H10) и до 4,0% насыщенных соединений (циклопентан и гомологи, пентан, гептан) [1].
Потенциальные ресурсы ГФСБ в Украине составляют 10 тыс. т в год. Количество сероуглерода, содержащееся во фракции – 3 тыс. т в год.
Однако, в настоящее время, не существует простого, надежного и безопасного способа переработки ГФСБ [2]. Поэтому актуальной является необходимость разработки нового способа переработки этой фракции.
В данной работе описана переработка ГФСБ с использованием химического реагента аммиака, приведен анализ экспериментальных данных по разделению получаемых продуктов.
Цель: разделение продуктов органической фазы, полученной после обработки ГФСБ аммиаком.
Актуальность:
- Необходимость разработки эффективного способа разделения веществ органической фазы первичной переработки ГФСБ;
- Высокий спрос на чистые углеводородные соединения (бензол и дициклопентадиен) для промышленного синтеза.
Объект исследования: органическая фаза – смесь бензола и дициклопентадиена, – полученная при очистке ГФСБ химическим способом.
1. Способы переработки головной фракции сырого бензола
Состав ГФСБ зависит от условий ее отбора, а также от состава исходного сырья.
ГФСБ, выделяемая при ректификации сырого бензола, характеризуется следующими показателями [1]:
Плотность при 20 °С, кг/м3 – 930-980
Разгонка, °С:
начало кипения – 30-38
температура при отгонке 95% – 66-75
В соответствии с изменением состава головной фракции изменяется ее выход. При получении концентрированной головной фракции, выход ее обычно не превышает 2-3%. При высокой температуре вверху колонны, получают головную фракцию разбавленную бензолом, и выход ее достигает 4-6%.
Переработка головной фракции – сложная технологическая операция, связанная со значительными потерями и трудностями при извлечении бензола. Поэтому чрезвычайно важно стремиться к получению более концентрированной фракции [2].
Чем выше температура внизу колонны, тем более полно извлекается сероуглерод. Повысить температуру хотя бы до 90 ºС возможно лишь при большом рефлюксном числе.
Головная фракция при хранении приобретает ярко выраженный кислый характер, причем с увеличением продолжительности хранения кислотность ее растет. Установлено, что рост кислотности обусловлен образованием перекисей, и для стабилизации ГФСБ при хранении, ее необходимо ингибировать.
В головную фракцию переходит 41-46% циклопентадиена, к тому же имеют место прямые технологические потери. Остаточное количество циклопентадиена во фракции БТКС составляет обычно 0,1-0,15%.
Близость температур кипения сероуглерода и циклопентадиена (42,5 и 46,5 º С соответственно) при примерно одинаковом их содержании очень затрудняет выделение концентрированной головной фракции только ректификацией.
Промышленное применение нашел способ переработки головной фракции методом термической полимеризации, основанный на свойстве циклопентадиена образовывать под воздействием нагрева дициклопентациен с резко отличной от других компонентов фракции температурой кипения 166,6 º С. Самопроизвольно переход циклопентадиена в дициклопентациен приводит к тому, что с течением времени состав фракции и характеристика ее разделения значительно изменяются [1,2].
Впервые в промышленности процесс термической полимеризации сероуглеродной фракции был осуществлен цехом ректификации Макеевского коксохимического завода [1]. Процесс термической полимеризации осуществляется в агрегате периодического действия при температуре не выше 120º С при полном возврате конденсата образующихся паров. Головная фракция загружается в куб ректификации, в котором, благодаря подогреву глухим паром, осуществляется полимеризация циклопентадиена в димер, а также его сополимеризации с некоторыми ненасыщенными соединениями. Продукты, которые не полимеризуются и не выделяются, конденсируются и возвращаются в куб.
Продолжительность процесса термической полимеризации головной фракции зависит в основном от состава фракции и составляет 12 – 24 часа. При проведении полимеризации непрерывно меняется состав фракции вследствие образования полимеров, а также потери легкокипящих углеводородов через воздушники. Благоприятно процесс полимеризации проводить по возможности быстро, чтобы минимизировать неизбежные потери сероуглерода через воздушники. Окончание процесса полимеризации определяется прекращением изменения состава загрузки куба [1,3-5].
Специалистами Винницкого национального технического университета предложен способ извлечения сероуглерода из головной фракции путем обработки ее водным раствором аминов или амидов с получением соответствующих дитиокарбаматов. Данный способ реализуется в две стадии. На первой ступени образуется соль диалкилдитиокарбаминовой кислоты по реакции:
(1.1)
Alk – CH3, C2H5, C3H7, C4H9; M – K, Na, NH4
На второй ступени соль превращается в соответствующие дитиокарбаматы некоторых 3-d металлов по следующей схеме:
(1.2)
М ' – Cu2+, Co2+, Ni2+, Zn2+, Mn2+, Fe2+, Sn2+, Pb2+; An – Cl-, NO-, 1/2 SO42- [7].
2. Физико–химические основы процесса переработки ГФСБ аммиачным способом
Как показывает литературный обзор (пункт 1), в наше время существует мало способов переработки ГФСБ, а те способы, которые имеются, далеки от совершенства в технологическом, экологическом и экономическом аспектах.
В настоящее время способ термической полимеризации не применяется, вследствие его пожаро- и взрывоопасности, неэкологичности, крупных (до 30%) потерь основных компонентов и значительных экономических затрат [1,2].
Способ, разработанный специалистами Винницкого национального технического университета, еще не вышел за рамки лабораторных испытаний и не был применен в технологических условиях. Кроме того, амины являются относительно дорогими реагентами и в Украине не производятся.
Исследования были направлены на изучение способа извлечения сероуглерода из головной фракции путем связывания его химическим реагентом с получением ценных химических продуктов, безопасных в применении, хранении и транспортировке [4].
В качестве реагента для извлечения сероуглерода из головной фракции был выбран водный раствор аммиака. Выбор аммиака обусловлен тем, что он является относительно недорогим и доступным. Кроме того, аммиак может взаимодействовать с сероуглеродом головной фракции избирательно. В тоже время, соединения, получаемые при взаимодействии сероуглерода с аммиаком, могут быть использованы для производства важных и ценных химических продуктов.
Взаимодействие происходит по следующим схемам:
Схема 1, t ≥ 120 °С, образуется тиомочевина
CS2 + 2NH3 → H2N−CS−NH2 + H2S (2.1)
Схема 2, t = 113 °С, образуется роданид аммония
CS2 + 2NH3 → NH4−S−C≡N + H2S (2.2)
Схема 3. Изомеризация роданида аммония в тиомочевину, t ≥ 160 °С
NH4−S−C≡N → H2N−C−NH2 (2.3)
Схема 4. Образование сернистого аммония
H2S + 2NH3 → (NH4)2S (2.4)
При температуре 20-25 °С взаимодействие сероуглерода и аммиака протекает чрезвычайно медленно, а технологически выгодная реакция идет при повешенной температуре и давлении. В тоже время, увеличение температуры недопустимо, так как компоненты реакционной смеси – сероуглерод и аммиак – легколетучие и ядовитые компоненты. Исходя из данных требований, процесс проводили в герметичном автоклаве.
Для определения оптимальных условий проведения процесса взаимодействия ГФСБ и аммиака было исследовано влияние времени контакта, температуры и соотношения реагентов на степень извлечения CS2 . После 3 часов наблюдается незначительное изменение степени извлечения сероуглерода, поэтому оптимальным временем для проведения дальнейших опытов было принято время - 3 часа [6].
Температура кипения сероуглерода – 42,5 °С, а водный раствор аммиака имеет высокое парциальное давление – 0,1 МПа (40 °С). Очевидно, что взаимодействие между CS2 и NH3 в интервале температур 80-150°С протекает в газовой фазе. Давление, создаваемое в автоклаве, благоприятно влияет на реакции 2.1-2.3, поскольку они идут в газовой среде с уменьшением числа молей компонентов системы и сопровождаются поглощением образующихся промежуточных продуктов (дитиокарбаминат аммония, тиомочевина, роданид аммония, сернистый аммоний) водной фазой. По результатам опытов видно, что при изменении соотношения NH3: CS2 с 2:1 до 7:1 степень извлечения сероуглерода увеличивается от 77,3% до 99,8%. При стехиометрическом соотношении NH3: CS2 = 2:1 степень извлечения CS2 составляет 77,3%.
Анализ полученных данных показал, что при увеличении температуры с 85 до 150 °С степень извлечения возрастает с 75,5 до 98% (при соотношении NH3: CS2= 5:1). При температуре 115 °С достигается практически полное извлечение сероуглерода из органической фазы в водную фазу в форме роданистых соединений (при соотношении NH3: CS2= 7:1) [6].
Таким образом, было выбрано мольное соотношение NH3: CS2= 7:1, время контакта 3 часа, температура 120 °С.
3. Экспериментальная часть
В лабораторных условиях провели экспериментальные исследования, в которых использовали:
- головную фракцию сырого бензола состава, %:
CS2 – 32,9; циклопентадиен – 0,9; дициклопентадиен – 33,1;
бензол – 25,6;
легкие компоненты (ненасыщенные, алканы, циклоалканы) – 7,5. - водный раствор 25%-го аммиака.
3.1 Методика выделения CS2 из ГФСБ.
Как было описано выше, для проведения реакции использовали лабораторную установку - автоклав. Автоклав состоит из корпуса с крышкой, в который помещается стакан с реакционной смесью.
В стакан помещали расчетное количество ГФСБ и 25 %-ного аммиака. Затем стакан опускали в автоклав и плотно закрывали крышкой. Автоклав ставили в термостат, нагретый до определенной температуры. Далее автоклав нагревали и выдерживали определенное время.
После выдержки автоклав доставали на воздух, затем охлаждали под проточной водой 30 минут. Затем смесь переливали в делительную воронку и разделяли на две фазы: водную и органическую [9].
3.2 Методика анализа продуктов водной и органической фаз
Анализ аммиачно – солевого раствора
Для анализа системы сернистый аммоний - роданистый аммоний - тиомочевина была разработана методика, суть которой заключается в раздельном определении сернистого и роданистого аммония. Определение роданида аммония проводят титрованием азотнокислой ртутью (II) с предварительным осаждением сернистых соединений уксуснокислым кадмием Cd (CH3COO)2. Определение сульфидов и тиомочевины состоит из определения общей серы путем титрования с I2, осаждения сульфидов Cd (CH3COO)2 и определения тиомочевины. Количество сульфидов определяют по разнице объема, пошедшего на титрование общей серы и тиомочевины.
Анализ органической фазы
Анализ органической фазы проводили хроматографическим способом на хроматографе КристаллЛюкс-4000.
Условия хроматографирования [5]:
- Газ-носитель – гелий;
- Фаза – ПЕГА, 15%;
- Носитель – динахром;
- Температура термостатирования – 65 °С;
- Скорость газа – носителя – 40 мл / мин;
- Длина колонки – 4,5 м.
Компоненты головной фракции определяются по хроматограмме (рис. 3.1). Основные компоненты смеси проявляются в такой последовательности:
- легкокипящие(до С8)насыщенные углеводороды;
- легкокипящие (до С5)ненасыщенные углеводороды;
- сероуглерод(время удерживания относительно бензола 0,21);
- циклопентадиен(время удерживания относительно бензола 0,25);
- н-нонан(время удерживания относительно бензола 0,72);
- бензол.
Рисунок 3.1–Хроматограмма головной фракции сырого бензола с введением 12,3% н-нонана
Опыт считается законченным после того, как пик бензола полностью вырисуется на хроматограмме.
В конической колбе с притертой пробкой емкостью 50 мл взвешивают с точностью до 0,0002 г 1 - 1,5 г н-нонана, после чего добавляют с точностью до 0,0002 г исследуемой пробы в количестве 10-15 г. После этого рассчитывается содержание н-нонана в полученной смеси, которое должено составлять 10 - 15% (по массе). Пробу тщательно взбалтывают в конической колбе и с помощью микрошприца вводят в хроматограф.
Расчет содержания сероуглерода: определение содержания сероуглерода проводится путем сопоставления площадей пиков н-нонана и сероуглерода, которые определяются по хроматограмме.
Расчет производится по следующей формуле [5] (3.1):
где СCS2 – концентрация сероуглерода в головной фракции,% (по массе);
С – концентрация н-нонана в смеси, которая анализируется,% (по массе);
SCS2 – площадь пика сероуглерода, мм2;
S – площадь пика н-нонана, мм2;
KCS2 – калибровочный коэффициент
3.3 Разделение продуктов органической фазы - бензола и дициклопентадиена
В данной работе были рассмотрены и проведены исследования трех способов разделения органической фазы: простой перегонки, перегонки с водяным паром и под вакуумом.
3.3.1 Простая перегонка
Органическая фаза после извлечения сероуглерода представляет собой смесь бензола, дициклопентациена (ДЦПД), легких компонентов, циклопентадиена (ЦПД) и сероуглерода, который не прореагировал. Плотность 0,880 г/см3.
Состав органической фазы представлен в таблице 3.1
№ опыта |
t,°С |
Содержание, % |
||||
CS2 |
Бензол |
ЦПД |
ДЦПД |
лeгкие |
||
1 |
85 |
10,6 |
33,5 |
0,04 |
43,8 |
6,2 |
2 |
100 |
5,8 |
36,4 |
0,07 |
45,6 |
6,9 |
3 |
115 |
2,1 |
36,8 |
0,07 |
46,6 |
7,3 |
4 |
160 |
0 |
38,2 |
1,34 |
49,3 |
11,3 |
Таблица 3.1 – Состав органической фазы в зависимости от температуры проведения экспериментов
Концентрация бензола при отсутствии потерь должна увеличиваться пропорционально количеству извлеченного сероуглерода, потому что в условиях опыта бензол не участвует в химических превращениях. Это подтверждают экспериментальные значения для температур 85-115 º С.
Простая перегонка осуществляется при атмосферном давлении, в обычных перегонных приборах. Проведение процесса заключается в следующем: органическая фаза в перегонной колбе нагревается на печи и переходит в пар, далее по отводной трубке и нисходящему холодильнику конденсируется в приемник. В колбе остается высоколетучий остаток.
Дальнейший анализ состава полученных смесей органической фазы, а именно: бензол в приемнике и дициклопентадиен, оставшийся в колбе, проводится хроматографическим способом на хроматографе КристалЛюкс-4000.
3.2.2 Перегонка с водяным паром
При нагревании до высоких температур продукты реакции могут разлагаться.
В отличие от простой перегонки, применение острого пара позволяет провести разделение веществ при более низкой температуре, вследствие чего уменьшаются потери легколетучих компонентов.
Лабораторная установка для перегонки органической фазы, полученной после взаимодействия сероуглерода ГФСБ с аммиаком, изображена на рисунке 3.2.
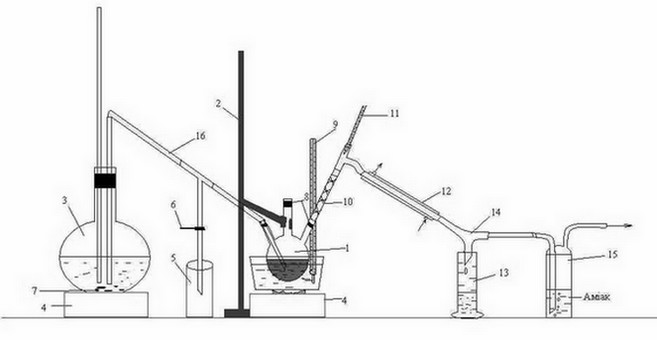
Рисунок 3.2 – Лабораторная установка для перегонки с водяным паром органической фазы, полученной после взаимодействия сероуглерода ГФСБ с аммиаком.
1 – трехгорлая колба, 2 – штатив, 3 – колба, 4 – печь, 5 – приемник конденсата, 6 – зажим, 7 – кипелки, 8 – пробки, 9, 11 – термометр, 10 – дефлегматор-«елочка», 12 – холодильник, 13 – приемник бензола, 14 – аллонж, 15 – склянка Дрекселя, 16 – переходная трубка
Головную фракцию, полученную после взаимодействия с аммиаком, нагревали на водяной бане в трехгорлой колбе 1, закрепленной на штативе 2.
Перегонку вели с острым паром, полученным в колбе 3, и по переходной трубке 16 направленным в трехгорлую колбу 1. Началом перегонки считали появление первой капли в приемнике 13, окончанием – резкое изменение (падение или увеличение) температуры, при которой шла непрерывная перегонка. Образовавшаяся смесь паров воды и бензола, направляется через дефлегматор-«елочка» 10, проходит холодильник 12, откуда уже конденсированная смесь стекает по аллонжу 14 в приемник 13. Также, через аллонж 14 проходит пар Н2S, попадает в склянку Дрекселя 15, где поглощается аммиаком.
3.2.3 Перегонка под вакуумом
Исследуемые вещества при атмосферном давлении перегоняются с большими потерями, кроме того ДЦПД при увеличении температуры может деполимеризоваться.
В тоже время, применение для разделения продуктов органической фазы водяного пара на производстве будет связано с образованием большого количества сточных вод. С целью устранения этих недостатков применили перегонку под вакуумом.
На практике перегонку под вакуумом проводят обычно при давлении от 50 до 1 мм рт. ст.[9]
Аппаратурное оформление для перегонки под вакуумом подобно аппаратуре для перегонки при атмосферном давлении, но с некоторыми дополнительными деталями. Прибор для перегонки под вакуумом состоит из следующих частей: печи для нагрева колбы, перегонной колбы, холодильника, приемника дистиллята, вакуум-насоса, а также приборов для измерения и регулирования давления.
Лабораторная установка для перегонки органической фазы под вакуумом приведена на рис. 3.3.

Рисунок 3.3 – Лабораторная установка для перегонки под вакуумом органической фазы, полученной после взаимодействия сероуглерода ГФСБ с аммиаком.
1 – перегонная колба, 2 – штатив, 3 – печь,4 – пробки, 5,7 – термометр, 6 – дефлегматор-«елочка», 8 – холодильник, 9 – аллонж, 10 – приемник бензола, 11 – склянка Дрекселя
Отличие в процессе перегонки под вакуумом от перегонки с водяным паром состоит в том, что для создания вакуума в первом случае, к приемнику подсоединяют толстостенной резиновой трубкой манометр и насос.
4. Анализ экспериментальных данных
4.1 Процесс выделение СS2 из ГФСБ
В результате протекания реакции образуется водная и органическая фазы следующего состава (рис. 4.1):
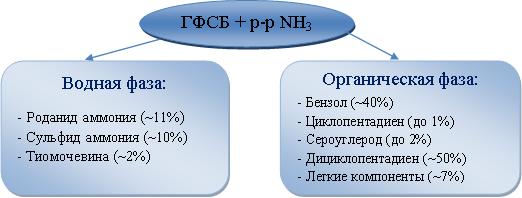
Рисунок 4.1 – Состав водной и органической фаз.
4.2 Процесс разделения продуктов органической фазы - бензола и дициклопентадиена
4.2.1 Простая перегонка
В результате проведения простой перегонки был получен отгон бензола в приемнике и тяжелый остаток в колбе.
Хроматографический метод анализа позволил определить состав этих проб:
• в приемнике: 0,76% СS2, 3,97% ЦПД, 74,69% бензола, 1,18% ДЦПД;
• остаток в колбе: 0,05% СS2, 0,03% ГПД, 48,31% бензола, 38,05% ДЦПД.
Исходная органическая фаза имела следующий состав:
2,10% СS, 0,07% ЦПД, 36.8% бензола, 46,6% ДЦПД.
Дициклопентадиен способен при повышении температуры до 115º С самопроизвольно переходить в мономер, следовательно необходимо вести перегонку при наименьшей температуре. Для снижения температуры были использованы другие методы - перегонка с водяным паром и под вакуумом.
4.2.2 Перегонка с водяным паром и под вакуумом
Хроматограммы, полученные в результате анализа продуктов перегонки головной фракции с водяным паром, представлены на рис. 4.2 – 4.4.
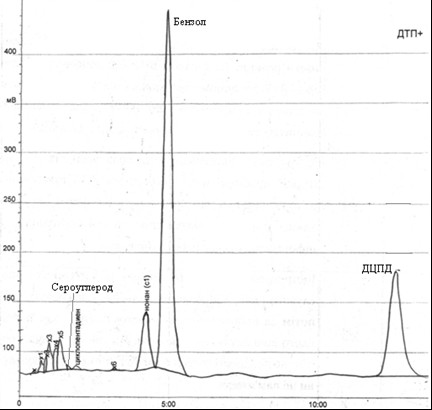
Рис. 4.2 – Хроматограмма исходной головной фракции, полученной после обработки головной фракции аммиаком
Согласно результатам анализа хроматограммы, в исходной пробе содержится 62,8% бензола, 25,8% дициклопентадиена, 0,19% сероуглерода.
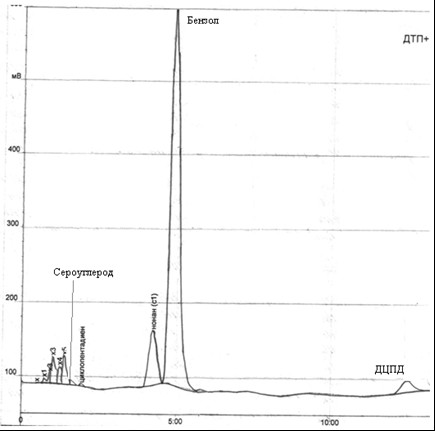
Рис. 4.3 – Хроматограма пробы в приемнике бензола, полученная после перегонки ГФСБ с водяным паром
Согласно данным анализа, в приемнике содержится 81,7% бензола, 3,7% дициклопентадиена, 0,59% сероуглерода.
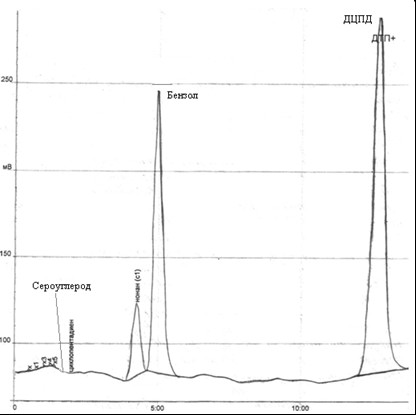
Рис. 4.4 – Хроматограмма остатка в колбе после перегонки ГФСБ с водяным паром.
При анализе хроматограммы получили следующие показатели: количество дициклопентадиена 55,7%, бензола 30,7%, сероуглерода 0,005%.
Результаты разделения бензола и дициклопентадиена различными методами представлены в табл. 1, %:
Перегонка с водяным паром | Перегонка под вакуумом | ||
Исходная проба |
Бензол |
62,8 |
58,82 |
ДЦПД |
25,8 |
21,53 |
|
СS2 |
0,19 |
0,19 |
|
В приемнике |
Бензол |
81,7 |
90,04 |
ДЦПД |
3,7 |
0,22 |
|
СS2 |
0,59 |
0,01 |
|
Остаток в колбе |
Бензол |
30,7 |
17,68 |
ДЦПД |
55,7 |
42,00 |
|
СS2 |
0,005 |
2,97 |
Таблица 1 - Результаты перегонок с водяным паром и под вакуумом
Сравнивая результаты опытных данных, можно сделать вывод, что перегонка с водяным паром и под вакуумом являются достаточно эффективными, при их применении получаем 82-91%-ный бензол и насыщенную дициклопентадиеном (42-56%) остаточную фракцию.
5. Пилотная установка для разделения продуктов органической фазы
Для разделения продуктов органической фазы предлагается применять ректификационную установку.
В ректификационных колоннах исходная смесь в результате массообмена между паровой и жидкой фазами, движущихся противотоком, разделяется на два компонента: дистиллят, который обогащен более летучим компонентом, и кубовый остаток, содержащий намного меньше летучего компонента.
Расчет насадочной ректификационной колонны непрерывного действия.
Расчет ректификационной колонны сводится к определению геометрических размеров - диаметра и высоты. Установка работает при атмосферном давлении и с довольно агрессивными жидкостями, поэтому принимаем в качестве насадки керамические кольца Рашига размером 10 × 10 × 1,5, удельная поверхность насадки а = 440 м2/м3, свободный объем ε = 0,7 м3/ м3, насыпная плотность ρ = 700 кг/м 3 [11].
На рис. 5.1 приведена принципиальная схема насадочной ректификационной установки непрерывного действия.
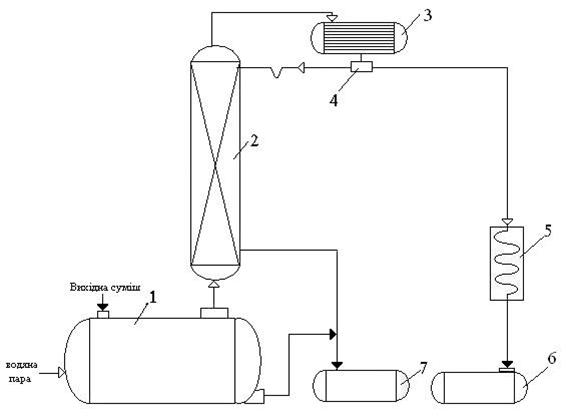
Рис. 5.1 – Принципиальная схема насадочной ректификационной установки непрерывного действия
1 – перегонный куб, 2 – насадочная ректификационная колонна, 3 – дефлегматор, 4 – делитель потока, 5 – теплообменник, 6 – приемник дистиллята, 7 – емкость для кубовой жидкости
Исходную смесь и водяной пар подают в перегонный куб 1, откуда пары поступают в ректификационную колонну 2.
Стекая вниз колонны, жидкость взаимодействует с паром и поднимается наверх колонны. Начальный состав пара примерно равен составу кубового остатка, т.е. содержит малое количество легколетучего компонента (бензола). В результате массообмена с жидкостью, пар обогащается легколетучим компонентом. Для более полного обогащения, верхнюю часть колонны орошают флегмой (в соответствии с заданным флегмовым числом). Часть конденсата выводится из дефлегматора в виде готового продукта разделения – дистиллята, который охлаждается в теплообменнике 5 и поступает в приемник дистиллята 6.
Из нижней части колонны, а также нижней части перегонного куба, непрерывно отводится кубовый остаток - продукт, обогащенный труднолетучим компонентом (дициклопентадиеном). Кубовый остаток поступает в емкости для кубовой жидкости 7.
Расчет пилотной установки разделения продуктов органической фазы здесь не приводится, вследствие его громоздкости.
В результате проведенного расчета: D = 6 см, Hнасадки = 1,5 м.
ВЫВОДЫ
- Выполнен аналитический обзор способов переработки ГФСБ, в результате которого установлено, что на данный момент существует мало способов переработки ГФСБ, а те способы, которые имеются, далеки от совершенства в технологическом, экологическом и экономическом аспектах. Ранее применяемый в промышленности метод термической полимеризации сейчас не используется, вследствие его пожаро- и взрывоопасности, неэкологичности, крупных (до 30%) потерь основных компонентов и значительных экономических затрат.
- Рассмотрены физико–химические основы переработки ГФСБ аммиачным способом. Данный химический метод позволяет практически полностью (97-99%) выделить сероуглерод из ГФСБ (при соотношении СS2:NH3=1:7, времени контакта 3 часа и температуре 120°С). Кроме того выбранный метод является экологически безопасным, так как на первой стадии происходит связывание токсичного сероуглерода.
- Показано, что для разделения продуктов можно применять различные виды перегонок. Однако выяснено, что с точки зрения эффективности эти способы существенно отличаются.
- При простой перегонке разделение происходит при температуре 80°С, но в силу неустойчивости температур и больших потерь ценных химических компонентов, ее применение нецелесообразно.
- Перегонка с острым паром показала следующие результаты в виде чистых продуктов: 82% бензол и 56% ДЦПД. Недостаток этого метода заключается в том, что применение водяного пара связано с дополнительными затратами на оборудование для производства пара, а следовательно с повышением себестоимости получаемых продуктов.
- Исследования показали, что наиболее технологичным и экономичным является способ перегонки под вакуумом (получен отгон бензола с концентрацией до 92% и ДЦПД – 42%).
При написании данного реферата магистерская работа еще не закончена. Окончательное завершение - декабрь 2012 г. Полный текст работы и материалы по теме могут быть получены у автора или его руководителя после указанной даты.
СПИСОК ЛИТЕРАТУРЫ
- Лейбович Р.Е., Обуховский Я.М., Сатановский С.Я. Технология коксохимического производства. – М.: Металлургия, 1966. – 463 с.
- Коляндр Л.Я. Новые способы переработки сырого бензола. – М.: Металлургия, 1976. – 192 с.
- Карлинский Л.Е. Выделение циклопентадиена из головной фракции сырого бензола / Л.Е. Карлинский, З.А. Бучкина, М.К. Горлов и др. // Кокс и химия. – 1968 – № 11. – С. 30 – 34.
- Химия и технология сероуглерода/ А.А. Пеликс, Б.С. Аранович, Е.А. Петров, Р.В. Котомкина. – Л.: Химия, 1986. – 224 с.
- Глузман Л.Д. Лабораторный контроль коксохимического производства/ Л.Д. Глузман. М.: Металлургия, 1968. – 473 с.
- О возможности извлечения сероуглерода из головной фракции сырого бензола химическим методом / И.Г. Крутько,А.В. Кипря, В.А. Колбаса, А.С. Комаров, К.А. Сацюк // Вісник Національного технічного університету «Харківський політехнічний інститут». Збірник наукових праць. Тематичний випуск «Хімія, хімічна технологія та екологія». – Харків: НТУ «ХПІ». – 2010. – № 11. – С. 43 – 47.
- Титов Т. С., Пелишенко С. В., Гордиенко О. А., Петрук Р. В.,Сандомирский О. В. Экологические вопросы коксохимических производств и пути их решения. Тези доповідей, 1 том, V Міжнародна науково-технічна конференції студентів, аспірантів та молодих вчених,Серія: хімія та сучасні технології, 2011. – 564 с.
- Крутько И.Г., Кіпря О.В., Комаров А.С. Извлечение сероуглерода из головной фракции сырого бензола раствором аммиака. Состав и свойства органической и водной фаз. Наукові праці Донецького національного технічного університету. Серія: Хімія і хімічна технологія, 2011. – Випуск 17 (187). – с. 167 – 171.
- Препаративная органическая химия. Под ред. Н. С. Вульфсона, М.: Химия, 1964 г., 908 с.
- Людмирская Г. С., Барсукова Т. А., Богомольный А. М. Равновесие жидкость – пар: Справ. изд. Под ред. А. М. Богомольного. Л.: Химия, 1987. – 336 с.
- Основные процессы и аппараты химической технологии: Пособие по проектированию/Г. С. Борисов, В. П. Брыков, Ю. И. Дытнерский и др. Под ред. Ю. И. Дытнерского, 2-е изд., перераб. и допол. М.: Химия, 1991. - 496 с.
- Курсовое проектирование по предмету «Процессы и аппараты химической промышленности»: Учеб. пособие для учащихся техникумов/ М.Н. Кувшинский, А. П. Соболева. – 2-е изд., перераб. и допол. – М, 1980. – 223 с.