Abstract
- Introduction
- 1. Methods of processing the head fraction of crude benzene
- 2. Physico–chemical bases of the recycling process HFCB ammonia method
- 3. The experimental part
- 3.1 Separation of products of the organic phase – benzene and dicyclopentadiene
- 3.1.1 The simple distillation
- 3.1.2 Distillation with steam
- 3.1.3 Distillation with uses vacuum
- 4. Analysis of experimental data
- 4.1 The process of separating of products of the organic phase – benzene and dicyclopentadiene
- 4.1.1 A simple distillation
- 4.1.2 Distillation with steam and vacuum
- 5. Pilot plant for separation the products of the organic phase
- Conclusion
- List of sources
Introduction
The crude benzene, obtained in the process of coking coal in the future processed to obtain pure products. Scheme processing has pre-processing stage is distillation, which provides separation of low-boiling compounds and high boiling. A mixture of low-boiling components, obtained at the same time, called parent (HFCB) or serouglerodnoy fraction. Exit the head fraction is 2.0-3.5%. In enterprises, processing benzene, which is derived from sulfur Donetsk coal fraction of the parent contains 20-35% carbon disulfide, cyclopentadiene 15-35%, 20-50% of benzene, 2-5% of dicyclopentadiene, and 10% unsaturated (olefins C5H10) and up to 4.0% of saturated compounds (cyclopentane, and homologs, pentane, heptane)[1].
However, at present time, there is no simple, reliable and safe method processing HFCB [2]. Therefore, the need is urgent develop new ways of processing this fraction.
In this work describes the processing of GFSB using chemical reagent ammonia, the analysis of experimental data on the separation the resulting products.
The purpose of the work: separation products of the organic phase obtained after processing HFCB ammonia.
Actuality:
- need develop an effective method of separating substances of the organic phase primary processing HFCB;
- high the demand for pure hydrocarbon compounds (benzene and dicyclopentadiene) for the industrial synthesis.
The object of study: the organic phase - a mixture of benzene and dicyclopentadiene - received when cleaning HFCB chemically.
1. Methods of processing the head fraction of crude benzene
Composition of GFSB depends on the conditions of its selection and the composition of the feedstock.
HFCB released during distillation of crude benzol, is as follows [1]:
Density at 20 °С, kg/m3 – 930-980
Distillation, °С:
beginning of the boil – 30-38
temperature at distillation of 95% – 66-75
According to changing the composition of head fraction changing its output. At receipt of a concentrated head fraction, it usually does not output than 2-3%. At high temperatures at the top of the column are head fraction diluted with benzene, and its output reach 4-6%.
Processing of head fraction - a complex process operation associated with significant loss and difficulty in removing benzene. So it is extremely important to seek a more concentrated fraction [2].
The higher the temperature at the bottom of the column, the more fully recovered carbon disulfide. To increase temperature of at least 90 º C is possible only if large reflux including.
The head fraction when storage becomes pronounced acidic character, and with increasing duration of storage increases its acidity. Been established that an increase of acidity due to the formation of peroxides, and to stabilize HFCB during storage, it should be inhibited.
In the head fraction goes 41-46% cyclopentadiene, in addition, there are direct technological losses. The residual amount of cyclopentadiene at a fraction of BTKS is usually 0.1-0.15%.
Affinity the boiling points of carbon disulfide, and cyclopentadiene (42.5 and 46,5 º C, respectively) at approximately the same content they are hampering the the head of concentrated fractions only rectification.
Industrial use has found a way of processing method of head fraction thermal polymerization, which is based on the property of cyclopentadiene form under the influence of heating ditsiklopentatsien with sharply different from the other components of the fraction of boiling point 166,6 º C. Self-shift cyclopentadiene into ditsiklopentatsien leads to the fact that over time the composition of the fraction and characterization of the separation significantly altered [1,2].
Specialists Vinnytsia National Technical University proposed a method recovery of carbon disulfide from the head fraction by processing of water solution of amines or amides to produce the corresponding dithiocarbamates. This method is realized in two stages. The first stage is formed salt dialkilditiokarbaminovoy acid of reaction:
(1.1)
Alk – CH3, C2H5, C3H7, C4H9; M – K, Na, NH4
In the second stage of the salt turns the appropriate dithiocarbamates of some 3-d metals as follows:
(1.2)
М ' – Cu2+, Co2+, Ni2+, Zn2+, Mn2+, Fe2+, Sn2+, Pb2+; An – Cl-, NO-, 1/2 SO42- [7].
2. Physico–chemical bases of the recycling process HFCB ammonia method
As the literature review (paragraph 1), presently there are few ways of processing HFCB, and those methods that are available are far from perfect in the technological, ecological and economic aspects.
At the present time thermal polymerization method is not used, because of its fire and explosion hazards, not ecology, large (up to 30%) loss main components and significant economic costs [1,2].
The method, developed by the specialists of Vinnitsa National Technical University, has not went beyond the laboratory testing and has not been used in technological terms. In addition, the amines are relatively expensive reagents and Ukraine are not made it's.
The studies were aimed at studying ways to remove carbon disulfide from the head fraction by binding it's to a chemical reagent and produce valuable chemical products that are safe to use, storage and transportation [4].
As a reagent for the extraction of carbon disulfide from the head fraction was selected water solution of ammonia. The choice of ammonia caused by the fact that it is relatively inexpensive and accessible. In addition, ammonia can interact with carbon disulfide head fraction selectively. At the same timethe compounds obtained by the interaction of carbon disulfide and ammonia, can be used to make important and valuable chemical products .
The interaction is the following schemes:
Scheme 1, t ≥ 120 °С, formed by thiourea
CS2 + 2NH3 → H2N−CS−NH2 + H2S (2.1)
Scheme 2, t = 113 °С, formed by ammonium thiocyanate
CS2 + 2NH3 → NH4−S−C≡N + H2S (2.2)
Scheme 3. Isomerization of ammonium thiocyanate into thiourea, t ≥ 160 °С
NH4−S−C≡N → H2N−C−NH2 (2.3)
Scheme 4. The formation of ammonium sulphide
H2S + 2NH3 → (NH4)2S (2.4)
At a temperature of 20-25 ° C the interaction of carbon disulfide and ammonia proceeds very slowly, and technologically advantageous the reaction proceeds in the hanging temperature and pressure. At the same time, the temperature increase is unacceptable, since the components of the reaction mix - carbon disulfide and ammonia - toxic and highly volatile components. Based on of these requirements, the process is conducted in a hermetically sealed autoclave.
Molar ratio was chosen is NH3: CS2= 7:1, contact time of 3 hours, the temperature 120 °С.[6]
3. The experimental part
In the laboratory, conducted pilot studies in which used:
- the head fraction of crude benzene composition, %:
CS2 – 32,9; cyclopentadiene – 0,9; dicyclopentadiene– 33,1;
benzene – 25,6;
lightweight components (unsaturated, alkanes, cycloalkanes) – 7,5. - water solution 25% of ammonia.
3.1 Separation of products of the organic phase – benzene and dicyclopentadiene
In this work have been reviewed and investigated of the three ways of separating the organic phase: simple distillation, steam distillation and with vacuum.
3.1.1 Simple distillation
The organic phase after extraction of carbon disulfide is a mixture of benzene, ditsiklopentatsiena (DCPD) lightweight components, cyclopentadiene (CPD) and carbon disulfide, which did not react. The density of 0.880 g / cm3.
The composition of the organic phase is shown in table 3.1
№ of experience |
t,°С |
Capacity, % |
||||
CS2 |
benzene |
CPD |
DCPD |
lightweight components |
||
1 |
85 |
10,6 |
33,5 |
0,04 |
43,8 |
6,2 |
2 |
100 |
5,8 |
36,4 |
0,07 |
45,6 |
6,9 |
3 |
115 |
2,1 |
36,8 |
0,07 |
46,6 |
7,3 |
4 |
160 |
0 |
38,2 |
1,34 |
49,3 |
11,3 |
Table 3.1 – The composition of the organic phase, depending on the temperature of the experiments
The concentration of benzene without of losses must increase in proportion retrieved carbon disulfide, because under the experimental conditions benzene was not involved in chemical reactions. This is confirmed experimental values for temperatures 85-115 º C.
Simple distillation carried at atmospheric pressure in conventional distillation apparatus. Carrying out the process is as follows: the organic phase in the distillation flask is heated on the stove and turns into steam, then along the outlet tube and top-down cooler condenses in the receiver. In the flask is still highly volatile residue.
Further analysis of the obtained compounds of the organic phase, namely benzene in the receiver and dicyclopentadiene, which left in flask, by chromatographic method is held on chromatograph KristallLyuks-4000.
3.1.2 Distillation with steam
When heated to high temperatures, the reaction products can decompose.
In contrast to simple distillation, the use of steam allows for separation of compounds at much lower temperatures, resulting in reduced loss of highly volatile components.
Laboratory installation for the distillation of the organic phase received after the interaction of carbon disulfide HFCB with ammonia, shown in figure 3.2.
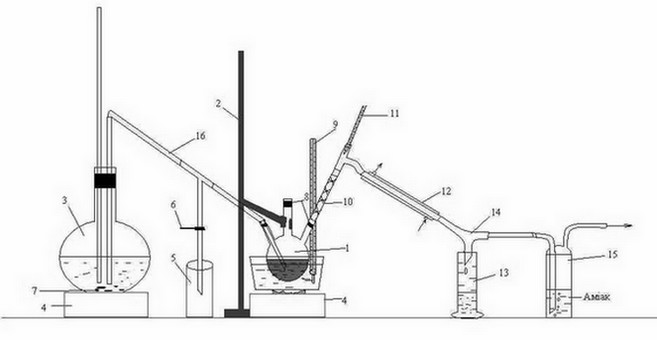
Figure 3.2 – Laboratory installation for the distillation of the organic phasereceived after interaction ammonia with carbon disulfide of the HFCB
1 – three-necked flask, 2 – Stand 3 – flask, 4 – oven, 5 – condensate receiver, 6 – clamp,
7 – kipelki, 8 – tube, 9, 11 – thermometer 10 – reflux, "Tree", 12 – refrigerator,
13 – receiver of benzene, 14 – allonge, 15 – Drexel flask, 16 – tube transition
Head fraction received after interaction with ammonia was heated in a water bath in a three-neck flask 1, fixed to a stand2.
The resulting mixture of water vapors and benzene, routed through reflux "Tree" 10, is a refrigerator 12, from which the condensed mixture flows down the rider 14 to receiver 13. Also, a rider is 14 pairs of H 2 S, falls into the bottle Dressel 15, where the ammonia is absorbed.
3.1.3 Distillation with vacuum
The test substances were distilled off at atmospheric pressure with large losses, in addition DCPD with increasing temperature can depolymerize.
At the same time, the use of products for the separation of the organic phase in the production of water vapor is due to the formation of large quantity of wastewater. The purpose eliminate these drawbacks used distillation with vacuum.
Laboratory installation for the distillation of the organic phase with vacuum is shown in Fig. 3.3.

Figure 3.3 – Laboratory installation for vacuum distillation of the organic phasereceived after interaction ammonia with carbon disulfide of the HFCB.
1 – distilling flask, 2 – stand 3 – oven, 4 – plugs, 5,7 – thermometer 6 – reflux–"Tree", 8 – refrigerator, 9 – allonge, 10 – the receiver of benzene, 11 – Drexel flask
The difference in the process of distillation with vacuum from the steam distillation is that to create a vacuum in the first case, to a receiver connected via a thick-walled rubber tube manometer and the pump.
4. Analysis of experimental data
4.1 The process of separating the organic phase products - benzene and dicyclopentadiene
4.1.1 A simple distillation
The result of simple distillation was obtained benzene in the receiver and heavy residue in the flask.
Chromatographic method of analysis allowed to define the composition of these tests:
• at the receiver: 0,76% СS2, 3,97% CPD, 74,69% benzene, 1,18% DCPD;
• residue in the flask: 0,05% СS2, 0,03% CPD, 48,31% benzene, 38,05% DCPD.
The original organic phase had the following composition:
2,10% СS, 0,07% CPD, 36.8% benzene, 46,6% DCPD.
At higher temperatures up to 115 º C, dicyclopentadiene is capable spontaneously go into the monomer. Therefore necessary to conduct the distillation at minimum temperature. To reduce the temperature were used other methods - steam distillation and distillation with vacuum.
4.1.2 The steam distillation and the distillation with vacuum
Chromatograms obtained from analysis of the products of distillation head fractions with water vaporare shown in Figure. 4.2 – 4.4.
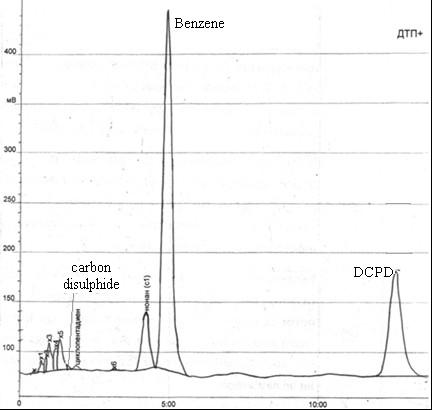
Fig. 4.2 – Chromatogram of the original head fraction obtained after treatment of head fraction by ammonia
According to results of analysis of chromatograms, in the original sample contained 62.8% benzene, 25.8% of dicyclopentadiene, 0.19% of carbon disulfide.
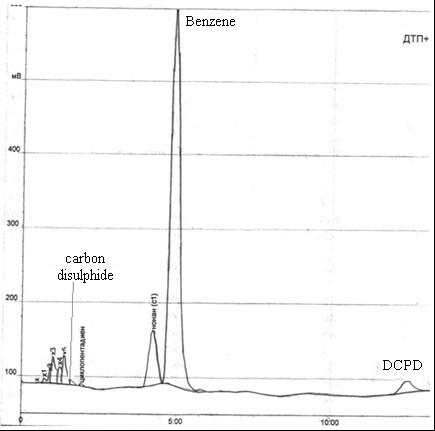
Рис. 4.3 – Xromatogramma obtained after steam distillation sample in the receiver benzene
According to the data analysis, the receiver contains 81.7% benzene, 3.7% dicyclopentadiene, 0.59% of carbon disulfide.
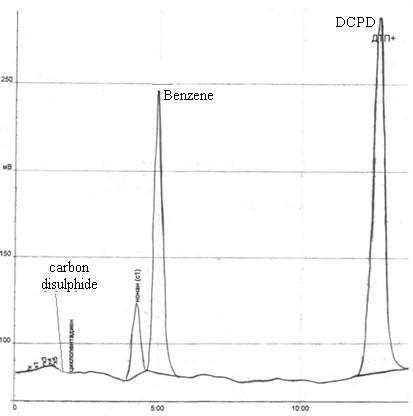
Рис. 4.4 – Hromatograma residue in the flask after distillation HFCB with steam.
In the analysis chromatogram obtained the following parameters: dicyclopentadiene 55.7%, 30.7% benzene, carbon disulfide 0.005%.
Results separation of benzene and dicyclopentadiene by different methods shown in table. 1, %:
Steam distillation | Distillation with vacuum | ||
The original sample |
Benzene |
62,8 |
58,82 |
DCPD |
25,8 |
21,53 |
|
СS2 |
0,19 |
0,19 |
|
In the receiver |
Benzene |
81,7 |
90,04 |
DCPD |
3,7 |
0,22 |
|
СS2 |
0,59 |
0,01 |
|
The residue in the flask |
Benzene |
30,7 |
17,68 |
DCPD |
55,7 |
42,00 |
|
СS2 |
0,005 |
2,97 |
Table 1 - The results of the distillations with steam and the distillations with vacuum
By comparing the results of experimental data, we can conclude that the distillation with steam and the distillation with vacuum are quite effective, as they use we get 82-91% benzene and saturated by dicyclopentadienyl (42-56%) the residual fraction.
5. Pilot plant for the separation the products of the organic phase
for the separation products of the organic phase is proposed to use the rectification installation.
The calculation of distillation column is reduced to the determination of it's geometric size - the diameter and height. The plant operates at the atmospheric pressure and with a fairly aggressive fluids, so take as the attachments ceramic Raschig rings size by 10 × 10 × 1,5, specific surface of attachments а = 440 m2/m3, free space ε = 0,7 m3/ m3, bulk density ρ = 700 kg/m 3 [11].
In Fig. 5.1 shows a basic scheme of a packed distillation installation continuous action.
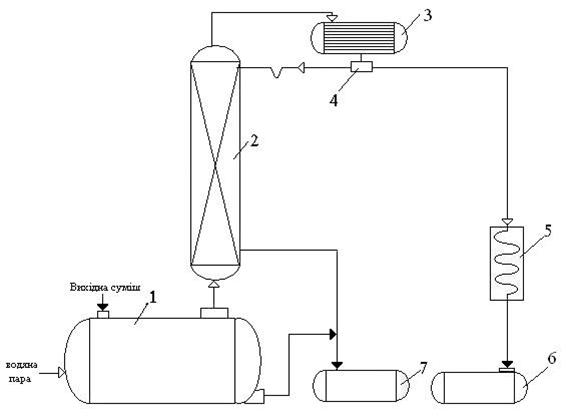
Fig. 5.1 – Basic scheme of a packed distillation installation continuous action
1 – distilling tank, 2 – packed distillation column, 3 – reflux, 4 – the flow divider, 5 – the heat exchanger, 6 – distillate receiver, 7 – the tank for bottoms liquid
original mixture and water steam is fed into an distilling tank, where pairs enter the distillation column 2.
Flowing down the column, the liquid reacts with the steam and rises to the top column. Starting composition of the vapor is approximately equal to the composition of bottoms residue, ie contains a small amount of highly volatile components (benzene). The result mass exchange with liquid, vapor is enriched highly volatile component. For a more complete enrichment, top of the column are irrigated reflux (in accordance with a given the reflux ratio). Part of the condensate removed from reflux in the form of finished product separation - the distillate, which is cooled in heat exchanger 5 and enters to the receiver distillate 6.
From the bottom of the column and the bottom of the distillation cube, a continuous assigned bottoms - a product enriched in low-volatility component (dicyclopentadienyl). Bottoms goes to the tank for bottom fluid 7.
The calculation of pilot plant for separation products of the organic phase is not presented here, because of its complexity.
The result of these calculations: D = 6 sm, Hattachments = 1,5 m.
Conclusion
- Is made an analytical review methods of processing HFCB, which resulted in found that at the moment there are few ways HFCB processing, and the ways that are far from excellence in the technological, environmental and economic aspects. Previously employed in the industry method of thermal polymerization are not used due to its fire-and explosion, not eco-friendly, large (up to 30%) losses of main components and large economic costs.
- Are considered the physico–chemical bases of processing HFCB by the ammonia method. Given chemical method can almost completely (97-99%) to allocate of carbon disulfide of HFCB (at a ratio of CS 2 : NH 3 = 1:7, contact time of 3 hours and a temperature of 120 ° C). In addition selected method is environmentally safe, since the first stage, the binding of toxic carbon disulfide.
- It is shown that separation of products you can use different types of distillations. However, found that in terms of efficiency, these methods substantially different.
- With a simple distillation separation occurs at a temperature of 80 ° C, but because temperature is instability, and there are large losses of valuable chemical components, its use is impractical.
- Distillation with acute vapor showed the following results in the form of pure product: 82% benzene and 56% of the DCPD. The disadvantage of this method lies in the fact that the use of steam due to the additional costs on equipment for the production of steam, and therefore with increasing cost of the products.
- Researches showed that the most technologically advanced and cost-effective way is distillation with vacuum (obtained from the benzene concentration up to 92% and DCPD - 42%).
In writing this essay master's work yet is not finished. Final completion - the December 2012. Full text of the work and materials on the topic may be obtained from the author or her scientific adviser after this date.
List of sources
- Лейбович Р.Е., Обуховский Я.М., Сатановский С.Я. Технология коксохимического производства. – М.: Металлургия, 1966. – 463 с.
- Коляндр Л.Я. Новые способы переработки сырого бензола. – М.: Металлургия, 1976. – 192 с.
- Карлинский Л.Е. Выделение циклопентадиена из головной фракции сырого бензола / Л.Е. Карлинский, З.А. Бучкина, М.К. Горлов и др. // Кокс и химия. – 1968 – № 11. – С. 30 – 34.
- Химия и технология сероуглерода/ А.А. Пеликс, Б.С. Аранович, Е.А. Петров, Р.В. Котомкина. – Л.: Химия, 1986. – 224 с.
- Глузман Л.Д. Лабораторный контроль коксохимического производства/ Л.Д. Глузман. М.: Металлургия, 1968. – 473 с.
- О возможности извлечения сероуглерода из головной фракции сырого бензола химическим методом / И.Г. Крутько,А.В. Кипря, В.А. Колбаса, А.С. Комаров, К.А. Сацюк // Вісник Національного технічного університету «Харківський політехнічний інститут». Збірник наукових праць. Тематичний випуск «Хімія, хімічна технологія та екологія». – Харків: НТУ «ХПІ». – 2010. – № 11. – С. 43 – 47.
- Титов Т. С., Пелишенко С. В., Гордиенко О. А., Петрук Р. В.,Сандомирский О. В. Экологические вопросы коксохимических производств и пути их решения. Тези доповідей, 1 том, V Міжнародна науково-технічна конференції студентів, аспірантів та молодих вчених,Серія: хімія та сучасні технології, 2011. – 564 с.
- Крутько И.Г., Кіпря О.В., Комаров А.С. Извлечение сероуглерода из головной фракции сырого бензола раствором аммиака. Состав и свойства органической и водной фаз. Наукові праці Донецького національного технічного університету. Серія: Хімія і хімічна технологія, 2011. – Випуск 17 (187). – с. 167 – 171.
- Препаративная органическая химия. Под ред. Н. С. Вульфсона, М.: Химия, 1964 г., 908 с.
- Людмирская Г. С., Барсукова Т. А., Богомольный А. М. Равновесие жидкость – пар: Справ. изд. Под ред. А. М. Богомольного. Л.: Химия, 1987. – 336 с.
- Основные процессы и аппараты химической технологии: Пособие по проектированию/Г. С. Борисов, В. П. Брыков, Ю. И. Дытнерский и др. Под ред. Ю. И. Дытнерского, 2-е изд., перераб. и допол. М.: Химия, 1991. - 496 с.
- Курсовое проектирование по предмету «Процессы и аппараты химической промышленности»: Учеб. пособие для учащихся техникумов/ М.Н. Кувшинский, А. П. Соболева. – 2-е изд., перераб. и допол. – М, 1980. – 223 с.