Реферат за темою випускної роботи
Зміст
- Вступ
- 1. Актуальність теми
- 2. Аналіз існуючих конструкцій шлаковоза
- 2.1 Шлаковоз з гвинтовим механізмом кантування чаші
- 2.2 Зубчастий механізм кантування чаші шлаковоза
- 3. Опис запропонованої конструкції четырехзвенного механізму кантування чаші шлаковоза
- 4 Розрахункова частина
- 4.1 Синтез і кінематичне дослідження четырехзвенного механізму
- 4.2 Визначення координат центру тяжіння і об'єму рідини, що моделює шлак
- 4.3 Розрахунок моменту опору кантуванню чаші
- Висновки
- Перелік посилань
Вступ
Кислородно-конвертерне виробництво сталі, в даний час, є одним з лідируючих, оскільки воно дозволяє в короткі терміни переплавляти передільний чавун у високоякісну сталь. Процес виплавки сталі супроводжується виходом побічних продуктів, одним з яких є шлак. На багатьох великих металургійних підприємствах утилізація шлаку досягає 70÷80% і більше. В даний час поставлене і вирішується завдання переробки всього металургійного шлаку в придатний для будівельної індустрії продукт і повної ліквідації на території заводів шлакових відвалів. Основну кількість шлаку гранулюють, деяку частину переробляють на щебінь, пемзу, шлаколіті вироби, мінеральну вату, мінеральні добрива. Грануляцію здійснюють на деякому віддаленні від печі або цеху [1].
Для прибирання шлаку від печей і транспортування його на переробку або у відвал застосовують шлаковози. До шлаковозів пред'являють наступні основні вимоги: форма чаші повинна сприяти безперешкодному виходу з неї затверділого шлаку на шлаковому відвалі; має бути виключено самовілне перекидання чаші, як при його кантуванні, так і при рухомому або зупиненому шлаковозі; має бути забезпечена поперечна стійкість шлаковоза при перекиданні чаші як навантаженої, так і порожньої; конструкція, форма і матеріал чаші, а також спосіб її кріплення повинні забезпечувати високу довговічність чаші; привід механізму кантування повинен допускати можливість регулювання швидкості зливу шлаку на грануляційних установках [1].
Тому було спеціально розроблено та досліджено за допомогою сучасних технічних засобів - кривошипно-шатунний механізм кантування чаші шлаковоза. При цьому вивчався процес кантування чаші, а саме, характер зміни моменту опору при кантуванні чаші.
1. Актуальність теми
Металургійні підприємства належать до найбільш великих народногосподарських об'єктів, що значною мірою визначають рівень економічного розвитку. З усього різноманіття техногенних утворень, що отримуються в металургійному виробництві, основний об'єм (до 80%) від загальної кількості твердих промислових відходів (ТПО) складають шлакові відвали. Переробка шлаків визначає практичну суть організації безвідходного металургійного виробництва.
Розташовані в міській смузі шлакові відвали порушують ландшафт територій, для розміщення відвалів відчужуються земельні угіддя, погіршується екологічна обстановка регіону.
Нині у більшості високорозвинених країн використання силікатної продукції металургійних підприємств досягає 90%. У будівельній індустрії використовуються їх в'яжучі властивості. Проте найцінніше, що знаходиться в шлаку, це метал. Способів витягання металу зі шлаків, які випробувані в промислових умовах, немає. Тому метал на підприємствах витягається тільки з твердих шлаків при первинній переробці на гранульованій установці і при вторинній - на подрібнювально-сортувальних установках.
Існуючі в даний момент часу механізми перекидання чаші шлаковоза не можуть забезпечити рівномірне зливання шлаку на гранульовані установки з метою отримання гранул з шлаку однакової фракції для зручності переробки на подрібнювальних установках.
Зіткнувшись з цим питанням, була знайдена відповідь при дослідженні і конструюванні фізичної моделі кривошипо-шатунного механізму кантування, який забезпечує рівномірне зливання шлаку на гранульовані установки, що забезпечує ефективнішу переробку шлаку з меншими витратами.
2. Аналіз існуючих конструкцій шлаковоза
Нині на підприємствах металургійного комплексу експлуатують шлаковози, що відрізняються не лише об'ємом чаш, але і конструкцією механізмів їх кантування.
2.1 Шлаковоз з гвинтовим механізмом кантування чаші
Гвинтовий механізм кантування чаші (рис. 2.1.), який змонтований на рамі, включає: електродвигун 14 змінного струму; одноступінчатий циліндричний редуктор 13; проміжний вал, сполучений з редуктором муфтою, який несе на собі шестерню 12; пару знаходящихся у зачепленні один з одним однакових циліндричних зубчастих коліс 11, одне з яких отримує обертання від шестерні 12; два паралельно розташованих, змонтованих на підшипниках кочення вантажних гвинта 10 з трапецеїдальним самогальмуючим різьбленням; дві гайки 9, що закріплені в траверсі 8, яка вільно закріплена (на втулці) на одній з цапф 6 опорного кільця. Шестерня 12 і колеса 11 закриті кожухом.
Через систему передач обертання від електродвигуна 14 перетворюється гвинтами 10 в поступальну ходу гайок 9 і траверси 8, а отже і опорного кільця з чашею. Знаходячись в зачепленні з нерухомими рейками 3, зубчасті сектори 5 при цьому обкатуються по них і приводять в обертання опорне кільце з чашею.
Таким чином, при русі катків 7 по направляючих 4 відбувається перекидання чаші при одночасному переміщенні її від середини рами шлаковоза до краю. У міру наближення чаші до краю рами, кут повороту чаші зростає досягаючи 116÷118 град за 1,3÷1,5с. Перекидання можна робити в обидві сторони. Виключення електродвигуна при досягненні чашею крайніх положень здійснюється командоапаратом 1, який пов'язаний з нижнім гвинтом 10 за допомогою кинематичной черв'ячної передачі 2. Розглянутий механізм має малий термін служби гвинтів і гайок у зв'язку з важкими умовами їх роботи [2].
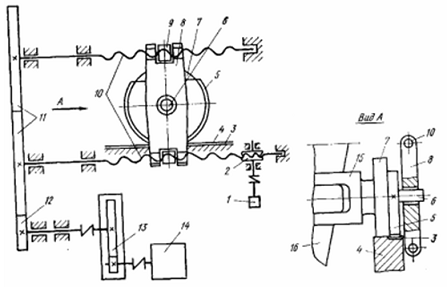
Рисунок 2.1 – Кінематична схема гвинтового механізму кантування чаші шлаковоза
2.2 Зубчастий механізм кантування чаші шлаковоза
У цьому типі конструкції шлаковоза кантування чаші відбувається через зубчасті передачі (рис. 2.2.). Від фланцевого електродвигуна 1 через самотормозящийся редуктор 2 з консольною шестернею 10 обертання передають зубчастому сектору 3, який чітко закріплений на цапфі 7 опорного кільця 4 чаші. Сектор 3 і опорне кільце разом з іншим зубчастим сектором 5, який виконаний разом з катком 6, переміщають шляхом обкатування сектором 5 і катком 6 нерухомих зубчастих і гладких сегментів 11, які встановлені на стойках лафета 13. При цьому забезпечують переміщення опорного кільця з чашею в перпендикулярному напрямі відносно осі залізничної колії і повороту чаші на кут до 118?.
Постійність міжцентрової відстані між віссю вихідного валу редуктора 2 і віссю цапф 7 опорного кільця 4 при кантуванні забезпечується водилами 12, які закріплені на цапфах 7 опорного кільця 4 і сполучені з осями 14 лафета 13 [2].
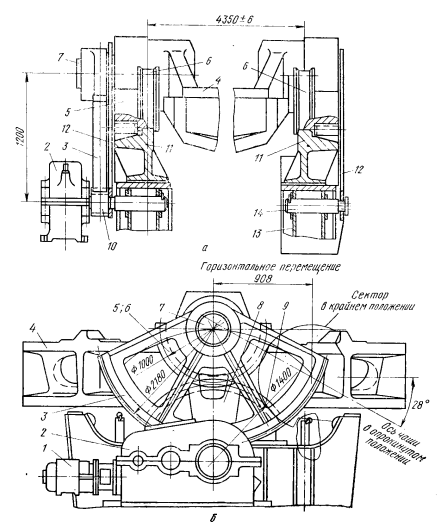
Рисунок 2.2 – Зубчастий механізм кантування чаші шлаковоза.
3. Опис запропонованої конструкції чотирьохланкового механізму кантування чаші шлаковоза
Кінематична схема чотирьохланкового механізму кантування чаші шлаковоза приведена на рисунку 3.1. Від мотор-редуктора 1 передається крутильний момент на кривошип 2, який жорстко закріплений на вихідному валу мотор-редуктора. Кривошип 2 через шатун 3 передає зусилля на важіль 4, який жорстко закріплений на цапфі чаші шлаковоза. У наслідку повороту важеля 4 відбувається кантування чаші, при цьому чаша переміщається на деяку відстань перпендикулярно залізничним коліям. При кантуванні чаші зубчасте колесо 5 і ролик 6, що жорстко закріплені на цапфі чаші, переміщаються відповідно по рейці 7 і доріжці 8, які встановлені на рамі шлаковоза. Слід зазначити, що при повному оберті кривошипа 2 відбувається повний цикл кантування чаші, а саме як кантування, так і повернення чаші в початкове положення.
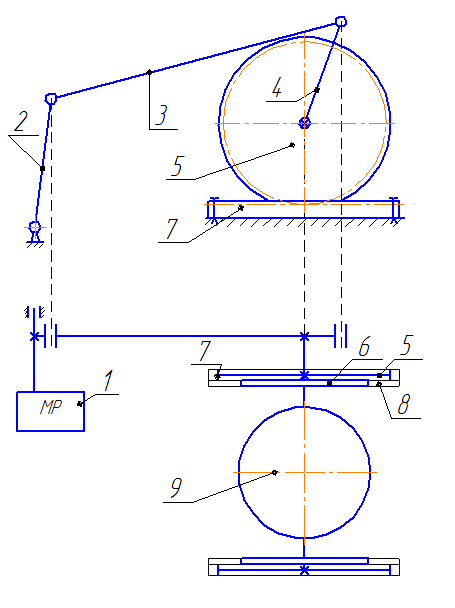
Рисунок 3.1 – Кінематична схема чотирьохланкового механізму кантування чаші шлаковоза
4 Розрахункова частина
4.1 Синтез і кінематичне дослідження чотирьохланкового механізму
Метою синтезу чотирьохланкового механізму є визначення геометричних розмірів ланок і координат центру осі обертання кривошипа. Це завдання можна вирішити графічним шляхом з використанням програми "Компас 10" (мал. 4.1). Для цього, заздалегідь знявши необхідні геометричні виміри з моделі шлаковозной візка, малюємо в "Компасі 10" спрощений вид візка. Далі задаємося, виходячи з конструктивних міркувань, довжини: кривошипа l1 , шатуна l2 і важеля l3, а також враховуємо те, що центр цапфи чаші при вертикальному розташуванні чаші φ=0° розташований на одній осі з вихідним валом редуктора, на якому жорстко закріплений кривошип. Оскільки центр осі цапфи під час кантування зазнає горизонтальне переміщення, а важіль жорстко закріплений на цапфі опорного кільця чаші, то при повороті чаші на певний кут - важіль теж буде обертатися на цей кут. Знаючи, що початковий кут повороту φ0=0°, а кінцевий φк=120°, – розбиваємо механізм повороту на чотири положення при переміщенні кута повороту чаші на 30°.
Отримані розміри: l1 =1000мм, l2 =2200мм, l3 =1370мм.
Кінематичний аналіз механізму включає визначення швидкостей і прискорень точок ланок, кутових швидкостей повороту чаші і обертання кривошипа, побудову графіків їх залежності від кута повороту чаші і планів швидкостей і прискорень.
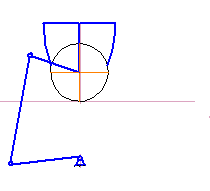
Рисунок 4.1 – Синтез важільного механізму
(анімація: об'єм 7,3 кб, кадрів 5, кількість циклів повтору 8, затримка між кадрами 1 с)
При куті повороту чаші φ1=0° положення ланок механізму показано на рис.4.2 .
Кутову швидкість повороту чаші можна визначити з формули:

де φ1 – кут повороту чаши;
t – час за який чаша обертаеться на цей кут.
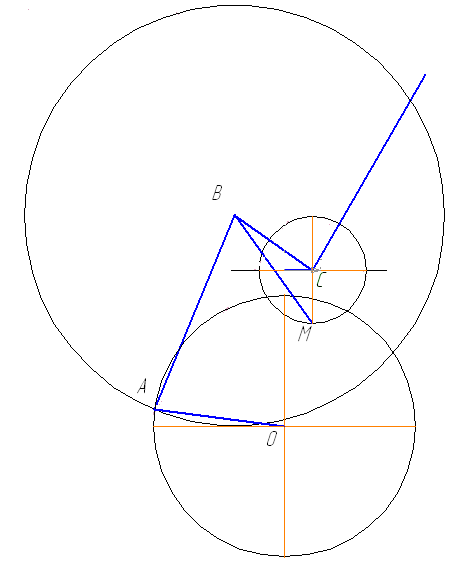
Рисунок 4.2 – Положення механізму при φ = 30°
При куті повороту чаши φ1=30° час цього поворота дорівнює:

де tк – вчас кантування чаші, задаємося tк=75с.
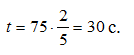
Тоді кутова швидкість при цьому куті повороту рівна [5]:
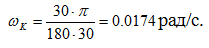
Швидкість т. В можна розкласти на переносну разом з центром осі цапфи і відносну, яка викликана обертанням відносно МСЦ. Векторна формула матиме наступний вигляд [5]:
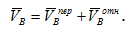
Відомо, що вектор відносної швидкості т.В буде спрямований перпендикулярно СВ, а вектор переносної швидкості - паралельно переміщенню осі цапфи. Значення цих швидкостей можна визначити по формулах:

R – радіус зубчастого колеса, R=0,62м;

l1 – довжина важеля, l1=1м,
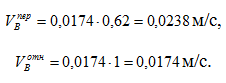
Будуємо план швидкостей для цього положення важелів (рис.4.3). Приймаємо масштабний коефіцієнт μ=2·10-3 (м/с)/мм . Вектори переносної і відносної швидкостей т.В виходитимуть з полюса Рv згідно зі своїми напрямами мають довжину [5]:
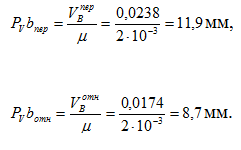
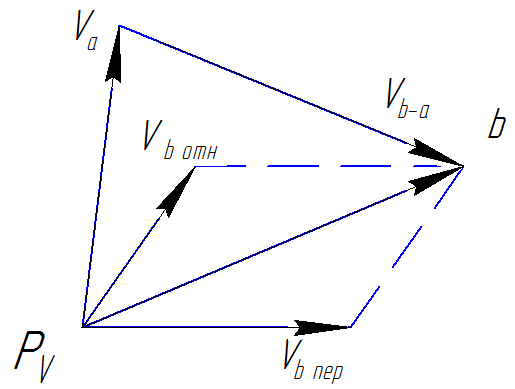
Рисунок 4.3 - План швидкостей для положення φ=30° (μ=2·10-3(м/с)/мм)
Будуємо вектор швидкості т. В склавши вектори переносної і відносної швидкостей. Вимірявши його довжину визначаємо значення швидкості т.В :

Для визначення швидкості т.А складемо інше векторне рівняння [5]:
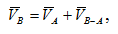
де – вектор швидкості т. А, який спрямований перпендикулярно ОА;
– вектор швидкості т.В относительно т.А, відносно т.А, який спрямований перпендикулярно ВА.
Проводимо з полюса пряму, що перпендикулярна ОА, а з кінця вектору пряму перпендикулярну ВА, і в місці їх перетину буде кінець вектору швидкості
і початок вектору швидкості
. Замірявши довжини цих векторів, можемо визначити їх значення:
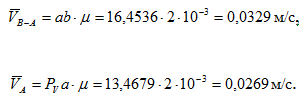
Кутову швидкість кривошипа визначимо з формули [5]:

де l3 – довжина кривошипа, l3=1,37 м.
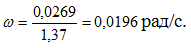
Прискорення т.А векторно можна розкласти [5] на нормальне і тангенціальне:
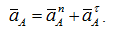
Оскільки кутова швидкість кривошипа постійна ω=const, то тангенціальне прискорення т.А:
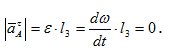
Отже:

Будуємо план прискорень для цього положення важелів (рис. 4.4). Приймаємо масштабний коефіцієнт . Вектор прискорення т. А виходитиме з полюса Pa і спрямований паралельно ОА від А до О. Його величину визначимо з формули:
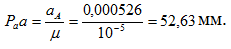
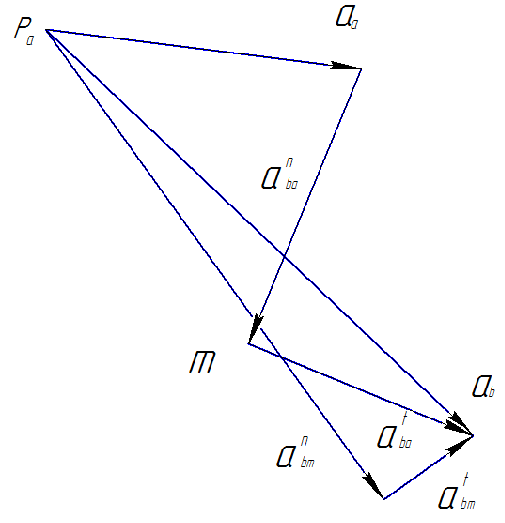
Рисунок 4.4 – План прискорень для положення φ=30° (μ=2·10-5(м/с2)/мм)
Вектор прискорення т.В, який належить шатуну, можна представити у вигляді векторної суми [5]:
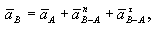
де – вектор прискорення т.В відносно т.А нормальне, яке спрямоване паралельно ВА від В до А;
– вектор прискорення т.В відносно т.А тангенціальне, яке спрямоване перпендикулярно ВА.
Нормальне прискорення т.В відносно т.А дорівнює:

Будуємо вектор нормального прискорення т.В відносно т.А на плані прискорень. Він виходить з кінця вектору і дорівнює:

Крім того, вектор прискорення т.В, який належить важелю, можна розкласти на наступну суму векторів :
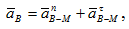
де – вектор нормального прискорення т.В відносно МСЦ, спрямований паралельно ВМ від В до М;
– вектор тангенціального прискорення т.В відносно МСЦ, спрямований перпендикулярно ВМ.
Нормальне прискорення т.В відносно МСЦ визначимо по формулі:

де lBM – відстань від т.В до МСЦ, lBM=1,40003 м.

Будуємо вектор нормального прискорення т.В відносно МСЦ на плані прискорень. Він виходить з полюса і рівний:

Проводимо з кінця вектору пряму, яка перпендикулярна ВМ. У точці їх перетину буде кінець вектору прискорення т.В. Вимірявши довжини векторів
і
, можемо вичислити їх значення:
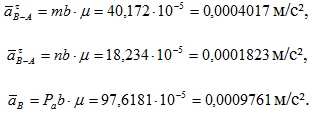
Значення кутових швидкостей, швидкостей і прискорень для інших положень механізму обчислюються аналогічно, їх величини приведені в таблиці 4.1.