Wassara - Water-Powered Drilling Systems
Wassara offers the mining and construction industry complete systems for effective drilling in soil and rock, based on our core competence in water-powered drilling. At the heart of all systems is the patented Wassara™ in-the-hole hammer, which is powered by high-pressure water instead of air. It is the use of high-pressure water that brings a number of advantages such as long straight holes, low energy consumption, and a working environment free of oil mist and dust.
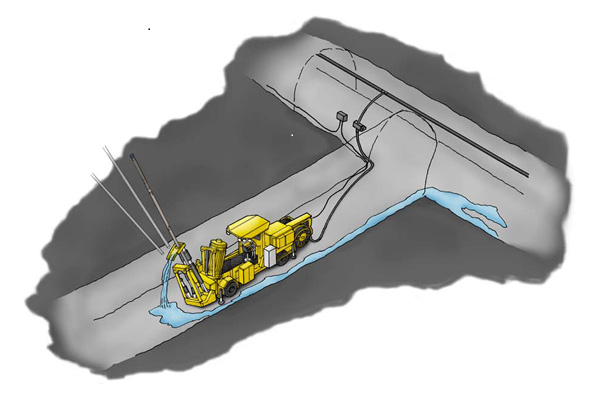
Fig. 1 - Wassara production drilling system.
Production drilling systems and slot drilling systems
For the mining industry Wassara offers two different systems: the Wassara production drilling system, which is used for drilling blast holes, and the Wassara slot drilling system, which is used for burn-cut drilling. All components in the systems have been designed to ensure optimum performance.
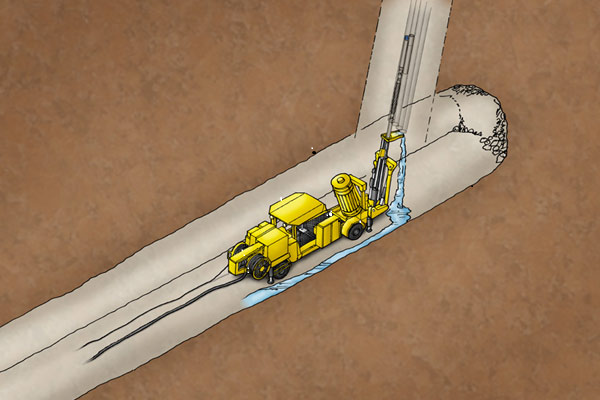
Fig. 2 - Wassara slot drilling system.
Water-powered drilling systems for sublevel caving
Wassara water-powered drilling systems have enabled Swedish mining company LKAB to scale up its sublevel caving operation in the iron ore mines in Kiruna and Malmberget by approximately a factor of two. This is due to the fact that the Wassara system drills very long, straight holes, which results in well-fragmented ore after blasting. This has made it possible to increase the distance between sublevels from 15m to 30m, resulting in large cost savings for LKAB.
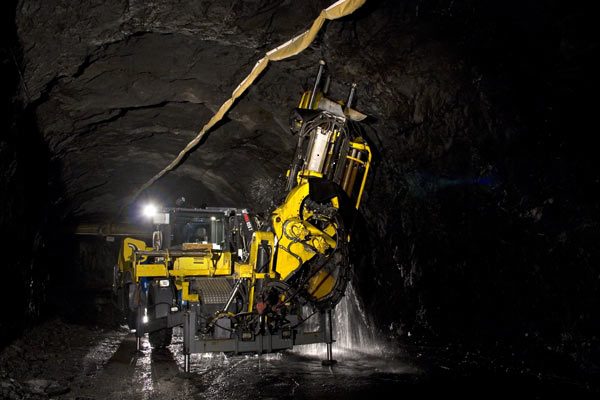
Fig. 3 - Wassara drilling in the LKAB mines.
Blast-hole drilling systems.
The Wassara production drilling system for blast-hole drilling consists of hammers, bits, check valves, drill tubes, high-pressure swivels, high-pressure hoses and electric high-pressure water pumps. It was originally developed for Swedish mining company LKAB, which was in search of a drilling method that could enable it to scale-up its mining operations. Neither air hammers nor top hammers were deemed suitable for this task. LKAB has currently drilled more than 13,000,000m with the system. More and more mines are now beginning to discover the benefits of the Wassara system.
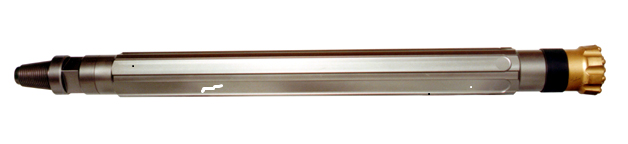
Fig. 4-The Wassara hammer with stabilised casing enables straight drilling with superior precision.
Slot drilling systems.
The Wassara slot drilling system consists of pilot hammers, bits, check valves, guided drill tubes, drill tubes, high-pressure swivels, high-pressure hoses and electric high-pressure water pumps. The first step is to drill the pilot hole, and the pilot tube is then inserted into the pilot hole. The second hole is then drilled parallel to the pilot hole thanks to the pilot tube. A new pilot hole is drilled and the process is repeated until the required slot length is achieved. Finally the blast holes are drilled. The advantage of this method is that the blast holes can be optimised regarding direction and numbers with respect to the slot. Blasting is then performed towards the slot.
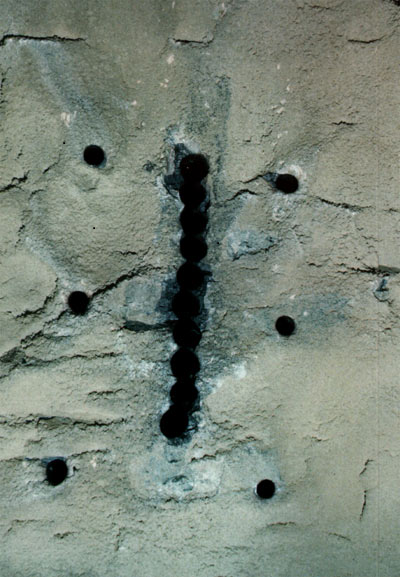
Fig. 5-Slot with blast holes prior to blasting