Abstract
Maintenance
- 1. Theme urgency
- 2. Goal and tasks of the research
- 3. Methods of managing an asynchronous electric engine
- 3.1 Rheostat control method
- 3.2 Frequency control method
- 4. Quasi frequency managing control method
- 4.1 The formation of quasi sinusoidal voltages in the phases of the load during one interval switching thyristors
- 4.2 Description of computer model of the process
- References
1. Theme urgency
The mine scraper conveyor operating conditions are characterized by a large range variation of moments of resistance. It is not uncommon locking drag chain of scraper conveyor, or start the fully loaded weight of a mountain mass. As a result, there is probability to stop working body during the working process, as well as the failed launch. Removal the high moment of resistance of the conveyor manually is a very hard process. This is a due to search for technical solutions for the automation removal the high moment of resistance of the scraper conveyor.
Thus, the scientific and practical relevance is the investigation and the justification of parameters of the quasi frequency electric drive of the scraper conveyor as a tool of automating removal the high moment of resistance.
2. Goal and tasks of the research
The goal of research is to improve the operational efficiency of the scraper conveyor by tools of the automatic removal the high moment of resistance, which made on the basis of the justification parameters and structure of quasi frequency converters.
Tasks of the research:
- To analyze the conditions exploitation mine scraper conveyor and the technical capabilities of the angular velocity control of asynchronous engine in the context of the functions of removal the high moment of resistance.
- To develop and explore mathematical and computer models of the "quasi frequency converter – asynchronous engine".
- To justify the parameters and structure of the automatic removal the high moment of resistance of the scraper conveyor.
- To develop the schematic of the automatic removal the high moment of resistance of the scraper conveyor.
3. Methods of managing an asynchronous electric engine
3.1 Rheostat control method
One of the ways to increase the starting torque is a rheostat control. This method is used for heavy starting conditions, under heavy load on the shaft. Rheostatic start is used only for asynchronous engines with phase rotor. The rotor circuit includes starting rheostat. Rheostat control start is used for increasing the starting torque.
The figure 1 shows a rheostatic starter scheme (fig. 1 a) and mechanical characteristics (fig. 1 b) of rheostat control method.
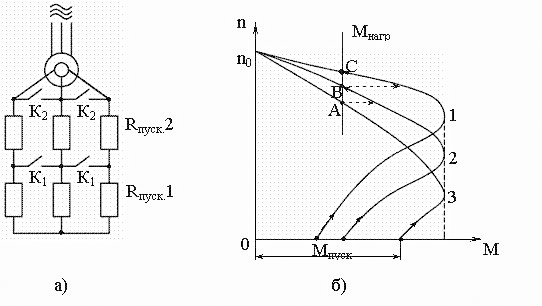
Figure 1 – Asynchoronous engine start diagram when the rheoatat control method is used
(animation: 7 frames, 5 cycles of repeating, 144 kilobytes)
(a – rheostatic starter scheme, b – mechanical characteristics)
When asynchronous engine is starting (fig. 1 a), the starting rheostat is fully included in the rotor circuit (Rïóñê3 = Rïóñê1 + Rïóñê2), so the relay contacts K1 and K2 are open. The engine will run by the characteristic 3 (fig. 1 b) under the force of starting torque Mïóñê. For a constant load on the shaft and the included rheostat Rïóñê3 acceleration ends at the point A. The engine has to to switch the contacts K1 for further acceleration, and the starting resistance will be reduced to Rïóñê2 and acceleration will continue by the characteristic 2 to the point B. When contacts K2 are swithed, starting rheostat will be completely removed (Rïóñê = 0) and the final acceleration of the engine will continue at its natural mechanical characteristic 1 and ends at point C. Rheostat control method can be used only for asynchronous with a phase rotor [1].
3.2 Frequency control method
It is also possible to control the asynchronous engine rotor speed by changing the frequency of the supply voltage (fig. 2). In the process of frequency control speed mode of the asynchronous engine it is important to stabilize the value of the critical moment of the machine.
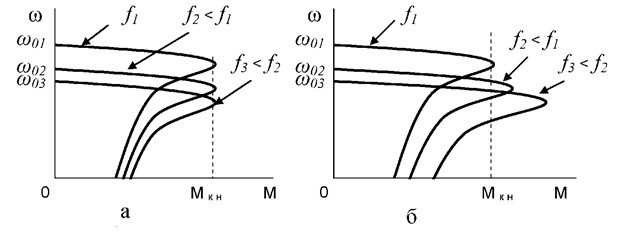
Figure 2 – Asynchoronous engine start diagram when the frequency control method is used
(a – Uô/f = const; á – Uô = const)
4. Quasi frequency managing control method
This problem can be solved with the quasi frequency engine management, which makes it possible to:
- get the low speed rotation of the rotor;
- increase the torque;
- engine reversing without extra contactor (depending to the order of switching thyristors).
Analysis of possible ways to control asynchronous engine speed modes allows the conveyor to give preference to quasi frequency method, the realization of which will makes it possible to do an automatic removal of the high moment of resistance of scraper conveyor.
4.1 The formation of quasi sinusoidal voltages in the phases of the load during one interval switching thyristors
The quasi frequency voltage forming is made by switching thyristors by turn according to a specified algorithm. And thyristor switching frequency (fñ/fm = 6n ± 1) sets the sinusoidal voltage frequency.
The reverse of the engine at low angular speed is achieved by thyristor switching order. And the process is accompanied by increased engine electromagnetic torque.
Quasi sinusoidal voltage diagram analysis (fig. 3) allows us to conclude that synchronization with equal moments of the instantaneous phase voltages during the computer simulation must be provided [2]. These points match to the lower peaks of the rectified line voltage pulsations. This situation is considered to justifying the structure of a computer model of the quasi frequency electric system.
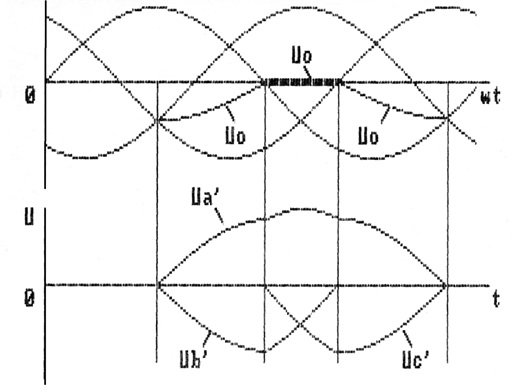
Figure 3 – Quasi sinusoidal voltages forming in the phases of the load during the one period of thyristor switching
4.2 Description of computer model of the process
To use quasi frequency control method for an automatic removal the high moment of resistance, it is necessary to research deeply the characteristics of this method to design a computer model of this process (fig. 4).
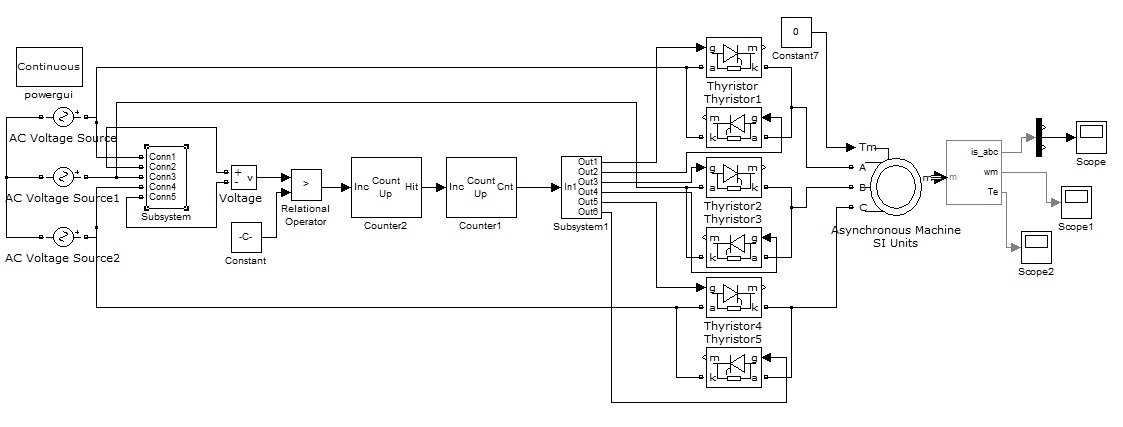
Figure 4 – Quasi frequency control method model
Diode rectifier is conected to the three-phase electrical system (subsystem, fig. 4) at the output of which we get 300 Hz frequency voltage. Relational operator is used to convert analog signal into pulses. It tracks the voltage peaks and generates single pulses of the same frequency according to them. Counter2 devides the pulses frequency to 7. Counter1 forms a ledder signal, which increases by 1 for each input pulse. The counter resets and starts to count again when it accumulates 6 pulses. Subsystem1 (fig. 5) separates impulses to thyristors according the specified control algorythm.
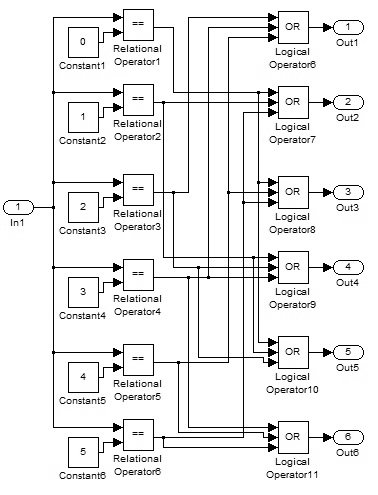
Figure 5 – Subsystem1 structure
Furthermore, the pulses enter the thyristor switch, which is composed of blocks thyristor. It forms the specified frequency voltage. The voltage signal enters to the asynchronous engine (asynchronous machine, fig. 4) from which we take the parameters of the system.
As a result, the electric parameters of the processes can be obtained through the simulation. For example, the figure 6 shows a diagram of quasi frequency currents to determine the permissible duration of treatment quasi frequency control method during the automatic removal high moment of resistance.
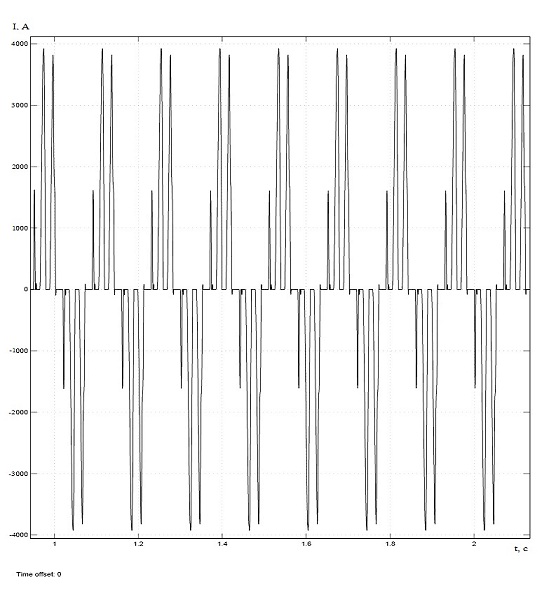
Figure 6 – Stator currents diagram
This master's work is not completed yet. Final completion: December 2012. The full text of the work and materials on the topic can be obtained from the author or his head after this date.
References
- Ýëåêòðîòåõíèêà: àñèíõðîííûé äâèãàòåëü. [Ýëåêòðîííûé ðåñóðñ]. – Ðåæèì äîñòóïà: model.exponenta.ru.
- Ìàðåíè÷ Ê.Í. Àñèíõðîííûé ýëåêòðîïðèâîä ãîðíûõ ìàøèí ñ òèðèñòîðíûìè êîììóòàòîðàìè. – Äîíåöê: ÄîíÃÒÓ, 1997. – 64 ñ.