Abstract
Содержание
- Introduction
- 1.Analysis of the research object
- 2. Goal and tasks of the research
- 3.The review of technical decisions on perfection of the electric drive of scraper conveyors
- Conclusion
- References
- 1. Скребковые конвейеры. Справочник / Под ред. А.В. Леусенко. – М.: Недра, 1992. – 221 с.
- 2. Расчёт и конструирование горных транспортных машин и комплексов / Под ред. И.Г. Штокмана. – М.:Недра, 1975. – 464 с.
Introduction
Scraper Conveyors are an integral, essential part of modern mining and manufacturing process, they establish and regulate the pace of production, provide for its rhythm, enhance productivity and increase production, and most importantly scraper conveyor is the main vehicle of mining mass abatement in the slaughter of the mine. Drawbar organ scraper conveyor is an endless chain (one, two or three) with fixed scrapers on it.
Operating conditions associated with the conveyor sticking traction body in connection with various types of jamming. Designed for the fluid coupling is not fully perform its functions through the pre-protective high inertia. Therefore, the actual problem is that more effective protection. One solution to this problem can be disabling and subsequent induction-dynamic braking of the drive. In this connection it is necessary to theoretically justify such a decision. For this purpose, a dynamic model of the object, a study which will determine the value of the length of time necessary to detect locking and spacing off and subsequent inhibition.
If you pull the chain jamming and subsequent deceleration occurred over the three characteristic states:
– drive induction motor is connected to the network up and running in the engine mode;
– elements of the drive and pull the chain moving by inertia in the off pressure to the braking mode of pressure;
– BP switched to induction-dynamic braking.
1 Analysis of the research object
Scraper conveyor is a structure shown in Figure 1.
Each has its drive from one to two drive units 3. The structure of the drive unit are connected in series are asynchronous motor with squirrel cage rotor 4, 5, and fluid coupling , reducer gear 6. As a rule, drive units scraper conveyors are equipped with a three domestic production reduction. However, in the world have experience with planetary gear units, which differ High Yield and allow external dimensions usual gear to pass twice more in the moment. The main purpose is to ensure a smooth coupling of the electric starter assembly line, the protection of the scraper chain 7 of rush when locking [1].
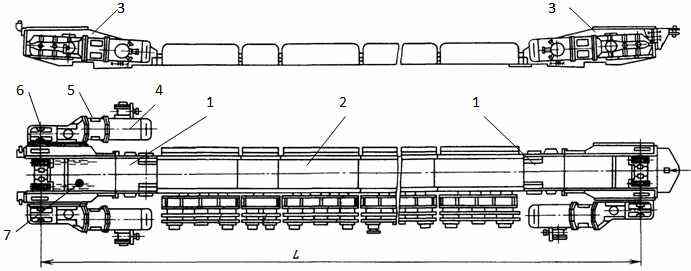
Figure 1 – The device scraper conveyor SP–202M
2 Goal and tasks of the research
The purpose of research is increase of productivity of work of the mine scraper conveyor on the basis of prevention of an impulse scraper circuits at latching on the basis of a substantiation of parameters and structure of means of high-speed protection against dynamic overloads.
For achievement of this purpose should blow are solved following problems[2]:
– the state-of-the-art review of researches and technical decisions on a problematics of maintenance of accident-free operation of mine scraper conveyors is executed;
– to develop mathematical model of research of processes in a drive of the scraper conveyor at latching with the purpose of definition of information parameter for application in means of protection;
– to prove algorithm and to develop structural and basic schemes of means of automatic protection scraper circuits from impulses at latching;
– to prove requirements on safe and accident-free operation of the developed means of automation.
3 The review of technical decisions on perfection of the electric drive of scraper conveyors
Now there are following directions on development of electric drives of underground scraper conveyors:
– use as safety device SL of the conveyor electromagnetic couplings dry friction;
– application electromagnetic coupling slidings;
– application of the automated electric drive on the basis of the engine of a direct current;
– application of the asynchronous electric drive with use thyristor a regulator of a pressure;
– application of converters of frequency;
– application starting and control device on the basis of thyristor switchboards;
– application of a drive with use of two-high-speed asynchronous electric motors.
Conclusion
Thus, process inductive-dynamic braking the induction motor allows to receive a high brake current the induction motor in the established mode under condition of effective suppression EMF of rotation, thus during suppression EMF of rotation for reception of initial splashes in a current of induction braking. Depending on corners detenting thyristor Intensity of braking the induction motor of average capacity are within the limits of (0.3-6) with. Such result does system of inductive-dynamic braking the induction motor admissible with reference to the electric drive of mountain machines.