Реферат за темою випускної роботи
Зміст
- Вступ
- 1. Актуальність теми
- 2. Мета і задачі дослідження
- 3. Аналіз об’єкту дослідження
- 4. Огляд технічних рішень по удосканалюванню електроприводу скребкових конвейерів
- Висновки
- Перелік посилань
Вступ
Скребкові конвеєри є складовою, невід’ємною частиною сучасного гірничо-технологічного процесу, вони встановлюють та регулюють темп виробництва, забезпечують його ритмічність, сприяють підвищенню продуктивності праці та збільшенню випуску продукції, а головне скребковий конвеєр є основним транспортним засобом гірничої маси у очисному вибої шахти. Тяговим органом скребкового конвейера є нескінченний ланцюг (один, два або три) з закріпленими на ньому скребками.
Умови експлуатації конвеєра пов’язані зі стопорінням тягового органу у зв’язку з різного роду заклинюваннями. Призначена для цього гідромуфта не повністю виконує свої функції пуско-захисні через високу інерційність. Тому актуальною є задача підвищення ефективності захисту. Одним з варіантів вирішення цієї задачі може бути вимкнення та наступне індукційно-динамічне гальмування приводу. У зв’язку з цим необхідно теоретично обґрунтувати таке рішення. З цією метою побудована динамічна модель об’єкта, дослідження якої дозволить з’ясувати величину тривалості часу необхідну для виявлення стопоріння та інтервали вимкнення, та наступного гальмування.
При заклинюванні тягового ланцюга та наступному гальмуванні приводу матимуть місце три характерних стани:
– привідний асинхронний двигун залишається підключеним до мережі та працює у двигунному режимі;
– елементи приводу та тягового ланцюга рухаються по інерції при вимкненому АД до увімкнення гальмуючого режиму АД;
– АД переключається у режим індукційно-динамічного гальмування.
1 Актуальність теми
Оскільки характерною особливістю експлуатації скребкового конвеєра у складі вибійного вуглевидобувного комплексу є висока ймовірність стопоріння скребкового ланцюга у результаті обрушення фрагментів породи на став, перспективним засобом здійснення захисту тягового ланцюга від пориву при заклинюванні може бути швидкодіюче вимкнення АД від мережі з наступним переводом в режим індукційно-динамічного гальмування.
Таким чином, наукову і практичну актуальність має обґрунтування параметрів і структури технічного засобу швидкодіючого захисту електропривода скребкового конвеєра від динамічних перевантажень.
2 Мета і задачі дослідження
Метою дослідження є підвищення продуктивності роботи шахтного скребкового конвеєра на основі запобігання поривам скребкового ланцюга при стопорінні на основі обґрунтування параметрів і структури технічних засобів швидкодіючого захисту від динамічних перевантажень.
Для досягнення цієї мети мають дути вирішені наступні задачі:
- Виконаний аналітичний огляд досліджень і технічних рішень із проблематики забезпечення безаварійної експлуатації шахтних скребкових конвеєрів.
- Розробити математичну модель дослідження процесів в приводі скребкового конвеєра при стопорінні з метою визначення інформаційного параметру для застосування в засобі захисту.
- Обґрунтувати алгоритм та розробити структурну та принципову схеми засобу автоматичного захисту скребкового ланцюга від поривів при стопорінні.
- Обґрунтувати вимоги щодо безпечної і безаварійної експлуатації розробленого засобу автоматизації.
3 Аналіз об’єкту дослідження
Скребковий конвеєр являє собою конструкцію яка представлена на рисунку 1.
Кожен його привод містить від одного до двох приводних блоків 3. До складу приводного блоку входять з’єднані послідовно асинхронний двигун з короткозамкненим ротором 4, гідромуфта 5 і редуктор 6. Як правило, приводні блоки скребкових конвеєрів вітчизняного виробництва оснащені триступеневими редукторами. Однак, у світовій практиці є досвід використання планетарних редукторів, які відрізняються підвищеним ресурсом і дозволяють у габариті звичайного редуктора передавати удвічі більший момент. Основним призначенням гідромуфти є забезпечення повільності пуску електропривода конвеєра, захист скребкового ланцюга 7 від пориву при стопорінні [1].
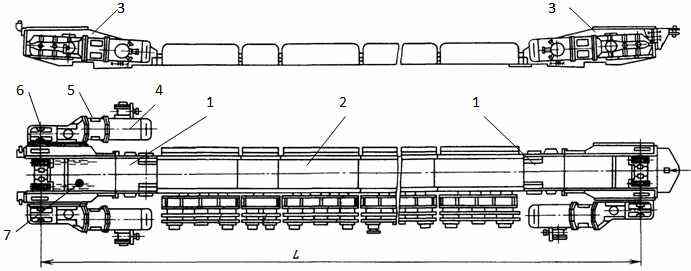
Рисунок 1 – Улаштування скребкового конвеєра СП–202М
4 Огляд технічних рішень по удосканалюванню електроприводу скребкових конвеєрів
В даний час існують наступні напрямки по розробці електроприводів підземних скребкових конвеєрів:
– використання в якості запобіжного пристрою СЛ конвеєра електромагнітних муфт сухого тертя;
– застосування електромагнітних муфт ковзання;
– застосування автоматизованого електроприводу на основі двигуна постійного струму;
– застосування асинхронного електроприводу з використанням тиристорного регулятора напруги;
– застосування перетворювачів частоти;
– застосування пускорегулюючих пристроїв на основі тиристорних комутаторів;
–застосування приводу з використанням двошвидкісних асинхронних електродвигунів.
Застосування електромагнітних муфт сухого тертя [2] поліпшує динаміку пуску конвеєра, тому що його двигун у цьому випадку може включатися вхолосту, а потім, за допомогою електромагніта, плавно збільшує стискуюче зусилля в СЛ. Однак практика експлуатації показала, що після кількох спрацьовувань сталеві диски муфт притираються один до одного, зменшуються шорсткості їхніх поверхонь, у результаті чого муфта змінює свою механічну характеристику.
Інститутами Гіпровуглемаш і Автоматгормаш [3] був розроблений привод П110Е, що містить планетарний редуктор і електромагнітну муфту ковзання (ЕМК). Основу останньої складає індуктор, розташований у зазорі магнитопроводу з обмоткою збудження (ОЗ). Величина обертаючого моменту АД, переданого через планетарний механізм на СЛ конвеєра, залежить від величини ковзання індуктора і регулюється струмом обмотки збудження.
Основний недолік приводу з ЕМК – висока складність і вартість виготовлення, малий ККД системи, інерційність захисту СЛ від поривів при заклинюванні, оскільки команда на захист СЛ відпрацьовується електромеханічною системою. Застосування приводу з ЕМК зв’язано з великими витратами як у виготовлювача, так і в споживача.
Принцип дії тиристорних асинхронних електроприводів на основі трифазних тиристорних регуляторів напруги (ТРН) полягає в зміні величини напруги, яка подається на АД гірничої машини при його пуску. Захист від поривів тягового органу при стопоріннях у них забезпечується індукційно-динамічним гальмуванням АД. Однак, керування пуском СК, що припускає зміну в процесі пуску електромагнітного моменту його АД за заданим закону не дозволяє одержати стійкий ступінь зниженої швидкості СЛ, визначає залежність інтенсивності розгону приводу від величини моменту опору руху.
Найбільш широкими регулювальними можливостями АД володіють перетворювачі частоти (ПЧ) [4]. Вони керують безпосередньо частотою обертання ротора, зміною частоти напруги на статорі. Ці позитивні якості реалізуються без використання зворотного зв’язку по швидкості приводу.
Однак, ПЧ конструктивно складні, містять велику кількість силових напівпровідникових приладів (СНП). Це визначає їхню високу вартість, значні масогабаритні параметри, утруднює рудникове вибухозахищене виконання їхніх оболонок, ефективне охолодження СНП. З цих причин ПЧ важко використовувати у вугільних шахтах.
Силові тиристорні комутатори (СТК) струму разом з імпульсним і фазовим регулюванням величини трифазної напруги дозволяють формувати квазисинусоїдні напруги знижених частот, а значить – змінювати частоту обертання асинхронного двигуна, що підключається. У схемі тиристорного пускорегулюючого пристрою для асинхронного електроприводу гірничих машин [5] був прийнятий реверсивний силовий тиристорний комутатор, що складається з п’яти пар паралельно включених тиристорів. Такий комутатор дозволяє реалізувати плавний пуск електродвигуна гірничої машини за допомогою комбінованого квазичастотно-фазового керування. Запропонована схема керування комутатором забезпечила підвищення енергетичних показників приводу, розширення діапазону регулювання при квазичастотному керуванні. Однак у ній не повною мірою враховані особливості роботи електроприводу підземного скребкового конвеєра: не передбачені засоби захисту його тягового ланцюга від динамічних перевантажень.
Експлуатація скребкового конвеєра відрізняється наявністю значних моментів опору, що змінюються в широкому діапазоні і є суттєво збільшеними на початку руху скребкового ланцюга. Коефіцієнт тертя, який обумовлює величину моменту опору тягового органу (kт.) залежить від конструкції конвеєра, виду вантажу, що транспортується, його вологості та крупності і функцією швидкості руху (v) скребкового ланцюга: kт = 0,62-0,2v2 + 0,07v3 .
Одноприводний скребковий конвеєр можна представити як систему з двома зосередженими масами: маса m1 – приведена маса тягового органу і приєднаного до нього вантажу; m2 – приведена маса ротора двигуна і елементів передачі (рис. 2) [2] .
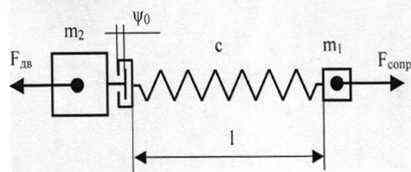
Рисунок 2 – Розрахункова схема процесу пуску скребкового конвеєра
Пуск скребкового конвеєра можна умовно розділити на три етапи. На першому етапі відбувається прискорений рух ротора двигуна та елементів трансмісії за рахунок зазорів у передачі. Кутова швидкість ротора двигуна наприкінці цього етапу (за умови рівноприскореного руху) описується рівнянням:
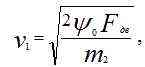
де Ψ0 – сумарний приведений зазор у системі, що складається із зазорів у зубчастих передачах, шліцьових та шпонкових з’єднаннях, зазору між зубцями приводної зірочки та тяговим органом;
На другому етапі відбувається рух ротора двигуна за наявності пружної деформації трансмісії і тягового органа до моменту, коли пускове зусилля зрівняється із зусиллям статичних опорів. Збільшення кутової швидкості ротора визначається рівнянням:
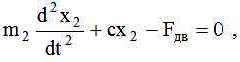
що інтегрується при початкових умовах:
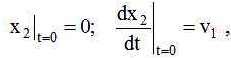
де х2 – переміщення маси m2; с – приведена жорсткість трансмісії і тягового органу.
Третій етап пуску є завершальним. На цьому етапі рух тягового органу описується системою рівнянь:
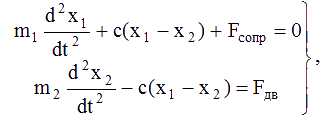
де х1 – переміщення маси m1; Fсопр – зусилля опору переміщення тягового органа.
Інтенсивність розгону тягового органу конвеєра при пуску обумовлена параметрами приводів, величинами опорів руху, що нелінійно зменшуються зі збільшенням швидкості руху скребкового ланцюга і характеризується значними прискореннями рухомих елементів приводу. Функціональним елементом приводу конвеєра, спеціально призначеним для уповільнення розгону, є гідромуфта . Її оребрене насосне та турбінне колеса встановлюються, відповідно, на вал асинхронного двигуна і вхідний вал редуктора. Проміжок між колесами в корпусі муфти заповнений рідиною. Отже, насосне колесо, обертаючись зі швидкістю вала двигуна призводить до кутового руху рідини, яка, у свою чергу діє на турбінне колесо, передаючи на нього обертовий момент двигуна. Встановлені особливості впливу гідромуфти на динаміку пуску електроприводу скребкового конвеєра пояснюються її механічною характеристикою [6].

де а1, а2, а3 – постійні для окремих зон сімейства механічних характеристик; Мm – момент на валу турбінного колеса гідромуфти; vн, vm – кутові швидкості насосного та турбінного коліс.
Близький до номінального момент на валу турбінного колеса гідромуфти в процесі пуску може бути отриманий при кутовій швидкості насосного колеса, близькій до номінальної. Отже, на початку пуску двигун конвеєра розганяється майже без навантаження, а наприкінці розгону ротора рух ривком передається до скребкового ланцюга, що є фактором підвищення динамічних навантажень в трансмісії конвеєра.
Різке гальмування, викликане раптовим стопорінням тягового органу, є найбільш небезпечним режимом роботи конвеєра, оскільки його рухомі елементи, окрім статичних сил, що розвиваються двигуном за рахунок електромагнітного моменту, знаходяться під впливом динамічних сил, викликаних уповільненням рухомих мас.
Розглянуті вище технічні рішення можуть бути застосовані в автоматизированному електроприводі шахтних конвеєрів. Однак, необхідність здійснення зворотнього зв’язку за швидкістю (використання датчика швидкості) не дозволяє ефективно застосовувати ці схеми у приводах скребкових конвеєрів. З іншого боку, привід перспективного скребкового конвеєра повинен бути позбавлений гідромуфт, а їхні функції повинні бути переданими іншим, більш ефективним технічним засобам. Одним з варіантів вирішення цієї задачі може бути вимкнення та послідуюче індукційно-динамічне гальмування приводу. З цією метою побудована динамічна модель об’єкта та нам необхідно з’ясувати яка тривалість часу необхідна для виявлення стопоріння та інтервали вимкнення, та послідуюче гальмування (рис. 3) [7].
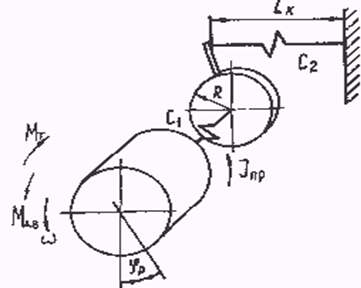
Рисунок 3 – Динамічна модель скребкового конвеєра при заклинюванні тягового ланцюга;
Ефективність процесу динамічного гальмування асинхронного двигуна значною мірою визначається величиною постійного (випрямленого) струму у фазах його статора. З іншого боку, величина цього струму обумовлюється напругою, що підведена до статора величиною ЕРС обертання, що індуктується в обмотках статора обертовим полем струмів ротора. В разі, якщо ЕРС обертання за своєю полярністю співпадатиме з полярністю підведеної напруги, її дія буде спрямована на зменшення величини струму гальмування. Це визначатиметься різністю потенціалів миттєвих значень підведеної напруги і ЕРС обертання і призводитиме до зменшення інтенсивності гальмування двигуна. Таким чином, ефективне динамічне гальмування асинхронного двигуна може відбуватися за умови відсутності у його статорних обмотках зворотної ЕРС обертання.
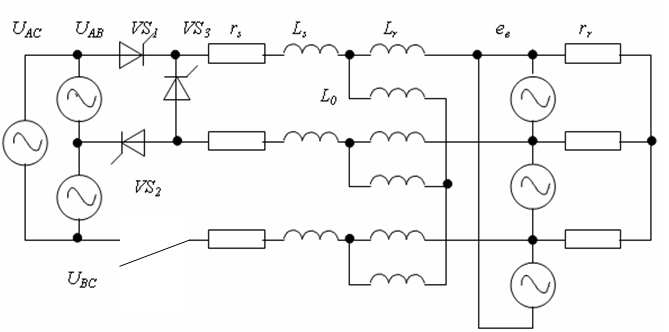
Рисунок 4 – Розрахункова схема щодо аналізу дослідження процесу індукційно-динамічного гальмування асинхронного двигуна;
Ефективність способу індукційно-динамічного гальмування асинхронного двигуна полягає в усуненні зазначеної ЕРС обертання (на початку гальмового процесу), яке супроводжується створенням значних за амплітудою імпульсів гальмового струму. У гірничій промисловості режим індукційно-динамічного гальмування використовується для повільної зупинки електроприводів бремсбергових стрічкових конвеєрів, екстреної зупинки електроприводів деяких інших гірничих машин.
Процес індукційно-динамічного гальмування створюється силовою тиристорною схемою в ланцюзі статора асинхронного двигуна відповідно до рис. 4 і передбачає чергування станів динамічного (ДГ), індукційного (ІГ) та, власне, індукційно-динамічного (ІДГ) гальмування двигуна [8].
Струм динамічного гальмування створюється за допомогою подачі на статор через тиристори VS1 і VS2 півхвиль лінійної напруги UАВ мережі. Ефект індукційного гальмування створюється при замиканні через тиристор VS3 ЕРС обертання (еоб) ротора АД:

де p – число пар полюсів асинхронного двигуна; Is; ir – струми статора і ротора; L0 – індуктивність головного магнітного поля в розрахунку на фазу асинхронного двигуна.
Процес індукційно-динамічного гальмування ілюструється діаграмами відповідних параметрів асинхронного двигуна і живлячої мережі (рис. 5). На інтервалах динамічного гальмування полярності uАВ і eоб збігаються. При цьому uАВ > eоб. Початок ДГ визначається кутом відпирання α тиристорів VS1 і VS, а закінчення – кутом їхньої провідності β. Гальмовий струм i визначається відмінністю між миттєвими значеннями uАВ і eоб.

де rн; Lн – загальні активний опір та індуктивність ланцюга протікання гальмового струму.
На інтервалі ІТ тиристор VS3 знаходиться у провідному стані, у той час, як, тиристори VS1 і VS – у не провідному. Величина гальмового струму iГ визначається миттєвими значеннями ЕРС обертання двигуна (eоб).

На кожному з інтервалів ДГ та ІГ величина ЕРС обертання визначається відповідними її амплітудою (Еоб mi ) та початковою фазою ( γ):
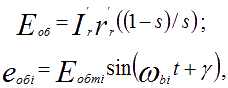
де ωbi – кутова частота ЕРС обертання, що відповідає i-му інтервалу гальмування, зменшується, остаточно, до нуля.
У міру зменшення кутової швидкості асинхронного двигуна зменшуються амплітуда та частота його ЕРС обертання, і настає стан, коли полярності uAB і eоб будуть відмінними одна від одної. В цьому разі тиристори VS1; VS2; VS3 перебуватимуть у відкритому стані, а гальмовий струм двигуна iГ визначатиметься сумою абсолютних виличин миттєвих значень uАВ і eоб (інтервал ІДТ):

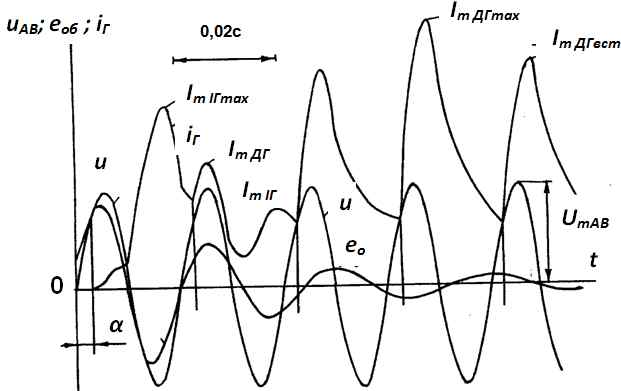
Рисунок 5 – Діаграми формування струму статора асинхронного двигуна в процесі його індукційно-динамічного гальмування;
Вирази вирішуються поетапно у порядку появи інтерваалів з характерними, розглянутими вище станами гальування. При цьому враховуються відповідні початкови умови, величина і частота ЕРС обертання асинхронного двигуна. Їхнім рішенням є наступний вираз:
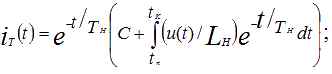
де tп; tк – моменти початку та закінчення відповідного гальмового інтервалу, С = u(tн)/zн ; ТН – постійна часу обмоток ротора двигуна (Тн = Lн/rн).
У скребкового конвеєра типа СП–202М, оснащеного двома АД потужністю по 45кВт та двома тяговими ланцюгами з розривним зусиллям 373 кН, показує, що обмеження розтягуючого зусилля в тяговому ланцюзі при стопорінні на допустимому рівні може бути досягнено при больше 76 ел. град, (рис.6)[8]. Стосовно до приводу скребкового конвеєра, оснащенному двома АД потужністю по 55 кВт та двома тяговими ланцюгами з розривним зусиллям 470 кН, величина кутів управління тиристорами регулятору при індукційно-динамічному гальмуванні, повинна не перевищувати 72 ел. град.
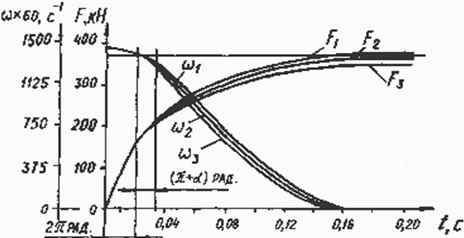
Рисунок 6 – Параметри процесу стопоріння тягового ланцюга при ввімкненні індукційно-динамічного гальмування;
При відсутності струму через VS1 і VS2 струм у тиристорі VS3 визначається величиною ЕРС самоіндукції асинхронного двигуна

де tni – момент початку зазначеного вище і-го стану;
Гальмовий струм істотно залежить від величини кутів α відпирання тиристорів VS1; VS2. Його величина визначає рівень гальмового моменту (МГ), що впливає на інтенсивність гальмування двигуна:
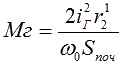
де ω0 і Sпоч – відповідно, синхронна частота обертання ротора асинхронного двигуна та його ковзання на початку ІДГ.
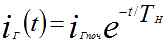
де iГ поч – початкова величина гальмового струму відповідного інтервалу.
По закінченні гасіння зворотної ЕРС обератння асинхронного двигуна його гальмовий струм буде визначатися тільки провідним станом тиристорів VS1; VS2 з урахуванням кута α їх фазового регулювання.
Технічна реалізація розглянутого принципу застосована в апараті управління гальмуванням електропривода гірничої машини АТЭМ (рис. 7) [9]. В апараті передбачені фіксовані уставки терміну гальмування електропривода скребкового конвеєра: 0,15 с; 0,5 с; 0,8с; електропривода стрічкового конвейера: 16 с; 32 с.; 64 с. В процесі роботи команда на гальмування асинхронного двигуна електропривода формується при відключенні основного контактора КМ1. У цьому випадку схема апарата реалізує наступний алгоритм:
– ввімкнення контактора КМ2 ланцюга гальмування;
– визначення відсутності струму в силовому ланцюзі контактора КМ1 (задіяні датчики струму ТА1 і ТА2, блок реле БР1);
– формування затримки часу на початок гальмування і подальше відпирання тиристорів VS1; VS2 із заданими величинами фазових кутів α відпирання.
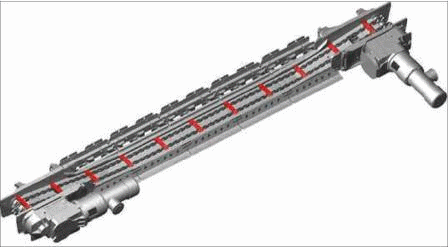
Рисунок
6 – Процес роботи скребкового
конвеєру
(анімація:4 кадра, 6 ціклів повторення,111 кБ)
Затримка часу на початок процесу індукційно-динамічного гальмування необхідна для виключення умов створення короткого замикання в разі ввімкнення тиристора VS2 при наявності струму в мережі контактора КМ1. Функція створення фазових кутів α відпирання тиристорів виконується спільною роботою блока синхронізації (БС) схеми фазового управління з фазними напругами мережі та блоків управління БУ1 і БУ2. Формування імпульсів, що безпосередньо надходять на ланцюги управління тиристорів виконується блоками формування імпульсів (БФІ1 та БФІ2). Ці ж блоки реалізують функцію гальванічної розв’язки силових ланцюгів
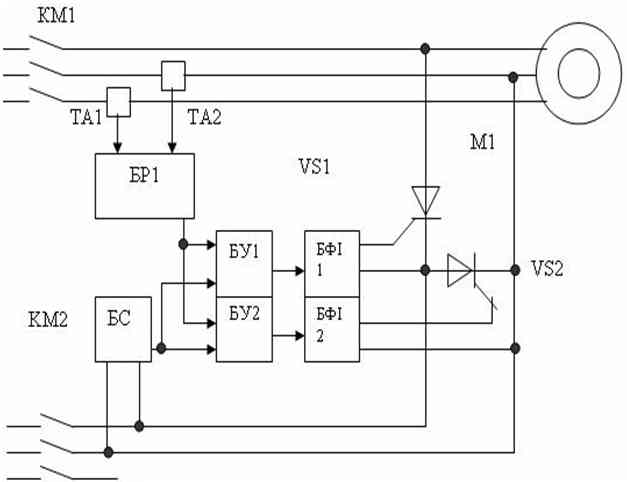
Рисунок 7 – Структурна схема апарата АТЭМ електроживлення приводного двигуна і ланцюгів блоків управління.
Висновки
Таким чином, процес індукційно-динамічного гальмування АД дозволяє отримати високий гальмівний струм АД в установленому режимі за умови ефективного подавлення ЕРС обертання, при цьому у процесі подавлення ЕРС обертання для отримання початкових сплесків струму індукційного гальмування. У залежності від кутів відпирання тиристорів Інтенсивність гальмування АД середньої потужності знаходяться у межах (0,3–6) с. Такий результат робить систему індукційно-динамічного гальмування АД допустимою для умов роботи електроприводу гірничих машин.
Перелік посилань
- Скребковые конвейеры. Справочник / Под ред. А.В. Леусенко. – М.: Недра, 1992. – 221 с.
- Расчёт и конструирование горных транспортных машин и комплексов / Под ред. И.Г. Штокмана. – М.:Недра, 1975. – 464 с.
- А.с. 572022 СССР, МКИ2В65GG23/26. Привод скребкового конвейера / И.В. Рикман, Б.Я. Маластовский, В.Н. Хорин и др (СССР). – №2101854/03; Заявлено 13.02.75; Опубл. 25.05.78, Бюл. №19. – 2 с.: 1 ил.
- Справочник по преобразовательной технике / Под ред. И.М.Чиженко. – Киев: Техника, 1978. – 447 с.
- Шавелкин А.А. Тиристорное пускорегулирующее устройство для асинхронного электропривода горных машин / Автореф. дис. канд.техн.наук. – Одесса, ОПИ, 1988. – 16 с.
- Чугреев Л.И. Динамика конвейеров с цепным тяговым органом. – М.: Недра, 1976. – 256 с.
- Маренич К.Н. Асинхронный электропивод горнах машин с тиристорними комутаторами. – Донецк, ДонГТУ, том / Дис.канд. техн. наук: 05.09.03 – Донецк., ДПИ, 1991. – 238 с.: Библиогр.: с. 171 – 183.
- Справочник по преобразовательной технике / Под ред. И.М.Чиженко. – Киев: Техника, 1978. – 447 с.
- Номенклатурный
справочник продукции АО
Первомайский электромеханический завод имени Карла Маркса
. – Донецк, 2003.