Реферат по теме выпускной работы
Содержание
Введение
Актуальность проблемы переработки медного лома в условиях ограниченности сырьевых рынков для промышленно развитых стран в последние годы становится все острее. Так, опережающие темпы роста машиностроительного комплекса и привлекательность экспорта металлопроката на фоне ограниченной сырьевой базы рудного сырья, медленного освоения разведанных месторождений и практически остановленной геологоразведки новых месторождений создает все возрастающий дефицит медного сырья для металлургических и литейных предприятий.
С другой стороны, все интенсивнее идет процесс массового выбытия основных фондов (устаревшие станки, металлоконструкции и пр.), ввиду их высокой изношенности. Поэтому в настоящее время очень высок интерес металлургических и литейных производств к поиску сырья на вторичных рынках, а возрастающая стоимость энергоносителей заставляет искать более эффективные способы их переработки в товарную продукцию.
Содержание работы
Металлургические процессы производства меди на заводах вторичной цветной металлургии, как правило, включают пиро- и гидрометаллургический переделы, конвертирования, огневое рафинирование и разливку. Пирометаллургический передел лома и отходов ведут в агрегатах различной конструкции: в шахтных, отражательных, электродуговых печах, в конвертерах.
Для плавки лома и отходов сплавов меди используют, как правило, стационарные, поворотные и вращающиеся отражательные печи.
Для рафинирования медных сплавов используют обработку расплава с помощью различных дутьевых и горелочных устройств или вводят рафинирующие флюсы. Основу примесей, содержащихся в медном ломе, составляют свинец, олово, цинк, железо, никель, мышьяк, сурьма и сера. Небольшое количество висмута, теллура, хрома и серебра также может изредка встречаются в расплаве.
Олово, как постоянный спутник вторичной меди при окислении кроме оксида олова (SnO) образует диоксид олова (SnO2), который частично растворяется в меди и не образует силикатов. В этом случае в шлак (рафинирующий флюс) переходят станнаты основных металлов (обычно кальция). Применяют также способ рафинирования вторичной оловосо¬держащей меди продувкой расплава смесью метан-кислород через верхнюю сводовую фурму. Показатели процесса приведены в табл. 1 в сравнении с применяемыми в промышленности технологиями рафинирования в барабанной и стационарной отражательной печи и по способу "Контимельт". Аналогичные результаты получены для удаления из меди висмута и мышьяка.
Отражательная печь | Способ «Контимельт» | Барабанная печь | Продувка сверху |
---|---|---|---|
0,216/0,095 | 0,32/0,12 | 0,05/0,003 | 0,155/0,0015 |
0,012/0,005 | 0,127/0,017 | ---- | 0,16/0,0054 |
0,204/0,158 | 0,277/0,169 | 0,005/0,0045 | 0,0115/0,0027 |
На заводе в г. Лимож (Франция) чёрновую медь (98% меди) и ме-таллический лом (92% меди) перерабатывают в отражательной печи, с использованием газокислородного дутья. После стандартного цикла: окисления, съёма шлака и восстановления получают аноды, содержащие, г/т: 600 серебра, 1100 мышьяка, 2200 свинца, 500 никеля, 400 олова, 250 сурьмы, 100 селена, 100 железа, 20 висмута, 100 цинка, 10 серы. Отмечается, что при вдувании газокислородной смеси в расплав окисление и ошлакование олова, железа и цинка через 15-20мин достигает 90?98%. Примеси никеля, мышьяка, сурьмы и свинца окисляются менее эффективно. Используя содовый флюс, удалось окислить 80% мышьяка и сурьмы, а также около 90% свинца (до 0,05 и 0,07%, соответственно) лишь при перегреве расплава до 1127°С . Расход природного газа в процессе составил 30-50нм3/т вторичной меди.
Скорость окисления снижается в ряду Fe-Zn-Sn, то есть при достижении концентрации примеси, определяемой коэффициентом вза¬имного влияния, начинается окисление следующего в ряду металла.
Большое внимание на практике уделяется подбору оптимального состава флюсов. Для удаления олова, свинца и сурьмы необходимо обрабатывать расплав при температуре 1117-1147°С воздухом и флюсом при соотношении CaO : Na2O = (1,5-2,5) :1. В результате за 10мин обработки содержание олова снижается с 800 до 9г/т.
Наиболее рациональный технологический вариант - переработка в отражательных печах качественного лома с получением товарных медных сплавов. Однако этот вид плавки имеет и определенные недостатки. Он имеет низкую производительность, цикличность процесса и высокий расход качественного топлива (мазут, газ, угольная пыль), а также требует больших трудозатрат.
Одним из наиболее распространённых процессов переработки низкокачественного вторичного медьсодержащего сырья является шахтная восстановительная плавка. Большую часть вторичной меди выплавляют в шахтных печах. Преимущества шахтной плавки в металлургии меди объясняется некоторыми преимуществами таких печей по сравнению с отражательными и электрическими. К числу основных преимуществ шахтных печей следует отнести их высокую удельную производительность, высокий коэффициент использования тепла, высокую десульфурацию и незначительный расход огнеупоров в связи с применением кессонированных стенок.
К основным недостаткам шахтной плавки необходимо отнести расход дорогого и дефицитного топлива (кокса) и необходимость подавать на плавку в основном крупнокусковой материал, из-за чего необходимо окусковывать сыпучие материалы перед их загрузкой в шахтную печь.
Выплавка чёрной меди из лома и отходов в шахтных печах – процесс непрерывный. В верхнюю часть шахты печи подается и слоями загружается шихта и кокс, а снизу из горна почти непрерывно (за исключением периода выпуска металла и небольшого следующего за этим периодом наполнения горна) выпускается шлак и периодически через 60 - 90 минут – расплавленный металл. В связи с этим столб шихты по мере выпуска металла и шлака опускается вниз, освобождая место новым порциям шихты. Таким образом, шихта непрерывно движется по шахте печи сверху вниз, последовательно проходя через все зоны печи.
Медь, выплавленная из лома и отходов в отражательных или шахтных печах, содержит, как уже указывалось, значительное количество примесей, основными из которых являются цинк, олово, свинец, никель, сурьма и железо. Все эти примеси необходимо отделить от меди.
Первой операцией по отделению основной массы этих примесей является конвертирование чёрной меди, заключающееся в продувке через слой расплавленной чёрной меди воздуха. Операция эта осуществляется в аппарате, носящем название конвертер, откуда и сам процесс получил название конвертирование. Целью конвертирования является максимальное удаление цинка, олова, свинца и частично сурьмы в газовую фазу и перевод никеля, железа и части сурьмы в шлак с тем, чтобы в меди, остающейся в конвертере после продувки, содержалось этих примесей как можно меньше.
Однако практически отделить медь от примесей в конвертере удается лишь частично, так как:
- цинк, свинец, олово, сурьма и никель неизбежно остаются в небольших количествах в конвертерной меди;
- часть меди переходит в шлак вместе с частью никеля, сурьмы, цинка, свинца и олова, из которого приходится эти металлы извлекать повторно.
В результате конвертирования чёрной меди образуются три основных продукта:
- конвертерная (черновая) медь, в которой концентрируются полностью благородные металлы, если они содержались в исходном сырье, загружаемом в конвертер;
- конвертерные шлаки, в которые переходит почти всё железо, значительная часть никеля, небольшая часть меди, а также часть свинца, олова, цинка, сурьмы и других примесей;
- пыль, уловленная из отходящих газов конвертера, содержащая основную часть цинка, часть олова, свинца и сурьмы и немного меди.
Для непосредственного технического применения черновая медь не пригодна, и поэтому ее обязательно подвергают рафинированию с целью очистки от вредных примесей и попутного извлечения благородных металлов, селена и теллура.
Цель огневого рафинирования на предварительной (перед электрохимической) стадии производства сводится к частичной очистке меди от примесей, обладающих повышенным сродством к кислороду, и подготовке ее к последующему электролитическому рафинированию. Методом огневого рафинирования из расплавленной меди стремятся максимально удалить серу, кислород, железо, никель, цинк, свинец, мышьяк, сурьму и растворенные газы.
Небольшие включения (несколько частиц на миллион частиц меди) таких элементов как селен, теллур и висмут могут значительно ухудшить электропроводность и обрабатываемость меди свойства, которые особенно важны для промышленности, производящей кабельнопроводниковую продукцию, являющейся крупнейшим потребителем рафинированной меди. Электролитическое рафинирование считается основным процессом, который позволяет получить медь, отвечающую наиболее жестким требованиям электротехники.
Сущность электролитического рафинирования меди заключается в том, что литые анод (отлитый, как правило, из меди огневого рафинирования) и катоды - тонкие матрицы из электролитной меди - по переменно завешивают в электролитную ванну, заполненную электролитом, и через эту систему пропускают постоянный ток. В процессе электролитического рафинирования решаются две основные задачи: глубокая очистка меди от примесей и попутное извлечение сопутствующих ценных компонентов. В результате электролитического рафинирования предполагается получить медь высокой чистоты (99,90…99,99% Cu). В целом анодная медь является многокомпонентным сплавом и обычно имеет химический состав, приведенный в табл. 2
Cu | S | Fe | Ni | Pb | As | Bi | Se+Te | Au | Ag |
---|---|---|---|---|---|---|---|---|---|
99.5- | до | до | до | до | до | до | до | до | до |
99,8 | 0,015 | 0,015 | 0,5 | 0,05 | 0,2 | 0,01 | 0,06 | 0,03 | 0,5 |
Для осуществления электролитического рафинирования меди аноды, отлитые после огневого рафинирования, помещают в электролизные ванны, заполненные сернокислым электролитом. Между анодами в ваннах располагаются тонкие медные листы - катодные основы.
Электролит представляет собой водный раствор сульфата меди (160…200 г/л) и серной кислоты (135…200 г/л) с примесями и коллоидными добавками, расход которых составляет 50…60 г/т Cu. Чаще всех в качестве коллоидных добавок используют столярный клей и тиомочевину. Они вводятся для улучшения качества (структуры) катодных осадков. Рабочая температура электролита 50…55 0С.
При включении ванн в сеть постоянного тока происходит электрохимическое растворение меди на аноде, перенос катионов через электролит и осаждение ее на катоде. Примеси меди при этом в основном распределяются между шламом (твердым осадком на дне ванн) и электролитом.
В результате электролитического рафинирования получают: катодную медь; шлам, содержащий благородные металлы; селен; теллур и загрязненный электролит, часть которого иногда используют для получения медного и никелевого купоросов. Кроме того, вследствие неполного электрохимического растворения анодов получают анодные остатки (анодный скрап). Следует отметить, что чем выше в исходной меди содержание благородных металлов, тем ниже будет себестоимость электролитной меди.
Между тем все вышеперечисленные технологии переработки медного лома требуют значительных энергетических и материальных затрат. Кроме того они несут достаточно тяжелую нагрузку на окружающую среду.
Для снижения энергетических затрат и уменьшения нагрузки на окружающую среду разработана система технология, совмещающая выплавку, разливку и прокатку медной продукции.
Операционные циклы процесса Properzi состоят из плавки, рафинирования, непрерывного литья, затвердевания и прокатки непрерывнолитой заготовки из меди для производства готовой бухты электролитической медной катанки.
В настоящее время в промышленности имеются рафинирующие печи (рис.1) на 25, 40, 80 и 120 тонн / сутки. Эти печи имеют основную кладку и возможностью наклона агрегата. Магнезитовые кирпичи и бетон являются обязательными элементами, позволяющими выдержать химическую агрессивность вдуваемых кислорода и флюсовых добавок, а также получаемых оксидов, шлаков и газов. Как следствие этого, печь должна поддерживаться при высокой температуре, поскольку основные огнеупоры быстро разрушаются при циклическом нагревании и охлаждении.
Наклон печи также является обязательным функциональным элементом не только для контроля уровня во время плавки, но и потому, что воздух и топливо вдувают под уровень жидкого металла в печи на стадии рафинирования. Это осуществляется через одну, две или три фурмы, которые расположены выше уровня жидкого металла во время операций заправки и плавления и ниже уровня металла в процессе переработки.
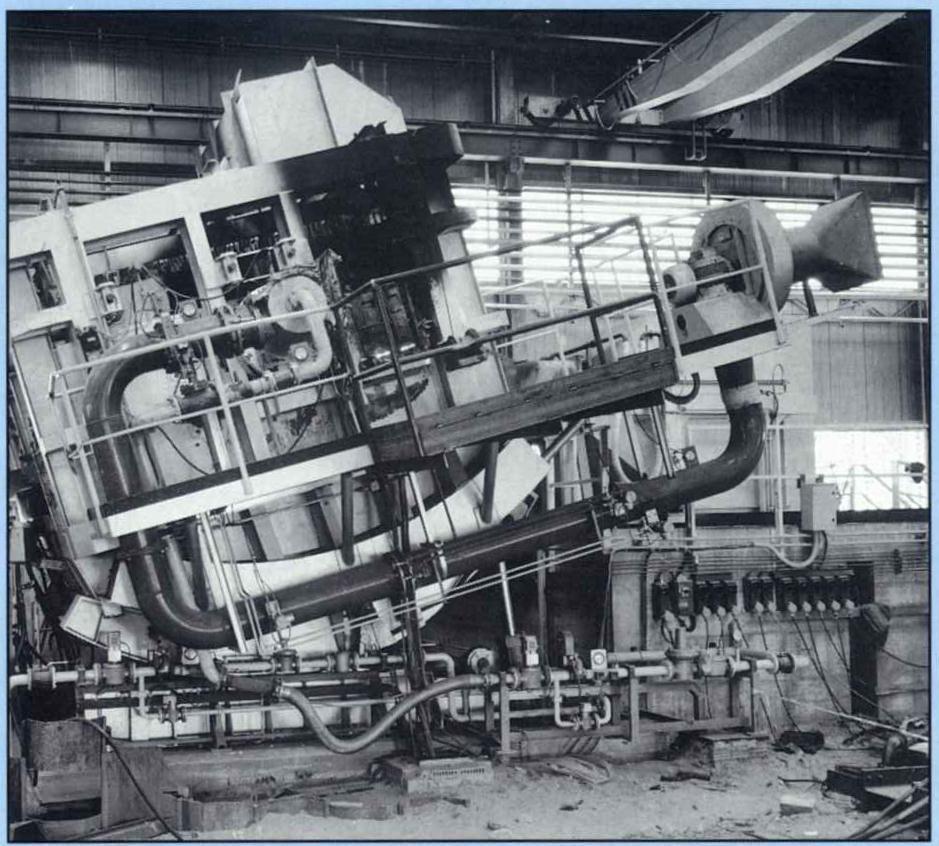
Рисунок 1. Общий вид наклонной рафинирующей печи
Период расплавления длится обычно около восьми-десяти часов. Переменная мощность горелок (окислительных и восстановительных) используются для быстрого расплавления и тщательного окисления металла. Температура в печи поддерживается на высоком уровне, чтобы получить лучшую гомогенизацию расплавленной меди. Как только первичный шлак полностью удаляется из печи процесс окисления жидкой ванне осуществляется путем введения воздуха под поверхность жидкой ванны.
Эта операция обычно длится около двух часов, а печь в это время имеет наклон 20 градусов к горизонту. При этом содержание кислорода достигает 10, 000 до 12, 000 ppm. Окисленные примеси становятся светлее, чем расплавленная медь, и плавают на поверхности жидкой ванны, формируя слой вторичного шлака. Для интенсификации этого процесса в расплав добавляются некоторые реагенты.
Удаление примесей свинца, олова и никеля, которые иногда присутствуют в относительно больших количествах, может вызвать некоторые затруднения. В таких случаях второй цикл рафинирования может быть необходим для полного удаления примесей. Для этого используются специальные добавки. Поскольку любой расплав имеет определенное количество примесей, зависящих от исходного лома, технология рафинирования должна корректироваться в соответствии с уровнем примесей и требованиями, предъявляемыми к конечному продукту.
На завершающей стадии плавки проводятся окончательное рафинирование. При этом из печи удаляются конечный шлак и оставшиеся флюсовые добавки. Печь еще раз наклоняется, что позволяет инжектировать пар и топливо в расплав и значительно снизить содержание кислорода (до 200-350 ppm). Содержание других примесей ниже 5 ppm.
Заключение
Использование операционных циклов процесса Properzi снижает энергетические и материальные затраты. Кроме того уменьшает нагрузки на окружающую среду. Технологический процесс изготовления медной катанки совмещает в одной технологической цепочке следующие операции: плавка шихты, отливка непрерывной заготовки, ее прокатка до размера катанки, осветление, охлаждение и смотка в бухты. Процесс непрерывного литья и прокатки имеет значительные технико-экономические преимущества перед старым процессом отливки слитков, их последующего нагрева, прессования и волочения.
Примечание
При написании данного реферата, магистерская работа еще не завершена. Окончательное завершение: декабрь 2012 г. Полный текст и материалы по теме могут быть получены у автора и его руководителя после указанной даты.
Литература
- Карел С., Zeitlon B. Metall, 1981, Bd, №35,№5, p. 417-421
- Базилевский В.М., Истрин М.А., Барташев И.Л. Вторичные цветные металлы (Справочник). Часть 3. Металлургия меди и свинца. Издательство литературы по чёрной и цветной металлургии. –М.: 1957. – 200 с.
- Купряков Ю.П. Производство тяжёлых цветных металлов из лома и отходов.- Харьков.: Основа.1992. -399 с.
- Худяков И.Ф., Тихонов А.И., Деев В.И., Набойченко С.С. Металлургия меди, никеля и кобальта. Часть 1. Металлургия меди. -М.: Металлургия. 1977. -356с.
- Береговский В.И., Кистяковский Б.Б. Металлургия меди и никеля. –М.: «Металлургия». 1972. -367 с.
- Савенков Ю.Д. Рафинированная медь Украины: / Ю.Д. Савенков, В.И. Дубоделов, В.А. Шпаковский, В.А. Кожанов, Е.В. Штепан _ Донецк: Издательство, 2008._176с.
- Бредихин В.Н. Медь Вторичная: Монография / Бредихин В.Н., Маняк Н.А., Кафтаненко А.Я – Донецк: ДонНТУ, 2006 р.