Abstract
Content
Introduction
The relevance of problems of recycling copper scrap in an environment of limited commodity markets of the industrialized countries in recent years, it has become increasingly so outpacing the growth of the machine-building complex and attractive exports steel products with limited raw materials for ferrous, slow development of deposits and exploration of new fields virtually stopped growing shortage of copper produces raw materials for the steel and foundry industries.
On the other hand, the deadliest being the mass retirement of capital stock (obsolete machines, hardware, etc.), due to their high age. So now the very high interest of metallurgical and foundry industries to find raw materials on secondary markets, and the increasing cost of energy leads to find more effective ways of their processing in commercial products.
Content of work
Metal copper production factory, the secondary non-ferrous metals usually include Pyro-and hydrometallurgical remaking converting, refining and casting. Pyrometallurgical Division of scrap and waste are in units of varying design: mine, reverberatory, electric arc furnaces, converters.
To smelt copper alloy scrap and waste are generally stationary, rotating and swiveling reverberatory furnaces.
To reduce energy costs and reduce the burden on the environment developed technology that combines steel smelting, casting and rolling of copper products.
Operating cycles process Properzi consist of smelting, refining, continuous casting, solidification of continuous casting and rolling of copper to produce the finished bays electrolytic copper rod.
Currently, there are industry refining furnace (fig. 1.) for 25, 40, 80 and 120 tons/day.
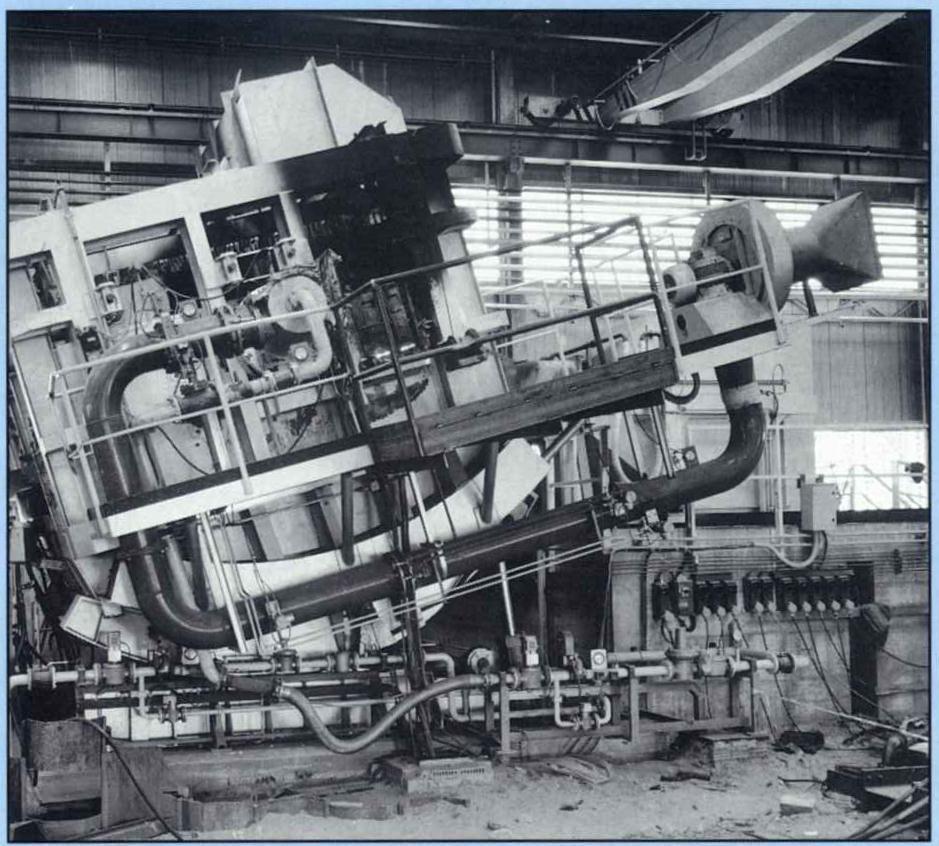
Figure 1-General view of the inclined refining furnace
Conclusion
Use operating cycles Properzi process reduces energy and material costs also reduces the burden on the environment. Technological process of manufacture of copper rod combines in a single chain: melting furnace, continuous casting billet and its rolling to fit rods, Dodge, cooling and winding of the Bay. The process of continuous casting and rolling mill has significant technical and economic advantages over the old process of casting ingots, their subsequent heating, pressing and drawing.
Important Note
When writing this author's abstract, Master's work is not completed yet. Final completion:December 2012. Full text and materials on the subject can be obtained from the author and his manager after that date.
Literature
- Карел С., Zeitlon B. Metall, 1981, Bd, №35,№5, p. 417-421
- Базилевский В.М., Истрин М.А., Барташев И.Л. Вторичные цветные металлы (Справочник). Часть 3. Металлургия меди и свинца. Издательство литературы по чёрной и цветной металлургии. –М.: 1957. – 200 с.
- Купряков Ю.П. Производство тяжёлых цветных металлов из лома и отходов.- Харьков.: Основа.1992. -399 с.
- Худяков И.Ф., Тихонов А.И., Деев В.И., Набойченко С.С. Металлургия меди, никеля и кобальта. Часть 1. Металлургия меди. -М.: Металлургия. 1977. -356с.
- Береговский В.И., Кистяковский Б.Б. Металлургия меди и никеля. –М.: «Металлургия». 1972. -367 с.
- Савенков Ю.Д. Рафинированная медь Украины: / Ю.Д. Савенков, В.И. Дубоделов, В.А. Шпаковский, В.А. Кожанов, Е.В. Штепан _ Донецк: Издательство, 2008._176с.
- Бредихин В.Н. Медь Вторичная: Монография / Бредихин В.Н., Маняк Н.А., Кафтаненко А.Я – Донецк: ДонНТУ, 2006 р.