Abstract
Contents
- Introduction
- 1. Goal and tasks of the research
- 2. Design of the laboratory facility
- 3. Creating a mathematical model
- Output
- References
Introduction
In the context of the global increase in energy prices, the priority of industry is a worldwide introduction of innovative energy-saving technologies that help minimize the share of energy costs in the cost of hire and improve, thus its competitiveness. In the fully specified direction corresponds to the process of casting-rolling roller, whose idea was proposed by Henry Bessemer in 1856 [1-2].
Despite the fact that the technology roll-casting-rolling reached the industrial implementation [3,10], the relevance of studies of this technology is still very high because of its high research intensity, and, to date, not settled some technological elements. Confirmation of this fact may be the fact that the leading research centers in the area of metallurgy have created over the past few years a whole set of laboratory facilities: the Rhine-Westphalian School, Aachen, Institute for the Study of iron to them. Max-Planck equation, Dusseldorf (Germany), University of Oxford (UK), a technological institute, Osaka (Japan) and the Institute of Industrial Materials, Mr. Bouchervil (Canada), etc.
Analysis of the results of scientific work done on these machines, showed that currently remain
unresolved or require further study of the following types of questions [9]:
- to achieve a uniform warm-taking at speeds of rolls ? 0,5 rad / s;
- how to optimize the supply of metal in a bath of crystallization;
- organization of the process of obtaining high-quality side edge strip;
- start-up elements of the system aren't optimized;
- how to optimize the depth of the bath of molten metal between the rollers, etc.
Based on the analysis of structural features known from the literature of experimental machines roll casting-rolling [5,8] can be concluded about the advisability of studying the object in small laboratory settings. According to this was proposed a small laboratory setup for the implementation of process-roll casting-rolling on the alloys with low liquidus temperature.
1. Goal and tasks of the research
The development of constructive, kinematic and hydrodynamic scheme of small laboratory setup for the implementation of process-roll casting-rolling on the alloys with low liquidus temperature.
2. Design of the laboratory facility
In designing the experimental setup used a vertical pattern of the process [4,7] when molten metal is fed from the furnace to the casting bath, and after to the space between rolls, zone of crystallization of the metal, under the action of gravity.
Rolls-molds are composed of water-cooled copper sleeve and two axial inserts that provide the desired character of warm-taking with the inner surface of the tires (Fig. 2). Each cylinder has its own unique DC drive, which ensures the implementation of high torque and the ability to manage the process with the required plastic deformation. In addition, provided the possibility of regulating the distance between the rollers, thus expanding the range of thicknesses studied a finite band: a maximum of 4.0 mm.
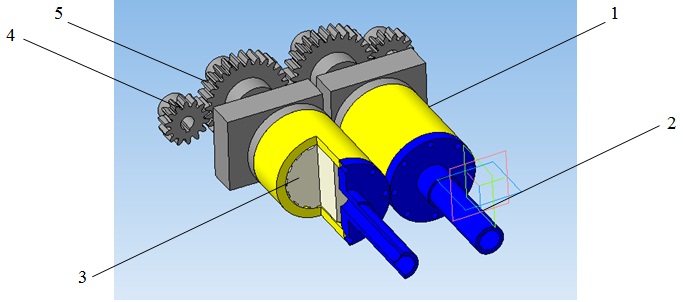
Figure 1 – The scheme of the node roll-molds (3D model):
1. water-cooled sleeve;
2. oporoa-carts;
3. inner box;
4. pinion gear;
5. driven gear.
The results of the design in the form of 3D models and photos of draft power are shown in Figure 3.
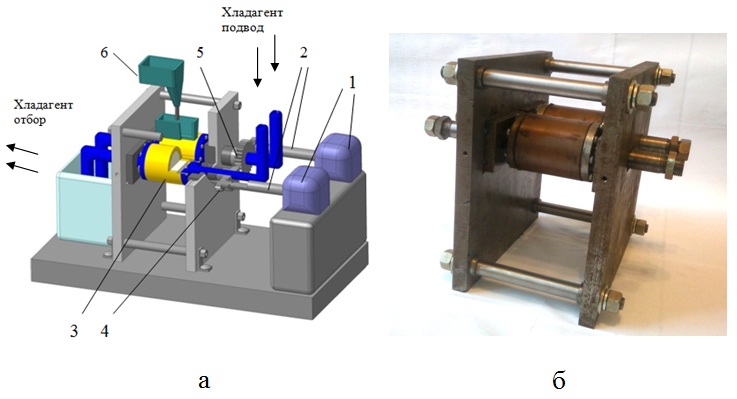
Figure 2 – The model projected a laboratory setting process, roll casting-rolling:
a - volume model of the laboratory setup process, roll casting-rolling, where 1 - the drive motors,
2 - spindles, 3 - cylinders, 4 - pinion gear, 5 - driven gear, 6 - bucket filling material,
b - photo lab full-scale installation.
Specifications made in the laboratory setting of the filling stand are presented in Table 1:
.jpg)
Table 1 – Main characteristics of the designed experimental set-roll casting process of rolling
3. Creating a mathematical model
Additionally, in parallel with the creation of a physical model was developed mathematical model allowing to study the process of casting a variety of materials for the above installation. The model is implemented in the software package ANSYS [6].
For the mathematical modeling of roll casting-rolling was selected generic software package ANSYS Int., Which is used to solve the problems associated with many branches of science and technology, such electrical engineering, electromagnetism, hydrodynamics, gas dynamics, etc.
Creating a mathematical model to study the processes of mixing and solidification of molten metal strip at the
roll casting was carried out in an environment ANSYS CFX, has the following features:
- modeling of inviscid, laminar and turbulent flows;
- modeling of heat transfer, including various types of convection, radiation and conjugate heat transfer, etc.
The basis of the developed mathematical model is a solution using the finite element method of unsteady heat conduction basic equation :

And Navier-Stokes equations, which include:
- the continuity equation (conservation of mass);
- the momentum equation (momentum conservation);
- the energy equation (energy conservation).
The solution of problems of fluid flow and solidification was realized in three-dimensional interpretation, with the following assumptions: non-deformable rolls, during the turbulent melt on contact between the roller and the metal holds a permanent adhesion.
As the spilled metal was chosen as lead. The boundary conditions are: thermal conductivity - 23.2 W / (m • K), specific heat capacity of spilled metal - 138.84 J / (kg • K), the density of the spilled metal - 10 641 kg / m 3. The technological characteristics are taken as close to the capabilities of the laboratory setup: external rotor diameter - 76 mm, the length of the zone of crystallization-deformation - 40 mm, strip thickness - 3.25 mm, the initial temperature of the molten metal - 327 ° C, constant spilled metal.
Output
Based on the analysis of designs available laboratory facilities designed version of a small laboratory device designed to study the hydrodynamics of the melt stream and optimize a number of technological parameters. The results of the primary mathematical modeling for the technical characteristics of the facility showed that it allows a wide range of modeling materials with a sufficiently low temperature crystallization.
References
- Nakayama, K. Twin roll caster / K. Nakayama //Zairyo to Prosesu CAMP ISIJ. -2009. -22.- C. 242-245.
- Степанов, А. H. Производство листа из расплава /А. И. Степанов, Ю. В. 3ильберг, А. А. Неуструев. - М.: Металлургия, 1978. - 160с.
- Schueren, V. The Castrip Process - an Update on Process Development at Nucor Steel’s First Commercial Strip Casting Facility / V. Schueren, P. Cambell, W. Blejde // Iron & Steel Technology.-2008.-July.-C.64-70.
- Santos, C.A. /Journal of Materials Processing Technology.-2000.-102.-C.33-39.
- Saitoh, T. Two-dimensional model for twin-roll continuous casting/ T.Saitoh, H. Hojo, H. Yaguchi, C.G. Kang,// Metall Trans.-1989.-20.B.-C. 381.
- Гридін, О. Ю. Математичне моделюванне процесу валкової розливки прокатки за допомогою програми Ansys/ О. Ю. Гридін, В. М. Данченко// Металлургическая и горнорудная промышленность. - 2008. - №5. - С. 90-94.
- Twin roll caster / Nakayama K. //Zairyo to Prosesu = CAMP ISIJ. 2009. 22. C. 242-245. Яп., огл. на. англ.
- The Castrip Process – an Update on Process Development at Nucor Steel’s First Commercial Strip Casting Facility / V. Schueren, P. Cambell, W. Blejde et al. // Iron & Steel Technology. 2008. July. C. 64-70 Англ.
- Данченко В.Н. Кардинальные изменения технологии и проблемы теории производства сталь ного проката // Металлург. и горноруд. пром-сть. - 2000. - № 8-9. – С. 13-19.
- Modelling of Melt Flow and Solidification in the Twin-Roll Strip Casting Process / B. Wang, J.-Y. Zhang, J.-F. Fan et al. // Steel Research International. 2009. 80. No 3. C. 218-222. AHen.