Abstract
Ñîäåðæàíèå
- Introduction
- 1. Theme urgency
- 2. Goal and tasks of the research
- 3. Methods to improve efficiency
- Conclusion
- References
Introduction
Ukraine is going through a difficult and controversial period of the new system of economic relations. The objective conditions for change and development of all forms of ownership, the emergence of wage labor, the expansion of foreign economic relations and the complexity required other than the above methods of management. First of all it concerns the management of material production. In many respects erroneous focus on assistance to foreign capital and foreign trade in goods to the detriment of the domestic, financial fraud and abuse of administrative structures, the penetration into all spheres of social production of crime has led society to the brink of serious shocks and crises. In addition, today's problems are generated by some of the incompetence of the leaders in the field of management, lack of knowledge of fundamental principles and techniques of modern management, the inability to use the positive experience of the old and the creative approach to the management of enterprises in market conditions. The main tasks of economic development at present is full efficiency of production and employment of sustainable products companies in the domestic and international markets. To withstand the intense competition and win the trust of customers need to stand out against the backdrop of the enterprises of the same type. It is well known that a buyer interested in the quality of the product and its price. The higher quality and lower price, better and more profitable for the buyer. These figures are just placed in production costs.
1. Theme urgency
The crisis state of the economy has deteriorated significantly, that puts the need to address the problems associated with an increase in production efficiency. crisis exacerbates and complicates the solution of problems of economic efficiency, determines the need for a thorough investigation of its causes, requires the introduction of new concepts for process control, new methods to improve production efficiency. The lack of a level of industrial complexes and methodological developments on the most effective methods of production management in the transition to a market economy leads to the fact that labor collectives intuitively looking for a way out of crisis without proper impact assessment and taking into account new factors acting on the effectiveness of their work. This often leads to loss of efficiency. This determines the relevance of the study, the need in theoretical and practical generalization performance management of production on an industrial complex and the solutions to problems through the introduction of new mechanisms to improve production efficiency. Master's thesis is devoted to developing and ensuring efficiency in the enterprises of Ukraine.
2. Goal and tasks of the research
The purpose of this paper is to examine methods to improve production efficiency company, to identify factors and ways to improve efficiency at the enterprise and put them in the industrial sector in Ukraine. The main objectives of the study. The objective is to analyze and study the mechanism of increasing the efficiency of production of the enterprise, the basic methods, application methods for increasing efficiency in Ukraine.
3. Methods to improve efficiency
Before the supreme command of any company or organization is a task to create an effective management system, aimed at achieving strategic goals. For this purpose, different approaches can be applied and methodological improvements: the standards for systems management, business model accuracy, benchmarking, reengineering, the approach of "six sigma", balanced scorecard, etc. etc. Here are some of them [1]:
A. Reengineering
Business process reengineering (BPR - Business Process Reengineering) is defined as "the fundamental rethinking and radical redesign of business processes (BP) to achieve a radical improvement in the basic performance of the enterprise: the timing, quality, cost and service." Reengineering is inherently provides for the replacement of the old methods of managing the new, more modern, and on this basis, a dramatic improvement in key performance indicators of enterprises. The purpose of business process reengineering (BPR) is a systemic restructuring of material, financial and information flows, aimed at simplifying the organizational structure, redistribution, and minimizing the use of various resources, reduction of the timing of customer needs, improving their quality of service [2]. For companies with a high degree of business diversification, a variety of partnership re-engineering of business processes provides the following tasks:
- - to determine the optimal sequence of functions performed, which leads to a reduction in cycle time manufacturing and selling of goods and services, customer service, resulting in increased turnover are the capital and the growth of all economic indicators of the company;
- - optimization of resource use in a variety of business processes, resulting in minimized costs and ensured optimal combination of different activities;
- - construction of adaptive business processes, aimed at rapid adaptation to changing needs of end users of products, production technologies, the behavior of competitors in the market and, consequently, improve the quality of customer service in a dynamic environment;
- - determination of rational schemes of interaction with partners and customers and as a result, revenue growth, optimization of financial flows;
- - synchronization and coordination of concurrent processes.
B. Total Productive Maintenance (TPM)
Modern equipment, which, as a rule, high-tech, requires not only the current state of knowledge of staff, who maintain the equipment in contact one way or another (and, directly or indirectly in contact with him almost every employee of the company), but the modern system of relations between employees. Building such a system of relationships - a complex, requiring a long-time problem, without which the most advanced equipment that does not give effect to which it is intended. However, this task can be greatly facilitated and accelerated through the use of world experience in the effective management of equipment. Today, the most complete expression of that experience found in the model, denoted by the abbreviation "TPM" [4].
Content of TPM:
- -TPM is to create an enterprise that constantly strives to limit and enhance the effectiveness of the integrated production system.
- -a means of achieving the goal is the creation of a mechanism which, covering direct jobs, aimed at preventing all forms of loss ("zero accidents", "zero breakdowns", "null marriage") throughout the life cycle of the production system.
- -to achieve the goal involve all divisions: engineering, business and management, but above all - production.
- involved in achieving the goal of the entire staff - from senior manager to the employee's "first line".
- desire to achieve zero losses realized in the framework of the hierarchically related small groups, which brings together all workers [5].
C. The system "Orderings» (5S)
System 5S, as well as the TPM, was created in the late 60's and 70's at the enterprises of Japan. It contained some measures to bring order, clarity, strengthening discipline and creating a safe working environment, with the participation of all staff. The system became the basis of 5S management and production efficiency. This system allowed virtually no capital cost to attract not only increase productivity to reduce costs to reduce the level of marriage and the injury, but also create the necessary conditions for starting the implementation of complex and expensive industrial and organizational innovation, provide high efficiency, primarily due to a radical change, the attitude of staff to their work.
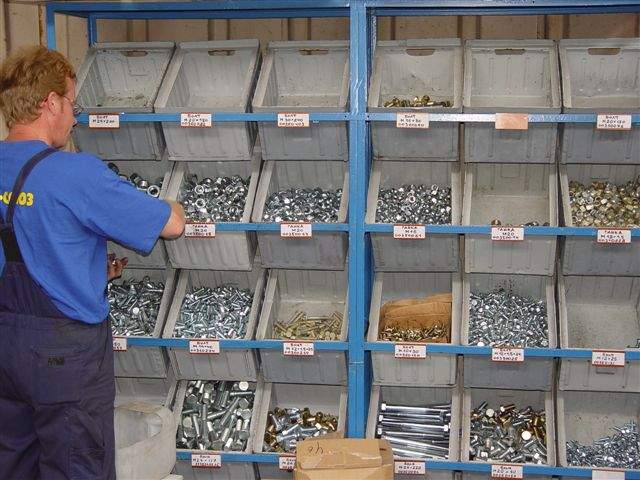
Figure 1 – Example of 5S
The development of the system has improved the 5S discipline staff to keep the equipment and the room clean. At the same time, according to experts of the Japanese Association of production services (JIPM), without the simultaneous deployment of TPM 5S system does not lead to significant sokrascheyiyu breakdowns, stoppages of equipment and product defects, because the perfect retention of the equipment does not guarantee against failure. The two systems interact well with one another, and function much better with [1].
Figure 1 shows the five elements of 5S, which indicate the following:
- - Seiri - organization (literally - "sort"). In the process of organizing objects are classified according to the degree necessary. The definition of necessary and unnecessary urgent and unnecessary items. The principles of division of objects on the necessary and unnecessary recorded. Elimination of unnecessary items is carried out after their inventory.
- - Seiton - accuracy of (literally - "to put in place"). The purpose of careful organization of the workplace - storage or placement of objects the most efficient way to comply with the requirements of safety, quality and efficiency. Items removed from the corridors, if they interfere with passage or aisle. Corridors must remain secure even if the emergency lighting is turned off. It is unacceptable to place objects where they might fall. The most frequently used objects closer to the operators. Easy things are placed on the upper shelves, heavy - at the height of the belt. Hang signs and symbols.
- - Seiso - cleaning (literally - "to shine"). The purpose of cleaning - to remove dust, dirt, oil stains, chips to make the equipment clean. Purification of the workplace makes it safer, improves the condition of the equipment, thus preventing defects, damage and downtime. The system practiced by TRM cleaning, combined with the test equipment that allows you to immediately identify the fault by visual diagnosis.
- - Seiketsu - standardize, standardize. As a result, the deployment of 5S in the enterprise, the conditions for maintaining the equipment in a clean and hygienic condition. To maintain this condition is necessary to make standard rules remove unwanted things, the location of objects in the workplace clean. These rules are usually fixed, how and what to do, how to evaluate the quality of work that should be taken in emergency situations, etc.
- - Shitsuke - discipline (literally - "support"). Discipline is the means and the purpose of deploying 5S. It involves changing habits of people for their compliance with the requirements of orderly and safe operation. It is important that employees not only to faithfully fulfill the requirements placed upon them, but also to understand their meaning [1,6-9].
Conclusion
Thus, the efficiency and performance - it is essentially synonymous terms, which are characterized by the same scoring process. We should realize that the overall system performance is a concept much broader than the productivity and profitability. In this work, were considered the most popular at this stage of the global economy methods of increasing production efficiency of the enterprise as benchmarking, 6 Sigma, Balanced Scorecard, reengineering, system of TPM, the system 5S. As you can see, these systems offer different approaches from different sides of production, they work separately, but I believe that comprehensive implementation of at least some of the proposed method gives important effects, and will pay for itself soon. There remains only the choice for companies who really want to live, not exist. First of all, changes and implementations of such systems and methods need to be prepared as a staff and senior management. Changing philosophy requires considerable effort, desire, perseverance, time. Not to implement such systems, most importantly to achieve its performance.
References
- A.I. Momot, Quality management and quality system elements - AK: Center for textbooks, 2007 – 368ñ.
- Telnov Y.F. Reengineering of business processes, Tutorial / Moscow International Institute of Econometrics, Informatics, Finance and Law. - Ì. , 2003. - 99ñ.
- Koch R. strategy. How to create and maintain an effective strategy. St. Petersburg. Peter, 2003
- How do the Japanese company. - M.: Economy, 1989. - Ñ. 130.
- Metallsertifikat [electronic resource]. - Mode of access:http://www.mc.misis.ru
- Kupriyanov T.M., Rastimeshin V.E.: "Ordering / 5S-guidance system of order, cleanliness, and strengthening discipline, with the participation of all staff" / / "Meat technologies" ¹7, 8, 9 2007 ã. [Ýëåêòðîííûé ðåñóðñ]
- Rastimeshin V.E., Kupriyanov, T.M. How to start a quality workplace / / Methods of Quality Management. - 2003. - ¹ 5. - Ñ. 4-10.
- Rastimeshin V.E., Kupriyanov, T.M. How to clean up the office / / Methods of Quality Management. - 2003. - ¹ 7. - Ñ. 12-15.
- Deryabin P.M. Why is it necessary to introduce a system of "ordering" / / Methods of Quality Management. - 2004. - ¹ 2. - Ñ. 14.