Recently, the world's acutely affects the limited energy resources and raw materials. Their high price is significantly determines the cost of production of the chemical industry. Accordingly, the priorities for the professionals of Chemical Technology Profile is to reduce the energy cost of industrial machines and systems and increas or maintain their production capacity.
The implementation of this is possible due to the introduction of new designs, more intensive processes and the use of secondary energy resources. Obviously, the complex application of these techniques help to solve the existing problems.
The principle of operation of any industrial unit is based on one or more physical / chemical or physico-chemical process. Usually, it is well-studied processes laws and regularities which are known and widely used.
However, it is currently known to science, more than 10 000 different effects and processes, only a small portion of which is used for the needs of the application. This is mainly due to the need of a large amount of research work.
Using computer programs of data analysis, modeling and design can significantly reduce the time spent on the stages of data collection, classification, ordering, processing and analysis, design and conduct experiments, analyze and interpret the experimental data, the formation of technical specifications and proposals, preparation of preliminary and detailed design of the project, implementation and improvement.
Figure 1. Computer programs as a
projector tools
As already noted, at the moment we know a lot of the different effects. And learn and implement all of them, even using modern computer technology is extremely difficult. However, if the pre-set a goal: to find the processes enabling conversion of energy from one form to another and conditions of which are sold in the intervals, we can identify a relatively small number of promising but not yet sufficiently studied processes. One of these processes - the vortex effect was chosen by us as the object of study.
Vortex effect is the
effect of
separation the twisting gas or liquid in a cylindrical or conical
chamber into two fractions. On the periphery of the swirling flow with
higher temperature, and in the center - hooked cooled stream.
To get an idea of the reasons for this seemingly paradoxical
phenomenon, it is necessary first of all to consider the motion of the
gas in the vortex tube.
The vortex chamber has a cylindrical shape. At one end of the pipe
nozzle is located a rectangular tangential entry of gas. The other end
of the tube is open. At the gas outlet of the nozzle is formed stream
entering the vortex tube on a high speed flow around the inner surface
of the pipe, the gas becomes a rotational movement and is moving out of
it along a helical path If in a plan view, the gas preferably moves the
periphery devices (Fig. 3)
If the bottom of the tube equiped with a diaphram, the flow pattern changes as follows: the flow from the nozzle, will also move in and out along the periphery of the upper end of the pipe, however, in this case from the atmosphere into the diaphragm will be pulled a certain amount of gas which will twist peripheral flow and entrained upwards into the pipe thus will move two streams, one moves tangentially, and the other axially with relatively to the pipe axis. (Fig. 4).
If to the top of of pipe install the control device in the form of a cone, you can change the flow area of the gas outlet, the flow pattern is changed as follows: the distribution of the tangential velocity at the same does not change significantly, but the presence of resistance increases the pressure in the pipe, and there comes a time when a part of flux located in the central zone starts to go out through the aperture. That axial flow direction changes on the opposite (Fig. 5).
Figure 2.
The operation
principle
of the vortex effect
Figure 3. Flow pattern of the peripheral
flow
If the bottom of the tube equiped with a diaphram, the flow pattern changes as follows: the flow from the nozzle, will also move in and out along the periphery of the upper end of the pipe, however, in this case from the atmosphere into the diaphragm will be pulled a certain amount of gas which will twist peripheral flow and entrained upwards into the pipe thus will move two streams, one moves tangentially, and the other axially with relatively to the pipe axis. (Fig. 4).
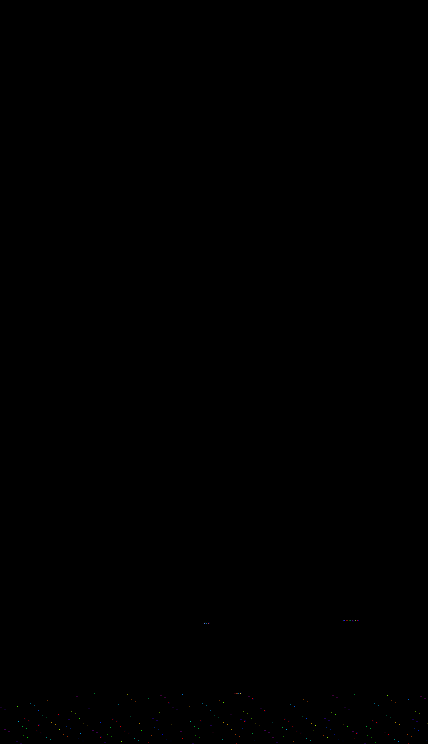
Figure 4. Flow pattern
of the two
streams that have the same direction
If to the top of of pipe install the control device in the form of a cone, you can change the flow area of the gas outlet, the flow pattern is changed as follows: the distribution of the tangential velocity at the same does not change significantly, but the presence of resistance increases the pressure in the pipe, and there comes a time when a part of flux located in the central zone starts to go out through the aperture. That axial flow direction changes on the opposite (Fig. 5).
Figure 5. Flow
pattern of the
countercurrent vortex
effect
Thus between two oppositely moving flows, heat transfer begins to
occur, caused by the difference in their thermodynamic temperature.
From the top of the pipe is the hot flow and from the bottom - cold[1]
Using this effect to the needs of the application can simultaneously
carry out several processes:
- Cooling and heating;
- Cooling and degassing;
- The separation of the phases and cooling;
The feasibility of using a vortex effect it is primarily determined by its characteristics in comparison with other methods of heating, cooling and vacuum.
Features of the vortex effect which can provide a positive result of its use are as follows:
1. Simplicity and reliability of the part of the installation in which the gas expansion. As in most other devices of similar purpose this part are the least reliable installation. In this case devices based on the vortex effects have clear advantage.
2. The possibility of combining several processes: cooling and heating, cooling and vacuum, cooling and phase separation, etc. without significantly complicating the device.
3. Simplicity and precision of regulation of the flow obtained through the installation in a wide range.
4. The speed and ease of start, stop and content in reserve.
5. Ability to use for any gas-production environments, different pressure drops (from a few MPa to tens of kPa) and a wide range of gas flow (from thousands to few m3/h)
6. Small dimensions and weight of the vortex tubes allow organically incorporate them into the design of the system in which they are used.
- Cooling and heating;
- Cooling and degassing;
- The separation of the phases and cooling;
The feasibility of using a vortex effect it is primarily determined by its characteristics in comparison with other methods of heating, cooling and vacuum.
Features of the vortex effect which can provide a positive result of its use are as follows:
1. Simplicity and reliability of the part of the installation in which the gas expansion. As in most other devices of similar purpose this part are the least reliable installation. In this case devices based on the vortex effects have clear advantage.
2. The possibility of combining several processes: cooling and heating, cooling and vacuum, cooling and phase separation, etc. without significantly complicating the device.
3. Simplicity and precision of regulation of the flow obtained through the installation in a wide range.
4. The speed and ease of start, stop and content in reserve.
5. Ability to use for any gas-production environments, different pressure drops (from a few MPa to tens of kPa) and a wide range of gas flow (from thousands to few m3/h)
6. Small dimensions and weight of the vortex tubes allow organically incorporate them into the design of the system in which they are used.
There
are two different levels of research facility - empirical and
theoretical.
At the empirical level, the study takes a process of gaining knowledge as a result of human interaction directly with the object of study. Through the senses researcher receives specific information about individual phenomena. At this level of knowledge applicable observation, experiment and measurement. The result of these studies is an empirical generalization, which is expressed in established by observation and experimentation facts.
In addition to the empirical level there is a theoretical research level. At the theoretical level, the objects under study are replaced by their idealized counterparts. For this level of knowledge is characterized by: a thought experiment, modeling, etc. It was modeling as a theoretical method of learning that has become widespread to acquire new knowledge, including for objects of chemical technology.
Was selected scientific simulation, in particular - computer simulation.
An important component of cognitive activity are research tools, which, in the case of computer simulation, speaking a variety of programs and application software packages.
At the moment, there are a large number of application software packages to model chemical processes [2], [3], [4]. These packages use a variety of approaches to modeling and have different tools convenient or inconvenient for solving a particular application.
As the simulation tools used an application software package SolidWorks and in particular its module for modeling the flow of liquids and gases - Flow simulation.
Flow simulation - the software fully integrated into SolidWorks to calculate the liquid and gas flows within and outside the model of SolidWorks, and also calculates the heat transfer from, to and between these models, convection, radiation and conduction through technology computing gidrgazodinamiki (CFD). To perform computational analysis using Flow Simulation is necessary to:
1. Create a solid model in Solid works
2. Create a project of the study
3. Set boundary conditions of the simulation.
4. Ask the goals of the project
5. And run a calculation
6. View and analyze the results to determine the accuracy of the solution [5], [6],
At the empirical level, the study takes a process of gaining knowledge as a result of human interaction directly with the object of study. Through the senses researcher receives specific information about individual phenomena. At this level of knowledge applicable observation, experiment and measurement. The result of these studies is an empirical generalization, which is expressed in established by observation and experimentation facts.
In addition to the empirical level there is a theoretical research level. At the theoretical level, the objects under study are replaced by their idealized counterparts. For this level of knowledge is characterized by: a thought experiment, modeling, etc. It was modeling as a theoretical method of learning that has become widespread to acquire new knowledge, including for objects of chemical technology.
Was selected scientific simulation, in particular - computer simulation.
An important component of cognitive activity are research tools, which, in the case of computer simulation, speaking a variety of programs and application software packages.
At the moment, there are a large number of application software packages to model chemical processes [2], [3], [4]. These packages use a variety of approaches to modeling and have different tools convenient or inconvenient for solving a particular application.
As the simulation tools used an application software package SolidWorks and in particular its module for modeling the flow of liquids and gases - Flow simulation.
Flow simulation - the software fully integrated into SolidWorks to calculate the liquid and gas flows within and outside the model of SolidWorks, and also calculates the heat transfer from, to and between these models, convection, radiation and conduction through technology computing gidrgazodinamiki (CFD). To perform computational analysis using Flow Simulation is necessary to:
1. Create a solid model in Solid works
2. Create a project of the study
3. Set boundary conditions of the simulation.
4. Ask the goals of the project
5. And run a calculation
6. View and analyze the results to determine the accuracy of the solution [5], [6],
Based on the above characteristics and purposes of scientific research
and the studies of work in this area, plan of the research
have the following steps:
1. Conduct a meaningful calculation of the vortex tube, which works with the chosen parameters, according to the procedures carried out in the literature.
2. Make a computer model of the vortex tube in the application software package.
3. Make a plan of numerical experiments and carry out a number of experiments required in the model.
4. Analyze the results and draw conclusions about the future direction of research.
1. Conduct a meaningful calculation of the vortex tube, which works with the chosen parameters, according to the procedures carried out in the literature.
2. Make a computer model of the vortex tube in the application software package.
3. Make a plan of numerical experiments and carry out a number of experiments required in the model.
4. Analyze the results and draw conclusions about the future direction of research.
According to the procedures described in the literature [1], was produced
meaningful calculation of the vortex tube design of the Moscow Power
Engineering Institute (Fig. 6)
Designed device has the following characteristics:
1 Technological characteristics:
Flow of the working gas: G = 200 kg/h
The initial gas pressure: P = 0,6 MPa
The initial gas temperature: 20 ⁰ C
Rated temperature of the cooled gas: -10 ⁰C
Nominal cooling capacity: 1700 W
2 Constructive characteristics:
Device length: L = 1,2 m
Working length: Lp = 930 mm
The diameter of the working part Dp = 38 mm
In application software package was created three-dimensional model of the vortex tube according to the structure shown in Figure 6.
Figure 6. The
vortex tube developed
by the Moscow Power Engineering Institute
Designed device has the following characteristics:
1 Technological characteristics:
Flow of the working gas: G = 200 kg/h
The initial gas pressure: P = 0,6 MPa
The initial gas temperature: 20 ⁰ C
Rated temperature of the cooled gas: -10 ⁰C
Nominal cooling capacity: 1700 W
2 Constructive characteristics:
Device length: L = 1,2 m
Working length: Lp = 930 mm
The diameter of the working part Dp = 38 mm
In application software package was created three-dimensional model of the vortex tube according to the structure shown in Figure 6.
Figure 7.
Three-dimensional model
of the vortex device
In order to obtain the most complete information about the
object being studied drafted a plan of full factorial experiment.
Experiment planning dramatically improves the accuracy and reduces the
amount of experimental research. It allows you to find the optimum
function, which characterizes the process under study.
Because studies are conducted for practical purposes, they aim to identify opportunities to enhance efficient operation of a pilot plant. Accordingly, the purpose of the planning of the experiment is to determine the extremes (high and low) of the response in the domain.
The vortex tube that is modeled, designed for temperature separation, and the main object of study is the temperature of the cold stream. It is regarded as the output variable, which is an unknown function of several factors, t= f(x1, x2 ... xi).
Multifactorial experiment gives the opportunity to change it strategy after the next step. Multifactorial planning is based on a rather general mathematical formalism allows to obtain the mathematical model of the process.
As the factors of varying was selected mass flow and pressure of the feed stream entering the device. Both of these factors can be set as desired.
For values of the factors in the center of the experiment was used flow and gas pressure obtained by the calculation unit (200 kg/h, 0.6 MPa). The values for intervals varying flow and pressure are set such that a transition from one experience to another change situation considerably . For the selected parameter, these intervals are: 100 kg/h and 0.2 MPa.
For convenience the experimental design and analysis of experimental data used encoding factors. Coding of all factors and normalized dimensionless variables taking during the experiment values -1, 0, +1. The combination of two factors on two levels at which implements all the possible combinations of factor levels requires holding 4 experiments
Table 1. Matrix-encoded of the two-factor experiment
In addition experiment was performed for two working gases: air and carbon dioxide, respectively, the required number of experiments is 8.
Because studies are conducted for practical purposes, they aim to identify opportunities to enhance efficient operation of a pilot plant. Accordingly, the purpose of the planning of the experiment is to determine the extremes (high and low) of the response in the domain.
The vortex tube that is modeled, designed for temperature separation, and the main object of study is the temperature of the cold stream. It is regarded as the output variable, which is an unknown function of several factors, t= f(x1, x2 ... xi).
Multifactorial experiment gives the opportunity to change it strategy after the next step. Multifactorial planning is based on a rather general mathematical formalism allows to obtain the mathematical model of the process.
As the factors of varying was selected mass flow and pressure of the feed stream entering the device. Both of these factors can be set as desired.
For values of the factors in the center of the experiment was used flow and gas pressure obtained by the calculation unit (200 kg/h, 0.6 MPa). The values for intervals varying flow and pressure are set such that a transition from one experience to another change situation considerably . For the selected parameter, these intervals are: 100 kg/h and 0.2 MPa.
For convenience the experimental design and analysis of experimental data used encoding factors. Coding of all factors and normalized dimensionless variables taking during the experiment values -1, 0, +1. The combination of two factors on two levels at which implements all the possible combinations of factor levels requires holding 4 experiments
Table 1. Matrix-encoded of the two-factor experiment
Experiment number | Levels
of the variables |
Responses | |
G | P | tx ⁰С | |
1 | -1 | -1 | t11 |
2 | +1 | -1 | t12 |
3 | -1 | +1 | t13 |
4 | +1 | +1 | t14 |
In addition experiment was performed for two working gases: air and carbon dioxide, respectively, the required number of experiments is 8.
The
data obtained from experiments are presented in tables and graphs.
Analyzing the data it can be concluded that the effect of the gas flow to the mode of the vortex tube when the mode decrease or increase from its nominal will impair its effectiveness. In the first case it is called because the small fraction of the pipe is used. In the second case, the temperature of the product stream will be insufficient.
Increasing the pressure in the device enhances the effect of the energy separation of the two gases, but it obviously leads to increased costs necessary to create these pressures (the installation of more powerful compressors and their exploitation).
If we compare the effect of temperature separation of the two gases it is clear that, all else being equal parameter sets the value of the effect of temperature will be higher for the separation of carbon dioxide. We can conclude that the causes of lower temperatures are in other experimental parameters in pending gas.
Since the mathematical model is described by certain gases, known set of constants and variables, it can be heat, molecular weight M (density), dynamic viscosity, thermal conductivity. Determination of the effect of these parameters on the effect of temperature division obviously is the goal of further research.
Also, during the research determined the internal parameters of the model that works with standard identified in the structural characteristics of the calculation. We determined the speed and pressure of the working flow along the axis of the chamber.
Figure
8.
The pressure values in the longitudinal axis of the vortex tube
The pressure distribution along the axis
of the camera in the device does not contradict the theoretical
concepts of modern hydrodynamics. The jump in pressure at the 0,35-0
due to the presence of local resistance in the form of a diaphragm.
Velocity fluctuations along the axis of the machine apparently caused by turbulent interaction of individual elements of the swirl flow. This leads to significant losses as axial flow of mixed peripheral z, thus reducing heat transfer therebetween. Therefore, finding ways to increase the ideal structure of the two streams can also be the next target of the research work.
Table
2. The values of the
factors and response functions for air
Experiment number | Levels of the variables | Responses | ||
G (kg/h) | P (MPa) | tx ⁰С | Px (MPa) | |
1 | 100 | 0,4 | -12,8 | 0,136 |
2 | 300 | 0,4 | -10,3 | 0,105 |
3 | 100 | 0,8 | -16,1 | 0,124 |
4 | 300 | 0,8 | -12,3 | 0,159 |
Table 3. The
values of the
factors and response functions for carbon dioxide
Experiment number | Levels of the variables | Responses | ||
G (kg/h) | P (MPa) | tx ⁰С | Px (MPa) | |
1 | 100 | 0,4 | -15,6 | 0,134 |
2 | 300 | 0,4 | -11,1 | 0,13 |
3 | 100 | 0,8 | -17,2 | 0,121 |
4 | 300 | 0,8 | -14,7 | 0,157 |
Analyzing the data it can be concluded that the effect of the gas flow to the mode of the vortex tube when the mode decrease or increase from its nominal will impair its effectiveness. In the first case it is called because the small fraction of the pipe is used. In the second case, the temperature of the product stream will be insufficient.
Increasing the pressure in the device enhances the effect of the energy separation of the two gases, but it obviously leads to increased costs necessary to create these pressures (the installation of more powerful compressors and their exploitation).
If we compare the effect of temperature separation of the two gases it is clear that, all else being equal parameter sets the value of the effect of temperature will be higher for the separation of carbon dioxide. We can conclude that the causes of lower temperatures are in other experimental parameters in pending gas.
Since the mathematical model is described by certain gases, known set of constants and variables, it can be heat, molecular weight M (density), dynamic viscosity, thermal conductivity. Determination of the effect of these parameters on the effect of temperature division obviously is the goal of further research.
Also, during the research determined the internal parameters of the model that works with standard identified in the structural characteristics of the calculation. We determined the speed and pressure of the working flow along the axis of the chamber.
Figure 9. The velocities along the longitudinal axis of the vortex tube
Velocity fluctuations along the axis of the machine apparently caused by turbulent interaction of individual elements of the swirl flow. This leads to significant losses as axial flow of mixed peripheral z, thus reducing heat transfer therebetween. Therefore, finding ways to increase the ideal structure of the two streams can also be the next target of the research work.
Vortex
effect and devices
running on its
principle is a promising object of research. The main part of the
investigation and the search for possible ways of intensification of
this process should be carried out by computer simulation, as it allows
you to bypass the difficulties that arise in the study of this process,
which is characterized, the critical values of pressure, speed, cost,
complex embodiment of the installation.
When using a vortex effect as the basis of refrigeration and heating units should try to make the most of the energy flows.
The results that was obtaining during study shows the capabilities intensification of the process. They are: creating the most ideal structure of two interacting flows and use of denser environments. At the next stage of investigation is expected to create a vortex countercurrent effect using viscous fluid that will likely require application of additional forces to unwind flow and accordingly modifying the model. In writing this essay master's work is not yet complete. Final completion: December 2012. The full text of the work and materials on the topic can be obtained from the author or his head after that date.
When using a vortex effect as the basis of refrigeration and heating units should try to make the most of the energy flows.
The results that was obtaining during study shows the capabilities intensification of the process. They are: creating the most ideal structure of two interacting flows and use of denser environments. At the next stage of investigation is expected to create a vortex countercurrent effect using viscous fluid that will likely require application of additional forces to unwind flow and accordingly modifying the model. In writing this essay master's work is not yet complete. Final completion: December 2012. The full text of the work and materials on the topic can be obtained from the author or his head after that date.
1. Мартынов А.В. Что такое
вихревая труба? / Мартынов А.В., Бродянский В.М. / Москва:
«Энергия». 1976.-
152 с.
2. Ошовский В.В. Использование компьютерных систем конечно-элементного анализа для моделирования гидродинамических процессов / Ошовский В.В., Охрименко Д.И., Сысоев А.Ю. // «Наукові праці Донецького національного технічного університету». Серия «Химия и химическая технология». Выпуск № 15. Донецк. 2010.
3. Ошовский В.В. Применение компьютеризованной системы моделирования в процессе обучения студентов химиков— технологов на примере расчёта абсорбционной очистки газа от сероводорода / Ошовский В.В., Сысоев А.Ю., Охрименко Д.И. // «Наукові праці Донецького національного технічного університету». Серия «Химия и химическая технология». Выпуск № 14. Донецк. 2010.
4. Голубев А. В. Компьютерное моделирование распределения охлаждающего газа в установках сухого тушения кокса / Голубев А. В., Збыковский Е. И., Дюбанов А. В., Топоров А. А. // «Наукові праці Донецького національного технічного університету». Серия «Химия и химическая технология». Выпуск № 18. Донецк. 2012.
5. Алямовский А.А. Компьютерное моделирование в инженерной практике / Алямовский А.А. // СПб: БХВ Петербург. 2005. – С. 163-170.
6. SolidWorks Flow Simulation 2012 Technical Reference // 2012.- С. 3-10.
7. Касаткин А.Г. Основные процессы и аппараты химической технологии / Касаткин А.Г. // «Химия». Москва. 1970. – С. 52-56.
8. Мелюшев Ю.К. Основы автоматизации химических производств и техника вычислений / Мелюшев Ю.К. // «Химия». Москва 1982. – С. 117-119.
2. Ошовский В.В. Использование компьютерных систем конечно-элементного анализа для моделирования гидродинамических процессов / Ошовский В.В., Охрименко Д.И., Сысоев А.Ю. // «Наукові праці Донецького національного технічного університету». Серия «Химия и химическая технология». Выпуск № 15. Донецк. 2010.
3. Ошовский В.В. Применение компьютеризованной системы моделирования в процессе обучения студентов химиков— технологов на примере расчёта абсорбционной очистки газа от сероводорода / Ошовский В.В., Сысоев А.Ю., Охрименко Д.И. // «Наукові праці Донецького національного технічного університету». Серия «Химия и химическая технология». Выпуск № 14. Донецк. 2010.
4. Голубев А. В. Компьютерное моделирование распределения охлаждающего газа в установках сухого тушения кокса / Голубев А. В., Збыковский Е. И., Дюбанов А. В., Топоров А. А. // «Наукові праці Донецького національного технічного університету». Серия «Химия и химическая технология». Выпуск № 18. Донецк. 2012.
5. Алямовский А.А. Компьютерное моделирование в инженерной практике / Алямовский А.А. // СПб: БХВ Петербург. 2005. – С. 163-170.
6. SolidWorks Flow Simulation 2012 Technical Reference // 2012.- С. 3-10.
7. Касаткин А.Г. Основные процессы и аппараты химической технологии / Касаткин А.Г. // «Химия». Москва. 1970. – С. 52-56.
8. Мелюшев Ю.К. Основы автоматизации химических производств и техника вычислений / Мелюшев Ю.К. // «Химия». Москва 1982. – С. 117-119.