Abstract
Сontent
- Introduction
- 1. Applications manganite
- 2. Theme urgency
- 3. Goal and tasks of the research
- 4. Preparation of rare earth perovskite manganite
- 4.1 On ceramic technology
- 4.2 Chemical methods of mortar
- Conclusion
- References
Introduction
Among the most promising inorganic oxide materials occupy an important place manganite perovskite structure (AxB1-x)1-yMn1+yO3±Δ, where A - the rare earth (La, Pr, Nd), B - the divalent metal (Ca, Sr, Ba, Pb). The interest in rare-earth manganites called urgent problems of microelectronics in the creation of systems with isotropic magnetoresistance, operating at room temperature.
Manganite - it's a solid solution with a peculiar relationship of the electrical, magnetic and structural properties, which can be adjusted by changing their production technology and chemical composition, including doping. Their micrographs are shown in figure 1.
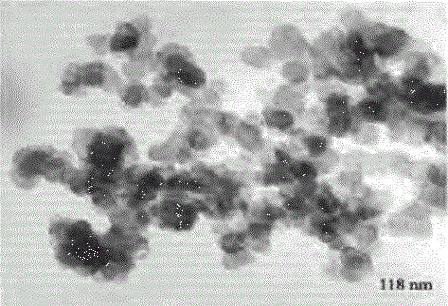
Figure 1 - The micrographs manganite powders of different dispersion
(Animation: 10 shots, 7 cycles of repetition, 473 KB)
Properties of magnetic semiconductors as of giant magnetoresistance materials have been known for a long time, but special scientific interest began only in 1994, after the publication of the article Gina S. in which the results of crystals of lanthanum manganite was confirmed only in the films which means that the multilayer films have a problem with the application and to look for other physical systems. And so it began its massive study.
Currently known properties of the films is strongly dependent on the technology of their production. The main problem manganite - finding the best technology with high sensitivity for weak fields.
1. Applications manganite
The high sensitivity of the resistivity to the magnetic field and the presence of a large number of coexisting phase states makes the metal oxide solid solutions manganite attractive target for the practical application of research in: highly sensitive sensors, magnetoresistive memory cells as a component of catalysts of chemical reactions, a magnetic recording device, a solid electrolyte fuel cell, and magnetoresistive sensors sensitive magnetic field.
2. Theme urgency
Search and optimization methods for producing rare earth materials in the manganite nanodispersed state - for now urgent scientific and technical challenge because the solution will increase the surface area of ??the catalysts and their efficiency. Also it is important to study the effect of crystallite size on the electromagnetic properties, which plays a special role to obtain samples with precisely specified characteristics.
3. Goal and tasks of the research
The aim of the study is to research and develop the conditions for obtaining the rare earth perovskite manganite for nanosized materials with the required set of electromagnetic parameters.
For realization of the need to solve a number of problems osnovnyx:
- investigate different technologies for allowing synthesis of nanoparticulate system.
- determine the role of dispersion of the powders in the formation of properties.
- study of physical and chemical processes for the synthesis and their contribution to the final characteristics.
4. Preparation of rare earth perovskite manganite
Numerous studies of rare-earth manganites relate mainly to explore a wide range of physical properties, and technology of powder materials is almost not given sufficient attention, also driven the fewest of information they receive - a very controversial [1].
To obtain experimental batches of rare-earth manganites and conduct a comparative analysis of their use solid-phase reaction method oxides and carbonates (ceramic technology) Some methods and mortar Chemistry: codeposition and spray hydrolysis. For the synthesis we selected was the system of La0,6Sr0,3Mn1.1O3±Δ, because strontium-substituted lanthanum manganite have the highest Curie temperatures with a significant magnetoresistive effect [2].
4.1 On ceramic technology
Ceramic technology based on solid-phase reaction method, the initial batch ingredients. Now about 90% of total production of functional materials provided by this method [3]. It's simple and cheap, has a high degree of reproducibility. Along with this, the method has some shortcomings, as a result of which one has to resort to more sophisticated technologies such as instant chemistry methods [2].
For the synthesis of the rare-earth manganite La0,6Sr0,3Mn1.1O3±Δ as raw materials used lanthanum oxide (La2O3), manganese (Mn3O4) and strontium carbonate (SrCO3) jet qualification "reagent grade" and "analytical grade." Raw materials are analyzed for major components dried at a temperature of 130-150°C in an oven at Protvino layer of 40-60 mm, not less than one day. Then they were mixed in an appropriate ratio, and performs a series of processing operations as shown in the flow diagram in Figure 4.1 [4].
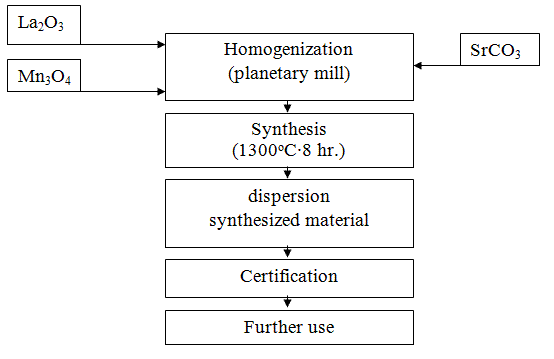
Figure 4.1 - Technology diagram of the method of obtaining the ceramic lanthanum strontium manganite
The most crucial is the operation of homogenization (mixing) - grinding the mixture of the starting components and dispersion of the synthesized material. Qualitative batch preparation enhances its uniformity and fineness, and as a consequence, the ability of the synthesis reaction, and pulverizing the material increases its activity as a result, how particle size reduction and distortion of the crystal lattice, increases the speed of the sintering process heterophasic products [2].
Mixing - shredding the original oxide-carbonate raw materials and dispersing the finished material was carried out in a planetary mill. Grinding bodies to carry out its complex movement as a result of double-speed drums agate workers: together with the platter (which strengthened drums) and around its own axis. Impact force agate grinding bodies several times by hitting balls in a ball mill, which results in higher dispersion efficiency in planetary mills compared with spherical. In addition, a high degree of purity of the charge and on the impurity content of the material [2].
Synthesis was carried out in the form of powder or in the form of briquettes. Poured the batch layer 50-60 mm high alumina or alundum Kapsel and loaded alternately in a tunnel furnace. Allowed the synthesis of another furnace construction with selection opridelennym synthesis temperature and time so as to ensure the completeness of the passage of solid phase reaction. Kapsel advance rate through the channel is to provide an 8-hour stay of the material in the zone temperature 1100-1300°C [5].
In a tunnel kiln passes the thermal decomposition of strontium carbonate in the mixture:
SrCO3→SrO + CO2↑
Intermediate products, which are differential-limiting step in the synthesis process of the material and certainly depends on the activity of the starting components [6]..
Persistent perovskite structure ceramic batch can be prepared at 1300°C • 8 hr. (synthesis as a powder) and at 1000°C • 12 hours., 1300°C • 6 hr. (Synthesis as tablets) [7].
4.2 Chemical methods of mortar
For nano-sized powders, which affect the formation of the properties of rare-earth manganites, increased demand for chemical technology of materials. Chemistry Methods soluble powders can directly synthesize the desired product (bypassing keramikoobrazuyuschih receive individual components) with different dispersion nano particles (20-60 nm), which is not provided ceramic technology (100 nm and above). We used the methods of co-precipitation (Fig. 4.2) and the spray hydrolysis (Fig. 4.2, 4.3) [2].
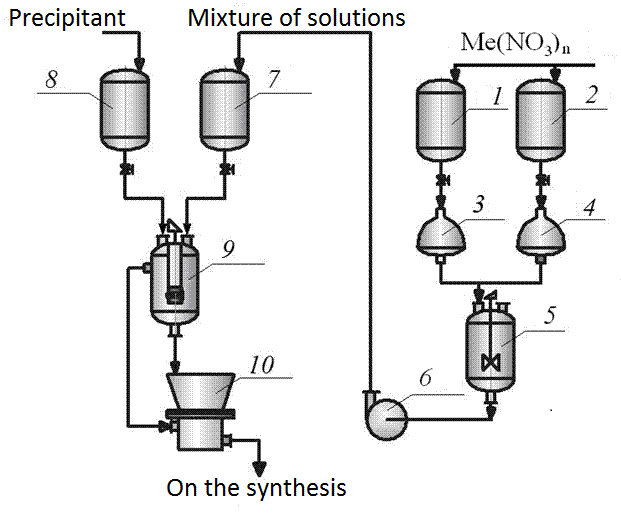
Figure 4.2 - Diagram of the installation methods of obtaining manganite mortar Chemistry
1, 2 - collections of solutions, 3, 4 - automatic dispensers, 5 - mixing solutions, 6 - Pump 7 - lifting capacity of 8 - collection of precipitant solution, 9 - downcomer, 10 - suction filter
Methods based on the coprecipitation of soluble compounds through various chemical reactions between the alkaline agent (a mixture solution of ammonium carbonate and hydroxide) with aqueous solutions of salts containing cations of different metals in the desired proportions. The absence of grinding operations in the manufacture of the initial charge for high purity end products. By varying the deposition conditions (feedrate solutions stirrer speed, temperature, pH of the medium) is regulated dispersion of calcined powders[2].
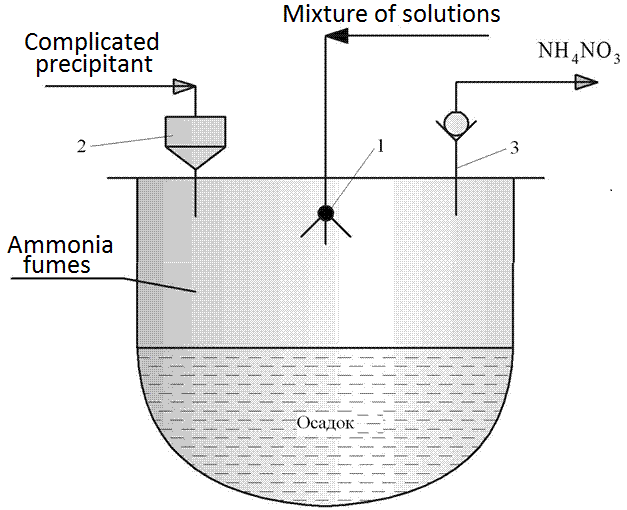
Figure 4.3 - Scheme of the reactor for the deposition of spray hydrolysis
1 - ultrasonic disperser, 2 - fitting for the supply of complex precipitant, 3 - fitting for the steam NH4NO3
Installing the spraying method using hydrolysis similar to that shown in Figure 4.2. The difference lies in the design of the deposition reactor (item 9), the circuit is shown in Figure 4.3. The method involves spraying using ultrasound (or air) mixture of solutions of salts in the solution of complex precipitant postupauschego gravity of the reactor pressure vessel through the fitting (item 2). The method involves spraying a mixture of not only the salt solutions, but a non-solvent (for the circuit of Fig. 4.3 not shown). However, this technique in the preparation of manganite was not used. The chemical reaction takes place mainly in the evaporation chamber of the reactor provides most of the unwanted fumes NH4NO3 during the deposition. After draining the solution, the suspension was stirred and, after maturation and verify complete precipitation was poured on a suction filter or other filtration equipment for the extraction and washing. The paste was then dried and heat-treated at 800-900°C for 10-11 hours [2].
Conclusion
In this paper we describe the production of rare-earth manganites different methods. Based on scanning electron microscopy shows that the methods of chemistry mortar synthesize powders of the desired product nanosize particle dispersion (20 - 60 nm), which is not provided with ceramic technology (100 nm). The best method is co-precipitation. It is based on the coprecipitation of nitrate solutions of the corresponding metal complex precipitant.
This method gives the chemistry mortar material powders of rare earth perovskite manganite most legkosinteziruemye (800 °C • 11 hr.; 900 °C • 10 hr.) A mixture prepared by mechanically require significantly higher temperatures and duration of the synthesis. Sleep perovskite structure ceramic batch can be prepared at 1300 ° C • h 8 (synthesis as a powder) and at 1000 ° C • 12 hours., 1300 ° C • 6 hr. (synthesis as pellets).
Detailed consideration of the physical and chemical processes can control the properties of the finished product and intensify the technology, while providing the optimum combination of chemical and electrical properties at the lowest energy cost.
This work will be finished by January 2014, with the meterialy to contact me or my scientific supervisor – Yuriy Prilipko.
References
- Нагаев Э.Л. Манганиты лантана и другие магнитные проводники с гигантским магнитосопротивлением // Успехи физических наук. - 1996. - Т. 166. - № 8. - С. 833-858.
- Прилипко Ю.С. Взаимосвязь между условиями получения и свойствами редкоземельных манганитоперовскитов // Наукові праці ДонНТУ. Серія: Хімія і хім. технологія. – 2011. – В.17(187). – С: 171-175.
- Прилипко Ю.С. Функциональная керамика. Оптимизация технологии: монография. – Донецк: Норд-Пресс, 2007. – 492с.
- Труханов С.В. Особенности магнитного состояния в системе La0.7Sr0.3MnO3-у (0<у<0.25) / С.В. Труханов // ЖЭТФ - 2005 - Т. 127, вып .1- С. 107-119.
- Белоус А.Г. Влияние химического состава и температуры спекания на структуру твердых растворов Lai-xSrxMn03±Y / А.Г. Белоус, О.И. Вьюнов, Е.В. Пашкова и др. // Неорганические материалы- 2003 — Т. 39, № 2 - С.212-222.
- Товстолиткнін О.I. Структура та магніто резистивні властивості полікристалічних зразків (La1-уNdy)1-xSrxMn03 / 0 .І. Товстолиткін, Щ.І. В’юнов, К.П. Данільченко, А.Г. Білоус // Укр. Ф1з. Журн - 2004.-Т.49, №9 - С.906-911.
- Добровицкий В.В. Гигантское магнитосопротивление, спин- переориентационные переходы и макроскопические квантовые явления в магнитных наноструктурах / В.В. Добровицкий, А.К. Звездин, А.Ф. Попков // УФН.-1996- Т. 166, №4, С. 439-447.