Реферат за темою випускної роботи
Зміст
- Вступ
- 1. Актуальність теми
- 2. Мета дослідження
- 3. Значення та застосування динасових вогнетривів
- 4. Фізико-хімічні основи виробництва
- 5. Вплив домішок на властивості динасових вогнетривів
- 6. Технологія виробництва динасових вогнетривів
- 6.1 Сировинні матеріали
- 6.2 Підготовка сировини
- 6.3 Пресування динасових виробів
- 6.4 Сушка динасу
- 6.5 Випал динасу
- 7. Експериментальна частина
- Перелік посилань
Вступ
Вогнетривка галузь відіграє суттєву роль в гірничо-металургійному комплексі, який займає стратегічно важливе місце в економіці України. Але в процесі ринкових реформ вогнетривкі підприємства зіткнулись з загальними для економіки проблемами кризового характеру. Саме ця галузь гостро потребує впровадження у виробництво сучасних технологічних рішень, забезпечуючи підвищення конкурентоспроможності вогнетривкої продукції на світовому ринку при зниженні використання енергії, сировини і матеріалів.
Вогнетривка промисловість посідає важливе місце серед базових галузей промисловості Донецької області. На сьогодні їх частка складає приблизно 5 відсотків від загального обсягу виробництва промислової продукції в області і у перспективі вона буде зростати.
Стратегія розвитку вогнетривкої промисловості заснована на інноваційно-інвестиційній моделі наково технічного прогресу і є подальшою конкретизацією відповідних розділів Програми науково-технічного розвитку
. Пріоритетними напрямками є:
- Оновлення обладнання вогнетривкого виробництва, заміна морально та фізично зношеного обладнання на підприємствах з виробництва вогнетривів;
- Розробка нових видів вогнетривів, легковагих виробів з низькою теплопровідністю для металургійних агрегатів, зокрема ля доменних печей та нагрівачів повітря, шиберних затворів, машин безперервного лиття;
- Подальше впровадження стратегії технічного переозброєння кар’єрів з видобутку вогнетривкої сировини;
- Удосконалення технології виробництва динасових вогнетривів, розширення номенклатури вробів.
Динасом називають вогнетривкий матеріал, що містить не менш, ніж 93 % кремнезему. Динасові вироби складаються із тридиміту, кристобаліту, остаточного кварцу, скла змінного складу, кристалічних силікатів кальцію. Від хімічного й мінералогічного складу динасу залежать його вогнетривкість, міцність, непроникність. Основним сировинним матеріалом для виробництва динасу є кристалічні кварцити. В якості мінералізаторів зазвичай використовують додатки оксиду кальцію. Під час випалу сирцю відбуваються складні фізико-хімічні процеси, що супроводжуються модифікаційними перетвореннями кварцу в тридиміт і кристобаліт, необоротним розширенням динасового сирцю та інші. Особливістю випалу динасу є те, що процес спікання динасу відбувається без ущільнення, а навпаки найчастіше із збільшенням пористості. Динас зміцнюється при випалі завдяки перетворенням, що протікають під час перекристалізації (утворення кристалічного зростку тридиміту), і реакціям диоксиду кремнію з мінералізаторами.
Динас серед вогнетривких матеріалів має цілком заслужено переважне значення завдяки його кращій будівельній міцності при високих темпертурах. Динас – один з небагатьох традиційних вогнетривких матеріалів, який зберігає свою міцність і вогнестійкість, не розм'якшуючись до температури свого плавлення вище 1700 °С.
1. Актуальність теми
Екологічна ситуація в Донецькій області оцінюється фахівцями як критична. Наш регіон є великим промисловим центром України з розвиненою важкою індустрією, який на протязі багатьох років тримає основний курс на здобування вугілля, металу та інших енергетичних і матеріальних ресурсів. Екологічна обстановка в області ускладнюється наявністю великої кількості відходів, особливо токсичних. На даний час у Донецькій області накопичено більш, ніж 4 млрд. тонн промислових відходів. Площа земель, що зайняті відходами, наближується до 2 % території області. Найбільшими постачальниками промислових відходів є вугільна, гірничодобувна, хімічна, металургійна та енергетична галузі промисловості.
З одного боку, ці відходи є одним з джерел екологічних проблем, а з другого боку, вони вміщують цінні компоненти та можуть бути потенціальною вторинною сировиною. Але в силу того, що технологічні процеси здійснюються таким чином, щоб забезпечити оптимальні параметри виробництва основної продукції, побічні матеріали мають нестабільний склад, не сортуються, складуються та зберігаються без урахування можливого наступного використання. Тому роботи, в яких досліджується можливість використання цих відходів як ресурсів вторинної сировини для виробництва скломатеріалів, керамічних, будівельних, вогнетривких виробів, можна вважати актуальними. Такий підхід не тільки розширює мінерально-сировинну базу промисловості, але й дозволяє забезпечити екологічну безпеку.
В Донецькій області розташована більшість вогнетривких заводів України. Основним завданням вогнетривкої промисловості сьогодні є підвищення якості вітчизняних матеріалів і виробів до рівня світових стандартів, що зробить їх конкурентноспроможними.
У теперішній час суттєво підвищились вимоги до будівельних, керамічних і вогнетривких матеріалів. Науковий прогрес потребує створення нових видів виробів з новими властивостями і високими показниками, що може бути досягнуто шляхом використання додатків.
2. Мета дослідження
Метою даної роботи було дослідження можливості отримання динасових виробів з використанням різноманітних додатків.
3. Значення та застосування динасових вогнетривів
З другої половини XVІІІ століття починається промисловий переворот, важливим результатом якого був активний розвиток в області металургії, будівництва, виробництва кераміки та ін.
Для футеровки доменної, цементовипалювальної, скловарних, коксових печей, які працюють при високих температурах, були потрібні вогнетриви.
Динасові цеглини з'явилися в 1820 році у Англії (Уєльс), завдяки розробкам В. Юнга, що додав в пісок невеликі дози вапна, що сприяло процесу спеканія. З 1899 року активно починає розвиватися виробництво кремнеземистих (динасових) на вапняній зв'язці і бокситових цеглин.
Динас отримав свою назву від імені чистої кварцовою породи, з якої він вперше був виготовлений. Сполучною речовиною для кварцових зерен тоді було застосоване вапно.
Динас серед вогнетривких матеріалів має цілком заслужено переважне значення, завдяки його кращої будівельної міцності при високих темпертурах.
Динас – один з небагатьох традиційних вогнетривких матеріалів, який зберігає свою міцність і вогнестійкість, не розм'якшуючись до температури свого плавлення вище 1700 °С .
Він знаходить досить широке застосування (рис. 3.1) у печах кольорової металургії, в скляній промисловості, де його використовують для кладки верхньої будови ванних скловарних, а також горшкових печей[9].
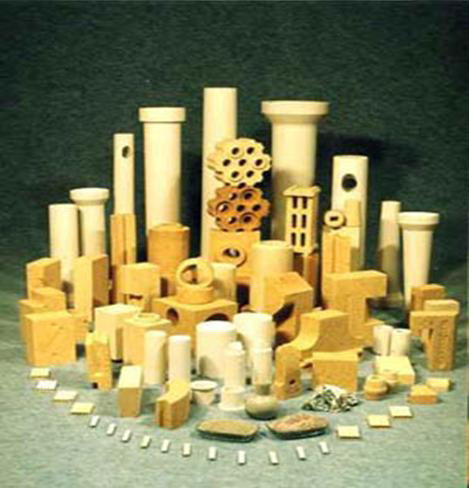
Рисунок 3.1 – Динасові вогнетриви
Динас широко використовують для будівництва коксових печей [11]. Відсутність додаткової усадки, висока температура деформації і достатня термічна стійкість легковагого динасу дозволяють використовувати його для стінової кладки і перекриття розпірних склепінь великих пічних прольотів високотемпературних печей. Також легковагий динас застосовують для футеровки кришок нагрівачів. Він працює в різноманітних печах для нагріву металу і для тигельної плавки кольорових металів на машинобудівничих заводах. Він застосовується як для кладки малого робочого простору так і для великовантажних камерних печей для нагріву великих силікатів.
Крім металургії та машинобудування, він може знайти широке застосування в керамічній промисловості і промисловості будівельних матеріалів. В численних високотемпературних печах, у яких застосування легковагої динасу для робочої футеровки виключається за температурними або інших причин, він може бути використаний як дешевий теплоізоляційний вогнетрив в шарі, розташований безпосередньо за робочою футеровкою. Зокрема, динасовий легковаговик застосовують для ізоляції склепінь скловарних печей і підвісних головних склепінь мартенівських печей.
4. Фізико-хімічні основи виробництва
Кремнезем відомий в одній аморфній і семи основних кристалічних модифікаціях[9]. Аморфною являється кварцове скло; кристалічними – β-кварц, α-кварц, γ-тридиміт, β-тридиміт, α-тридиміт, β-кристобаліт, α-кристобаліт. На рисунку 4.1 приведена схема перетворення одних кристалічних модифікацій кремнезему в інші по Феннеру. На осі абсцис відкладені температури, а на ординат в довільному масштабі – тиск пари модифікацій двооксиду кремнію.
Відповідно до основних положень хімічної термодинаміки прийнято вважати, що чим вище парціальний тиск, тим менш стійка речовина.
β-кварц – двооксид кремнію SiO2, в природі в основному знаходиться у вигляді β-кварцу, який зустрічається у формі кварцового піску, кварцитів, гірського кришталю, пісковиків, домішки в глинах і каолінах і у вигляді складової частини багатьох вивержених порід.
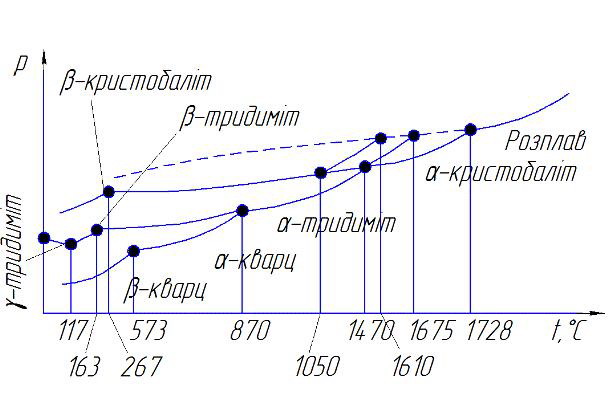
Рисунок 4.1 – Діаграмма Феннера
При 573 °С β-кварц повністю і швидко переходить в α-кварц і вище цієї температури не існує. При охолодженні α-кварц повністю переходить назад в β-кварц.
Чистий α-кварц (при відсутності мінералізаторів) при 1300-1450 °С (при середній температурі 1050 °С; переходить через проміжний метакристобаліт в α-кристобаліт. У присутності відповідних мінералізаторів α-кварц переходить в α-тридиміт безпосередньо в інтервалі 1200-1470 °С; з великою швидкістю цей перехід відбувається при температурі вище 1300 °С.
α-тридиміт в природі не зустрічається, тому що при охолодженні він швидко і повністю переходить в β-тридиміт, а останній – в γ-тридиміт. При температурах вище області його стійкості, тобто> 1470 °С, α-тридиміт існує в нестійкому стані аж до розплавлення при 1675 °С. В інтервалі 1470-1675 °С α-тридиміт повільно переходить в α-кристобаліт.
β-тридиміт є проміжною модифікацією, яка існує в інтервалі 117-163 °С.
γ-тридиміт, хоча і є нестійкою модифікацією, існує при звичайних температурах протягом необмеженого часу.
α-кристобаліт стійкий в інтервалі 1470-1728 °С і при 1728 °С плавиться. При температурі нижче 1470 °С α-кристобаліт нестійкий аж до 267 °С, коли він переходить в β-кристобаліт.
β-кристобаліт, хоча і є нестійкою модифікацією, подібно до γ-тридиміту може існувати при звичайних температурах невизначено довго і зустрічається (рідко) в природі. При нагріванні в інтервалі 180-270 °С β-кристобаліт швидко переходить в α-кристобаліт.
Розплавлений кремнезем може бути охолоджений без переходу в кристалічну фазу [9]. В цьому випадку виходить кварцове скло. При нагріванні кварцового скла до 1200 °С воно легко кристалізується у формі кристобаліту; при добавці Na2O кварцове скло можна закрісталлізувати у формі тридиміту.Останнім часом відкриті нові модифікації кременезема. При високій температурі він дисоціює на SiO і кисень, які при зниженні температури в особливих умовах конденсації за відсутності парів води утворюють нову модифікацію SiO2 з щільністю 1,98. Особливістю цієї модифікації є волокниста форма кристалів.
Піддаючи звичайне кварцове скло високому тиску (до сотень тисяч атмосфер) при одночасному впливі на нього високої температури, можна отримати нову модифікацію SiO2 – важкий кремнезем з щільністю 3,01. Відомі й інші модифікації SіO2[10].
Для технології динасу ці нові модифікації кремнезему ролі не грають.
У разі чистого кремнезему (сума домішок менше 0,01%) тридиміт не є самостійною фазою, він утворюється лише в присутності мінералізаторів і містить не менше 0,1% лужних оксидів. У зв'язку з цим в діаграму Феннера були внесені відповідні корективи (рисунок 4.2).
Чистий α-кварц при нагріванні до 1400-1450 °С переходить в аморфну фазу змінної щільності і в розплав, а також частково в кристобаліт, утворючий при 1728 °С розплав. Досить однорідне скло виходить лише при 1850-1950 °С. Точка кипіння кварцового розплаву умовно приймається 2800 °C (PSiO2= 102 кПа).
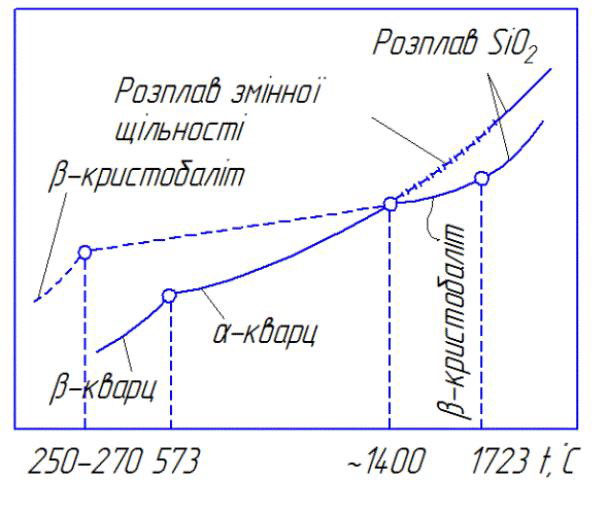
Рисунок 4.2 – Діаграмма стану SiO2 по Прянішникову
5. Вплив домішок на властивості динасових вогнетривів
Відомими вченими проведено ряд досліджень щодо вибору мінералізаторів. Tsigler та ін [2] у своїй роботі для збільшення фази трідіміта використовували гіпс, відходи від випалу піриту і конвертерні шлаки. Turchinova та інші [3] застосовували піритові золи в дослідженні їх впливу на динасову цеглу. Bulakh та ін. [6] для поліпшення термічної стабільності та збільшення розмірів кристалів трідіміта використовували хромівую руду, хроміт-переклазовий бій і карбід кремнію. Дослідники також використовували суху добавку [4]вапнякового порошку разом з оксидом заліза для проведення екологічно чистого виробництва динасової цегли. Khonchik та ін [5] використовували вапняк, доменний шлак і відходи фосфогіпсу, що призводило до зменшення вмісту залишкового кварцу і підвищенню вмісту трідіміта. P>
Роботи, проведені відомими дослідниками в минулому, свідчать про вивчення різних типів мінералізаторів. Однак робіт з дослідження впливу введення металевих добавок на динасовий цегла було небагато. Мінералізатори в металевій формі не досліджувалися зовсім. P>
У роботі Р. Картік, А. Баннерджі та ін [5] для вивчення перетворень, що проходять в динасовому матеріалі, а також його властивостей, в нього, була введена різна кількість металевих добавок; був зроблений порівняльний аналіз його властивостей з матеріалом динасу без металевих добавок. Динасовий цегла піддавався випалу в тунельної печі при температурі 1430 ± 10 °С протягом 24-30 ч. Дослідження показало, що чим вищий вміст металевої добавки, тим сильніше ущільнення структури завдяки зменшенню пористості і збільшення уявної щільності. Тенденція до тріщин у динасового цеглі пов'язана з режимом його охолодження в печі. Було відзначено, що при збереженні одного і того ж режиму охолодження трещинообразование зменшується зі збільшенням вмісту металевої добавки. Оборотне теплове розширення цегли до температури 1000 ° С помітно зменшувалася в порівнянні з цеглою, що не містить металевої добавки. Також зазначалося, що сильне теплове розширення знижується зі збільшенням кількості металевої добавки. Для визначення фазового складу обпаленої матеріалу вивчалася його мікроструктура і проводився рентгенофазового аналіз. P>
У розробках С. Селвараджи, С. Адака, Р.К.[4] Синха та ін. зроблені спроби поліпшення термомеханічних властивостей динасового вогнетрива шляхом введення в матрицю вторинної фази, такої як SiC.
У якості вихідних матеріалів використовувалися високоякісний промисловий кварцит (0-2,8 мм), кварцова борошно (-0,09 мм) і (-0,10 мм) з хімічним складом, наведеним у табл. 1. У складах зразків використовували вапняну суспензію, вапняний порошок і гематитової порошок в якості мінералізатора, і декстринового суспензію в якості зв'язки. При розрахунку складів враховувалися два основні фактори: (а) розмір зерна і (б) хімічний склад. P>
Усі вихідні матеріали змішували при кімнатній температурі стандартним промисловим способом. Після змішування цеглини формувалися за допомогою гідравлічного преса під тиском 0,5 т/см2 , відпресовані зразки висушували у відповідності зі стандартною кривою «температура – час» до температури 110 °С протягом 24 год в тунельної сушарці . Після сушіння зразки спікається в тунельної печі при 1430 °С з витримкою 35 ч.
Були виготовлені шість серій зразків цеглин з різною кількістю добавки SiС для подальшого визначення їх фізичних і механо-хімічних властивостей після випалу у відповідність зі стандартами 150 при відборі трьох зразків для кожної температури випалу. p>
Кварцит | Кварцове борошно | SiC | |
SiO2 | |||
Al2O | |||
Fe2O3 | |||
CaO | |||
Na2O | |||
K2O | |||
Втрати при прокалюванні | |||
SiC | |||
MgO | |||
Si+SiO2 |
Дослідження показало у зразках, що містять більш ніж 5 мас. % SiС, спостерігалося утворення «чорної серцевини» в результаті окислення SiС в процесі випалу з утворенням SiO 2 і СО. З дифрактограм обпаленої цегли зробили висновок, що основними кристалічними фазами є трідіміт і кристобалит з невеликою кількістю залишкового кварцу. Кількість залишкового кварцу збільшується зі збільшенням кількості добавки SiС. Збільшення істинної щільності матеріалу з добавкою SіС пояснюється, зокрема, збільшенням вмісту залишкового кварцу і більш високою щільністю SiС. Напівкількісна оцінка фаз показала, що добавка SiС посилює утворення трідіміта. Із збільшенням вмісту SiС величина ДН збільшилася з 1550 ° С до більш ніж 1650 ° С. Із збільшенням вмісту SiC швидкість повзучості знижувалася через присутність SiC на межзеренних кордонах, що протидіяло ковзанню зерен в процесі деформації. Величини теплопровідності і ГППР підвищуються з підвищенням вмісту SiC через високу щільність, що здається і теплопровідність SiC. Теплове розширення цегли, що містить SiC, було менше в порівнянні з таким для звичайного динасового цегли. P>
У статті В.Я. Грінберга, Є.А. Гімпельмана [2] наводяться результати дослідження впливу мінералізючий добавок на міцність динасу. Для виготовлення зразків використовували кристаллічний кварцит з 98,1% SiО 2 , який застосовується на Первоуральському динасовому заводі для виробництва коксового динасу.
У пошукових експериментах змінними були добавки: вапняно-залізиста суміш (ВЗС), ТiO2, А1203, MgO, S. Ці добавки були обрані з метою отримання сіталлообразої структури зв'язки, яка б дозволила поліпшити механічні властивості динасу [2]. В результаті проведених дослідів з'ясувалося, що при вмісті ВЗС менше 2,2% і більше 3,2% (за СаО) міцність динасу знижується, а в зазначених межах практично не впливає на неї. Тому в подальших дослідах зміст ВЗС було постійним (2,6% по Сао).
В основних лабораторних експериментах досліджуваними добавками служили ТiO2, А1203, MgO, S. В якості характеристики міцності динасу приймалась межа міцності при стисненні.
Після проведенних досідів можна зробити висновок, що введення домішок ТiO2 і S в кварцову основу дозволяє збільшити міцність динасових виробів, у той час як введення А1203 і MgO знижує її.
Максимальне значення межі міцності при стиску, досягається при вмісті добавок ТiO2 1,5% і S 0,5% і дорівнює 75,9 МПа.
Випущена промислова партія коксових динасових виробів з добавками портландцементу і ТiO2. Межа міцності при стисненні виробів склала 80 МПа.
6. Технологія виробництва динасових вогнетривів
6.1 Сировинні матеріали
Основною сировиною для виробництва динасу служать кварцити або кварцові пісковики. Кварцити і пісковики – це породи осадового походження , рідше магматичного. Кварцити і пісковики близькі, але кварцити відрізняються більш щільною будовою.
Найважливішою сировиною , яку використовують у масовому виробництві динасових вогнетривів є кристалічні кварцити.
При виготовленні динасових мас в них вводять невеликі кількості мінералізуючих добавок.
Мінералізатори – добавки , які спеціально вводяться в шихту, які служать для зв'язування кварцових зерен виробів в монолітну масу, для прискорення переродження кварцу в тридиміт і кристобаліт, для впливу на процеси мінералоутворення в бажаному напрямку.
Як мінералізатор найчастіше використовується вапно, тобто іони кальцію.
Другий мінералізатор - залізовмісні добавки, наприклад, залізна окалина (80% FeО, 10-11% Fe2О3, 6-7% SiO2 і домішки Al2О3), пірит або піритні огарки (50% Fe2О3, 27?28% FeO, 13-14% SіО2, 7-8% Al2О3).
Крім мінералізуючих добавок в динасову масу вводять ЛСТ, в перерахунку на суху ЛСТ – 0,5-1%) .
В еспериментальній частині було дослідженно вплив мікрокремнезему на властивості динасових вогнетривів.
Мікрокремнезем є побічним продуктом металургійного виробництва при виплавці феросіліцію і його сплавів, що утворюються в результаті відновлення вуглецем кварцу в електропечах. В процессі виплавки кремнієвих сплавів деяка частина монооксиду кремнію переходить в газоподібний стан і після окислення і конденсації утворює надзвичайно дрібний продукт у вигляді кулястих часток з високим вмістом аморфного кремнезему [10].
6.2 Підготовка сировини
Кварцити зазвичай надходять на динасові заводи в шматках розміром 50-300 мм в поперечнику.
Для дроблення кварциту на I ступені застосовують дробарки з розмірами зіва 1200X1500X150 мм, на II ступені дроблення застосовують або щекові дробарки, або конусні. Після дроблення кварцит при найбільшому розмірі шматків 60 мм містить 10-20% фракцій менше 10 мм. Зі збільшенням твердості кварцитів вміст цих фракцій зменшується. Дрібний помел кварцитів частіше роблять на бігунах з масою ковзанок 5-7 т або короткоконусними дробарками. Розмелений кварцит надходить на розсів.
Динасова шихта складається з суміші сухих порошків кварцитів різних фракцій. До складу шихти іноді, вводять також динасовий бій. Добавка динасового бою сприяє зменшенню зростання виробів під час випалення і, отже, знижує напруги, що виникають в них при випалюванні. Однак динасовий бій зменшує вогнетривкість, тому його вводять лише в шихту коксових фасонних виробів, вогнетривкість яких допускається більш низькою. Динасова маса складається з суміші зволоженої шихти з мінералізаторамита іншими добавками. Вміст у масі минерализуючої добавки, що містить вапно, характеризує її лужність. Зерновий склад маси робить вирішальний вплив на процес переродження кварцу, щільність виробів при температурах випалу та експлуатації.
Вапно вводять в масу зазвичай у вигляді вапняного молока, з яких надходить і вся вода, необхідна для зволоження [7].
Динасова маса непластична, і міцність сирцю, отриманого з неї навіть при великих тисках, низька. Вапно зв'язує зерна кварциту повільно, і достатню зміцнення сирцю відбувається тільки після його сушіння. З метою підвищення міцності свіжесформованого сирцю вводять клеючі органічні добавки, які вигоряють при випалюванні і не надають шкідливого впливу на властивості готових виробів.
В якості такої добавки може буди сульфітно-спиртова барда.
В якості клеючої добавки можна застосовувати меласу(цукрова патока) 0,2-0,5 %. Недоліком меласи є її здібність розріджувати свіжесформовану динасову масу.
6.3 Пресування динасових виробів
Динас пресують на механічних пресах під тиском 25-60 МПа. Для отримання щільного динасу і сирцю з міцністю, що дозволяє безпосередню садку його на пічну вагонетку тунельну, тиск пресування має становити близько 100 МПа.
Задовільне пресування мас на механічних ричажних пресах досягається при відношенні товщини виробів до гідравлічного радіусу в межах 0,65-0,85.
На ступінь пресованої маси впливає склад мінералізуючих добавок. Зі зменшенням вмісту в масі вапняного молока, пресування погіршується. Покращєння пресування спостерігається при введенні вапняно-глинистою добавки (1,5% СаО +0,5 А12О3), середня-при введенні вапняної добавки (2% СаО) і найгірша - при введенні залізно-вапняної добавки (1,6% FeO +0 , 4% СаО). Вилежування динасових мас погіршує їх пресування.
Розміри пресових форм внаслідок зростання динасу при випалюванні приймають на 2-3,5% менше розмірів готових виробів.
6.4 Сушка динасу
Динасовий сирець сушать у тунельних сушилах. Джерелом тепла служать димові гази чи гаряче повітря, яке відбирається з печей або отримане від калориметра.
6.5 Випал динасу
При випалюванні динасу відбуваються наступні найбільш важливі процеси:
1. взаємодія SiO2 і СаО з отриманням силікатів кальцію, які утворюють з силікатами оксиду заліза FeO тверді розчини;
2. розширення динасового сирцю в результаті поліморфних перетворень кремнезему;
3. утворення розплаву складного складу, розчинення в ньому кварцу і випадіння з пересичені розплаву (перекристалізація) тридиміта;
4. зміни механічної міцності динасу.
Спікання динасу при випаленні відбувається без ущільнення, частіше з розпушенням і збільшенням пористості;
Невелика кількість вологи, що залишилася в сирці після сушки, віддаляється в інтервалі 100-200 °С [6]. При 450 °С починається помітне розкладання Са (ОН) г, що закінчується при 560 °С. При цьому механічна міцність сирцю падає. При 573 °С відбувається перехід β-кварцу в α-кварц. Цей перехід, як показала практика, не викликає в сирці великих внутрішніх напружень і не небезпечний для його міцності.
Міцність динасу в інтервалі 600-700 °С внаслідок реакції між СаО і SiO2 з утворенням 2CaO-SiO2 і деякої кількості 3CaO-SiO2 дещо підвищується. В інтервлі 800-1100 °С при взаємодії силікатів кальцію з тонкозернистим кремнеземом утворюється псевдоволластоніт α – CaO – SiO2; починаючи з 1000-1100 °С повільно відбувається перехід α – кварцу в α – кристобаліт відповідно до правила Оствальда . При цьому у виробах також не виникає великих внутрішніх напружень, здатних викликати утворення тріщин.
При 1100-1350 °С незворотні перетворення кварцу в модифікації з низькою щільністю відбуваються інтенсивніше. У цьому інтервалі з'являється рідка фаза , за участю якої в процесі перекристалізації починається кристалізація тридиміта; вироби при цьому збільшуються в об’ємі, міцність їх трохи зменшується. Для попередження утворення тріщин на виробах швидкість підйому температури в інтервалі 1100-1350 °С слід знижувати.
Випалення в інтервалі 1350-1430 °С необхідно вести дуже обережно, так як швидкість переродження кварцу і зростання динасу в цьому інтервалі значно збільшуються. При великій швидкості підйому температури, особливо в окислювальному середовищі, відбувається інший механізм переродження, а сааме α – кварц переходить переважно в α – кристобаліт. Відбувається так зване сухе переродження динасу, на виробах при цьому з'являється багато тріщин, і міцність їх різко знижується. При підйомі температури з малою швидкістю, в присутності мінералізаторів і при слабо відновлювальної середовищі в печі «сухого» переродження, не відбувається. Відновлювальна атмосфера в печі усуває можливість місцевого допалювання палива в обсязі садки, робить його більш «м'яким» і, переводячи оксид заліза в закис, знижує в'язкість силікатного розплаву і тим самим у великій мірі усуває внутрішні напруги в випалювальному сирці. Велика швидкість підйому температури вище 1350 °С чинить негативний вплив на рівномірність розподілу температури в обсязі садки.
Витримка при кінцевій температурі випалу необхідна для завершення перекристалізації кварцовою маси і вирівнювання температур в об’ємі печі. Вона залежить від виду виробів, що випалюються, вихідної сировини і типу печі. У великих періодичних печах витримка при випалюванні коксового динасу становить не менше 40 ч.
Охолодження динасу до 400 °С слід проводити в можливо короткий термін, нижче 400 °С і особливо в інтервалі 300-100 °С повільно, так як при цьому відбуваються швидкі оборотні перетворення α, β – кристобалта зі зменшенням об’єму на 2,8 %.
На кожному заводі динас слід обпалювати по температурної кривої, яка встановлюється дослідним шляхом для кожного типу печі в залежності від якості сировини (кварцитів і мінералізаторів) та асортименту виробів.
Основним видом печі для випалення динасу служить тунельна піч.
7. Експериментальна частина
Для проведення досліджень виготовляли зразки на основі заводської динасової маси з додаванням мікрокремнезему, відпрацьованих графітових електродів та кварцового піску з високим вмістом кремнезему. В якості мінералізуючих додатків застосовували оксид кальцію у вигляді вапняного молока і оксида заліза у вигляді концентрату залізорудного. Кварцовий пісок додавали з ціллю покращення хімічного складу динасу, тобто підвищення вмісту кремнезему.
Була зроблена спроба додаткового введення вуглецю у вигляді відпрацьованих графітових електродів з ціллю створення відновлювального середовища при випалі, що у свою чергу сприяє більш інтенсивному утворенню тридиміту, підвищений вміст якого у виробах є переважним.
В роботі також проведені дослідження з метою отримання динасових легковагових вогнетривів з добавкою мікрокремнезема, які виготовляли методом додатків, що вигорають. В якості останніх використовували кокс (30 % у шихті).
Зразки формували із маси з відносною вологістю 7,5-8 % напівсухим пресуванням у металевих формах діаметром і висотою 30 мм під тиском 25-30 МПа. Випал здійснювали в лабораторній електричній печі при максимальній температурі 1430 °С за кривою випалу, яка відрізнялася від умов виробництва більш високою швидкістю підйому та зниження температури. Після випалу зразки динасу випробували за стандартними методиками для визначення водопоглинання, щільності, відкритої пористості, межи міцності при стиску. У таблиці 7.1 наведені отримані результати (кожне значення є середньою арифметичною величиною із трьох паралельних).
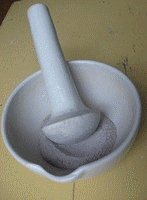
Рисунок 7.1 – Технологічний процес виготовлення кспериментальних зразків (анімація, 8 кадрів, 154 Кбайт, 10 циклів)