Реферат по теме выпускной работы
Содержание
- Введение
- 1. Актуальность темы
- 2. Цель и задачи исследования, планируемые результаты
- 3. Значение и применение динасоых огнеупоров
- 4. Физико-химические основы производства
- 5. Влияние добавок на свойства динасовых огнеупоров
- 6. Технология произодства динасовых онеупоров
- 6.1 Сырьевые материалы
- 6.2 Подготовка сырья
- 6.3 Прессование динасовых изделий
- 6.4 Сушка динаса
- 6.5 Обжиг динаса
- 7. Экспериментальная часть
- Выводы
- Список источников
Введение
Огнеупорная промышленность играет существенную роль в горно-металлургическом комплексе, который занимает стратегически важное место в экономике Украины. Но в процессе рыночных реформ огнеупорные предприятия столкнулись с общими для экономики проблемами кризисного характера. Именно эта отрасль остро нуждается во внедрении в производство современных технологических решений, обеспечивая повышение конкурентоспособности огнеупорной продукции на мировом рынке при снижении использования энергии, сырья и материалов. P>
Огнеупорная промышленность занимает важное место среди базовых отраслей промышленности Донецкой области. На сегодня их доля составляет примерно 5 процентов от общего объема производства промышленной продукции в области и в перспективе будет возрастать.
Стратегия развития огнеупорной промышленности основана на инновационно-инвестиционной модели научно-технического прогресса и является дальнейшей конкретизацией соответствующих разделов «Программы научно-технического развития» Приоритетными направлениями являются:
1. Обновление оборудования огнеупорного производства, замена морально и физически изношенного оборудования на предприятиях по производству огнеупоров;
2. Разработка новых видов огнеупоров, легковесных изделий с низкой теплопроводностью для металлургических агрегатов, в частности для доменных печей и воздухонагревателей, шиберных затворов, машин непрерывного литья;
3. Дальнейшее внедрение стратегии технического перевооружения карьеров по добыче огнеупорного сырья;
4. Совершенствование технологии производства динасовых огнеупоров, расширение номенклатуры изделий.
Динасом называют огнеупорный материал, содержащий не менее 93% кремнезема. Динасовые изделия состоят из тридимита, кристобалита, остаточного кварца, стекла переменного состава, кристаллических силикатов кальция. От химического и минералогического состава динаса зависят его огнеупорность, прочность, непроницаемость. Основным сырьевым материалом для производства динаса являются кристаллические кварциты. В качестве минерализатора обычно используют добавки оксида кальция. При обжиге сырца происходят сложные физико-химические процессы, сопровождающиеся модификационными преобразованиями кварца в тридимит и кристобалит, необратимым расширением динасового сырца и другие. Особенностью обжига динаса является то, что процесс спекания динаса происходит без уплотнения, а наоборот чаще с увеличением пористости. Динас упрочняется при обжиге благодаря преобразованиям, протекающих при перекристаллизации (образование кристаллического сростка тридимита), и реакции диоксида кремния с минерализаторами.
Динас среди огнеупорных материалов имеет вполне заслуженно преимущественное значение благодаря его лучшей строительной прочности при высоких температурах. Динас – один из немногих традиционных огнеупорных материалов, который сохраняет свою прочность и огнеупорность, не размягчаясь до температуры своего плавления выше 1700 °С.
1. Актуальность темы
Экологическая ситуация в Донецкой области оценивается специалистами как критическая. Наш регион является крупным промышленным центром Украины с развитой тяжелой индустрией, который на протяжении многих лет держит основной курс на получение угля, металла и других энергетических и материальных ресурсов. Экологическая обстановка в области осложняется наличием большого количества отходов, особенно токсичных. В настоящее время в Донецкой области накоплено более 4 млрд. тонн промышленных отходов. Площадь земель, занятых отходами, приближается к 2% территории области. Крупнейшими поставщиками промышленных отходов является угольная, горнодобывающая, химическая, металлургическая и энергетическая отрасли промышленности.
С одной стороны, эти отходы являются одним из источников экологических проблем, а с другой стороны, они содержат ценные компоненты и могут быть потенциальной вторичным сырьем. Но в силу того, что технологические процессы осуществляются таким образом, чтобы обеспечить оптимальные параметры производства основной продукции, побочные материалы имеют нестабильный состав, не сортируются, складируются и хранятся без учета возможного последующего использования. Поэтому работы, в которых исследуется возможность использования этих отходов как ресурсов вторичного сырья для производства стекломатериалов, керамических, строительных, огнеупорных изделий, можно считать актуальными. Такой подход не только расширяет минерально-сырьевую базу промышленности, но и позволяет обеспечить экологическую безопасность.
В Донецкой области расположено большинство огнеупорных заводов Украины. Основной задачей огнеупорной промышленности сегодня является повышение качества отечественных материалов и изделий до уровня мировых стандартов, что сделает их конкурентоспособными.
В настоящее время существенно повысились требования к строительным, керамическим и огнеупорным материалам. Научный прогресс требует создания новых видов изделий с новыми свойствами и высокими показателями, что может быть достигнуто путем использования добавок.
2. Цель исследования
Целью данной работы было исследование возможности получения динасовых изделий с использованием различныхдобавок.
3. Значение и применение динасовых огнеупоров
Со второй половины XVIII века начинается промышленный переворот, важным результатом которого было активное развитие в области металлургии, строительства, производства керамики и др.
Для футеровки доменных, стекловаренных, коксовых печей, работающих при высоких температурах, требовались огнеупоры.
Динасовый кирпич появился в 1820 году в Англии (Уельс), благодаря разработкам В. Юнга, который добавил в песок небольшие дозы извести, что способствовало процессу спекания. С 1899 года активно начинает развиваться производство кремнеземистых (динасовых) на известковой связке и бокситовых кирпичей.
Динас получил свое название от имени чистой кварцевой породы, из которой он впервые был изготовлен. Связующим веществом для кварцевых зерен тогда была применена известь.
Динас среди огнеупорных материалов имеет вполне заслуженно преобладающее значение, благодаря его лучшей строительной прочности при высоких темпертурах.
Динас – один из немногих традиционных огнеупорных материалов, который сохраняет свою прочность и огнеупоность, не размягчаясь до температуры своего плавления выше 1700 °С.
Он находит достаточно широкое применение (рис. 3.1) в печах цветной металлургии, в стекольной промышленности, где его используют для кладки верхнего строения ванных стекловаренных, а также горшечных печей [9].
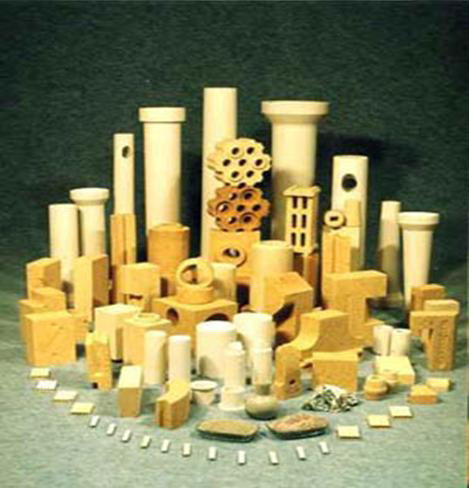
Рисунок 3.1 - Динасовые огнеупоры
Динас широко используют для строительства коксовых печей [11]. Отсутствие дополнительной усадки, высокая температура деформации и достаточная термическая устойчивость легковесного динаса позволяют использовать его для стеновой кладки и перекрытия распорных сводов больших печных пролетов высокотемпературных печей. Также легковесный динас применяют для футеровки крышек нагревателей. Он работает в различных печах для нагрева металла и для тигельной плавки цветных металлов на машиностроителных заводах. Он применяется как для кладки малого рабочего пространства, так и большегрузных камерных печей для нагрева больших силикатов.
Помимо металлургии и машиностроения, он может найти широкое применение в производстве керамики и промышленности строительных материалов. В многочисленных высокотемпературных печах, в которых применение легковесного динаса для рабочей футеровки исключается по температурным или иным причинам, он может быть использован как дешевый теплоизоляционный огнеупор в слое, расположенный непосредственно за рабочей футеровкой. В частности, динасовый легковес применяют для изоляции сводов стекловаренных печей и подвесных главных сводов мартеновских печей.
4. Физико-химические основы производства
Кремнезем известен в одной аморфной и семи основных кристаллических модификациях [9]. Аморфной является кварцевое стекло; кристаллическими - β-кварц, α-кварц, γ-тридимит, β-тридимит, α-тридимит, β-кристобалит, α-кристобалит. На рисунке 4.1 приведена схема преобразования одних кристаллических модификаций кремнезема в другие по Феннеру. На оси абсцисс отложены температуры, а на ординат в произвольном масштабе – давление пара модификаций диоксида кремния.
соответствии с основными положениями химической термодинамики принято считать, что чем выше парциальное давление, тем менее стойкое вещество.
β-кварц – диоксид кремния SiO2, в природе в основном находится в виде β-кварца, который встречается в форме кварцевого песка, кварцитов, горного хрусталя, песчаников, примеси в глинах и каолинах и в виде составной части многих изверженных пород.
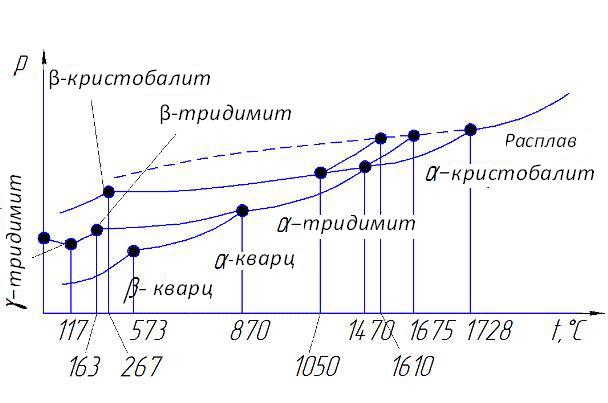
Рисунок 4.1 – Диаграмма Феннера
При 573 °С β-кварц полностью и быстро переходит в α-кварц и выше этой температуры существует. При охлаждении α-кварц полностью переходит обратно в β-кварц.
Чистый α-кварц (при отсутствии минерализато) при 1300-1450 °С (при средней температуре 1050 °С; переходит через промежуточный метакристобалит в α-кристобалит. В присутствии соответствующих минерализато α-кварц переходит в α-тридимит непосредственно в интервале 1200-1470 °С, с большой скоростью этот переход происходит при температуре выше 1300 °С.
α-тридимит в природе не встречается, так как при охлаждении он быстро и полностью переходит в β-тридимит, а последний - в γ-тридимит. При температурах выше области его устойчивости, т.е.> 1470 °С, α-тридимит существует в неустойчивом состоянии до расплавления при 1675 °С. В интервале 1470-1675 °С α-тридимит медленно переходит в α-кристобалит.
β-тридимит является промежуточной модификацией, которая существует в интервале 117-163 °С.
γ-тридимит, хотя и является неустойчивой модификацией, существует при обычных температурах в течение неограниченного времени.
α-кристобалит устойчив в интервале 1470-1728 °С и при 1728 °С плавится. При температуре ниже 1470 °С α-кристобалит неустойчивый до 267 °С, когда он переходит в β-кристобалит.
β-кристобалит, хотя и является неустойчивой модификацией, подобно γ-тридимита может существовать при обычных температурах неопределенно долго и встречается (редко) в природе. При нагревании в интервале 180-270 °С β-кристобалит быстро переходит в α-кристобалит.
Расплавленный кремнезем может быть охлажден без перехода в кристаллическую фазу [9]. В этом случае получается кварцевое стекло. При нагревании кварцевого стекла до 1200 °С оно легко кристаллизуется в форме кристобалита, при добавке Na2 O кварцевое стекло можно закристаллизовать в форме тридимита.
В случае чистого кремнезема (сумма примесей менее 0,01%) тридимит не является самостоятельной фазой, он образуется только в присутствии минерализато и содержит не менее 0,1% щелочных оксидов. В связи с этим в диаграмму Феннера были внесены соответствующие коррективы (рисунок 4.2).
Чистый α-кварц при нагревании до 1400-1450 °С переходит в аморфную фазу переменной плотности и в расплав, а также частично в кристобалит, утворючий при 1728 °С расплав. Достаточно однородное стекло получается лишь при 1850-1950 °С. Точка кипения кварцевого расплава условно принимается 2800 °°C (PSiO2 = 102 кПа).
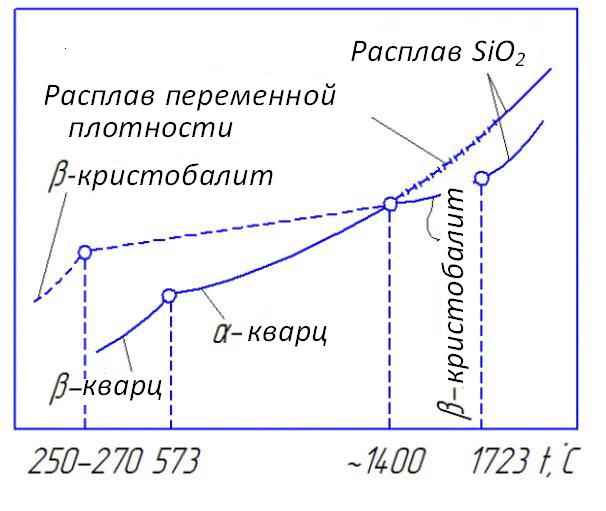
Рисунок 4.2 – Диаграмма состояния SiO 2 по Прянишникову
5. Влияние добавок на свойства динасовых огнеупоров
Известными учеными проведен ряд исследований по выбору минерализато. Tsigler и др. [2] в своей работе для увеличения фазы тридимита использовали гипс, отходы обжига пирита и конвертерный шлак. Turchinova и другие [3] применяли пиритовые золы в исследовании их влияния на динасового кирпич. Bulakh и др.. [6] для улучшения термической стабильности и увеличения размеров кристаллов тридимита использовали хромивую руду, хромит-переклазовий бой и карбид кремния. Исследователи также использовали сухую добавку [4] известнякового порошка вместе с оксидом железа для проведения экологически чистого производства динасового кирпича. Khonchik и др. [5] использовали известняк, доменный шлак и отходы фосфогипса, что приводило к уменьшению содержания остаточного кварца и повышению содержания тридимита.
Работы, проведенные известными исследователями в прошлом, свидетельствуют об изучении различных типов минерализато. Однако работ по исследованию влияния введения металлических добавок на динасовый кирпич было немного. Минерализатором в металлической форме не исследовались вовсе.
В работе Р. Картик, А. Баннерджи и др. [5] для изучения преобразований, проходящих в динасового материале, а также его свойств, в него, была введена разное количество металлических добавок; был произведен сравнительный анализ его свойств с материалом динаса без металлических добавок. Динасовый кирпич подвергался обжигу в туннельной печи при температуре 1430 ± 10 °С в течение 24-30 ч. Исследование показало, что чем выше содержание металлической добавки, тем сильнее уплотнение структуры благодаря уменьшению пористости и увеличения кажущейся плотности. Тенденция к трещинам в динасового кирпиче связана с режимом его охлаждения в печи. Было отмечено, что при сохранении одного и того же режима охлаждения трещинообразование уменьшается с увеличением содержания металлической добавки. Оборотное тепловое расширение кирпича до температуры 1000 °С заметно уменьшалась по сравнению с кирпичом, не содержит металлической добавки. Также отмечалось, что сильное тепловое расширение снижается с увеличением количества металлической добавки. Для определения фазового состава обожженной материала изучалась его микроструктура и проводился рентгенофазовый анализ.
В разработках С. Селвараджы, С. Адака, Р.К. Синха и др.[4] предприняты попытки улучшения термомеханических свойств динасового огнеупоров путем введения в матрицу вторичной фазы, такой как SiC.
В качестве исходных материалов использовались высококачественный промышленный кварцит (0-2,8 мм), кварцевая мука (-0,09 мм ) и (-0,10 мм) с химическим составом, приведенным в табл. 1. В составах образцов использовали известковую суспензию, известковый порошок и гематитовой порошок в качестве минерализатора, и декстринового суспензию в качестве связи. При расчете составов учитывались два основных фактора: (а) размер зерна и (б) химический состав.
Все исходные материалы смешивали при комнатной температуре стандартным промышленным способом. После смешивания кирпича формировались с помощью гидравлического пресса под давлением 0,5 т/см2, отпрессованные образцы высушивали в соответствии со стандартной кривой «температура - время» до температуры 110 ° С в течение 24 ч в туннельной сушилке. После сушки образцы спекается в туннельной печи при 1430 °С с выдержкой 35 ч.
Были изготовлены шесть серий образцов кирпичей с разным количеством добавки SiС для дальнейшего определения их физических и механо-химических свойств после обжига в соответствии со стандартами 150 при отборе трех образцов для каждой температуры обжига.
Кварцит | Кварцевая мука | SiC | |
SiO2 | |||
Al2O | |||
Fe2O3 | |||
CaO | |||
Na2O | |||
K2O | |||
Потери при прокаливании | |||
SiC | |||
MgO | |||
Si+SiO2 |
Исследование показало в образцах, содержащих более 5 масс. % SiС, наблюдалось образование «черной сердцевины" в результате окисления SiС в процессе обжига с образованием SiO2 и СО. С дифрактограмм обожженного кирпича сделали вывод, что основными кристаллическими фазами являются тридимит и кристобалит с небольшим количеством остаточного кварца. Количество остаточного кварца увеличивается с увеличением количества добавки SiС. Увеличение истинной плотности материала с добавкой SиС объясняется, в частности, увеличением содержания остаточного кварца и более высокой плотностью SiС. Полуколичественная оценка фаз показала, что добавка SiС усиливает образование тридимита. С увеличением содержания SiС величина ДО увеличилась с 1550 °С до более чем 1650 °С. С увеличением содержания SiC скорость ползучести снижалась из-за присутствия SiC на межзеренных границах, противодействовало скольжение зерен в процессе деформации. Величины теплопроводности и ГППР повышаются с повышением содержания SiC из-за высокой плотности, что кажется и теплопроводность SiC. Тепловое расширение кирпича, содержащий SiC, было меньше по сравнению с таковым для обычного динасового кирпича.
В статье В.Я. Гринберга, Е.А. Гимпельмана [2] приводятся результаты исследования влияния минерализючий добавок на прочность динаса. Для изготовления образцов использовали кристалличний кварцит с 98,1% SiО 2, который применяется на Первоуральский динасовый заводе для производства коксового динаса.
В поисковых экспериментах переменными были добавки: известково-железистая смесь (ВЗС), ТiO2, А1203, MgO, S . Эти добавки были выбраны с целью получения ситаллообразои структуры связи, которая позволила улучшить механические свойства динаса. В результате проведенных опытов выяснилось, что при содержании ВЗС менее 2,2% и более 3,2% (по СаО) прочность динаса снижается, а в указанных пределах практически не влияет на нее. Поэтому в дальнейших опытах содержание ВЗС было постоянным (2,6% по СаО).
В основных лабораторных экспериментах исследуемыми добавками служили ТiO2, А1203, MgO, S. В качестве характеристики прочности динаса принималась предел прочности при сжатии.
После проведенных исследований можно сделать вывод, что введение примесей ТiO2 и S в кварцевую основу позволяет увеличить прочность динасовых изделий, в то время как введение А1203 и MgO снижает ее.
Максимальное значение предела прочности при сжатии, достигается при содержании добавок ТiO2 1,5% и S 0,5% и равна 75,9 МПа.
Выпущена промышленная партия коксовых динасовых изделий с добавками портландцемента и ТiO2. Предел прочности при сжатии изделий составила 80 МПа.
6. Технология производства динасовых огнеупоров
6.1 Сырьевые материалы
Основным сырьем для производства динаса служат кварциты или кварцевые песчаники.
Важнейшей сырьем, которое используется в массовом производстве динасовых огнеупоров является кристаллические кварциты.
При изготовлении динасовых масс в них вводят небольшие количества минерализующих добавок.
Минерализаторы - добавки, которые специально вводятся в шихту, которые служат для связывания кварцевых зерен изделий в монолитную массу, для ускорения перерождения кварца в тридимит и кристобалит, для воздействия на процессы минералообразования в желаемом направлении.
Как минерализатор чаще используется известь, т.е. ионы кальция.
Второй минерализатор - железосодержащие добавки, например, железная окалина (80% FeО, 10-11% Fe2О3, 6-7% SiO2 и примеси Al2О3), пирит или пиритные огарки (50% Fe2O3 27-28% FeO, 13-14% SиО2, 7-8% Al2О3).
Кроме минерализующих добавок в динасового массу вводят ЛСТ, в пересчете на сухое ЛСТ - 0,5-1%).
В експериментальнoй части было исследовано влияние микрокремнезема на свойства динасовых огнеупоров.
Микрокремнезем является побочным продуктом металлургического производства при выплавке ферросилиция и его сплавов, образующихся в результате восстановления углеродом кварца в электропечах. В процессе выплавки кремниевых сплавов некоторая часть монооксида кремния переходит в газообразное состояние и после окисления и конденсации образует чрезвычайно мелкий продукт в виде шарообразных частиц с высоким содержанием аморфного кремнезема [ 10].
6.2 Подготовка сырья
Кварциты обычно поступают на динасовые заводы в кусках размером 50-300 мм в поперечнике.
Для дробления кварцита на I ступени применяют дробилки с размерами зева 1200×1500×150 мм, на II ступени дробления применяют щековые дробилки или конусные. После дробления кварцит при наибольшем размере кусков 60 мм содержит 10-20% фракций менее 10 мм. С увеличением твердости кварцитов содержание этих фракций уменьшается. Размолотый кварцит поступает на рассев.
Динасового шихта состоит из смеси сухих порошков кварцитов различных фракций. В состав шихты иногда вводят также динасовый бой. Добавка динасового боя способствует уменьшению роста изделий при обжига и, следовательно, снижает напряжения, возникающие в них при обжиге. Однако динасовый бой уменьшает огнеупорность, поэтому его вводят только в шихту коксовых фасонных изделий, огнеупорность которых допускается более низкой. Динасового масса состоит из смеси влажной шихты с минерализаторами и другими добавками.
Известь вводят в массу обычно в виде известкового молока, из которых поступает и вся вода, необходимая для увлажнения [7].
динасового масса непластичная и прочность сырца, полученного из нее даже при больших давлениях, низкая. Известь связывает зерна кварцита медленно, и достаточное укрепление сырца происходит только после его сушки. С целью повышения прочности свижесформованого сырца вводят клеящие органические добавки, выгорают при обжиге и не оказывают вредного воздействия на свойства готовых изделий.
В качестве такой добавки может буди сульфитно-спиртовая барда.
В качестве клеящей добавки можно применять мелассы (сахарная патока) 0,2-0,5%. Недостатком мелассы является ее способность разжижать свижесформовану динасового массу.
6.3 Прессование динасовых изделий
Динас формуют только полусухим прессованием на механических прессах под давлением 25-60 МПа.
На степень прессованной массы влияет состав минерализующих добавок. С уменьшением содержания в массе известкового молока, прессования ухудшается. Улучшение прессования наблюдается при введении известково-глинистой добавки (1,5% СаО +0,5 А12О3). Вылеживание динасовых масс ухудшает их прессование.
Размеры прессовых форм вследствие роста динаса при обжиге принимают на 2-3,5% меньше размеров готовых изделий.
6.4 Сушка динаса
Динасовый сырец сушат в туннельных сушилах. Источником тепла служат дымовые газы или горячий воздух, который отбирается из печей или полученный от калориметра.
6.5 Обжиг динаса
При обжиге динаса происходят следующие наиболее важные процессы:
1. взаимодействие SiO2 и СаО с получением силикатов кальция, которые образуют с силикатами оксида железа FeO твердые растворы;
2. расширение динасового сырца в результате полиморфных превращений кремнезема;
3. образования расплава сложного состава, растворение в нем кварца и выпадения из пересыщенного расплава (перекристаллизация) Тридимит;
4. изменения механической прочности динаса.
Спекание динаса при обжиге происходит без уплотнения, чаще с разрыхлением и увеличением пористости
Небольшое количество влаги, оставшейся в сырце после сушки, удаляется в интервале 100-200 °С [6]. При 450 °С начинается заметное разложение Са (ОН) г, что оканчивается 560 °°С. При этом механическая прочность сырца падает. При 573 °С происходит переход β-кварца в α-кварц. Этот переход, как показала практика, не вызывает в сырце больших внутренних напряжений и не опасен для его прочности.
Прочность динаса в интервале 600-700 °С вследствие реакции между СаО и SiO2 с образованием 2CaO-SiO2 и некоторого количества 3CaO-SiO2 несколько повышается. В интервли 800-1100 °С при взаимодействии силикатов кальция с тонкозернистыми кремнеземом образуется Псевдоволластонит α-CaO-SiO2; начиная с 1000-1100 °С медленно происходит переход α-кварца в α-кристобалит согласно правилу Оствальда. При этом в изделиях также не возникает больших внутренних напряжений, способных вызвать образование трещин.
При 1100-1350 °С необратимые преобразования кварца в модификации с низкой плотностью происходят интенсивнее. В этом интервале появляется жидкая фаза, при участии которого в процессе перекристаллизации начинается кристаллизация Тридимит, изделия при этом увеличиваются в объеме, прочность их несколько уменьшается. Для предупреждения образования трещин на изделиях скорость подъема температуры в интервале 1100-1350 °С следует снижать.
Обжиг в интервале 1350-1430 °С необходимо вести очень осторожно, так как скорость перерождения кварца и рост динаса в этом интервале значительно увеличиваются. При большой скорости подъема температуры, особенно в окислительной среде, происходит другой механизм перерождения, а именно из α-кварц переходит преимущественно в α-кристобалит. Происходит так называемое сухое перерождение динаса, на изделиях при этом появляется много трещин, и прочность их резко снижается. При подъеме температуры с малой скоростью, в присутствии минерализато и при слабо восстановительной среде в печи «сухого» перерождения, не происходит. Восстановительная атмосфера в печи устраняет возможность местного дожигания топлива в объеме сады, делает его более «мягким» и, переводя оксид железа в закись, снижает вязкость силикатного расплава и тем самым в значительной степени устраняет внутренние напряжения в обжиговой сырце. Большая скорость подъема температуры выше 1350 ° С оказывает отрицательное влияние на равномерность распределения температуры в объеме сады. P>
Выдержка при конечной температуре обжига необходима для завершения перекристаллизации кварцевой массы и выравнивание температур в объеме печи. Она зависит от вида изделий, выгорают, исходного сырья и типа печи. В крупных периодических печах выдержка при обжиге коксового динаса составляет не менее 40 ч.
Охлаждение динаса до 400 °С следует проводить в возможно короткий срок, ниже 400 °С и особенно в интервале 300-100 °С медленно, так как при этом происходят быстрые оборотные преобразования α, β - кристобалта с уменьшением объема на 2,8%.
На каждом заводе динас следует обжигать по температурной кривой, устанавливается опытным путем для каждого типа печи в зависимости от качества сырья (кварцитов и минерализато) и ассортимента изделий.
Основным видом печи для обжига динаса служит туннельная печь.
7. Экспериментальная часть
Для проведения исследований изготовляли образцы на основе заводской динасового массы с добавлением микрокремнезема отработанных графитовых электродов и кварцевого песка с высоким содержанием кремнезема. В качестве минерализующих добавок применяли оксид кальция в виде известкового молока и оксид железа в виде концентрата железорудного. Кварцевый песок добавляли с целью улучшения химического состава динаса, т.е. повышение содержания кремнезема.
Была сделана попытка дополнительного введения углерода в виде отработанных графитовых электродов с целью создания восстановительного среды при обжиге, что в свою очередь способствует более интенсивному образованию тридимита, повышенное содержание которого в изделиях является предпочтительным.
В работе также проведены исследования с целью получения динасовых легковесных огнеупоров с добавкой микрокремнезема, которые изготавливали методом выгорающих добавок. В качестве последних использовали кокс (30% в шихте).
Образцы формировали из массы с влажностью 7,5-8% полусухим прессованием в металлических формах диаметром и высотой 30 мм под давлением 25-30 МПа. Обжиг проводили в лабораторной электрической печи при максимальной температуре 1430 °С по кривой обжига, отличавшейся от условий производства более высокой скоростью подъема и снижения температуры. После обжига образцы динаса испытали по стандартным методикам для определения водопоглощения, плотности, открытой пористости, между прочности при сжатии. В таблице 7.1 приведены полученные результаты (каждое значение является средней арифметической величиной с трех параллельных). Технологический процесс изготовления экспериментальных образцов представлен на рисунке 7.1
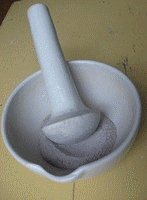
Рисунок 7.1 – Технологический процесс изготовления экспериментальных образцов (анимация, 8 кадров, 154 Кбайт, 10 циклов)