Реферат за темою випускної роботи
При написанні даного реферату магістерська робота ще не завершена. Остаточне завершення: січень 2014 року. Повний текст роботи та матеріали по темі можуть бути отримані у автора або його керівника після зазначеної дати.
ЗМІСТ
- Вступ
- 1. Актуальність теми
- 2. Мета і завдання дослідження
- 3. Класифікація тонкостінних виробів
- 4. Дослідження особливостей застосування ультразвуку для механічної обробки тонкостінних циліндричних виробів
- 5. Конструкторська частина
- Попередні висновки
- Список використаної літератури
ВСТУП
В наш час все більша увага приділяється розвитку і вдосконаленню обробки виробів зі зніманням відносно невеликих шарів металу і створення на поверхні і в поверхневому шарі необхідних фізико-механічних властивостей і шорсткості.
Постійний розвиток техніки на сучасному етапі вимагає використання деталей, які мають тонкі стінки (з метою економії матеріалу і полегшення конструкції в цілому). Зараз їх кількість значно збільшується в загальній масі деталей, що піддаються механічній обробці. Тонкостінні труби, як і оболонкові конструкції, забезпечуючи високу щільність компонування, знаходять широке застосування в самих різних галузях промисловості і, що особливо важливо, у відповідальних областях: нафтовидобувної, літако- і ракетобудуванні, кріогенної техніки і холодильних установках, космічних і військово - промислових розробках.
Рішення проблеми зниження металоємності виробів призвело до появи всезростаючого числа деталей, входять у ці вироби. Вони характеризуються як нежорсткі, одну з основних груп яких складають тонкостінні циліндричні деталі.
У світовій практиці металообробки розроблено велику кількість методів обробки. За своєю сутністю вони ускладнилися. Інтенсивність протікання процесів руйнування, деформування, перетворення матеріалу деталей значно зросла. У розробці та вдосконаленні методів обробки має місце тенденція одночасного впливу на оброблювані заготовки і деталі механічних навантажень і хімічних речовин, теплового або магнітного полів, електричної та променевої енергії, енергії елементарних частинок і т.д. в різному їх поєднанні.
Накопичений досвід показує, що не існує універсальних методів обробки деталей з різних конструкційних матеріалів, так як кожен має свою конкретну область раціонального застосування. Технолог і конструктор повинні вибрати високоефективний метод обробки з великого числа можливих або створити на основі їх суміщення комбінований метод виготовлення деталі.
В даний час у всіх провідних галузях машинобудування все в більших масштабах застосовують високоенергетичні і комбіновані методи обробки матеріалів. Ці методи розвиваються швидкими темпами не тільки в силу своєї відносної молодості, наявності запасу ще не реалізованих ідей і можливостей, універсальності використовуваних енергоносіїв, а й головним чином завдяки розвитку сучасного машинобудування.
1. АКТУАЛЬНІСТЬ РОБОТИ
У процесі різання оброблювана деталь і ріжуча кромка інструменту здійснюють пружні коливання. Тому для досягнення особливо високої точності обробки необхідно не тільки проводити статичний аналіз взаємного розташування оброблюваної деталі та інструменту (що безпосередньо впливає на точність обробки), а й певною мірою аналізувати коливальну систему верстат-пристосування-інструмент-оброблювана деталь динамічно, тобто в ході коливань.
Якщо на додаток до сили різання, що змінюється з високою частотою за синусоїдальним законом, з'являється ще одна складова, близька по своїй частоті до частоти власних коливань інструменту або оброблюваної деталі, то можуть виникнути биття, що знижують точність обробки. При цьому може створитися таке положення, що обробка взагалі виявиться неможливою. При звичайному різанні прийнято вважати, що практично всі коливальні явища небажані. У всіх навчальних посібниках вказано, що необхідно використовувати такі режими різання, при яких не виникають коливання. При цьому звернуто увагу на те, що обробка деталі не повинна проводитися в низькочастотній області коливань, де амплітуда досить велика і може спостерігатися помітне тремтіння оброблюваної деталі та інструмента. Проте вже давно давалися рекомендації проводити обробку з накладенням високочастотних коливань, зокрема ультразвукових.
У ході вивчення цього відносно нового методу обробки було встановлено, що він є одним з перспективних методів обробки майбутнього, і це було пов'язано з його особливостями:
- істотне зниження сил різання при обробці;
- усунення наросту;
- забезпечення доступу СОТС в зону різання;
- зниження висоти мікронерівності обробленої поверхні в кілька разів порівняно з обробкою, на однакових режимах, без ультразвукових коливань інструменту;
- зниження до мінімуму або відсутність залишкових напруг на обробленій поверхні після застосування ультразвукової технології;
- зниження контактного тертя.
Одночасно із збільшенням кількості тонкостінних труб підвищуються і технічні вимоги до точності розмірів поверхонь, форми та їх взаємного розташування. У прецизійному машинобудуванні допуски становлять близько мікрометрів. Відомі рішення з отримання труб методами пластичного деформування. Для отримання циліндричних виробів підвищеної точності успішно застосовується розкатування. Але неможливість обробки отворів складної конфігурації, так само складність конструкції, що тягне за собою ускладнену технологію виготовлення розкатки, її підвищену собівартість і знижену надійність. З’являється питання про доцільність застосування розкатування, і доводитися вдаватися до різання. Різання по своїй сутності менш продуктивно, ніж пластичне деформування, так як формоутворення відбувається не в обсязі заготовки, а по її поверхні. При обробці різанням геометрично можлива точність формоутворення знижується внаслідок прояву технологічної спадковості і власне похибок точіння. Практика показує, що при інтенсифікації режимів різання зазвичай погіршується точність обробки, виникають інтенсивні вібрації.
Тому розробка способів і засобів, що забезпечують задану точність вихідних параметрів тонкостінних циліндричних виробів і знижують трудомісткість їх виготовлення, є актуальною науковою задачею.
2. МЕТА І ЗАВДАННЯ ДОСЛІДЖЕННЯ
Метою даної роботи є підвищення якості виробів машинобудування на основі спеціальних композиційних технологій, шляхом розробки загального підходу їх створення, що базується на композиції особливостей синтезу різних варіантів технологій, в якій кількість напрямків підвищення якості виробів визначається числом варіантів технологій, що входять до складу композиційної технології.
Для досягнення зазначеної мети в магістерській роботі були поставлені такі завдання:
- Створення лабораторного стенду для вивчення механізмів ультразвукового впливу на процес різання. Визначення позитивних і негативних факторів застосування ультразвукового точіння. Визначення факторів, здатних позитивно впливати на процес ультразвукового точіння.
- Дослідження впливу ультразвукового впливу при точінні на якість поверхні та поверхневого шару, на формування стружки.
- Дослідження динамічних характеристик пружної системи ультразвукової установки.
- Дослідження впливу ультразвукового впливу на стійкість різального інструменту, вивчення природи цього впливу, визначення шляхів підвищення стійкості інструменту при УЗ впливі на процес різання.
- Вибір раціональних режимів обробки з метою мінімізації залишкових деформацій тонкостінних виробів.
- Визначення деформуючої здатності технологічних залишкових напружень при обробці точінням тонкостінних циліндричних виробів складного поверхневого обриси з метою управління їх залишковими деформаціями.
3. КЛАСИФІКАЦІЯ ТОНКОСТІННИХ ВИРОБІВ
Для виконання синтезу технологічного процесу повинна бути певна база даних, з якої можна було б проводити вибір необхідних варіантів рішень або відносити одержувані рішення до якого-небудь класу об'єктів. При всьому цьому зміст бази даних має бути підпорядковане певним законам, а розташування технологічних об'єктів повинно виконуватися за деякими закономірностям. Ця проблема вирішується за допомогою класифікації тонкостінних виробів.
При проектуванні технологічних процесів визначення загальних властивостей об'єктів допомагає знайти загальні принципи, які призводять до простішого проекту технології виготовлення тонкостінних виробів. На сьогоднішній день поки не розроблені строгі методи класифікації і немає загальних правил, що дозволяють виділяти класи та об'єкти. Однак, класифікуючи, ми об'єднуємо в одну групу об'єкти, що мають однакову будову і поведінку. Розумна класифікація, безсумнівно, частина будь якої точної науки [1,5].
Класифікація тонкостінних виробів суттєво полегшує розуміння основної проблеми і подальший розвиток загального теоретичного підходу синтезу технологічного процесу комбінованої обробки тонкостінних виробів. Класифікація допомагає визначити узагальнену, спеціалізовану і збиральну ієрархію об'єктів і класів. Метою класифікації є знаходження загальних властивостей об'єктів і їх поведінки [1,6].
На рисунку 3.1 представлена класифікація виробів з тонкостінними поверхнями. Класифікація виробів здійснюється за такими ознаками:
- за видом виробу;
- за жорсткістю виробу;
- за призначенням;
- за товщиною стінок виробу;
- за типом внутрішніх порожнин;
- за видом виконуваних експлуатаційних функцій;
- за якістю поверхневого шару;
- за методами обробки;
- за ступенем прецизійності.
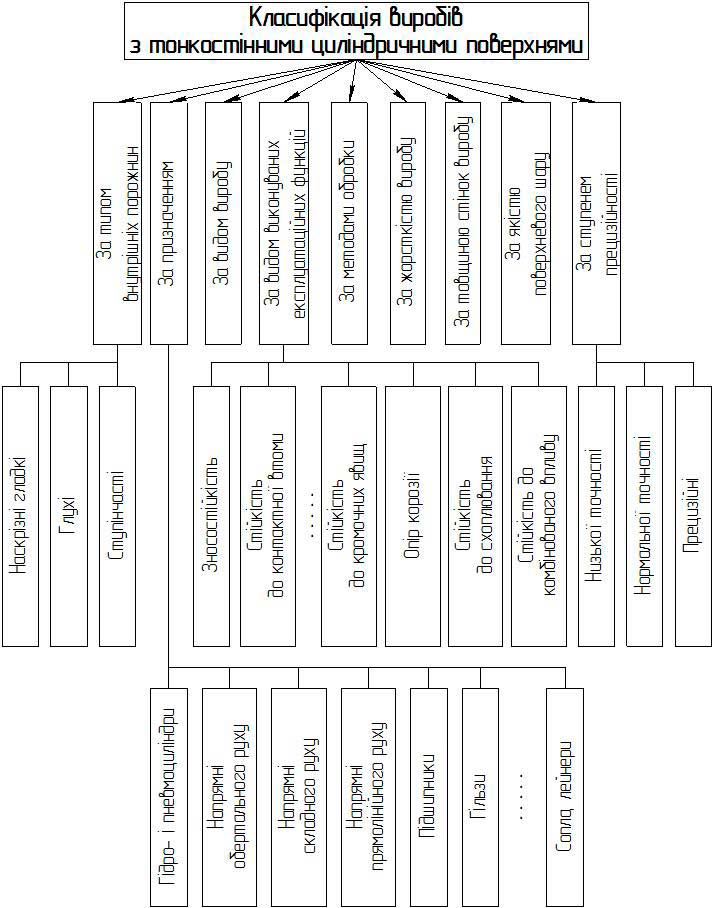
Рисунок 3.1 – Класифікація тонкостінних циліндричних виробів
По виду, вироби з тонкостінними циліндричними поверхнями поділяються таким чином: втулки і стакани; диски та кільця; циліндри і труби [1,7].
До дисків і кілець можна віднести такі вироби, в яких відношення висоти Н до діаметру D не перевищує значення Н/D≤0,5. При цьому для кілець відношення зовнішнього D до внутрішнього d діаметру не повинно перевищувати наступного значення D/d≤2,0. Для втулок і склянок значення відношення висоти до діаметра знаходиться в наступних межах 0,5 < Н/D ≤ 2,0. Циліндри і труби мають відношення висоти до діаметра, яке перевищує значення Н/D > 2,0.
За жорсткістю, вироби з циліндричними поверхнями поділяються на такі: жорсткі, нормальної жорсткості і нежорсткі.
До жорстких можна віднести такі вироби, на деформацію яких не впливають сили закріплення у пристосуваннях при обробці. До нормально жорстких відносяться вироби, деформація яких від закріплення в пристосуванні при обробці знаходиться в межах допуску на обробку. Для нежорстких виробів необхідні спеціальні пристосування для забезпечення заданої жорсткості, так як без цих пристосувань можлива деформація вироби, що перевищує допуск на обробку.
За товщиною стінок, вироби з циліндричними поверхнями поділяються на вироби з товщиною стінок: 0,3 … 1,0 мм; 1,0 … 3,0 мм; 3,0 … 10,0 мм.
За типом внутрішніх порожнин, тонкостінні циліндричні вироби поділяються на такі: наскрізні гладкі, глухі і ступінчасті.
За ступенем прецизійності, тонкостінні циліндричні поверхні можуть бути наступні: низькою точності, нормальної точності, прецизійні.
За призначенням, тонкостінні циліндричні поверхні можна поділяти на: напрямні обертального, складного і прямолінійного рухів, гідро-і пневмоциліндри, підшипники, гільзи, сопла, лейнери та ін.
По виду виконуваних експлуатаційних функцій, тонкостінні циліндричні поверхні можуть реалізовувати наступні функції: стійкість до контактної втоми, зносостійкість, стійкість до кромочних явищ, опір корозії, стійкість до схоплювання, стійкість до комбінованого впливу та ін.
4. ДОСЛІДЖЕННЯ ОСОБЛИВОСТЕЙ ЗАСТОСУВАННЯ УЛЬТРАЗВУКУ ДЛЯ МЕХАНІЧНОЇ ОБРОБКИ ТОНКОСТІННИХ ЦИЛІНДРИЧНИХ ВИРОБІВ
Конструкції верстатів, призначені для механічної обробки, не можуть не допускати невеликих коливань оброблюваної деталі та інструменту, які утворюють свого роду коливальну систему. Загальним випадком є різання з накладенням вібрацій, при якому сили різання діють у вигляді імпульсів, а виділення тепла незначне. Звичайне різання, яке супроводжується виділенням тепла і обумовлено дією сил різання, що складаються з статичної постійної складової і накладеної на неї змінної складової (що змінюється за синусоїдальним законом), являє собою лише окремий випадок. Ці обставини необхідно враховувати при розгляді принципів точної обробки.
Вібраційне різання пов'язано з використанням спеціального обладнання, яке потребує вмілому поводження, що створює певні складності. Однак після відповідного налаштування такого обладнання надалі вже не потрібно особливо високої кваліфікації обслуговуючого персоналу. У такому випадку навіть при наявності лише низькокваліфікованих робітників можна налагодити безперервне виробництво деталей, що володіють малим розкидом розмірів і практично постійною точністю. Вібраційне різання дозволяє здійснювати точну обробку, використовуючи тільки точіння. При цьому можна точно обробити навіть матеріали, які раніше для отримання необхідної точності завжди піддавали шліфуванню. Роботи, які перш виконувалися, наприклад, на дорогих шліфувальних верстатах (круглошліфувальних, плоскошліфувальних, внутрішліфувальних і т. п.), при вібраційному різанні виявляються непотрібними. Таким чином, вібраційне різання має цілу низку переваг, які дозволяють знизити трудомісткість робіт і матеріальні витрати.
До особливостей застосування ультразвуку при механічній обробці тонкостінних циліндричних виробів можна віднести:
- зменшення опору різання;
- підвищення точності обробки;
- кімнатна температура різання;
- виключення утворення наросту;
- при такій обробці не утворюються пластичні деформації і не виникають задирки;
- шорсткість одержуваної поверхні визначається тільки геометричними факторами;
- стружка сходить плавно;
- поліпшується змащуюча і охолоджуюча дія МОТС;
- у отримуваної поверхні відстані між мікронерівностями виявляються більш задовільними;
- поверхня може бути райдужною;
- підвищується зносостійкість;
- зростає корозійна стійкість;
- підвищується стійкість інструменту.
Всі перераховані переваги в тій чи іншій мірі можуть бути реалізовані при вібраційному різанні. Розглянемо вплив кожної з них більш докладно. Об'єктом розгляду є коливальна система, що має низьку частоту власних коливань, на яку діють імпульсні сили різання. Необхідно відзначити, що період цих сил і тривалість їх дії дуже малі. При проведенні досліджень вимірюють імпульсну силу різання, яка усереднюється і дає середню силу різання. Для вимірювань використовують експериментальну установку, де силу різання визначають за деформації пружного елемента, на який наклеєні тензометричні датчики. Можна вважати, що при вібраційному різанні абсолютне значення миттєвої сили різання або імпульсної сили різання має зменшуватися. При цьому середня сила різання буде в 3-10 разів менше развиваємої при звичайному різанні.
При вібраційному різанні, коли сили є імпульсними, у разі вмілого використання перехідної області динамічних характеристик коливальної системи верстата вдається створити такі умови, за яких пружні коливання як би призупиняються і переміщення стають статичними, а середня сила різання зменшується.
Підвищення точності обробки при вібраційному різанні відбуваються за рахунок коливання ріжучої кромки різця. При цьому протягом часу ріжуча кромка знаходиться в контакті з оброблюваної деталлю і утворюється стружка. Можна вважати, що за цей час положення ріжучої кромки (вершини різця) в процесі різання залишається незмінним. Коливання оброблюваної деталі теж як би припиняються. Це дозволяє підвищити точність обробки. Навіть при використанні різання з вібраціями в серійному виробництві розкид розмірів одержуваних деталей суттєво знижується. Вибірковий контроль показав, що навіть при малих глибинах різання (кілька мікрометрів) точність обробки зберігається на необхідному рівні тривалий час.
При імпульсному впливі сили в імпульсній формі виділяється і теплота в процесі різання. У цьому відношенні вібраційне різання істотно відрізняється від звичайного. При вібраційному різанні середня сила різання різко зменшується. У свою чергу, середня температура різання теж істотно знижується (приблизно до рівня кімнатної). При цьому на стружці не з'являються кольори мінливості, що спостерігається при звичайному різанні через окислення. Стружку, що утворилася після вібраційного різання, можна, не боячись обпектися, брати голими руками, що при звичайному різанні в загальному випадку немислимо.
Звичайне різання можна зіставити з пайкою, при якій нагрітий паяльник міцно притиснутий до деталі. Навпаки, при вібраційному різанні нагрів відбувається тільки в результаті постійних швидких переміщень паяльника вгору-вниз, при цьому пайку ніколи не вдалося б закінчити. При звичайному різанні суттєвою проблемою стає температура, що розвивається. Під дією цієї температури можуть відбуватися теплові деформації оброблюваної деталі, що погіршує точність обробки. Тим часом у разі вібраційного різання встановлюється, температура в більшості випадків не знижує точності.
Виключення утворення наросту. При вібраційному різанні не відбувається підвищення температури; стружка утворюється в області нестійкості коливальної системи різець - оброблювана деталь під час перехідного процесу. Тому навіть якщо й припустити, що існують деякі фактори, що стимулюють виникнення наросту на ріжучій кромці різця, то через короткочасність взаємодії схоплювання наросту з ріжучої кромкою не відбувається.
Таким способом можна здійснювати прецизійне різання тонкостінних виробів, які раніше зазвичай обробляли шліфуванням; вібруючим алмазним інструментом можна різати загартовані сталі. Можна сподіватися, що в перспективі замість шліфувальних верстатів для обробки (заточування) інструменту будуть використовуватися верстати з вібруючим ріжучим інструментом. На основі вібраційного принципу різання можна буде створити досить різноманітне нове верстатне обладнання [3].
5. КОНСТРУКТОРСЬКА ЧАСТИНА
В області ультразвукових частот, створюваних магнітострикційними вібраторами, здійснити вібраційну обробку без створення концентратора відповідної конструкції і вибору підходящої геометрії інструменту практично не вдається.
Для коливальних систем ріжучого інструменту з магнітострикційними вібраторами необхідно виконання наступних умов:
- коли інструмент закріплений на концентраторі, використовуваному для збільшення амплітуди коливань, необхідно, щоб досягався резонанс частот вібратора та інструменту;
- ріжучий інструмент повинен легко кріпитися до вібратора або концентратора і легко зніматися з них;
- для коливальної системи інструменту слід визначити координати вузлів коливань і кріпити інструмент до супорта саме в цих місцях;
- якщо коливальна система інструменту з'єднується з супортом у вузлах коливань на болтах, то необхідно підібрати такі конструкції, при яких частота власних коливань системи не змінювалася б [3].
Прості геометричні міркування показують, що при коливаннях вершини різця під кутом до напрямку його руху буде погіршуватися точність обробки, тобто коливання виявляться шкідливими. Тому існує три методи накладення коливань на інструмент:
- в напрямку осьової складової сили різання;
- в радіальному напрямку;
- в напрямку головної складової сили різання.
З урахуванням накладення коливань різного напрямку була спроектована установка, для накладення високочастотних коливань на інструмент в радіальному і тангенціальному напрямках, що показує її універсальність. Установка, яка зображена на малюнку 5.1, попередньо була спроектована в системі автоматизованого проектування SolidWorks і здійснювала тільки коливання в радіальному напрямку.
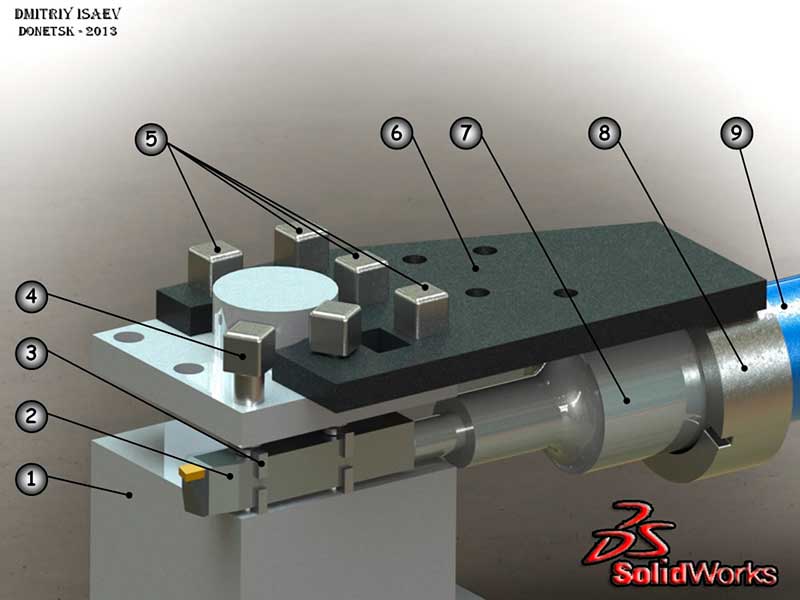
Рисунок 5.1 – Установка для радіального напряму коливань
(1- різцетримач;; 2 – різець; 3 – напрямні опори; 4 – гвинти М14; 5 – гвинти М14(укорочені); 6 – сталевий лист; 7 – концентратор ступінчастий; 8 – кільце; 9 – магнітострикційний перетворювач)
Установка складається з ступінчастого концентратора 7, до якого через шпильку прикріплюється різець 2. В кільце 8, приварене до листа 6, кріпиться по зовнішній різьбі магнітострикційний перетворювач 9. Концентратор з різцем кріпляться по внутрішній різьбі до перетворювача. Зібраний вузол встановлюють на різцетримач верстата 1 і закріплюють гвинтами 5. Згідно з раніше проведеними розрахунками, різець встановлюється в робоче положення між напрямними опорами 3 і підтискається гвинтами 4.
Досліди планується проводити на базі токарно-гвинторізного верстата моделі 1М61 [8]. Для даного типорозміру верстатів призначена спроектована установка, приклад роботи якої зображений на рисунку 5.2.
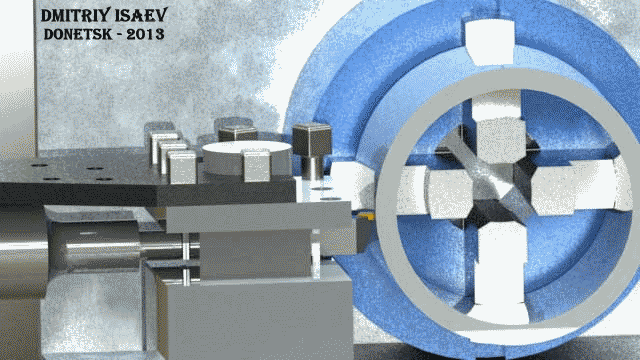
Рисунок 5.2 – Анiмацiйний приклад роботи установки для радіального накладення коливань, розроблений в SolidWorks(8 рисункiв, 22 кадри/с, объем - 507кб)
Відомо, що накладення тангенціальних високочастотних коливань на інструмент - більш перспективний напрямок досліджень, тому передбачаємо перенастроювання установки, як зображено на рисунку 5.3 для забезпечення тангенціальних коливань.
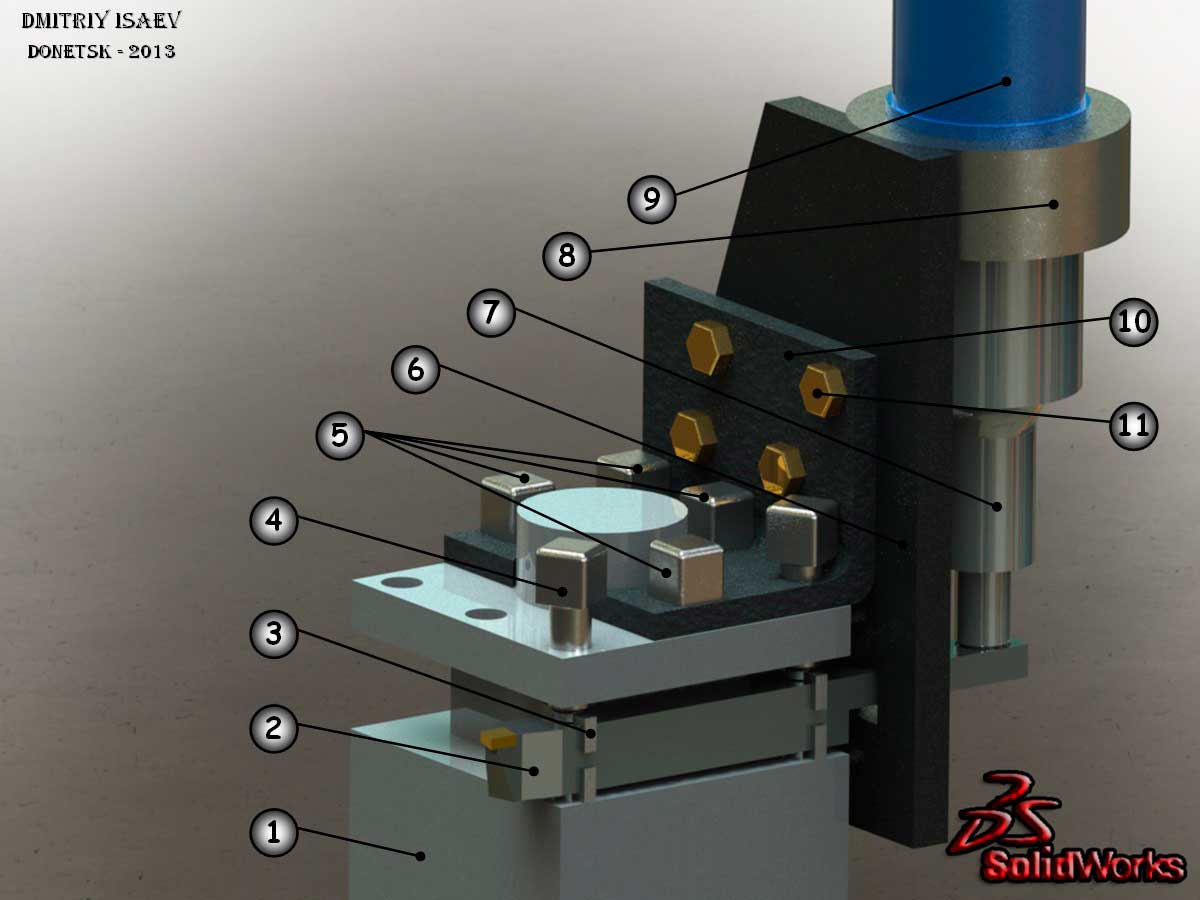
Рисунок 5.3 – Установка для тангенціального напряму коливань
(1- різцетримач; 2 – різець; 3 – напрямні опори; 4 – гвинти М14; 5 – гвинти М14(укорочені); 6 – сталевий лист; 7 – концентратор ступінчастий; 8 – кільце; 9 – магнітострикційний перетворювач; 10 – сталевий кут; 11 – гвинти М12)
Вузол, що складається з магнітострикційного перетворювача 9, кільця 8, ступінчастого концентратора 7 і сталевого листа 6 встановлюємо вертикально і закріплюємо гвинтами 11 до сталевого кута 10, який кріпиться до різцетримача 1 за допомогою гвинтів 5. Різець 2, що має подовжену хвостову частину, встановлюється в робоче положення і закріплюється гвинтами 4. Різець до концентратора кріпитися за допомогою шпильки.
Далі перетворювач підключається до ультразвукового генератору (в даному випадку - моделі УЗГ1-1), який перетворюватиме електричну енергію промислової частоти в електричну енергію ультразвукової частоти [9]. Так як перетворювач в ході роботи нагрівається - передбачено підведення охолоджуючої рідини електронасосом верстата до сопел перетворювача, розташованих на задній частині корпусу.
ПОПЕРЕДНІ ВИСНОВКИ
У даній роботі проведено аналіз сучасного стану питання вібраційного різання тонкостінних виробів. Таким чином можна здійснювати прецизійне різання тонкостінних виробів, які раніше зазвичай обробляли шліфуванням; вібруючим алмазним інструментом можна різати загартовані сталі. Можна сподіватися, що в перспективі замість шліфувальних верстатів для обробки (заточування) інструменту будуть використовуватися верстати з вібруючим ріжучим інструментом. На основі вібраційного принципу різання можна буде створити досить різноманітне нове верстатне обладнання.
Комбінований метод обробки, а саме застосування ультразвукових коливань у процесі токарної обробки тонкостінних виробів потребують подальшого дослідження, оскільки застосування ультразвуку призводить до помітного зниження сили різання, що в свою чергу значно знижує пружні віджимання в системі ВПІД, зниження шорсткості, підвищення корозійно- і зносо- стійкості, підвищення точності і значне зниження зносу обладнання.
При написанні даного реферату магістерська робота ще не завершена. Остаточне завершення: січень 2014 року. Повний текст роботи та матеріали по темі можуть бути отримані у автора або його керівника після зазначеної дати.
СПИСОК ВИКОРИСТАНОЇ ЛІТЕРАТУРИ
- Таровик А.Б., Михайлов А.Н. Классификация и особенности эксплуатации изделий с тонкостенными цилиндрическими поверхностями // Cб. трудов межд. науч.-тех. конф. в г. Севастополе 17 – 22 сентября 2012 г. – Донецк: ДонНТУ, 2012.
- Таровик А.Б., Михайлов А.Н. Классификация комбинированных методов обработки тонкостенных цилиндрических изделий // Прогресивні технології і системи машинобудування: Міжнародний зб. наукових праць. - Донецьк: ДонНТУ, 2012.
- Кумабэ Д. Вибрационное резание: Пер. с яп. С.Л. Масленникова/ Под ред. И.И. Портнова, В.В. Белова. – М.: Машиностроение, 1985. – 424 с.
- Астахов С.А. Высокопроизводительное точение тонкостенных закалённых цилиндрических заготовок // Автореферат диссертации по машиностроению и машиноведению. - Тула:ТулГУ, 2012.
- Хубка В. Теория технических систем: Пер. с нем. – М.: Мир, 1987. – 208 с.
- Михайлов А.Н. Основы синтеза функционально-ориентированных технологий машиностроения. – Донецк: ДонНТУ, 2008. – 346 с.
- Кривошапко С.Н. Аналитические поверхности в архитектуре зданий, конструкций и изделий. – М.: Либроком, 2012. – 328 с.
- Станок токарно-винторезный модели 1М61. Руководство по эксплуатации. - М:Машиностроение, 1981.
- Генератор ультразвуковой модели УЗГ1-1. Руководство по эксплуатации. - М:МашГиз, 1985.