Реферат по теме выпускной работы
Содержание
- 1. Актуальность темы
- 2. Цель и задачи исследования
- 3. Предполагаемая научная новизна
- 4. Предполагаемая практическая полезность заключается
- 5. Анализ возможностей обработки криволинейных поверхностей
- 5.1 Особенности механической обработки криволинейных поверхностей
- 5.2 Оптимизация режимов резания при механической обработке криволинейных поверхностей
- 6. Определение влияния кинематических углов в плане лезвия инструмента на шероховатость криволинейных поверхностей
- Список источников
1. Актуальность темы
Среди разнообразных видов поверхностей деталей машин особое место занимают криволинейные поверхности, механическая обработка которых весьма затруднена.
Обеспечение точности и качества поверхностного слоя деталей, рабочая поверхность которых ограничена фасонным профилем, представляет собой сложную технологическую задачу. Обработка фасонных поверхностей требует сложной кинематики относительного движения заготовки и инструмента и характеризуется переменными значениями технологических факторов, определяющих условия обработки.
В связи с вышеуказанным, тема работы, посвященная повышению производительности токарной обработки криволинейных поверхностей деталей машин за счет выбора рациональных параметров процесса резания является весьма актуальной и представляет большой практический интерес.
2. Цель и задачи исследования
Целью исследования является повышение производительности и снижение себестоимость точения криволинейных поверхностей деталей машин за счет обоснования рациональных параметров механической обработки.
Основные задачи исследования:
- Анализ возможностей обработки криволинейных поверхностей деталей машин;
- Исследование закономерностей формирования параметров поверхностного слоя при точении криволинейных поверхностей с учетом переменности геометрических параметров инструментов;
- Исследование закономерностей изменения сил и температур резания при точении криволинейных поверхностей с учетом переменности параметров сечения среза;
- Оптимизация режимов точения криволинейных поверхностей с учетом переменности параметров процесса резания по критериям максимальной производительности и минимальной себестоимости;
- Обоснование целесообразности применения смазочно-охлаждающих технологических сред (СОТС) для повышения производительности обработки;
- Создание программного обеспечения теоретических расчетов параметров поверхностного слоя, температур резания и оптимальных режимов точения криволинейных поверхностей;
- Разработка технологического процесса обработки деталей
прокатные ролики
с обеспечением повышения производительности и снижения себестоимости.
3. Предполагаемая научная новизна заключается
- В разработке теоретических моделей определения тепловых потоков и температур при точении криволинейных поверхностей с учетом переменности параметров процесса резания.
- В установлении аналитических зависимостей оптимальных по производительности и себестоимости режимов резания от условий обработки при точении криволинейных поверхностей.
4. Предполагаемая практическая полезность заключается
- В создании обоснованных рекомендаций по выбору оптимальных режимов резания и рациональной области применения СОТС для различных условий токарной обработки криволинейных поверхностей.
- В разработке технологического процесса обработки деталей
прокатные ролики
с обеспечением повышения производительности и снижения себестоимости.
5. Анализ возможностей обработки криволинейных поверхностей
В различных отраслях машиностроения возникает необходимость изготовления деталей, поверхность которых ограничена сложным фасонным профилем. К таким деталям относят формовочные валки трубоэлектросварочных и прокатных станов (рис.1), подающие и калибровочные валки правильных станов; различные бегунки колесных, гусеничных, подъемно-транспортных машин, пуансоны и матрицы штампов и пресс-форм, кулачки, роторы и статоры воздуходувок, лопатки газовых турбин, направляющие аппараты и др.
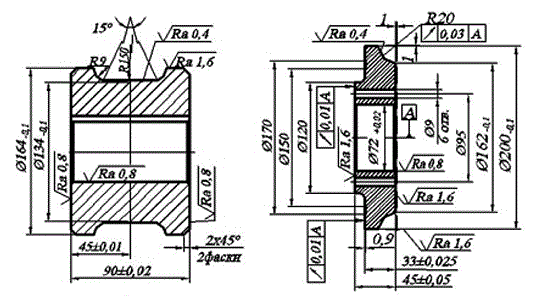
Рисунок 1 – Примеры деталей, имеющих фасонный профиль
Фасонные поверхности деталей машин делятся на [1, 2]:
- Алгебраические поверхности, т.е. описываемые математическими уравнениями (линейчатые, нелинейчатые, винтовые);
- С числовыми табличными координатами для отдельных точек (профили пера лопаток и т.д.);
- Конструктивные поверхности, обусловленные конструктивно необходимостью;
- Переходные поверхности (радиусные переходы от хвостовой части к рабочей у лопатки турбины и др.).
В крупносерийном и массовом производствах для обработки наружных и внутренних фасонных поверхностей на универсальных и агрегатных станках, полуавтоматах, автоматах, автоматических линиях, на гибких модулях с ЧПУ применяют [1, 2].
- Призматические и круглые фасонные резцы для заготовок с различной формой образующей; фасонные резцы;
- Протяжки для фасонных тел вращения и отверстий; (в трех выше отмеченных случаях форма режущих кромок инструментов совпадает с фасонным профилем заготовок);
- Способ копирования при прямом и непрямом действии копировального ролика и копира.
В первом случае контакт осуществляется силами тяжести груза, гидравлического давления или сжатия пружины, а во втором – через гидравлическое, пневматическое или электронное управление.
Наиболее широко применяется гидрокопирование, включая объемное копирование и копирование с передачей движения в масштабе путем сочетания копиров с рычажными механизмами – пантографами.
В ряде случаев роль копиров выполняют:
- Построители в виде отдельных механизмов или устройств на основе сложных электрических схем;
- метод настроечных кинематических цепей, связывающих вращение обрабатываемой заготовки или режущего инструмента с вспомогательным перемещением заготовки или инструмента.
В единичном, мелкосерийном и серийном производствах обработку заготовок с фасонными поверхностями целесообразно осуществлять на станках с программным управлением. Обоснованный экономический выбор вида автоматизированного оборудования – автоматов с ЧПУ, автоматов с ЦПУ и кулачковых автоматов можно производить с помощью графиков, представленных на рис. 2 [1, 2]. Применяемые схемы установки заготовок с фасонными поверхностями на токарных станках с ЧПУ регламентированы ГОСТ 3.1107.
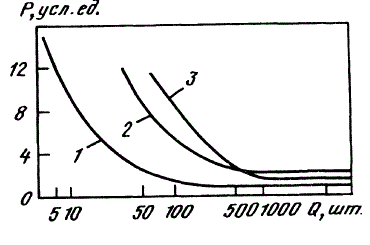
Рисунок 1 – Зависимость стоимости единицы продукции от размеров партии и вида оборудования: 1 – автомат с ЧПУ; 2 – автомат с ЦПУ; 3 – кулачковый автомат
Реализация обработки фасонных заготовок на токарных, фрезерных и многоцелевых станках с ЧПУ осуществляется в следующей последовательности [3]:
- Разрабатывается технологический процесс;
- Рассчитывается управляющая программа на основе расчетно-технологической карты и записи программы;
- Проводится контроль управляющей программы на координатографе и вносятся необходимые исправления;
- Проводится пробная обработка детали на станке с ЧПУ;
- Осуществляется контроль обработанной детали, вносятся исправления в программу расчета и в технологически процесс;
- Проводится обработка партии деталей.
5.1 Особенности механической обработки криволинейных поверхностей
Механическая обработка криволинейных поверхностей весьма затруднена. Прежде всего, их обработка характеризуется переменными исходными параметрами процесса резания: переменный радиус и осевой профиль фасонной поверхности, переменность припуска и физико – механических свойств материала заготовки и др.
Кроме того, обработка криволинейных поверхностей характеризуется переменностью параметров процесса резания: кинематических геометрических параметров лезвия инструмента и сечения срезаемого слоя, и как следствие – сил, температур резания, параметров обработанной поверхности [3].
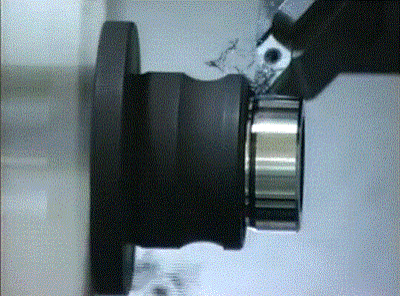
Рис. 1.1 Процесс точения криволинейной поверхности
(анимация: 6 кадров, 7 циклов повтроения)
При обработке сложных фасонных поверхностей для увеличения стойкости инструмента и повышения качества обработки необходимо станки с ЧПУ оснащать системами автоматического управления [3].
Системы автоматического управления должны обеспечивать постоянство скорости резания, круговой подачи, сил и температур резания в любой зоне обрабатываемой фасонной поверхности. Это осуществляется путем автоматического регулирования частоты вращения заготовки или инструмента независимо от причин, которые могут вызвать изменение сил или температур резания.
Такие системы повышают стабильность физических критериев оптимизации и надежность технологического процесса в целом, обеспечивая высокую производительность и качество обработки.
В настоящее время основное внимание при исследованиях особенностей механической обработки криволинейных поверхностей уделяется вопросам точности обработки [4-10]. Информация о закономерностях формирования поверхностного слоя криволинейных поверхностей деталей машин практически отсутствует, что требует проведения исследований в этом направлении.
Ко многим деталям с фасонными поверхностями, например, к прокатным роликам, предъявляются повышенные требования по прочности и износостойкости при высоких температурах, в связи с чем для их изготовления используются нержавеющие, жаропрочные и высокопрочные стали и сплавы, обладающие весьма низкой обрабатываемостью.
Одним из перспективных путей повышения эффективности механической обработки и трудоспособность инструмента является использование СОТС.
Значительный вклад в развитие науки о физико-химические процессы, происходящие в зонах контакта обрабатываемого и инструментального материалов, обычно называемой трибологии резки, при использовании МОТС внесли отечественные и зарубежные ученые Г.В. Виноградов, М.Б. Гордон, И.В. Гребіщіков, Г.И. Єпіфанов,М.И. Клушин, В.Н. Латышев, П.А. Ребиндер, Г. Мерчант, В.Я. Кізельштейн, Ф.П. Боуден, Д. Тейлор и др..[10-16].
В ряде работ высказываются предположения о том, что МОТС могут предоставлять не только позитивное, но и негативное воздействие на процесс резки. Есть противоречивые сведения о влиянии воды, кислорода, воздуха и вакуума на процесс резания, не ясен состав и свойства защитных пленок на контактных площадках, еще нет детального описания механизма химических реакций, протекающих при резке [17].
Цель применения СОТС – снижение износа режущего инструмента, улучшение качества обрабатываемой поверхности и повышение производительности труда [18]. В соответствии с существующими взглядами СОТС предоставляет в процессе резки охлаждающую, смазочную, диспергирующее и моющее действия.
Эффективные СОТС имеют большое влияние на качество поверхности: шероховатость, глубину и степень наклепаного слоя. В основном, СОТС уменьшают шероховатость поверхности на 0,5-1 класс, а также снижают глубину и степень клеветы поверхностных слоев детали. Например, кислород и СОТС, что имеют в смысле кислород, повышают качество поверхности за счет уменьшения или полной ликвидации нароста на резцы [19-21].
Применение СОТС при обработке металлов резанием позволяет повышать производительность оборудования, точность и чистоту обработки, снизить брак, улучшить условия труда и в ряде случаев сократить число технологических операций [22]
Для процессов металлообработки СОТС выбирают в соответствии с типом операций и их технологическим особенностям, характеристикой обрабатываемых материалов, и т.д. Рекомендации по выбору СОТС для различных условий обработки металлов резанием приведены в [22-27]. Выбор СОТС также определяется рекомендациями по транспортировке и хранению, приготовлению рабочих растворов, контролю и корректировке качества, утилизации, охраны труда при работе с СОТС.
Методика расчета охлаждающих свойств СОТС представлена в [28]. Приведены уравнения, которые позволяют определить влияние физико-химических свойств СОТС на коэффициент теплоотдачи, который увеличивается с ростом теплопроводности и скорости движения жидкости и уменьшается с увеличением площади охлаждаемой поверхности, температуропроводности и динамической вязкости жидкости. Коэффициент теплоотдачи зависит также от температуры пограничного слоя [28].
В наше время есть перечень статей по расчету тепловых потоков и температур резки с использованием СОТС и интенсификации процесса резания [29-32]; повышению производительности обработки труднообрабатываемых материалов с использованием СОТС [33-35].
Несмотря на наличие большого количества информации по поводу применения СОТС, в научно-справочной литературе практически отсутствует информация о количественные оценки возможностей уменьшения температуры резки и повышения производительности обработки деталей машин за счет СОТС.Существующая методика расчета тепловых потоков и температур в зоне резания с учетом действия СОТС не учитывает особенностей обработки криволинейных поверхностей с переменными параметрами процесса резания. Для этих видов поверхностей представляет интерес дальнейшее развитие методики определения сил и температур в зоне резания при использовании различных СОТС.
5.2 Оптимизация режимов резания при механической обработке криволинейных поверхностей
При анализе возможностей повышения производительности и снижения себестоимости обработки весьма важен правильный выбор режимов резания. Важнейшей задачей современного машиностроения является достижение более высокой производительности обработки с обеспечением заданного уровня качества поверхностного слоя деталей, что может быть достигнуто за счет обоснования оптимального уровня параметров обработки.
В области режущего инструмента, есть достаточно большое количество работ, посвященных оптимизации его параметров и условий эксплуатации с точки зрения различных критериев эффективности. Наибольшее внимание в технической литературе уделено определению рациональных режимов резания.
Среди работ, посвященных определению рациональных режимов, необходимо отметить труда М.И. Клушина, Макарова А.Д., В.К. Старкова [36-40] и других специалистов.
В отношении обработки металлов резанием целевые функции должны быть представлены в зависимости от величин, которые необходимо автоматизировать. В зависимости от того, является ли все использованные зависимости от критериев переменных линейными или есть хотя бы одна нелинейная, говорят о линейную или нелинейную оптимизацию [42, 43]. В зависимости от вида расчета технологических и экономических ограничений и формы целевой функции применяются различные методы оптимизации режимов резания [44]. Большое внимание уделяется уточнению использованных технологических и экономико-организационных зависимостей [45, 46]. и др.
Первостепенное значение имеет выбор критерия оптимизации. Наиболее эффективным для решения практических задач был бы такой критерий, который бы учитывал все вопросы, которые интересуют производство. Отсутствие такого универсального критерия является причиной разнообразия технико-экономических показателей, которые используются в качестве критерия оптимизации.
В работе [44] предлагается применять одновременно несколько критериев, например, минимальной стоимости и максимальной производительности или максимально прибыльные.
В опубликованных работах по оптимизации режимов не приводится общий критерий, учитывающий все существующие на практике. Самым простым способом решения задачи многокритериальной оптимизации является выбор главного критерия эффективности и перевод других в разряд критериальных ограничений. В этом случае выходит задача однокритеріальної оптимизации, для решения которой на практике существует достаточно много эффективных и хорошо зарекомендовавших методов. [41, 42].
Для практического использования представляет интерес возможность выполнения аналитических расчетов оптимальных режимов резания, что достаточно просто обеспечивается методом геометрического программирования. Методика оптимизация режимов резания с использованием МГП, представленная в работе [47]., дает аналитическое решение для определения оптимальных режимов резания при точении по критерию минимальной себестоимости.
Современные тенденции в оптимизации режимов резания направлены на решение многокритериальных задач, обеспечивающих одновременное улучшение параметров обработки по различным критериям. Одним из направлений многокритериальной оптимизации является использование мультипликативной свертки критериев, позволяющих различные критерии оптимизации привести к единому критерию, обеспечивающему наилучшее сочетание каждого из них [48].
Представляет интерес дальнейшее развитие МГП с применением мультипликативных критериев с учетом переменности параметров процесса резания при обработке криволинейных поверхностей.
6. Определение влияния кинематических углов в плане лезвия инструмента на шероховатость криволинейных поверхностей
Обеспечение заданного уровня качества деталей машин во время их механической обработки – важная задача технологии машиностроения, в связи с чем выполнены исследования влияния на шероховатость обработанных поверхностей геометрических параметров режущего инструмента достаточно актуальны.
В настоящее время широко известны общие закономерности формирования шероховатости обработанных поверхностей в зависимости от условий механической обработки, которые являются основой прогнозирования уровня шероховатости на стадии проектирования технологических процессов и управления параметрами шероховатости на стадии изготовления деталей машин.
Во время обработки криволинейных поверхностей имеет место сложный характер изменения как кинематических геометрических параметров лезвия инструмента, так и параметров среза поверхностного слоя, связанный с кривизной поверхности, что существенно усложняет анализ влияния этих параметров на уровень шероховатости. Исследования в этом направлении весьма ограничены.
Целью представленной работы является установление закономерностей формирования шероховатости криволинейных поверхностей тел вращения во время токарной обработки с учетом переменных кинематических углов в плане лезвия инструмента.
Во время обработки резцами среднее арифметическое отклонение профиля определяется следующими общими уравнениями [51].:

где r – радиус при вершине резца; s – подача; φ – главный угол в плане резца; φ1 – вспомогательный угол в плане резца; Rzі – расчетная высота неровностей профиля:
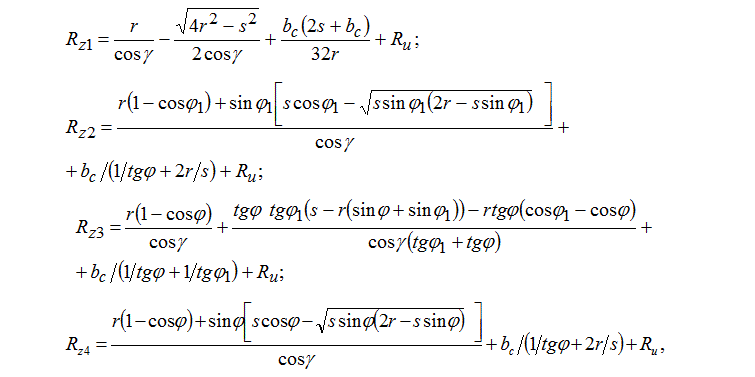
где γ – передний угол резца; Rи – высота неровностей профиля на вершине резца; bс – величина пластического оттеснения:
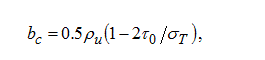
где ρи – радиус скругления режущей кромки инструмента; σТ, τ0 – предел текучести и мощность обрабатываемого материала.
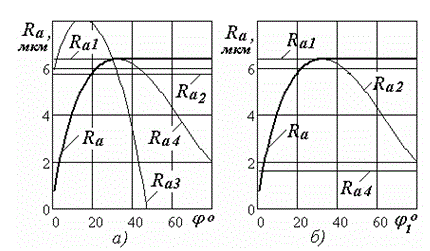
Рис.2.1 Графики зависимостей параметра шероховатости поверхности Rа от углов в плане лезвия инструмента: главных φ – а) и вспомогательных φ1 – б)
На рис. 2.1 преведены графики зависимостей параметра шероховатости поверхности Rа от углов в плане лезвия инструмента для следующих условий: – радиус при вершине резца r = 0,5мм; подача s = 0,2мм/об; главный угол в плане; φ = 90°; дополнительный угол в плане φ 1 = 30°.
Графики свидетельствуют о том, что для заданных условий существенное влияние на шероховатость поверхности Rа углы в плане имеют лишь в диапазоне их изменения до 30°, когда с увеличением как основных, так и вспомогательных углов в плане шероховатость растет. Дальнейшее изменение углов в плане не влияет на шероховатость, которая определяется шероховатостью Rа1 и от них не зависит. Влияние главного угла в плане при постоянном вспомогательном углу определяется в соответствии Rа4, при этом шероховатость Rа2, которая зависит от вспомогательного угла, остается постоянной. Влияние вспомогательного угла в плане при постоянном главном углу определяется в соответствии Rа2, при этом остается постоянной шероховатость Rа2, которая зависит от главного угла в плане.
Во время обработки криволинейных поверхностей кинематические углы в плане как главные, так и вспомогательные одновременно изменяются (рис.2.2).
Пример определения кинематических главных и вспомогательных углов в плане приведен для выпуклой поверхности с постоянным радиусом кривизны (образующая поверхность вращения - круг, центр принятой системы координат является центром кривизны, то есть центром круга).
Положение вершины лезвия на указанной криволинейной поверхности определяется мгновенным углом поворота, который рассчитывается следующим образом:

где ζ=х/ρ – безразмерная координата.
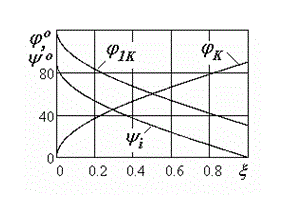
Рис. 2.2. Графики изменения кинематических углов в плане лезвия инструмента во время обработки криволинейной поверхности
Кинематический главный φК и дополнительный φ1К углы в плане определяются относительно направления движения подачи DS мгновенным углом поворота ψi:

Графики изменения мгновенных углов поворота ψi и кинематических главных φК и вспомогательных φ1К углов в плане приведены на рис. 2.3.
Закономерности формирования шероховатости указанной криволинейной поверхности в отличие от ранее исследованных (рис. 2.1) заключаются в одновременном изменении кинематических главных и вспомогательных углов в плане.
Графики изменения параметров шероховатости Rаi в зависимости от расположения вершины лезвия на обработанной криволинейной поверхности с учетом одновременного изменения кинематических углов в плане приведены на рис. 2.4.
Графики свидетельствуют о том, что для заданных условий влияние на шероховатость криволинейной поверхности Rа в диапазоне изменения угла до 30°, а координаты до 0,1 (рис.3) имеет главный угол в плане ψ: при его увеличении шероховатость растет (влияние главного угла в плане ψ определяется шероховатостью Rа4). В связи с тем, что вспомогательный угол ψ1 по всей длине криволинейной поверхности превышает 30° (рис. 2.3), его влияние на шероховатость поверхности отсутствует (влияние вспомогательного угла в плане ψ1 определяется шероховатостью Rа3). Дальнейшая смена главного угла в плане ψ>30° также не влияет на шероховатость. Она остается постоянной и определяется в соответствии шероховатостью Ra1, которая от углов в плане не зависит.
Таким образом, на основании установленных закономерностей изменения кинематических углов в плане лезвия инструмента во время токарной обработки криволинейных поверхностей определенное влияние главных и вспомогательных углов в плане лезвия инструмента на шероховатость обработанной поверхности. В результате выполненных исследований для заданных радиусов при вершине лезвия и подач установлены количественные связи шероховатости с углами в плане лезвия инструмента, которые составляют основание для разработки методов управления шероховатостью во время обработки криволинейных поверхностей.
Список источников
- Гжиров Р. И. Программирование обработки на станках с ЧПУ / Р.И. Гжиров, П.П. Серебреницкий. – Л.: Машиностроение, 1990. – 489 с.
- Дерябин А. Л. Программирование технологических процессов для станков с ЧПУ / А.Л. Дерябин. – М.: Машиностроение, 1984. – 51 с.
- Шарин Ю.С. Технологическое обеспечение станков с ЧПУ М.: Машиностроение, 1986. – 176с.
- Лещенко А.И. Анализ точности обработки фасонных поверхностей в зависимости от погрешности настройки инструментов на программ-ную операцию вісник приазовського державного технічного університету 2008 р. Вип. № 18 с. 129-133.
- Марецкая В.В. Моделирование технологических процессов механической обработки с использованием программного комплекса «Моделирование В Технических Устройствах» («МВТУ») // Известия вузов. Машиностроение. – 2004. – № 4. – с. 39-52.
- Марецкая В.В. Исследование отклонений профиля рабочей поверхности валка, вызванных упругими отжатиями элементов технологической системы // Справочник. Инженерный журнал. – 2006. – № 12. – с. 50–54.
- Марецкая В.В. К вопросу автоматизации направленного формирования показателей качества деталей // Вестник компьютерных и информационных технологий. – 2008. – № 3. – с. 29–34.
- Камсюк М.С., Грановский Э.Г. Определение отклонений, обусловленных отжатиями технологической системы при контурном фрезеровании // Известия вузов. Машиностроение. – 1981. – №5 – с. 139–143.
- Грановский Э.Г., Камсюк М.С. Точность обработки сложноконтурных поверхностей деталей // Основные направления развития технологии машиностроения: Труды МВТУ. – 1981. – № 348. – с.110–127.
- Технологическая наследственность в машиностроительном производстве / под ред. А.М. Дальского. – М.: Изд-во МАИ, 2000. – 364 с.
- Виноградов Ю.М. Применение химическиактивных веществ для повышения эффективности СОЖ при резании металлов / Ю.М.Виноградов. – М.: Изд. МДНТН, сб. №1, 1966, с. 1-13
- Зорев Н.Н. Обработка резанием тугоплавких сплавов / Н.Н. Зорев, З.М.Фетисова. – М.: Машиностроение, 1966, с. 64-69
- Мерчант М.Ю., В сб. Международная конференция по смазке и износу / М.Ю. Мерчант. – М.: ИЛ., 1956. с. 95-105
- Матвеевский Р.М. Температурная стойкость граничных смазочных слоев и твердых смазочных покрытий при трении металлов и сплавов / Р.М.Матвеевский. – М.: Наука, 1971. – 213 с.
- Носовский И.Г. Исследование изнашивания металлов в различных газовых средах / И.Г.Носовский. – Редиздат Аэрофлота, 1956. – 120 с.
- Чубаров А.Д. Деформирование и роль температурного фактора в процессе резания титановых сплавов / А.Д. Чубаров, Н.Н. Новиков. - М.: Вестник машиностроения, 1959, №9. – с. 40-43
- Латышев В.Н. Повышение эффективности СОЖ / В.Н Латышев – М.: Машиностроение, 1975. – 88 с.
- Смазочно-охлаждающие технологические средства для обработки металлов резанием: Справочник / Под ред. С.Г. Энтелиса, Э.М. Берлинера. – М.: Машиностроение, 1986. – 352 с., ил.
- Боуден Ф.П. Трение и смазка твердых тел / Ф.П. Боуден, Д.А. Тейбор. - М.: Машиностроение, 1968, 493 с.
- Кривоухов В.А. Обрабатываемость резанием жаропрочных и титановых сплавов / В.А. Кривоухов. - М.: Машгиз, 1961. - 270 с.
- Латышев В.Н. Влияние газовой среды и смазочного материала на температуру поверхностей трения / В.Н. Латышев. - Изд. АН СССР: Маши-ностроение 1971, №4. – с. 109-111
- Топлива, смазочные материалы, технические жидкости. Ассортимент и применение: Справ. Изд./ К.М. Бадыштова, Я.А. Бердштадт, Ш.К. Богданов и др.; Под ред. В.М. Школьникова. – М.: Химия, 1989. – 432с.
- Худобин Л.В. Техника примения смазочно-охлаждающих средств в металлообработке / Л.В. Худобин, Е.Г. Бердичевский. – М.: Машинострое-ние, 1977. – 189 с. с ил.
- Справочник по обработке металлов резанием / Ф.Н. Абрамов, В,В. Коваленко, В.Е. Любимов и др. - К.: Техника, 1983. – 239 с.. ил. – Биб-лиогр.: с. 235-237.
- Прогрессивные режущие инструменты и режимы резания металлов. Справочное издание / В.И. Баранчиков, А.В. Жариков, Н.Д. Юдина и др. М.: Машиностроение, 1990.
- Базовый ассортимент смазочно-охлаждающих технологических сред для обработки металлов резанием // Тематический обзор. – Централь-ный научно-исследовательский институт информации и технико-экономических исследований нефтеперерабатывающей и нефтехимической промышленности. 1986 г.
- Топлива, смазочные материалы, технические жидкости. Ассортимент и применение: Справочник / И.Г. Анисимов, К.М. Бадыштова, С.А. Бнатов и др.; Под ред. В.М, Школьникова. Изд. 2-е перераб. И доп. – М.: Из-дательский центр «Техинформ», 1999. – 596 с.: ил.
- Расчет тепловых потоков и температур резания при точении с использованием смазочно-охлаждающих жидкостей. / Т.Г. Ивченко (ДонНТУ, г. Донецк, Украина) Надійність інструменту та оптимізація технологічних систем. Збірник наукових праць. – Краматорськ, ДДМА. вип.26, 2010. – c. 90-96.
- Теоретичні основи керування температурою різання з використанням охолоджуючих середовищ / Т.Г. Івченко (ДонНТУ, м. Донецьк, Україна) Надійність інструменту та оптимізація технологічних систем. Збірник наукових праць. Вип.18. – Краматорськ: ДДМА, 2006. – c. 39-45.
- Вплив способу подачі охолоджуючого середовища на температуру різання / Т.Г. Івченко, В.Г. Нечепаєв, О.М. Гнитько (ДонНТУ, м. Донецьк, Україна) Надійність інструменту та оптимізація технологічних систем. Збірник наукових праць. Вип.16 . – Краматорськ: ДДМА, 2005. – c. 34-38
- Интенсификация процесса резания сборными режущими инструментами с использованием охлаждающих технологических сред / Александр Михайлов, Татьяна Ивченко, Ольга Дубоделова (ДонНТУ, г. Донецк, Украи-на) Tehnologii Modern, Calitate, Restructurare. Vol. 1. – Chisinau: Universitates Tecnica a Moldovei, 2005. c. 289-295
- Влияние функциональных технологических свойств смазочно-охлаждающих технологических сред на выбор оптимальных режимов реза-ния / Вадим Богуславский, Татьяна Ивченко Пер. с англ. Ирина Зайцева In-fluence of functional properties of technological cutting fluid on a choice of opti-mum cutting regimes [электронный ресурс]. – Режим доступа: http://www.modtech.ro/vol3no22011/2_FINAL_Bogouslavskiy_Vadim.pdf.
- Повышение производительности обработки труднообрабатываемых материалов с применением смазочно-охлаждающих жидкостей / В.А. Богуславский, Т.Г. Ивченко, Зантур Сахби (ДонНТУ, г. Донецк, Украина) Наукові праці Донецького національного технічного університету. Серія: Машинобудування і машинознавство. Випуск 7(166). – Донецьк: ДонНТУ, 2010. – c. 9-16.
- Vadim Bogouslavskiy, Tatiana Ivchenko. Optimisation of cutting regimes at application of technological cutting fluid // ModTech International Conference 25-27th May 2011, Vadul lui Voda: Chisinau, 2011. P. 669-672. (Index to Scientific & Technical Proceedings of Thomson Scientific - Institute for Scientific In-formation (ISI).
- Клушин М.И. Определение стойкости режущих инструментов, обеспечивающих получение максимально возможной прибыли и производи-тельности общественного труда / М.И. Клушин, Г.Г. Аносов. – Вестник ма-шиностроения, №6, 1970. – с.74-76.
- Макаров А.Д. Оптимизация процессов резания / А.Д. Макаров – М.: Машиностроение, 1976. – 278 с.
- Старков В.К. Обработка резанием. Управление стабильностью и качеством в автоматизированном производстве / В.К. Старков. – М.: Маши-ностроение, 1989. – 296 с.
- Старков В.К. Технологические методы повышения надежности обработки на станках с ЧПУ / В.К. Старков. – М.: Машиностроение, 1984. – 120 с.
- Старков В.К. Оптимизация процесса резания по энергетическим критериям / В.К. Старков, М.В. Киселев // Вестник машиностроения. – М.: 1989, №4. – с. 41-45.
- Якобс Г. Оптимизация резания. Параметризация способов обработки резанием с использованием технологической оптимизации / Г. Якобс, Э.Якобс, Д. Кохан // Пер. с нем. – М.: Машиностроение, 1981. – 279 с.
- Гильман А.М. Оптимизация режимов обработки на металлорежущих станках / А.М. Гильман. – М.: Машиностроение, 1972. – 188 с.
- Евтушенко Ю.Г. Методы решения экстремальных задач и их применение в системах оптимизации / Ю.Г. Евтушенко. – М.: Наука, 1982. – 432 с.
- Кроль О.С. Оптимизация и управление процессом резания. Учеб. Пособие. / О. С.Кроль, Г.Л. Хмелевский. – К.: УМК ВО, 1991. – 140 с.
- Карпусь В. Е. Системные критерии механообрабатывающих технологических систем / В.Е. Карпусь С.В. Луцкий. // Резание и инструмент в технологических системах. – Харьков: ХГПУ, 2000, Вып.57. – с.105-109
- Реклейтис Г. Оптимизация в технике: В 2-х кн. Кн. 2. / Г. Реклейтис, А.Рейвиндран, К. Рэгсдел. // Пер. с англ. – М.: Мир, 1986, - 320 с.
- Ивченко Т. Г. Использование метода геометрического программирования для расчета оптимальных режимов резания при точении / Т.Г.Ивченко Научный вестник ДГМА. – Краматорск: ДГМА, 2011. – №2 (8 Е). с.110-116.
- Король K.O., Ивченко Т.Г. Многокритериальная оптимизация режимов резания на основе мультипликативной свертки критериев ИНЖЕНЕР: студенческий научно-технический журнал / Донецк: ДонНТУ, 2012, № 13. - с.124-128.
- Суслов А.Г. Качество поверхностного слоя деталей машин / А.Г. Суслов. - М.: Машиностроение, 2000. - 320с.
- Качество машин: Справочник. В 2 т. Т.1 / А.Г. Суслов, Э.Д. Браун, Н.А. Виткевич и др. - М.: Машиностроение, 1995. - 256с.
- Грановский Г.И., Грановский В.Г., Резание металлов: Учебник для вузов / Г.И. Грановский, В.Г. Грановский. - М.: Высш. шк.,1985. - 304с.
Замечание! При написании данного реферата магистерская работа еще не завершена. Окончательное завершение: декабрь 2013 г. Полный текст работы и материалы по теме могут быть получены у автора или его руководителя после указанной даты.