Реферат за темою випускної роботи
Зміст
- 1. Актуальність теми
- 2. Мета і задачі дослідження
- 3. Передбачувана наукова новизна
- 4. Передбачувана практична корисність
- 5. Аналіз можливостей обробки криволінійних поверхонь
- 5.1 Особливості механічної обробки криволінійних поверхонь
- 5.2 Оптимізація режимів різання при механічній обробці криволінійних поверхонь
- 6. Визначення впливу кінематичних кутів в плані леза інструменту на шорсткість криволінійних поверхонь
- Перелік посилань
1. Актуальність теми
Серед різноманітних видів поверхонь деталей машин особливе місце займають криволінійні поверхні, механічна обробка яких дуже ускладнена.
Забезпечення точності і якості поверхневого шару деталей, робоча поверхня яких обмежена фасонним профілем, є складним технологічним завданням. Обробка фасонних поверхонь вимагає складної кінематики відносного руху заготівлі і інструменту і характеризується змінними значеннями технологічних чинників, що визначають умови обробки.
У зв'язку з вище згаданим, тема роботи, присвячена підвищенню продуктивності токарної обробки криволінійних поверхонь деталей машин за рахунок вибору раціональних параметрів процесу різання є дуже актуальною і представляє великий практичний інтерес.
2. Мета і задачі дослідження
Метою роботи є підвищення продуктивності і зниження собівартість точіння криволінійних поверхонь деталей машин за рахунок обгрунтування раціональних параметрів механічної обробки.
Задачі дослідження:
- аналіз можливостей обробки криволінійних поверхонь деталей машин;
- дослідження закономірностей формування параметрів поверхневого шару при точінні криволінійних поверхонь з урахуванням змінності геометричних параметрів інструментів;
- дослідження закономірностей зміни сил і температур різання при точінні криволінійних поверхонь з урахуванням змінності параметрів перерізу зрізу;
- оптимізація режимів точіння криволінійних поверхонь з урахуванням змінності параметрів процесу різання закритеріями максимальної продуктивності і мінімальноїсобівартості;
- обгрунтування доцільності застосування мастильно-охолоджувальних технологічних середовищ(МОТС) дляпідвищення продуктивності обробки;
- створення програмного забезпечення теоретичнихрозрахунків параметрів поверхневого шару, температур різання і оптимальних режимів точіння криволінійних поверхонь;
- розробка технологічного процесу обробки деталей
прокатні ролики
із забезпеченням підвищення продуктивності і зниження собівартості.
3. Передбачувана наукова новизна полягає:
- У розробці теоретичних моделей визначення теплових потоків і температур при точінні криволінійних поверхонь з урахуванням змінності параметрів процесу різання.
- У встановленні аналітичних залежностей оптимальних по продуктивності і собівартості режимів різання від умов обробки при точінні криволінійних поверхонь.
4. Передбачувана практична корисність полягає:
- У створенні обгрунтованих рекомендацій по виборуоптимальних режимів різання і раціональної сферизастосування МОТС для різних умов токарної обробки криволінійних поверхонь.
- У розробці технологічного процесу обробки деталей
прокатні ролики
із забезпеченням підвищенняпродуктивності і зниження собівартості.
5. Аналіз можливостей обробки криволінійних поверхонь
В різних галузях машинобудування виникає необхідність виготовлення деталей, поверхня яких обмежена складним фасонним профілем. До таких деталей відносять формувальні валяння трубоэлектросварочных і прокатних станів (рис.1), подаючі і калібрувальні валяння правильних станів; різні бігунки колісних,підйомно-транспортних машин, пуансони і матриці штампів і прес-форм, куркульки, ротори і статориповітродувок, лопатки газових турбін, направляючіапарати та інше.
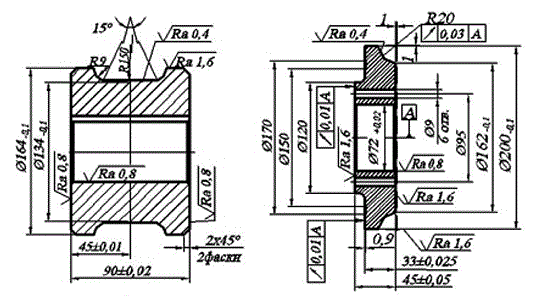
Рис.1 – Приклади деталей, що мають фасонний профіль
Фасонні поверхні деталей машин діляться на [1, 2]:
- поверхні алгебри, тобто описувані математичними рівняннями(лінійчасті, нелінійчасті, гвинтові);
- з числовими табличними координатами для окремих точок(профілі пера лопаток і так далі);
- конструктивні поверхні, обумовлені конструктивною необхідністю;
- перехідні поверхні(переходи радіусів від хвостової частини до робочої у лопатки турбіни та ін.).
У великосерійному і масовому виробництвах для обробки зовнішніх і внутрішніх фасонних поверхонь на універсальних і агрегатних верстатах, напівавтоматах, автоматах, автоматичних лініях, на гнучких модулях з ЧПУ застосовують [1, 2].
- призматичні і круглі фасонні різці для заготівель з різною формою тієї, що утворює; фасонні різці;
- протягання для фасонних тіл обертання і отворів; (у трьох вище відмічених випадках форма різальних кромок інструментів співпадає з фасонним профілем заготовок);
- спосіб копіювання при прямій і непрямій дії копіювального ролика і копира.
У першому випадку контакт здійснюється силами тяжіння вантажу, гідравлічного тиску або стискування пружини, а в другому – через гідравлічне, пневматичне або електронне управління.
Найширше застосовується гідрокопіювання, включаючи об'ємне копіювання і копіювання з передачею руху в масштабі шляхом поєднання копиров з важільними механізмами – пантографами.
У ряді випадків роль копиров виконують:
- будівники у вигляді окремих механізмів або пристроїв на основі складних електричних схем;
- метод настроювальних кінематичних ланцюгів, що зв'язують обертання оброблюваної заготівлі або різального інструменту з допоміжним переміщенням заготівлі або інструменту.
У одиничному, дрібносерійному і серійному виробництвах обробку заготівель з фасонними поверхнями доцільно здійснювати на верстатах з програмним управлінням. Обгрунтований економічний вибір виду автоматизованого устаткування - автоматів з ЧПУ, автоматів з ЦПУ і кулачкових автоматів можна робити за допомогою графіків, представлених на рис.2 [1, 2]. Вживані схеми установки заготівель з фасонними поверхнями на токарних верстатах з ЧПУ регламентовані ГОСТ 3.1107.
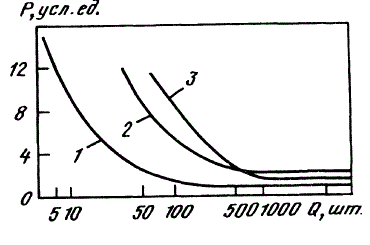
Рис.1 – Залежність вартості одиниці продукції від розмірів партії і виду устаткування : 1 – автомат з ЧПУ; 2 – автомат з ЦПУ; 3 – кулачковий автомат
Реалізація обробки фасонних заготівель на токарних, фрезерних і багатоцільових верстатах з ЧПУ здійснюється в наступній послідовності [3]:
- розробляється технологічний процес;
- розраховується програма, що управляє, на основі розрахунково-технологічної карти і запису програми;
- проводиться контроль програми, що управляє, на координатографі і вносяться необхідні виправлення;
- проводиться пробна обробка деталі на верстаті з ЧПУ;
- здійснюється контроль обробленої деталі, вносяться виправлення в програму розрахунку і в технологічно процес;
- проводиться обробка партії деталей.
5.1 Особливості механічної обробки криволінійних поверхонь
Механічна обробка криволінійних поверхонь дуже ускладнена. Передусім, їх обробка характеризується змінними початковими параметрами процесу різання: змінний радіус і осьовий профіль фасонної поверхні, змінність припуска і физико-механічних властивостей матеріалу заготівлі і інше.
Крім того, обробка криволінійних поверхонь характеризується змінністю параметрів процесу різання : кінематичних геометричних параметрів леза інструменту і перерізу зрізуваного шару, і як наслідок – сил, температур різання, параметрів обробленої поверхні [3].
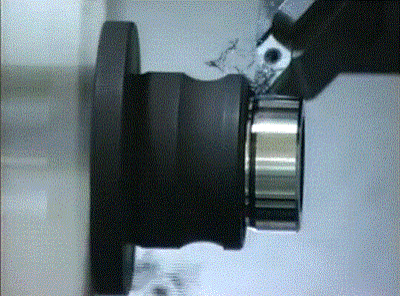
Рис. 1.1 Процес точіння криволінійної поверхні
(анімація: 6 кадрів, 7 циклів повторення)
При обробці складних фасонних поверхонь для збільшення стійкості інструменту і підвищення якості обробки необхідно верстати з ЧПУ оснащувати системами автоматичного управління [3].
Системи автоматичного управління повинні забезпечувати постійність швидкості різання, кругового подання, сил і температур різання у будь-якій зоні оброблюваної фасонної поверхні. Це здійснюється шляхом автоматичного регулювання частоти обертання заготівлі або інструменту незалежно від причин, які можуть викликати зміну сил або температур рызання.
Такі системи підвищують стабільність фізичних критеріїв оптимізації і надійність технологічного процесу в цілому, забезпечуючи високу продуктивність і якість обробки.
Нині основна увага при дослідженнях особливостей механічної обробки криволінійних поверхонь приділяється питанням точності обробки [4-10]. Інформація про закономірності формування поверхневого шару криволінійних поверхонь деталей машин практично відсутня, що вимагає проведення досліджень в цьому напрямі.
До багатьох деталей з фасонними поверхнями, наприклад, до прокатних роликів, пред'являються підвищені вимоги по міцності і зносостійкості при високих температурах, у зв'язку з чим для їх виготовлення використовуються нержавіючі, жароміцні і високоміцні стали і сплави, що мають дуже низьку оброблюваність.
Одним з перспективних шляхів підвищення ефективності механічної обробки та працездатності інструменту є використання МОТС.
Значний внесок у розвиток науки про фізико-хімічні процеси, що відбуваються в зонах контакту оброблюваного та інструментального матеріалів, зазвичай званої трибології різання, при використанні МОТС внесли вітчизняні та зарубіжні вчені Г.В. Виноградов, М.Б. Гордон, І.В. Гребіщіков, Г.І. Єпіфанов,М.І. Клушин, В.Н. Латишев, П.А. Ребіндер, М. Мерчант, В.Я. Кізельштейн, Ф.П. Боуден, Д. Тейлор та ін.[10-16].
У ряді робіт висловлюються припущення про те, що МОТС можуть надавати не тільки позитивну, але й негативну дію на процес різання. Є суперечливі відомості про вплив води, кисню, повітря та вакууму на процес різання, не з'ясований склад і властивості захисних плівок на контактних площадках, ще немає детального опису механізму хімічних реакцій, що протікають при різанні[17].
Мета застосування МОТС – зниження зношування ріжучого інструменту, покращення якості оброблюваної поверхні та підвищення продуктивності праці [18]. У відповідності з існуючими поглядами МОТС надає в процесі різання охолоджувальну, мастильну, диспергуючу та миючий дії.
Ефективні МОТС мають великий вплив на якість поверхні: шорсткість, глибину та ступінь наклепаного шару. Здебільшого, МОТС зменшують шорсткість поверхні на 0,5-1 клас, а також знижують глибину та ступінь наклепу поверхневих шарів деталі. Наприклад, кисень і МОТС, що мають у змісті кисень, підвищують якість поверхні за рахунок зменшення або повної ліквідації наросту на різці[19-21].
Застосування МОТС при обробці металів різанням дозволяє підвищувати продуктивність обладнання, точність і чистоту обробки, знизити брак, поліпшити умови праці та в ряді випадків скоротити число технологічних операцій [22].
Для процесів металообробки МОТС вибирають відповідно до типу операцій та їх технологічним особливостями, характеристикою оброблюваних матеріалів, тощо. Рекомендації щодо вибору МОТС для різних умов обробки металів різанням наведені в [22-27]. Вибір МОТС також визначається рекомендаціями по транспортуванню та зберіганню, приготуванню робочих розчинів, контролю та коректуванню якості, утилізації, охорони праці при роботі з МОТС.
Методика розрахунку охолоджуючих властивостей МОТС представлена в [28]. Наведено рівняння, які дозволяють визначити вплив фізико-хімічних властивостей МОТС на коефіцієнт тепловіддачі, який збільшується з зростанням теплопровідності та швидкості руху рідини та зменшується зі збільшенням площі охолоджуваної поверхні, температуропровідності та динамічної в'язкості рідини. Коефіцієнт тепловіддачі залежить також від температури прикордонного шару [28].
У наш час є перелік статей щодо розрахунку теплових потоків і температур різання з використанням МОТС та інтенсифікації процесу різання [29-32]; підвищенню продуктивності обробки важкооброблюваних матеріалів з використанням МОТС [33-35].
Незважаючи на наявність великої кількості інформації з приводу застосування МОТС, в науково-довідковій літературі практично відсутня інформація про кількісні оцінки можливостей зменшення температури різання та підвищення продуктивності обробки деталей машин за рахунок МОТС.
Існуюча методика розрахунку теплових потоків і температур в зоні різання з урахуванням дії СОТС не враховує особливостей обробки криволінійних поверхонь зі змінними параметрами процесу різання. Для цих видів поверхонь представляє інтерес подальший розвиток методики визначення сил і температур в зоні різання при використанні різних СОТС.
5.2 Оптимізація режимів різання при механічній обробці криволінійних поверхонь
При аналізі можливостей підвищення продуктивності і зниження собівартості обробки дуже важливий правильний вибір режимів різання. Найважливішим завданням сучасного машинобудування є досягнення найбільш високої продуктивності обробки із забезпеченням заданого рівня якості поверхневого шару деталей, що може бути досягнуто за рахунок обґрунтування оптимального рівня параметрів обробки.
В області різального інструменту, є досить велика кількість робіт присвячених оптимізації його параметрів і умов експлуатації з погляду різних критеріїв ефективності. Найбільшу увагу в технічній літературі приділено визначенню раціональних режимів різання.
Серед робіт, присвячених визначенню раціональних режимів, необхідно відзначити праці М.І. Клушина, Макарова А.Д., В.К. Старкова [36-40] та інших фахівців.
Відносно обробки металів різанням цільові функції повинні бути представлені в залежності від величин, які необхідно автоматизувати. Залежно від того, чи є всі використані залежності критеріїв від змінних лінійними або є хоча б одна нелінійна, говорять про лінійну або нелінійну оптимізацію [42, 43]. Залежно від виду розрахунку технологічних і економічних обмежень і форми цільової функції застосовуються різні методи оптимізації режимів різання [44]. Велика увага приділяється уточненню використаних технологічних і економіко-організаційних залежностей [45, 46]. и др.
Першорядне значення має вибір критерію оптимізації. Найбільш ефективним для рішення практичних завдань був би такий критерій, який би враховував всі питання, які цікавлять виробництво. Відсутність такого універсального критерію є причиною розмаїття техніко-економічних показників, які використовуються як критерій оптимізації.
У роботі [44] пропонується застосовувати одночасно кілька критеріїв, наприклад, мінімальної вартості та максимальної продуктивності або максимально прибуткові.
В опублікованих роботах з оптимізації режимів не приводиться загальний критерій, що враховує всі існуючі на практиці. Найпростішим способом рішення завдання багатокритеріальної оптимізації є вибір головного критерію ефективності й переклад інших у розряд критеріальних обмежень. У цьому випадку виходить завдання однокритеріальної оптимізації, для рішення якої на практиці існує досить багато ефективних і добре зарекомендованих методів [41, 42].
Для практичного використання представляє інтерес можливість виконання аналітичних розрахунків оптимальних режимів різання, що досить просто забезпечується методом геометричного програмування. Методика оптимізація режимів різання з використанням МГП, представлена в роботі [47]., дає аналітичне рішення для визначення оптимальних режимів різання при точінні за критерієм мінімальної собівартості.
Сучасні тенденції в оптимізації режимів різання спрямовані на рішення багатокритерійних завдань, що забезпечують одночасне поліпшення параметрів обробки за різними критеріями. Одним з напрямів багатокритерійної оптимізації є використання мультиплікативної свертки критеріїв, що дозволяють різні критерії оптимізації привести до єдиного критерію, що забезпечує найкраще поєднання кожного з них [48].
Представляє інтерес подальший розвиток МГП із застосуванням мультиплікативних критеріїв з урахуванням змінності параметрів процесу різання при обробці криволінійних поверхонь.
6. Визначення впливу кінематичних кутів у плані леза інструмента на шорсткість криволінійних поверхонь
Забезпечення заданого рівня якості деталей машин під час їх механічної обробки &ndash важлива задача технології машинобудування, в зв’язку з чим виконані дослідження впливу на шорсткість оброблених поверхонь геометричних параметрів різального інструменту достатньо актуальні.
У наш час широко відомі загальні закономірності формування шорсткості оброблених поверхонь в залежності від умов механічної обробки, які є основою прогнозування рівня шорсткості на стадії проектування технологічних процесів та керування параметрами шорсткості на стадії виготовлення деталей машин.
Під час обробки криволінійних поверхонь має місце складний характер зміни як кінематичних геометричних параметрів леза інструменту, так і параметрів зрізу поверхневого шару, пов’язаний з кривизною поверхні, що суттєво ускладнює аналіз впливу цих параметрів на рівень шорсткості. Дослідження в цьому напрямку досить обмежені.
Метою представленої роботи є встановлення закономірностей формування шорсткості криволінійних поверхонь тіл обертання під час токарної обробки з урахуванням змінних кінематичних кутів у плані леза інструменту.
Під час обробки різцями середнє арифметичне відхилення профілю визначається наступними загальними рівняннями [51]:

де r – радіус при вершині різця; s – подача; φ – головний кут в плані різця; φ1 – допоміжний кут в плані різця; Rzі – розрахункова висота нерівностей профілю:

де γ – передній кут різця; Rи – висота нерівностей профілю на вершині різця; bс – величина пластичного відтиснення:
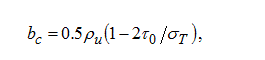
де ρи – радіус скруглення різальної кромки інструменту; σТ, τ0 – межа плинності і потужність оброблюваного матеріалу.
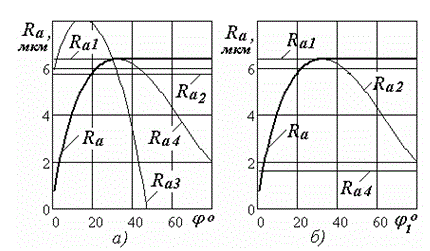
Рис.2.1 Графіки залежностей параметра шорсткості поверхні Rа від кутів в плані леза інструменту: головних φ – а) і допоміжних φ1 – б)
На рис. 2.1 наведені графіки залежностей параметра шорсткості поверхні Rа від кутів в плані леза інструменту для наступних умов: – радіус при вершині різця r = 0,5мм; подача s = 0,2мм/об; головний кут в плані; φ = 90° додатковий кут в плані φ 1 = 30°.
Графіки свідчать про те, що для заданих умов суттєвий вплив на шорсткість поверхні Rа кути в плані мають лише в діапазоні їх зміни до 30°, коли зі збільшенням як головних, так і допоміжних кутів в плані шорсткість зростає. Подальша зміна кутів у плані не впливає на шорсткість, яка визначається шорсткістю Rа1 і від них не залежить. Вплив головного кута у плані при постійному допоміжному куті визначається відповідно Rа4, при цьому шорсткість Rа2. Вплив допоміжного кута у плані при постійному головному куті визначається відповідно Rа2, при цьому постійною залишається шорсткість Rа2, яка залежить від кута в плані.
Під час обробки криволінійних поверхонь кінематичні куті в плані як головні, так і допоміжні одночасно змінюються (рис.2.2).
Приклад визначення кінематичних головних та допоміжних кутів у плані наведений для опуклої поверхні з постійним радіусом кривини (образуюча поверхні обертання – коло, центр прийнятої системи координат є центром кривини, тобто центром кола).
Положення вершини леза на вказаній криволінійній поверхні визначається миттєвим кутом повороту, який розраховується наступним чином:

де ζ=х/ρ – безрозмірна координата.
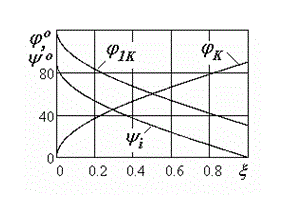
Рис. 2.2. Графіки зміни кінематичних кутів в плані леза інструменту під час обробки криволінійної поверхні
Кінематичні головний φК та допоміжний φ1К кути в плані визначаються відносно напрямку руху подачі DS миттєвим кутом повороту ψi:

Графіки зміни миттєвих кутів повороту ψi та кінематичних головних φК і допоміжних φ1К кутів у плані наведені на рис. 2.3.
Закономірності формування шорсткості вказаної криволінійної поверхні на відміну від раніш досліджених (рис. 2.1) полягають в одночасній зміні кінематичних головних і допоміжних кутів у плані.
Графіки зміни параметрів шорсткості Rаi в залежності від розташування вершини леза на обробленій криволінійній поверхні з урахуванням одночасної зміни кінематичних кутів у плані наведені на рис. 2.4.
Графіки свідчать про те, що для заданих умов вплив на шорсткість криволінійної поверхні Rа в діапазоні зміни кута до 30°, а координати до 0,1 (рис.3) має головний кут у плані ψ: при його збільшенні шорсткість зростає (вплив головного кута у плані ψ визначається шорсткістю Rа4). У зв’язку з тим, що допоміжний кут ψ1 по всій довжині криволінійної поверхні перевищує 30° (рис. 2.3), його вплив на шорсткість поверхні відсутній (вплив допоміжного кута у плані ψ1 визначається шорсткістю Rа3). Подальша зміна головного кута в плані ψ>30° також не впливає на шорсткість. Вона залишається постійною і визначається відповідно шорсткістю Ra1, яка від кутів у плані не залежить.
Таким чином, на підставі встановлених закономірностей зміни кінематичних кутів у плані леза інструменту під час токарної обробки криволінійних поверхонь визначений вплив головних та допоміжних кутів у плані леза інструменту на шорсткість обробленої поверхні. В результаті виконаних досліджень для заданих радіусів при вершині леза та подач встановлені кількісні зв’язки шорсткості з кутами у плані леза інструменту, які складають підставу для розробки методів керування шорсткістю під час обробки криволінійних поверхонь.
Перелік посилань
- Гжиров Р. И. Программирование обработки на станках с ЧПУ / Р.И. Гжиров, П.П. Серебреницкий. – Л.: Машиностроение, 1990. – 489 с.
- Дерябин А. Л. Программирование технологических процессов для станков с ЧПУ / А.Л. Дерябин. – М.: Машиностроение, 1984. – 51 с.
- Шарин Ю.С. Технологическое обеспечение станков с ЧПУ М.: Машиностроение, 1986. – 176с.
- Лещенко А.И. Анализ точности обработки фасонных поверхностей в зависимости от погрешности настройки инструментов на программ-ную операцию вісник приазовського державного технічного університету 2008 р. Вип. № 18 с. 129-133.
- Марецкая В.В. Моделирование технологических процессов механической обработки с использованием программного комплекса «Моделирование В Технических Устройствах» («МВТУ») // Известия вузов. Машиностроение. – 2004. – № 4. – с. 39-52.
- Марецкая В.В. Исследование отклонений профиля рабочей поверхности валка, вызванных упругими отжатиями элементов технологической системы // Справочник. Инженерный журнал. – 2006. – № 12. – с. 50–54.
- Марецкая В.В. К вопросу автоматизации направленного формирования показателей качества деталей // Вестник компьютерных и информационных технологий. – 2008. – № 3. – с. 29–34.
- Камсюк М.С., Грановский Э.Г. Определение отклонений, обусловленных отжатиями технологической системы при контурном фрезеровании // Известия вузов. Машиностроение. – 1981. – №5 – с. 139–143.
- Грановский Э.Г., Камсюк М.С. Точность обработки сложноконтурных поверхностей деталей // Основные направления развития технологии машиностроения: Труды МВТУ. – 1981. – № 348. – с.110–127.
- Технологическая наследственность в машиностроительном производстве / под ред. А.М. Дальского. – М.: Изд-во МАИ, 2000. – 364 с.
- Виноградов Ю.М. Применение химическиактивных веществ для повышения эффективности СОЖ при резании металлов / Ю.М.Виноградов. – М.: Изд. МДНТН, сб. №1, 1966, с. 1-13
- Зорев Н.Н. Обработка резанием тугоплавких сплавов / Н.Н. Зорев, З.М.Фетисова. – М.: Машиностроение, 1966, с. 64-69
- Мерчант М.Ю., В сб. Международная конференция по смазке и износу / М.Ю. Мерчант. – М.: ИЛ., 1956. с. 95-105
- Матвеевский Р.М. Температурная стойкость граничных смазочных слоев и твердых смазочных покрытий при трении металлов и сплавов / Р.М.Матвеевский. – М.: Наука, 1971. – 213 с.
- Носовский И.Г. Исследование изнашивания металлов в различных газовых средах / И.Г.Носовский. – Редиздат Аэрофлота, 1956. – 120 с.
- Чубаров А.Д. Деформирование и роль температурного фактора в процессе резания титановых сплавов / А.Д. Чубаров, Н.Н. Новиков. - М.: Вестник машиностроения, 1959, №9. – с. 40-43
- Латышев В.Н. Повышение эффективности СОЖ / В.Н Латышев – М.: Машиностроение, 1975. – 88 с.
- Смазочно-охлаждающие технологические средства для обработки металлов резанием: Справочник / Под ред. С.Г. Энтелиса, Э.М. Берлинера. – М.: Машиностроение, 1986. – 352 с., ил.
- Боуден Ф.П. Трение и смазка твердых тел / Ф.П. Боуден, Д.А. Тейбор. - М.: Машиностроение, 1968, 493 с.
- Кривоухов В.А. Обрабатываемость резанием жаропрочных и титановых сплавов / В.А. Кривоухов. - М.: Машгиз, 1961. - 270 с.
- Латышев В.Н. Влияние газовой среды и смазочного материала на температуру поверхностей трения / В.Н. Латышев. - Изд. АН СССР: Маши-ностроение 1971, №4. – с. 109-111
- Топлива, смазочные материалы, технические жидкости. Ассортимент и применение: Справ. Изд./ К.М. Бадыштова, Я.А. Бердштадт, Ш.К. Богданов и др.; Под ред. В.М. Школьникова. – М.: Химия, 1989. – 432с.
- Худобин Л.В. Техника примения смазочно-охлаждающих средств в металлообработке / Л.В. Худобин, Е.Г. Бердичевский. – М.: Машинострое-ние, 1977. – 189 с. с ил.
- Справочник по обработке металлов резанием / Ф.Н. Абрамов, В,В. Коваленко, В.Е. Любимов и др. - К.: Техника, 1983. – 239 с.. ил. – Биб-лиогр.: с. 235-237.
- Прогрессивные режущие инструменты и режимы резания металлов. Справочное издание / В.И. Баранчиков, А.В. Жариков, Н.Д. Юдина и др. М.: Машиностроение, 1990.
- Базовый ассортимент смазочно-охлаждающих технологических сред для обработки металлов резанием // Тематический обзор. – Централь-ный научно-исследовательский институт информации и технико-экономических исследований нефтеперерабатывающей и нефтехимической промышленности. 1986 г.
- Топлива, смазочные материалы, технические жидкости. Ассортимент и применение: Справочник / И.Г. Анисимов, К.М. Бадыштова, С.А. Бнатов и др.; Под ред. В.М, Школьникова. Изд. 2-е перераб. И доп. – М.: Из-дательский центр «Техинформ», 1999. – 596 с.: ил.
- Расчет тепловых потоков и температур резания при точении с использованием смазочно-охлаждающих жидкостей. / Т.Г. Ивченко (ДонНТУ, г. Донецк, Украина) Надійність інструменту та оптимізація технологічних систем. Збірник наукових праць. – Краматорськ, ДДМА. вип.26, 2010. – c. 90-96.
- Теоретичні основи керування температурою різання з використанням охолоджуючих середовищ / Т.Г. Івченко (ДонНТУ, м. Донецьк, Україна) Надійність інструменту та оптимізація технологічних систем. Збірник наукових праць. Вип.18. – Краматорськ: ДДМА, 2006. – c. 39-45.
- Вплив способу подачі охолоджуючого середовища на температуру різання / Т.Г. Івченко, В.Г. Нечепаєв, О.М. Гнитько (ДонНТУ, м. Донецьк, Україна) Надійність інструменту та оптимізація технологічних систем. Збірник наукових праць. Вип.16 . – Краматорськ: ДДМА, 2005. – c. 34-38
- Интенсификация процесса резания сборными режущими инструментами с использованием охлаждающих технологических сред / Александр Михайлов, Татьяна Ивченко, Ольга Дубоделова (ДонНТУ, г. Донецк, Украи-на) Tehnologii Modern, Calitate, Restructurare. Vol. 1. – Chisinau: Universitates Tecnica a Moldovei, 2005. c. 289-295
- Влияние функциональных технологических свойств смазочно-охлаждающих технологических сред на выбор оптимальных режимов реза-ния / Вадим Богуславский, Татьяна Ивченко Пер. с англ. Ирина Зайцева In-fluence of functional properties of technological cutting fluid on a choice of opti-mum cutting regimes [электронный ресурс]. – Режим доступа: http://www.modtech.ro/vol3no22011/2_FINAL_Bogouslavskiy_Vadim.pdf.
- Повышение производительности обработки труднообрабатываемых материалов с применением смазочно-охлаждающих жидкостей / В.А. Богуславский, Т.Г. Ивченко, Зантур Сахби (ДонНТУ, г. Донецк, Украина) Наукові праці Донецького національного технічного університету. Серія: Машинобудування і машинознавство. Випуск 7(166). – Донецьк: ДонНТУ, 2010. – c. 9-16.
- Vadim Bogouslavskiy, Tatiana Ivchenko. Optimisation of cutting regimes at application of technological cutting fluid // ModTech International Conference 25-27th May 2011, Vadul lui Voda: Chisinau, 2011. P. 669-672. (Index to Scientific & Technical Proceedings of Thomson Scientific - Institute for Scientific In-formation (ISI).
- Клушин М.И. Определение стойкости режущих инструментов, обеспечивающих получение максимально возможной прибыли и производи-тельности общественного труда / М.И. Клушин, Г.Г. Аносов. – Вестник ма-шиностроения, №6, 1970. – с.74-76.
- Макаров А.Д. Оптимизация процессов резания / А.Д. Макаров – М.: Машиностроение, 1976. – 278 с.
- Старков В.К. Обработка резанием. Управление стабильностью и качеством в автоматизированном производстве / В.К. Старков. – М.: Маши-ностроение, 1989. – 296 с.
- Старков В.К. Технологические методы повышения надежности обработки на станках с ЧПУ / В.К. Старков. – М.: Машиностроение, 1984. – 120 с.
- Старков В.К. Оптимизация процесса резания по энергетическим критериям / В.К. Старков, М.В. Киселев // Вестник машиностроения. – М.: 1989, №4. – с. 41-45.
- Якобс Г. Оптимизация резания. Параметризация способов обработки резанием с использованием технологической оптимизации / Г. Якобс, Э.Якобс, Д. Кохан // Пер. с нем. – М.: Машиностроение, 1981. – 279 с.
- Гильман А.М. Оптимизация режимов обработки на металлорежущих станках / А.М. Гильман. – М.: Машиностроение, 1972. – 188 с.
- Евтушенко Ю.Г. Методы решения экстремальных задач и их применение в системах оптимизации / Ю.Г. Евтушенко. – М.: Наука, 1982. – 432 с.
- Кроль О.С. Оптимизация и управление процессом резания. Учеб. Пособие. / О. С.Кроль, Г.Л. Хмелевский. – К.: УМК ВО, 1991. – 140 с.
- Карпусь В. Е. Системные критерии механообрабатывающих технологических систем / В.Е. Карпусь С.В. Луцкий. // Резание и инструмент в технологических системах. – Харьков: ХГПУ, 2000, Вып.57. – с.105-109
- Реклейтис Г. Оптимизация в технике: В 2-х кн. Кн. 2. / Г. Реклейтис, А.Рейвиндран, К. Рэгсдел. // Пер. с англ. – М.: Мир, 1986, - 320 с.
- Ивченко Т. Г. Использование метода геометрического программирования для расчета оптимальных режимов резания при точении / Т.Г.Ивченко Научный вестник ДГМА. – Краматорск: ДГМА, 2011. – №2 (8 Е). с.110-116.
- Король K.O., Ивченко Т.Г. Многокритериальная оптимизация режимов резания на основе мультипликативной свертки критериев ИНЖЕНЕР: студенческий научно-технический журнал / Донецк: ДонНТУ, 2012, № 13. - с.124-128.
- Суслов А.Г. Качество поверхностного слоя деталей машин / А.Г. Суслов. - М.: Машиностроение, 2000. - 320с.
- Качество машин: Справочник. В 2 т. Т.1 / А.Г. Суслов, Э.Д. Браун, Н.А. Виткевич и др. - М.: Машиностроение, 1995. - 256с.
- Грановский Г.И., Грановский В.Г., Резание металлов: Учебник для вузов / Г.И. Грановский, В.Г. Грановский. - М.: Высш. шк.,1985. - 304с.
Зауваження! При написанні даного реферату магістерська робота ще не завершена. Остаточне завершення: грудень 2013 р. Повний текст роботи та матеріали по темі можуть бути отримані у автора або його керівника після зазначеної дати.