Реферат за темою випускної роботи
Зміст
- Вступ
- 1. Сучасний стан питання і вибір напрямів дослідження
- 1.1 Різьбові з'єднання як елемент металургійних машин
- 1.2 Визначення необхідного зусилля затягування
- 1.3 Контроль затягування різьбових з'єднань
- 1.4 Постановка завдань дослідження
- Висновки
- Перелік посилань
Вступ
Різьбові з'єднання є найбільш відповідальними елементами металургійного обладнання [1]. У ряді випадків неправильне затягування різьбових з'єднань металургійних машин призводить до значного погіршення роботи механізмів, що відповідно впливає на надійність і довговічність роботи машин.
Різьбові з'єднання працюють переважно з попереднім затягуванням, завдяки якому зовнішнє змінне навантаження передається на різьбову деталь лише частково. На практиці при своєчасному попередньому затягуванні напруги зменшуються в результаті нерівностей на стиках, релаксації напруги і так далі. Застосування методів контролю стає обов'язковим для відвертання поломок механізмів.
При виборі найбільш ефективного методу контролю слід врахувати ряд чинників : тип конструкції, вимоги до надійності, якість виготовлення, що оточують умови, кваліфікація персоналу – які не дозволяють зробити однозначний і простий вибір. Істотним недоліком є умова застосування певного методу контролю лише для відповідної групи різьбових з'єднань. Наприклад: метод контролю кута повороту гайки – простий у виконанні, проте не придатний для з'єднань з короткими болтами, оскільки розрахунковий кут повороту гайки для таких болтів невеликий і погрішності методу позначаються найбільшою мірою; метод контролю моменту затягування гайки – грунтований на вимірі моменту, що обертає, за допомогою проградуйованих ключів, не ефективний для великогабаритних різьбових з'єднань.
Можливе рішення цієї проблеми – розробка методу контролю, який зміг би охопити усі основні види різьбових з'єднань (довгі, короткі, великогабаритні) металургійних машин. Для цього необхідно виявити недоліки існуючих методів контролю, математично обгрунтувати найбільш перспективний метод і підтвердити його експериментальним шляхом.
Ефективність грунтується на проведенні своєчасних ремонтних робіт після затягування або заміни різьбових з'єднань, зниження динамічного навантаження і зменшення кількості відмов, пов'язаних з різьбовими з'єднаннями.
1. Сучасний стан питання і вибір напрямів дослідження
1.1 Різьбові з'єднання як елемент металургійних машин
Різьбове з'єднання – роз'ємне з'єднання деталей машин за допомогою гвинтової або спіральної поверхні(різьблення). Це з'єднання найбільш поширене із-за його численних достоїнств. У простому випадку для з'єднання необхідно закрутити дві деталі, що мають різьблення з відповідними один до одного параметрами. Для роз'єднання необхідно виконати дії в зворотному порядку [2,3].
Резьба – рівномірно розташовані виступи або западини постійного перерізу, утворені на циліндричній або конічній поверхні по гвинтовій лінії з постійним кроком. Є основним елементом різьбового з'єднання.
Класифікація і основні ознаки резьб [4]:
- одиниця виміру діаметру (метрична, дюймова, модульна, питчевая різьби);
- розташування на поверхні (зовнішнє і внутрішнє різьби);
- напрям руху гвинтової поверхні (права, ліва);
- число заходів (одно- і багатозахідна);
- профіль (трикутний, трапецеїдальний, прямокутний, круглий та ін.);
- поверхня, на якій розташовано різьба (циліндричне різьблення і конічне різьблення);
- призначення (кріпильна, кріпильний ущільнювач, ходова та ін.).
Метричне різьблення (рисунок 1) є основним типом кріпильного різьблення. Профіль різьблення встановлений ГОСТ 9150-81 і є рівностороннім трикутником з кутом профілю α = 60°. Профіль різьблення на стержні відрізняється від профілю різьблення в отворі величиной притуплювання його вершин і западин. Основними параметрами метричного різьблення є: номінальний діаметр – d(D) і крок різьблення – Р, встановлювані ГОСТ 8724–81 [5].
По ГОСТ 8724-81 кожному номінальному розміру різьблення з великим кроком відповідає декілька дрібних кроків. Різьблення з дрібним кроком застосовуються в тонкостінних з'єднаннях для збільшення їх герметичності, для здійснення регулювання в приладах точної механіки і оптики, з метою збільшення опірності деталей самоотвинчиванию.
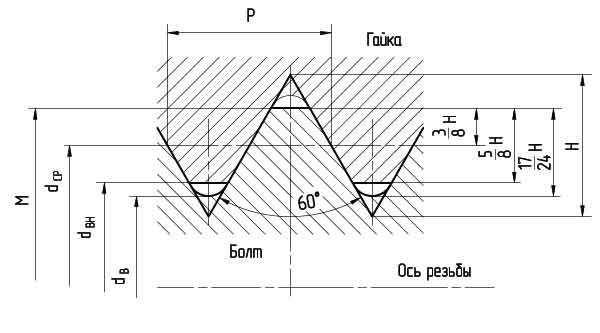
Рисунок 1 – Метрична різьба
Характеристики різьбових з'єднань
Достоїнства [6]:
- технологічність;
- взаємозамінюваність;
- універсальність;
- надійність;
- масовість.
Недоліки:
- розкручування (самовідвінчуання) при змінних навантаженнях і без застосування спеціальних пристроїв (засобів);
- отвори під кріпильні деталі викликають концентрацію напруги;
- для ущільнення (герметизація) з'єднання необхідно використати додаткові технічні рішення.
Стандартні кріпильні різьбові деталі дуже різноманітні за формою, точності виготовлення, матеріалу, покриттю. Їх розділяють на деталі загального призначення і спеціальні, призначені для застосування в певних видах виробів або в особливих умовах [7].
Основними є болти, гвинти, шпильки і анкери.
Болт (рисунок 2) складається з двох частин: голівки і стержня з різьбленням. У більшості конструкцій болтів на його голівці є конічна фаска, що згладжує гострі краї голівки і полегшує накладення гайкового ключа при згвинченні.
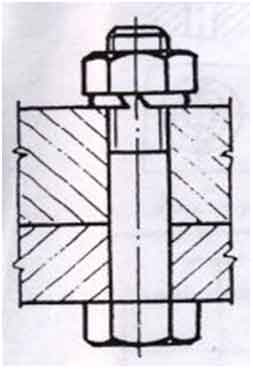
Рисунок 2 – Болт
Болти, що випускаються промисловістю, розрізняють [8]:
- за формою і розмірам голівки;
- за формою стержня;
- по кроку різьблення;
- за характером виконання;
- по точності виготовлення.
Форма і розміри голівки болта залежать від призначення і умов роботи.
Болти з шестигранними голівками отримали широке застосування в промисловості.
Шпилька – кріпильна деталь, призначена для з'єднання деталей між собою, що мають гладкі отвори або різьбові отвори, виконана у вигляді циліндричного стержня на кінцях якого є різьблення [9].
Шпилька різьбова використовується для стягання і фіксації на заданій відстані елементів металевих конструкцій з метричним різьбленням. Також шпилька різьбова може використовуватися для кріплення підвісних конструкцій.
Різьбові з'єднання є одними з найбільш відповідальних елементів металургійного устаткування. У ряді випадків неправильне затягування призводить до значного погіршення роботи механізмів, що відповідно впливає на надійність і довговічність роботи машини. Тому необхідно досліджувати основні функції різьбових з'єднань, якими є правильне затягування і контроль.
1.2 Визначення необхідного зусилля затягування
При обслуговуванні металургійного устаткування постійно виникають проблеми, пов'язані з різьбовими з'єднаннями, які вимагають негайного усунення. Щоб уникнути цих проблем необхідно знати правильну технологію затягування. Цим питанням займалися такі фахівці: Седуш С.В., Седуш В.Я., Биргер И.А., Иоселенич Г.Б., Кравець Л.С., Песин Л.М. і інші. У книзі Биргер И.А., Иоселенич Г.Б. Різьбові і фланцеві з'єднання
розглянуті загальні принципи проектування різьбових і фланцевих з'єднань. Приведені зведення про розрахунок різьбових з'єднань на міцність при постійних і змінних навантаженнях в умовах нормальних, знижених і підвищених температур; показаний вплив конструктивних і технологічних чинників на міцність з'єднань. Дані рекомендації по оптимальних конструкціях різьбових і фланцевих з'єднань. У книзі Седуш С.В. Розрахунок і конструювання гідравлічних інструментів
, Кравець Л.С., Песин Л..
Технологія затягування
Велику частину різьбових з'єднань, вживаних в сучасних машинах, збирають з попереднім затягуванням. Правильне затягування з'єднання – одно з основних умов надійної роботи з'єднання.
Напругу попереднього затягування встановлюють відповідно до умов герметичності і щільності(жорсткості) стику. Останнє є необхідною умовою забезпечення міцності різьбових з'єднань при змінних навантаженнях [1]:
σ0 = σр(1-x),
где σ0 = F0/A1 – напруга попереднього затягування(F0 – сила затягування);
σр = Fр/A1 – номінальна напруга від найбільшого зовнішнього (робочою) навантаження, що виникає в стержні болта (шпильки) при роботі;
х – коефіцієнт основного навантаження (зазвичай х = 0,2 ... 0,4).
При σ0 ≤ σр(1-x) стик розкривається і зовнішнє навантаження повністю передається на болт, різко знижуючи довговічність з'єднання.
На практиці, як правило, напруга попереднього затягування зменшується в результаті того, що зім'яло нерівностей на стиках, релаксації напруги і т. д. Можливо також підвищення робочих навантажень при роботі машини на нерозрахунковому режимі (наприклад, внаслідок гідравлічного удару, при роботі на резонансному режимі та ін.). З урахуванням цього розрахункову напругу затягування збільшують в ν раз:
σ0 = νσр(1-x).
Згідно з умовою щільності стику ν = 1,25 ... 2,00 при постійному вантаженні і ν – 2,5 ... 4,0 при змінному вантаженні.
Відповідно до умови герметичності ν = 1,3 ... 2,5 при м'яких прокладеннях; ν = 2,5 ... 3,5 при металевих фасонних прокладеннях; ν = 3,0 ... 4,0 при плоских металевих прокладеннях [1].
Підвищення напруги попереднього затягування призводить до істотного зменшення долі робочого навантаження, що сприймається болтами з'єднання, і сприяє її збереженню при експлуатації.
Таким чином, велика сила затягування є ефективним засобом підвищення надійності роботи різьбових з'єднань (рисунок 3).
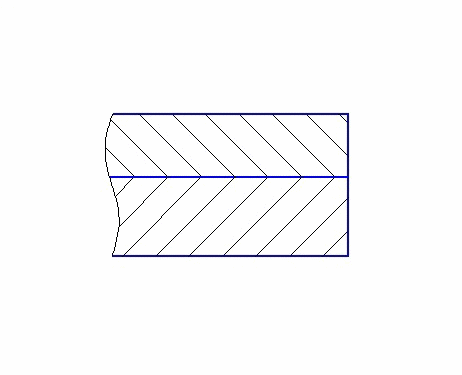
Рисунок 3 - Затягування різьбового з'єднання
(анімація: 6 кадрів, 6 циклів повторення, 45,8 кілобайт
Щоб уникнути появи пластичних деформацій (залишкового подовження і скручування) верхню межу напруги затягування обмежують значенням коефіцієнта запасу міцності, що мінімально допускається, по постійній напрузі.
Слід зазначити, що збільшення напруги затягування іноді знижує граничну амплітуду циклу (межа витривалості з'єднання). Проте в цьому випадку доля зовнішнього навантаження, що сприймається болтом, як правило, істотно зменшується [1].
Основні чинники, що впливають на правильну роботу різьбових з'єднань
Попри те, що на перший погляд різьбове з'єднання є дуже простим елементом устаткування, воно може стати джерелом проблем при монтажно-демонтажних і ремонтних роботах. На практиці з'ясовується, що для конструювання різьбових з'єднань потрібний методичний і точний підхід, що виключає помилки. Дослідження показують, що ушкодження в різьбових з'єднаннях виникають, головним чином, із-за наступних чинників [10-15]:
- були неправильно підібрані компоненти з'єднання;
- недостатнє або перевищене зусилля попереднього затягування;
- нерівномірний розподіл зусилля попереднього затягування.
У зв'язку з цим, найбільш важливим стає питання правильного вибору компонентів вживаних різьбових з'єднань і визначення правильної величини зусилля попереднього затягування.
Для досягнення надійного різьбового з'єднання вирішальне значення має правильне значення зусилля затягування. Вона має бути необхідною. Чим точніше виконано попереднє затягування, тим якісніше буде з'єднання, однак, з іншого боку, зі збільшенням точності збільшується вартість процедури попереднього затягування.
Недостатнє попереднє затягування може привести до [10-20]:
- зміщенню поверхні з'єднання під дією осьового навантаження;
- зростанню амплітуди напруги болта;
- старінню гвинта;
- відгвинчуванню гайки від вібрації;
- ковзанню з'єднання під дією зрушуючого моменту.
Занадто сильне попереднє затягування може привести до [10-20]:
- статичному перевантаженню болта;
- відгвинчуванню болта під дією зовнішнього розтягуючого навантаження в результаті пластичного подовження;
- розриванню болти ще при попередньому затягуванні.
Є два найбільш суттєвих чинника тих, що знижують міцність різьбового з'єднання [1]:
- самоводгвінчування;
- послаблення зусилля затягування.
О самоводгвінчуванні:
- після закінчення процесу фіксації у болтовому з'єднанні утворюється навантаження стискування, оскільки болт затягується, немов пружина і гайка, переміщаючись до голівки болта, починає створювати між частинами, що фіксуються, стискаючу силу. Як тільки напруга стискування зникає, виникають умови, сприяючі відкручуванню гайки. Існуюче в різьбленні, а також між гайкою і голівкою болта тертя утрудняє затягування болта [2];
- коли на різьбове з'єднання впливають змінні навантаження або вібрація, знижується викликаний тертям ефект блокування, що дозволяє гайці ковзати по різьбленню вільно, зменшуючи силу зчеплення. Вібраційні дії можуть бути в поперечному або подовжньому напрямі, а також комбінованими, такими, що діють в обох напрямах. Найбільшу небезпеку представляють поперечні вібрації і знакозмінні горизонтальні навантаження. Вони досить швидко призводять до послаблення звичайних незафіксованих різьбових з'єднань. При чергуванні подовжніх вібрацій і осьових навантажень послаблення різьбових з'єднань менш значне.
Про послаблення зусилля затягування:
- в результаті змін осьових навантажень на болт, а також температурного режиму, відбувається збільшення довжини болта і, як результат, зменшення зусилля затягування. Причиною подібного зменшення може бути і деформація матеріалу прокладення. Зміна в довжині може статися при: просіданні, коли шорсткі поверхні контактуючих деталей (наприклад, шайби, гайки) під впливом тиску болтового натягнення деформуються [5];
- прослизанні, коли тиск на опорну поверхню гайок або болтів вищий за опір стискування матеріалів деталей, що сполучаються.
Інструмент
При затягуванні різьбових з'єднань паралельно робиться контроль зусилля попереднього затягування. Основними інструментами для затягування різьбових з'єднань є:
- Динамометричний ключ (рисунок 4) – це прецизійний інструмент для затягування різьбових з'єднань з точно заданим моментом. При проектуванні будь-яких будівельних конструкцій, будь-якого промислового або будівельного устаткування, будь-якої техніки, передбачається її складання з певним значенням моменту, що крутить, для кожного конкретного з'єднання [1-4].
- На відміну від традиційних інструментів гідравлічні пристосування (рисунок 5) створюють осьовий тиск, який забезпечує надійніше затягування і зменшує вірогідність зрізування і послаблення болта під навантаженням. Крім того, їх здатність ефективного використання механічних умов дозволяє зменшити втому болта в умовах динамічних навантажень. Гідравлічний принцип затягування болтів має наступні переваги [1]:
- точно відома величина розтягування від первинного навантаження;
- величина розтягування від первинного навантаження може бути максимально наближена до межі пружності болта;
- можливість одночасного затягування декількох болтів;
- гідравлічні пристосування простіше і безпечніше в експлуатації, ніж динамометричні ключі;
- ідеально підходить для систем автоматичного затягування болтів.
- Гайковерт – ручний інструмент, призначений для закручування і відкручування різьбових з'єднань на болтах і гайках, а також для укручування і викручування глухарів і анкер-шурупов, з регульованим моментом, що крутить [4].
- Ключ для виміру кута повороту гайки (рисунок 6) – вимір кута повороту гайки при монтажі з точністю 10... 15° не викликає утруднень, його виконують із застосуванням мірних підкладок.
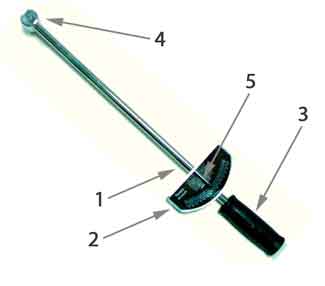
Рисунок 4 – Динамометричний ключ
1 – корпус, 2 – шкала, 3 – ручка, 4 – квадрат для торцевої голівки, 5 – стрілка
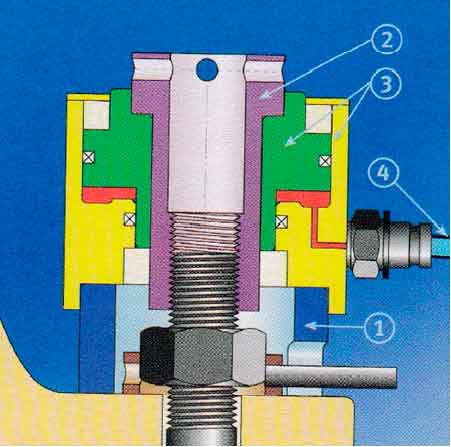
Рисунок 5 – Гідроключ
1 – Патрон, що закручує, 2 – Гідравлічне пристосування, 3 – Робоча гайка, 4 – Гідравлічний тиск
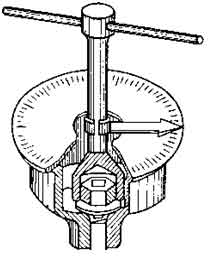
Рисунок 6 – Ключ для затягування з'єднань, контрольованої по куту повороту гайки
Необхідність вивчення питання зусилля попереднього затягування яскраво відображається при моделюванні несправностей різьбових з'єднань.
Моделювання несправностей різьбових з'єднань
Побудова моделі є процедурою визначення головної причини несправності на основі існуючого переліку видів відмов. Складання блок-схеми моделі у вигляді дерева причинно-наслідкових зв'язків зазвичай використовують, щоб побачити співвідношення причин і наслідків між відмовами різних видів. Усі дані для процедури діагностування вже існують і не вимагають повторної оцінки. Якщо модель використовують в цілях побудови прогнозу, то відповідні дані мають бути спрогнозовані [Гост Р ИСО 13379-2009].
Дерево причинно-наслідкових зв'язків упорядковує наявні знання таким чином:
- з минулого досвіду відома головна причина відмови одного або декількох видів;
- співвідношення між відмовами різних видів можуть бути описані через чинники впливу або критерії ініціалізації;
- діагностичні ознаки відмови деякого виду можуть ініціювати інші відмови, робити або не робити на них впливу.
Дерево причинно-наслідкових зв'язків несправностей різьбових з'єднань показане на рисунке 7.
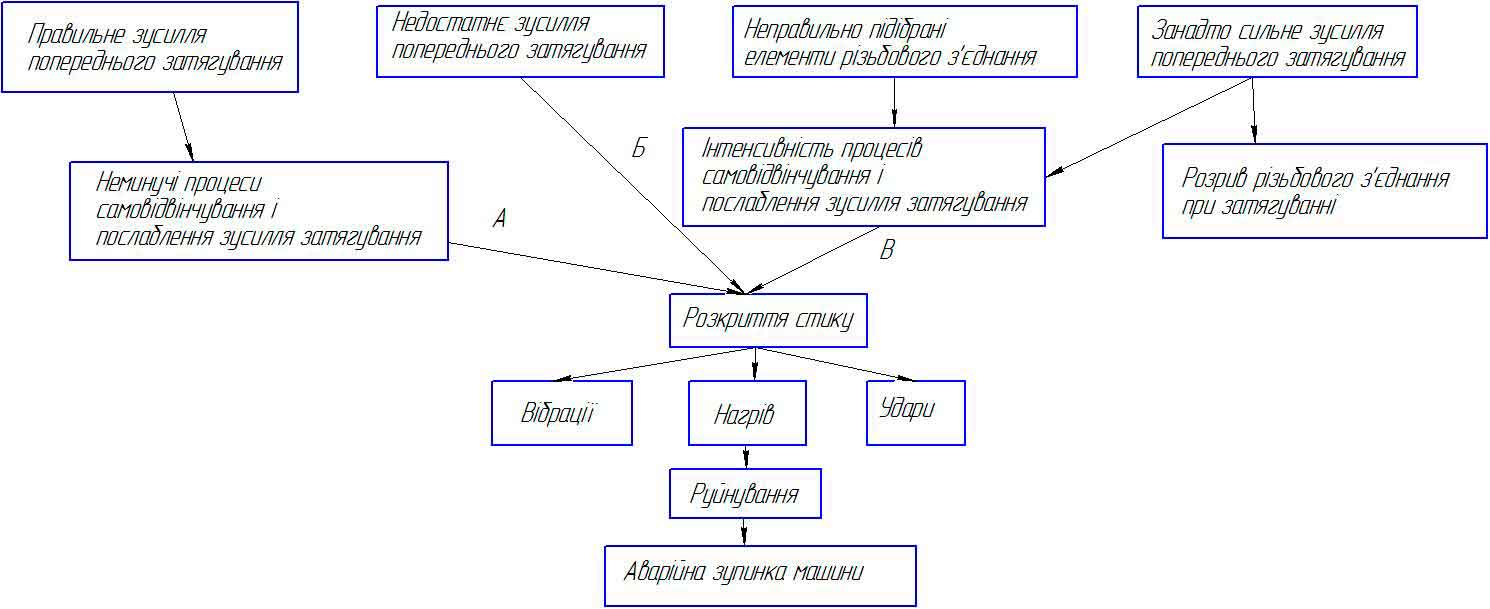
Рисунок 7 – Дерево причинно-наслідкових зв'язків несправностей різьбових з'єднань
А – мінімальна швидкість процесів, Б – стик розкритий спочатку, В – висока швидкість процесів
На рисунку видно, що найнебезпечніший стан при недостатньому зусиллі попереднього затягування (Б). В цьому випадку стик розкритий спочатку, тому удари і вібрації призводять до неправильної роботи усього механізму, а також до руйнування різьбового з'єднання. При неправильному підборі компонентів і занадто сильному зусиллі (В) – середня швидкість розкриття стику.
Нормальна робота машини залежить (А) від правильного вибору компонентів різьбового з'єднання і сили попереднього затягування. При цьому неминучі процеси самоотвинчивания і послаблення зусилля проходять при мінімальних швидкостях.
З дерева причинно-наслідкових зв'язків видно, що після розкриття стику різьбове з'єднання працює неправильно, слідством чого стають аварійні зупинки машини. Тому основними завданнями цієї роботи є виявлення залежностей різних характеристик до і після розкриття стику, розробка експлуатаційного методу контролю, який дозволить своєчасного запобігати наслідкам послаблення зусилля попереднього затягування.
1.3 Контроль затягування різьбових з'єднань
Контроль різьбових з'єднань здійснюється з метою підтримки заданого зусилля затягування. Його розрізняють двох видів:
- монтажний;
- експлуатаційний.
Монтажний контроль застосовується безпосередньо при затягуванні різьбового з'єднання. Виділяють такі основні методи:
- Акустичний контроль механічної напруги в різьбових з'єднаннях – грунтований на вимірі характеристик пружних хвиль, що поширюються в середовищі, розрахунок діючої величини механічної напруги здійснюється на основі прецизійних вимірів часу поширення УЗ хвиль в матеріалі [12-15].
- Контроль по подовженню болта (гвинта) – грунтований на вимірі зміни відстані при затягуванні між кінцем болта і корпусом, застосовуючи для цього індикатори або шаблони. Для відповідальних різьбових з'єднань застосовують дротяні тензодатчики (наклеювані на гладку частину болта або такі, що заливаються в центральний отвір), які після виміру можуть залишатися на деталі при подальшій експлуатації [1].
- Метод контролю по куту повороту гайки – в цьому випадку в технічних умовах на складання різьбового з'єднання вказують кут повороту гайки(у градусах). Вимір кута повороту гайки при монтажі з точністю 10 ... 15° не викликає утруднень; його виконують із застосуванням мірних підкладок, шаблонів і ін..
- Контроль по моменту затягування, що крутить, гайки – Грунтований на вимірі моменту, що обертає, за допомогою проградуйованих ключів: динамометричних і граничних. Затягування припиняється при досягненні моментом на ключі значення, встановленого технічними умовами.
- Метод осьового витягу шпильки (болта) – полягає в попередньому розтягуванні болта (шпильки) із зусиллям, рівним необхідному зусиллю затягування, подальшим закручуванням гайки від руки до упору в опорну поверхню і зняттям навантаження з болта скиданням гідравлічного тиску, після чого з'єднання отримує задане зусилля затягування. Шпилька (болт) повинні виступати над гайкою не менше чим на 0,8d, де d – діаметр шпильки.
Експлуатаційний контроль нині не використовується на металургійних підприємствах. Тому у наш час це питання актуальне. При рішенні можливе скорочення тимчасового ресурсу при технічному обслуговуванні і ремонті, що приведе до збільшення об'єму продукції, що реалізовується.
1.4 Постановка завдань дослідження
Метою цієї роботи є розробка експлуатаційного методу контролю зусилля затягування.
Завдання:
- визначити основні властивості різьбових з'єднань як елементу металургійних машин;
- розробити математичну модель у вигляді залежностей;
- запропонувати гіпотези по проведенню експерименту;
- підготувати стенд для реалізації експерименту;
- провести експеримент;
- оцінити результати експерименту;
- перевірити відповідність результатів проведення експерименту з адекватністю математичної моделі;
- практичне застосування;
- перевірити ефективність розробленого методу контролю.
Висновки
Експлуатаційний контроль нині не використовується на металургійних підприємствах. Тому у наш час це питання актуальне. При рішенні можливе скорочення тимчасового ресурсу при технічному обслуговуванні і ремонті, що приведе до збільшення об'єму продукції, що реалізовується.
У рамках проведених досліджень виконано:
- Досліджені різьбові з'єднання, як елементи металургійних машин.
- На підставі аналізу літературних джерел виділені основні види різьбових з'єднань.
- Досліджена методика визначення зусилля попереднього затягування.
- Виявлені основні методи контролю зусилля затягування різьбових з'єднань.
- Розроблено дерево причинно-наслідкових несправностей різьбових з'єднань.
При написанні цього реферату магістерська робота ще не завершена. Остаточне завершення: листопад 2013 року. Повний текст роботи і матеріали по темі можуть бути отримані у автора або його керівника після вказаної дати.
Перелік посилань
- Седуш С.В. Расчет и конструирование гидравлических инструментов / С.В. Седуш – Донецк: 2004. – 152 с.
- Биргер И.А., Иоселенич Г.Б. Резьбовые и фланцевые соединения / И.А. Биргер, Г.Б. Иоселенич – М.: Машиностроение, 1990.– 368 с.
- Сидоров В.А., Седуш В.Я., Кравченко В.М. Техническое диагностирование механического оборудования / В.А. Сидоров, В.Я. Седуш, В.М. Кравченко. – Донецк: ООО «Юго Восток, Лтд», 2009. – 459 с.
- Портной Л.С., Песин Л.М. Ручные машины для монтажных работ / Л. С. Портной, Л.М. Песин. – К.: Будівельник, 1977. – 132 с.
- Рабинер Е.Г. Монтаж и эксплуатация подшипниковых узлов / Е.Г. Рабинер. – М.: Машгиз, 2–е издание, 1960. – 275 с.
- Бабат Г.И. Индукционный нагрев металла и его промышленное применение / Г.И. Бабат. – М., Л.: Энергия, 2–е изд., 1965. – 552 с.
- Бейзельман Р.Д., Цыпкин Б.В. Перель Л.Я. Подшипники качения / Р.Д. Бейзельман, Б.В. Цыпкин, Л.Я. Перель. – М.: Машиностроение, 1975.
- Федоров Б.Ф. Рациональный способ рачпрессовки и запрессовки деталей / Б.Ф. Федоров. – М., Свердловск: Машгиз, 1955. – 68 с.
- Александров М.П. Подъемно-транспортные машины / М.П. Александров. – М.: Высшая школа, 1972.
- Александров Б.И., Василец Ф.П. Влияние технологии изготовления и асимметрии цикла на циклическую прочность и долговечность соединений / Б.И. Александров, Ф.П. Василец. - Вестник машиностроения, 1964, № 4.
- Байков Б.А. Влияние пониженных температур на прочность крепежных винтов / Б.А. Байков. – Изв. вузов.: Машиностроение, 1968, № 6.
- Биргер И.А. Расчет резьбовых соединений / И.А. Биргер. – М.: Оборонгиз, 1959 – 252 с.
- Биргер И.А., Иосилевич Г.Б. Резьбовые соединения / И.А. Биргер, Г.Б. Иосилевич. – М.: Машиностроение, 1973 – 256 с.
- Биргер И.А., Шорр Б.Ф., Иосилевич Г.Б. Расчет на прочность дета¬лей машин / И.А. Биргер, Б.Ф. Шорр, Г.Б. Иосилевич. – М.: Машиностроение, 1979 – 702 с.
- Биргер И.А., Кутепова Т.В. Распределение нагрузки в резьбовых соединениях тонкостенных деталей / И.А. Биргер, Т.В. Кутепова – Вестник машиностроения, 1973, № 5.
- Вольфсон А.С., Либерман Л.Я. Испытание на длительную прочность резьбовых соединений / А.С. Вольфсон , Л.Я. Либерман. – Заводская лаборатория, 1968, № 11.
- Гоулд Д., Микич М. Площади контакта и распределение давлений в болтовых соединениях / Д. Гоулд, М. Микич. – Конструирование и технология машиностроения, 1972, № 3 – 99 с.
- Зенкевич О. Метод конечных элементов в технике / О. Зенкевич. – М.: Мир, 1975 – 539 с.
- Змиевский В.И., Замилацкий Е.П., Приведенцева В.С. Свинчиваемость резьбовых соединений из титановых сплавов / В.И. Змиевский, Е.П. Замилацкий, В.С. Приведенцева. – Вестник машиностроения, 1975, № 1 – 47 с.
- Иванов С.И., Шатунов М.П., Красота В.К. Меридиональные остаточные напряжения в резьбовой части болта / С.И. Иванов, М.П. Шатунов, В.К. Красота. – Вестник машиностроения, 1982, № 11 – 38 с..