Content
- Introduction
- 1. Relevance of the topic
- 2. Tasks and objectives
- 3. Estimated newness
- Conclusion
- References
Introduction
Protection of heating systems and equipment for thermal power plants against corrosion over a long period of time is still one of the most urgent problems of modern engineering. Negative results of internal corrosion are not only reduce the time while equipment is operated in heating systems, thermal power plants or boilers, but also greatly reduce the power sources of heat and electricity, increasing the economic costs of restoration and repair of equipment. Currently, thermal degassing of water is the primary mean of protection against internal corrosion of boilers, water supply, etc., therefore the possibility of reducing the costs of ancillary processes and, above all, of the degassing of water, can be a major source for improving energy performance of heat and power production.
Operation time of heating systems that are powered with undeaerated water, i.e. water which contains dissolved gases, is
1. Relevance of the topic
Analysis of published data showed that the loss of metal from corrosion during the operation time of metal equipment is about 8% of the original mass. Taking into account the great amount of expensive metal equipment used in thermal energy, then based on this figure it is easy to imagine the damage caused by the corrosion of equipment.
Metal corrosion damage often leads to emergency stops of power equipment or reduce its capacity. Damage often limits the production of electricity and heat supply to consumers together with simultaneous burnout of fuel.
Presence of the LPH (low pressure heaters) favors the development of corrosion, because the water temperature after usage of the LPH increases on a few tens of degrees. According to the Vant-Hoff law increase of the temperature of 10 ° C accelerates the reaction in 2 times or more [1, p.83]. Figure 1 shows the dependence of the steel corrosion rate on the water temperature, where 1 — tap water, 2 — Na-cationated water, 3 — chemically demineralized water, 4 — H-Na-cationated water. The whole tract of water is corroded by the combined action of oxygen and carbonic acid. Effect of the water alkalinity on steel corrosion rate shown in Figure 2. which in turn is a factor dependent on the temperature and pressure in the deaerator.
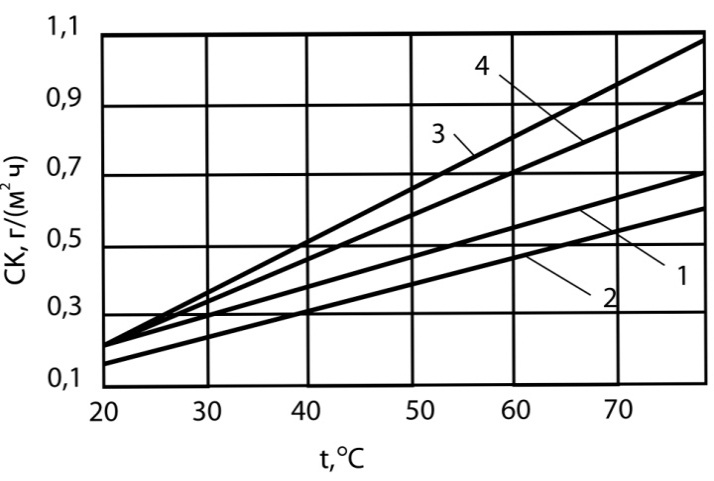
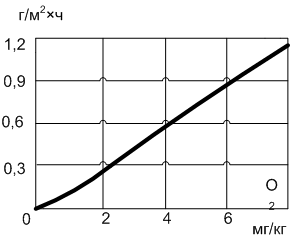
There is a formidable task of the corrosion protection technique to ensure the safe operation of the metal at high temperature and pressure at the power stations. Condensate-powered circuit of modern thermal power plant includes a significant number of pieces of equipment that can be corrosive destructed under the influence of oxygen and carbonic acid dissolved in the water.
Changes in the current economic conditions, including a sharp increase in the prices of fuel and energy resources with a shortage of funds for the replacement of worn-out equipment have pointed out the problem of increasing energy and economic efficiency of the degassing process [1].
Inefficiency of control methods of the degassing processes and instability of technological parameters (TP), deficiencies in the operation and mistakes encountered in the design, which don’t allow to organize optimal performance of the degasser, all these problems often lead to serious disturbances in the entire system and significantly affect the efficiency of degassing.
Currently, control of TP of the de-aeration process is not perfect, accurate to ensure effective degassing process. The quality of the de-aeration can be affected by various factors, such as the occurrence of subcooling at which performance of the de-aerator falls sharply. Also the energy efficiency of the process depends on the de-aeration technology and quality of the deaerator control operation, preventing instability of the TP.
The important conditions for ensuring effective control of the de-aeration process are the proper organization of the necessary temperature conditions, equip of the deaeration plants with modern quality control equipment for de-aeration, the application of modern management techniques and forecasting the TP of de-aeration process.
The main conrolled process parameters of the dearation is the level of deaerated water
Industrial controllers are fairly versatile devices, as they are intended to solve a large variety of tasks. In case when one of them is used only to control the degassing process, only a part of its functionality will be taken, therefore it indicates the redundancy. A special programming language Alfa is used here, so it becomes harder to debug and operation, as it requires specially trained personnel.
2. Tasks and objectives
In order to improve the energy and economic efficiency of the water thermal degassing it is necessary to predict the processes occurring in the deaerator, with the possibility of further optimization on the basis of operational control. However, carrying out the analysis of a permissible level of oxygen and carbon dioxide in the deaerated water as boundary values of equipment efficiency is not sufficient to achieve a certain economic and energetic effect.
This can be done by developing a monitoring system of the degassing process parameters and creation of the conditions for its introduction to the power stations.
For today, the water quality is monitored by means of dissolved oxygen for which the adjustable parameters are specified endpoints of degassing efficiency: the residual concentration of dissolved oxygen and carbon dioxide [2]. Measurement error is ± (3mkg/dm3 4% of the measured value).
Therefore, the main objective is to develop a system of monitoring the de-aeration process parameters, designed for quality control of the de-aeration process, in particular, monitoring of the concentration of oxygen in the water. The system should be simple to operate and debugging, reliable, have the required metrological characteristics, have a small weight and dimensions, which will introduce into the existing ACSTP (automatic control system of the technological parameters).
During the master’s work the following tasks should be solved:
- Determine the percentage of oxygen in deaerated water, using the automatic control system of technological parameters of the de-aeration process;
- Perform a variety of measuring change methods, on the basis of which the measuring channel monitoring system will be implemented;
- Review the existing prototype of the device to control the quality of the de-aeration process;
- Analyze the advantages and disadvantages of these prototypes, make some conclusions concerning the improvement of the measurement process and processing the results;
- Develop a block diagram of the measuring channel of degassing process control system parameters;
- Evaluate the metrological characteristics of the measuring channel of monitoring system;
- Offer the design of control system having a possibility of streamlined debugging, low weight and dimensions for the introduction of the ACSTP.
- System for the control of de-aeration process technological parameters must meet the following requirements:
— Permissible temperature steam: 210;
— Range of measuring pressure, MPa: from 0 to 1
— Measurement speed, ms: 0.5;
— Power supply, 5;
— Nominal supply frequency, 400 Hz;
— The range of supply voltage deviation from the nominal, −20% to +20;
— Accuracy of measurement of pressure,%: 0.8;
— Level measurement error,%: 0.5;
— Temperature measurement error,%: 0.1; - The control system of the de-aeration process technological parameters must be technological in manufacturing, and has maximum standardized parts.
3. Estimated newness
The implementation of new technologies of control the degassing process parameters provides a deep and systematic study of the degassing process, besides drawing up a mathematical model and an optimization algorithm would assess the impact of each of the options, ensure complete and unambiguous description of its relationships. The main advantage of such technologies is a reliable supply of standard de-aeration quality at the highest possible efficiency of the heat-mass-transfer implemented processes to simplify the debugging and operation of the control system.
The proposed system improves the quality of the researched de-aeration process due to greater accuracy in measurement, which reduces the economic losses due to the quality of de-aeration.
Conclusion
One of the most important national objectives is to increase the efficiency and reliability of the entire complex of equipment for thermal power plants using fossil fuels.
One important aspect of the creation of resource-and energy-saving technologies is to improve the heat and mass transfer processes in the chemical, energetic, food and other industries. From the point of view of resource-economy the de-aerators are of particular interest because of the processes complexity occurring in them, accounting an often change of industries needs in purified water.
Existing technologies of de-aeration and de-aeration process control are simple, however, in many cases; the desired result of deaeration is not achieved due to high energy cost.
Such a solution can greatly simplify the control of the degassing process, the participation of the operator can be reduced to a minimum, and control will be going automatically saving the given parameters of the process.
Note: When this essay was written the master’s project wasn’t complete yet.
Final completion: December 2013. Full text of the work and all the materials on the topic can be obtained from the author or his supervisor after that date.
References
- Комарчев И. Г. Безреагентный метод удаления диоксида углерода из воды // Электрические станции. 1988. № 8. С.
43-45. - Шарапов В. И. О применении кислородомеров при исследовании и эксплуатации теплоэнергетического оборудования // Энергосбережение и водоподготовка. 2005. № 5.
- Шарапов В. И., Малинина О. В., Цюра Д.В. О предельной массообменной и энергетической эффективности термических деаэраторов //Энергосбережение и водоподготовка. 2003. № 2. С.
61-64. - Шарапов В.И., Малинина О.В. Определение теоретически необходимого расхода выпара термических деаэраторов // Теплоэнергетика. 2004. № 4. С.
63-66. - Шарапов В.И., Цюра Д.В. Термические деаэраторы. Ульяновск: УлГТУ. 2003. 560 с.
- ГОСТ
16860-88. Термические деаэраторы. М.: Изд-во стандартов. 1989. - Деаэраторы с ТСА // www.fisonic.com.
- Справочно-информационные материалы по применению вакуумных деаэраторов для обработки подпиточной воды систем централизованного теплоснабжения. М.: СПО ОРГРЭС. 1997. 20 с.
- Руководящие указания по проектированию термических деаэрационных установок питательной воды котлов
- Оликер И.И. Термическая деаэрация воды в отопительно — производственных котельных. 1972 г.