Реферат по теме выпускной работы
Содержание
- Введение
- 1. Актуальность темы
- 2. Цель и задачи исследования
- 3. Результаты исследования
- 3.1 Анализ процесса подъема как объекта автоматизации
- 3.2 Критический обзор известных технических решений по автоматизации процесса подъема
- 3.3 Обоснование и разработка системы автоматизации процесса подъема
- Выводы
- Список источников
Введение
Среди стационарного электромеханического оборудования на шахте наиболее ответственными агрегатами являются подъемные установки, которые служат для подъема полезных ископаемых на поверхность земли, спуска и подъема людей, обеспечения шахты необходимыми материалами и оборудования.
В настоящее время уровень автоматизации шахтных подъемных установок остается достаточно низким, вследствие чего понижается качество контроля параметров и оперативности срабатывания защит от недопустимых режимов работы, понижается надежность их работы, а также эффективность самого технологического процесса в целом.
В связи с особой технологической важностью шахтных подъемных установок в шахтном производстве, большими размерами ущерба от аварий, а также высоким уровнем требований к безопасности подъема людей для управления и контроля такими установками допустимо применение лишь автоматизированных систем, предусматривающих обязательное участие человека. По мере совершенствования систем автоматизации шахтных подъемных установок объем функций, выполняемых человеком, неуклонно уменьшался, и в настоящее время за ним остались функции, трудно поддающиеся автоматизации либо более надежно выполняемые человеком в штатной и особенно в нештатной ситуации, а также функции общего контроля ситуации и принятия экстренных мер [1].
1. Актуальность темы
Повышение технико-экономических показателей функционирования клетевой подъемной установки во многом определяются эффективностью функционирования системы автоматического управления [2].
В настоящее время повышение надежности и долговечности оборудования, уменьшение расхода электроэнергии, увеличение производительности, а также контроль всех технологических параметров, влияющих на рабочее состояние подъемной установки, осуществляется при помощи современных средств автоматизации. Наиболее рациональным с точки зрения контроля является разработка автоматизированной системы, позволяющей собирать информацию со всех мест технологического участка, осуществлять их непосредственную обработку и передачу. Использование цифровых датчиков и средств микропроцессорной техники для обработки и передачи информации позволяет с высокой точностью контролировать достаточное количество параметров шахтной подъемной машины, передавать данные на пульт диспетчера и на верхний уровень системы автоматизации, сохранять показания датчиков за продолжительный период и анализировать характер их изменения во времени.
2. Цель и задачи исследования
Целью работы является повышение надежности системы управления клетевой подъемной установкой за счет рассредотачивания ее структуры системы управления и использования активного резервирования компонентов, а также организации приема, обработки, хранения и передачи информации о технологическом процессе на пульт диспетчера.
Для достижения поставленной цели должны быть решены следующие задачи:
- Анализ процесса подъема, как объекта автоматизации;
- Критический обзор известных технических решений связанных с подъемными установками;
- Обоснование и разработка системы автоматизации клетевой подъемной установки;
3. Результаты исследования
3.1 Анализ процесса подъема как объекта автоматизации
Шахтные подъемные установки предназначены для выдачи на поверхность добываемого угля и получаемой при проходке горных выработок породы, быстрого и безопасного спуска и подъема людей, транспортирования крепежного леса, горно-шахтного оборудования и материалов. При помощи подъемной установки производится также осмотр и ремонт армировки и крепления ствола шахты. На крупных шахтах, как правило, имеются две-три действующие подъемные установки, и каждая из них предназначена для определенных целей (выдачи угля, спуска-подъема людей, выдачи породы и т.д.), а не является резервом другой. От надежной, бесперебойной и производительной работы шахтного подъема зависит ритмичная работа всей шахты в целом, поэтому к подъемным установкам (из всего комплекса электромеханического оборудования шахты) представляют особые требования в отношении надежности и безопасности.
Современные шахтные подъемные машины являются наиболее мощными из всего стационарного оборудования на шахте. Мощность электропривода подъемной машины достигает 1000кВт, а крупных – 2000кВт и выше. Электропривод подъемных установок потребляет до 40% всей электроэнергии, расходуемой шахтой. Подъемные машины устанавливают на весь срок эксплуатации шахты. Вес подъемных машин составляет 20-300 т.
Скорость движения подъемных сосудов в стволе достигает 15-20 м/сек (54-72 км/час), т.е. близка к скорости движения железнодорожных составов. Так как такая скорость развивается на коротких расстояниях (равных длине шахтного ствола), подъемные машины должны иметь надежное управление и безотказно действующие тормозные устройства [3].
Шахтные подъемные установки разделяются:
- по назначению – на главные, или грузовые (для транспортирования угля); вспомогательные, или грузолюдские (для транспортирования породы, материалов и оборудования, а также спуска и подъема людей из шахты); людские (только для спуска и подъема людей);
- по типу ствола шахты – на вертикальные и наклонные;
- по типу органов навивки подъемных канатов – на установки с постоянным радиусом навивки (с подъемными машинами с цилиндрическими барабанами или с ведущим шкивом трения) и установки с переменным радиусом навивки канатов (с подъемными машинами с бицилиндрическим барабаном);
- по типу привода подъемных машин – на установки с асинхронным электродвигателем и с двигателем постоянного тока;
- по типу подъемных сосудов – на клетевые, скиповые, комбинированные (скипо-клетевые) и с бадьями (при проходке стволов);
- по степени уравновешенности – на уравновешенные и неуравновешенные.
Подъемные установки шахт и рудников – наиболее сложные и ответственные объекты в общей технологической цепи транспортировки полезного ископаемого с забоя на поверхность. Сложность их обусловлена тем, что электрическая схема подъемной машины должна выполнять множество контрольных и защитных функций и обеспечивать автоматическое управление мощным приводом постоянного или переменного тока при значительной, переменной по уровню нагрузке для поддержания с большой точностью заданной скорости сосуда на всех участках его движения.
Автоматизация подъемных машин на шахтах и рудниках выполняется по индивидуальным проектам на базе различных серийно выпускаемых технических средств и аппаратуры. На рисунке 1 приведена схема шахтного подъема.
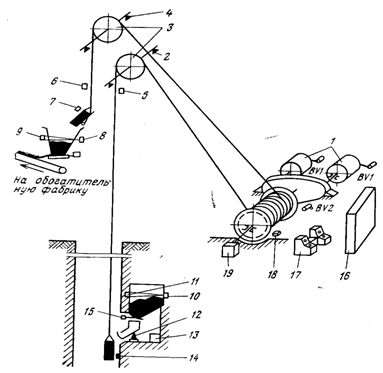
Рисунок 1 – Схема шахтного подъёма
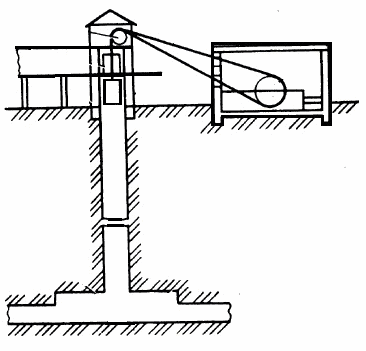
Рис. 2 – Клетевая подъемная установка (анимация: 7 кадров, 6 циклов повторения, 48 килобайт)
На данном рисунке приведены следующие обозначения: 1 – подъемные двигатели; 2, 4 – магнитоупругие индуктивные датчики; 3 – подшипники копровых шкивов; 5,6 – бесконтактные индуктивные датчики; 7,14 – взрывобезопасные магнитные выключатели; 8 – верхний бункер; 9,11 – датчики; 10 – нижний бункер; 12 – силоизмерительный датчик; 13 – электронный блок; 15 – исполнительный механизм; 16 – схема управления подъемной машины; 17 – пульт управления подъемной машины; 18 – датчик износа тормозных колодок.
Основными требованиями, предъявляемыми к системе автоматизации, будут:
- обеспечение точного расчетного движения подъемных сосудов в соответствии с тахограммой;
- защита подъемной машины с включением предохранительного торможения в следующих случаях;
- блокировка запрещающая включения подъемной машины после переподъема или зависания сосудов в стволе в сторону;
- система автоматизации должна обеспечивать своевременный и непрерывный сбор информации со всех участков технологического комплекса;
- система автоматизации должна обеспечивать контроль состояния основных параметров технологического процесса подъема;
- непрерывный контроль всех параметров безопасности шахтной подъемной установки;
- повышение качества контроля параметров и оперативности срабатывания защит от недопустимых режимов работы;
- повышение надежности ШПУ;
- постоянный мониторинг ситуации и обеспечение условий для своевременного принятия предупредительных и защитных мер по обеспечению безопасной работы ШПУ;
- регистрация, хранение и автоматизирование воспроизведение исторической информации о работе установки [4].
3.2 Критический обзор известных технических решений по автоматизации процесса подъема
Известна система связи «магнитная запись — шаговый двигатель» (МЗ—ШД), на которую получены патенты в разных странах. Система МЗ—ШД позволяет преобразовать перемещение подъемного каната, несущего магнитные метки, в пропорциональный этому перемещению поворот ротора шагового электродвигателя. Разрешающая способность внедрённых систем равна 0,1 и, т. е. каждому перемещению каната на 0,1 м соответствует поворот ротора шагового электродвигателя на определенный дискретный угол, называемый шагом. Причем направление вращения (шагания) ротора двигателя определяется направлением движения каната, несущего магнитную запись.
На базе системы МЗ—ШД создана аппаратура «Горизонт», которая выдает импульсы в отдельных точках пути движения подъемного сосуда в соответствии со схемой автоматического управления; выдает электрический сигнал для определения пройденного пути подъемными сосудам с помощью сельсинного указателя глубины. В систему МЗ—ШД (рис. 3) входят: один из подъемных канатов, на котором нанесены равномерно по всей длине магнитные метки; четыре магнитомодуляционных датчика 1ДМ, (1ДМ2), 2ДМ4 (2ДМ2), установленных попарно вдоль каната в реагирующих на магнитное поле меток; два блока 1БВ, 2БВ воспроизведения магнитных меток, записанных на канате, и выдачи импульсов в схему управления шаговым двигателем; два усилителя 1У, 2У сигналов от каждого блока воспроизведения до мощности, необходимой для возбуждения обмоток шагового двигателя; два четырехтактных шаговых двигателя 1ШД, 2ШД.

Рисунок 3 – Функциональная схема системы МЗ—ШД аппаратуры «Горизонт»
Промышленные испытания и опыт эксплуатации аппаратуры «Горизонт» показали высокую надежность. Недостатком системы МЗ—ШД является двойное преобразование информации; поступательного движения подъемного каната в комбинацию электрических сигналов на выходе блоков воспроизведения, а затем этих сигналов в механический поворот вала, который с помощью этажных выключателей, командоаппаратов и сельсинов снова преобразуется в электрические сигналы для управления машиной.
Электрические устройства управления и защиты, выполненные на базе использования транзисторных логических схем, не только исключают все перечисленные выше недостатки электромеханических устройств, но и обеспечивают выполнение новых режимов работы подъемных установок. Транзисторные устройства управления и защиты сравнительно просто могут быть унифицированы для различных типов подъемных машин и различных режимов работы.
Аппаратура «Скип» изготовлена Донецким заводом им. Ленинского комсомола Украины и установлена на скиповом подъеме шахты «Ново–Центральная» Донецкуголь. Выполнена в виде набора блоков логических элементов, которые представляют собой отдельные узлы аппаратуры. Информация о пройденном подъемным сосудом пути в виде импульсов формируется с помощью магнитных меток, нанесенных на головном канате, Магнитные метки длиной 300 мм наносятся продольным намагничиванием с постоянным шагом по длине каната, равным 600 мм. Считывание магнитных меток осуществляется тремя спаренными магнитомодуляционными датчиками, расположенными на двух стойках у головного каната, что обеспечивает информацию о перемещении подъемного сосуда и о направлении движения его с точностью 100 мм [5].
Аппарат защиты и контроля движения (далее по тексту АЗКД) шахтной подъемной установки (ШПУ) является системой, предназначенной для обеспечения защиты и контроля работы ШПУ. АЗКД обеспечивает точный контроль над всеми основными параметрами шахтного подъемника, такими как скорость, ускорение и положение подъемного сосуда. Устройство обеспечивает контроль работы ШПУ независимо от их типа: фрикционных, однобарабанных, двухбарабанных, проходческих, и предназначено, как для установки на новых объектах, так и для замены электромеханических систем типа АЗК–1 с ЭОС–3 и ОСП. АЗКД работает независимо от системы управления подъемника и в случае превышения скорости или избыточного перемещения выдает команду аварийной остановки. Устройство смонтировано в металлическом шкафу. На двери шкафа находится панель оператора c органами управления и индикации. Связь с главным контроллером осуществляется, в таком случае, по Ethernet каналу. В системе предусмотрена архивация и запись на жесткий диск панельного компьютера всех данных, необходимых для контроля рабочего цикла подъёмной установки.
Применение АЗКД обеспечивает повышение производственной безопасности и эффективности работы ШПУ за счет:
- высокой точности контроля параметров безопасности;
- быстродействия системы защиты;
- представления оперативному персоналу достоверной и полной информации о параметрах движения;
- регистрации, хранения и воспроизведения сохраняемой информации о параметрах безопасности, режимах работы и срабатывании защит;
- увеличения количества путевых команд управления и защиты.
Для получения информации о скорости и положении подъемного сосуда в АЗКД используется отдельный импульсный датчик с приводом от вала барабана. Так как датчик импульсов дает относительную информацию о положении сосуда, то для определения абсолютного значения положения, дополнительно используются точки синхронизации отсчета в верхнем и в нижнем положениях в стволе. В верхней точке синхронизации, для определения положения в абсолютных единицах, используется путевой выключатель синхронизации. Путевой выключатель вблизи нижнего положения сосуда позволяет системе автоматически сравнить путь, вычисленный по сигналам импульсного датчика, с действительным расстоянием между путевыми выключателями. Это позволяет системе компенсировать вытяжку канатов и износ фрикционных накладок, обеспечивая тем самым точный контроль графика скорости для целей управления. Абсолютное значение скорости вычисляется путем измерения периода следования импульсов, получаемых от датчика импульсов. АЗКД непрерывно контролирует соответствие скорости и положения сосуда в соответствии с графиком защитной тахограммы, заданным в системе. Если измеренное значение скорости превышает значение, заданное защитной тахограммой, происходит размыкание цепей защиты. Система позволяет выбрать один из графиков скорости в зависимости от режима работы, например, для перемещения грузов или людей. Для повышения безопасности, АЗКД использует второй независимый измеритель скорости, например дополнительный тахогенератор, что обеспечивает самоконтроль системы, а так же защиту от пробуксовки и проскальзывания. На вход АЗКД из системы управления подъемником подается сигнал о заданном направлении движения сосуда. Система АЗКД проверяет по фазировке сигналов от импульсного датчика соответствие действительного направления движения заданному [6].
Системы управления и автоматизации фирмы «АВВ» построена на основе микропроцессорных программируемых контроллеров. Весь алгоритм управления подъемной машиной по сигналам из ствола, а также механизмами, установленными в стволе, реализуется главным контроллером подъемной установки. Система стволовой сигнализации и связи соединяется с системой управления подъемом посредством модемной связи. Для цепей сигналов защиты из ствола и цепей связи с датчиками положения сосудов в стволе предусмотрена аппаратная связь. Наглядная визуальная информация о состоянии механизмов в стволе представляется на видовом экране компьютера оператора подъемной машины [7].
Для осуществления связи с подъемной сосудов и реализации некоторых функций в алгоритмах работы стволовой сигнализации используется стволовая радиостанция фирмы «FHF» типа MR90, являющейся многоканальной системой радиопередачи речи и данных для применения в подземных выработках. Система радиосвязи служит для посылки информации от технологического оборудования в клети в систему управления подъемной машины [8].
3.3 Обоснование и разработка системы автоматизации процесса подъема
На рисунке 4 приведена структурная схема разрабатываемой системы согласно составленному алгоритму и способу управления.
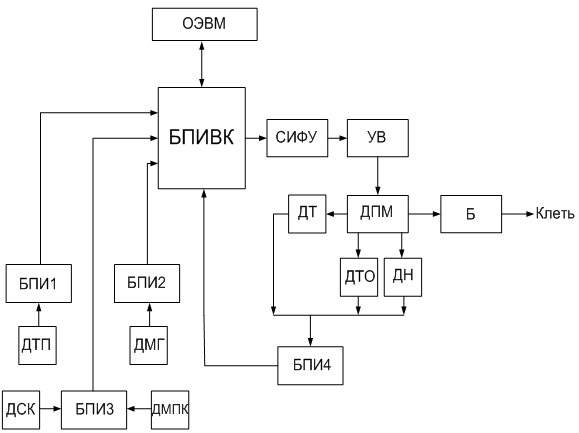
Рисунок 4 – Структурная схема автоматизированной системы объекта
На рисунке приведены следующие обозначения: ОЭВМ – Оператор ЭВМ; БПИВК – Блок приема информации и выдачи команд; СИФУ – Система импульсно–фазового управления; УВ – Управляемый выпрямитель; ДПМ – Двигатель подъемной машины; Б – Барабан; ДН – Датчик напряжения; ДТО – Датчик температуры обмоток; ДТ – Датчик тока; ДТП – Датчик температуры подшипникового узла; ДСК – Датчик скорости клети; ДМПК – Датчик местоположения клети; ДМГ – Датчик массы груза; БПИ1,2,3,4 – Блок приема информации от датчиков.
Принцип работы данной системы заключается в следующем: в машинный зал, а также вверху, внизу ствола и у копра устанавливаются соответствующие блоки БПИ1,2,3,4, которые в свою очередь осуществляют прием информации от технологических датчиков контроля технологического процесса. Каждому сигналу от датчика, с целью передачи его на большие расстояния без потерь, присваивается соответствующий адрес, при помощи которого блок приема информации и выдачи команд будет проводить опрос каждого блока и передача данных осуществляется по протоколу. Эти сигналы поступают в цифровом виде на блок приема информации и выдачи команд. Далее вся информация поступает оператору ЭВМ на пульт управления, откуда ведется контроль за состоянием технологического процесса, где оператор собирая данные, может осуществлять управление двигателем подъемной машины в соответствии с заданными параметрами и режимами работы. Во всех блоках в качестве устройства согласования для аналоговых сигналов используются операционные усилители, а для дискретных применяется гальваническая развязка. Блок приема информации и выдачи команд предусматривает в своем составе два микроконтроллера (основной и резервный), которые соединены между собой устройством переключения. При выходе из строя основного микроконтроллера устройство переключения включает в работу резервный микроконтроллер. Для большей эффективности работы, диаграмма подъема условно делится на восемь участков и при сбое системы резервный микроконтроллер начинает свою работу с того момента, на котором остановился основной.
Алгоритм разрабатываемого нами блока приведен на рисунке 5 и работает следующим образом: на блок приема информации и выдачи команд поступают сигналы о состоянии технологических параметров от четырех блоков приема информации по всему технологическому комплексу подъема, которые условно можно выделить как подсистему сбора информации. Алгоритм блока приема информации и выдачи команд предусматривает подпрограммы, на которые подразделяются алгоритмы блоков, которые передают на него сигналы о состоянии технологических параметров. Алгоритм работы данных блоков представлен на следующих рисунках:
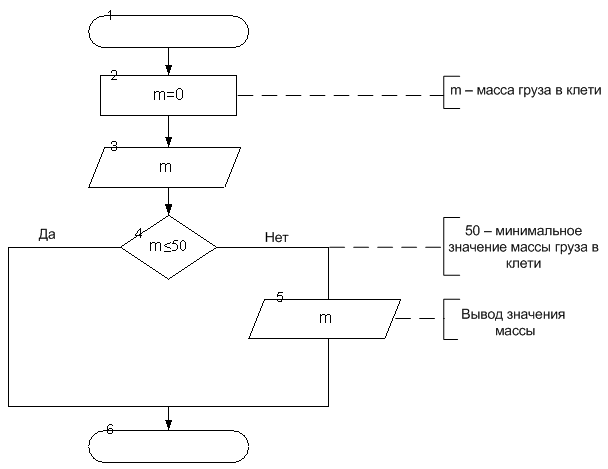
Рисунок 5 – Алгоритм работы блока приема информации №2
Блок БПИ №2 выполняет функцию приема информации от датчика ДМГ о состоянии массы груза в клети. Алгоритм работы данного блока заключается в следующем: в данном случае опрос идет датчика массы груза в клети, в качестве которого может выступать тензодатчик. Передача данных будет осуществляться в том случае, если масса груза в клети m будет составлять более пятидесяти килограмм.
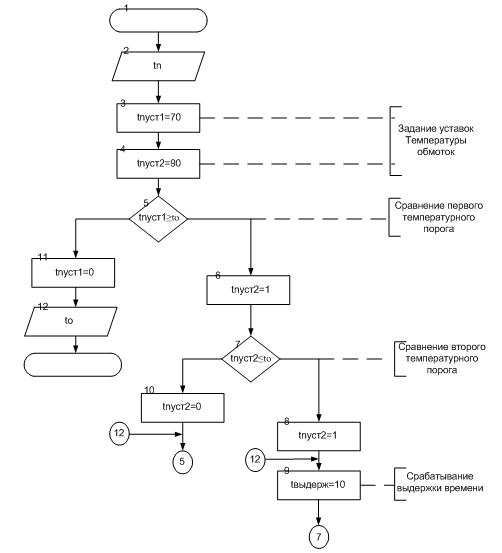
Рисунок 6 – Алгоритм работы блока приема информации №1
Блок БПИ №1 выполняет функцию приема информации от датчика ДТП о состоянии температуры подшипникового узла. Алгоритм работы данного блока заключается в следующем: в данном случае информация передается от датчика температуры подшипниковых узлов. Изначально программно задаются две уставки температуры tnуст1 и tnуст2, которые равны соответственно 70 и 90 . При срабатывании первого температурного порога tnуст1 информация передается на пульт диспетчера с выдачей предупредительной сигнализации. Далее сравнивается значение второго температурного порога tnуст2, при превышении которого с выдержкой времени tвыдерж в 10с происходит отключение двигателя подъемной машины, с выдачей информации на пульт диспетчера о превышении заданной температуры.
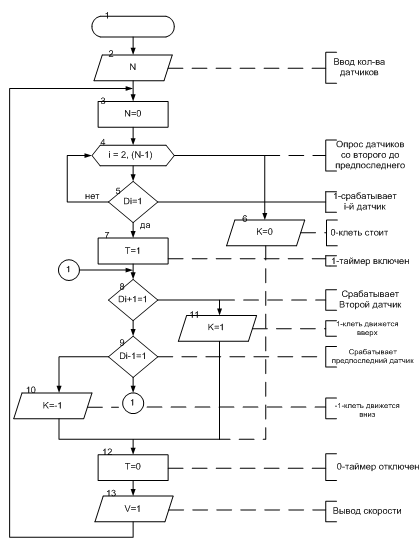
Рисунок 7 – Алгоритм работы блока приема информации №3
Блок БПИ №3 выполняет функцию приема информации от датчиков ДСК и ДМПК о скорости и местоположении сосуда в стволе. Алгоритм работает следующим образом: датчики контроля скорости клети N, в качестве которых могут применяться индуктивные датчики, размещаются по всей длине ствола. На клеть устанавливается магнитная метка. При прохождении данной метки через датчик, включится таймер, и сигнал будет передаваться на пульт диспетчера. Будет происходить подсчет количества импульсов, что позволит судить о скорости клети, а также зная номер сработавшего датчика, будет возможность судить о местоположении клети в стволе и о том, в каком направлении она движется.
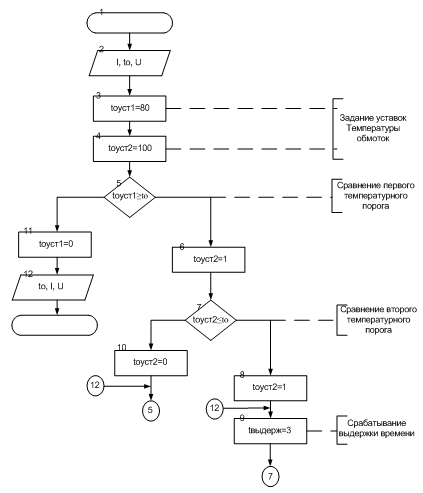
Рисунок 8 – Алгоритм работы блока приема информации №4
Блок БПИ №4 выполняет функцию приема информации от датчиков ДТ, ДН и ДТО о напряжении, токе и температуре обмоток двигателя. Алгоритм работы данного блока заключается в следующем: в данном случае информация передается от трех датчиков: датчика температуры обмоток, датчика тока и датчика напряжения. Как и в предыдущем случае будут задаваться две уставки температуры tоуст1 и tоуст2, которые равны соответственно 80 и 100 . Передача информации о значениях тока и напряжения осуществляется непрерывно и независимо от температурных процессов электропривода. При срабатывании первого температурного порога tоуст1 информация передается на пульт диспетчера с выдачей предупредительной сигнализации. Далее сравнивается значение второго температурного порога tоуст2, при превышении которого с выдержкой времени tвыдерж в 3с происходит отключение двигателя подъемной машины, с выдачей информации на пульт диспетчера о превышении заданной температуры.
Выводы
В результате исследования произведен анализ технологического процесса подъема как объекта автоматизации, сформулирована цель и задачи исследования. Сделан критический обзор известных технических решений по автоматизации процесса подъема. Произведено обоснование и разработка системы автоматизации подъемной установки: была разработана структурная схема автоматизации объекта и алгоритм работы каждого блока.
При написании данного реферата магистерская работа еще не завершена. Окончательное завершение: декабрь 2013 года. Полный текст работы и материалы по теме могут быть получены у автора или его руководителя после указанной даты.
Список источников
- Система управления и комплексной защиты шахтной подъёмной установки / [Кащич А., Марищенко А., Божок Н. и др.] // Cистемная интеграция, добывающая промышленность. – 2005. – №2. – С.26–34.
- Руководство по ревизии, наладке и испытанию шахтных подъемных установок: нормативное производственно–практическое издание/В.Р. Бежок, В.Г. Калинин, В.Д. Коноплянов, Е.М. Курченко; Под общей редакцией В.А. Корсуна. – Донецк, 2009. – 672 с.
- Дроздова, Л.Г. Стационарные машины: Учеб. пособие. – Владивосток: Изд-во ДВГТУ, 2007. – 157 с.
- Гаврилов П.Д., Гимельштейн Л.Я., Медведев А.Е. Автоматизация производственных процессов: Учебник для ВУЗов.– М.: Недра, 1985. – 216с.
- Правицкий Н.К. – Рудничные подъемные установки. –Харьков, 1956, 301 с.
- Аппарат защиты и контроля движения [Электронный ресурс]. – Режим доступа: http://www.ooo–yuep.com/ru/azkd
- ABB AB – Mine Hoist Systems [Электронный ресурс]. – Режим доступа: http://www.mining–technology.com/contractors/.
- Каталог продукции компании FHF [Электронный ресурс]. – Режим доступа: http://www.fhf–bt.org/.
- Стороженко М. А. Аппаратура управления и контроля рудничными подъёмными установками / М.А. Стороженко, А.Ф. Кирей. – М.: «Недра», 1980.
- Евстифеев А.В. Микроконтроллеры AVR семейств Tiny и Mega фирмы ATMEL. – 5-е изд., стер. – М.: Издательский дом «Додэка–XXI», 2008. – 560с.