Реферат за темою випускної роботи
Зміст
- Вступ
- 1. Актуальність теми
- 2. Мета і завдання дослідження
- 3. Результати дослідження
- 3.1 Аналіз процесу підйому як об'єкта автоматизації
- 3.2 Критичний огляд відомих технічних рішень з автоматизації процесу підйому
- 3.3 Обгрунтування та розробка системи автоматизації процесу підйому
- Висновки
- Перелік посилань
Вступ
Серед стаціонарного електромеханічного обладнання на шахті найбільш відповідальними агрегатами є підйомні установки, які служать для підйому корисних копалин на поверхню землі, спуску і підйому людей, забезпечення шахти необхідними матеріалами та обладнанням.
В даний час рівень автоматизації шахтних підйомних установок залишається досить низьким, внаслідок чого знижується якість контролю параметрів і оперативності спрацьовування захистів від неприпустимих режимів роботи, знижується надійність їх роботи, а також ефективність самого технологічного процесу в цілому.
У зв'язку з особливою технологічної важливістю шахтних підйомних установок у шахтному виробництві, великими розмірами шкоди від аварій, а також високим рівнем вимог до безпеки підйому людей для управління і контролю такими установками допустимо застосування лише автоматизованих систем, які передбачають обов'язкову участь людини. У міру вдосконалення систем автоматизації шахтних підйомних установок обсяг функцій, виконуваних людиною, неухильно зменшувався, і в даний час за ним залишилися функції, що важко піддаються автоматизації або більш надійно виконуються людиною в штатній і особливо в нештатній ситуації, а також функції загального контролю ситуації та прийняття екстрених заходів [1].
1. Актуальность темы
Підвищення техніко-економічних показників функціонування клітьовою підйомної установки багато в чому визначаються ефективністю функціонування системи автоматичного керування [2].
В даний час підвищення надійності та довговічності обладнання, зменшення витрат електроенергії, збільшення продуктивності, а також контроль всіх технологічних параметрів, які впливають на робочий стан підйомної установки, здійснюється за допомогою сучасних засобів автоматизації. Найбільш раціональним з точки зору контролю є розробка автоматизованої системи, що дозволяє збирати інформацію з усіх місць технологічного ділянки, здійснювати їх безпосередню обробку та передачу. Використання цифрових датчиків і засобів мікропроцесорної техніки для обробки і передачі інформації дозволяє з високою точністю контролювати достатню кількість параметрів шахтної підйомної машини, передавати дані на пульт диспетчера і на верхній рівень системи автоматизації, зберігати показники датчиків за тривалий період і аналізувати характер їх зміни в часі.
2. Цель и задачи исследования
Метою роботи є підвищення надійності системи управління клітьовою підйомною установкою за рахунок розподілу її структури системи управління та використання активного резервування компонентів, а також організації прийому, обробки, зберігання та передачі інформації про технологічний процес на пульт диспетчера.
Для досягнення поставленої мети повинні бути вирішені наступні завдання:
- Аналіз процесу підйому, як об'єкта автоматизації;
- Критичний огляд відомих технічних рішень пов'язаних з підйомними установками;
- Обгрунтування та розробка системи автоматизації клітьової підйомної установки;
3. Результати дослідження
3.1 Аналіз процесу підйому як об'єкта автоматизації
Шахтні підйомні установки призначені для видачі на поверхню вугілля, що видобувається і одержуваної при проходці гірських виробок породи, швидкого і безпечного спуску і підйому людей, транспортування кріпильного лісу, гірничо-шахтного обладнання та матеріалів. За допомогою підйомної установки проводиться також огляд і ремонт армування та кріплення ствола шахти. На великих шахтах, як правило, є дві-три діючі підйомні установки, і кожна з них призначена для певних цілей (видачі вугілля, спуску-підйому людей, видачі породи і т.д.), а не є резервом інший. Від надійної, безперебійної та продуктивної роботи шахтного підйому залежить ритмічна робота всієї шахти в цілому, тому до підйомних установок (із усього комплексу електромеханічного обладнання шахти) представляють особливі вимоги щодо надійності і безпеки.
Сучасні шахтні підйомні машини є найбільш потужними з усього стаціонарного обладнання на шахті. Потужність електроприводу підйомної машини досягає 1000кВт, а великих – 2000кВт і вище. Електропривод підйомних установок споживає до 40% всієї електроенергії, що витрачається шахтою. Підйомні машини встановлюють на весь термін експлуатації шахти. Вага підйомних машин складає 20-300 т.
Швидкість руху підйомних посудин у стволі досягає 15-20 м / сек (54-72 км / год), тобто близька до швидкості руху залізничних складів. Так як така швидкість розвивається на коротких відстанях (рівних довжині шахтного ствола), підйомні машини повинні мати надійне управління і безвідмовно діючі гальмівні пристрої [3].
Шахтні підйомні установки розділяються:
- за призначенням – на головні, або вантажні (для транспортування вугілля); допоміжні, або грузо–людські (для транспортування породи, матеріалів і устаткування, а також спуску і підйому людей із шахти); людські (тільки для спуску і підйому людей);
- за типом стовбура шахти – на вертикальні і похилі;
- за типом органів навивки підйомних канатів – на установки з постійним радіусом навивки (з підйомними машинами з циліндричними барабанами або з ведучим шківом тертя) і установки з перемінним радіусом навивки канатів (з підйомними машинами з біціліндрічним барабаном);
- за типом приводу підйомних машин – на установки з асинхронним електродвигуном і з двигуном постійного струму;
- за типом підйомних посудин – на Клітьові, скіпові, комбіновані (скіпо-клітьові) і з цебрами (при проходженні стволів);
- за ступенем врівноваженості – на урівноважені і неврівноважені.
Підйомні установки шахт і копалень – найбільш складні і відповідальні об'єкти в загальному технологічному ланцюзі транспортування корисної копалини з вибою на поверхню. Складність їх обумовлена тим, що електрична схема підйомної машини повинна виконувати безліч контрольних і захисних функцій і забезпечувати автоматичне керування потужним приводом постійного або змінного струму при значній, змінної за рівнем навантаженні для підтримки з великою точністю заданої швидкості судини на всіх ділянках його руху.
Автоматизація підйомних машин на шахтах і рудниках виконується за індивідуальними проектами на базі різних серійно випускаємих технічних засобів та апаратури. На рисунку 1 приведена схема шахтного підйому.
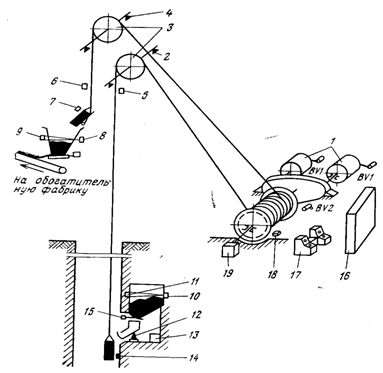
Рисунок 1 – Схема шахтного підйому
На даному рисунку наведені такі позначення: 1 – підйомні двигуни; 2, 4 – магнитоупругі індуктивні датчики; 3 – підшипники копрових шківів; 5,6 – безконтактні індуктивні датчики; 7,14 – вибухобезпечні магнітні вимикачі; 8 – верхній бункер; 9,11 – датчики; 10 – нижній бункер; 12 – силовимірювальний датчик; 13 – електронний блок; 15 – виконавчий механізм; 16 – схема управління підйомної машини; 17 – пульт управління підйомної машини; 18 – датчик зносу гальмівних колодок.
Основними вимогами, що пред'являються до системи автоматизації, будуть:
- забезпечення точного розрахункового руху підйомних посудин згідно з тахограммой;
- захист підйомної машини з включенням запобіжного гальмування в наступних випадках;
- блокування забороняє включення підйомної машини після перепідйому або зависання судин в стовбурі в сторону;
- система автоматизації повинна забезпечувати своєчасний і безперервний збір інформації з усіх дільниць технологічного комплексу;
- система автоматизації повинна забезпечувати контроль стану основних параметрів технологічного процесу підйому;
- безперервний контроль всіх параметрів безпеки шахтної підйомної установки;
- підвищення якості контролю параметрів і оперативності спрацьовування захистів від неприпустимих режимів роботи;
- підвищення надійності ШПУ;
- постійний моніторинг ситуації і забезпечення умов для своєчасного прийняття запобіжних та захисних заходів щодо забезпечення безпечної роботи ШПУ;
- реєстрація, зберігання і автоматизування відтворення історичної інформації про роботу установки [4].
3.2 Критичний огляд відомих технічних рішень з автоматизації процесу підйому
Відома система зв'язку "магнітний запис – кроковий двигун" (МЗ–КД), на яку отримано патенти в різних країнах. Система МЗ–КД дозволяє перетворити переміщення підйомного каната, несучого магнітні мітки, в пропорціональний цьому переміщенню поворот ротора крокового електродвигуна. Роздільна здатність впроваджених систем дорівнює 0,1 і, тобто кожному переміщенню каната на 0,1 м відповідає поворот ротора крокового електродвигуна на певний дискретний кут, званий кроком. Причому напрямок обертання (крока) ротора двигуна визначається напрямком руху каната, несучого магнітний запис.
На базі системи МЗ–КД створена апаратура "Горизонт", яка видає імпульси в окремих точках шляху руху підйомної посудини у відповідності зі схемою автоматичного управління; видає електричний сигнал для визначення пройденого шляху підйомними судинах за допомогою сельсину покажчика глибини. У систему МЗ–КД (рис. 2) входять: один з підйомних канатів, на якому нанесені рівномірно по всій довжині магнітні мітки; чотири магнітомодуляційні датчика 1ДМ, (1ДМ2), 2ДМ4 (2ДМ2), встановлених попарно вздовж каната в реагуючих на магнітне поле міток; два блоки 1БВ, 2БВ відтворення магнітних міток, записаних на канаті, і видачі імпульсів у схему управління кроковим двигуном; два підсилювачі 1У, 2У сигналів від кожного блоку відтворення до потужності, необхідної для порушення обмоток крокової двигуна; два чотиритактних крокових двигуна 1ШД, 2ШД.

Рисунок 2 – Функціональна схема системи МЗ–КД апаратури "Горизонт"
Промислові випробування і досвід експлуатації апаратури "Горизонт" показали високу надійність. Недоліком системи МЗ–КД є подвійне перетворення інформації; поступального руху підйомного каната в комбінацію електричних сигналів на виході блоків відтворення, а потім цих сигналів в механічний поворот валу, який за допомогою поверхових вимикачів, командоаппаратів і сельсинов знову перетворюється в електричні сигнали для управління машиною.
Електричні пристрої керування і захисту, виконані на базі використання транзисторних логічних схем, не тільки виключають всі перераховані вище недоліки електромеханічних пристроїв, але і забезпечують виконання нових режимів роботи підйомних установок. Транзисторні пристроїв управління та захисту порівняно просто можуть бути уніфіковані для різних типів підйомних машин і різних режимів роботи.
Апаратура "Скіп" виготовлена Донецьким заводом ім. Ленінського комсомолу України і встановлена на скіповом пійомі шахти "Ново–Центральна" Донецьквугілля. Виконана у вигляді набору блоків логічних елементів, які являють собою окремі вузли апаратури. Інформація про пройдений підйомною посудиною шляху у вигляді імпульсів формується за допомогою магнітних міток, нанесених на головному канаті, Магнітні мітки довжиною 300 мм наносяться поздовжнім намагнічуванням з постійним кроком по довжині каната, рівним 600 мм. Зчитування магнітних міток здійснюється трьома спареними магнітомодуляціоннимі датчиками, розташованими на двох стійках у головного каната, що забезпечує інформацію про переміщення підйомної посудини і про напрямок руху його з точністю 100 мм [5].
Апарат захисту і контролю руху (далі по тексту АЗКД) шахтної підйомної установки (ШПУ) є системою, призначеної для забезпечення захисту і контролю роботи ШПУ. АЗКД забезпечує точний контроль над усіма основними параметрами шахтного підйомника, такими як швидкість, прискорення і положення підйомної посудини. Пристрій забезпечує контроль роботи ШПУ незалежно від їх типу: фрикційних, однобарабанних, двобарабанних, прохідницьких, і призначене, як для установки на нових об'єктах, так і для заміни електромеханічних систем типу АЗК–1 з ЕОС–3 і ОСП. АЗКД працює незалежно від системи управління підйомника і в разі перевищення швидкості або надлишкового переміщення видає команду аварійної зупинки. Пристрій змонтовано в металевій шафі. На двері шафи знаходиться панель оператора c органами управління та індикації. Зв'язок з головним контролером здійснюється, в такому випадку, по Ethernet каналу. У системі передбачена архівація та запис на жорсткий диск панельного комп'ютера всіх даних, необхідних для контролю робочого циклу підйомної установки.
Застосування АЗКД забезпечує підвищення виробничої безпеки та ефективності роботи ШПУ за рахунок:
- високої точності контролю параметрів безпеки;
- швидкодії системи захисту;
- представлення оперативному персоналу достовірної та повної інформації про параметри руху;
- реєстрації, зберігання та відтворення інформації, що зберігається про параметри безпеки, режимах роботи і спрацьовуванні захистів;
- збільшення кількості подорожніх команд управління і захисту.
Для отримання інформації про швидкість і положенні підйомної посудини в АЗКД використовується окремий імпульсний датчик з приводом від валу барабана. Так як датчик імпульсів дає відносну інформацію про становище судини, то для визначення абсолютного значення положення, додатково використовуються точки синхронізації відліку у верхньому та нижньому положеннях у стволі. У верхній точці синхронізації, для визначення положення в абсолютних одиницях, використовується шляховий вимикач синхронізації. Подорожній вимикач поблизу нижнього положення судини дозволяє системі автоматично порівняти шлях, обчислений за сигналами імпульсного датчика, з дійсним відстанню між колійними вимикачами. Це дозволяє системі компенсувати витяжку канатів і знос фрикційних накладок, забезпечуючи тим самим точний контроль графіка швидкості для цілей управління. Абсолютне значення швидкості обчислюється шляхом вимірювання періоду проходження імпульсів, одержуваних від датчика імпульсів. АЗКД безперервно контролює відповідність швидкості та положення посудини відповідно до графіка захисної тахограмми, заданих в системі. Якщо виміряне значення швидкості перевищує значення, задане захисної тахограммой, відбувається розмикання ланцюгів захисту. Система дозволяє вибрати один з графіків швидкості залежно від режиму роботи, наприклад, для переміщення вантажів або людей. Для підвищення безпеки, АЗКД використовує другий незалежний вимірювач швидкості, наприклад додатковий тахогенератор, що забезпечує самоконтроль системи, а так само захист від пробуксовки і прослизання. На вхід АЗКД з системи керування підйомником подається сигнал про заданому напрямку руху посудини. Система АЗКД перевіряє за фазировке сигналів від імпульсного датчика відповідність дійсного напрямку руху заданому [6].
Системи управління і автоматизації фірми "АВВ" побудовані на основі мікропроцесорних програмованих контролерів. Весь алгоритм управління підйомною машиною за сигналами зі стовбура, а також механізмами, встановленими в стовбурі, реалізується головним контролером підйомної установки. Система стовбурової сигналізації та зв'язку з'єднується з системою управління підйомом за допомогою модемного зв'язку. Для ланцюгів сигналів захисту зі стовбура і ланцюгів зв'язку з датчиками положення судин у стовбурі передбачена апаратна зв'язок. Наочна візуальна інформація про стан механізмів у стовбурі представляється на видовому екрані комп'ютера оператора підйомної машини [7].
Для здійснення зв'язку з підйомною судиною і реалізації деяких функцій в алгоритмах роботи стовбурової сигналізації використовується стовбурова радіостанція фірми "FHF" типу MR90, що є багатоканальної системою радіопередачі мови і даних для застосування в підземних виробках. Система радіозв'язку служить для посилки інформації від технологічного обладнання в кліті в систему управління підйомної машини [8].
3.3 Обгрунтування та розробка системи автоматизації процесу підйому
На рисунку 3 наведена структурна схема системи, що розробляється відповідно до складеного алгоритму і способу управління.
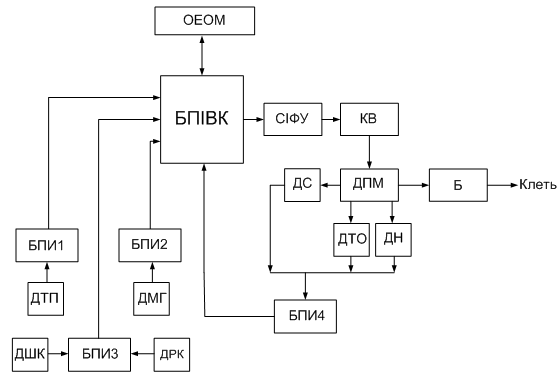
Рисунок 3 – Структурна схема автоматизованої системи об'єкта
На рисунку наведено такі позначення: ОЕОМ – Оператор ЕОМ; БПІВК – Блок прийому інформації та видачі команд; СІФУ – Система імпульсно–фазового управління; КВ – Керований випрямляч; ДПМ – Двигун підйомної машини; Б – Барабан; ДН – Датчик напруги; ДТО – Датчик температури обмоток; ДС – Датчик струму; ДТВ – Датчик температури підшипникового вузла; ДШК – Датчик швидкості кліті; ДРК – Датчик розташування кліті; ДМВ – Датчик маси вантажу; БПІ1, 2,3,4 – Блок прийому інформації від датчиків.
Принцип роботи даної системи полягає в наступному: в машинний зал, а також угорі, внизу стовбура і у копра встановлюються відповідні блоки БПІ 1, 2, 3, 4, які в свою чергу здійснюють прийом інформації від технологічних датчиків контролю технологічного процесу. Кожному сигналу від датчика, з метою передачі його на великі відстані без втрат, присвоюється відповідний адрес, за допомогою якого блок прийому інформації та видачі команд проводитиме опитування кожного блоку і передача даних здійснюється за протоколом. Ці сигнали надходять в цифровому вигляді на блок прийому інформації та видачі команд. Далі вся інформація надходить оператору ЕОМ на пульт управління, звідки ведеться контроль за станом технологічного процесу, де оператор збираючи дані, може здійснювати управління двигуном підйомної машини у відповідності з заданими параметрами і режимами роботи. У всіх блоках в якості пристрою узгодження для аналогових сигналів використовуються операційні підсилювачі, а для дискретних застосовується гальванічна розв'язка. Блок прийому інформації та видачі команд передбачає у своєму складі два мікроконтролера (основний і резервний), які з'єднані між собою пристроєм перемикання. При виході з ладу основного мікроконтролера пристрій перемикання включає в роботу резервний мікроконтролер. Для більшої ефективності роботи, діаграма підйому умовно ділиться на вісім ділянок і при збої системи резервний мікроконтролер починає свою роботу з того моменту, на якому зупинився основний.
Алгоритм розроблюваного нами блока наведений на рисунку 4 і працює наступним чином: на блок прийому інформації та видачі команд надходять сигнали про стан технологічних параметрів від чотирьох блоків прийому інформації по всьому технологічному комплексу підйому, які умовно можна виділити як підсистему збору інформації. Алгоритм блоку прийому інформації та видачі команд передбачає підпрограми, на які поділяються алгоритми блоків, які передають на нього сигнали про стан технологічних параметрів. Алгоритм роботи даних блоків представлений на наступних рисунках:
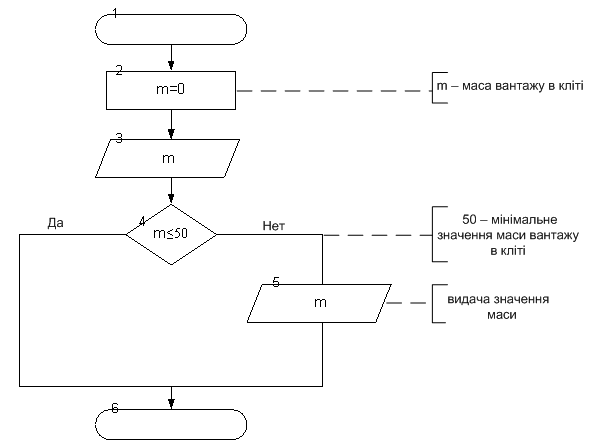
Рисунок 4 – Алгоритм роботи блоку прийому інформації № 2
Блок БПІ № 2 виконує функцію прийому інформації від датчика ДМВ про стан маси вантажу в кліті. Алгоритм роботи даного блоку полягає в наступному: в даному випадку опитування йде датчика маси вантажу в кліті, в якості якого може виступати тензодатчик. Передача даних буде здійснюватися в тому випадку, якщо маса вантажу в кліті m становитиме понад п'ятдесят кілограм.
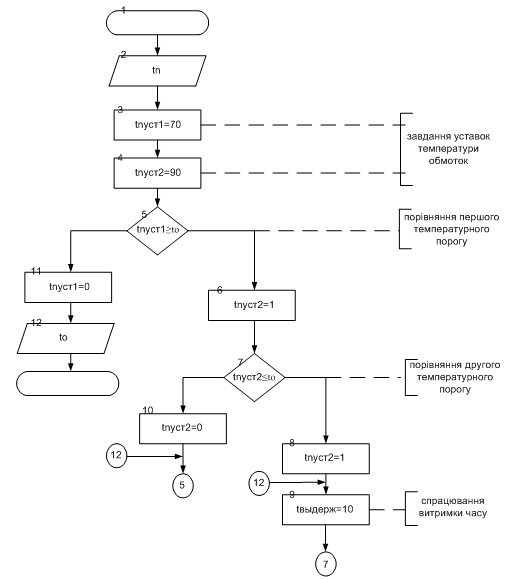
Рисунок 5 – Алгоритм роботи блоку прийому інформації № 1
Блок БПІ № 1 виконує функцію прийому інформації від датчика ДТВ про стан температури підшипникового вузла. Алгоритм роботи даного блоку полягає в наступному: в даному випадку інформація передається від датчика температури підшипникових вузлів. Спочатку програмно задаються дві уставки температури tnуст1 і tnуст2, які дорівнюють відповідно 70 і 90. При спрацьовуванні першого температурного порогу tnуст1 інформація передається на пульт диспетчера з видачею попереджувальної сигналізації. Далі порівнюється значення другого температурного порогу tnуст2, при перевищенні якого з витримкою часу tвидерж в 10с відбувається відключення двигуна підйомної машини, з видачею інформації на пульт диспетчера про перевищення заданої температури.
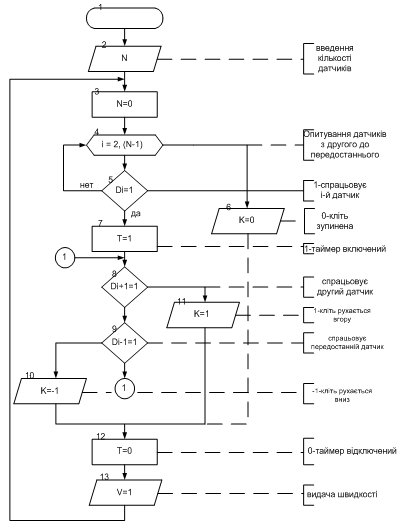
Рисунок 6 – Алгоритм роботи блоку прийому інформації № 3
Блок БПІ № 3 виконує функцію прийому інформації від датчиків ДШК і ДРК про швидкість і місцеположення судини в стовбурі. Алгоритм працює наступним чином: датчики контролю швидкості кліті N, у якості яких можуть застосовуватися індуктивні датчики, розміщуються по всій довжині стовбура. На кліть встановлюється магнітна мітка. При проходженні даної мітки через датчик, включиться таймер, і сигнал буде передаватися на пульт диспетчера. Відбуватиметься підрахунок кількості імпульсів, що дозволить судити про швидкість кліті, а також знаючи номер спрацював датчика, буде можливість судити про місцезнаходження кліті у стволі і про те, в якому напрямку вона рухається.
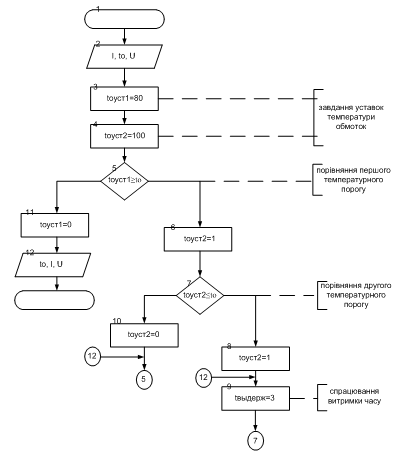
Рисунок 7 – Алгоритм роботи блоку прийому інформації № 4
Блок БПІ № 4 виконує функцію прийому інформації від датчиків ДС, ДН і ДТО про напругу, струмі і температурі обмоток двигуна. Алгоритм роботи даного блоку полягає в наступному: в даному випадку інформація передається від трьох датчиків: датчика температури обмоток, датчика струму і датчика напруги. Як і в попередньому випадку будуть задаватися дві уставки температури tоуст1 і tоуст2, які дорівнюють відповідно 80 і 100. Передача інформації про значення струму і напруги здійснюється безперервно і незалежно від температурних процесів електроприводу. При спрацьовуванні першого температурного порогу tоуст1 інформація передається на пульт диспетчера з видачею попереджувальної сигналізації. Далі порівнюється значення другого температурного порогу tоуст2, при перевищенні якого з витримкою часу tвидерж в 3с відбувається відключення двигуна підйомної машини, з видачею інформації на пульт диспетчера про перевищення заданої температури.
Выводы
У результаті дослідження проведений аналіз технологічного процесу підйому як об'єкта автоматизації, сформульована мета і задачі дослідження. Зроблено критичний огляд відомих технічних рішень з автоматизації процесу підйому. Вироблено обгрунтування та розробка системи автоматизації підйомної установки: була розроблена структурна схема автоматизації об'єкта та алгоритм роботи кожного блоку.
При написанні даного реферату магістерська робота ще не завершена. Остаточне завершення: грудень 2013 року. Повний текст роботи та матеріали по темі можуть бути отримані у автора або його керівника після зазначеної дати.
Перелік посилань
- Система управления и комплексной защиты шахтной подъёмной установки / [Кащич А., Марищенко А., Божок Н. и др.] // Cистемная интеграция, добывающая промышленность. – 2005. – №2. – С.26–34.
- Руководство по ревизии, наладке и испытанию шахтных подъемных установок: нормативное производственно–практическое издание/В.Р. Бежок, В.Г. Калинин, В.Д. Коноплянов, Е.М. Курченко; Под общей редакцией В.А. Корсуна. – Донецк, 2009. – 672 с.
- Дроздова, Л.Г. Стационарные машины: Учеб. пособие. – Владивосток: Изд-во ДВГТУ, 2007. – 157 с.
- Гаврилов П.Д., Гимельштейн Л.Я., Медведев А.Е. Автоматизация производственных процессов: Учебник для ВУЗов.– М.: Недра, 1985. – 216с.
- Правицкий Н.К. – Рудничные подъемные установки. –Харьков, 1956, 301 с.
- Аппарат защиты и контроля движения [Электронный ресурс]. – Режим доступа: http://www.ooo–yuep.com/ru/azkd
- ABB AB – Mine Hoist Systems [Электронный ресурс]. – Режим доступа: http://www.mining–technology.com/contractors/.
- Каталог продукции компании FHF [Электронный ресурс]. – Режим доступа: http://www.fhf–bt.org/.
- Стороженко М. А. Аппаратура управления и контроля рудничными подъёмными установками / М.А. Стороженко, А.Ф. Кирей. – М.: «Недра», 1980.
- Евстифеев А.В. Микроконтроллеры AVR семейств Tiny и Mega фирмы ATMEL. – 5-е изд., стер. – М.: Издательский дом «Додэка–XXI», 2008. – 560с.