Abstract
Content
- Introduction
- 1. Analysis of methods for removing scale
- 1.1 etching in sulfuric acid solution
- 1.2 etching in hydrochloric acid solution
- 1.3 etching in nitric acid solution
- 2.Testing of tensile
- 2.1 of experiencing the samples obtained from the flowsheet without descaling
- 2.2 of experiencing the samples obtained from the flowsheet using descaling
- 2.3 of experiencing samples obtained on the technological scheme which provides compression plate in the cold
- Findings
- List of sources
Introduction
On the Tube Works "Slavsant" (city Anthracite) for the production of electric-welded pipe is used as a blank roll-rolled hot-rolled. In the process of forming billets rolled into rolls into metal slag affects the quality of the finished product, working conditions and status of the instrument. Asked to perform descaling by the elastic-plastic bending strips. In the course of the work carried out tests of the mechanical properties of the initial samples and samples of strip strips obtained after removal of scale by alternating elastic-plastic bending and after compression. It was important to ensure that the strength and plastic properties of the metal will change acceptable for the stable operation of electric welding machine limits.
1. Analysis of methods for removing scale
1.1 etching in sulfuric acid solution
Sulfuric acid - strong dibasic acid. To use the technical etching acid. In accordance with GOST 2184-77 technical sulfuric acid produced in three grades: contact, towers and regenerated. The highest concentration of H2S04 monohydrate has contact sulfuric acid, which is divided into technical, containing 92.5% H2S04, technically improved (92,5-94,0%) H2S04, acid and oleum, containing no water.
Features metal etching in sulfuric acid solution as follows. Since the scale has a plurality of cracks, cavities and pores, reacting an acid with its components and clean the metal surface begins substantially simultaneously. Most easily interacts with nitrous acid, iron and magnetite and hematite dissolve poorly. Chemical etching process depends primarily on the thickness and structure of scale. Optimum etching conditions are created when the scale contains the maximum amount of wustite, and hematite is absent. As dissolution wustite layer scale adhesion to the base metal decreases. Under the influence of molecular hydrogen evolved scale mechanically separated from the substrate and deposited in the form of sludge on the bottom of the tub. Etching scale, not containing wustite, is very slow, which causes an increased waste of metal and the formation on the surface voids and pores. This creates the prerequisites for an intensive penetration of hydrogen in the steel and thus increases hydrogen embrittlement.
With increasing concentration of the sulfuric acid solution etching rate increases, reaches its maximum at a content of 25% solution, and then decreases in such a way that when 50% sulfuric acid concentration of the etching is very high. At high concentrations of sulfuric acid is nearly insoluble iron, which allows for transport and storage of concentrated sulfuric acid steel container. Typically the concentration of the etching solution does not exceed 20%, as its further increase leads to additional metal loss. When pickling in a sulfuric acid, a ferrous sulfate FeSO4, the number of which is increasing with increasing duration of use of the bath. With increasing concentration of the solubility of ferrous sulfate is reduced and it begins to crystallize in the solution as iron sulphate FeSO4 • 7H2O are deposited on the metal surface. The presence of large amounts of iron sulfate in the solution slows the etching duration, and the allocation of vitriol on the steel surface leads to a local nedotravu. With the accumulation of salts in a bath of sulfuric-acid composition of the iron must be periodically adjusted.
Atomic hydrogen into the metal and causes the so-called hydrogen embrittlement of steel, defining a number of characteristic appearance defects. Are hydrogen saturation slightly alters the strength characteristics were somewhat increasing the tensile strength and yield strength. Much stronger viscous properties vary with increasing duration of etching in 15% solution of sulfuric acid at a temperature of 70 ° C dramatically reduced elongation, reduction of area of ??the cross-sectional area. This means that the saturation metal hydrogen increases the tendency to brittle fracture.
In order to prevent hydrogen embrittlement and partial recovery of viscous properties of the steel etched metal subjected prolonged maturing or drying at a temperature of 100-200 ° C, in which process hydrogen evaporates. But is only a partial recovery of viscous characteristics. Thus, the reaction of the acid solution with the metal is undesirable since it leads to hydrogen embrittlement and irreversible loss of metal. The process of etching the metal in a solution of sulfuric acid are inherent in many significant shortcomings in economic, technological and environmental issues, which are due to the recent tendency for transition to the etching of the metal in hydrochloric acid solutions.
1.2 etching in hydrochloric acid solution
Hydrochloric acid - strong monobasic acid, which is a solution of hydrogen chloride in water. The main process for the preparation of hydrochloric acid - the synthesis of hydrogen and chlorine. The etching of the metal used synthetic hydrochloric acid technical (group B) with hydrogen chloride content 31% but GOST 857-69.
When the concentration of hydrochloric acid in contrast to the etching rate of sulfuric continuously and rapidly. The most favorable concentration of 15-20% should be considered. The etching solution of hydrochloric acid was used to a content of 1-5% free acid, the content of dissolved iron, should be not more than 100 g / l.
The advantage as compared with hydrochloric acid and sulfuric - etching rate is fast enough even at room temperature. The etching rate in a hydrochloric acid solution is more dependent on the concentration, and sulfuric acid - the temperature. With increasing temperature the rate of etching in hydrochloric acid solution increases. Heating of the etching solution is above 50 ° C is unacceptable because of the intense evaporation of harmful gases mainly as hydrogen chloride. Quantity of hydrogen etching in hydrochloric acid solution is much less than in sulfuric. Therefore saturation of the hydrogen etching in hydrochloric acid is also less. For example, the same hydrogen embrittlement were obtained by etching in 20% HCl and 5% H2SO4. The degree of hydrogenation metal by etching in hydrochloric acid solution 3-8 times lower than in solutions of sulfuric. Reduced hydrogen embrittlement - one of the main advantages of using hydrochloric acid.
The cost of neutralization of waste hydrochloric acid solutions is lower by 25%, and the process is much more efficient than in the neutralization of waste sulfuric acid. The possibilities are almost complete regeneration of hydrochloric acid solutions developed with the creation of environmentally friendly fully closed cycle. Table. 23 shows the modes of metal etching in a solution of hydrochloric acid. The disadvantage of this technology - heating the pickling solution to 60 ° C, which determines the increased volatility and deterioration of sanitary conditions in the etching department. Disadvantages of hydrochloric acid - the use of specialized containers during transport and storage, low working concentration in the etching, contributing to its high consumption and the need for additional storage tanks.
1.3 etching in nitric acid solution
Nitric acid - strong monobasic acid, the content of which both liquid and vapor amounts to 68.4%. Modern industrial methods for producing ammonia is based on the oxidation of oxygen. Diluted nitric acid produced 55, 47, 45% concentrated - 98 and 97%.
However, hydrogen is released during restores nitric acid to nitrous. Further recovery nitrous acid decomposes into nitrogen oxides and water As a result, by dissolving in nitric acid are not hydrogen, is the end product of the gaseous medium and the hydrogen absorption is no metal.
The gases in the etching is harmful to the respiratory organs.
2. Testing of tensile
2.1 of experiencing the samples obtained from the flowsheet without descaling
Tests were conducted on four samples tensile steel according to GOST 08kp 11701-804. Flat samples were tested (Figure 2.1)
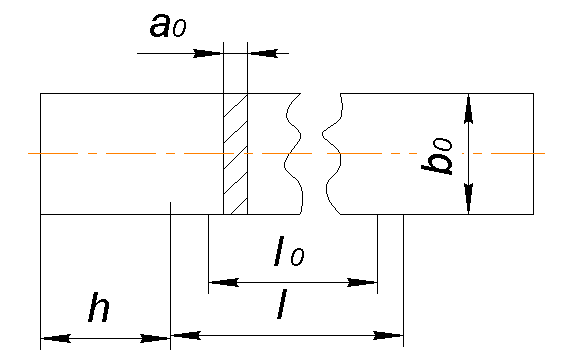
Figure 2.1 - Form of samples
The tests were carried out on a tensile testing machine P-10 (Fig. 2.2).
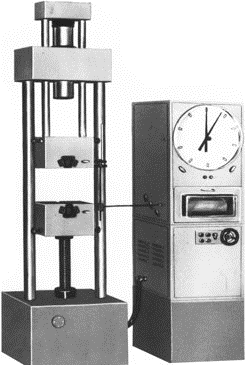
Figure 2.2 - Tensile Testing Machine P-10
Machine weight - 1260kg, max load - 100 kN, dimensions (LxWxH) - 1300h700h2500 mm, power supply - 380V. The prepared samples were fixed in the grips to the machine and it was applied pulling force. At the time of a significant jump in the value of his efforts was recorded (PT). Calculated the value of the yield stressèå ôèêñèðîâàëîñü (Pò). Ðàññ÷èòûâàëîñü çíà÷åíèå ïðåäåëà òåêó÷åñòè
Next, fix the value of effort that precedes the rupture of the sample (Pb). Calculated value of the yield strength.
There was a statistical analysis of the data and calculated the relative error of the experiment for each value.
Tests results presented in Figure 2.3.
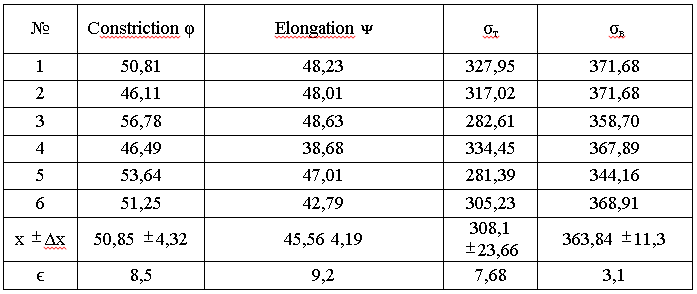
Figure 2.3 - Results of the tensile test specimens of steel 08kp
2.2 of experiencing the samples obtained from the flowsheet using descaling
The tests were conducted in a similar manner. Results on figure 2.4.
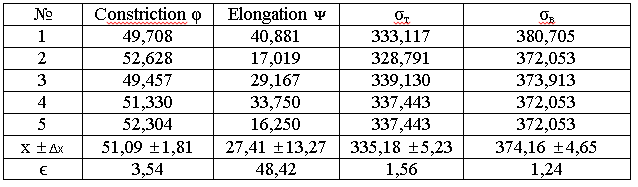
Figure 2.4 - Results of studies on the tensile specimens of steel 08kp after alternating elastic-plastic bending in the scale breaker
2.3 of experiencing samples obtained on the technological scheme which provides compression plate in the cold condition
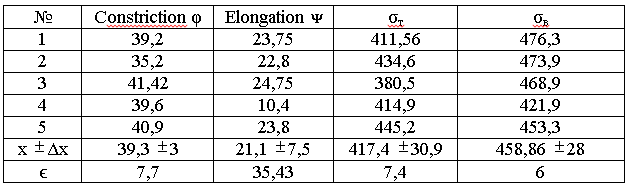
Figure 2.5 - Results of studies on the tensile specimens of steel 08kp after compression plate in the cold condition
Conclusion: test result showed that after applying the descaling change the mechanical properties of plastic and slightly, but after the application of compression occurs drop plastic properties and mechanical growth.
Findings
The proposed scheme descaling method of alternating elastic-plastic bending has a practical interest in the enterprise, in the near future to its industrial application. These innovations will improve the working conditions, the quality of the finished pipe. In the first part of this research work was carried out the following activities:
- In a review of existing methods for removing scale and concluded that instead of etching techniques it would be appropriate to use the method of alternating elastic-plastic bending.
- Been conducting research on the tensile specimens of the original billet samples that were subjected to an alternating-sign the elastic-plastic bending, and the samples that have been compressed. The experiments revealed that after alternating elastoplastic mechanical bending and plastic properties of the samples did not change significantly, indicating that the use of this method does not deteriorate descaling energy-power operating conditions forming mill.
In writing this essay master's work is not yet complete. Final completion: December 2013. Full text of the and materials on the topic can be obtained from the author or his manager after that date.
List of sources
- Matveyev YU.V., Vatkin YU.A., Krichevskiy YU.M. Svarnyye truby. - M.: Metallurgiya, 1972. - 184p.
- V.M.Druyan, YU.G.Gulyayev, S.O.Chukmasov. Teoriya ta tekhnologiya trubnogo virobnitstva.- Dnipropetrovs'k: RVA “DniproVAL”, - 2000,- p.587.
- Tekhnologiya staleprovolochnogo proizvodstva. - K., 1995, - 608p.
- Vinogradov A.G. Trubnoye proizvodstvo. - M.: Metallurgiya, 1981. - 344p.
- Suf'yanov, D. V. Teoreticheskoye issledovaniye protsessa prokhozhdeniya goryachekatannoy polosy cherez izgibno-rastyazhnoy okalinolomatel' / D.V. Su-f'yanov, N.N. Ogarokv, S.V. Denisov // Proizvodstvo prokata – 2012. - ¹ 10. p.31-34.