Реферат по теме выпускной работы
Содержание
- Введение
- 1. Актуальность темы
- 2. Цель и задачи исследования
- 3. Практическая часть
- Выводы
- Список источников
Введение
Железо и его сплавы являются основой современной технологии и техники. Еще в середине 70х годов прошлого столетия академик Патон Б.Е. назвал двадцатый век «железным», не согласиться с ним невозможно. В ряду конструкционных металлов железо стоит на первом месте и не уступит его еще долгое время, несмотря на то, что цветные металлы, полимерные и керамические материалы находят все большее применение. Железо и его сплавы составляют более 90 % всех металлов, применяемых в современном производстве.
Разработан ряд новых и эффективных способов повышения качества стали непосредственно в металлургическом производстве. В ИЭС им. Е. О. Патона разработана и прошла длительное опробование технология переплава различных отходов, относящаяся к специальным видам электрометаллургии, в частности к электрошлаковому переплаву. Отличительной ее ослбенностью является использование в качестве переплавляемого материала отходов в некомпактном виде. Отходы могут использоваться без подготовительных операций очистки.Электрошлаковый переплав стружки позволяет использовать возврат собственного производства для изготовления слитков, что значительно повышает коэффициент использования металла без снижения качества, надежности и работоспособности металлоизделий. Электрошлаковый переплав (ЭШП) является вторичным процессом рафинирования металлов. Он применяется для дальнейшей очистки после завершения первичных операций по удалению примесей и рафинированию. В качестве исходного материала обычно применяется сплошной расходуемый электрод из первичного металла, который может быть литым, полученным обработкой давлением или состоящим из лома. В 1971-72 гг. в том же институте был разработан процесс порционной электрошлаковой отливки, при котором в водоохлаждаемой изложнице при помощи не расходуемых электродов расплавляют смесь шлакообразующих компонентов. В изложницу через шлак заливают порцию стали из плавильного агрегата. При заливке электроды поднимают. После заливки ведут электрошлаковый обогрев, обеспечивающий поддержание зеркала металла жидким, тогда как залитый металл снизу затвердевает. Следующая порция заливаемой стали смешивается с остатком жидкой стали первой порции. Эти циклы повторяются до заполнения всей изложницы.
Электрошлаковое кокильное литье является разновидностью ЭШЛ. Технология электрошлакового кокильного литья позволяет получать отливки по механическим свойствам не уступающим прокату и без изменения химичемкого состава. Это двухстадийный процесс: вначале в электрошлаковой тигельной печи получают жидкий электрошлаковый металл, а затем заливают его в кокиль вместе со шлаком, использованным при плавке.
1. Актуальность темы
Важнейшим направлением совершенствования и развития отечественного литейного производства в условиях рыночных отношений является максимальное снижение себестоимости производимых литых заготовок при обеспечении заданного качества. По долгосрочным прогнозам стоимость металла непрерывно растет. В связи с этим перед предприятиями встает проблема полного использования любых отходов. Большую часть таких отходов составляет стружка. Переход металла в стружку составляет 25-50% при изготовлении деталей из заготовок. Переплав стружки в условиях рыночной экономики и конкуренции позволяет при рациональной технологии экономить значительное количество первичных дорогостоящих шихтовых материалов. Металлургами разработаны процессы Redsmelt, Hismelt, Primus, и др. Большинство этих процессов практически предусматривают длительный цикл подготовки отходов к переработке: сушка сырья, брикетирование, нагрев и удаление загрязнений, предварительное восстановление в твердой фазе, плавление и рафинирование, что значительно повышает цену металла. Электрошлаковая технология, характеризуется высокой экономичностью и широким диапазоном технических возможностей. Она обеспечивает высокое качество металла, получаемого переработкой металлоотходов (преимущественно стружки металлообработки), а так же электрошлаковая технология позволяет добиться сокращения затрат на всех стадиях переработки металлов и исключение некоторых стадий.
2. Цель и задачи исследования.
Целью исследования является исследование структуры слитка, полученного методом ЭШКП, исследование механических свойств полученной стали после различных видов термической обработки и разработка режима термической обработки для изделия шпонка, изготовленного из полученного металла.
3. Практическая часть
Для проведения исследования был выплавлен слиток с использованием стружки стали 40Х и стали 45, которая не подвергалась промывке и сушки (то есть возможны включения СОЖ, масла, окислов и т. п.) методом электрошлакового переплава нерасходуемым (графитовым) электродом. Был использован флюс основной марки АН-295, раскислители ФС-75+Аl(999), дополнительно был добавлен флюс АН-348А. Разливка стали проводилась под флюсом в кокиль. Затем был выполнен отжиг слитка и порезка его на образцы.
Был выполнен химический анализ слитка, который приведен в таблице.
Таблица – Химический состав слитка, % мас.
Зона слитка | С | Mn | Si | S | P | Cr | Ni | Cu | Al |
Верхняя часть | 0,57 | 0,63 | 0,11 | 0,024 | 0,021 | 0,32 | 0,229 | 0,18 | 0,052 |
Центральная часть | 0,49 | 0,62 | 0,12 | 0,024 | 0,023 | 0,34 | 0,229 | 0,18 | 0,047 |
Для исследования были отобраны образцы из трех разных участков слитка: верхней, средней и нижней части слитка. Изучение макроструктуры проводили на микроскопе Nu-2 при увеличении х100. Микроструктуру изучали на микроскопе Nu-2 при увеличениях х100 и х200. Количественную оценку пористости проводили с помощью программы Image Tool.
Микроструктура образцов показана на рисунке 1.
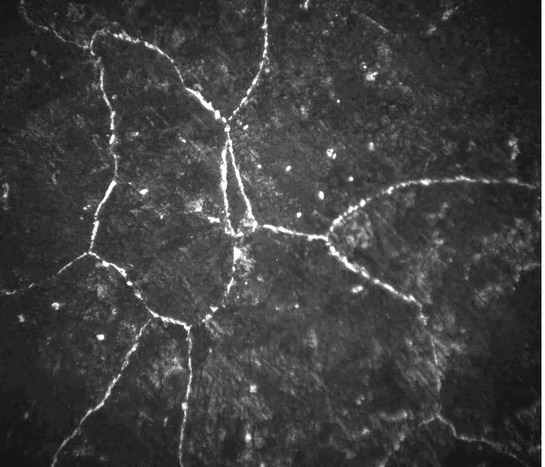
а) верхняя часть слитка в литом состоянии"
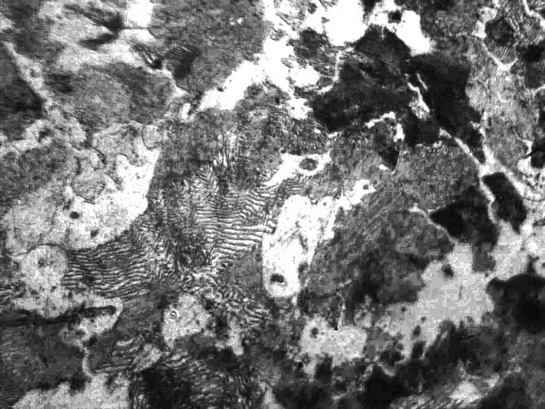
б) средняя часть слитка после отжига
Рисунок 1 – Микроструктура исследованных образцов
В результате обработки фотографий макроструктуры с помощью компьютерной программы Image Tool были получены частотные кривые распределения размеров пор по высоте слитка представлены на рисунке 2.
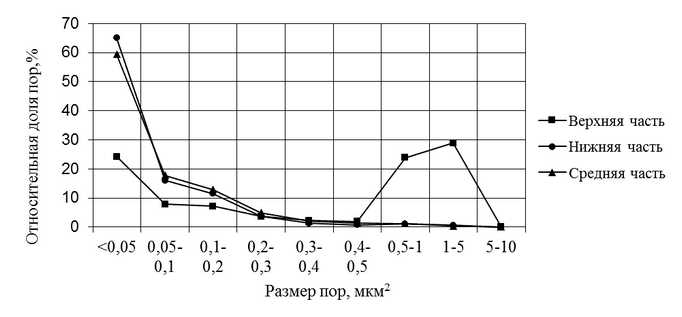
Рисунок 2 – Частотные кривые соотношения размеров пор и их количества
Как видно из рисунка, в верхней части слитка появляется большая доля пор со средней площадью 5 мкм2. В нижней и центральной части таких пор не обнаружено. Установленный эффект можно объяснить тем, что вместе с газовыми пузырями в верхнюю часть слитка поднимаются присутствующие в шихте загрязнения.
Выводы
Данная магистерская работа была посвящена актуальной на сегодняшний день проблеме по вторичному использованию металлических отходов механических цехов или подразделений. Рассмотрены различные методы переработки отходов механической обработки стальных изделий, из которых в качестве наиболее экономного был выбран и опробован метод переработки металлических отходов методом электрошлакового кокильного литья. В данной работе были рассмотрены распределения химического состава по высоте слитка, исследована его макроструктура и микроструктура, изучено распределение пор и их размеры по высоте слитка.
В дальнейшем планируется проведение механических испытаний на растяжение и ударную вязкость, для чего были изготовленны образцы по ГОСТ 1497-84 и ГОСТ 9454-78. Так же планируется изготовление контрольной шпонки из полученного слитка и разработка оптимального режима термической обработки для изготовленного изделия.
При написании данного реферата магистерская работа еще не завершена. Окончательное завершение: декабрь 2013 года. Полный текст работы и материалы по теме могут быть получены у автора или его руководителя после указанной даты.
Список источников
- Патон Б.Е., Медовар Б.И. Электрошлаковый металл / Патон Б.Е., Медовар Б. Н. - Киев: Наукова Думка, 1981. - 680 с.
- Кнорозов Б.В. Технология металлов и материаловедение / Кнорозов Б.В., Усова Л.Ф., Третьяков А.В. и др. – М. : Металлургия, 1987. – 800 с.
- Глебов А.Г., Мошкевич Е.И. Электрошлаковый переплав / Глебов А.Г., Мошкевич Е.И. - М.: Металлургия, 1985. - 343 с.
- Хольцгрубер В. Металлургические основы электрошлакового переплава сталей / Хольцгрубер В., Плекингер Э. // Черные металлы. - 1968. - № 12. - С. 30 - 41.
- Поволоцкий Д.Я. Электрометаллургия стали и ферросплавов / Поволоцкий Д.Я., Рощин В.Е., Мальков Н.В. - М.: Металлургия, 1995. - 592 с.
- Клюев М.М., Каблуковский А.Ф. Металлургия электрошлакового переплава / Клюев М.М., Каблуковский А.Ф. - М.: Металлургия, 1969. - 256 с.
- Медовар Б.И. Электрошлаковая технология за рубежом / Медовар Б.И., Цикуленко A.K., Богаченко А.Г. и др. - Киев: Наукова думка, 1982. - 319 с.
- Пат. 2263560 Российская Федерация, МПК B22D23/10, C22B9/18. Способ электрошлакового кокильного литья. Шульгин А.Ю., Карицын О.Н., Ранич С.Д., Авдюхин С.С.; заявитель и патентообладатель ООО "НОРМА-ИМПОРТ ИНСО". – № 2003110866/02; заявл. 16.04.03; опубл. 20.10.04.
- Гаревских И.А. Преимущества и вопросы совершенствования электрошлакового переплава стали / И.А. Гаревских, Ю.А. Шульте, В.Д. Максименко и др. // Сталь. - 1962. -№ 1.- С. 39-41.
- Лахтин Ю. М. Металловедение и термическая обработка металлов / Лахтин Ю. М. – [3-е изд.]. – М. : Металлургия, 1983. – 365 с.
- Бернштейн М. Л. Металловедение и термическая обработка стали // Т. 1 Методы испытаний и исследования / Бернштейн М. Л., Рахштадт А. Г. - М.: Металлургия, 1983. - 352 с.
- ГОСТ 1497-84. Металлы. Методы испытаний на растяжение. – М. : Издательство стандартов, 1985.
- ГОСТ 9454-78. Металлы. Метод испытания на ударный изгиб при пониженной, комнатной и повышенных температурах. – М. : Издательство стандартов, 1979.