Реферат по теме выпускной работы
Содержание
1. Теоретическая часть
Прокатный передел, являясь завершающим в полном металлургическом цикле, занимает в металлургии особое место. Он обеспечивает продукцией проката многих потребителей нашей страны и за рубежом. Сотни прокатных, станов металлургических заводов нашей страны поставляют машиностроительной промышленности, транспорту, строительным и другим организациям тысячи профилеразмеров проката.
Задачи постоянного совершенствования прокатного производства, увеличения производительности прокатных станов, расширения сортамента, роста количества проката из легированных и специальных сталей, поставки металлопродукции по теоретической массе и со знаком качества требуют постоянного улучшения качества прокатных валков.
Валки прокатных станов являются рабочим инструментом, при производстве и выполняют основную операцию прокатки - деформацию (обжатие) металла и придают ему требуемую форму. В процессе деформации металла, вращающиеся валки воспринимают давление, возникающее при прокатке, а также ряд других нагрузок и воздействий, связанных с этим.
К качеству прокатных валков предъявляются очень высокие требования потому, что они определяют нормальную работу стана, его производительность и качество выпускаемого проката.
Основной проблемой при изготовлении прокатных валков является выбор оптимальных режимов их термической обработки. Выбор того или иного режима зависит от условий работы валков. Применение отжига после ковки обусловлено необходимостью перекристаллизации структуры кованого металла, снижения твердости и уровня остаточных напряжений, предупреждения флокенообразования. Для получения мелкодисперсной структуры и растворения карбидной сетки часто после отжига валков применяют термическое улучшение.
Режимы термической обработки валков являются достаточно сложными и длительными, включают большое количество операций, разное время выдержки и как следствие, процесс в целом имеет различную продолжительность. Особенностью термической обработки заготовок больших сечений является возникновение значительных напряжений — термических, структурных и механических.
В современной металлургии существует ряд задач, в которых необходимо прогнозирование структуры стали после термической обработки. Исследование структурных превращений ведется, в основном, по изотермическим и термокинетическим диаграммам. Однако они имеют ограниченное применение, так как справедливы только для определенного химического состава стали. Также термокинетические диаграммы не могут дать достоверных сведений о структуре стали, если режим охлаждения отличается от режимов охлаждения в экспериментах. По этой причине термокинетические диаграммы используются только для количественной оценки устойчивости аустенита при непрерывном охлаждении.
2. Цели и задачи исследования
Целью данной магистерской работы является разработка лабораторных методов, позволяющих на основе результатов математического моделирования, осуществить физическое моделирование структурообразования прокатного валка из стали 70Х3ГНМФ диаметром 981мм и длинной 1866 мм на образцах малого сечения.
3. Практическая часть
С помощью программы ANSYS был построен график, показывающий изменение скорости охлаждения валка по его сечению после нагрева до температуры закалки, соответствующей 850°С.
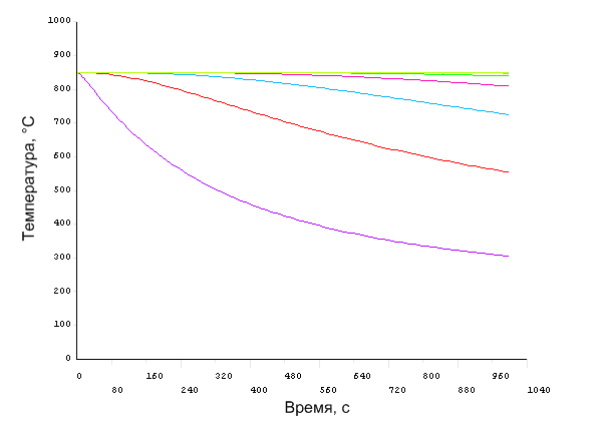
Рисунок 1- Охлаждение валка из стали 70Х3ГНМФ
По методике, предложенной Е. И. Казанцевым в справочном руководстве для расчетов и проектирования «Промышленные печи», были построены кривые, характеризующие различные скорости охлаждения модельных образцов сечением 20мм путем изменения температуры окружающей среды. Выяснили, что охлаждение при 400°С, наиболее близко характеризует охлаждение поверхности прокатного валка, а охлаждение при 500°С дает представление о том, как будет происходить охлаждение на расстоянии 80мм от поверхности валка. Эти кривые были нанесены на исходный график.

Рисунок 2- Охлаждение валка из стали 70Х3ГНМФ с наложенными кривыми охлаждения образцов(1-охлаждение при 400°С; 2- охлаждение при 500°С)
Была выполнена термическая обработка на образцах из заданной стали сечением 20 мм, которая заключалась в нагреве образцов до 850°С с дальнейшим переносом в печь, нагретую до 400°С и 500°С и выдержкой там 30минут. Окончательное охлаждение проводилось на воздухе.
После термической обработки была измерена твердость образцов и изучена их микроструктура. Твердость образца, после выдержки при 400°С составила 53HRC, а после выдержки при 500°С - 54 HRC. Микроструктура образцов приведена на рисунке 3.
Рисунок 3- Микроструктуры образцов после нагрева до 930°С с последующей выдержкой при 400°С и 500°С(1-охлаждение при 400°С; 2- охлаждение при 500°С)
В дальнейшем планируется проведение более тщательного анализа полученных данных и проверка достоверности результатов.
Список источников
- Гун Г. С. Обработка прокатных валков / Гун Г. С., Соколов В. Е., Огарков Н. Н. – Москва: Металлургия, 1983. - 112с.
- Требования к валкам широкополосных станов горячей прокатки / [утв. Сахаров О. Г.]. – Краматорск: Новокраматорский машиностроительный завод, 2000. – 17с.
- Гедеон М. В. Термическая обработка валков холодной прокатки / Гедеон М. В., Соболь Г. П., Паисов И. В. - Москва: Металлургия, 1973. - 344с.
- Медовар Л. Б. Современные валки прокатных станов. Требования, материалы и способы производства / Л. Б. Медовар, А. К. Цыкуленко, В. Е. Шевченко // Общие вопросы металлургии. – 2001. – с. 38.
- Мерзляков В. И. Обработка и ремонт прокатных валков / Мерзляков В. И. – Москва: Металлургия, 1957. – 235с.
- Горбатюк С. М. Повышение стойкости прокатных валков. / Горбатюк С. М., Седых Л. В. // Металлург. – 2010. - № 5. – с. 53-54.
- Малыхина О.Ю. Влияние основной термообработки на структуру и свойства кованой стали 150ХНМ. / Малыхина О.Ю., Титова Т.И., Шульган Н.А., Солнцев Ю.П. // Деформация и разрушение материалов. – 2006. - № 8. – с. 26-29.
- Валки листовых станов холодной прокатки / [Новиков В. Н., Белосевич В. К., Гамазков С. М., Смирнов Г. В.]. – М. : Металлургия, 1970. – 336 с.