Abstract
Сontent
- Introduction
- 1. Theme urgency
- 2. Goal and tasks of the research
- 3. The main material
- 3.1 The concepts of "efficiency" and "effectiveness"
- 3.2 The terms "process" and "process approach"
- 3.3 Determination of the effectiveness of production processes
- 3.4 Determination of the efficiency of production processe
- Conclusion
- References
Introduction
Ukraine's transition to market-based forms of management has created many complex economic problems. And one of them is economic efficiency and effectiveness of production. The main tasks of economic development at the present stage is the all-round increase production efficiency and stable employment positions by enterprises in the domestic and international markets. To survive the intense competition and win the trust of customers need it to stand out against the background of the enterprises of the same type.
It is well known that the buyer interested in the quality of products, and its price. The higher quality and lower price, the better and more profitable for the buyer. These indicators are just enclosed in cost of products. Thus, the cost is the basis for determining prices for the products. The systematic reduction of the cost of industrial production – one of the basic conditions for improving the efficiency of industrial production.
Production cost has a direct impact on earnings, the level of profitability. Therefore, the formation of production and distribution costs, their records are important for business organizations. From the level of the cost of production depends on the amount of income and the level of profitability of the enterprise: the economical use of manpower, material and financial resources in the production process, the higher the efficiency, the greater the profit.
World practice shows that the implementation of such a problem is usually guaranteed by the presence in the organization of the quality management system (QMS), which must conform to the principles of Total Quality Management (Total Quality Management – TQM). Total Quality Management is a philosophy that can and should be the basis of this activity for the continuous improvement of all processes of the organization. The philosophy of TQM is directly related to and based on a series of quality assurance standards laid down in a series of international ISO 9000 standards developed by the International Standards Organization (International Organization of Standartization – ISO).
1. Theme urgency
Efficiency – the most important socio-economic category, which is characterized by the properties of dynamism and historicity. At all stages of the historical development of society has always been interested in the question: What price costs and resources is achieved final production results. Consequently, the initial model is a quantitative evaluation is the ratio between the economic results and the costs of resources.
Maximization of outcomes per unit costs and resources and the minimization of costs and resources per unit of outcome – that is the primary purpose of the society and in the workplace, the individual. The critical state of the economy with particular relevance raises the need to address issues related to improving the efficiency of production.
General economic crisis worsens and complicates the solution of the problems of economic efficiency, makes it necessary not only in-depth study of its causes, but also the justification of new, innovative ways of overcoming the current economic situation.
This determines the relevance of the study, the need for theoretical and practical generalization performance management processes at the level of industrial production facilities (equipment), and solves problems through the creation of a mechanism to increase economic efficiency. Improving the efficiency and effectiveness of production is one of the most urgent problems, the successful solution of this problem provides tremendous opportunities decisions for the further development of the economy and improve the living standards of the population.
2. Goal and tasks of the research
The aim of this study is to examine ways to improve the effectiveness and efficiency of the production based on the requirements of ISO 9000.The task is to examine, analyze and study a mechanism to increase the efficiency and effectiveness of the production activity, the identification of factors and methods to increase the efficiency of production and put them in the industrial sector of Ukraine.
3.The main material
3.1 The concepts of "efficiency" and "effectiveness"
It is well known that the category of efficiency can be classified as the key to the economy. Efficiency is one of the most important indicators of human activity, taken from the point of view of its ability to provide the final result. As the economic efficiency category provides a unified qualitative and quantitative characterization of the effectiveness of management [1].
It is generally accepted that the term "efficiency" originally appeared in the economics literature in the works of William Petit (1623-1687 years) – English economist, the founder of classical economics, the founder of the labor theory of value - and the head of the school of the Physiocrats, the French economist Francois Quesnay (1694–1774 years). However, as independent economic concept of "efficiency" are not developed. They used the term to mean the performance and used it to evaluate these or other governmental or private actions, depending on whether or not they contributed to the revival of economic life [2].
Most authors agree that the founder of the theory of economic efficiency is a prominent Scottish economist Adam Smith. Later his ideas were developed in the writings of D. Ricardo, Marx and others. Representative of classical political economy, David Ricardo (1772–1823 years) have attempted to assess the effectiveness of capital. In particular, he proved that the less durable capital, the greater the need to constantly spent working for the preservation of its original efficiency. In D. Ricardo, the term "efficiency" is not used in the sense of "performance", and the ratio of the cost to a certain type. Since that time, the concept of "efficiency" acquires the status of an economic category [3].
Karl Marx said that "the production of effective when the minimum capital advanced to produce the maximum amount of product with the lowest possible amount of effort and resources." Contribute to the development of the category of performance made by such foreign scientists, as Peters T., Waterman R., J. Harrington, A. Fayol, G. Emerson, F. Taylor, Henry Ford and others, whose opinions converge in the fact that it is effectiveness from the point of view of managers is the most important characteristic of the company.
However, the "effectiveness" as an independent economic concept they have not explored, and only used the term to mean the impact of management and viewed it at the macro level on the actions of the subject of management – the state government. Thus, register C.R. McConnell and S.L. Bru directly science itself is defined by the concept of efficiency. According to the authors of "The Economics explores the problem of efficient use of scarce productive resources or management in order to meet the material needs of man." They note that the economic efficiency "describes the relationship between the number of resource units that are used in the production process and the resulting quantity of any product. More product from part of cost efficiency means. A smaller amount of product from a given amount of costs indicates reduced effectiveness " [4].
In domestic economic literature devoted to the concept of efficiency many scientific papers and studies. Discussions in this regard have not stopped with the beginning of radical economic transformation, when the plan was first put forward by other, seemingly more pressing issues. In overview, the efficiency (in Latin – an effective, productive, which gives the result) characterizes the development of various systems, processes and phenomena. The effectiveness serves as an indicator of development. She is its most important stimulus. In an effort to increase the effectiveness of a particular type of activity, and their set, we define the specific measures to facilitate the development process, and cut off those that lead to regression. As a category, it has two sides – qualitative and quantitative. The qualitative aspect reflects its logical, theoretical content that is the essence of the category.
The quantitative aspect reveals the effect of the law of economy of time, and it reflects the time savings in achieving the goals of social production during the whole reproductive process and its individual phases in the scale of the entire national economy and its individual regions, industries, business entities. That is, for all historical stages of development of human society, it must economize their strength, reaching expansion of output at the lowest cost of funds. And this is an objectively existing criterion of economic efficiency at all stages of the development of society. Several authors, including, A. Bugutsky, P.T. Sabluk, J.N. Novikov, M.M. Karaman think the effectiveness – it is not just the impact of production, and the ratio of the result or the effect of production to the cost of social labor. Thus, from the viewpoint A. Bugutskogo, production efficiency can be viewed as producing a cost-effective product, using a minimum amount of resources for a certain amount of product at minimum average total cost [5].
At the same time, D.C. Sabluk believes that the criterion of efficiency always shows the ratio of benefits to cost. Y.N. Novikov pointed out that the concept of "economic efficiency" is always a positive result, which is expressed in monetary terms. V.G. Andrijchuk defines economic efficiency as a ratio between resources and results of production at which receive cost indicators of production efficiency [6].
M.M. Karaman said that economic efficiency – the ratio of the result and all the cost of labor and the means used for its production [7].
Improving the efficiency of production is one of the most urgent problems, the successful solution of this problem provides tremendous opportunities decisions for the further development of the economy and improve the living standards of the population [8].
One of the conditions for the success of any enterprise in accordance with the requirements of MS ISO 9000 is to monitor and measure performance. However, any result may be interesting if it can be compared with the cost of its preparation. In other words, in the analysis of the company should be compared the effectiveness (the requirements ISO 9001:2008) with efficiency (the requirements ISO 9004:2000) [9].
Effectiveness is determined by the standards of ISO 9000:2005 as the extent to which planned activities and the achievement of planned results. In addition, explained that the impact can be considered enforcement, achieving (the degree of completeness of the action), performance, conduct (degree of execution) team responsibilities (debt), destination (target) promises. Efficiency, according to the standard ISO 9000:2005 – the relationship between the result achieved and the resources used [10].
The essence of efficiency – something that can be characterized by a certain number (the result achieved), that is the result of traditional attitudes to costs. In English, there are two terms – efficiency and effectiveness, the dictionary equivalents are the same – the "efficiency". However, between these terms there is a meaningful distinction: efficiency generally refers to the use of resources (resources), while the effectiveness (performance) is related to the organizational goals, behavior and development. In the first case, the notion of rationality characterizes the degree of effectiveness of the use of financial, organizational, material, time and human resources. Effective organization is focused on achieving effects due to structural and resource optimization and control of in-house costs. In the second case, the term "effect" is used in the context of relations "cause-result." On the relation between efficiency and effectiveness referred to in his famous work on management. "To be successful for a long time in order to survive and achieve its goals the organization must be both effective and efficient." According to the eminent scholar Peter Drucker, the efficiency is due to the fact that "should be done the right things (doing the right things). Both the first and second equally important ..." [11].
Effectiveness, in the sense that "do the right thing" is something intangible, it is difficult to determine, especially if the organization is internally inefficient. However, the effectiveness can usually measure and quantify, because it is possible to determine the monetary value of its inputs and outputs. That performance as an indicator of the correct doing things must be quantified. Consequently, the performance – a certain indicator of a certain process, an indication that the end result of the process is something, pre-planned.
Under the productivity of the organization refers to its ability to achieve the goals set by external, focus on the fact that all of its organizational decisions and actions meet the criteria set by the external environment. This is the focus of organizations on a constant search for new opportunities in the creation of new products, investment in the adaptation of its internal environment to the external circumstances and conditions of the activity for the future. In this way, organizations can be very effective, but is not effective.
3.2 The terms "process" and "process approach"
"The process – a set of interrelated or interacting activities which transforms inputs into outputs" or the English version of "Process – set of interrelated and interacting activities which transforms inputs into outputs". Process – a series of operations (activities) that take place over the source material (process), increase its value and lead to a definite result (the exit process). The value of the raw material increases due to the introduction of qualification of labor and knowledge [12].
Thus, a process – a sequence of actions grouped: – By type of activity (similar functions); – According to the result of (product); – In the added value for the client. Developers latest international standard quality system certification ISO 9000 emphasize that the main achievement of this version is just a process approach to achieve quality. ISO 9001 – quote: "This standard advocates the principle of the" process approach" when developing, implementing and improving the effectiveness of the quality management system to enhance customer satisfaction through the fulfillment of their demands. The successful operation of the organization shall determine and manage numerous linked activities.
An activity using resources, and managed to transform inputs into outputs, can be considered as a process. Often the output from one process directly forms the input to the next. The use of a system of processes in the organization, along with the identification and interactions, as well as their management processes can be considered as the "process approach". The advantage of the process approach is the ongoing control, which it provides at the junction of the individual processes within their system, as well as combinations and interactions.
Under the process approach to organizing and managing the activities of the enterprise (Figure 4.1) refers to the alignment of the company on business processes and enterprise management system to control how each business process separately, and all of the business processes. In this case, the company's quality system ensures the quality of technology execution of business processes within an existing or prospective organizational structure and organizational culture of the company.
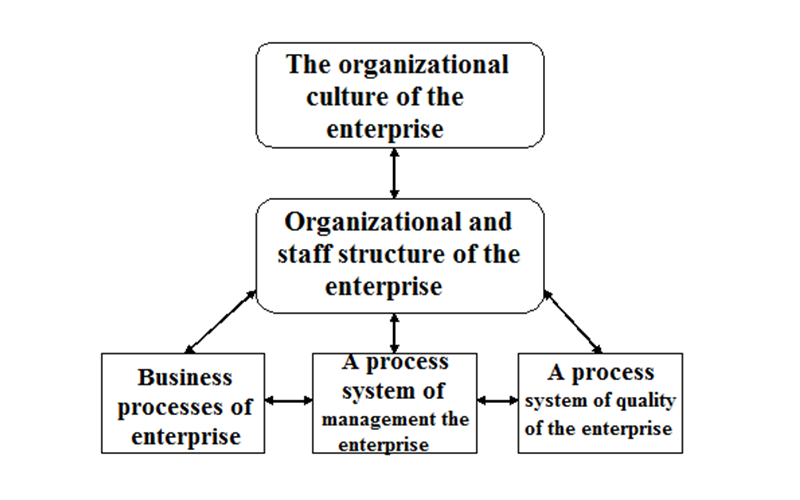
Figure 4.1 – Key elements of the process approach
As part of the process approach any enterprise is considered as a business system, which is a connected set of business processes, which are the ultimate goals is to manufacture products or services. Under the Business Process means a series of different activities, which together create a result (product, service) that has value to the customer, client or customer. The client can be another business process.
3.3 Determination of the effectiveness of production processes
To obtain an objective and reliable assessment is necessary that the performance of all processes determined by the overall scheme, which should be documented in the enterprise and updated as necessary. In the proposed algorithm, the definition of performance begins with the selection process and collects the necessary information for it, which can serve as sources of reports of departments, acts, protocols, regulatory documents, etc. Depending on the specific process and available data necessary to develop a list of indicators that best at the moment can describe the state of the process.
These indicators should meet the following requirements [13]:
– Unique (link with strategic indicators of the organization);
– "Transparency" for the leaders of the organization;
– Clarity of staff performing the process;
– Measurability (indicators should be measurable in numerical terms);
– Convenience for the owners of processes governing them on the basis of these indicators.
Avoid complex and difficult to measure indicators. It is best to be limited to simple indicators based on common sense.
It is necessary that the selected system process performance was:
a) complete enough to adequately assess the results of the processes and procedures;
b) the value of its values should be adequate information;
c) intuitive and easy enough to analyze and compare the information.
Normalized values of the indicators are selected on the basis of previous experience on the status and functioning of the process, as well as taking into account the requirements of regulatory documents. These values can be specified in the passport process. It is also necessary to decide the question of the target values of indicators, the sources of which are the policy and quality objectives, strategic plans, the company and its subsidiaries. The calculation formula for determining the current value of the index should reflect the meaning of the concept of "efficiency." The resulting value must be compared with the target values and the normalized performance indicator process and determine what actions need to be taken with respect to this indicator. Once all the parameters of the process considered necessary to calculate the overall efficiency of the process, taking into account the weight of its performance and evaluate.
3.4 Determination of the efficiency of production processes
Measuring the effectiveness of production involves the establishment of criteria of economic efficiency, which should be the same for all parts of the economy – from the enterprise to the national economy as a whole. Thus, the general criterion of economic efficiency is the increase in the productivity of social labor. Currently, the economic efficiency of production is estimated on the basis of this criterion, which is expressed in maximizing the growth of national income (net output) per unit of labor. At the level of the enterprise form a single criterion of efficiency of its activity can serve to maximize profits.
Production efficiency is specific quantitative expression in an interconnected system of indicators of the efficiency of the main elements of the manufacturing process.
The system of indicators of economic efficiency of production must comply with the following principles:
– Ensure the relationship of specific criteria and indicators of efficiency;
– To determine the level of efficiency in the use of all types used in the production of resources;
– Be capable of measuring the efficiency of production at different levels of governance;
– To encourage the mobilization of internal reserves to improve production efficiency.
In view of the above principles defined the following metrics efficiency.
1) The summary measure:
– The production of net output per unit of input resources;
– The profit per unit of total costs;
– Profitability of production;
– The cost of 1 ruble of commodity production;
– The share of output growth through intensification of production;
– Economic effect of use per unit of output;
2) the use of performance indicators of labor (staff):
– The growth rate of labor productivity;
– The share of output growth by increasing productivity;
– Absolute and relative release of employees;
– Utilization of useful fund of working time;
– Labor input per unit of output;
3) the use of performance indicators of productive assets:
– Total assets ratio;
– Return on assets ratio of the active part of fixed assets;
– Return on capital assets;
– Capital intensity per unit of output;
– Material consumption per unit of output;
– Utilization of the most important kinds of raw materials;
4) The performance indicators of financial assets:
– Working capital turnover;
– Return on working capital;
– The relative release of working capital;
– Specific capital investment (per unit increase in capacity or production);
– Return on capital investments;
– Payback period of capital investment, etc.
The level of economic efficiency in the industry depends on the variety of interrelated factors. For each industry due to its technical and economic features characterized by specific factors of efficiency.
All variety of growth factors, efficiency can be classified according to three criteria:
1) improve the efficiency of the sources, the main ones are: reduction of labor, materials science, the fund and the capital intensity of production, natural resources, saving time and improving product quality;
2) The main areas of development and improvement of production, which include: accelerating scientific and technological progress, improving technical and economic level of production, improvement of the structure of production, the introduction of organizational systems and controls and improve the forms and methods of production, planning, motivation, work, etc .;
3) in terms of the production management system, depending on factors which are subdivided into:
a) internal (-internal), the main ones are: the development of new products, mechanization and automation, the introduction of advanced technology and advanced equipment, improved use of raw materials, fuel, energy, improvement of management style, etc.;
b) external – is the improvement of the branch structure of industry and manufacturing, government economic and social policy, the formation of market relations and market infrastructure, and other factors [14].
Conclusion
The key to success of any company lies in the continuous improvement of the effectiveness and efficiency of production, a systematic analysis of production activities, the development and implementation of measures aimed at improving the effectiveness and efficiency of production. In this paper the concept of "efficiency", "effectiveness", "process", "process approach", is considered one of the methods to assess the efficiency of production processes. To function effectively, organizations need to identify and manage numerous interrelated and interacting processes.
Often the output from one process directly forms the input to the next. Systematic identification and management processes used by the organization, and above all to ensure their interactions can be considered as the "process approach". On the basis of the process approach the organization must identify the processes of design, production and delivery of products or services. With process control is achieved by meeting the needs of customers. As a result, management the results of the process transition in the management of the process itself. The effectiveness of the organization can be improved through the creation and management of a system of interrelated processes. This means that the organization should strive to join the process of creating products or services to the processes that allow tracking compliance of the products or services the needs of the customer.
This master's work is not completed yet. Final completion: December 2013. The full text of the work and materials on the topic can be obtained from the author or his head after this date.
References
- Економічна енциклопедія : у 3-х т. Т. 1 / редкол. В. Мочерний (відп. ред.) та ін. – К. : Вид. центр "Академія", 2000. – 864 с.
- Проблема эффективности в современной науке // Под ред. А.Д. Урсула. – Кишинев. Изд-во Штиинца, 1985. – 256 с.
- Рикардо Д. Начала политической экономики и податного обложения / Д. Рикардо. М. : Госиздат, 1929. – 368 с.
- Макконел К.Р. Экономикс: Принципы, проблемы, политика. В 2 т. / К.Р. Макконел, С.А. Брю – М.: Республика, 1992. – Т.1. – 399с.
- Бугуцкий А.Л. Повышение эффективности труда в сельском хозяйстве / Бугуцкий А.Л. – Е. : Урожай , 1990. – 168с.
- Андрійчук В.Г. Економіка аграрних підприємств/ Андрійчук В.Г. – 2. вид., доп. і перероб. – К.: КНЕУ, 2004. – 624с. – Бібліогр.: с. 612-614.
- Караман М.М. О сущности эффективности и экономической эффективности сельскохозяйственного производства в переходный период к рыночной экономике, их критерии и показатели/ М.М. Караман //Экономика Крыма. Научно-практический журнал. – 2002. – №4. – с. 10-13.
- Омельченко Е.В. Организационно-экономические основы повышения эффективности российского производственного предпринимательства: дис. д-ра экон. наук / Е.В. Омельченко. – М.: Российская академия предпринимательства,2002. – 314 c.
- Момот А.И., Бакало Е.А. Соотношение понятий «результативность» и «эффективность» при осуществлении производственной деятельности// Матеріали 6-ої Регіональної науково-практичної і студентської конференції. "Проблеми розвитку та упровадження систем управління якістю в регіоні". – Донецьк: ДонНТУ, 2009. – С. 114-117.
- Системы менеджмента качества. Основные положения и словарь. Третье издание : ISO 9000:2005. – [Действующий с 15.09.2005]. – Группа компаний «ИНТЕРСЕРТИФИКА», 2005. – 41с. – (Международный стандарт).
- Питер Ф.Друкер. Эффективный управляющий – Москва: BCI, 1994 – 268 с.
- Басовский Л.Е., Протасьев В.Б. Управление качеством: Б 27 Учебник. – М: ИНФРА7М, 2001. – 212 с. – (Серия «Высшее образование»).
- Определение результативности процессов СМК. Бурова Н.Д., Жмаев А.Н., Жилкин В.М [Электронный ресурс].– Режим доступа: http://www.klubok.net/article2265.html
- Т.А. Фролова. Экономика предприятия: конспект лекций [Электронный ресурс].– Режим доступа: http://www.aup.ru/books/m170/12_5.htm