Abstract
Contents
- Introduction
- 1. Relevance of the theme
- 2. Research goals and objectives, expected results
- 3. Review of existing studies
- 4. Analysis of the issues of structural and technological support for rotary machines
- 5. Study design issues multinomenclature rotor systems.
- Conclusions
- References
Introduction
High growth rates of world engineering continuously connected with the introduction of new progressive methods of processing metals. One of the ways of progressive engineering technology is the transition to metal forming in the cold instead of cutting . Application of this method of processing leads to a significant increase in productivity, improved accuracy , better mechanical properties and surface finish of machined parts and creates the preconditions for complex automation [ 2 ].
Currently, for the effective functioning of the enterprise throughout the automation is introduced , it becomes an integral part of the production process. And rightly and profitably , because reduce costs and improve product quality. Automated production - a system of machinery, equipment , vehicles, providing strictly coordinated in time execution of all stages of manufacturing of products , ranging from the preparation of starting and ending blank control ( test ) and finished product output at regular intervals [ 1 ].
1. Relevance of the topic
large proportion of time spent on productive work , in manufacturing machines and total duration of the production cycle , doing particularly acute problem of automation of production operations. Value of the solution to this problem depends not only on the task of improving product quality , cost of production and increase productivity. Automation of production processes through the application of technological systems of continuous action , made on the basis of rotor and rotor-conveyor machines, especially effective for mass production . That is, the development of structural and technological support for rotary machines for the manufacture of mass production is very urgent scientific task that is essential to the national economy .
For most characteristic mass production of one type of product , in which the required performance production machines is sufficient to ensure the conditions of merchantability machines combined into an automated system . However, in most cases, the production of consumer goods in the production of the means of production necessary release of the products of many different nomenclatures for a total mass release program product of any specific purpose (eg , jewelry, clothing, footwear and furniture accessories , bearings, power sources , resistors, capacitor electrodes , etc.). In this program of release of products for each of the nomenclature may be insufficient to ensure the conditions of merchantability automatic machine system . Similar problems are increasing in the current economy and the solution to these problems is the use of machines and lines multinomenclature [ 3 ].
2 . The purpose and objectives of the study
aim of this work is to improve the production of threaded parts on automatic rotary lines by combining large scale production of the group of products in several sizes in diversified mass , creating the desired structure of the entire system and components for products in several sizes .
This goal involves the solution of such problems :
- Analyze designs of rotary machines and lines, to explore issues of their design, especially manufacturing rod fasteners .
- investigate questions grouping items for co-processing in tool boxes .
- Develop methodology for structural synthesis of new multinomenclature rotary machines , which is carried out on the thread roll forming products in several sizes in each tool box.
- Complete analysis of the characteristics of rolling threads in multinomenclature rotary lines when combining large scale production in the mass .
object of study : process of manufacturing fasteners for automatic rotary diversified line.
subject of research : Thread rolling particularly instrumental in the group block automatic rotary diversified line .
3 . Review of existing studies
Issues of improving structures , processes and productivity of continuous systems has been widely discussed domestic and foreign authors . In these works, made ??deep studies of the operation of automatic rotor lines and developed a large number of different designs that can be applied in conditions multiproduct production. Significant contribution to the theory and practice of development and application of rotary and rotary - conveyor systems made Academician Koshkin L., Professor Kloosov I., Preuss V., Preuss V., Kornyukhin I., Frolovich E., Usenko N., Kashirtsev A., Zolotukhin V., Kryukov V., Chelishchev B., Tilipalov V., Grigorovich V., Mikhailov A. and many other researchers.
The analysis of the current state structures automatic rotary lines showed that diversified rotary lines are not widely used because of the difference in the forms of processed products . To improve the technical and economic indicators multiproduct manufacture of products promising application of rotary machines and lines, but their application for multiproduct production is limited due to the lack of principles and methods for the design of complex technological systems multinomenclature this type. Based on their review of the information it can be concluded that effective diversified line for production of fasteners still not been created.
4. Analysis of issues of structural and technological support for rotary machines
One variety of complex automatic lines are rotary automatic lines designed L.N.Koshkinym engineer .
Automatic rotary line - complex working machines , transport equipment , instruments, united by an automatic control system , which together with the workpiece move in arcs together with the impact on them guns. The most common automated rotary lines for operations performed by means of straight labor movement (stamping , drawing , pressing, assembly , control) . [4] Automatic rotary line consists of working rotors that are running manufacturing operations , and transport of rotors that move items from transactions processed (Fig. 1 ).

Figure 1 - Schematic diagram of automatic rotary lines : 1 - tool box ; 2 - transport rotor ; 3 - ticks ; 4 - move the line products in the processing ; 5 - working rotor ; 6 - Copy .
After some debate and a number of design decisions adopted rotary machine , so to speak , its present shape (Fig. 2) . For the transfer of items to the processing tools 3 process units 1 and rotor 9 detachably treated articles 8 have been developed transport rotors 2 and 7. Transport rotors in the simplest form is a disk in which circumferentially arranged gripper bodies resilient in the radial direction. Step between the gripping bodies transport rotors equal to the gap between the working position of the rotor technology . Transport rotors connected cogwheels 4,5 and 6 with the process with the rotor and form a kinematic chain of rigid them . This ensures synchronous rotation of rotors transport and process that enables reliable transmission processing and removal of objects processed products .

Figure 2 - standard rotary machine : a - a longitudinal section of the machine; b - a cross- sectional view ( plan view ); Lp - sector subjects receiving treatment; Lp - processing sector ; Lc - removal of processed product sector ; Lo.i - service sector instrument; h - stepwise distance between the working position .
Transfer processing of vehicle rotor technology is carried out in the sector Lp and eat processed object - in the sector Lc. In the sector of Lp implemented technological processing , and in the Gaza Lo.i. can be made maintenance tools (cleaning , lubricating , replacing , etc. ).
The cycle performance of a rotary machine is determined by the total for all the machines of the third class formula:
where Vtr - transport speed rotary machine , measured on the circle centers tool blocks ( initial circumference of the rotor ) , m / s ; h - step between the working position of the rotor , as measured by the circle centers instrument unit m
required duration of a processing cycle of the subject in a rotary machine can be obtained by choosing the number of working positions and values of the transport speed :
where UP - The number of working positions of the rotor located in the sector of processing Lp.
considering simultaneously the expression ( 1 ) and (2 ), we can make sure that
ie performance rotary machine can be assigned regardless of the duration of the technological cycle of processing by choosing the number of workstations that is a consequence of the basic properties of the third-class cars . This allowed the designers to develop rotary machines with similar performance for different duration and nature of technological operations , selecting the appropriate number of positions technological rotors.
Ensuring autonomy and its automatic tool replacement, automatic control over the processing , maintaining operabilitysion machines etc. - All this requires the introduction of car related devices , which greatly complicates the design of an automatic system of machines .
With the increasing number of objective functions , automatically operated machines , their kinematics is complicated , and a growing number of mechanisms should be placed around the object processing. Increased utilization of the workspace machines actuators and processing tools .
Reducing complexity kinematic machines can be achieved by simplifying , combining , separating or exclude individual functions. Naturally, this should not lead to the loss of the main features and benefits of automatic machines .
Since kinematic characteristics of the objective functions of machines largely determined by the nature of technological operations , the decrease in the kinematic complexity of machines is mainly due to the properties of processes , but is also determined by the properties of technological machines.
Automatic rotary machines and lines to fully satisfy the above conditions of the integrated automation . The question of economic payback automatic machine system is successfully solved by combining rotary machines in automatic rotary line. Since the performance of rotary machines do not directly depend on the duration of the process operation, at the design stage may be selected high enough in accordance with the requirement of economic return on the automated line that is economically feasible.
task of ensuring equal performance rotary machines included in-line , can be easily solved by varying the speed and number of workstations ( instrument unit ) technology rotors. Transferring items between technological processing rotors by transport rotors simple design .
Saving utilization of automatic rotary line when combining it several rotor machines solved by mitigating technological processing modes without compromising cost-effective performance by increasing the number of blocks in the technological tools rotors . Replacement of substandard tool in the process can be carried out without the rotor stop line on the fly by using special rotary changers tool blocks . The best conditions for sound technical solution of the problem of automatic tool change rotary lines are provided with application processes the third and fourth grades , and in some cases , the processing of geometric objects with flat guide , and processes for the second class. Simple rectilinear movement of the machining tools arranged in the autonomous instrument packages , most simply solve the problem of adjusting the rotor outside line on special stands . As a result, the performance loss is minimized and sustainable use of the coefficient of automatic rotary lines consisting of seven - ten rotary machine reaches 0,85 - 0,9.
Kinematic simplicity rotary machines also provide a simple linear motion processing tool using processes of the third and fourth classes .
Application automatic rotary lines compared to individual units is not rotary reduces production cycle 10-15 times , significantly reduced interoperable stocks blanks ( 20-25 times ) , released production area several times reduces the complexity of manufacturing and production costs capital expenditures will pay off in 1-3 years [4].
5. Study design issues multinomenclature rotor systems
transition to automatic machines and the more automatic systems machines is impossible without ensuring the universality of automatic machines , ie their ability to handle diverse forms of objects . Since the general trend of development of modern production is to increase the turnover of production facilities , it is necessary that the automatic system of machinery could be used regardless of the change of processing items .
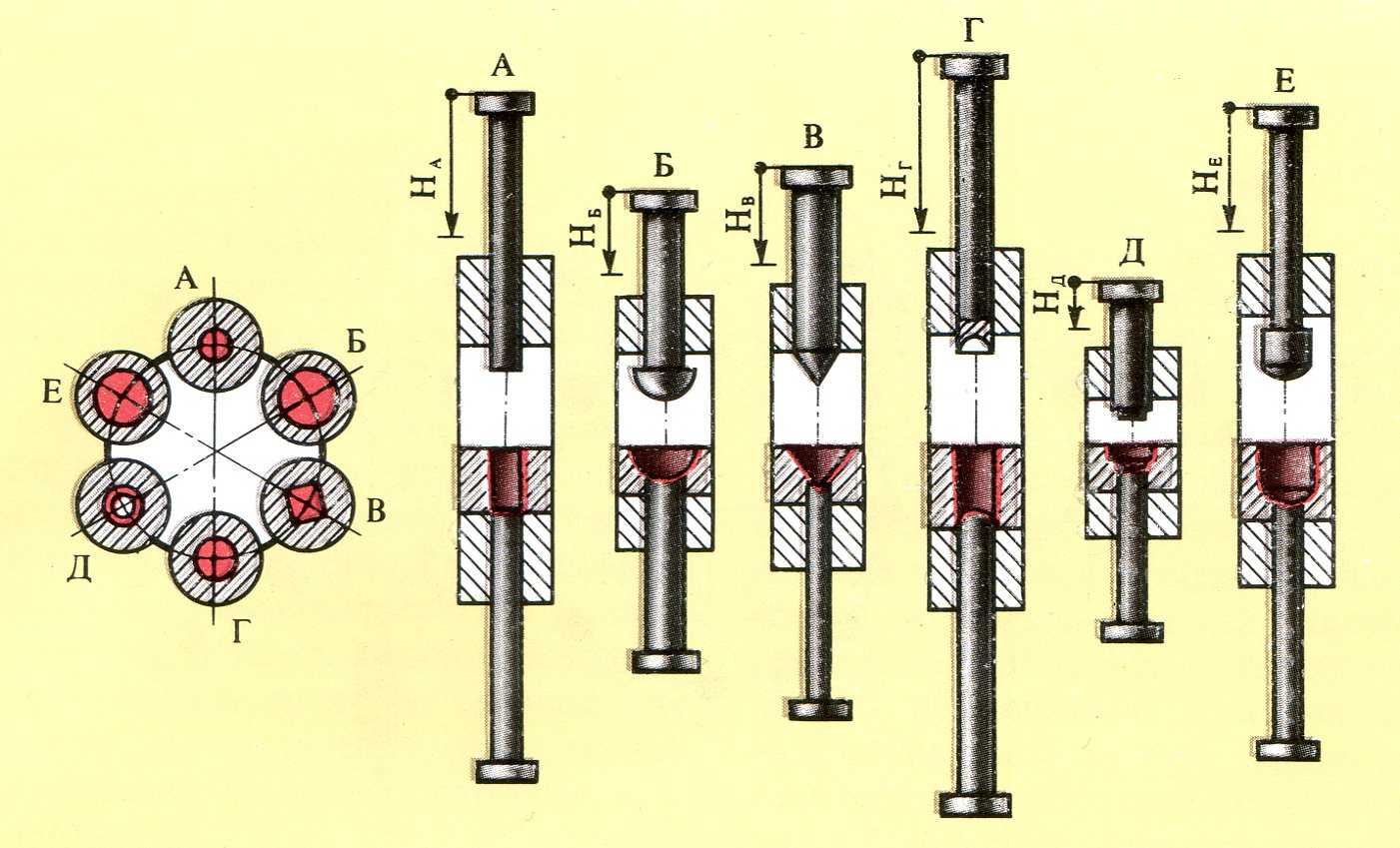
Figure 3 - Schematic tool blocks technological rotors for use on a different nomenclatures .
Versatility rotary machines and lines on the form objects treatment generally achieved using processes of the third and fourth classes , as in this case, the trajectory of the necessary process of the tool does not depend on the shape of workpiece and is straight (Fig. 3) . Technological operations of the third class will be different values ??of working strokes ( Ha , ..., He) and the required technological efforts. Because of this, there is a possibility of processing on the same line several similar items on group technology or treatment similar items on similar lines constituting a certain standard series . It should be emphasized that the great dignity design rotor lines is the ability to use them in a large number of uniform and standardized parts and assemblies. In serial samples rotor lines , such as metal forming , the exponent of unification ( coefficient of applicability ) can reach 60 %.
For most industries using third-class processes , usually characterized by mass of one type of product , in which the required performance production machines is sufficient to ensure the conditions of merchantability machines combined into an automated system . However, in most cases, the production of consumer goods in the production of means of production required the release of products in a variety of different nomenclatures total mass Product Range kakogolibo specific purpose (eg , jewelry, clothing, footwear and furniture accessories , bearings, power sources , resistors, capacitors , electrodes , etc.). In this program of release of products for each of the nomenclature may be insufficient to ensure the conditions of economic payback automatic machine system .
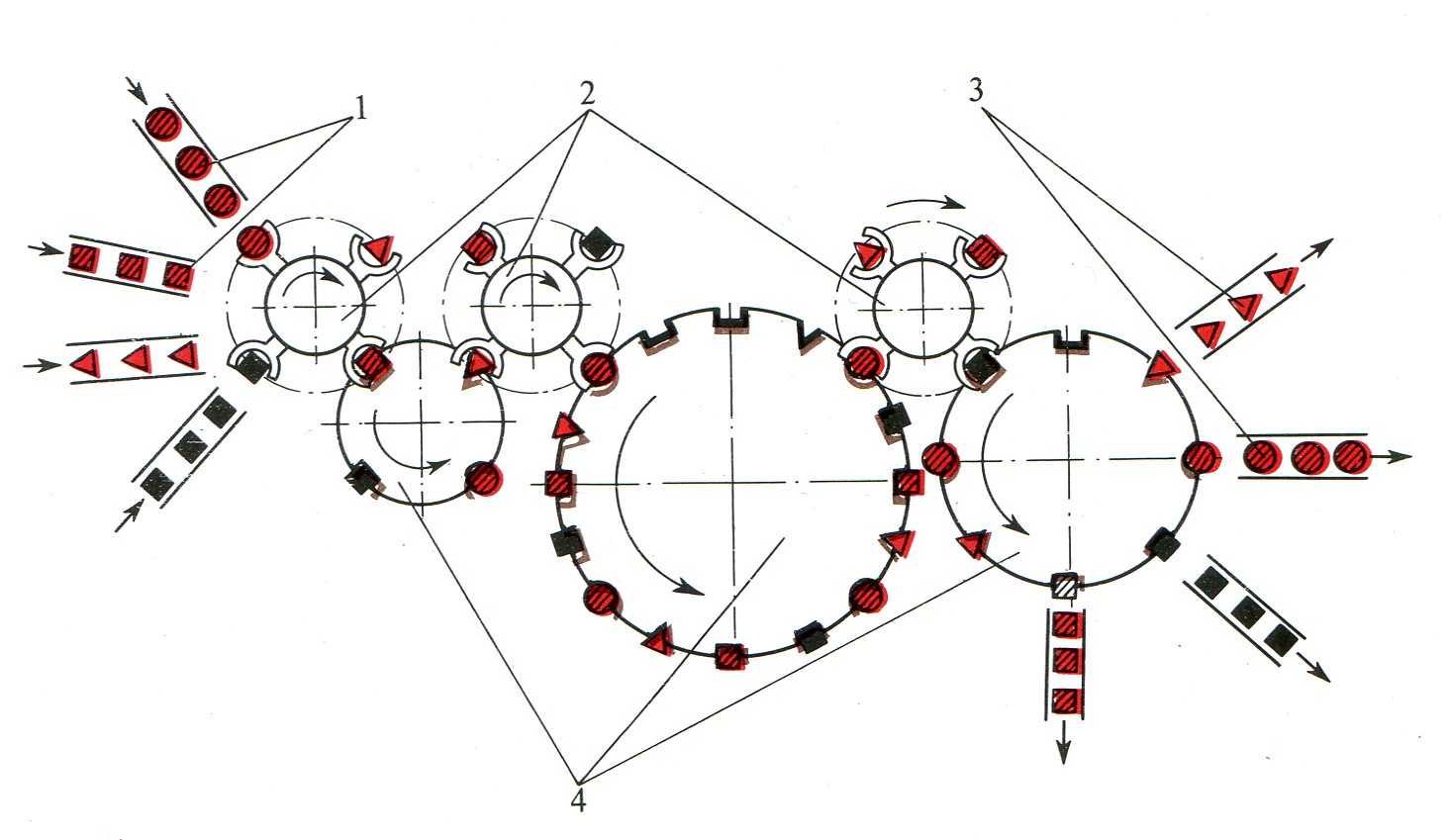
Figure 4 - Diagram of a rotary diversified line : 1 - boot devices ; 2 - transport rotors ; 3 - boxes of finished products; 4 - Process rotors
Addressing insufficient mass objects is achieved by using processing multinomenclature rotary machines and lines (Figure 4) , offering simultaneous production of different product ranges . Using a diversified line of each issue provides a uniform nomenclature of products and eliminates partial changeover from one line to another nomenclature . Naturally, the possibility of creating multinomenclature lines from both a technical and an economic side to the greatest degree is also implemented for the process of the third and fourth classes [ 4 ].
Aim of performing this work there is an increase in production efficiency threaded parts on automatic rotary lines by combining large scale production of the group of products in several sizes in diversified mass , creating the desired structure of the entire system and components for products in several sizes .
Thus , complex automation multiproduct production on the basis of rotor systems - a promising direction for research. As the analysis of the development of rotary systems for the implementation of integrated automation of production rod fasteners necessary to combine in a single thread different in their physical nature , duration, execution and performance processing machines in order to fully use in this process . The main requirements for the implementation of integrated automation software have equal performance process stream inlet and outlet lines of automatic machines , guarantee a simple , requiring minimal cost , transportation processing objects along the process stream , which regulates the flow of processing items in the oriented state .
An integrated production automation rod fasteners on the basis of automatic rotary lines effective due to their special properties : ease of formation of a single transport stream processing objects by applying rotor transport or conveyor device ; the possibility of combining rotary machines performing different operations in a single physical essence automatic line by changing the performance by changing the rotor speed and the number of their positions ; exception instrumental losses and downtime automatic line that reduce utilization , through the use of automatic tool changers without stopping automatic line rotary type ; ease of machining movements, simplify the management of the operation of the automated line .
Diversified rotary lines for the production of rod fasteners requires simplicity and identity forms parts that are processed , as the diversity of needs in a variety of drives and mechanisms of the labor movement and the clamp fixing . This complicates the construction and increases the overall dimensions of the machine , leading to a decrease in production efficiency . Automation of machining many nomenclatures considerably simplified if their processes are identical or similar . A large number of different operations increases the number of rotary machines , which should combine to provide technological actions in full .

Figure 5 - Scheme of work of diversified rotary line (animation: 24 frames, 5 cycles of repetition, 80 kilobytes)
Conclusion
Executed analysis of the design features of rotary machines and lines, their design issues , transmission products multinomenclature stream revealed that , despite the difference in the shapes of machined surfaces of products , combining a group of large-scale production of products in several sizes in diversified mass possibly using gauze. Existing methods for the production line and rod fasteners are imperfect and do not allow the most efficient use of production resources . For mezhrotornoy transmission products of different sizes in the stream should be used multinomenclature Group LP , which will reduce the complexity of constructive transport rotors
References
- Владзиевский, А. П. Автоматические линии в машиностроении/ А.П. Владзиевский , М., 1998
- Накатывание резьбы на деталях машин [электронный ресурс]. – Режим доступа: http://metizi.com...
- Прейс В.В. Технологические роторные машины вчера, сегодня, завтра - М.: Машиностроение, 1986 - 128 с.
- Соломатин, Н.А. Управление производством: Учебник/ под ред. Н.А. Соломатина. – М.: ИНФРА – М, 2001. – 219 с.
- Дейнеко В.Г., Новые способы непрерывного накатывания резьб и других профилей, М., 1961;
- Кошкин Л.Н. Комплексная автоматизация на базе роторных линий/ Л. Н. Кошкин, М.,1999.
- Шаумян Г.А. Комплексная автоматизация производственных процессов. М., "Машиностроение", 1973, 640с.
- Клусов И.А. Производительность автоматических роторных линий / И.А.Клусов // Автоматические роторные линии (исследование, расчет, проектирование) / Машгиз. - М, 1962 г. - Вып. 16. - С.19-31.
- Кошкин Л.Н. Роторные и роторно-конвейерные линии / Л.Н.Кошкин - М.: Машиностроение, 1986. - 320 с.
- Буленков Е.А. Исследование параметров маршрутизации изделий в многономенклатурных роторных системах с помощью многомерной алгебры групп / Е. А.Буленков, А. Н.Михайлов // Прогресивні технології і системи машинобудування: Міжнародний зб. наукових праць / Донец. нац. техн. ун-т. – Донецьк, 2005. - Вип. 29. - С.38–44.
- Буленков Е.А. Выбор рациональной структуры потока изделий для обеспечения загрузки многономенклатурных роторных линий / Е.А.Буленков, А.Н.Михайлов // Прогресивні технології і системи машинобудування: Міжнародний зб. наукових праць / Донец. нац. техн. ун-т. – Донецьк, 2006. - Вип. 31. - С.17 — 24..
- Автоматические роторные линии – от создания к современному этапу промышленного развития [электронный ресурс]. – Режим доступа: http://cyberleninka.ru...
- Технология накатывания резьбы на метизах и деталях машин [электронный ресурс]. – Режим доступа: http://nav-tech.narod.ru...