Реферат по теме выпускной работы
Содержание
- Введение
- 1. Актуальность темы магистерской работы
- 2. Цель и задачи исследования
- 3. Результаты литературного обзора и патентного поиска
- 3.1 Результаты литературного обзора
- 3.2 Результаты патентного поиска
- 4. Известные конструктивные схемы зарубежных разработчиков и выбор конструктивного решения
- 5. Разработка и изготовление физической модели желоба и выдача рекомендаций при проведении исследований
- Выводы
- Список источников
Введение
На сегодняшний день выплавка стали в дуговых электросталеплавильных печах из-за высокой конкуренции различных предприятий и стран получает все новые методы усовершенствования. Эти методы снижают затраты на производство стали посредством уменьшения времени плавки, использования различной шихты.
Одним из таких методов является заливка жидкого чугуна в ванну дуговой печи. Заливка чугуна может осуществляться сверху через отведенную крышку ДСП либо через специальное заливочное окно в корпусе печи. Заливка жидкого чугуна через окно печи осуществляется через специальный желоб, по которому чугун попадает в ванну дуговой печи, тем самым уменьшая время на загрузку шихты и уменьшая скорость размывания футеровки ДСП.
1. Актуальность темы магистерской работы
Применение в завалку электропечи жидкого чугуна производится посредством исследуемого желоба. Заливка жидкого чугуна в электропечь энергетически выгодно из-за выделения дополнительной химической энергии, но и ввода в ванну физического тепла. Температура жидкого чугуна перед заливкой в печь составляет 1150–1350?С, при этом его теплосодержание достигает 223–272 кВт*ч/т, что обеспечивает при замене 1% лома жидким чугуном около 2,23–2,72 кВт*ч/т дополнительной энергии. Химические реакции окисления кремния и марганца при содержании 1% жидкого чугуна в шихте дополнительно вносят около 1,40 кВт*ч/т. Содержание углерода в чугуне обеспечивает поступление тепла от его окисления в количестве 0,5 кВт*ч/кг. Кроме того, следует учитывать энергию растворения углерода, которая составляет около 0,6 кВт*ч/кг. Поэтому суммарный вклад 1% жидкого чугуна в тепловой баланс плавки составляет примерно 4,3 кВт*ч/т.
Однако, по некоторым данным, несмотря на снижение расхода энергии и сокращение продолжительности плавки, при работе на жидком чугуне, себестоимость готовой стали возрастает примерно в 1,3–1,5 раза. Стоит отметить, что в условиях дефицита стального лома и наличия избыточного количества передельного чугуна на металлургическом комбинате такой технологический вариант может быть экономически целесообразен даже для производства стали массового сортамента. Вместе с тем, существует оптимальное с точки зрения себестоимости готового полупродукта соотношение чугун-лом. Существуют расчетные данные, по которым для определенных конкретных условий производства (масса плавки 165 т) экономически оптимальное количество жидкого чугуна в шихте составляет окло 30%[1].
2. Цель и задачи исследования, планируемые результаты
Целью настоящего исследования является разработка и обоснование рациональных параметров передвижного желоба для заливки чугуна в дуговую электропечь
Для достижения поставленной цели необходимо решить следующие задачи:
- На основе сопоставительного анализа существующих технических решений разработать усовершенствованный желоб для заливки чугуна.
- Разработать методику расчета кинематических и энергосиловых параметров желоба.
- Провести проверку правильности принятых технических решений и полученных расчетных зависимостей на физическом аналоге желоба.
- Выдать рекомендации для промышленного использования предложенной разработки.
- Выполнить оценку технико-экономической эффективности разработанных технических решений.
3. Результаты литературного обзора и патентного поиска
3.1 Результаты литературного обзора
Общемировой тоннаж стали, производимой в ДСП, только за последние 12 лет возрос в 1,5 раза. Сегодня в мире, по разным оценкам, функционирует около 1200–1350 ДСП различной вместимости. На данный момент 11 стран выпускает более 10 млн.т электростали в год каждая, а на совокупную долю этих государств приходится почти 70% всего выплавляемого продукта. Однако, в отличие от ситуации, сложившейся в конвертерном производстве, в секторе электростали отсутствует доминирование одной страны, практически полностью определяющей прирост объемов производства. Здесь в группу ведущих мировых металлургических стран, кроме «традиционных» США, Японии, Италии и Германии, вошли также Индия, Турция, Испания и Мексика. Современные темпы прироста выплавки стали в ДСП следует рассматривать как свидетельство высокой конкурентоспособности электросталеплавильного производства, что обусловлено научно-техническим прогрессом в части стратегии функционирования и форматов построения соответствующих производств. За последние три десятилетия длительность плавки в ДСП сократилась со 180 мин до 40–45 мин при уменьшении удельных затрат электроэнергии с 630 кВт•час до 340–350 кВт•час на тонну выплавляемой стали. Часовая производительность печи становится основной ее характеристикой и для печей вместимостью 100–200 т и достигает 180–200 т/ч, а мощность печного трансформатора иногда превышает 1 МВА/т. Развитию процесса выплавки стали в ДСП в значительной мере поспособствовала концепция металлургического минизавода, получившая быстрое распространение с середины 1980-х годов. Совершенствование и трансформация агрегатов, входящих в состав такого сталелитейного модуля, привели к изменению технологических функций дуговой сталеплавильной печи [2].
В связи с тем, что основным способом выплавки стали является кислородно-конвертерный, потребляющий меньшее количество лома по сравнению с мартеновским, возникли предпосылки для более быстрого развития электросталеплавильного производства, работающего на твердой шихте. Вторая важная причина развития выплавки стали в электропечах —все возрастающая потребность в легированных сталях и чистом металле из металлизованных окатышей. Развитие электросталеплавильного способа производства стали будет идти параллельно с кислородно-конвертерным. На металлургических предприятиях с большим объемом производства низколегированной и трансформаторной сталей в основном применяют дуговые трехфазные электропечи вместимостью 50, 100 и 200 т. На специализированных заводах по производству высококачественной и специальной сталей применяют дуговые электропечи вместимостью 3–100 т, индукционные электропечи обычных конструкций и вакуумные.
Высококачественные слитки (по структуре и поверхности) получают в вакуумных электропечах с расходуемым электродом и в печах электрошлакового переплава. В последнее время для получения сталей для атомной и ракетной техники применяют электронно-лучевые плазменные печи. Ферросплавы выплавляют в дуговых электропечах на специализированных заводах.
Выплавка стали в дуговых электропечах основана на том, что электрическая энергия превращается в тепловую вследствие электрического разряда, протекающего в газовой среде или в вакууме. В электрическом разряде сосредоточиваются высокая концентрация энергии и огромные мощности в небольших объемах металла, в результате чего получаются высокие температуры и быстрое расплавление металла.
В настоящее время часть твердого лома заменяют на жидкий чугун. Заливка жидкого чугуна осуществляется при помощи съемного или стационарного желоба. Продолжительность заливки чугуна определяется организационными возможностями и обычно составляет 15–30 мин. Чугун необходимо заливать медленно, иначе возможны бурное окисление углерода чугуна и выбросы металла и шлака из печи. Плавление как самостоятельный период плавки начинается после заливки жидкого чугуна. Основной задачей этого периода являются расплавление металла и нагрев его выше температуры плавления (линии ликвидус) на 40–60°С, а также предварительное рафинирование металла[3].
3.2 Результаты патентного поиска
В результате патентного поиска были найдены патенты, которые имеют отношение к разработке прогрессивных способов выплавки стали в дуговых печах.
Патент RU 2302471 C1
Изобретение относится к черной металлургии, в частности к способам получения стали в дуговых электросталеплавильных печах. Способ включает подачу в печь металлолома и жидкого чугуна, расплавление, окислительный период, выпуск плавки с оставлением шлака и части металла в печи. Перед выпуском в печь присаживают известь в количестве 1–5% от массы завалки. Заливку чугуна при температуре 1250–1360°С в количестве 40–70% от массы завалки проводят на оставшийся в печи шлак и часть металла. После заливки чугуна проводят завалку извести в количестве 1–3% и металлолома в количестве 30–60% от массы завалки. Окисление проводят кислородом с расходом 8000–12000 м3/ч до содержания углерода не менее 0,10%. В ковш при выпуске присаживают кремний и марганецсодержащие ферросплавы из расчета введения кремния 0,10–0,25% и марганца 0,40–0,50% и известь из расчета 3–20 кг/т жидкой стали. Дальнейшую доводку стали по температуре и химическому составу проводят на агрегате ковш-печь. Изобретение позволяет повысить качество стали, сократить длительность плавки.
Заливка жидкого чугуна (40–70 тонн) проводилась из чугуновозного ковша посредством мостового крана при открытом своде печи на остаток печного шлака и металла. Далее загружали 1000–3000 кг извести и бадьей осуществляли завалку 30–60 тонн металлолома. Работа проводилась без последующих подвалок металлолома в печь. Окисление углерода проводили продувкой стали в печи газообразным кислородом через систему газокислородных горелок с расходом 8000–12000 м3/т. Во время окисления углерода температура в печи не превышала 1700°С, причем температура заливаемого чугуна изменялась в пределах 1250–1360°С. При достижении требуемого содержания углерода, фосфора и температуры проводили выпуск плавки с отсечкой печного шлака. Перед выпуском плавки в печь сверху по труботечкам загружалась известь в количестве 1000–5000 кг, после чего производили выпуск с оставлением в печи всего шлака и 10–15 тонн металла. При выплавке стали по заявляемому способу сокращается длительность плавки с 70–80 мин до 59–68 мин, электроэнергии с 300–420 кВт•ч/т до 290–320 кВт•ч/т, электродов с 3,50–3,60 кг/т до 2,00–2,90 кг/т, уменьшено содержание хрома и никеля до 0,03%, меди до 0,04%, загрязненность стали неметаллическими включениями (средний бал загрязненности не превышает 0,7)[4].
Патент RU 2258084 C1
Изобретение относится к черной металлургии, в частности к способам выплавки стали в дуговых электросталеплавильных печах. Способ выплавки стали включает завалку металлолома и извести. После проплавления металлолома при расходе электроэнергии 180–300 кВт•ч/т металлолома заливают сверху жидкий чугун при температуре 1280–1400°С в количестве 30–60% от массы завалки, содержащий, мас.%: (2,0–3,5) С, менее 0,01 Si, менее 0,015 Р, менее 0,025 S. Окисляют углерод газообразным кислородом при температуре в печи не более 1700 °С. При выпуске стали отсекают печной шлак и оставляют 10–15% от общей массы жидкого металла в печи. Подают в ковш во время выпуска шлакообразующую смесь, состоящую из извести и плавикового шпата в соотношении (0,8–1,2):(0,2–0,5) с расходом 10–17 кг/т стали, и присаживают ферросплавы. Способ позволяет снизить расход электроэнергии и электродов при выплавке стали, сократить длительность плавки, повысить качество стали, уменьшить расход раскислителей и легирующих.
Для этого предложен способ выплавки стали в дуговой электропечи, включающий завалку металлолома и извести, расплавление металлолома, заливку жидкого чугуна, окисление углерода газообразным кислородом, дефосфорацию, последующий выпуск стали в ковш и присадку в ковш во время выпуска шлакообразующей смеси, состоящей из извести и плавикового шпата, причем заливают жидкий чугун в количестве 30–60% от массы завалки, при содержании в нем, мас.%: углерода 2,0–3,5, менее 0,01 кремния, менее 0,015 фосфора, менее 0,025 серы, причем чугун заливают при температуре 1280–1400°С сверху в печь после проплавления металлолома при расходе электроэнергии 180–300 кВт•ч/т металлолома, температуру в печи при окислении углерода поддерживают не более 1700°С, выпуск стали в ковш проводят с отсечкой печного шлака с оставлением 10–15% от общей массы жидкого металла в печи, подают в ковш во время выпуска стали шлакообразующую смесь при соотношении в ней извести и плавикового шпата (0,8–1,2): (0,2–0,5) с расходом 10–17 кг/т стали и присаживают ферросплавы[5].
Патент RU 2197535 C2
Изобретение относится к способам получения стали в дуговых электросталеплавильных печах. Способ включает завалку в печь металлолома, заливку жидкого чугуна, расплавление металлошихты, дефосфорацию стали путем присадок порций железной руды или агломерата в смеси с известью, раскисление стали и шлака в печи, выпуск стали в ковш под печным шлаком, присадку в ковш десульфурирующей смеси, состоящей из извести, плавикового шпата и порошка алюминия. В состав завалки вводят агломерат или железную руду в количестве 30–60 кг/т стали. После проплавления металлошихты при расходе электроэнергии 220–320 кВтч/т металлолома в печь заливают жидкий чугун при температуре не ниже 1200oС со скоростью заливки 6–12 т/мин, проводят окисление газообразным кислородом с расходом 1500–3000 нм3/ч. Соотношение присаживаемых железной руды или агломерата в смеси с известью поддерживают соответственно (1–2): (2,5–3,5) при их расходе 70–110 кг/т стали. После чего спускают шлак через порог рабочего окна. Соотношение извести, плавикового шпата и порошка алюминия в вводимой в ковш десульфурирующей смеси поддерживают соответственно (1,1–1,5): (0,3–0,5):(0,05–0,1) при расходе смеси 14–18 кг/т стали. Способ позволяет снизить расход электроэнергии и электродов при выплавке стали, сократить длительность плавки, повысить качество стали.
Известны также способы заливки жидкого чугуна через желоб фирмы Пауль Вюрт
, а также в печь сверху. Однако в первом случае требуется дорогостоящее переоборудование печи, причем узким
местом при заливке чугуна является желоб (как стационарный, так и съемный) вследствие закозления
остатками шлака и чугуна при заливке. При этом заливка чугуна должна осуществляться с определенной повышенной температурой, т.к. незначительное падение температуры может вызвать замерзание заливаемого в печь чугуна в заливочном желобе и выходе последнего из строя со всеми аварийными последствиями. Заливка чугуна через желоб связана также с размывом футеровки желоба и загрязнением стали неметаллическими включениями экзогенного характера. Кроме того, значительны затраты на содержание желоба в рабочем состоянии.
Заливка чугуна через свод может быть организована при значительно более низкой температуре, однако при температуре чугуна менее 1200oС возможно спелеобразование, в результате которого мельчайшие частицы графита, оседая на короткой сети дуговой электросталеплавильной печи, могут вызвать короткое замыкание. Неотработанная технология заливки чугуна в печь сверху может вызвать выбросы чугуна, шлака и стали из печи, переливы, повышенный износ футеровки, незначительную степень дефосфорации и десульфурации.
Желаемыми техническими результатами изобретения являются: снижение расхода электродов при выплавке стали, сокращение длительности плавки, повышение качества стали.
Для этого в состав завалки вводят агломерат или железную руду в количестве 30–60 кг/т стали, после проплавления металлошихты при расходе электроэнергии 220–320 кВтч/т металлолома в печь заливают жидкий чугун при температуре не ниже 1200oС со скоростью заливки 6–12 т/мин, проводят окисление газообразным кислородом с расходом 1500–3000 нм3/ч, соотношение присаживаемых железной руды или агломерата в смеси с известью поддерживают соответственно (1–2): (2,5–3,5) при их расходе 70–110 кг/т стали, после чего спускают шлак через порог рабочего окна, а соотношение извести, плавикового шпата и порошка алюминия в вводимой в ковш десульфурирующей смеси поддерживают соответственно (1,1–1,5):(0,3–0,5):(0,05–0,1) при расходе смеси 14–18 кг/т стали[6].
4. Известные конструктивные схемы зарубежных разработчиков и выбор конструктивного решения
На рисунках 1 и 2 показаны конструкции желоба немецких фирм RHI и SIEMENS VAI. Желоб для заливки жидкого чугуна конструкции RHI помещается на передвижную тележку посредством мостового крана, а желоб SIEMENS VAI закреплен на передвижной тележке и не требует кантовки, что является преимуществом по сравнению с желобом RHI.
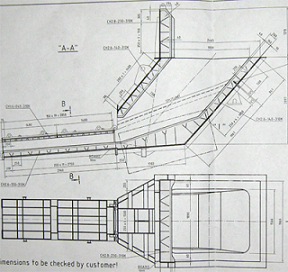
Рисунок 1 – Желоб для заливки жидкого чугуна конструкции RHI
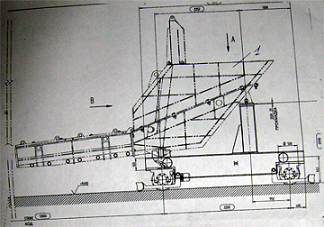
Рисунок 2 – Желоб для заливки жидкого чугуна конструкции SIEMENS VAI
Также существует конструкция желоба для заливки чугуна конструкции НКМЗ.
Желоб для заливки жидкого чугуна конструкции RHI помещается на передвижную тележку посредством мостового крана, а желоб SIEMENS VAI и НКМЗ закреплен на передвижной тележке и не требует кантовки, что является преимуществом по сравнению с желобом RHI.
5. Разработка и изготовление физической модели желоба и выдача рекомендаций при проведении исследований
При разработке физической модели за основу была взята конструкция желоба для заливки чугуна фирмы SIEMENS VAI. На данный момент сконструирована модель передвижного желоба (рис. 3.). На тележке закреплен привод, состоящий из электродвигателя и вручную собранного пятиступенчатого редуктора.
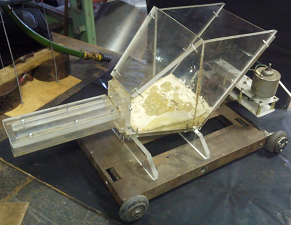
Рисунок 3 – Физическая модель передвижного желоба
При разработке модели желоба был выбран масштаб 1:10. Выбирая масштаб модели, следует также учитывать значительное влияние сил поверхностного натяжения жидкости на протекание процесса в модели агрегата при слишком малых сечениях ее каналов и отверстий. Диаметр отверстий на модели при использовании различных моделирующих жидкостей должен быть следующий: для воды – не менее 12 мм, глицерина – 10, керосина и масла – не менее 8 мм. Поскольку жидкую сталь при проведении опыта заменит вода, то диаметр выпускного отверстие желоба при выбранном масштабе соответствует условию более 12 мм.
Материалом для изготовления модели послужит органическое стекло, обладающее прозрачностью и легко поддающееся различным видам механической обработки, что позволяет точно скопировать практически любую конфигурацию контуров натурного образца исследуемого агрегата и проводить визуальные наблюдения за протекающими в модели гидрогазодинамическими процессами.
Для проведения исследований процесса протекания жидкого чугуна в желобе необходимо будет провести визуализацию жидкостного потока. Визуализация – это создание условий, способствующих появлению контрастной картины траекторий движения потоков моделирующей жидкости за счет введения в нее красящих жидких веществ или мелкодисперсных твердых частиц, имеющих высокий коэффициент отражения. Капли цветной жидкости или же частицы, уносимые оптически прозрачными потоками, в точности воспроизводят их движение и при надлежащей освещенности позволяют получить четкую картину распределения потоков в рабочем объеме моделируемого агрегата.
Визуализация течений считается важным фактором в исследовательской работе и, в первую очередь, в физическом моделировании гидродинамических процессов, так как не только позволяет сделать определенные выводы относительно качественной стороны изучаемых явлений, но и относится к одному из необходимых условий реализации оптического метода контроля времени перемешивания жидкости и фотометода измерения скорости жидкостных потоков. Для фиксирования результатов исследования будет проведена фотосъемка. В сложных условиях специальных видов фотосъемки гидродинамических процессов часто требуется разработка специальных приспособлений, позволяющих реализовать поставленную задачу в каждом конкретном случае с наибольшей эффективностью[7].
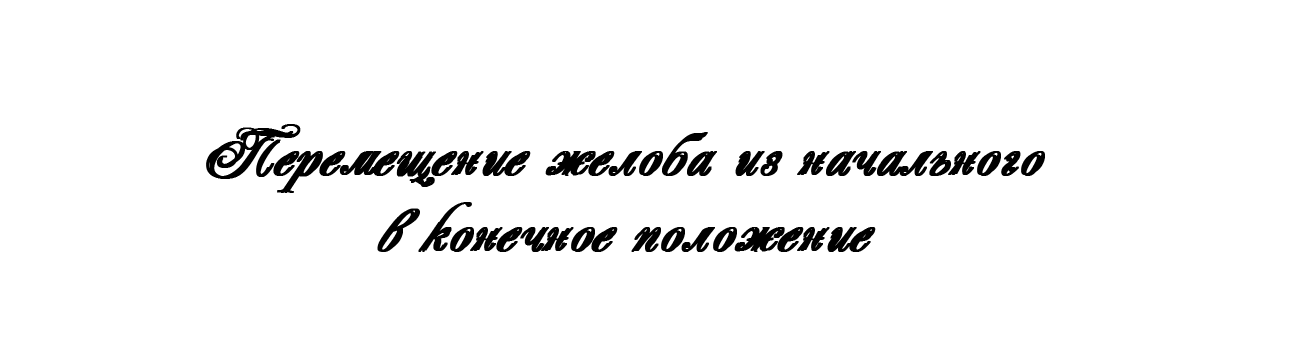
Рисунок 4 – Перемещение желоба из начального в конечное положение
(анимация: 8 кадров, 6 циклов повторения, 165 килобайт)
Выводы
Таким образом, разработки, направленные на усовершенствование плавки металла в электропечах являются перспективными за счет снижения затрат на твердый металлический лом, энергоресурсы и снижение себестоимости металла посредством заливки в печь жидкого чугуна.
Предлагаемый вариант желоба является более универсальным за счет конструктивных особенностей и устранением проблем с размытие футеровки жидким чугуном. Исследования позволяют увеличить срок службы желоба до проведения очередного ремонта.
При написании данного реферата магистерская работа еще не завершена. Окончательное завершение: декабрь 2014 года. Полный текст работы и материалы по теме могут быть получены у автора или его руководителя после указанной даты.
Список источников
- Информационный портал
Steel times
– Жидкий чугун для плавки стали в современной дуговой печи (ДСП). Режим доступа: http://steeltimes.ru/books/steelmaking/minizavod/244/244.php - Электрометаллургический прогресс/ Кукин С.В./ Металл &ndash 2007. – № 5. – С. 15.
- Информационный портал
Specural Com
– Заливка жидкого чугуна в мартеновскую печь и плавление. Режим доступа: http://specural.com/articles/category/5/message/63/ - Патент RU 2302471 C1 Россия, C21C5/52, C21C7/06. Способ выплавки стали в дуговой электропечи / Ю.Д. Девяткин, Е.П. Кузнецов, Н.А. Козырев и др.; ОАО
Новокузнецкий металлургический комбинат
. №2006114524/02; заявлено 27.04.2006; опубл. 10.07.2007. Режим доступа: http://bd.patent.su/2302000-2302999/pat/servl/servlet65cc.html - Патент RU 2258084 C1 Россия, C21C5/52, C21C7/06. Способ выплавки стали в дуговой электропечи / Л.А. Годик, А.И. Катунин, Н.А. Козырев и др.; ОАО
Новокузнецкий металлургический комбинат
. №2003136330/02; заявлено 15.12.2003; опубл. 10.08.2005. Режим доступа: http://bd.patent.su/2258000-2258999/pat/servl/servletab79.html - Патент RU 2197535 C2 Россия, C21C5/52, C21C7/06. Способ получения стали в дуговой электросталеплавильной печи /А.И. Катунин, Л.А. Годик, Н.А. Козырев и др.; ОАО
Кузнецкий металлургический комбинат
. №2000107730/02; заявлено 29.03.2000; опубл. 27.01.2003. Режим доступа: http://bd.patent.su/2197000-2197999/pat/servl/servlet9794.html - Еронько С.П., Быковских С,В. Физическое моделирование процессов внепечной обработки и розливки стали. – К.: Техника, 1998. – 136 с.