Abstract
Content
- Introduction
- 1. Theme urgency of master's work
- 2. Goal and tasks of the research
- 3. The results of the literature review and patent search
- 3.1 The results of the literature review
- 3.2 Patent search results
- 4. Notable design schemes and foreign developers choice constructive solutions
- 5. Development and production of a physical model of the trough and issuing recommendations for research
- Conclusion
- References
Introduction
To date, the output of steel in electric arc furnaces because of the high competition between different companies and countries are getting new methods of improvement. These methods reduce the production cost of steel by reducing melting time, the use of different charge.
One such method is to pour molten iron bath arc furnace. Pouring iron may be assigned to cover the top through chipboard or through a special injection port in the furnace body. Pouring molten iron through the window furnace through a special spout through which iron falls into a bath of the arc furnace, thereby reducing the time to download the charge and reducing the rate of erosion of the lining chipboard.
1. Theme urgency of master's work
Application in electric filling molten iron produced by the test chute. Pouring molten iron into an electric energetically favorable due to the release of additional chemical energy, but also the physical input into a bath of heat. Temperature before pouring molten iron into a furnace of 1150–1350°С while its heat content reaches 223–272 kW / tn, which provides for the replacement of 1% liquid iron scrap about 2,23–2,72 kW / tn additional energy. Chemical oxidation of silicon and manganese at a concentration of 1% in the molten iron charge additionally introduced around 1.40 kW / m The carbon content of the iron provides a flow of heat from its oxidation within a quantity of 0.5 kW / kg. Moreover, one should consider the energy dissolution carbon which is around 0.6 kW / kg. Therefore, the total contribution of 1% of liquid iron in the heat balance of melting is about 4.3 kW / tn
However, according to some, despite the reduction of energy consumption and reducing the duration of melting, when working with hot metal, the cost of finished steel increased by about 1.3–1.5 times. It is noteworthy that the shortage of scrap steel and the presence of an excess amount of pig iron at the metallurgical plant such technology option can be economically advisable even for the mass production of steel product mix. However, there is an optimum in terms of cost of finished intermediate iron-scrap ratio. There are estimates, which for certain specific conditions of production (mass melting 165 tons) cost-optimal amount of liquid pig iron in the charge is about 30%[1].
2. Goal and tasks of the research
The purpose of this research is the development and justification of rational parameters of mobile trough for casting iron in electric arc furnace
To achieve this goal it is necessary to solve the following problems:
- On the basis of a comparative analysis of existing solutions to provide an improved chute for casting iron.
- Develop methodology for calculating the kinematic and power parameters of the gutter.
- Conduct validation of engineering solutions and the calculated dependences of the physical analog of the gutter.
- Issue recommendations for industrial use of the proposed development.
- Evaluate the technical and economic efficiency of the developed solutions.
3. The results of the literature review and patent search
3.1 The results of the literature review
Global tonnage of steel produced in the EAF, the last 12 years increased by 1.5 times. In the world today, according to various estimates, There are about 1200–1350 chipboard different capacity. Currently 11 countries produces more than 10 million tonnes per year of electric each and an aggregate share these states account for nearly 70% of all smelted product. However, unlike the situation in BOF production in the sector of electric no domination of one country, almost entirely by production growth. Here the group of the world's leading metallurgical countries other than "traditional" U.S., Japan, Italy and Germany, also includes India, Turkey, Spain and Mexico. The current pace of growth in EAF steelmaking should regarded as evidence of the high competitiveness of electric steel production, due to scientific and technical progress in terms of strategy operation and construction of the corresponding production formats. Over the past three decades in EAF melting duration reduced from 180 minutes to 40–45 minutes at reducing the unit cost of electricity with 630 kW • h to 340–350 kW • h per tonne of steel produced. Hourly productivity of the furnace becomes a major its characteristic and for furnaces vmestimostyu100–200 m and reaches 180–200 tn / h, and the power of the furnace transformer sometimes exceeds 1 MVA / tn Development process in EAF steelmaking largely contributed to the concept of mini-plant metallurgical posses with the rapid spread of the mid-1980s. Improvement and transformation units that are part of such a steel module, led to a change in the technological functions EAF [2].
Due to the fact that the main method of steelmaking is the basic oxygen consuming fewer than scrap with open hearth, any prerequisites for the more rapid development of electric steel production, working on a solid charge. The second important reason for the development smelting of steel in electric-increasing demand for steel alloys and pure metal of metallized pellets. development of arc method of steel production will run parallel with the BOF. Metallurgical enterprises with high volume production of low-alloy steels and transformer mainly use three-phase arc electric capacity of 50, 100 and 200 tons at a specialized factory for the production of high-quality and special steels used electric arc furnaces capacity of 3–100 m, induction furnaces and vacuum conventional designs.
High quality bars (structure and surface) was prepared in vacuum electric furnace with a consumable electrode in electro-slag remelting furnace. Recently, for steels for nuclear and missile technology used electron-beam plasma furnace. Ferroalloys melted in electric arc furnaces at specialized plants.
Smelting of steel in electric arc furnace based on the fact that the electrical energy is converted into heat due to electrical discharge, flowing a gaseous medium or in vacuum. In an electric discharge concentrated high concentration of energy and huge power in small amounts of metal in thereby producing a high temperature and rapid melting of the metal.
Currently part of the solid scrap replaced by molten iron. Pouring molten iron is carried out using a stationary or removable trough. Duration of casting iron defined organizational capabilities and is usually 15–30 minutes. Cast iron must be filled slowly, otherwise there may be rapid oxidation of iron and carbon emissions of metal and slag from the furnace. Melting as a separate melting period begins after pouring molten iron. The main task of this period are heated to melt the metal and its higher melting temperature (liquidus line) at 40–60°C, and pre-refining metal[3].
3.2 The results of the patent search
As a result, patent search were found patents that are relevant to the development of advanced methods of steel production in electric arc furnaces.
Patent RU 2302471 C1
The invention relates to ferrous metallurgy, in particular to methods of producing steel in electric arc furnaces. The method comprises feeding the metal scrap into the furnace and molten iron meltdown oxidation period, leaving the tapping of slag and metal parts in the furnace. Before release into the furnace sits down lime in an amount of 1–5% by weight of the filling. Pouring cast iron at a temperature of 1250–1360°C in an amount of 40–70% by weight of the filling is carried out by remaining in the furnace slag and the metal part. After casting iron spend lime filling in an amount of 1–3% and scrap metal in an amount of 30–60% by weight of the filling. Oxidation is carried out with oxygen at a rate of 8,000–12,000 m3 / h until the carbon content of not less than 0.10%. In bucket sits down with the release of silicon and manganese ferroalloys introduction rate of silicon and manganese, 0.10–0.25% and 0.40–0.50% of lime based 3–20 kg / t molten steel. Further fine-tuning of steel temperature and chemical composition of conduct to ladle furnace. The invention improves the quality of the steel, reduce the duration of the heat.
Pouring molten iron (40–70 tons) carried out by ladle overhead crane at the open roof of the furnace for the remainder of furnace slag and metal. Next loaded 1000–3000 kg of lime and tub filling carried 30–60 tons of scrap metal. Work was carried out without further podvalok scrap into the furnace. Oxidation of carbon steel was carried out in a furnace blowing oxygen gas through the system at a rate of gas-oxygen burners 8000–12000 m3 / t During oxidation of carbon furnace temperature should not exceed 1700 ° C, the temperature of the filling iron varied within 1250–1360°C. When reaching the desired content of carbon, phosphorus, and temperature performed tapping cutoff furnace slag. Before releasing the melting furnace top trubotechkam loaded by lime in an amount of 1000–5000 kg, after which produced issue with leaving the furnace slag and just 10–15 tons of metal. For steelmaking by the proposed method reduces the duration of melting with 70–80 minutes to 59–68 minutes, with power 300–420 kW • h / tn to 290–320 kW • h / tn, electrodes 3.50–3.60 kg / tn up to 2,00–2,90 kg / t reduced content of chromium and nickel, up to 0.03% to 0.04% copper, steel contamination by nonmetallic inclusions (average score of contamination does not exceed 0.7)[4].
Patent RU 2258084 C1
The invention relates to the steel industry, in particular to methods of steelmaking in electric arc furnaces. The method includes filling steelmaking scrap and lime. After penetration of scrap metal at a rate of 180–300 kW • h / tn of scrap metal is poured on top the molten iron at a temperature of 1280–1400 ° C in an amount of 30–60% by weight of the filling, containing, wt.% (2.0–3.5) C, less than 0,01 Si, P less than 0.015, less than 0,025 S. oxidized carbon gaseous oxygen in a furnace at a temperature not exceeding 1700 ° C. When issuing dissected furnace steel slag, and allowed 10–15% of the total weight of the molten metal in the furnace. Fed into the ladle during tapping slagging mixture of lime and fluorspar in the ratio (0.8–1.2): (0.2–0.5) with a flow rate of 10–17 kg / t of steel and a seat ferroalloys. The method reduces power consumption and electrodes for steelmaking, shorten the duration of melting, improve steel quality, reduce deoxidizer and alloy fuel.
For this is provided a method of steelmaking in the electric arc furnace, comprising filling scrap and lime melting scrap pouring molten iron, carbon oxidation by oxygen gas, dephosphorization, the subsequent release of steel in the ladle and the additive into the ladle during tapping slag-forming mixture, consisting of lime and fluorspar, wherein the molten iron is poured in an amount of 30–60% by weight of the filling, if they contain it, wt.%: carbon 2.0–3.5, silicon less than 0.01, phosphorus less than 0.015, sulfur less than 0.025, wherein the iron is poured at a temperature of 1280–1400 ° C in a furnace top after penetration of the scrap at a rate of 180–300 kW • h / tn scrap, the temperature in the furnace during the oxidation of the carbon support is not more than 1700 ° C, production of steel in the ladle was carried out with a cut-off-furnace slag leaving 10–15% of the total weight liquid metal in the furnace is fed into the ladle during tapping steel slagging mixture therein at a ratio of lime and fluorspar (0.8–1.2): (0.2–0.5) at a flow rate of 10–17 kg / tn steel and ferro-alloys have a seat[5].
Patent RU 2197535 C2
The invention relates to methods of producing steel in electric arc furnaces. The method includes filling in the oven metal, pouring liquid iron melt of metal, by means of additives dephosphorization steel portion of iron ore agglomerate or mixed with lime, deoxidation of steel and slag in the furnace, ladle steel production under the furnace slag in the ladle desulfurization additive mixture of lime, fluorspar and aluminum powder. The composition is administered filling sinter or iron ore an amount of 30–60 kg / tn steel. After penetration of metal at a rate of electricity 220–320 kWh / t of scrap into the furnace molten iron is poured at a temperature of not lower than 1200 ° C. pouring at a speed of 6–12 m / min, is oxidized with oxygen gas at a rate of 1500–3000 Nm3 / h Sit down ratio of iron ore sinter or mixed with lime supported respectively (1–2): (2.5–3.5) at a flow rate of 70–110 kg / tn of steel. Then lowered the threshold slag working window. The ratio of lime and fluorspar aluminum powder introduced into the ladle desulfurization mixture is maintained respectively (1.1–1.5): (0.3–0.5): (0.05–0.1) mixture at a flow rate 14–18 kg / tn steel . The method allows reduce power consumption and electrodes for steelmaking, shorten the duration of melting, improve the quality of steel.
Methods are also known pouring molten iron through the chute by Paul Vyurt
, and also in the furnace top. However, in the former case requires a costly
refitting the oven, the narrow
place when pouring spout is iron (both fixed and removable), due to porpoise
remnants of slag and pig iron casting.
When this fill should be cast with a certain high temperature, since a slight drop in temperature may cause freezing poured into the oven
iron in the pour chute and out of the last system with all the consequences of the accident. Pouring iron through the chute is also linked to the erosion of the lining of the trough and pollution
nonmetallic inclusions become exogenous. In addition, significant maintenance costs gutters in working condition.
Solid iron through the roof can be arranged at much lower temperatures, but at a temperature less than 1200C may iron speleobrazovanie, in which tiny particles of graphite, settling for a short network electric arc furnace can cause a short circuit. Undeveloped technology in casting iron stove top can cause emissions of iron and steel slag from the furnace, play, increased wear of the lining, a slight degree of dephosphorization and desulfurization.
Desired technical results of the invention are: reduction of fuel electrodes for steelmaking, reducing the duration of melting, improve the quality of steel.
For this purpose, the filling composition is introduced or iron ore agglomerate in an amount of 30–60 kg / tn steel, after melting of metal at a rate Electricity 220–320 kWh / tn of scrap in the furnace is poured molten iron at a temperature not lower than 1200 ° C at a speed of 6–12 tn filling / m and gaseous oxidation Oxygen at a rate of 1500–3000 Nm3 / h ratio sits iron ore agglomerate or in admixture with lime support respectively (1–2): (2.5–3.5) at their flow rate of 70–110 kg / tn of steel slag then lowered the threshold of the working window, and the ratio of lime, fluorspar and aluminum powder introduced into the ladle desulfurization the mixture was kept, respectively (1.1–1.5): (0.3–0.5): (0.05–0.1) mixture at a flow rate 14–18 kg / tn of steel[6].
4. Notable design schemes and foreign developers choice constructive solutions
Drawing 1 and 2 show the structure of the trough of German firms and RHI SIEMENS VAI. Chute for pouring molten iron structure placed on RHI mobile cart by overhead crane, and gutter SIEMENS VAI fixed on a mobile cart and does not require tilting, which is an advantage compared to chute RHI.
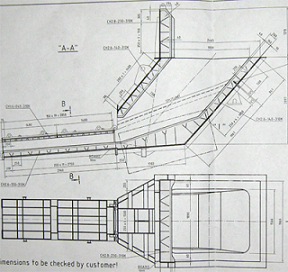
Drawing 1 – Trough for pouring molten iron construction RHI
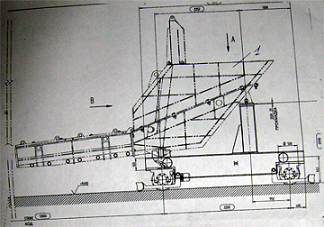
Drawing 2 – Trough for pouring molten iron construction SIEMENS VAI
There is also a design for casting iron trough design NKMZ.
Chute for pouring molten iron construction RHI placed on mobile cart by overhead crane, and gutter SIEMENS VAI and NKMZ mounted on a movable carriage and does not require tilting, which is an advantage compared with a groove RHI.
5. Development and production of a physical model of the trough and issuing recommendations for research
In developing the physical model was based on the design of the trough for casting iron firm SIEMENS VAI. Presently constructed model mobile trough (drawing 3), which will be fixed trough model. Mounted on the carriage drive comprising an electric motor and a manually collected five-stage gearbox.
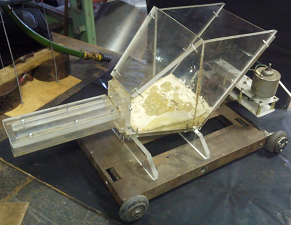
Drawing 3 – Physical model of the mobile trough
In developing the model was chosen trough 1:10. Choosing the scale model should also consider the significant impact of surface tension of the liquid on the process model unit when it is too small sections of the channels and holes. The diameter of the holes in the model using different simulating fluids should be as follows: water – not less than 12 mm, glycerol – 10, kerosene and oil – at least 8 mm. Since the molten steel during the experiment replace the water, the diameter of the outlet opening trough for the chosen scale, corresponds to a condition of over 12 mm.
Material for the model will plexiglass has transparent and easily lends itself to different types of mechanical processing that allows you to accurately copy virtually any configuration of the test specimens of the contours of the unit and carry out visual observations of flowing gidrogazodinamicheskimi model processes.
For research process flow of liquid iron in the trough would be necessary fluid flow visualization. Visualization – is the creation of conditions conducive to the emergence of contrasting pictures trajectories simulating fluid flows through the introduction of her coloring liquid substances or finely divided solids having a high reflectivity. Colored fluid droplets or particles carried by an optically transparent streams exactly reproduce their movements and allow adequate light to get a clear picture of the flow distribution in the working volume of the simulated machine.
Flow visualization is considered an important factor in research and, above all, in the physical modeling of the hydrodynamic processes, since it not only allows you to make definite conclusions about the qualitative aspects of the phenomenon, but also refers to one of the necessary conditions for the realization optical method of monitoring fluid mixing time and speed measurement Photomethod fluid streams. To fix the results of the study will be conducted photographing. Under extreme conditions, special types of photography hydrodynamic processes often requires the development of special adaptations that allow to implement task in each case with the greatest efficiency[7].
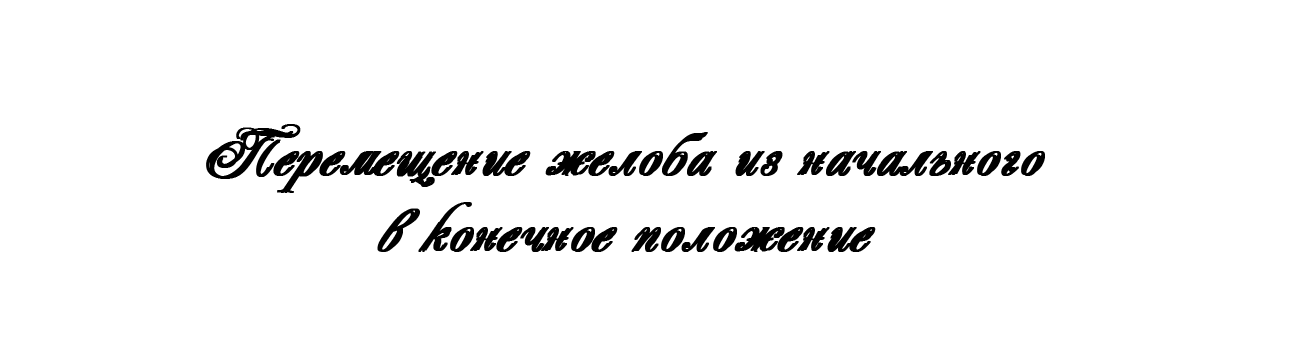
Drawing 4 – Moving trough from the initial to the final position
(animation: 8 frames, 6 cycles of repeating, 165 kilobytes)
Conclusion
Thus, development aimed at improving the metal smelting in electric furnaces are promising due to lower costs a solid metal scrap, energy and cost saving metal by pouring molten iron into a furnace.
The proposed variant of the trough is more versatile due to design features and troubleshooting blur lining fluid iron. Studies extend the operational life of the trough before the next repair.
This master's work is not completed yet. Final completion: December 2014. The full text of the work and materials on the topic can be obtained from the author or his head after this date.
References
- Информационный портал
Steel times
– Жидкий чугун для плавки стали в современной дуговой печи (ДСП). Режим доступа: http://steeltimes.ru/books/steelmaking/minizavod/244/244.php - Электрометаллургический прогресс/ Кукин С.В./ Металл &ndash 2007. – № 5. – С. 15.
- Информационный портал
Specural Com
– Заливка жидкого чугуна в мартеновскую печь и плавление. Режим доступа: http://specural.com/articles/category/5/message/63/ - Патент RU 2302471 C1 Россия, C21C5/52, C21C7/06. Способ выплавки стали в дуговой электропечи / Ю.Д. Девяткин, Е.П. Кузнецов, Н.А. Козырев и др.; ОАО
Новокузнецкий металлургический комбинат
. №2006114524/02; заявлено 27.04.2006; опубл. 10.07.2007. Режим доступа: http://bd.patent.su/2302000-2302999/pat/servl/servlet65cc.html - Патент RU 2258084 C1 Россия, C21C5/52, C21C7/06. Способ выплавки стали в дуговой электропечи / Л.А. Годик, А.И. Катунин, Н.А. Козырев и др.; ОАО
Новокузнецкий металлургический комбинат
. №2003136330/02; заявлено 15.12.2003; опубл. 10.08.2005. Режим доступа: http://bd.patent.su/2258000-2258999/pat/servl/servletab79.html - Патент RU 2197535 C2 Россия, C21C5/52, C21C7/06. Способ получения стали в дуговой электросталеплавильной печи /А.И. Катунин, Л.А. Годик, Н.А. Козырев и др.; ОАО
Кузнецкий металлургический комбинат
. №2000107730/02; заявлено 29.03.2000; опубл. 27.01.2003. Режим доступа: http://bd.patent.su/2197000-2197999/pat/servl/servlet9794.html - Еронько С.П., Быковских С,В. Физическое моделирование процессов внепечной обработки и розливки стали. – К.: Техника, 1998. – 136 с.