Реферат
ПРИМЕЧАНИЕ: Реферат носит постановочный характер, так как время его создания – апрель – май 2014 г., тогда как защита магистерской работы запланирована на январь 2015 г.
Содержание
- 1. Введение
- 2. Актуальность темы
- 3. Цель и задачи
- 4. Обзор существующих исследований
- Список источников
1. Введение
Повышение качества и производительности изготовления стержневых изделий, а соответственно себестоимости, является актуальной проблемой современной промышленности. Решение этих задач, а также сопутствующих проблем, обеспечит конкурентоспособность изделий.
Наиболее часто используемым методом получения стержневых изделий является метод холодной высадки или штамповки. Этот метод имеет достаточную производительность в сумме с приемлемым качеством получаемых изделий. Но учитывая спрос и количество используемых в промышленности изделий данного типа, вопрос повышение производительности для производства изделий является актуальным и поныне.
Поэтому теоретические и экспериментальные исследования, направленные на разработку, совершенствование и внедрение технологических процессов изготовления крепежных изделий на высокопроизводительных роторных линиях, являются важными и актуальными.
2. Актуальность темы
В настоящее время широко используются крепежные стержневые соединительные изделия такие как болты, винты, шурупы, гвозди и т.д. Для их изготовления применяется раздельное технологическое оборудование, что неэффективно, так как требует больших расходов на содержание производственных площадей, транспортирование деталей от станка к станку и др., решением этой проблемы является высоко автоматизированное производство. Изготовление этих изделий на одной технологической линии позволит повысить технико-экономические показатели их изготовления, снизить себестоимость и избежать транспортных расходов.
3. Цель и задачи
Целью работы является кратное увеличение производительности при изготовлении стержневых изделий, путём применения высокотехнологичного роторного оборудования.
При этом необходимо решить следующие задачи:
· Проанализировать возможность объединения всех операций изготовления изделия, начиная от подачи заготовки и заканчивая организацией хранения деталей.
· Составление высокопроизводительного и рационального технологического процесса
· Определения возможности применения новой кинематики при изготовления стержневых изделий или совершенствование уже имеющихся
· Разработка схемы роторной лини для изготовления изделий
· Проектирование новой функционально–ориентированной роторной линии.
4. Обзор существующих исследований
В настоящее время проводится большое количество исследований по разработке роторов и роторных линий. Усилиями многих ученых внесен значительный вклад в развитие. Среди которых Л. Н. Кошкин, И. А. Клусов и др.
В настоящее время для изготовления данных деталей используется традиционное оборудование–холодновысадочные автоматы дискретного действия, которые за один двойной ход высадочного ползуна обеспечивают выход одного изделия. Опыт эксплуатации холодноштамповочных автоматов показал, что их производство напрямую зависит от длины изделия. Так как длина изделия определяет ход ползуна и, следовательно, радиус кривошипа и длину шатуна, то для более длинных изделий ползун вынужден совершать больший ход на меньших скоростях. Диапазон размеров изготавливаемых деталей следующий:
– болты – М2…М100;
– гайки – М2…М100;
– винты – М2…М56;
– кольца стопорные: наружные и внутренние – 3…300;
– шайбы – М2…М100;
– шпильки – М6…М100;
– заклепки – 2…24;
– шплинты – 1,6…10;
Например, паспортная производительность холодновысадочных авто-матов достигает 12 шт/с при длине до 50 мм, а при длине 200 мм–3 шт/с. Это обусловлено инерционными и динамическими нагрузками, а также колебаниями машины.
Основным материалом для изготовления деталей типа тел вращения обычно является сталь различной прочности. Для изготовления гровер-шайб и тарельчатых шайб используется специальная пружинная сталь. В качестве защитного покрытия используется цинк (Zn).
Развитие машиностроения и металлообработки требует дальнейшего совершенствования технологических процессов и организации производства, повышения его эффективности и увеличения производительности труда на базе автоматизации производственных процессов.
Процессы штамповки получили широкое применение в различных отраслях промышленности, благодаря высокой производительности и экономической эффективности.
Холодная штамповка являлась одним из наиболее прогрессивных технологических методов производства; она имеет ряд преимуществ перед другими видами обработки металлов, как в техническом, так и в экономическом отношении.
В техническом отношении холодная штамповка позволяет:
1) получать детали весьма сложных форм, изготовление которых другими методами обработки или невозможно или затруднительно;
2) создавать прочные и жесткие, но легкие по массе конструкции деталей при небольшом расходе материала;
3) получать взаимозаменяемые детали с достаточно высокой точностью размеров, преимущественно без последующей механической обработки.
В экономическом отношении холодная штамповка обладает следующими преимуществами:
1) экономным использованием материала и сравнительно небольшими отходами;
2) весьма высокой производительностью оборудования, с применением механизации и автоматизации производственных процессов;
3) массовым выпуском и низкой стоимостью изготовляемых изделий.
Наибольший эффект от применения холодной штамповки может быть обеспечен при комплексном решении технических вопросов на всех стадиях подготовки производства, начиная с создания технологичных конструкций или форм деталей, допускающих экономичное изготовление их.
Холодная штамповка объединяет большое количество разнообразных операций, которые могут быть систематизированы по технологическим признакам.
По характеру деформаций холодная штамповка расчленяется на две основные группы: деформации с разделением материала и пластические деформации.
Первая группа объединяет деформации, которые приводят к местному разъединению материала путем среза и отделения одной его части от другой. Группа пластических, деформаций холодной штамповки включает операции по изменению формы гнутых и полых листовых деталей.
Имеется четыре основных вида деформаций холодной штамповки:
1) резка — отделение одной части материала от другой по замкнутому или незамкнутому контуру;
2) гибка — превращение плоской заготовки в изогнутую деталь;
3) вытяжка — превращение плоской заготовки в полую деталь любой формы или дальнейшее изменение ее размеров;
4) формовка — изменение формы детали или заготовки путем местных деформаций различного характера.
Каждый из основных видов деформаций холодной штамповки подразделяется на ряд отдельных конкретных операций, характеризуемых особенностью и назначением работы, а также типом штампа.
Штамповка деталей путем выполнения нескольких раздельных операций в большинстве случаев экономически невыгодна, вследствие чего обычно применяют методы комбинированной штамповки, одновременно сочетающие две или несколько из указанных деформаций и отдельных операций. Кроме того, на производстве используются сборочно–штамповочные операции, основанные на применении деформаций гибки, формовки или отбортовки.
Комбинированная штамповка представляет собой совмещение в одном штампе двух или нескольких технологически различных операций штамповки.
При штамповке мелких деталей на быстроходных прессах в различных отраслях промышленности: в приборостроении, точной механике, электро-технике, радиотехнике, при производстве предметов народного потребления и др., – в основном применяются комбинированные штампы последовательного и совмещенного действий. Каждый из этих типов штампов имеет свои достоинства и недостатки, свою область применения [1].
В совмещенных штампах все штамповочные операции выполняются за счет взаимного перемещения рабочих элементов штампа без шагового перемещения ленты. При этом точность размеров отштампованной детали будет определяться точностью исполнения штампа и условиями его эксплуатации.
В случаях, когда в штампах совмещенного действия сочетается вы-рубка по контуру с пробивкой отверстий, достигается высокая точность расположения их к наружному контуру. Однако в последовательных штампах представляется возможным объединить большое количество переходов в одном штампе (до 10), в то время, как в совмещенном штампе обычно объединяются два–три перехода, а следовательно, в таком случае не всегда удается полностью устранить последующие штамповочные операции.
При автоматической штамповке на быстроходных прессах при крупносерийном и массовом характере производства обычно стремятся к полному устранению последующих штамповочных операций с ручной подачей штучных заготовок. В противном случае резко снижается экономическая эффективность этого высокопроизводительного способа штамповки в связи с необходимостью автоматизации подачи штучных заготовок, которая представляет собой весьма сложную задачу, ибо она требует создания специальных и штамповки в автоматическом цикле на быстроходных прессах-автоматах при большом числе ходов в минуту, так как лента является выгодным и падежным транспортером, масса ленты мала, силы инерции незначительны и перемещать ее можно весьма быстро, сокращая, таким образом, время подачи материала.
Так, например, посредством штамповки плоских деталей в ленте в настоящее время детали многих изделий изготовляются на быстроходных прессах–автоматах с числом ходов до 500 в минуту и выше, в то время как со-вмещенные штампы, а также штампы с шиберной переброской эксплуатируются на быстроходных прессах-автоматах с числом ходов 200–300 в минуту.
К числу недостатков штампов совмещенного действия с пружинными и резиновыми съемниками относятся: обратная запрессовка вырубленной детали в ленту, трудность удаления деталей из ленты и прилипание их к съемнику, что осложняет условия работы штампа.
В тех случаях, когда конструкция совмещенного штампа позволяет удалять отштампованные детали на провал, создаются благоприятные условия для повышения быстроходности пресса. Последовательной штамповкой в ленте в основном изготовляются детали небольших (10–50 мм) и малых (до 10 мм) размеров. В отдельных случаях при последовательной штамповке плоских деталей их размеры составляют 200–250 мм. В штампах совмещенного действия возможно изготовление деталей больших размеров. Минимальный годовой выпуск деталей, при котором окупаются затраты на комбинированный штамп последовательного действия, может быть определен по методике, предложенной В.П.Романовским [1].
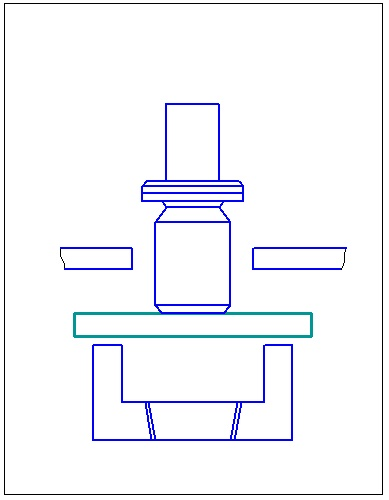
Исходя из технологических схем последовательной штамповки, которые определяют тип и конструкцию штампов последовательного действия, последовательную штамповку подразделяют на ряд видов Кроме видов последовательной штамповки, представленных на фиг. 65, имеет место также вырубка плоской заготовки на одной из первых позиций с передачей ее на формообразующие переходы шиберным или револьверным механизмом.
Из приведенных на рисунке 1.1 видов последовательной штамповки в ленте для автоматической штамповки на быстроходных прессах при высоком числе ходов ползуна в минуту предпочтительными являются: а, б и е, у которых отделение готовой детали от ленты производится на последнем переходе, что повышает надежность и устойчивость штампа в работе.
Вырубка по контуру на одном из первых переходов с передачей плоской заготовки на гибку, формовку и другие операции во многих случаях также осуществляется при повышенном числе ходов пресса, однако возможности значительного повышения числа ходов при этом ограничены, так как не успевает срабатывать исполнительный механизм штампа, что приводит к преждевременному выходу его из строя.
Следовательно, вопрос о том, при каком числе ходов пресса следует штамповать ту или иную деталь при переводе ее на скоростную штамповку, необходимо решать сообразуясь с возможными технологическими схемами ее изготовления. При этом вполне понятно, что наибольшее число ходов пресса будет иметь место при вырубке плоских деталей на провал.
Ниже описан ряд конструкций оригинальных штампов, нашедших применение в холодноштамповочном производстве предприятий, внедривших автоматическую штамповку па быстроходных прессах.
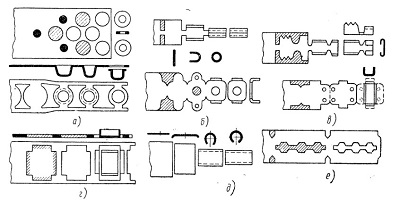
а — вырубка готовой детали на последней позиции штампа; б — отрезка готовой детали от ленты на последней позиции; в — отрезка заготовки от ленты после предварительной гибки или формовки; г — вырубка заготовки по контуру на первой позиции штампа с ее в ленту для передачи на последующие формоизменяющие позиции; д — отрезка заготовки на одной из первых позиций с последовательной гибкой на последних позициях; е — неполная вырезка контура детали с последующей отрезкой или отломкой детали от ленты
При автоматической штамповке мелких деталей на быстроходных прессах нашли широкое применение комбинированные штампы-автоматы с шиберными механизмами [2]. Штампы-автоматы с шиберными механизма-ми относятся к комбинированным штампам последовательного действия. Получение готовых деталей в таких штампах является одним из наиболее прогрессивных методов холодной штамповки.
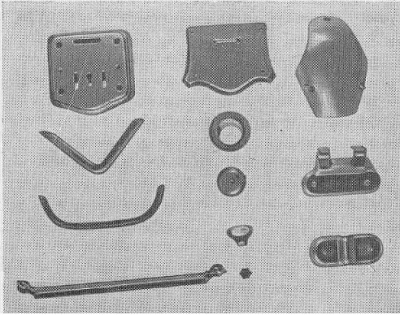
На рис. 1.2 показаны детали, изготовляемые на штампах с шиберными механизмами. Рассмотрим устройство и принцип действия нескольких типов штампов-автоматов с шиберными механизмами.
Штампы–автоматы с одним шибером. На рис 1.3 приведена конструкция штампа, предложенная Р. А. Долгополовым, с шиберной переброской вырубленной заготовки на формовочную матрицу. Штамп предназначен для изготовления детали массового производства (чемоданной пукли).
На этом штампе производится вырубка и вытяжка-формовка детали за один ход пресса.
Штамп работает следующим образом. При ходе ползуна пресса вниз клин 1 шибера воздействует на ролик 2 и отводит шибер 3 в крайнее левое положение, а клин перекрывателя 4 воздействует на ролик 5 и отводит перекрыватель 6 крайнее правое положение. По мере опускания ползуна пуансон 7 вырубает заготовку и при помощи прижима 8 укладывает ее на нижнюю плиту 9, справа от шибера, конец которого имеет форму в виде половины контура заготовки.
Во время холостого хода шибер и перекрыватель освобождаются от действовавших на них клиньев. Под действием пружин шибер подает заготовку на формовочную матрицу 10, а перекрыватель перемещается в крайнее левое положение и предотвращает вылет заготовки из штампа.
С последующего хода устанавливается цикл работы штампа, при котором совершается описанная выше кинематика движения, но уже одновременно с вырубкой происходит вытяжка–формовка детали на провал.
При работе описанного штампа вырубной пуансон опускается в матрицу на глубину 9–10 мм, что необходимо для более правильного укладывания вырубленной заготовки в нижнем этаже (второй ярус) штампа. В этом и заключается специфика работы штампов с шиберной переброской.
Эксплуатация описанного штампа производится на кривошипном прессе усилием 25 т промышленного типа при 215 ходах в минуту, оснащенном универсальной клино–роликовой подачей конструкции Р. А. Долгополова. До модернизации пресс работал при 120 ходах ползуна в минуту.
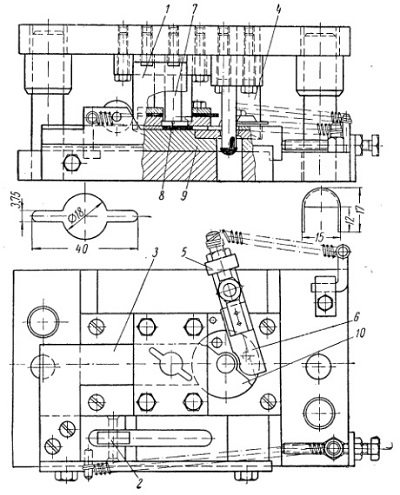
До внедрения описанного штампа, при выполнении операции формовки в отдельном штампе, трудоемкость изготовления чемоданной пукли составляла 1,51 ч на 1000 шт., после же внедрения – 0,33 ч.
В связи с тем, что машины первого класса, которыми и являются холодновысадочные пресса, характеризуются прерывистым циклом обработки, то единственным способом увеличения производительности является снижение времени цикла, то есть увеличение быстроходности пресса. А это приводит к высокоскоростному режиму работы, который характеризуется большими вибрациями, громким и вредным для рабочих шумом.
В настоящее время механические прессы, как правило, имеют значительно большее число ходов в минуту, чем прессы более раннего производства. Это относится особенно к прессам небольших усилий, предназначенных для холодной штамповки из рулонного материала. Увеличение числа ходов пресса, с одновременным использованием автоматических подач штампуемого материала является по сути единственным способом повышения их производительности.
Поскольку холодно–высадочные автоматы являются машинами 1 класса, в которых обработка и транспортировка не совмещены. Вследствие этого возникают холостые хода. Для увеличения производительности необходимо уменьшить холостые хода, а этого можно добиться повышением числа ходов, которое вызывает увеличение скоростей, ускорений и сил инерции движущихся частей пресса, что при определенных значениях их может вредно отразиться на стойкости сочленений деталей, совершающих возвратно-поступательное движение. В тихоходных прессах нет практической необходимости строго балансировать вращающиеся части; в быстроходных же это обязательно, так как незначительный дисбаланс в валах, зубчатых колесах и других вращающихся деталях может вызвать недопустимую вибрацию пресса.
В быстроходных прессах с числом ходов в минуту более 600—700 иногда недостаточно производить только статическую балансировку деталей; возникает необходимость динамической балансировки пресса, чтобы исключить его вибрацию. Следовательно, проектирование и изготовление быстроходных механических прессов связано с рядом дополнительных факторов, которые могут не учитываться при производстве тихоходных машин.