Реферат за темою випускної роботи
ПРИМІТКА: Реферат носить постановочний характер, так як час його створення – квітень – травень 2014 р. Тоді як захист магістерської роботи запланований на січень 2015 р.
Зміст
1. Введення
Підвищення якості та продуктивності виготовлення стрижневих виробів, а відповідно собівартості, є актуальною проблемою сучасної промисловості. Вирішення цих завдань, а також супутніх проблем, забезпечить конкурентоспроможність виробів.
Найбільш часто використовуваним методом отримання стрижневих виробів є метод холодного висадження або штампування. Цей метод має достатню продуктивність в сумі з прийнятною якістю одержуваних виробів. Але враховуючи попит і кількість використовуваних в промисловості виробів даного типу, питання підвищення продуктивності для виробництва виробів є актуальним і понині.
Тому теоретичні та експериментальні дослідження, спрямовані на розробку, вдосконалення і впровадження технологічних процесів виготовлення кріпильних виробів на високопродуктивних роторних лініях, є важливими і актуальними.
2. Актуальність теми
В даний час широко використовуються кріпильні стрижневі з'єднувальні вироби такі як болти, гвинти, шурупи, цвяхи і т.д. Для їх виготовлення застосовується роздільне технологічне обладнання, що неефективно, оскільки вимагає великих витрат на утримання виробничих площ, транспортування деталей від верстата до верстата та ін, рішенням цієї проблеми є високо автоматизоване виробництво. Виготовлення цих виробів на одній технологічній лінії дозволить підвищити техніко–економічні показники їх виготовлення, знизити собівартість і уникнути транспортних витрат.
3. Мета і завдання h2>
Метою роботи є кратне збільшення продуктивності при виготовленні стрижневих виробів, шляхом застосування високотехнологічного роторного обладнання.
При цьому необхідно вирішити такі завдання:
· Проаналізувати можливість об'єднання всіх операцій виготовлення виробу, починаючи від подачі заготовки і закінчуючи організацією зберігання деталей.
· Складання високопродуктивного та раціонального технологічного процесу
· Визначення можливості застосування нової кінематики при виготовлення стрижневих виробів або вдосконалення вже наявних
· Розробка схеми роторної лини для виготовлення виробів
· Проектування нової функціонально–орієнтованої роторної лінії.
4. Огляд існуючих досліджень
В даний час проводиться велика кількість досліджень з розробки роторів і роторних ліній. Зусиллями багатьох учених внесений значний внесок в розвиток. Серед яких Л.Н. Кошкін, І.А. Клус та ін
В даний час для виготовлення даних деталей використовується традиційне обладнання–холодновисадочні автомати дискретної дії, які за один подвійний хід висадочних повзуна забезпечують вихід одного виробу. Досвід експлуатації холодноштампувальні автоматів показав, що їх виробництво безпосередньо залежить від довжини виробу. Так як довжина виробу визначає хід повзуна і, отже, радіус кривошипа і довжину шатуна, то для більш довгих виробів повзун змушений здійснювати більший хід на менших швидкостях. Діапазон розмірів виготовляються деталей наступний:
– Болти – М2...М100;
– Гайки – М2...М100;
– Гвинти – М2...М56;
– Кільця стопорні: зовнішні і внутрішні – 3...300;
– Шайби – М2...М100;
– Шпильки – М6...М100;
– Заклепки – 2...24;
– Шплінти – 1,6...10;
Наприклад , паспортна продуктивність холодновисадочних автоматів досягає 12 шт/с при довжині до 50 мм, а при довжині 200 мм – 3 шт/с. Це обумовлено інерційними і динамічними навантаженнями, а також коливаннями машини.
Основним матеріалом для виготовлення деталей типу тіл обертання зазвичай є сталь різної міцності. Для виготовлення гровер–шайб і тарілчастих шайб використовується спеціальна пружинна сталь. В якості захисного покриття використовується цинк (Zn).
Розвиток машинобудування і металообробки вимагає подальшого вдосконалення технологічних процесів і виробництва, підвищення його ефективності і збільшення продуктивності праці на базі автоматизації виробничих процесів.
Процеси штампування отримали широке застосування в різних галузях промисловості, завдяки високій продуктивності та економічної ефективності.
Холодне штампування була одним з найбільш прогресивних технологічних методів виробництва; вона має ряд переваг перед іншими видами обробки металів, як у технічному, так і в економічному відношенні.
У технічному відношенні холодне штампування дозволяє:
1) одержувати деталі дуже складних форм, виготовлення яких іншими методами обробки або неможливо або важко;
2) створювати міцні і жорсткі, але легкі за масою конструкції деталей при невеликій витраті матеріалу;
3) отримувати взаємозамінні деталі з досить високою точністю розмірів, переважно без подальшої механічної обробки.
В економічному відношенні холодне штампування володіє наступними перевагами:
1) економним використанням матеріалу і порівняно невеликими відходами;
2) досить високою продуктивністю обладнання, із застосуванням механізації та автоматизації виробничих процесів;
3) масовим випуском і низькою вартістю виготовлених виробів.
Найбільший ефект від застосування холодного штампування може бути забезпечений при комплексному вирішенні технічних питань на всіх стадіях підготовки виробництва, починаючи зі створення технологічних конструкцій або форм деталей, що допускають економічне виготовлення їх.
Холодне штампування об'єднує велику кількість різноманітних операцій, які можуть бути систематизовані за технологічними признакам.
За характером деформацій холодне штампування розчленовується на дві основні групи: деформації з поділом матеріалу і пластичні деформації.
Перша група об'єднує деформації, які призводять до місцевого роз'єднанню матеріалу шляхом зрізу та відділення однієї його частини від іншої. Група пластичних, деформацій холодного штампування включає операції по зміні форми гнутих і порожнистих листових деталей.
Є чотири основних види деформацій холодного штампування:
1 ) різка–відділення однієї частини матеріалу від іншої за замкнутому або незамкнутому контуру;
2 ) гнучка–перетворення плоскої заготовки в вигнуту деталь;
3 ) витяжка–перетворення плоскої заготовки в порожнисту деталь будь–якої форми або подальше зміна її розмірів;
4 ) формовка–зміна форми деталі або заготовки шляхом місцевих деформацій різного характеру.
Кожен з основних видів деформацій холодного штампування підрозділяється на ряд окремих конкретних операцій, якi характеризуються особливістю і призначенням роботи, а також типом штампа.
Штампування деталей шляхом виконання декількох роздільних операцій в більшості випадків економічно невигідна, внаслідок чого зазвичай застосовують методи комбінованої штампування, одночасно поєднують дві або кілька із зазначених деформацій і окремих операцій. Крім того, на виробництві використовуються складально-штампувальні операції, засновані на застосуванні деформацій гнучкі, формування або отбортовки .
Комбінована штампування являє собою поєднання в одному штампі двох або кількох технологічно різних операцій штампування.
При штампуванні дрібних деталей на швидкохідних пресах в різних галузях промисловості: у приладобудуванні, точної механіки, електротехніці , радіотехніці, при виробництві предметів народного споживання та ін, – в основному застосовуються комбіновані штампи послідовного і суміщеного дій . Кожен з цих типів штампів має свої переваги і недоліки, свою область застосування [1].
В суміщених штампах все штампувальні операції виконуються за рахунок взаємного переміщення робочих елементів штампа без крокової переміщення стрічки. При цьому точність розмірів відштампованої деталі визначатиметься точністю виконання штампа та умовами його експлуатації.
У випадках, коли в штампах поєднаної дії поєднується вирубка по контуру з пробивкой отворів, досягається висока точність расположення їх до зовнішнього контуру. Однак в послідовних штампах представляється можливим об'єднати велику кількість переходів в одном штампі (до 10), в той час, як в суміщеному штампі зазвичай об'єднуються два–три переходу, а отже, в такому випадку не завжди вдається повністю усунути наступні штампувальні операції.
При автоматичної штампуванні на швидкохідних пресах при великосерійному і масовому характері виробництва зазвичай прагнуть до повного усунення подальших штампувальних операцій з ручною подачею штучних заготовок. В іншому випадку різко знижується економічна ефективність цього високопродуктивного способу штампування у зв'язку з необхідністю автоматизації подачі штучних заготовок, яка представляє собою досить складне завдання, бо вона вимагає створення спеціальних і штампування в автоматичному циклі на швидкохідних пресах–автоматах при великому числі ходів у хвилину, так як стрічка є вигідним і відмінковим транспортером, маса стрічки мала, сили інерції незначні і переміщати її можна вельми швидко, скорочуючи, таким чином, час подачі матеріалу.
Так, наприклад, за допомогою штампування плоских деталей у стрічці в наварте час деталі багатьох виробів виготовляються на швидкохідних пресах–автоматах з числом ходів до 500 в хвилину і вище, тоді як совміщені штампи, а також штампи з шиберной перекиданням експлуатуються на швидкохідних пресах–автоматах з числом ходів 200–300 на хвилину.
До числа недоліків штампів поєднаної дії з пружинними і гумовими знімачами відносяться: зворотна запрессовка вирубаної деталі в стрічку, труднощі видалення деталей з стрічки і прилипання їх до знімачами, що ускладнює умови роботи штампа.
У тих випадках, коли конструкція суміщеного штампа дозволяє видаляти відштамповані деталі на провал, створюються сприятливі умови для підвищення швидкохідності преса. Послідовної штампуванням в стрічці в основному виготовляються деталі невеликих (10–50 мм) і малих (до 10 мм) розмірів. В окремих випадках при послідовній штампуванні плоских деталей їх розміри становлять 200–250 мм. У штампах поєднаної дії можливе виготовлення деталей великих розмірів. Мінімальний річний випуск деталей, при якому окупаються витрати на комбінований штамп послідовної дії, може бути визначений за методикою, запропонованої В.П.Романовскім [1].
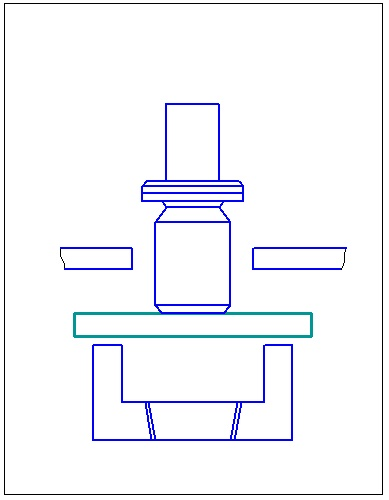
Виходячи з технологічних схем послідовної штампування , які визначають тип і конструкцію штампів послідовної дії, послідовну штампування поділяють на ряд видів Крім видів послідовної штампування, представлених на фіг .65, має місце також вирубка плоскою заготовки на одній з перших позицій з передачею її на формотворчих переходи шиберним або револьверним механізмом.
З наведених на малюнку 1.1 видів послідовної штампування в стрічці для автоматичного штампування на швидкохідних пресах при високому числі ходів повзуна в хвилину переважними є: а, б і е , у яких відділення готової деталі від стрічки проводиться на останньому переході, що підвищує надійність і стійкість штампа в роботі.
Вирубка по контуру на одному з перших переходів з передачею плоскою заготовки на гибку, формовку та інші операції в багатьох випадках також здійснюється при підвищеному числі ходів преса, однак можливості значного підвищення числа ходів при цьому обмежені, оскільки не встигає спрацьовувати виконавчий механізм штампа, що призводить до передчасного виходу його з ладу.
Отже, питання про те, при якому числі ходів преса слід штампувати ту чи іншу деталь при перекладі її на швидкісну штампування, необхідно вирішувати погодившись з можливими технологічними схемами її виготовлення. При цьому цілком зрозуміло, що найбільше число ходів преса буде мати місце при вирубці плоских деталей на провал.
Нижче описаний ряд конструкцій оригінальних штампів, що знайшли застосування в холодноштампувальні виробництві підприємств, що впровадили автоматичну штампування па швидкохідних пресах.
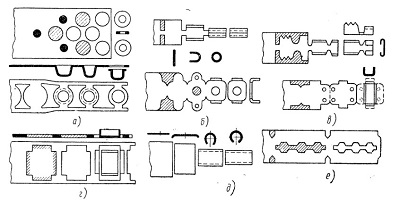
а - вирубка готової деталі на останній позиції штампа; б - відрізка готової деталі від стрічки на останній позиції; в - відрізка заготовки від стрічки після попередньої гнуття або формовки; г - вирубка заготовки по контуру на першій позиції штампа з її в стрічку для передачі на наступні формоізменяющіе позиції; д - відрізка заготовки на одній з перших позицій з послідовною гнучкою на останніх позиціях; е - неповна вирізка контура деталі з наступною відрізків або уламка деталі від стрічки
При автоматичної штампуванні дрібних деталей на швидкохідних пресах знайшли широке застосування комбіновані штампи–автомати з шиберними механізмами [2]. Штампи–автомати з шиберними механізмами відносяться до комбінованих штампам послідовної дії. Отримання готових деталей в таких штампах є одним з найбільш прогресивних методів холодного штампування.
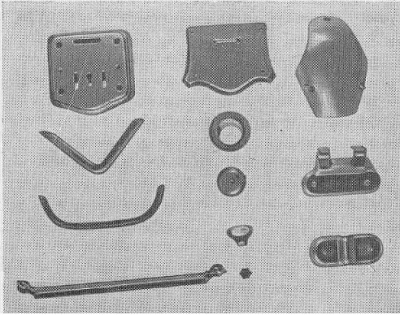
На рис. 1.2 показані деталі, що виготовляються на штампах з шиберними механізмами . Розглянемо пристрій і принцип дії декількох типів штампів-втоматів з шиберними механізмами.
Штампи–автомати з одним шибером. На рис 1.3 наведена конструкція штампа, запропонована Р.А. Долгополовим, з шиберной перекиданням вирубаної заготовки на формувальну матрицю. Штамп призначений для виготовлення деталі масового виробництва (чемоданної пуклі).
На цьому штампі проводиться вирубка і витяжка - формовка деталі за один хід преса.
Штамп працює таким чином. При ході повзуна преса вниз клин 1 шибера впливає на ролик 2 і відводить шибер 3 в крайнє ліве положення, а клин перекривателя 4 впливає на ролик 5 і відводить перекриватель 6 крайнє праве положення. У міру опускання повзуна пуансон 7 вирубує заготовку і за допомогою притиску 8 вкладає її на нижню плиту 9, праворуч від шибера, кінець якого має форму у вигляді половини контуру заготовки.
Під час холостого ходу шибер і перекриватель звільняються від діяли на них клинів. Під дією пружин шибер подає заготовку на формувальну матрицю 10, а перекриватель переміщається в крайнє ліве положення і запобігає виліт заготовки з штампа.
З подальшого ходу встановлюється цикл роботи штампа, при якому відбувається описана вище кінематика руху, але вже одночасно з вирубкою відбувається витяжка–формовка деталі на провал.
При роботі описаного штампа вирубною пуансон опускається в матрицю на глибину 9–10 мм, що необхідно для більш правильного укладання вирубаної заготовки в нижньому поверсі (другий ярус) штампа. У цьому і полягає специфіка роботи штампів з шиберной перекиданням.
Експлуатація описаного штампа проводиться на кривошипному пресі зусиллям 25т промислового типу при 215 ходах в хвилину, оснащеному універсальної клино–роликового подачею конструкції Р.А. Долгополова. До модернізації прес працював при 120 ходах повзуна в хвилину.
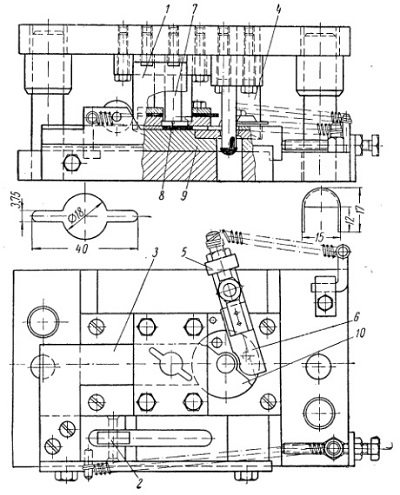
До впровадження описаного штампа, при виконанні операції формовки в окремому штампі, трудомісткість виготовлення чемоданної пуклі становила 1,51 год на 1000 шт., після ж впровадження – 0,33 ч.
У зв'язку з тим, що машини першого класу, якими і є холодновисадочниє преса, характеризуються переривчастим циклом обробки, то єдиним способом збільшення продуктивності є зниження часу циклу, тобто збільшення швидкохідності преса. А це призводить до високошвидкісного режиму роботи, який характеризується великими вібраціями, гучним і шкідливим для робочих шумом.
В даний час механічні преси, як правило, мають значно більше число ходів у хвилину, ніж преси більш раннього виробництва. Це відноситься особливо до пресів невеликих зусиль, призначених для холодного штампування з рулонного матеріалу. Збільшення числа ходів преса, з одночасним використанням автоматичних подач штампувало матеріалу є по суті єдиним способом підвищення їх продуктивності.
Оскільки холодно–висадочні автомати є машинами 1 класу, в яких обробка та транспортування не суміщені. Внаслідок цього виникають холості ходу. Для збільшення продуктивності необхідно зменшити холості ходу, а цього можна домогтися підвищенням числа ходів, яке викликає збільшення швидкостей, прискорень і сил інерції рухомих частин преса, що при певних значеннях їх може шкодно відбитися на стійкості зчленувань деталей, що здійснюють зворотно–поступальний рух. У тихохідних пресах немає практичної необхідності суворо балансувати обертові частини; в швидкохідних ж це обов'язково, так як незначний дисбаланс в валах, зубчастих колесах та інших обертових деталях може викликати неприпустиму вібрацію преса.
В швидкохідних пресах з числом ходів в хвилину більше 600–700 іноді недостатньо виробляти тільки статичну балансування деталей; виникає необхідність динамічного балансування преса, щоб виключити його вібрацію. Отже, проектування і виготовлення швидкохідних механічних пресів пов'язано з рядом додаткових факторів, які можуть не враховуватися при виробництві тихохідних машин.