Содержание
- Введение
- 1. Основные принципы создания САПР РИ
- 2. Эффективность проектирования сборного режущего инструмента на базе установленных взаимосвязей конструкторско-технологических решений.
- 3. Состояние и развитие проектирующих подсистем САПР РИ
- Список источников
Введение
Интенсивное развитие техники и технологии в конце XX века, быстрая смена номенклатуры изделий, появление станков с ЧПУ и ГАП, создание новых конструкционных и инструментальных материалов приводит к необходимости совершенствования конструкций металлорежущих инструментов.
Высокая производительность, гибкость, быстросменность, постоянство геометрических параметров - качества отвечающие требованиям современного производства - ведут к замене составного инструмента сборным. Расчет инструмента со всеми указанными параметрами и подбор оптимальных параметров является сложной, трудоемкой задачей, которые чрезвычайно трудно производить вручную. Поэтому все большее распространение получают системы автоматизированного проектирования режущего инструмента.
1. Основные принципы создания САПР РИ
В последние два десятилетие все большее распространение получают системы автоматизированного проектирования. Такие системы позволяют значительно сократить время проектирования и введения в эксплуатацию самого широкого спектра продукций: от архитектурных проектов до топологии микросхем. Системы САПР позволяют решать самые разные задачи, и применяются в самых разных отраслях. В частности, в машиностроении наиболее распространены два вида САПР: системы проектирования технологических процессов и системы твердотельного моделирования. Последние позволяют провести прочностные исследования деталей и конструкторский анализ узлов и механизмов ещё на стадии проектирования, а так же вносить исправления прямо по ходу анализа[1].
На сегодняшний день разработано несколько направлений в системах твердотельного моделирования. Ниже перечислены наиболее распространённые:
CAD-системы – предназначены для непосредственного создания модели.
CAE-системы – предназначены для автоматизированного расчета детали.
CAM-системы – предназначены для автоматизированного написания управляющей программы для станков с ЧПУ.
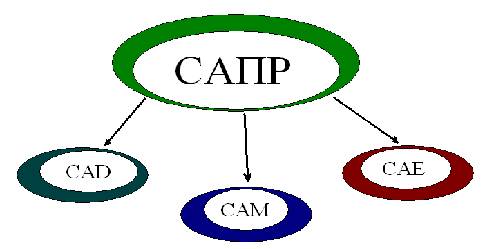
Рисунок 1 – Разновидности САПР
Системы автоматизированного проектирования занимают исключительное положение среди компьютерных приложений - это индустриальные технологии, непосредственно направленные в сферу самых важных областей материального производства.
За последние двадцать лет средства автоматизированного проектирования прошли путь от сравнительно простых чертежных систем до интегрированных программных комплексов, обеспечивающих единую поддержку всего цикла разработки, начиная от эскизного проектирования и заканчивая подготовкой производства, испытанием и сопровождением.
Современные системы автоматизированного проектирования не только дают возможность сократить срок внедрения новых изделий, но и оказывают существенное влияние на технологию производства, позволяя повысить качество и надежность выпускаемой продукции, что, в конечном счете, определяет ее конкурентоспособность. Трудно представить себе сегодняшнее промышленное предприятие или конструкторское бюро, на котором не было бы установлено несколько компьютеров и каких-либо программных продуктов, работающих в области автоматизации. Системы проектирования в масштабах предприятия за рубежом принято определять как CAD/CAM/CAE системы, в которых функции автоматизированного проектирования распределяются следующим образом: модули CAD (Computer Aided Design) -для геометрического моделирования и машинной графики; модули САМ (Computer Aided Manufacturing) - для технологической подготовки производства; модули CAE (Computer Aided Engineering) - для инженерных расчетов и анализа с целью проверки проектных расчетов. Таким образом, современные системы способны обеспечить автоматизированную поддержку работы инженеров и специалистов на всех стадиях проектирования и изготовления продукции[2].
В России традиционно не существовало деления задач проектирования на конструкторские, технологические и расчетные. Системы, обеспечивающие полную автоматизацию всего процесса проекирования или любого из его этапов, называют системами автоматизировал л оро проект лровалия (САПР).
Наиболее полно требованиям и сути современных САПР отвечают интегрированные комплексы высокоавтоматизированных специализированных систем, разработанных в рамках единой методологии. С этой точки зрения многие сегодняшние системы не являются Системами Автоматизированного Проектирования, так сказать, с большой буквы, а всего лишь "заготовки", на основе которых должны создаваться (или уже частично созданы) специализированные системы различного назначения и уровня. Подобный подход предусмотрен во многих современных разработках, однако, инструментом их специализации являются языки типа С++, либо внутренние языки, причем для доступа только к базовым функциям геометрического и графического ядра, без возможности информационной интеграции и отторжения созданной системы от этого ядра.
2. Эффективность проектирования сборного режущего инструмента на базе установленных взаимосвязей конструкторско-технологических решений.
В настоящее время одними из актуальных задач, стоящими перед производством, являются снижение себестоимости и повышение производительности металлообработки, повышение технологического уровня и конкурентоспособности металлообрабатывающего оборудования и режущего инструмента. Одним из основных направлений снижения себестоимости производства является повышение производительности операций металлообработки за счет увеличения скорости резания и использования более прогрессивных конструкций режущих инструментов.
Высокоскоростная технология резания имеет ряд существенных технических преимуществ по сравнению с традиционной, это - увеличение удельного съема материала в единицу времени, а, следовательно, повышение производительности и эффективности операции; уменьшение силы резания, нагрева и деформации обрабатываемой детали, что способствует повышению точности обработки нежестких деталей; повышение качества обработанной поверхности (при высокоточной настройке инструмента возможно получение обработанной поверхности высокого качества с 11а менее 0,5 мкм) и другие.
В условиях современного производства с экономической точки зрения в ряде случаев выгодно не заменять еще не устаревшее (морально или физически), но не обеспечивающее требуемой точности или производительности дорогостоящее оборудование, а оснастить его новой оснасткой и инструментом.
Современное состояние и перспективы развития металлообработки характеризуются широким использованием сборного режущего инструмента (РИС), оснащенного сменными механически закрепляемыми режущими элементами, выполненными из твердых сплавов, керамики и сверхтвердых материалов или с поликристаллическими вставками, или имеющими алмазное напыление[3]. Наибольшее применение находят следующие инструменты с механическим креплением режущих элементов: токарные проходные, подрезные, отрезные, расточные и автоматные резцы, кольцевые сверла, торцевые и концевые фрезы, наружные протяжки и другие инструменты, основные размеры которых стандартизованы.
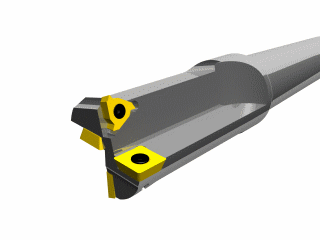
Рисунок 2 – Инструмент со сменными многогранными пластинами
(анимация: 10 кадров, 5 циклов повторения, 160 килобайт)
Многообразие условий обработки и недостаточное развитие расчетных методов, не позволяющих решать задачу выбора рациональной конструкции инструмента на стадии проектирования, привели к созданию большой номенклатуры инструмента одного назначения.
Стремительный рост информационных технологий и рыночно ориентированная адаптация производства послужили причиной разработки и внедрения систем автоматизированного проектирования (САПР) и систем сквозного проектирования- производства (CAD/CAM) сборных режущих инструментов, подавляющее большинство которых ориентировано на проектирование какого-либо вида инструмента, определенной его конструкции или элемента конструкции для конкретных производственных условий, в основе которых используются математические модели, построенные с применением различных подходов, в результате чего теряется взаимосвязь задач, преемственность моделей, данных и решений, что приводит к снижению качества проектирования и получению противоречивых решений.
Таким образом, актуальной является задача разработки обобщенной системы проектирования сборного режущего инструмента, разработанной с использованием системного подхода к формализации процессов и систем САПР РИС и CAD/CAM РИС, подчиняющейся единой системе управления моделируемым объектом, позволяющей обеспечить концептуальное единство используемых моделей, учитывающей факторы случайности процесса металлообработки и нечеткости исходных данных на проектирование, позволяющей автоматически строить алгоритм проектирования инструмента на основе некоторых знаний о законах его функционирования, создать единую среду для решения широкого круга задач, снизить затраты на разработку и исследование систем проектирования сборных режущих инструментов.
3. Состояние и развитие проектирующих подсистем САПР РИ
Проектирующие подсистемы САПР РИ являются основой развития автоматизированного проектирования в инструментальном производстве. Для автоматизированных систем технологической подготовки производства наиболее предпочтительным является использование аппаратных средств, позволяющих вести проектирование инструмента в диалоговом режиме. В этом случае можно спроектировать инструмент оптимальной конструкции[4].
Для режущего инструмента любого вида проектирующие подсистемы разрабатываются в следующей последовательности: отработка общих методических принципов проектирования; описание параметров обрабатываемых деталей; составление методики расчета параметров конструктивных элементов режущего инструмента (параметров технологического процесса и др.); отработка блок-схемы порядка расчета; определение составов и функций программных модулей; разработка программ расчета параметров инструмента (технологического процесса и др.).
Непременным условием создания высокоэффективной системы проектирования является определение правильной информационной структуры инструмента. Для того чтобы САПР РИ могла функционировать в режиме разработки оптимальной конструкции, должны быть раскрыты следующие связи: - просгранственные, определяющие место и (последовательность расположения отдельных элементов (например, главной и калибрующей режущих кромок, хвостовика и др.); - функциональные, определяющие величины параметров (например, параметры конструктивных элементов, обеспечивающие достаточные прочность и жесткость); - внешние, обусловленные характером и условиями взаимодействия инструмента с обрабатываемой деталью.
Внешние связи определяют формирование исходных данных. Режущий инструмент работает в определенных условиях, характеризуемых режимами резания, применяемой СОЖ, используемым оборудованием и др. Число внешних факторов достигает нескольких десятков, и поэтому их следует сгруппировать. Можно выделить три группы таких факторов. Первая характеризует обрабатываемую деталь и определяет связи непосредственно между заготовкой н инструментом[5]. К ней относятся: - химические, физические и механические свойства материала детали; - шероховатость обрабатываемой поверхности; - точность обрабатываемой детали; - геометрическая форма обрабатываемой детали; - метод получения заготовки детали; - основные размеры и касса детали; - дополнительные данные.
Вторая группа факторов относится непосредственно к самому инструменту. В нее входят:
- особенности конструкции инструмента;
- основные размеры инструмента;
- материал инструмента;
- необходимость перетачивания;
- особенности термообработки и методы нанесения износостойких покрытий на рабочую поверхность;
- дополнительные данные.
- дополнительные данные.
К третьей группе внешних факторов относятся условия эксплуатации режущего инструмента:
- режимы резания;
- характер производства (единичное, серийное и пр.);
- вид СОЖ и способ подхода ее в зону резании;
- регламентация стойкости инструмента;
- форма и необходимость отвода стружки;
- вид оборудования, на котором предполагается использование инструмента;
- дополнительные данные.
Из приведенных выше программных модулей с точки зрения формализации наибольший интерес представляет программа «материал». При выборе материала режущего инструмента невозможно установить определенные математические зависимости. Решение задачи выбора материала было реализовано в форме реляционной БД, формирование которой описано ниже.
Выявление внешних и внутренние связей у осевых инструментов позволяет учитывать до 20—30 факторов, влияющих на структуру САПР осевых режущих инструментов, из которых значительная часть влияет на выбор инструментального материала. Но учитывать все факторы нецелесообразно, т. к. усложняется практическое использование САПР РИ из-за увеличения необходимых исходных данных, а также трудно учесть ряд факторов (примене-ние СОЖ, нанесение покрытий и др.) из-за отсутствия экспериментальных данных. Поэтому более рационально выделить определяющие факторы[6].
При выборе материала для осевого инструмента определяющими факторами являются:
1) материал обрабатываемой детали;
2) характер предварительной подготовки детали с указанием состояния поверхности заготовки;
3) диаметр обрабатываемого отверстия;
4) режим резания;
5) тип производства деталей;
6) вид и степень автоматизации оборудовании;
7) жесткость системы СПИД;
8) особенности технологического процесса получения заготовки инструмента;
9) наличие данного инструментального материала.
Указанные девять факторов являются необходимыми для достаточно обоснованного выбора инструментального материала и частично учитывают другие факторы, не входящие в число этих девяти. Каждый фактор инвариантен. Обычно для выбора предлагается от 10 до 200 марок материалов для обрабатываемых деталей. Если карта выбора составляется для конкретного предприятия (отрасли), то число марок следует ограничить с учетом потребностей данного предприятия.
Работа будет вестись в программе PowerMill. PowerMILL является основным пакетом в программной линейке Delcam. PowerMILL предназначен для разработки управляющих программ для 3-осевых и многоосевых фрезерных станков с ЧПУ.
Данная программа хорошо стыкуется со многими CAD системами благодаря Delcam Exchange, которая отлично генерирует многие форматы в нужные. Особенно хорошо работает с пакетным модулем Delcam PowerSHAPE, в системе реализована концепция Total Modeling, которая позволяет в единой среде моделирования комбинировать разные техники моделирования.
Непосредственно для нас PowerMILL интересен для проектирования и изготовления сборных осевых инструментов, по готовым уже 3D моделям, изготовленным в CAD системах [7]. По готовым моделям назначаются нужные траектории инструментов, режимы резания и все необходимые параметры.
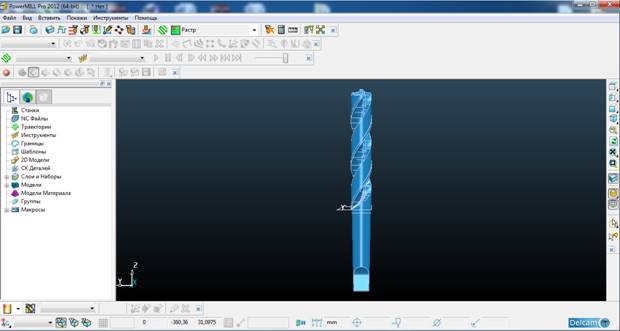
Рисунок 1 – Работа в PowerMILL.
Нельзя не отметить мощные и удобные средства модицирования сгенерированных траекторий. В других CAM системах распространена следующая идеология создания УП: вначале создаем все ограничивающие условия, подходы, отходы, далее- запускаем расчет и получаем готовую траекторию. На этом этапе остается либо принять результат, либо начать все заново. Система PowerMILL предоставляет средства для дальнейшей работы над траекториями. Вначале достаточно задать базовые параметры: тип стратегии, шаг, а если необходимо, то и направление. Очень богатая база подходов, отходов, врезаний и тп. В общем все зависит от собственной фантазии(в разумных пределах) и опыта. Так же удобное создание границ зон обработки, и расчет траектории в границах надежно застрахован от зарезов.
Как правило технолог работает с уже устоявшейся номенклатурой, и удобнее всего наполнить собственную базу данных реально используемыми инструментами. Для этого была разработана база данных в составе PowerMILL Utils[6-8]. Пользователь может заполнить базу собственными инструментами, задавая не только геометрические размеры инструмента и патрона, но и режимы резания применительно к различным материалам и станкам. Неудобство этого метода в том, что описание инструмента в PMUtils несколько отличается от описания инструмента в PM, как по интерфейсу так и по форме. Получится, что PMUtils ограничит ваши возможности по заданию параметров инструментов.
Однако, при изменении параметров проектирующегося инструмента приходится менять весь текст программы, а это долго и не удобно. Выходом из этого является создание макросов для отдельных инструментов и его траекторий.
Список источников
- www.prorobot.ru/referats/r16/prorobot.ru-16-0010.doc
- Ю.Е. Петухов: Некоторые направления развития САПР режущего инструмента// СТИН. 2003. № 8.
- Ю. А. Новосёлов: Проблематика автоматизации проектирования режущих инструментов// СТИН. 2008. № 9.
- Петpушин С.И., Баканов А.А., Махов А.В., Геометрический и силовой анализ сбоpных свеpл со сменными многогpанными пластинами/Технология машиностроения, Вып. 10(64), 2007. – С. 27 – 30.
- Основи теории проектирования осевих комбинированных инструментов : дис. … дтн : 05.03.01 / Малышко Иван Александрович. – Донецк, 1995. - 419
- Проектування комбінованого осевого інструмента : метод. вказівки / сост. Кіселева І.В. – Донецк : ДонНТУ, 2007. –54с
- Основы САПР. (CAD/CAM/CAE.)/ Кунву Ли – 2004. – СПб.:Питер. –560с
- Сахаров Г.Н. Металлорежущие инструменты./ Сахаров Г.Н. Арбузов О.Б., Боровой Ю.Л., Гречишников В.А., Киселев А.С. – М.: Машиностроение, 1989. – 328 с.
Примечание
При написании данного реферата магистерская работа еще не завершена. Окончательное завершение: декабрь 2014 года. Полный текст работы и материалы по теме могут быть получены у автора или его руководителя после указанной даты.