Зміст
- Вступ
- 1. Основні принципи створення САПР РІ
- 2. Ефективність проектування збірного ріжучого інструменту на базі встановлених взаємозв'язків конструкторсько-технологічних рішень
- 3. Стан і розвиток проектують підсистем САПР РІ
- Перелік посилань
Вступ
Інтенсивний розвиток техніки і технології в кінці XX століття , швидка зміна номенклатури виробів , поява верстатів з ЧПУ і ГАП , створення нових конструкційних та інструментальних матеріалів призводить до необхідності вдосконалення конструкцій металорізальних інструментів.
Висока продуктивність , гнучкість , швидкозмінною , сталість геометричних параметрів - якості відповідають вимогам сучасного виробництва - ведуть до заміни складеного інструменту збірним . Розрахунок інструменту з усіма зазначеними параметрами і підбір оптимальних параметрів є складною , трудомісткою завданням , які надзвичайно важко робити вручну . Тому все більшого поширення набувають системи автоматизованого проектування різального інструменту.
1.Основні принципи створення САПР РІ
В останні два десятиліття все більшого поширення набувають системи автоматизованого проектування. Такі системи дозволяють значно скоротити час проектування та введення в експлуатацію самого широкого спектра продукцій : від архітектурних проектів до топології мікросхем . Системи САПР дозволяють вирішувати найрізноманітніші завдання , і застосовуються в самих різних галузях. Зокрема , в машинобудуванні найбільш поширені два види САПР : системи проектування технологічних процесів і системи твердотільного моделювання. Останні дозволяють провести міцнісні дослідження деталей і конструкторський аналіз вузлів і механізмів ще на стадії проектування , а так само вносити виправлення прямо по ходу аналізу.[1]
На сьогоднішній день розроблено декілька напрямків в системах твердотільного моделювання. Нижче перераховані найбільш поширені :
CAD-системи - призначені для безпосереднього створення моделі.
CAE-системи - призначені для автоматизованого розрахунку деталі.
CAM-системи - призначені для автоматизованого написання керуючої програми для верстатів з ЧПУ.
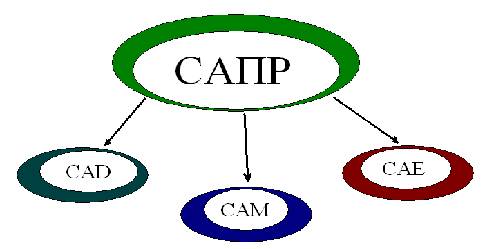
Рисунок 1 – Різновиди САПР
Системи автоматизованого проектування займають виняткове становище серед комп'ютерних додатків - це індустріальні технології , безпосередньо спрямовані в сферу найважливіших областей матеріального виробництва .
За останні двадцять років кошти автоматизованого проектування пройшли шлях від порівняно простих креслярських систем до інтегрованих програмних комплексів , які забезпечують єдину підтримку всього циклу розробки , починаючи від ескізного проектування і закінчуючи підготовкою виробництва , випробуванням і супроводом.
Сучасні системи автоматизованого проектування не тільки дають можливість скоротити термін впровадження нових виробів , а й справляють істотний вплив на технологію виробництва , дозволяючи підвищити якість і надійність своєї продукції, що , в кінцевому рахунку , визначає її конкурентоспроможність . Важко уявити собі сьогоднішнє промислове підприємство або конструкторське бюро , на якому не було б встановлено кілька комп'ютерів і яких-небудь програмних продуктів, що працюють в області автоматизації . Системи проектування в масштабах підприємства за кордоном прийнято визначати як CAD / CAM / CAE системи , в яких функції автоматизованого проектування розподіляються наступним чином: модулі CAD ( Computer Aided Design ) - для геометричного моделювання та машинної графіки ; модулі САМ ( Computer Aided Manufacturing ) - для технологічної підготовки виробництва; модулі CAE ( Computer Aided Engineering ) - для інженерних розрахунків та аналізу з метою перевірки проектних розрахунків . Таким чином , сучасні системи здатні забезпечити автоматизовану підтримку роботи інженерів і фахівців на всіх стадіях проектування і виготовлення продукції.[2]
У Росії традиційно не існувало поділу завдань проектування на конструкторські , технологічні та розрахункові. Системи, що забезпечують повну автоматизацію всього процесу проекірованія або будь-якого з його етапів , називають системами автоматизував л оро проект лровалія ( САПР).
Найбільш повно вимогам і суті сучасних САПР відповідають інтегровані комплекси високоавтоматизованих спеціалізованих систем , розроблених в рамках єдиної методології . З цієї точки зору багато сьогоднішніх системи не є Системами Автоматизованого Проектування, так сказати, з великої літери, а всього лише " заготовки", на основі яких мають створюватися (або вже частково створені ) спеціалізовані системи різного призначення і рівня. Подібний підхід передбачений в багатьох сучасних розробках , проте , інструментом їх спеціалізації є мови типу С + +, або внутрішні мови , причому для доступу тільки до базових функцій геометричного і графічного ядра , без можливості інформаційної інтеграції та відторгнення створеної системи від цього ядра.
2. Ефективність проектування збірного ріжучого інструменту на базі встановлених взаємозв'язків конструкторсько-технологічних рішень.
В даний час одними з актуальних завдань, що стоять перед виробництвом, є зниження собівартості і підвищення продуктивності металообробки, підвищення технологічного рівня та конкурентоспроможності металообробного обладнання та ріжучого інструменту. Одним з основних напрямків зниження собівартості виробництва є підвищення продуктивності операцій металообробки за рахунок збільшення швидкості різання і використання більш прогресивних конструкцій ріжучих інструментів.
Високошвидкісна технологія різання має ряд істотних технічних переваг порівняно з традиційною , це - збільшення питомої знімання матеріалу в одиницю часу, а, отже, підвищення продуктивності та ефективності операції ; зменшення сили різання , нагрівання і деформації оброблюваної деталі , що сприяє підвищенню точності обробки нежорстких деталей; підвищення якості обробленої поверхні ( при високоточної налаштуванні інструменту можливе отримання обробленої поверхні високої якості з 11а менше 0,5 мкм) та інші.
В умовах сучасного виробництва з економічної точки зору в ряді випадків вигідно не замінювати ще застаріле ( морально чи фізично ), але не забезпечує необхідної точності або продуктивності дороге устаткування, а оснастити його нової оснащенням та інструментом.
Сучасний стан та перспективи розвитку металообробки характеризуються широким використанням збірного ріжучого інструменту (РІС), оснащеного змінними механічно закріплюються ріжучими елементами, виконаними з твердих сплавів , кераміки і надтвердих матеріалів або з полікристалічними вставками , або мають алмазне напилення.[3] Найбільше застосування знаходять наступні інструменти з механічним кріпленням ріжучих елементів: токарні прохідні, підрізні, відрізні, розточувальні і автоматні різці, кільцеві свердла, торцеві і кінцеві фрези, зовнішні протяжки та інші інструменти, основні розміри яких стандартизовані.
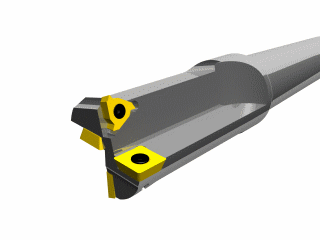
Рисунок 2 – Інструмент зі змінними багатогранними пластинами
(анімація: 10 кадрів, 5 циклів повторення, 160 кілобайт)
Різноманіття умов обробки і недостатній розвиток розрахункових методів , що не дозволяють вирішувати завдання вибору раціональної конструкції інструменту на стадії проектування, привели до створення великої номенклатури інструменту одного призначення.
Стрімке зростання інформаційних технологій і ринково орієнтована адаптація виробництва послужили причиною розробки і впровадження систем автоматизованого проектування ( САПР ) і систем наскрізного проектування - виробництва ( CAD / CAM) збірних різальних інструментів , переважна більшість яких орієнтовано на проектування якого виду інструменту, певної його конструкції або елемента конструкції для конкретних виробничих умов, в основі яких використовуються математичні моделі, побудовані із застосуванням різних підходів, внаслідок чого втрачається взаємозв'язок завдань , наступність моделей, даних та рішень, що призводить до зниження якості проектування та отримання суперечливих рішень.
Таким чином, актуальною є задача розробки узагальненої системи проектування збірного ріжучого інструменту, розробленої з використанням системного підходу до формалізації процесів і систем САПР РІС і CAD / CAM РІС, що підкоряється єдиній системі управління модельованим об'єктом , що дозволяє забезпечити концептуальну єдність використовуваних моделей, що враховує фактори випадковості процесу металообробки і нечіткості вихідних даних на проектування, що дозволяє автоматично будувати алгоритм проектування інструменту на основі деяких знань про закони його функціонування, створити єдине середовище для вирішення широкого кола завдань, знизити витрати на розробку і дослідження систем проектування збірних ріжучих інструментів.
Стан і розвиток проектують підсистем САПР РІ
Проектують підсистеми САПР РІ є основою розвитку автоматизованого проектування в інструментальному виробництві . Для автоматизованих систем технологічної підготовки виробництва найбільш переважним є використання апаратних засобів, що дозволяють вести проектування інструменту в діалоговому режимі. У цьому випадку можна спроектувати інструмент оптимальної конструкції.[4]
ПДля ріжучого інструменту будь-якого виду проектують підсистеми розробляються в наступній послідовності: відпрацювання загальних методичних принципів проектування; опис параметрів оброблюваних деталей; складання методики розрахунку параметрів конструктивних елементів різального інструменту (параметрів технологічного процесу та ін); відпрацювання блок- схеми порядку розрахунку ; визначення складів і функцій програмних модулів; розробка програм розрахунку параметрів інструменту ( технологічного процесу та ін.).
Неодмінною умовою створення високоефективної системи проектування є визначення правильної інформаційної структури інструменту. Для того щоб САПР РІ могла функціонувати в режимі розробки оптимальної конструкції, повинні бути розкриті наступні зв'язку:
- Просгранственние, що визначають місце і (послідовність розташування окремих елементів (наприклад, головною і калібрує різальних крайок, хвостовика та ін);
- Функціональні, що визначають величини параметрів (наприклад, параметри конструктивних елементів, що забезпечують достатні міцність і жорсткість);
- Зовнішні, обумовлені характером і умовами взаємодії інструменту з оброблюваної деталлю.
Зовнішні зв'язки визначають формування вихідних даних. Ріжучий інструмент працює в певних умовах, характеризуються режимами різання, застосовуваної МОР, використовуваним обладнанням та ін Число зовнішніх чинників досягає декількох десятків, і тому їх слід згрупувати. Можна виділити три групи таких чинників. Перша характеризує оброблювану деталь і визначає зв'язку безпосередньо між заготівлею н інструментом. До неї належать:
- Хімічні, фізичні та механічні властивості матеріалу деталі;
- Шорсткість оброблюваної поверхні;
- Точність оброблюваної деталі;
- Геометрична форма оброблюваної деталі;
- Метод отримання заготовки деталі;
- Основні розміри і каса деталі;
- Додаткові дані.
Друга група чинників відноситься безпосередньо до самого інструменту.[5] У неї входять:
- Особливості конструкції інструменту;
- Основні розміри інструменту;
- Матеріал інструменту;
- Необхідність перетачіванія;
- Особливості термообробки і методи нанесення зносостійких покриттів на робочу поверхню;
- Додаткові дані.
До третьої групи зовнішніх факторів відносяться умови експлуатації ріжучого інструменту:
- Режими різання;
- Характер виробництва (одиничне, серійне і пр.);
- Вид МОР і спосіб підходу її в зону різанні;
- Регламентація стійкості інструменту;
- Форма і необхідність відводу стружки;
- Вид обладнання, на якому передбачається використання інструменту;
- Додаткові дані.
З наведених вище програмних модулів з точки зору формалізації найбільший інтерес представляє програма « матеріал». При виборі матеріалу різального інструменту неможливо встановити певні математичні залежності. Рішення завдання вибору матеріалу було реалізовано у формі реляційної БД , формування якої описано нижче.
Виявлення зовнішніх і внутрішні зв'язків у осьових інструментів дозволяє враховувати до 20-30 факторів, що впливають на структуру САПР осьових ріжучих інструментів, з яких значна частина впливає на вибір інструментального матеріалу. Але враховувати всі фактори недоцільно, т. к. ускладнюється практичне використання САПР РІ через збільшення необхідних вихідних даних, а також важко врахувати ряд факторів ( застосований-ня МОР, нанесення покриттів тощо) через відсутність експериментальних даних. Тому більш раціонально виділити визначальні чинники.[6]
При виборі матеріалу для осьового інструменту визначальними факторами є:
1) матеріал оброблюваної деталі;
2) характер попередньої підготовки деталі із зазначенням стану поверхні заготовки;
3) діаметр оброблюваного отвору;
4) режим різання;
5) тип виробництва деталей;
6) вид і ступінь автоматизації обладнанні;
7) жорсткість системи СНІД;
8) особливості технологічного процесу одержання заготовки інструменту;
9) наявність даного інструментального матеріалу.
Зазначені дев'ять факторів є необхідними для досить обгрунтованого вибору інструментального матеріалу і частково враховують інші фактори , що не входять в число цих дев'яти. Кожен фактор інваріантний . Зазвичай для вибору пропонується від 10 до 200 марок матеріалів для оброблюваних деталей. Якщо карта вибору складається для конкретного підприємства (галузі), то число марок слід обмежити з урахуванням потреб даного підприємства.
Робота буде вестися в програмі PowerMill . PowerMILL є основним пакетом в програмній лінійці Delcam . PowerMILL призначений для розробки керуючих програм для 3 - осьових і багатоосьових фрезерних верстатів з ЧПУ.
Дана програма добре стикується з багатьма CAD системами завдяки Delcam Exchange, яка відмінно генерує багато форматів в потрібні. Особливо добре працює з пакетним модулем Delcam PowerSHAPE , в системі реалізована концепція Total Modeling, яка дозволяє в єдиному середовищі моделювання комбінувати різні техніки моделювання.
Безпосередньо для нас PowerMILL цікавий для проектування і виготовлення збірних осьових інструментів, за готовими вже 3D моделям, виготовленим в CAD системах.[7] За готовим моделям призначаються потрібні траєкторії інструментів, режими різання і всі необхідні параметри.
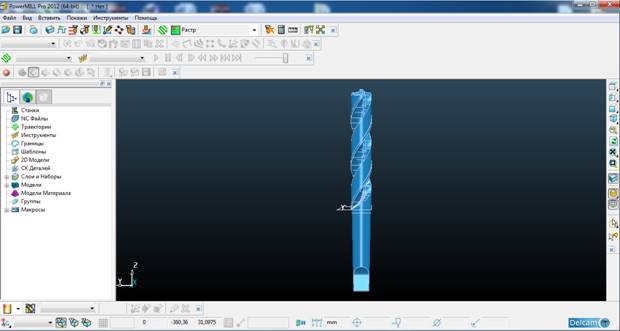
Рисунок 1 – Работа в PowerMILL.
Не можна не відзначити потужні та зручні засоби модіцірованія згенерованих траєкторій. В інших CAM системах поширена наступна ідеологія створення УП: спочатку створюємо всі обмежуючі умови, підходи, відходи, далі - запускаємо розрахунок і отримуємо готову траєкторію. На цьому етапі залишається або прийняти результат , або почати все заново. Система PowerMILL надає кошти для подальшої роботи над траєкторіями.
Спочатку досить задати базові параметри: тип стратегії, крок, а якщо необхідно, то і напрям. Дуже багата база підходів , відходів , врізання і тп. Загалом все залежить від власної фантазії (в розумних межах) і досвіду. Так само зручне створення меж зон обробки , і розрахунок траєкторії в межах надійно застрахований від врізів .Як правило технолог працює з вже усталеною номенклатурою, і найзручніше наповнити власну базу даних реально використовуваними інструментами. Для цього була розроблена база даних у складі PowerMILL Utils. [6-8]Користувач може заповнити базу власними інструментами, задаючи не тільки геометричні розміри інструмента і патрона, а й режими різання стосовно різних матеріалами і верстатів. Незручність цього методу в том , що опис інструменту в PMUtils дещо відрізняється від опису інструменту в PM, як по інтерфейсу так і за формою. Вийде, що PMUtils обмежить ваші можливості за завданням параметрів інструментів.
Однак, при зміні параметрів проектують інструменту доводиться міняти весь текст програми, а це довго і не зручно. Виходом з цього є створення макросів для окремих інструментів і його траєкторій.
Перелік посилань
- www.prorobot.ru/referats/r16/prorobot.ru-16-0010.doc
- Ю.Є. Пєтухов : Деякі напрямки розвитку САПР ріжучого інструменту / / СТIН . 2003 . № 8 .
- Ю. А. Новосьолов : Проблематика автоматизації проектування ріжучих інструментів / / СТIН . 2008 . № 9 .
- Петpушін С.І. , Баканов А.А. , Махов А.В. , Геометричний і силовий аналіз сбоpних свеpл зі змінними багатогранними пластинами / Технологія машинобудування , Вип. 10 ( 64 ) , 2007 . - С. 27 - 30.
- Основи теорії проектування осьових комбінованих інструментів: дис. ... Дтн : 05.03.01 / Малишко Іван Олександрович. - Донецьк , 1995 . - 419
- Проектування комбінованого осьового інструмента : метод . вказівки / сост. Кіселева І.В. - Донецьк : ДонНТУ , 2007 . - 54с
- Основи САПР. (CAD / CAM / CAE . ) / Кунву Лі - 2004 . - СПб. : Пітер . - 560с
- Сахаров Г.Н. Металорізальні інструменти . / Сахаров Г.Н. Арбузов О.Б. , Боровий Ю.Л. , Гречишников В.А. , Кисельов А.С. - М. : Машинобудування , 1989 . - 328 с.
Примітка
При написанні даного реферату магістерська робота ще не завершена. Остаточне завершення: грудень 2014 року. Повний текст роботи та матеріали по темі можуть бути отримані у автора або його керівника після вказаної дати.