Реферат по теме выпускной работы
Содержание
- Введение
- 1. Актуальность темы, цели и задачи
- 2. Анализ способов, обеспечивающих заданные высокие качество и точность обработки поверхностей
- 2.1 Тонкое точение
- 2.2 Шлифование
- 2.3 Метод пластического деформирования
- 2.4 Выводы
- 3. Выбор наиболее рационального способа обработки для получения качественных точных поверхностей по существующим критериям оценки
- 3.1 Критерий «максимум производительности»
- 3.2 Критерий «минимум себестоимости»
- 3.3 Выводы
- Список источников
Введение
Развитие машиностроения на современном этапе невозможно без постоянного повышения производительности труда и улучшения качества выпускаемых изделий. Для решения этой задачи разрабатываются и внедряются различные методы обработки. В моей работе будут рассматриваться тонкое точение, шлифование и метод пластического деформирования при обработке точных поверхностей детали «Вал», выполненной из стали 40Х.
1. Актуальность темы, цели и задачи
В настоящее время требования к качеству поверхностей значительно повысились, что связано с особыми требованиями эксплуатации изделия. Это вызвано значительным шагом вперед всех технологий обработки – появились высокоточные станки и усовершенствовались инструменты, разрабатываются и внедряются новые методы обработки (к таким методам обработки можно отнести метод поверхностного пластического деформирования в гибких гранулированных рабочих средах).
Целью данной работы является изучение вариантов обработки точных поверхностей детали типа «Вал».
Основной задачей является рассмотрение методов обработки точных поверхностей детали «Вал» путем применения тонкого точения, шлифования и пластического деформирования и, в дальнейшем, выбор наиболее выгодного метода обработки.
2. Анализ способов, обеспечивающих заданные высокие качество и точность обработки поверхностей
2.1 Тонкое точение
Этот метод точения широко применяют в авиационной, тракторной и автомобильный промышленностях при обработке цилиндрических и конических поверхностей (наружных и внутренних), а также торцовых поверхностей, уступов и др. Тонкое растачивание, в особенности цветных металлов, по точности и чистоте поверхности превосходит развертывание и не уступает шлифованию [3].
В виду малого сечения снимаемой стружки, небольших сил резания и незначительного нагрева заготовки исключается получение значительного деформированного слоя на обработанной поверхности. Из–за небольших упругих деформаций технологической системы обеспечивается точность обработки по 6–8–му квалитетам, для цветных металлов и сплавов – даже по 5–6–му квалитетам. Шероховатость обработанной поверхности у заготовки из стали и чугуна Rа 2,5…0,63 мкм, из цветных сплавов – Rа 0,32…0,16 мкм [5].
В качестве режущего инструмента для тонкого точения применяют:
- Резцы с пластинками твердого сплава марок ВК2 и ВК3М для тонкого обтачивания и растачивания чугуна; Т30К4 и Т60К6 для тонкого точения и растачивания стали, легких сплавов и цветных металлов.
- Алмазные резцы – для тонкого точения и растачивания легких сплавов, цветных металлов и неметаллических материалов.
Величина углов заточки резцов, оснащенных пластинками твердого сплава, применяемых при тонком точении, приведена в таблице 2.1.
Таблица 2.1. – Углы заточки резцов, оснащенных пластинами твердого сплава, применяемых при тонком точении.
Алмазные резцы значительно долговечнее твердосплавных резцов. Они позволяют работать сотни часов без переточки и переналадки и тем самым обрабатывать большое количество одинаковых деталей с соблюдением точности размеров.
Алмазные резцы изготовляют двух видов:
- с напаянными алмазами (рис. 2.1);
- с механических креплением алмаза в державке (рис. 2.2).
Для резцов использую кристаллы алмазов массой 0,2–0,6 карата (1 карат равен 0,2 г).
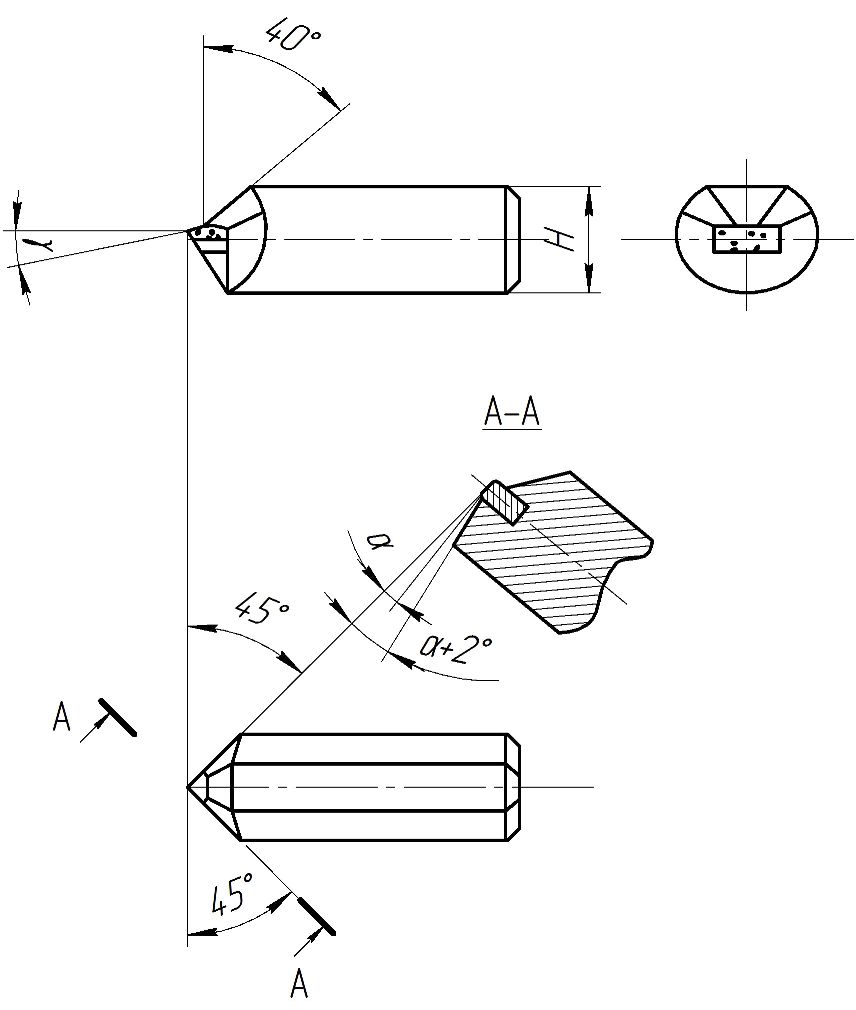
Рисунок 2.1 – Токарный резец с напаянным алмазом.
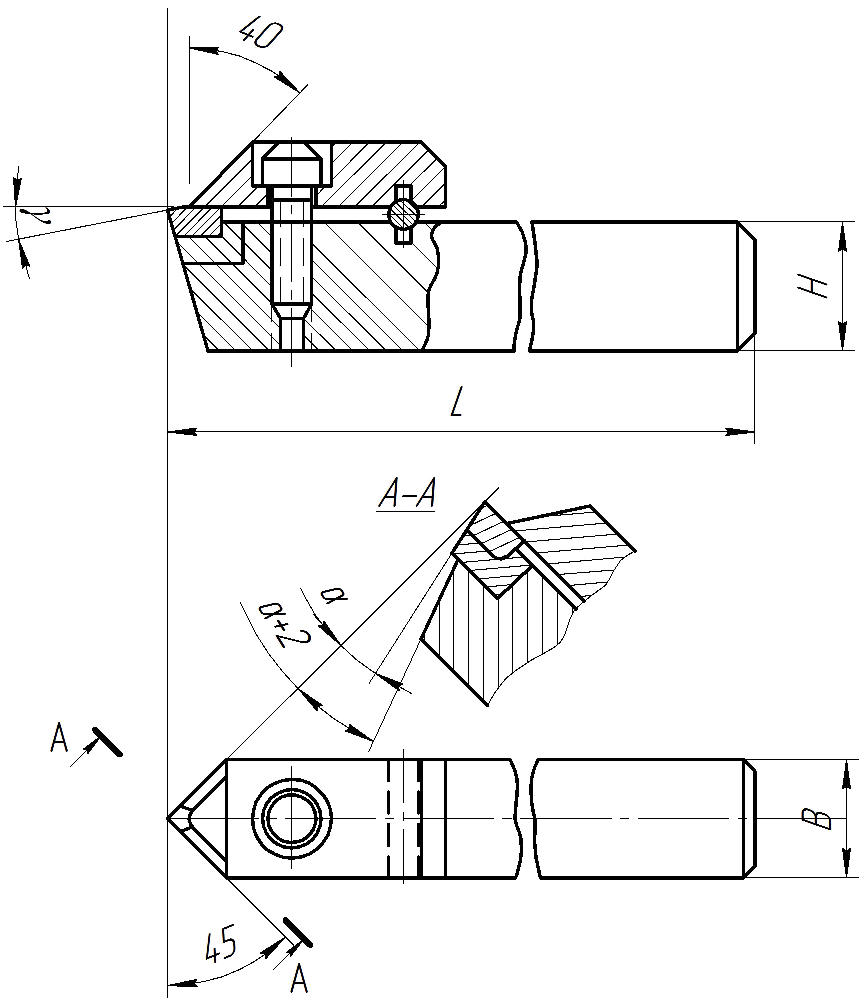
Рисунок 2.2 – Алмазный резец с механическим креплением алмаза.
2.2 Шлифование
Шлифование – один из видов обработки металлов резанием. При шлифовании припуск на обработку снимается абразивными инструментами – шлифовальными кругами. Шлифовальный круг представляет собой пористое тело, состоящее из большого количества мелких зерен. Эти зерна соединены между собой особым веществом, которое называется связкой. Твердые материалы, из которых образованы зерна шлифовального круга, называются абразивными материалами. Процесс шлифования состоит в том, что шлифовальный круг снимает с детали тонкий слой металла (стружку) острыми гранями своих абразивных зерен [7].
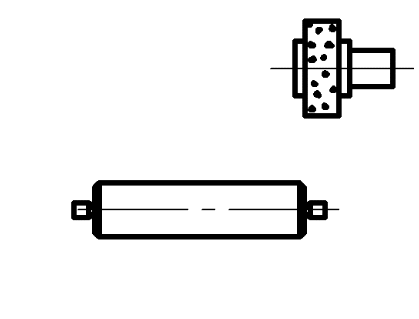
Рисунок 2.3 – Схема круглого наружного шлифования.
Применяются операции чернового, предварительного, окончательного и тонкого шлифования.
Черновое шлифование предусматривает обработку без предварительной токарной операции со снятием увеличенного припуска от 1 мм и более на диаметр. Эту операцию целесообразно выполнять на режимах силового и скоростного шлифования при vкр=50–60 м/с. В отличии от токарной обработки черновое шлифование обеспечивает более высокую точность обработки по 8–9–му квалитету и более низкий параметр шероховатости Ra=2,5–5,0 мкм не требует последующего предварительного шлифования. Его применение целесообразно при наличии точных заготовок или заготовок, имеющих плохую обрабатываемость лезвийным инструментом.
Предварительное шлифование обычно выполняют после токарной обработки с повышенной скоростью резания vкр=40–60 м/с. Предварительное шлифование осуществляют до термообработки для создания базовых поверхностей или в качестве промежуточной операции для подготовки поверхности к окончательной обработке. На операциях предварительного шлифования достигается точность 6–9–му квалитетам и параметр шероховатости поверхности Ra=1,2–2,5 мкм.
Окончательное шлифование позволяет получить точность обработки по 5–6–му квалитету и параметр шероховатости поверхности Ra=0,2–1,2 мкм. Наиболее часто применяют скорость резания vкр=35–40 м/с.
Тонкое шлифование применяют главным образом для получения параметра шероховатости Ra=0,025–0,1 мкм. Оно требует очень хорошей предварительной подготовки, так как снимаемый припуск при тонком шлифовании не превышает 0,05–0,1 мм на диаметр. Применение тонкого шлифования возможно при наличии прецизионного станка и специальных кругов, оно экономически целесообразно лишь в условиях единичного и мелкосерийного производства. В массовом производстве низкие параметры шероховатости поверхности более производительно и надежно получают на суперфинишных и полировальных станках [2].
2.3 Метод пластического деформирования
Поверхностно–пластическое деформирование (ППД) – один из наиболее простых и эффективных технологических путей повышения работоспособности и надёжности изделий машиностроения. В результате ППД повышаются твёрдость и прочность поверхностного слоя, формируются благоприятные остаточные напряжения, уменьшается параметр шероховатости Rа, увеличиваются радиусы закругления вершин неровности, относительная опорная длина профиля и т.п.[1].
Пластическая деформация поверхностного слоя, возникающая под действием усилий деформирующего тела, изменяет его физико–механические свойства и структуру. Степень пластической деформации и ее последствия зависят от характера деформации, ее режима, исходного состояния материала, макро– и микроструктуры, шероховатости поверхности, формы, размеров детали и ряда других факторов.
Изучение природы и закономерностей фазовых и структурных превращений, происходящих в материале детали под действием ППД, является необходимой предпосылкой для создания новых и оптимизации существующих технологических процессов и оборудования. Знание этих закономерностей позволяет расширить их технологические возможности и вскрыть внутренние резервы [6].
Формирование поверхностного слоя с заданными свойствами должно обеспечиваться технологией упрочнения. Наиболее широко применяют способы обкатывания и раскатывания шариковыми и роликовыми обкатниками наружных и внутренних цилиндрических, плоских и фасонных поверхностей. Цилиндрические наружные, внутренние, фасонные поверхности обрабатываются, как правило, на токарных, револьверных, сверлильных и других станках; плоские поверхности – на строгальных, фрезерных станках. Примеры обкатывания и раскатывания поверхностей роликами приведены на рис. 2.3. Обычно этими способами обрабатывают достаточно жёсткие детали из стали, чугуна и цветных сплавов. На рисунке 2.3., а показана схема обработки цилиндрических наружных и внутренних поверхностей.
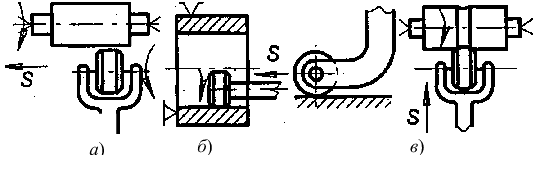
Рисунок 2.4 – Схемы обработки роликом:а – наружных и внутренних цилиндрических поверхностей;б – плоских поверхностей; в – фасонных поверхностей.
Качество обрабатываемой поверхности при обкатывании роликами и шариками в значительной степени зависит от режимов деформирования: силы обкатывания (или давления на ролик и шарик), подачи, скорости, числа рабочих ходов и применяемой смазочно–охлаждающей жидкости. До обкатывания и раскатывания заготовки обрабатывают точением, шлифованием и другими способами, обеспечивающими точность, по 7–9–му квалитету. Припуск на обработку обычно рекомендуется выбирать равным 0,005...0,02 мм.
Пластическое поверхностное деформирование может быть отделочно–упрочняющей операцией (улучшает шероховатость поверхности и упрочняет поверхностный слой), отделочно–упрочняющей и калибрующей операцией (кроме сказанного выше, повышает точность обработки); отделочно–калибрующей операцией (упрочнения не происходит).
Наряду с изложенными выше способами широко применяют центробежное (инерционное) упрочнение. При этом используется центробежная сила шариков (роликов), свободно сидящих в радиальных отверстиях быстровращающегося диска. Схема центробежной обработки поверхности шариками показана на рис. 2.3. Шарики 2 при вращении диска 3 смещаются в радиальном направлении нанося многочисленные удары по заготовке 1 и пластически деформируя поверхность. Для получения поверхностей с минимальным параметром шероховатости и упрочнённым слоем небольшой глубины применяют алмазное выглаживание. Процесс аналогичен обкатыванию, но инструментом служит кристалл алмаза, находящийся в специальной державке.
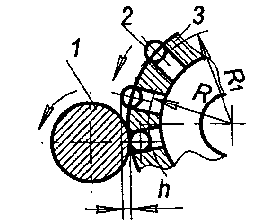
Рисунок 2.5 – Схема центробежной обкатки.
К методам пластического деформирования, упрочняющим поверхности деталей, относятся: обработка дробью, гидровиброударная обработка; электромагнитное, ультразвуковое упрочнение и др.[1].
2.4 Выводы
Выше были рассмотрены способы обработки, которые обеспечивают высокое качество и точность обработанных поверхностей. Сложность явлений, сопровождающих процессы размерно–чистовой обработки лезвийным или деформирующим инструментом, и многообразие факторов, влияющих на образование неровностей, обусловливают отклонение их форм и размеров от геометрически правильных.
3. Выбор наиболее рационального способа обработки для получения качественных точных поверхностей по существующим критериям оценки
Любой технологический процесс должен быть экономичным. При проектировании технологического процесса могут быть установлены такие режимы резания, которые позволят получить очень высокую производительность труда. При этом, однако, стойкость инструмента будет низкой, что вызовет большой расход инструмента. Для обеспечения высокой эффективности производства необходимо технологические факторы процесса резания рассмотреть с экономической точки зрения.
3.1 Критерий «максимум производительности»
Для обеспечения максимальной производительности штучное время обработки должно быть минимальным [4].
Для операции точения, выполняемого за один проход, штучное время определяется.

где TL – суммарное время простоя, приходящееся на одну деталь;
Т – стойкость инструмента;
s – подача;
1/n, 1/n1 – показатели степени при скорости и подаче;
t – глубина резания;
v – скорость резания;
l – длина прохода инструмента;
D – диаметр заготовки;
λ=1/πD
A=K·b-1/n2
Условие максимальной производительности можно записать в следующем виде:
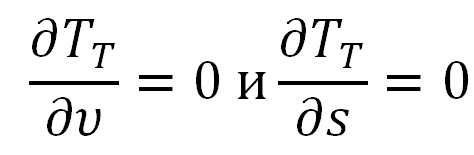
или
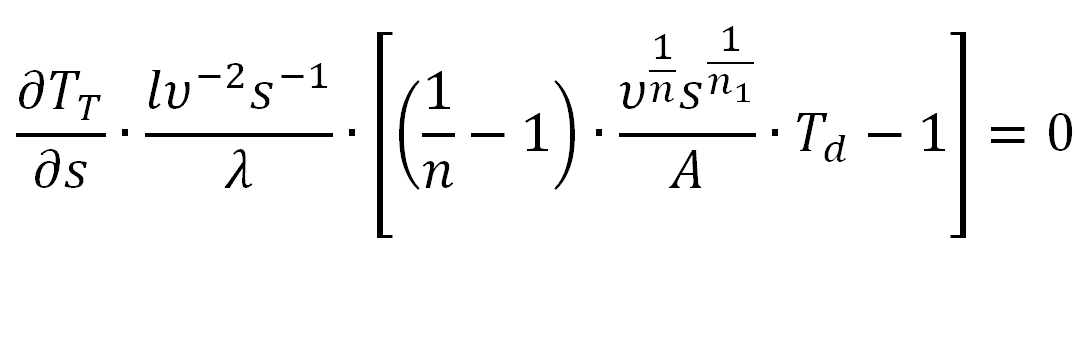


Т.е.

Уравнения 3.1 и 3.2 не могут быть справедливы одновременно и, следовательно, минимум штучного времени или максимум производительности не является единственным. (рис. 3.1).
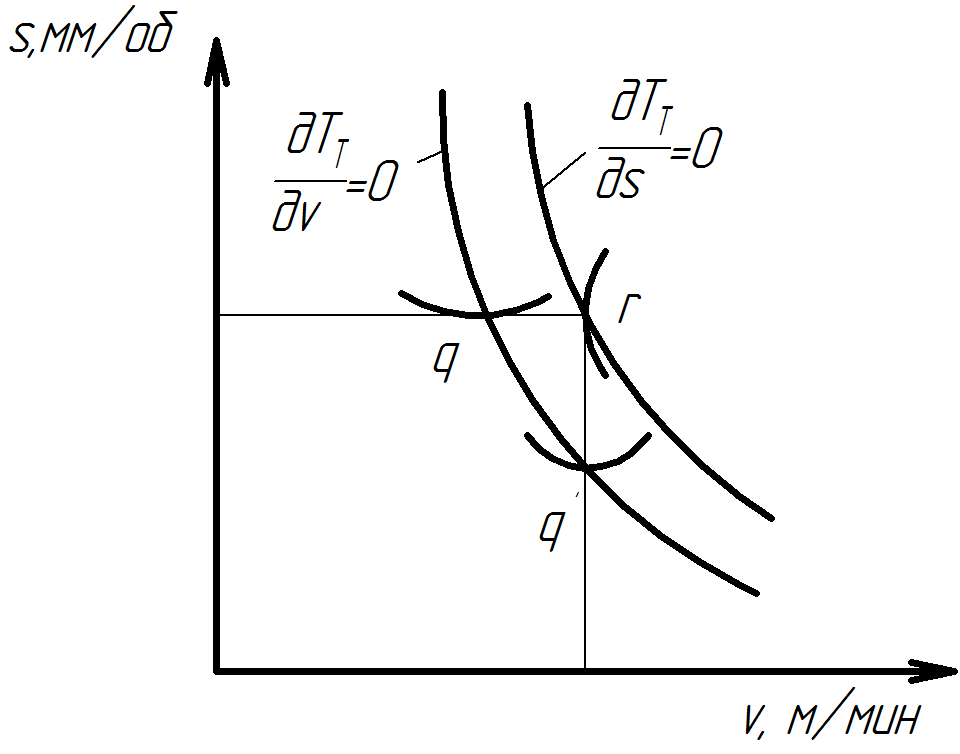
Рисунок 3.1 – Зависимость подачи s от скорости резания v для случая максимума производительности и отсутствия ограничений.
Наибольшая производительность будет достигнут при максимально допустимой подаче и соответствующей скорости резания, определенной из уравнения 3.2.
3.2 Критерий «минимум себестоимости»
Себестоимость обработки детали складывается из нескольких статей. Для простоты рассмотрим обработку одним инструментом.
1 Непроизводительные затраты С, приходящиеся на одну деталь, включают стоимость закрепления и снятия одной детали, стоимость простоя оборудования. Непроизводительные затраты подсчитываются по формуле
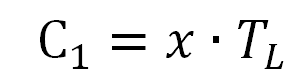
где х – стоимость 1 мин;
TL – суммарное время простоя, приходящееся на одну деталь.
2 Стоимость машинного времени обработки C2 определяется как произведение стоимости 1 мин машинного времени х на машинное время обработки Tc

3 Стоимость времени на смену инструмента C3 определяется как произведение стоимости 1 мин на время смены инструмента, приходящиеся на одну деталь
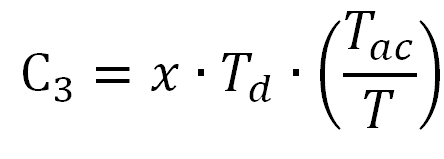
где Td – время смены инструмента;
Tac – действительное время обработки одной детали;
Т – стойкость инструмента.
4 Стоимость инструмента, отнесенная к одной детали C4, равна стоимости инструмента, приходящейся на режущее лезвие у, умноженное на число режущих лезвий, используемых при обработки данной детали

5 Стоимость инструмента, приходящаяся на одно лезвие, зависит от вида инструмента. Для напайного инструмента эта величина равна:

В себестоимость могут быть включены и другие затраты, такие, как затраты на охлаждающую жидкость, на разработку инструмента, на обрабатываемый материал, хотя перечисленные затраты, кроме затрат на обрабатываемый материал, могут быть включены в накладные расходы. Таким образом, себестоимость детали равняется

где C5 – стоимость материала.
Исключая стоимость материала, имеем
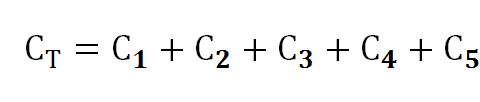
Рассматривая уравнение 3.3, видим, что себестоимость детали может быть снижена путем сокращения времени закрепления и снятия детали, времени простоя и времени смены инструмента. Для этого могут быть использованы как технические, так и организационные методы. Совершенствование материала инструмента и заточки повышает стойкость инструмента, уменьшает количество смен инструмента и стоимость заточки, приходящуюся на одну деталь, тем самым снижая себестоимость детали. Износ режущего инструмента может быть также снижен путем изменения свойств обрабатываемого материала. Влияние скорости резания на себестоимость детали представлено на рис.3.2,а. Изменение штучного времени (или производительность) в зависимости от скорости резания показано на рис. 3.2,б, [4].

Рис.3.2 – Зависимость себестоимости (С) и штучного времени TT обработки детали от скорости резания v: 1 – затраты на обработку C2, 2 – затраты на инструмент и его смену (C3+C4), 3 – общие затраты (себестоимость) С, 4 – время на смену инструмента (Td·Tac/Tc), 5 – полное (штучное) время, 6 – машинное время.
3.3 Выводы
При выборе наиболее экономичного способа обработки, использовались 2 критерия оценки: «минимум себестоимости» и «максимум производительности». Выбор критерия зависит от заданных требований на производстве. На данный момент на производстве преимущественно пытаются обеспечить требуемую производительность при минимуме себестоимости.
Список источников
- Технология машиностроения: курс лекций / А.Г. Ткачёв, И.Н. Шубин. – Тамбов: Изд-во Тамб. гос. техн.ун-та, 2009. – 164 с. – 100 экз. – ISBN 978-5-8265-0857-2.
- Наерман М.С. Справочник молодого шлифовщика. – М.: Высш. шк., 1985. – 207 с., ил. – (Профтехобразование).
- Тонкое точение. [Электронный ресурс]. – Режим доступа:http://machinetools.aggress.ru/...
- Армарего И. Дж. А., Браун Р.Х. Обработка металлов резанием. Пер. с англ. В.А. Пастунова. М., «Машиностроение», 1977. 325с.
- Точение.[Электронный ресурс]. – Режим доступа:http://dlja-mashinostroitelja...
- Бойко Н.И. Ресурсосберегающие технологии повышения качества поверхностных слоев деталей машин: Учебное пособие для вузов ж.-д. транспорта.- М.: Маршрут, 2006. – 198 с.
- Шлифование металлов. [Электронный ресурс]. – Режим доступа:http://www.markmet.ru...