Abstract
Contents
- Introduction
- 1. Topic relevance
- 2. Purpose, objectives, novelty and practical value of the research
- 3. Analytical review
- 4. Justification and line of work
- 5. Description of the developed mechanism
- 6. Developed mechanism operating principle
- References
Introduction
Directional drilling technology and technique, as well as elaborate methodology of borehole trajectories’ design and adjustment are among the means of geological survey improvement. These means provide the decrease of drilling amount and increase the informational content which borehole possess at the same time.
The use of directional drilling of unilateral and multilateral wells allows reducing of the drilling works amount and its terms. Additionally, it can lower the costs of searching, surveying and further development of mineral deposits.
Drilling of deviating holes requires not only activities related to deepening of the shaft in specified direction, but also a variety of additional works. These include orientation of whipstocks using peculiar technical devices – orientators.
Given study is devoted to development of self-orienting whipstock for the conditions of directional well drilling.
1. Topic relevance
Directional drilling of boreholes provides better geological data quality, less expenses, and also complication control upon geological survey of mineral deposits. The technology of borehole directional drilling should provide reduction of time-consuming and usage of tangible assets and increase efficiency of deposit operation.
Usage of self-orienting whipstock systems is sufficiently relevant, because setup and orientation processes are simple, orientation is carried out in automated or semi-automated remote mode, and the amount of technological operations and means which are used for creation of specific borehole direction reduces.
2. Purpose, objectives, novelty and practical value of the research
Research purpose: to develop a principle system of boring head self-orienting in directional wells and the design of remotely controlled orientator.
Research objectives:
- Analyze already existing ways of orientation and structures for boring head orientation.
- Investigate self-orienting unit operation of ball-type boring head.
- Design versatile self-orienting device for orientation of diverting heads in angle holes.
Scientific novelty:
- The technique of structure parameters calculation for ball-type self-orienting unit is suggested.
- For steady head operation weight and geometric parameters of self-orienting unit are set.
- The range of stable self-orienting device operation is set by the zenith angle of directional well.
Practical value:
- It is expected that efficiency of boring head orientation will increase, because unit’s remote work principle reduces additional time consumption.
- The system of repeated orientation is stipulated, which does not require boring head recovery from a well.
- A set of design documentation for versatile self-orienting device is developed.
3. Analytical review
Self-orienting systems are intended for automatic turning of device body under the weight of orientator. Such systems are implemented in a self-orienting attachment OP, AFOR orientator and “Kedr” orientation unit.
Self-orienting principle is based on capability of eccentrically suspended mass to take specific position in directional well. Taking this into account, two types of devices can be implemented: first one presupposes the placement of eccentric mass into whipstock while in the second type a special unbalanced orientator attachment is connected to the whipstock. The simplest device of first type is deflecting wedge with a blank welded inside, which is loosely discarded into the well. It is assumed that eccentrically fixed weight will orientate tip of the wedge in the desired direction relative to the apsidal plane. The reliability of such device is not high.
It is more efficient to use unbalanced device connected to the whipstock mechanism and loosely suspended by bearings on a drill pipe which serves as a roller, as in whipstock DD-1-TPI, or the usage of peculiar unbalanced attachment OP-3 or AFOR-1, designed by ZabSRI. It should be noted that this self-orienting method is less laborious and very promising.
Attachment OP–3 (Fig. 1) is used for orientation of TZ type whipstocks, and it is also can be used with other types of whipstocks after applying some structure changes. Attachment OP–3 consists of setting unit, unbalance and suspension unit. Suspension unit is intended for setting up whipstock relative to the unbalance action plane and consists of adapter 1, which is connected to the stator of TZ whipstock, clamping nut 2 and adjusting sleeve 3. Lead unbalance weight 5 is placed in the body 4, which is a tube with a longitudinal cut.
Bush 6 enables torque transfer and feeding of washing fluid on to a face. In the bottom part it is connected to the whipstock rotor and in the top part it is connected to the lower adapter 7 of the suspension unit. The later includes body 8, bearing 9, support shaft 10 and upper adaptor 11. At the conjugated ends of the body 8 and adaptor 11 are cams which provide torque transfer in the closed position.
Operating procedure of attachment OP-3 and TZ whipstock is as follows. Upper rotor and stator adaptors are being removed from the whipstock and then the attachment is being connected to the whipstock. Then the system setup is carried out. To do so the nut 2 is loosened and required angle between whipstock action plane and unbalance suspension plane is being set. After that the cam 2 is tightened back and the whipstock is dropped into the well. Whipstock and orientator are loosely suspended on a bearing.
Head is reciprocated prior to the drilling, and under the force of the unbalance the whipstock sets at required angle. When setting the whipstock on the face, cams on the adaptor 11 and body 8 of the attachment OP-3 are closing and provide torque transfer from drilling column to the rock cutting tool.
In the process of borehole deflection the second orientation of whipstock is possible. Orientation attachment OP-3 can be used in the boreholes with a zenith angle not less than 3°.
This system has such advantages as orientation on the automatic mode, and also quite simple setup technology. It is important that load weight shouldn’t exceed orientator body weight. There is also a limitation for zenith angle in the range of 5° to 60°.
Whipstock orientator of continuous operation Kedr
(Fig. 2) includes skirt 1 with a groove 2 and a standard end surface 3. Other principal orientator elements are ball 4 and a basket 5. Basket is situated in the end of splined connector 8 in a form of sockets placed on the perimeter of outer edge of splined connector 8 for the placement of ball 4. Shaft rotor 6 of the whipstock comes through the skirt 1 and doesn’t have any connection to it. Shaft 6 is made composite, and the components are connected via splined connector 8 (Kedr
has two splined connectors for the increase of shaft stroke). Whipstock body-stator 7 is connected to the skirt 1. On the shaft 6 under the splined connector 8 the return spring 9 is placed.
Whipstock orientation starts with the whipstock placement on the face of directional hole under pressure. With the downward movement and shortening of shaft 6, by clamping of splined connector 8, spring 9 is being compressed, ball 4 frees up, orientates and by the force of gravity falls into lower socket of basket 5. Whipstock of continuous operation placement on the face is followed by brief increase (adjacent circulation holes are open), and then decrease of wahsing fluid pressure (adjacent circulation holes match), which can be observed on the drilling pump pressure gauge.
For the orientation the whipstock is unloaded and uplifted above the face. Upon unload the basket 5 with a ball put into it’s socket 4 under pressure of compressed spring 9 moves up and interacts with a helical surface 3 of the skirt 1.
Under the effect of the ball 4, skirt 1 turns along with the whipstock body.
The turn of skirt 1 and body 7 of whipstock continues until the position of ball 4 matches the position of the socket 2 of the skirt 1. In this case ball 4 falls into the socket 2. Specific upward movement of shaft 6 occurs, which leads to matching of slots in shaft 6 with other slots of whipstock circulation system. As a result upon orientation first there is an increase, and then decrease of washing fluid pressure, which is percieved as a signal of whipstock orientation.
In the orientation process the required orientation angle of whipstock can be set not in one, but in two, three or more operations of setting and detachment from the face until the signal of orientation is received.
Significant advantage of the orientator is the ability of repeated orientation already at the stage of drilling the well in specified direction. Repeated orientation significantly increases the precision of inclination, especially in the long curvature sections.
Automatic face orientator AFOR-57 (Fig. 3) is designed for orientation of whipstocks of any type upon directional drilling of wells with 59 and 76 mm of diameter and with zenith angles from 3° up to 60°.
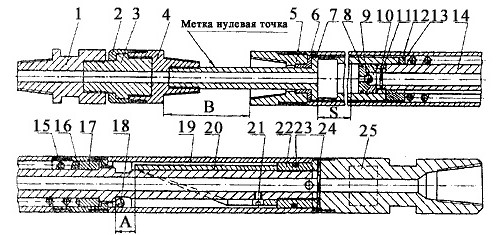
Figure 3 – Automatic face orientator AFOR-57
1 – adapter; 2 – nut; 3 – hub; 4 – semi-coupling; 5 – upper semi-coupling; 6, 17 – bearings; 7 – splined shaft; 8 – sealing ring; 9 – valve ball; 10 – valve; 11 – valve pin; 12 – bevel shell; 13 – dowel pin; 14 – shaft; 15 – spring; 16 – basket; 18 – ball; 19 – body; 20 – skirt; 21 – retaining device; 22 – piston; 23 – sealing; 24 – hinge pin; 25 – upper adapter.
This orientator is a hydromechanical analogue of deflecting complex Kedr
mechanical orientator, and to some extent has a simillar design as OGSh orientator.
It consists of three functional devices: setting unit in the form of dismountable splined connector, controlling device in a form of an interconnected holes system and orientation device in a form of screwing mechanism with a ball that is set loosely in the apsidal plane. All devices are arranged into two assembly units – setting unit and control-orienting unit.
Setting unit consists of an adapter 1, nut 2, hub 3 and semi-coupling 4.
Control-orienting unit consists of rotor and stator parts. Rotor includes splined shaft 7, valve 10 with a ball 9, shaft 14, spring 15, skirt 20 with helical surface and orientation socket. Stator includes upped semi-coupling 5, bevel shell 12, basket 16, which has sockets on it’s end surface for placing ball 18, body 19, adaptor 25 with installed into it hinge pin 24, which serves for blocking rotor and stator.
Operation principle is as follows: upon lowering into directional hole the ball 18 sets in the apsidal plane of the hole. On feeding of washing liquid the valve 10 locks, and in the plane under the piston 22 hydraulic pressure is being built. Piston 22 with the shaft 14 connected to it move down, and the ball 18 places and locks in one of the sockets of the basket 16.
Upon further movement of shaft 14 down the skirt 20 hits ball 18 with its helical surface and provides the turn of shaft 14, which is transferred via dowel pin 13 to the setting unit and a whipstock attached to it. Next the shaft 14 continues downward movement until radial holes match circular groove of the shaft 7. At the same time the pressure build-up stops and washing fluid starts to circulate in the well. This moment is monitored via drilling pump pressure gauge and indicates the completion of orientation process.
Automatic face orientator AFOR-57 has such advantages: orientation in automatic mode; high turning point transfer capabilities in virtue of rolling; reasonably easy setup technology. The disatvantages include a limitation for zenith angle (3–60°) and possible setting distortion due to fixed position of the basket.
4. Justification and line of work
Based on analytical review on this topic the development of deflecting boring head self-orienting system will be done. The prototype for mechanism enchancement is automatic face orientator AFOR-57.
Development process sipulates improvement of mechanism operation principle by changing some units of mechanism, changing structural components. New design as compared to the prototype will have a different placing of ball in the aspidal plane principle with a help of specific basket, and also the fluid outlet principle will be different. Additionally, operation of ball-type self-orienting unit will be studied and the technique of it’s structural parameters calculation will be developed.
5. Description of the developed mechanism
Orientator (fig. 4) consists of adapter 1 for connecting with drilling shaft and adapter 2 for connectung with the whipstock. Mechanism includes skirt 7 connected to the shaft 21 via hinge pin 9. Skirt 7 is threaded to the piston 6. Ball 10 is being loosely rolled between shaft 21 and a body 3. In coupling 4 groove 11 is located for the ball 10. Inner coupling ledge 4 is in contact with piston 13, which rests against helical spring 14. Inside the shaft 21 ball 16 overlaps inner cavity of the shaft. Shaft 19 is connected to the shaft 15 via coupling 17, which forms cavity 23 for the fluid output through holes 22 on shaft 21. Shaft 19 is installed on the bearings 18. Shaft 20 has a splined stroke.
6. Developed mechanism operating principle
Orientator connects to the whipstock and being dropped on the pipes column to the hole and being hanged above the face. Upon dropping of orientator the ball sets in apsidal plane of the well. After that the drilling pump is being started and washing fluid enters shaft cavity 21 (Fig. 4). Pressure increases, which leads to movement of piston 6, skirt 7 and the shaft 21. The later moves down and allows the ball 10 which is placed in the groove to hit the sockets of basket 11. Skirt continue to move down, approaching the ball, turns simultaneously with the shaft 21, and by that the required angle of well orientation is achieved. Shaft 21 continues to move and pushes piston 13 and spring 14. Bottom part of the shaft 21 moves and enters cavity 23. Through the holes 22 the washing fluid enters cavity 23. Pressure gauge shows the drop of pressure, which is an indication of orientation process completion.
After orientation process is finished, the whipstock with the orientator are being placed on the face, orientator moves down. Then threads of adaptor 2 and semi-coupling 24 are being connected.
Upon drilling torque transfers through adapter 1, orientator body 3 and adaptor 2 to the whipstock.
Список источников
- Сулакшин С.С. Направленное бурение. – М.: Недра, 1987. – 272 с.
- Зиненко В.П. Направленное бурение. – М.: Недра, 1990. – 151 с.
- Калинин А.Г., Григорян Н.А., Султанов Б.З. Бурение наклонных скважин: Справочник/Под ред. А.Г. Калинина. – М.: Недра, 1990. – 348 с.
- Калинин А.Г. Искривление скважин. – М.: Недра,1987. – 304 с.
- Морозов Ю.Т. Методика и техника направленного бурения на твёрдые полезные ископаемые. – Л.: Недра, 1987. – 221 с.
- Сулакшин С.С. Закономерности искривления и направленное бурение геологоразведочных скважин. – М.: Недра, 1966, – 285 с.
- Сулакшин С.С., Калинин А.Г., Спиридонов Б. И. Техника и технология направленного бурения скважин. – М.: Недра, 1967, 216 с.
- Шитихин В.В. Технические средства для направленного бурения скважин малого диаметра. – Л.: Недра, 1978. – 112 с.
- Курсове та дипломне проектування бурових робіт: Навчальний посібник/О.І. Калініченко, О.С. Юшков, Л.М. Івачов та інші – Донецьк: ДонНТУ, 1998. – 153 с.
- Юшков А.С., Серик Е.Л. Бурение геологоразведочных скважин. – М.: Недра, 1976. – 286 с.
- Пилипец В. И. Бурение скважин и добыча полезных ископаемых: В 2-х томах. Том 1. Учебник для вузов. – Донецк, ООО «Типография «Новый мир» 2010. – 760с.