Abstract
Contents
- Introduction
- 1 Mathematical model of evaporation potassium hydroxide
- 2 Block diagram of the ACS value of the initial solution flows and the heating steam
- 3 Block diagram ACS solution concentration of potassium hydroxide
- Conclusion
- References
Introduction
Chemical industry allows to synthesize materials that are not in the nature, use them to create all kinds of machines and equipment for the construction of dwellings and the production of consumer goods. Therefore, the chemical industry in the world is growing rapidly.
The chemical industry produces synthetic rubber, plastics, synthetic fibers, artificial fuels, dyes, drugs and more.
Evaporation – the process of concentrating solutions by removing volatile substances volatile liquid solvent vapor.
This process is widespread (in the chemical, food, metallurgical and other areas) because of the fact that many substances obtained as a dilute aqueous solutions and for further manufacturing steps are necessary in concentrated form. Also, due to the concentration of solution decreases the volume and reduced the cost of their transportation.
In the process of evaporation is a partial removal of the solvent from the total solution at its boiling point. This is a fundamental difference between evaporation from evaporation, which occurs on the surface of the solution at any temperatures below the boiling point. In some cases evaporated solution is subjected to crystallization in the next evaporators specifically designed for this purpose.
In practice, often as a warming agent during evaporation using water vapor, which is called the heating or primary. The primary steam is obtained from steam or exhaust steam. Steam, which is formed by evaporation boiling solution, called secondary. The heat needed to support the process usually lead through the wall. The process is performed under vacuum at elevated and atmospheric pressure. Selection pressure is largely dependent on the properties and evaporating the possibility of using secondary steam heat.
1 Mathematical model of evaporation potassium hydroxide
Evaporator being bulky apparatus as an object of regulation, the channel flow of the heating steam – the concentration of the resulting solution
has considerable inertia. The dynamics of main evaporator control channel concentration resulting solution – consumption of the heating steam
can describe the linear differential equation of ideal mixing provided that the fluid level in the apparatus constant, ie stabilization of the condition of the material balance. Changing the concentration of potassium hydroxide output ΔQ volume V of the system by changing the concentration in the initial solution ΔQ0 must change eliminated steam consumption ΔF2 [1–3].
Adjusting the concentration of potassium hydroxide is carried out by changing the heating steam flow F2 through the control valve that regulates a range of 0...100%. On the drive (actuator) control valve receives a signal setting the valve opening in the form of a normalized current signal 4...20 mA. The maximum speed of the rod is 25 %/s.
According to its dynamic properties of the actuator is an aperiodic link of the first order with a time constant of 1 s. The pipeline from the valve prior to entering the evaporator simulated inertia component of the first order with a transfer coefficient K = 3/100 and the constant time T = 2 [4]. The input signal level shall be given as a percentage of the stroke position stroke Regulatory Body (RB).
The scheme simulation of model actuator (MA) with the regulatory body (RB) and the pipeline to the evaporator is shown in Fig. 1

Figure 1 – The scheme simulation of the model MA and RB, pipeline to the evaporator
2 The scheme simulation of the ACS value of the initial solution flows and the heating steam
In accordance with ideology selected management combined ACS stabilize the concentration of potassium hydroxide solution consists of two units [5–8]. Internal circuit – a circuit stabilize the cost source solution – the heating steam
. It regulates the heating steam flow F2 at a certain ratio of stock solution flow F1 (so-called flow ratio controller). The outer contour of stabilizing the concentration of KOH solution obtained by changing the steam flow F2 changes the task of the regulator and its value depending on the concentration of KOH output evaporator.
Construct and analyze dynamic flow ratio regulator stock solution and the heating steam. The scheme simulation of the ACS value streams will be built according to the principle rejected.
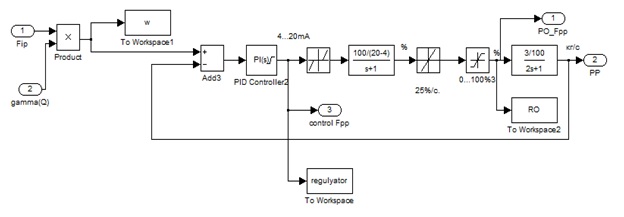
Figure 2 – The scheme simulation of the ACS value output streams solution and the heating steam
From the structure of the ACS is seen that the output value of the regulator limited range of its possible output 4...20 mA, and is a unit of the dead zone in the range -4....4 mA, resulting from the lower limit of the range output controller. Following is MA model, RB and pipeline discussed above
The main objective synthesis of the ACS is to choose the law regulating and determining tuning parameters of the regulator. With the practice of value flow regulators accept PI control law.
The parameters setting, very close to optimal, may be obtained from the study of the dynamics of a closed system. As a method of controller tuning parameters choose the method of automatic configuration block PID-control simulation package Matlab, since the methods of automatic optimization is a powerful tool of modern industrial controllers. Automatic configuration method based on three stages: identifying the object model, determining parameters and controller tuning parameters.
Choosing the aforementioned method due to the fact that the regulator parameters defined by existing and widespread methods of Ziegler and Nichols MP and CHR (Chien, Hrones and Reswick) then adjusted manually or automatically in the analysis of the dynamics of ACS.
When setting the regulator focuses on working off set point signal changes as the heating circuit control the flow of steam in relation to the expenditure of the initial solution is an internal circuit ACS concentration of potassium hydroxide. Thus, given the restrictions on the controller output signal 4...20 mA and speed RO 25 %/c, settings PI regulator have the following meanings: Kp = 0, Ku = 0.67 providing performance equal to 16.6 sec. In animation figure 1 shows a graph of the transient response of the regulator setting value, and number 2 in the heating steam consumption schedule by changing the cost of the initial solution of 0.6 kg/s to 0.5 kg/s.
Transfer characteristic cost the heating steam is aperiodic nature of the overshoot 8% regulation time 473 s. These figures are satisfactory for the internal circuit.
In animation figure 3 and in figure 4 shows graphs of transient characteristics of the output control signal PI regulator, and move the regulator.
From these graphs it follows that the regulator does not exceed the limit zone 4...20 mA required the heating steam consumption of 2.4 kg/s is provided by the valve at 80%.
3 The scheme simulation of the ACS solution concentration of potassium hydroxide
The outer contour of stabilizing the concentration of KOH solution obtained by changing the steam flow F2 and corrects the problem regulator value depending on the concentration of KOH output evaporator [9–11].
Powered ACS performance requirements of the following concentrations:
- aperiodic transient nature of acceptable overshoot 5...10%;
- the installation (adjustment) 20 minutes;
- Time working outside disturbances 8-10 minutes.
Exit the concentration of potassium hydroxide solution at 40% setpoint setting requires an external regulator for concentration. Since the channel management concentration – the heating steam consumption
has great inertia [12, 13], and based on the practice must select PID control law.
To calculate the initial values of the parameters of the regulator concentration method was used by CHR response to external disturbances. Initial estimates following: Kp = -0.026, Ku = -6e-4, Kd = -2.1. However, this sense of differential component of the controller output beyond its limits output and therefore data initial values have been optimized through automatic adjustment method.
The simulation results were obtained for the structural scheme ACS. Subsystem ACS value flows realized on Fig. 3.
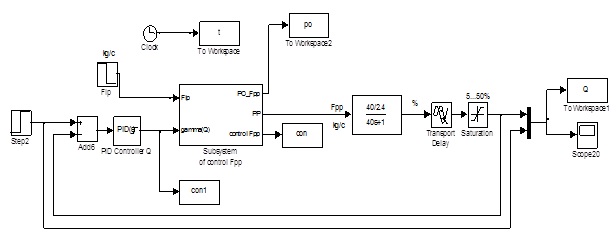
Figure 3 – The scheme simulation of the ACS solution concentration of potassium hydroxide
The results provide automatic configuration specified requirements as transient. Schedule transient response of the regulator, schedule transient response KOH concentration and timetable of the transition process controller setpoint value when developing a concentration of 40% given in animation figures 5, 6 and 7 respectively.
Analysis of transient response on the concentration of the solution of potassium hydroxide output shows that the regulator out the external disturbances to the system for 9 minutes without departing from the acceptable range of variation in concentration that meets the requirements.
Transfer characteristic on the concentration of the solution is aperiodic nature of the overshoot 6% regulation time 527 s.
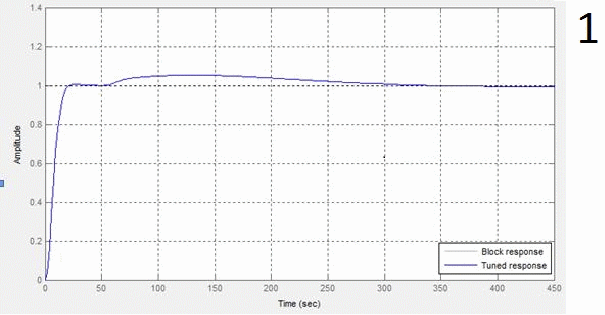
1 – window settings block PID-control,
2 – figure transition process steam consumption by changing the cost of the initial solution of 0.6 kg/s to 0.5 kg/s,
3 – schedule transient output regulator by changing the cost of the initial solution of 0.6 kg/s to 0.5 kg/s,
4 – schedule of progress of the transition process of the regulatory body when changing spending stock solution of 0.6 kg/s to 0.5 kg/s,
5 – window settings block PID-control regulator concentration,
6 – graph transient response KOH concentration,
7 – figure transition process controller setpoint value when developing a concentration of 40%
Figure 4 – Obtained graphics of the transition process from modeling
(animation: 7 frames, 5 cycles of repeat, 106 kilobytes)
Conclusion
- The mathematical model of potassium hydroxide evaporation under the linear differential equation.
- Composite CAP complex model. The synthesis of automatic regulation of evaporation of a solution of potassium hydroxide. As laws regulating the channel management
concentration – consumption of the heating steam
is selected PID-law, and the channelflow source solution – consumption of the heating steam
PI-law. Options regulators were determined by Chien, Hrones and Reswick and optimized by means of automatically block PID-control. The simulation results show the performance of the CAP and the ability of the developed systems, basic indicators which are mainly:
- no static error;
- regulation time – about 20 minutes;
- aperiodic nature of transients with the overshoot permissible;
- satisfactory working time disturbances;
- compensation disturbances due selected by the management principle rejected.
This master's work is not completed yet. Final completion: December 2015. The full text of the work and materials on the topic can be obtained from the author or his head after this date.
References
- Кафаров В. В., Глебов М. Б. Математическое моделирование основных процессов химических производств: Учебн. пособие для вузов. – М.: Высш. шк., 1991. – 400 с.
- Курко В. И. Методы исследования процесса выпаривания химических растворов. – М.: Химическая промышленность, 1977. – 191 с.
- Борисов Г. С., Брыков В. П., Дытнерский Ю. И. Основные процессы и аппараты химической технологии: Пособие по проектированию / Под ред. Дытнерского Ю. И., 2-е изд., перераб. и дополн. – М.: Химия, 1991. – 496 с.
- Дытнерский Ю. И. Процессы и аппараты химической технологии: Учебник для вузов. Изд. 2-е В 2-х кн.. Часть 2. Массообменные процессы и аппараты. – М.: Химия, 1995. – 368 с.: ил.
- Таубман Е. И. Выпаривание. – М., 1982.
- Иоффе И. Л. Проектирование процессов и аппаратов химической промышленности: Учебник для техникумов. – Л.: Химия, 1991. – 352 с.: ил.
- Гельперин Н. И. Основные процессы и аппараты химической технологии. – М.: Химия, 1981. – 812 с.:ил.
- Клюев А. С. Проектирование систем автоматизации технологических процессов: Справочное пособие. Изд. 2-е, перераб. и доп. – М.: Энергоатомиздат, 1990. – 464 с.: ил.
- Плановский А. Н., Николаев П. И. Процессы и аппараты химической и нефтехимической технологии:Учебник для вузов. Изд. 3-е, перераб. и доп. – М.: Химия, 1987. – 496 с.
- Плановский А. Н., Рамм В. М., Каган С. З. Процессы и аппараты химической технологии. Изд. 5-е. – М.: Химия, 1991. – 848 с.
- Гуров А. М., Починкин С. М. Автоматизация технологических процессов. – М.:Высшая школа, 1979. – 355 с.
- Колач Т. А., Радун Д. В. Выпарные станции. – М.: Машгиз, 1963. – 219 с.
- Гельперин Н. И., Пебалк В. Л., Костанян А. Е. Структура потоков и эффективность колонных аппаратов химической промышленности. – М.: Химия, 1977. – 262 с.