Реферат по теме выпускной работы
Содержание
- Введение
- 1. Актуальность темы и новизна темы
- 2. Цель и задачи исследования
- 3. Результаты исследований
- 3.1 Характеристика магистральной конвейерной линии как объекта автоматизации
- 3.2 Обзор существующих технических решений в области автоматизации магистральной конвейерной линии
- 3.3 Обоснование и разработка системы автоматизированного контроля магистральной конвейерной линии
- Выводы
- Список источников
Введение
Горная промышленность является одной из важнейших отраслей нашего региона. Эффективность угледобычи в значительной степени зависит от четкости и надежности работы шахтного транспорта. В угольных шахтах и рудниках для доставки полезного ископаемого из забоя, а также его транспортировки широко применяются ленточные конвейеры.
Технологический процесс транспортировки грузов и материалов является одним из важнейших в функционировании угольной шахты.
Современные угольные шахты характеризуются высокой концентрацией производства, использованием высокопроизводительной угольной техники и сложных энергоемких электромеханических систем. Эффективность угледобычи в значительной степени зависит от четкости и надежности работы шахтного транспорта, поэтому процесс транспортировки угля требует большой надежности, эффективности, высокого КПД.
1. Актуальность и новизна темы
Ленточные конвейеры и конвейерные линии – это сложные объекты автоматизации как с позиции управления ими, так и с точки зрения обеспечения безопасности эксплуатации.
Основной задачей автоматизации конвейерных линий является централизованное управление процессом пуска и остановки, обеспечение автоматических защит с целью уменьшения энергозатрат, расхода материалов и исключения аварийных режимов работы. Кроме того, актуальной становится задача автоматического контроля температурных режимов работы ленточного конвейера.
К аварийным тепловым режимам работы ленточного конвейера относится нагрев барабанов, ленты и роликоопор, а также перегрев двигателя конвейера.
Основными причинами появления мест локального перегрева ленточного конвейера являются: заклинивание ролика вследствие поломки подшипников ролика, чрезмерное трение ленты. Поэтому для обеспечения безопасной работы ленточного конвейера необходимо постоянно контролировать температуру роликов, ленточного полотна, других механизмов конвейера и температуру окружающего его воздуха.
2. Цель и задачи исследования
Вследствие возгорания лент происходит до 30% пожаров на шахтах. Пожары, связанные с возгоранием лент, приводят к гибели людей, длительным простоям и материальным затратам.
Целью исследования является повышение уровня безопасности эксплуатации шахтного ленточного конвейера путем создания системы автоматизированного контроля тепловых режимов работы, позволяющую минимизировать риск возгорания элементов конвейера.
Предотвращения перегрева, и как следствие, возгорания ленты поможет уменьшить материальные затраты на восстановление конвейерной ленты, поскольку она является самым дорогим элементом конвейера.
3. Результаты исследований
3.1 Характеристика магистральной конвейерной линии как объекта автоматизации
Подземный транспорт – наиболее сложная составная часть транспорта предприятия. Он содержит три основных транспортных комплекса: участковый, магистральный и комплекс околоствольного двора. Участковый транспорт объединяет средства и специальное оборудование, предназначенное для перемещения грузов от очистных и подготовительных забоев до основных магистральных выработок (основного горизонта), а также в обратном направлении – различных вспомогательных материалов, оборудования и в обоих направлениях – людей. Магистральный транспорт обслуживает все грузопотоки по магистральным выработкам и связывает участковый комплекс с комплексом околоствольного двора. Транспортный комплекс околоствольного двора предназначен для приема и отправки всех грузов, поступающих в шахту и из нее.
Распространенность ленточных конвейеров на производстве обусловлена их преимуществами: высокой производительностью, простотой конструкции, небольшим расходом энергии, надежностью, возможностью транспортировки груза на большие расстояния с большой скоростью и т.п.
Автоматизация конвейерного транспорта предусматривает оснащение средствами автоматического контроля и зашиты каждого конвейера и управление, как отдельными конвейерами, так и всей линией.
Под автоматизированной конвейерной линией понимается такая линия, конвейеры которой объединены общей системой управления, обеспечивающей соблюдение необходимых блокировок и защит, а также автоматическую реализацию законов пуска, остановки и дозапуска конвейерной линии.
Основными факторами, влияющими на процесс автоматизации конвейерных линий, являются: разнообразие технологических схем конвейерных линий по конфигурации, длине, числу конвейеров и ответвлений; разнотипность конвейеров по их технологическому назначению, производительности, конструктивному исполнению, длине и динамическим характеристикам; разнотипность приводов конвейеров по числу и типу двигателей и т.д.
Системы автоматизации конвейерных линий с учётом современного уровня совершенствования конвейеров должны обладать функциональными возможностями, обеспечивающими:
– управление конвейерной линией с пульта управления;
– автоматический пуск конвейеров в линии в направлении против грузопотока с помощью пускового устройства;
– автоматическую подачу звукового предупредительного сигнала перед пуском конвейерной линии;
– возможность дозапуска части конвейерной линии при остальных работающих конвейерах;
– автоматический контроль скорости движения ленты конвейера;
– включение на пуск каждого последующего конвейера только после достижения предыдущим конвейером заданной скорости;
– оперативное отключение всей конвейерной линии с пункта управления;
– экстренное прекращение пуска и экстренную остановку любого конвейера из любой точки по его длине;
– автоматическое аварийное отключение конвейера при следующих нарушениях: отсутствии сигнала о достижении заданной скорости при пуске, снижении скорости во время работы несущего полотна или тяговой цепи до 75% номинальной при неисправности привода конвейера, недопустимом перегреве приводных барабанов, масла в турбомуфтах; сходе ленты в сторону; завале мест перегрузки и неисправностях цепей управления и контроля:
– возможность наложения тормозов при оперативном и аварийном отключении ленточных конвейеров только при скорости ленты меньше 0,5м/с;
– для конвейеров с автоматической натяжной станцией при снижении скорости ленты до 75% номинальной включение натяжной станции на увеличение натяжения ленты;
– сигнализацию на пульте управления о числе конвейеров, работающих в линии, маршруте;
– сигнализацию на блоках управления о неисправном состоянии и причине неисправности конвейера;
– информацию о состоянии конвейерной линии в систему оперативного диспетчерского контроля и управления шахты.
Целью автоматизации конвейеров является повышение их производительности, надежности, безопасности работы и снижение травматизма. Последнее достигается за счет введения различных блокировок, защит и расширения информационных возможностей аппаратуры автоматизации.
3.2 Обзор существующих технических решений в области автоматизации магистральной конвейерной линии
Сейчас почти все конвейерные линии на шахтах автоматизированы. Развитие автоматизации шахтных конвейерных линий в течение длительного периода определялось необходимостью снижения трудоемкости управления и повышения безопасности эксплуатации конвейерного транспорта. В связи с этим широкое распространение получило автоматизированное управление конвейерной линией, техническая сущность которого заключается в централизации управления процессами пуска-остановки конвейеров, а также в обеспечении автоматической защиты при возникновении аварийных ситуаций.
Для автоматической защиты от перегрева подшипников электромеханического оборудования, а также автоматического контроля и регулирования различных тепловых процессов большое распространение получили датчики ТДЛ-2, в которых чувствительным элементом является легкоплавкий сплав Вуда [1].
Термодатчик ТДЛ-2 имеет латунный наконечник, в который сплавом Вуда впаян стержень, соединенный через пружину с валиком. Такое соединение, заменяющее храповой механизм, обеспечивает относительный поворот стержня и валика только в направлении разворота витков пружины, нижний конец которой через втулку соединен с валиком, а верхний – закреплен в корпусе датчика.
При подготовке датчика к защите поворотом ручки на 90° по часовой стрелке, валиком заводится пружина, и замыкаются контакты. При нагреве наконечника до температуры размягчения сплава (65–75–°С) стержень освобождается, и подвижная часть, разворачиваясь, размыкает (или замыкает) контакты. После устранения причины перегрева и остывания сплава поворотом ручки датчик приводится в рабочее состояние.
В горной промышленности существует достаточно большое количество способов автоматизации конвейеров и конвейерных линий. Основными системами автоматизации ленточных конвейеров и конвейерных линий являються АУК-1М, АУК.3 САУКЛ, УКИ и другие.
Рассмотрим комплекс управления конвейерами и конвейерными линиями АУК-1М (далее аппаратура АУК-1М [1–2].
Аппаратура АУК-1М предназначена для контроля и управления работой стационарных линий (до трех ответвлений) и полустационарных неразветвленных линий, состоящих из ленточных и скребковых конвейеров. Число конвейеров в линии до 10.
Аппаратура АУК-1М выполняет следующие основные функции:
1) последовательный автоматический пуск конвейеров, включенных в линию в порядке, обратном направлению движения грузопотока, с необходимой выдержкой времени между пусками отдельных приводов;
2) пуск с пульта управления или с выносного кнопочного поста как всей конвейерной линии так и его части;
3) запуск с пульта управления или с выносного кнопочного поста части конвейерной линии без отключения работающих конвейеров и с подачей предупредительной сигнализации;
4) местный пуск любого привода конвейера при осмотрах, ремонтах и испытании;
5) контроль заданного максимального времени запуска каждого конвейера;
6) автоматическое отключение привода конвейера при аварийных режимах и отключение следующих конвейеров, подающих груз на поверхностный конвейер;
7) возможность экстренного прекращения запуска с любой точки конвейерной линии;
8) возможность работы аппаратуры на разветвленной конвейерной линии.
В целом комплекс выполняет 53 функции, а также обеспечивает выполнение следующих блокировок:
1) исключает пуск конвейера при неисправности цепей управления звуковой сигнализации;
2) обеспечивает пуск последующего конвейера линии только после установления рабочей скорости движения несущего органа предварительного конвейера;
3) обеспечивает отключение всех конвейеров, транспортирующих груз на остановившийся конвейер;
4) делает невозможным автоматизированный запуск конвейера, переведенного на ремонтно-отладочный режим;
5) делает невозможным включение конвейера в ремонтно-наладочном режиме при фиксации элементов пуска;
6) делает невозможным повторный запуск конвейера при аварийном отключении средствами контроля движения его несущего органа, а также пуск конвейера в случае его заштыбовки.
Наряду с указанными функциями аппаратура АУК-1М имеет целый ряд различных защит, сигнализации и телефонную связь.
Структурная схема аппаратуры АУК-1М приведена на рисунке 1.
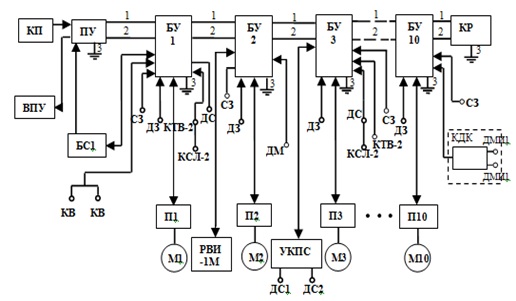
Рисунок 1 – Структурная схема аппаратуры АУК-1М
В состав аппаратуры АУК-1М входят:
– Пульт управления ПУ;
– Выносной прибор-указатель ВПУ;
– Блоки управления БУ (по количеству конвейеров линии);
– Блок конечного реле БКР;
– Датчики скорости ДС типа УПДС или ДКС, ДМ-2 или ДМ-2М;
– Датчики контроля схода ленты типа КСЛ-2;
– Кабель-тросовые выключатели типа КТВ-2;
– Датчики заштыбовки ДЗ;
– Телефонные трубки;
– Сирены типа ВСС-3М или гудки типа ГПРВ-2М.
Данная аппаратура широко используется на шахтах, удовлетворяет всем требованиям, предъявляемым к локальным средствам автоматизации конвейерных линий, но не контролирует температурные режимы работы конвейерных линий.
Рассмотрим аппаратуру АУК.3.
Комплекс АУК.3 – аппаратура нового поколения на базе микропроцессоров и обеспечивает следующие виды управления:
1) местное автоматизированное управление конвейером;
2) централизованное автоматизированное управление конвейерной линией;
3) автоматическое управление конвейерной линией, осуществляемое по командам технологических датчиков с соблюдением необходимых защитных отключений и блокировок;
4) автоматический последовательный запуск конвейеров, включенных в линию в порядке, обратном направлению движения грузопотока;
5) запуск части конвейерной линии;
6) пуск конвейеров конвейерной линии без остановки уже работающих конвейеров;
7) отключение части конвейерной линии;
8) управления одиночным конвейером без применения пульта управления.
Комплекс АУК-3 обеспечивает следующие защиты и блокировки:
1) контроль запуска конвейера по времени;
2) контроль целостности линии предупредительной сигнализации;
3) контроль снижения скорости движения ленты конвейера ниже допустимой величины;
4) контроль превышения скорости движения ленты конвейера выше допустимой величины;
5) контроль пробуксовки ленты по приводного барабана;
6) контроль снижения скорости приводного барабана ниже допустимой величины;
7) контроль снижения скорости ленты для наложения тормозов;
8) отключение конвейера из любой точки по его длине;
9) контроль схода ленты конвейера в сторону.
Комплекс АУК-3 обеспечивает следующую информацию и связью:
1) номер отключенного (аварийного) конвейера;
2) количество работающих конвейеров в линии;
3) причина аварийного отключения конвейера (дифференцированная);
4) остановка конвейерной линии в связи с отключением впереди находится технологической цепочки.
Функциональные возможности комплекса увеличены на 28 новых функций по сравнении с комплексом АУК.1М.
Следующая аппаратура – САУКЛ [1–3].
Система автоматизированного управления конвейерными линиями (САУКЛ) предназначена для:
- централизованного автоматизированного управления и контроля работы разветвленными и неразветвленными конвейерными линиями, состоящих из ленточных конвейеров, предназначенных для транспортировки груза и перевозки людей, с числом конвейеров управляемых через один комплект АПУ и АЛС до 60 единиц и неограниченным числом маршрутов;
– централизованного или местного автоматизированного управления и контроля работы отдельными конвейерами, входящих или не входящих в состав конвейерной линии;
– телеуправления и контроля состояния сопутствующим вспомогательным оборудованием;
– автоматической регистрации и хранения информации о работе конвейеров и сопутствующего оборудования, командах управления и настройках, защитных отключениях и блокировках.
Аппаратура САУКЛ рассчитана на применение в подземных выработках шахт, опасных по газу и пыли.
Структурно система САУКЛ состоит из комплекта пульта управления, который располагается в диспетчерской шахты и комплектов аппаратных средств, устанавливаемых на конвейерах.
Искробезопасность в САУКЛ обеспечивается гальванической развязкой электрических цепей пульта управления, линии связи, линии телефона, линии модулей линейных, линии взаимоблокировки, цепи питания датчика электродного и цепей питания электронных схем, а также применением схем, обеспечивающих ограничение мощности возможной искры за счет ограничения тока короткого замыкания.
Телефонная связь осуществляется по двухпроводной линии и обеспечивает телефонная симплексный канал между пультом управления и блоками управления конвейерами.
Реализация функций САУКЛ осуществляется с помощью программ, которые находятся в ПУ и в каждом БУК.
Структурная схема аппаратуры САУКЛ приведена на рисунке 2.
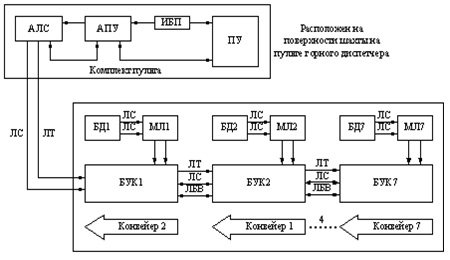
Рисунок 2 – Структурная схема аппаратуры САУКЛ
На сегодняшний день разработана единственная аппаратура контроля температуры приводных барабанов АКТЛ-1 [3]. Аппаратура предназначена для контроля обечайки нефутерованого приводного барабана ленточного конвейера и для защиты ленты от возгорания при пробуксовке. Контроль осуществляется как в процессе вращения так и при неподвижном состоянии барабана.
В состав аппаратуры АКТЛ-1 входят стабилизированный источник питания, высокочастотный генератор сигналов, термодатчик, узел приема–передачи сигналов и блок сигнализации. Термодатчик ТД-1 представляет собой полую стальную шпильку, внутри которой расположен термочувствительный элемент, выполненный в виде катушки индуктивности с ферритовым сердечником. Термодатчик герметизируется эпоксидным компаундом и встраивается в обечайку барабана. Принцип датчика основан на использовании эффекта резкого уменьшения магнитной проницаемости при нагревании его до определенной температуры.
В случае пробуксовки конвейера обечайка приводного барабана и термодатчик нагреваются. При нагревании обечайки до температуры 700С конвейер отключается. Повторно конвейер можно запустить только после снижения температуры обечайки барабана на 5–7 °С ниже допустимой.
Данная аппаратура автоматизации и защиты конвейеров обладает рядом недостатков:
– сложность конструкции и принципа действия;
– невозможность оперативного переноса на другой объект контроля;
– невозможность согласования с аппаратурой автоматизации конвейерных линий;
– невозможность управления натяжной станцией ленточного конвейера;
– невозможность сбора информации о тепловом режиме от нескольких конвейеров линии.
Таким образом, все вышеперечисленные системы и средства автоматизации не выполняют требуемых функций контроля и диагностики нарастания температуры при работе ленточного конвейера. Большинство из них выполнены на устаревшей элементной базе, что значительно сокращает функциональные возможности аппаратуры.
Для наиболее полного контроля необходимо использовать современные средства отбора, диагностики и мониторинга состояния приводного двигателя, приводного барабана, роликоопор и ленты конвейера.
3.3 Обоснование и разработка системы автоматизированного контроля магистральной конвейерной линии
К тепловым режимам работы ленточного конвейера относятся нагрев барабанов, ленты и роликоопор, а также нагрев двигателя до температуры, при которой возможно возгорание угольной пыли или других горючих веществ и материалов из-за отсутствия или отключения защит, предотвращающих аварийный режим работы конвейера.
Причиной пожара может стать перегрев подшипников двигателя из-за недостаточной их смазки, перекосов вала и т.д.
Основной характеристикой нагрузочных режимов является тепловая характеристика электродвигателя. Работа АД всегда сопровождается его нагревом, что обусловлено происходящими в нем процессами и потерями энергии. Нормативный срок службы электродвигателя определяется, в конечном счете, допустимой температурой нагрева его изоляции. В современных двигателях применяется несколько классов изоляции, допустимая температура нагрева которых составляет для класса А – 105 °С, Е – 120 °С, В – 130 °С, F – 155 °C, H – 180 °C, С свыше 180 °С. Превышение допустимой температуры ведет к преждевременному разрушению изоляции и существенному сокращению срока его службы.
Процесс нагрева приводного барабана, ленты и распределенных физических элементов ленточного конвейера (роликоопор) определяется режимом его работы, натяжением набегающей и сбегающей ветвей ленты, удельной нагрузкой на ленту, техническим состоянием роликоопор (заштыбовка), а также технологическими параметрами ленточного конвейера, такими как: ширина ленты, диаметр приводного барабана и длина ленточного конвейера.
Основной влияющий параметр – это погонная масса транспортируемого материала. Повышение загрузки конвейера и ослабленное натяжение ленты приводит к увеличению дуги рабочего проскальзывания, что повышает истирание ленты и может вызвать аварийную пробуксовку. В случае пробуксовки возрастает температура в зоне сцепления ленты и барабана, которая достигает 300–350 °С за 15 мин его работы. В случае рабочего проскальзывания происходят потери энергии, затрачиваемые на преодоление сил трения, часть которых вызывает изменение температуры в зоне контакта барабан – лента.
Рассмотрим процесс нагрева для фрикционной пары «приводной барабан – лента» (рис.3).
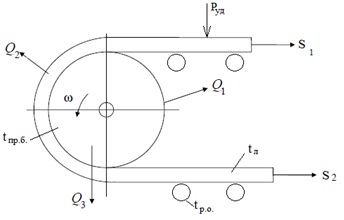
Рисунок 3 – Структурная схема пары «приводной барабан – лента»
На рис. 3 приведено: S1 и S2 – натяжение набегающей и сбегающей ветвей ленты; Q1 – количество тепла, отведенное излучением; Q2 – количество тепла, отведенное естественной конвекцией; Q3 – количество тепла, отведенное вынужденной конвекцией, tпр.б – температура приводного барабана; tр.о – температура роликоопор; tл – температура ленты; Руд – удельная нагрузка на ленту.
Уравнение теплового баланса процесса нагрева приводного барабана и ленты имеет вид [7]:

где Qобр – количество тепла, образованное во время работы конвейера, ккал/ч;
Qнб – количество тепла, затрачиваемое на нагрев барабана и ленты, ккал;
Q1 – количество тепла, отведенное излучением, ккал/ч;
Q2 – количество тепла, отведенное естественной конвекцией, ккал/ч;
Q3 – количество тепла, отведенное вынужденной конвекцией, ккал/ч;
T – время работы конвейера.
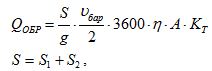
где S – суммарное натяжение ветвей ленты;
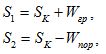
где Wгр и Wпор – сопротивления движению ленты соответственно на груженой и порожней ветвях.
Анализ уравнения теплового баланса и диаграммы натяжения показывает, что тепловой режим работы ленточного конвейера определяется удельной нагрузкой на ленту, а также усилиями натяжения груженной и порожней ветвей.
Эффективный температурный контроль режимов работы ленточного конвейера может быть обеспечен системой автоматизированного контроля с техническими средствами отбора информации, выполняющими следующие основные функции:
– обеспечение контроля фактической температуры окружающей среды в месте установки конвейера по всей его длине с возможностью сбора, обработки и хранения полученной информации;
– контроль превышения температуры в точках ее возможного повышения, например, у роликов конвейера, электродвигателя, барабана, с подачей местного светового сигнала о месте превышения температуры, сигнала по линии связи;
– контроль средней температуры и скорости ее изменения вдоль участков конвейера с передачей сигнала по линии связи о месте возможной аварии;
– обеспечение контроля усилия натяжения ленты и удельной нагрузки на ней.
Для получения наиболее полной тепловой модели работы ленточного конвейера необходимо прямым или косвенным методом контролировать все влияющие параметры. К прямым (контактным) методам контроля относится измерение натяжения ветвей ленты, удельная нагрузка на ленту, измерения температуры подшипниковых узлов статора двигателя, температуры приводного барабана. К косвенным (бесконтактным) методам относятся измерение температуры нагрева ленты и роликоопор.
Для контроля нагрева ленты и роликоопор по всей длине конвейера, а также предупреждения возгорания ленты применяется линейный температурный извещатель (термокабель) PHSC, производства компании Protectowire (США) [8].
Линейный тепловой извещатель PHSC представляет собой уникальный тепловой детектор в виде кабеля, который позволяет выявить источник перегрева в любом месте по всей его длине.
Термокабель PHSC TRI-Wire генерирует отдельные сигналы срабатывания («Предтревога») и пожарной тревоги в зависимости от установленных температурных порогов срабатывания защиты.
Температура приводного барабана ленточного конвейера измеряется термосопротивлением, включенным в мостовую схему.
Удельная нагрузка на ленту определяется конвейерными весами фирмы SBS, позволяющими автоматически тарировать ленту, осуществлять мониторинг отклонений взвешивания и отсутствие груза на ленте, обнаруживать материал остающийся на ленте, фиксировать процент времени прохождения пустой ленты за выбранный период времени. Интеллектуальный цифровой датчик удельной нагрузки SFT в конструктивном исполнении IP 65 не требует тарировки и обеспечивает очень высокое разрешение (1:1'000'000).
Натяжение груженой ветви ленты измеряется тензорезистивным преобразователем, установленным на натяжной станции.
Контроль температуры подшипниковых узлов двигателя осуществляется при помощи термоконтроллера.
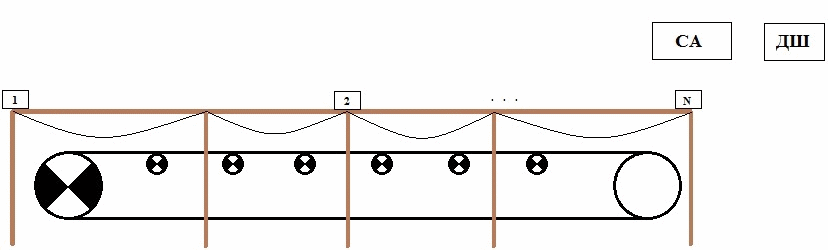
Рисунок 4 Диагностика нагрева роликоопор (анимация: 11 кадров, 5 циклов, интервал 700 мс, 129 кб)
На рис.4 указаны: 1, 2 … N – интерфейсные модули термокабеля, СА – система автоматизации, ДШ – диспетчер шахты.
Выводы
Проблема контроля над превышением температуры нагревания элементов шахтного ленточного конвейера по его длине является достаточно сложной, она связана со значительной протяженностью линии контроля, которая может превышать 2 километра. Кроме того, сказываются тяжелые условия эксплуатации шахтного оборудования: вибрация, угольная пыль, возможность резкого повышения температуры и др.
Применение разработанной системы позволяет осуществлять эффективный и своевременный контроль тепловых режимов работы шахтного ленточного конвейера, предупреждает развитие аварийных ситуации, минимизирует затраты на ремонт и восстановление ленты и, как следствие, сокращает непозволительные простои оборудования, а также повышает его долговечность.
При написании данного реферата квалификационная работа магистра не завершена. Дата окончательного завершения работы – январь 2016 г. Полный текст работы и материалы по теме работы могут быть получены у автора или его научного руководителя после указанной даты.
Список источников
- Груба В. И., Никулин Э. К., Оголобченко А. С. Технические средства автоматизации в горной промышленности. – К.: ИСМО, 1998. – 373 с.
- Справочник по автоматизации шахтного конвейерного транспорта / Н. И. Стадник, В. Г. Ильюшенко, С. И. Егоров и др. – К.: Техника, 1992. – 438с.
- Автоматизация подземных горных работ/ Под ред. проф. А. А. Иванова. – К.: Вища школа, 1987. – 328с.
- Требования к автоматизации шахтных конвейеров и конвейерных линий. – М.: Недра, 1981. – 25 с.
- Автоматизация производства на угольных шахтах / Г. И. Бедняк, В. А. Ульшин, В. П. Довженко и др. – К.: Техника, 1989. – 272с.
- Гаврилов П. Д., Гимельштейн Л. Я., Медведев А. Е. Автоматизация производственных процессов. Учебник для вузов. М.: Недра, 1985, 215 с.
- Д. В. Хананов, А. Я. Грудачев. Аналіз процесів нагріву конвеєрної стрічки при повній пробуксовці приводного барабана шахтного конвеєра в аварійному режимі роботи. Наукові праці Донецького національного технічного університету. Донецьк: ДВНЗ „ДонНТУ“, 2009. – С. 256–265. – (Сер.Гірничо-електромеханічна; Вип.17(157)
- Линейный тепловой извещатель PHSC (термокабель) [Электронный ресурс]. Режим доступа: http://www.phsc.ru/
- Венгеров И. Р. Теплофизика шахт и рудников. Математические модели. – Монография в 2-х том. том 1 – Донецк: Норд-Пресс, 2008. – 632с.
- Правила безопасности в угольных и сланцевых шахтах. М.: «Недра», 1986. – 432с.
- Шахмейстер Л. Г., Дмитриев В. Г. Теория и расчет ленточных конвейеров – 2-е изд., перераб. и доп. – М.: Машиностроение, 1987. – 336 с.