Содержание
- Введение
- 1. Характеристика и свойства высокоуглеродистой стали для проволоки высокой прочности
- 2. Виды термической обработки проволоки
- 3. Постановка задачи и цели исследований
- 4. Материалы, методика, оборудование для исследования
- 5. Результаты исследований
- Выводы
- Список источников
Введение
От 8 до 10% количества мирового производства технического железа и стали перерабатывается в проволоку. Номенклатура изделий, изготавливаемых из проволоки, весьма разнообразна, например, канаты, пружины, винты, гвозди, иглы, грозозащитная проволока, арматура для резины, тканей и железобетона. Ежегодно, применяется десятки миллионов тонн проволоки. Высокопрочная проволока основное свое применение нашла при изготовлении канатов, пружин и арматуры для предварительно напряженного железобетона. Эти изделия являются ответственными деталями сложных машин и конструкций, поэтому к ним предъявляются высокие требования по качеству [1].
За последние годы, спрос на высокопрочную проволоку в мире увеличился вдвое. Так, например, 2010 году на внутреннем рынке Украины было реализовано 910,9 тыс. тонн высокопрочной проволоки. По итогам 2013-2014 гг. спрос на высокопрочную проволоку увеличился в среднем на 6,8% по сравнению с 2010 годом. Наблюдавшийся на внутреннем рынке Украины рост потребления проволоки, в значительной мере определялся развитием строительного сектора, машиностроительного комплекса, добывающих отраслей, где активно используются данная продукция [2]. В России в 2009 г. внутреннее потребление проволоки различных видов составило 37,1 млн. тонн (110,4% к 2008 г.), в том числе поставки отечественной продукции дос-тигли 32 млн. тонн (107% к 2006 г.). Также в России, по мнению экспертов, до 2017 года потребность в высокопрочной проволоки составит больше 12 млн. тонн [2].
Таким образом, потребление высокопрочной проволоки с каждым годом увеличивается, поэтому актуальным является вопрос об усовершенствовании технологии производства и термической обработки проволочной заготовки с целью получения необходимого уровня свойств проволоки.
1.Характеристика и свойства высокоуглеродистой стали для проволоки высокой прочности
Для изготовления проволоки высокой прочности применяют высокоуглеродистые стали с содержанием углерода 0,6-1,0%. Для проволоки высокой прочности чаще всего используют углеродистые высоколегированные стали марок 70, 75, 80, 85 и др. Химический состав определяется требованиями ГОСТ 10543 [3]. Однако в составе стали не должно быть примесей, которые неблагоприятно влияют на свойства при проведении необходимой для проволоки термической обработки - патентирования.
Для высокопрочной стали наиболее типичная работа под действием растягивающих сил. Прочность высокопрочных сталей на растяжение характеризуется временным сопротивлением разрыву и пределом текучести. Для установления свойств прочности изготовленной высокопрочной стали ее испытывают на растяжение и на изгиб в холодном состоянии. Для этого образец сгибают под углом 45 ... 1800, в зависимости от марки стали, вокруг оправки диаметром 1 ... 5 диаметров образца. После изгиба на внешний растянутой стороне образца не должно быть никаких трещин, отслоений или взлома. Проводят также испытания стали на удар, определяя тем самым ее способность сопротивляться возникающим в процессе работы динамическом воздействия. Испытания стали на удар позволяет узнать степень ее хрупкости, качество обработки и ударную вязкость (отношение работы, затраченной на разрушение образца к площади его поперечного сечения в месте излома). Ударная вязкость стали весьма важный показатель, влияющий на прочность конструкций, которые подвержены динамическим нагрузкам при значительной отрицательной температуре воздуха [4].
Таким образом, для изготовления высокопрочной проволоки применяется высокоуглеродистая сталь с содержанием углерода 0,6-1,0 %. Именно структура и свойства стали в дальнейшем обеспечивают необходимый комплекс свойств готовой проволоки.
2. Виды термической обработки проволоки
Классический способ термообработки катанки - это патентирование и отжиг на зернистый перлит. Патентирование в цехе производится на протяжных агрегатах, которые в своем составе имеют: печь для нагрева; селитровую ванну; промывочную ванну - 2шт; травильную ванну; ванну для бурения; сушильное устройство; намоточное устройство. [5].
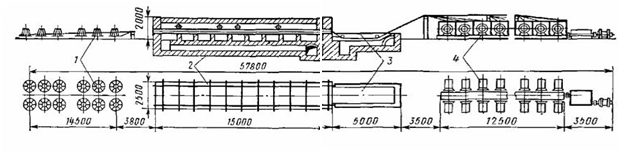
Рисунок 1 - Схема установки для патентирования
Патентирование заключается в нагреве заготовки до температуры 950-980°С и охлаждение ее в селитровой ванне при температуре 450-550°С (температуры зависят от химического состава металла). Такие температуры соли обеспечивают превращение переохлажденного аустенита в тонкопластинчатый перлит (сорбит) с толщиной пластинок цементита 10-40 нм и феррита 60-200 нм [5]. Патентирование стали необходимо проводить с учетом непрерывности процесса волочения, поэтому проволока по выходе из фильер пропускается через трубки, уложенные в печь, нагретую до температуры закалки стали; после нагрева проволоку протягивают через соляную ванну, затем извлекают из нее. Охлаждают, наматывают на барабаны и вновь протягивают через следующие фильеры. Длину печи, ванны расстояние от ванны до намоточного барабана и скорость движения проволоки рассчитывают так, чтобы проволока прогрелась до нужных температур, завершились происходящие превращения, и проволока успела охладиться на воздухе. В микроструктуре патентируемой стали не должно быть мартенситных включений и избыточного феррита. Такая структура позволяет проводить волочения с высокими степенями обжатия и обеспечивает после волочения упрочнение стали с сохранением повышенной пластичности и вязкости [6].
Существует множество публикаций, которые описывают разные способы нагрева и охлаждения проволочной заготовки. Безусловный интерес представляет нагрев проволочной заготовки в низкотемпературной плазме и электролитах. Однако отсутствует информация о структуре и свойствах, обработанных таким образом сталей. Отказаться от использования расплавов солей можно путем использования низколегированных сталей, однако это не выгодно, из-за растущего дефицита легирующих элементов.
Последние годы большой интерес представляют технологии, в которых в качестве охладителя при сорбитизации используется вода. Com-plex Water Bath Processing – это процесс, в котором температуры аустенитизации при промежуточном патентировании составляют 800°С-820°С, а при заключительном – 820°С-850°С. Это положительный аспект данной технологии, т. к. эти температуры ниже, чем при патентировании в расплаве свинца [7].
Еще одна технология бессолевой сорбитизации – это сорбитизации стали на воздухе, который движется. При изучении сорбитизации потоком движущегося воздуха, было выяснено, что повышение температуры аустенитизации и продолжительности выдержки образцов приводит к монотонному увеличению микротвердости стали [7]. Это связано с тем, что растет зерно аустенита и его гомогенность, а это увеличивает устойчивость переохлажденного аустенита, его склонность к переохлаждению и получения более дисперсных структур при распаде[8].
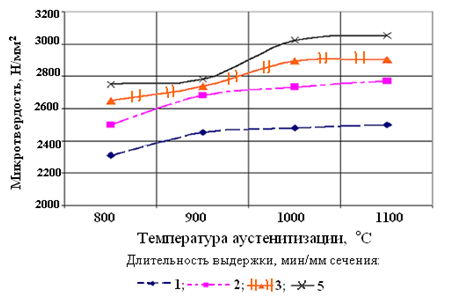
Рисунок 2 - Влияние температуры аустенитизации и времени выдержки на микротвердость структуры катанки из стали 70 при охлаждении потоком воздуха, который движется со скоростью 4м/с
С уменьшением скорости охлаждения уменьшается и твердость катанки. Увеличение температуры нагрева и длительности выдержки приводит к повышению значений микротвердости продуктов диффузионного распада переохлажденного аустенита [9].
В настоящее время внедряются новые технологии в процесс термиче-ской обработки проволоки. Одна из таких технологий – это сорбитизация стали в сыпучем графите. Известно, что при охлаждении с температуры аустенитизации сталей в сыпучем графите возможны самопроизвольные структурно-фазовые превращения, которые позволяют получить необходимый уровень свойств без энергозатрат на процесс охлаждения. Знания о фазово-структурных превращениях в металлах базируется на их термодинамике, механизме и кинетике. Кинетику фазово-структурных превращений характеризуют параметры, кинетические кривые и диаграммы. Известно, что сыпучий графит в отличии от жидких (вода, масло, расплавленные соли) и газообразных (воздух, газы) сред является «псевдо твердой» податливой охлаждающей средой, он обеспечивает более равномерную передачу тепла от металла [9].
Исследования многих ученых показали, что проведенное в реальных неизотермических условиях охлаждение образцов проволочной заготовки в среде порошкообразного графита свидетельствует о том, что предварительная холодная пластическая деформация при последующих процессах аустенитизации и распада переохлажденного аустенита способствует ускорению зарождения центров продуктов распада. В работе [9] изучается влияние условий формирования сорбитной структуры в высокоуглеродистой катанке путем аустенитизации и после-дующего охлаждения в порошкообразном графите. Для этого образцы катанки из стали 75 аметром 6,5 мм, стали 70 диаметром 6,5 мм, стали 75 диаметром 5,5 мм и стали 80 диаметром 5,5 мм нагревали до 950° с удельной выдержкой из расчета 1,5 мин/мм сечения, после чего образцы извлекали из печи и помещали для дальнейшего охлаждения в графитовый порошок при комнатной температуре. Полученные значения микротвердости подтверждают тот факт, что, с увеличением содержания углерода в стали и уменьшением диаметра катанки и при таком способе охлаждения, микротвердость увеличивается.
Структура стали после сорбитизации в порошкообразном графите состоит из сорбита, структура которого является наиболее желательной при проведении данной термообработки. В ходе таких исследований учеными были получены кинетические кривые превращения переохлажденного аустенита в перлитные структуры. Кинетические кривые дают основания для построения реальных диаграмм распада переохлажденного аустенита в неизотермически охлаждающей среде графита. Такие исследования свидетельствуют о возможности отказа от токсичных солевых ванн в пользу порошкообразного графита [10].
Еще одна нетрадиционная технология термической обработки высокопрочной проволоки – это патентирование проволоки в кипящем слое. С целью устранения патентирования проволоки в токсичных свинцовых и взрывоопасных селитровых ваннах Уральским политехническим институтом, Гипрометизом и Белорецким металлургическим комбинатом разработана технология и опытно-промышленный агрегат для патентирования проволоки в кипящем слое.
Агрегат представляет собой печь для нагрева проволоки длинной 3350 мм и ванну охлаждения длиной 4640 мм, разделенные перегородкой толщиной 250 мм. Температура кипящего слоя в печи 950°С, а в ванне может регулироваться от 60°С до 500°С [11].
В качестве псевдоожижаемого мелкозернистого материала в печи и ванне использовали белый корунд с частицами размером 100мкм. Для патентирования проволоки в кипящем слое было отобрано свыше 50 тонн проволоки. Результаты исследований показали, что временное сопротивление разрыву, относительное удлинение и относительное поперечное сужение проволоки удовлетворяют требованиям ТУ 93-67 для патентируемой проволоки. Микроструктура проволоки после патентирования на установке с кипящем слоем – сорбит с наличием небольшого количества феррита. Также в ходе исследований, учеными Уральского политехнического института было установлено, что температуру печи с кипящем слоем можно изменять в широких пределах (от 800°С до 1000°С). Изменение температуры нагрева значительно влияет на структуру и свойства проволоки из высокоуглеродистой стали. С повышением температуры кипящего слоя увеличивается устойчивость аустенита, его превращение при охлаждении идет при более низких температурах, что повышает дисперсность феррито-карбидной смеси и уменьшает количество избыточного феррита. Эти структурные изменения сопровождаются повышением прочностных свойств проволоки. Подробнейшие сравнительные исследования показали, что проволока патентированная в кипящем слое, не отличается от патентируемой в свинце и селитре не только по своим механическим свойствам, но и по ряду физических свойств.
Еще в 1972 г. для производства и эксплуатации печей ванн с кипящим слоем в Англии была создана фирма «Hudfire Development Limited». Она разработала установку для патентирования проволоки в кипящем слое, состоящую из трех зон [11].
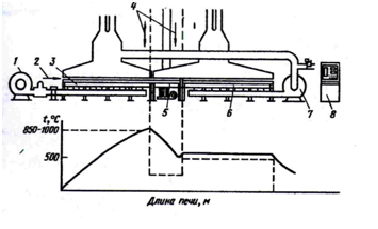
Рисунок 3 - Схема агрегата для патентирования проволоки в кипящем слое и изменение температуры проволоки в процессе ее движения через агрегат
Отмечается, что эти печи имеют значительные преимущества перед обычными, так как упрощается намотка проволоки, в четыре раза уменьшается длина печи, снижается окисление проволоки, достигается ее высокая температурная однородность. В тоже время замена кипящим слоем охлаждающей селитровой ванны позволяет устранить отложение соли на проволоке, окисление ванны и очистить атмосферу от вредного воздействия испарений соли [11].
3. Постановка задачи и цели исследований
В качестве термической обработки проволоки из высокоуглеродистой стали применяется патентирование в расплавах солей, которое обеспечивает получение структуры сорбита. Однако патентирование в жидких средах является очень трудоемким и энергозатратным процессом. Расплавы солей также являются очень взрывоопасными и негативно влияют экологию окружающей атмосферы.
Компромиссным решением, которое обеспечивает снижение трудоем-кости и энергозатрат на процесс термообработки проволоки, а также улучшает условия труда на производстве, является сорбитизация заготовки для проволоки в сыпучих средах.
Поэтому, цель данной магистерской работы – это изучение условий формирования структуры сорбита в высокопрочной проволоки из высокоуглеродистых сталей путем аустенитизации и дальнейшего охлаждения в сыпучих средах типа порошкообразного графита.
4. Материалы, методика, оборудование для исследования
Материалом для данной работы послужила проволочная заготовка из холоднодеформированной высокоуглеродистой стали 85 с различными степенями обжатия вплоть до 75% диаметром 2 мм. Химический состав данной стали приведен в таблице 1 [12].
C | Si | Mn | Ni | S | P | Cr | Cu |
0.82-0.9 | 0.17-0.37 | 0.5-08 | <0.25 | <0.035 | <0.035 | <0.25 | <0.2 |
В опытах изучали закономерности охлаждения образцов из стали 85 в порошкообразном графите. Для этого образцы O 2,0 мм и длиной 30 мм укладывали в жаропрочные керамические тигли, засыпали древесным углём, который служил в качестве защитной среды от обезуглероживания и окисления поверхности, и загружали в нагревательные электрические печи МП-2УМ, предварительно нагретую до температуры 950±10°С и 1000±10°С; общее время нагрева и выдержки при этой температуре составляло 10 мин для полного завершения перлито-аустенитного превращения и формирования однофазного аустенитного состояния.
После окончания выдержки образцы по одному во избежание потерь тепла быстро переносили в тигель с серебристым порошкообразным графитом дисперсностью 6-7 мкм; длительность выдержки в нем 0 – 12 с; после этого образцы резко охлаждали в воде.
Шлифы изготавливали по стандартной методике с последующим их травлением в 4%-ом спиртовом растворе азотной кислоты. Микроструктуру образцов изучали на микроскопе МИМ – 7 с последующим фотографированием; измерение микротвёрдости проводили на микротвердомере ПМТ-3 при нагрузке 1 Н.По микроструктурам исследуемых образцов оценивали долю превращённого аустенита по методу секущих (ГОСТ 5639) и строили кинетические кривые превращения переохлаждённого аустенита в продукты распада.
5. Материалы, методика, оборудование для исследования
На рисунке 4 и 5 представлены микроструктуры проволоки после сорбитизации в порошкообразном графите при температуре 950° и 1000° соответственно. По микрофотографиям с помощью метода секущих считали объемные доли фаз. По результатам расчетов были получены кинетические кривые в координатах процент распада – время распада.
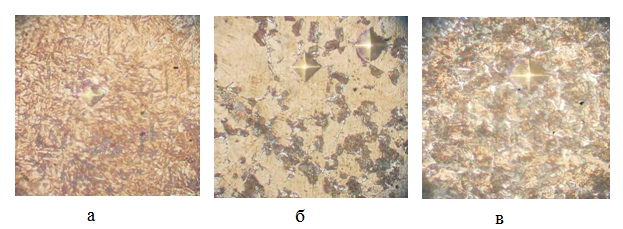
Рисунок 4 - Микроструктура проволоки со степенью ПХПД 27 % после сорбитизации в сыпучем графите, с, 160: а)1, б) 6, в) 9 при температуре 950°С
Видно, что при выдержке в течение 1 с структура состоит из мартенсита, следовательно, распад ещё не начался; при выдержке 6 с структура частично состоит из мартенсита и продуктов распада, т. е. происходит частичный распад аустенита, а при 9 с – полностью из продуктов распада, что свидетельствует о полном завершении процесса распада переохлаждённого аустенита.
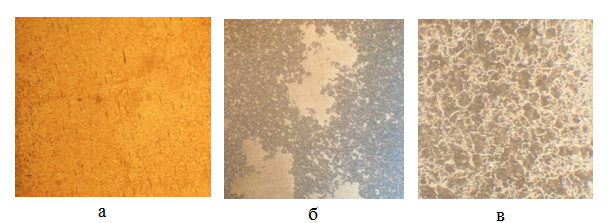
Рисунок 5 - Микроструктура проволоки со степенью ПХПД 27 % после сорбитизации в сыпучем графите, с, 160: а)1, б) 8, в)12 при температуре 1000°С
По микрофотографиям с помощью метода секущих считали объемные доли фаз. По результатам расчетов были получены кинетические кривые в координатах процент распада – время распада. Кинетические кривые представлены на рисунке 6 и 7.
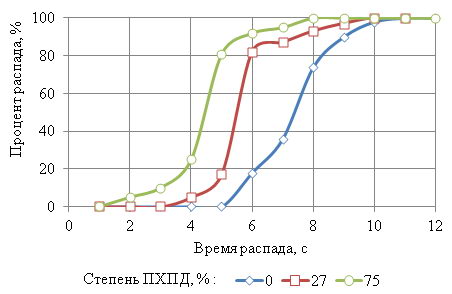
Рисунок 6 - Кинетические кривые проволоки после сорбитизации в сыпучем графите при температуре 950°С
Из рисунка 6 видно, что в проволоке с ПХПД 0% распад аустенита на-чался на 6с, а завершился на 10 с. В проволоке с ПХПД 27% распад начался на 6 с и закончился на 10 с. А в проволоке с ПХПД 75% распад аустенита начался на 2 с, а завершился на 8с. Получается, что распад переохлажденного аустенита проволоки с ПХПД 0% длился 4 с, 27% длился 4 с, а проволоки с ПХПД 75% 6 с.
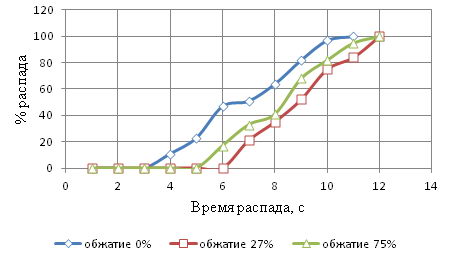
Рисунок 7 - Кинетические кривые проволоки после сорбитизации в сыпучем графите при температуре 1000°С
Из рисунка 7 видно, что в проволоке с ПХПД 0% распад аустенита на-чался на 4с, а завершился на 11 с. В проволоке с ПХПД 27% распад начался на 7 с и закончился на 12 с. А в проволоке с ПХПД 75% распад аустенита начался на 6 с, а завершился на 12с. Получается, что распад переохлажденного аустенита проволоки с ПХПД 0% длился 7 с, 27% длился 5 с, а проволоки с ПХПД 75% 6 с.
Сравнивая полученные результаты после сорбитизации при температуре 950°С с результатами при температуре 900°С можно сделать вывод, что распад аустенита в проволоке с ПХПД 0% начался позже на 2 с. В проволоке с ПХПД 27% распад аустенита начался позже на 4 с, в проволоке с ПХПД 75% распад начался раньше на 1 с.
При сравнении результатов после сорбитизации при температуре 950°С и результатов после сорбитизации при 1000°С, видно, что распад проволоки с ПХПД 0% начался одинаково на 4с, однако, закончился позже. В проволоках с ПХПД 27% и 75% распад начался и закончился позже.
Далее с помощью микротвердомера ПМТ-3 при нагрузке 50 грамм измеряли микротвердость продуктов распада переохлажденного аустенита. После чего построили графики зависимости микротвердости продуктов распада от времени изотермической выдержки, которые представлены на рисунке 8.
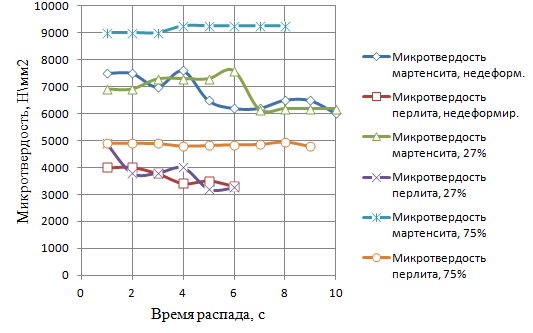
Рисунок 8 - Зависимость микротвердости структурных составляющих образцов от времени выдержки в графите по степни ПХПД при температуре 950°С
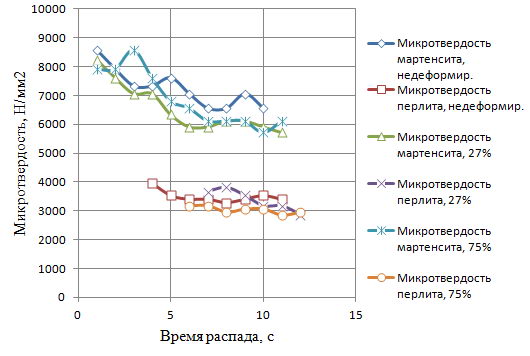
Рисунок 9 - Зависимость микротвердости структурных составляющих образцов от времени выдержки в графите по степни ПХПД при температуре 1000°С
Таким образом, повышение степени ПХПД приводит к ускорению времени начала распада переохлажденного аустенита в среде порошкообразного графита, но при этом увеличивает длительность этого распада. Ускорение начала распада вероятно связано с введенными дефектами кристаллического строения, которые увеличивают количество мест для зарождения новой фазы, тем самым снижая длительность инкубационного периода.
Сравнение полученных результатов с данными для распада от 900°С свидетельствует о том, что для недеформированных и деформированных образцов с малыми степенями обжатия начало распада при температуре 950°С затормаживается, в то же время, у сильнодеформированных образцов начало распада фиксируется раньше. Это можно объяснить следующим образом. Известно, что рост температуры аустенитизации способствует возрастанию размера зерна аустенита и ускорению его гомогенизации, в результате чего затрудняется его распад при последующем охлаждении, что и было получено для образцов с ПХПД 0 и 27 %. В случае высокой степени ПХПД внедренное большее количество дефектов не успевает достаточно снизиться за указанное (10 мин) время выдержки и препятствует росту зерна и гомогенизации аустенита, одновременно облегчая зародышеобразование при последующем охлаждении. В следствие этого, распад аустенита для образцов с большой предшествующей деформацией ускорился.
Выводы
Магистерская работа посвящена актуальной научной задаче изучения влияния параметров аустенитизации на распад переохлажденного аустенита высокоуглеродистой стали:
- Формирование структуры сорбита в высокоуглеродистой проволочной заготовки путем аустенитизации и дальнейшем охлаждении в бессолевых средах принципиально возможно и требует детального изучения.
- На основании анализа литературных источников определено, что порошкообразный графит является актуальной охлаждающей средой для сорбитизации, т. к. позволяет получить необходимую структуру и уровень свойств проволочной заготовки. Также охлаждение в сыпучем графите позволяет экономить энергозатраты и улучшить экологию окружающей среды.
- Проведен ряд экспериментов по использованию среды порошкообразного графита для сорбитизации стали.
- Целесообразно более глубокое изучение данного вопроса для поиска новых и усовершенствования старых режимов термической обработки проволочной заготовки, с целью повышения и улучшения механических характеристик проволоки, а также продление срока службы.
Дальнейшие исследования направлены на следующие аспекты:
- Качественное совершенствование применения среды сыпучего графита для сорбитизации.
- Адаптация сорбитизации в графите в производственных условиях.
Список источников
- Виды и применение проволоки [Электронный ресурс] / Интернет журнал – Режим доступа: http://www.sportobzor.ru/poleznye-sovety/vidy-i-primenenie-provoloki.html
- Рынок металлов: прогнозы старые и новые [Электронный ресурс] / Информационно-аналитический журнал – Режим доступа: http://www.metalbulletin.ru/analytics/color/341/
- ГОСТ 3282-74. Проволока стальная. Технические условия. – Введ. 1974-17-01. – М.: Изд-во стандартов, 1976. – 17 с.
- Циммерман Р. Металлургия и материаловедение / Р. Циммерман, К. Гюнтер; пер. с нем. – М.: Металлургия, 1982. – 480 с.
- Гуляев А.П. Металловедение. Учебник для вузов / Гуляев А.П. – [6-е изд.]. – М.: Металлургия, 1986. – 544 с.
- Жучков С.М. Новая технология и оборудование для повышения качества катанки / С.М. Жучков // Наука та Інновації. – 2007 - № 3. – С. 43 – 49.
- Алимов В.И. Бессолевая сорбитизация проволоки / В.И. Алимов // Металлургия: Сб. науч. трудов. ДВУЗ «ДонНТУ» - Донецк. – 1999. – Випуск 8 (141). – С. 129 – 133.
- Алимов В.И. Влияние режима термообработки на структуру и свойства предварительно ускоренно охлажденной с прокатного нагрева катанки / В.И. Алимов, О.В. Олейникова, Т.С. Коржова // Металлургия: Сб. науч. трудов ДонНТУ. – 2011. – Вып. 13 (194). – С. 170-179.
- Алимов, В.И. Фазовые и структурные превращения при деформационно-термической обработке проволоки / В.И. Алимов, О.В. Пушкина. – Донецк: Донбасс, 2012. – 242 с.
- Пат. на кор. Модель Укр. №65131, МПК С21Д9/52 (2006.01). Спосіб сорбітизації дротяної заготівки для музичних струн в сипучому графіті / Алімов В. І., Туков В. А., Алімова С. В., Максаков А. І., Олейнікова (Пушкіна) О. В., Пономарьова І. В. - № и 2011 06109; заявл. 16.05.2011, Бюл. № 22.
- Башнин Ю.А. Технология термической обработки стали / Башнин Ю.А., Ушаков Б.К., Сеней А.Г. – М.: Металлургия, 1986. – 424 с.
- Сорокин В.Г. Стали и сплавы: Марочник / В.Г. Сорокин, М. А. Гервасьев – М.: «Интермет Инжиниринг», 2001. – 608с.