Abstract
Contents
- Introduction
- 1. Characteristics and properties of high carbon steel wire of high strength
- 2. Types of heat treatment wire
- 3. Setting goals and objectives of research
- 4. Materials, methods and equipment for investigation
- 5. Research results
- Conclusions
- List of sources
Introduction
From 8 to 10% of the amount of global production of commercial iron and steel is processed into a wire. The range of products made from wire, very diverse, for example, ropes, springs, screws, nails, needles, Lightning protection wire reinforcement for rubber, fabric and concrete. Every year, tens of millions of tons of used wire. High-wire main found its application in the manufacture of ropes, springs and valves for prestressed concrete. These products are critical parts of complex machines and structures, so they are subject to high quality requirements [1].
In recent years, demand for high-strength wire in the world has doubled. For example, in 2010 in the domestic market it was sold 910.9 thous. Tons of high-tensile wire. According to the results of 2013-2014. demand for high-strength wire has increased on average by 6.8% compared with 2010. Observed in the domestic market consumption growth wires is largely determined by the development of the construction industry, mechanical engineering, mining industries, which are widely used in these products [2]. In Russia in 2009 the domestic consumption of various types of wire was 37.1 million. Tons (110.4% to 2008), including the delivery of domestic products dos crucibles 32 million. Tons (107% to 2006) . Also in Russia, according to experts, until 2017 the need for high-strength wire will be more than 12 million. tons [2].
Thus, the consumption of high-tensile wire increases every year, so urgent is the question of improving production technology and thermal processing wire rod in order to obtain the required level of properties of the wire.
1.Characteristics and properties of high carbon steel wire of high strength
For the manufacture of high strength wire used high-carbon steel with a carbon content of 0.6-1.0%. For high strength wire used most often high-alloy carbon steel grades 70, 75, 80, 85, and others. The chemical composition is determined by the requirements of GOST 10543 [3]. However, in the steel should not be impurities which adversely affect the desired properties during heat treatment of the wire - patenting.
For high-strength steel is the most typical work under the influence of tensile forces. Durability of high tensile steel is characterized by tensile strength and yield strength. To determine the properties of high strength steel made it tested for tensile and flexural strength in the cold state. For this sample bent at an angle of 45 ... 1800, depending on the grade of steel around a mandrel diameter of 1 ... 5 diameters sample. After bending the outer side of the stretched sample there should be no cracks, peeling or cracking. Also conducted tests began to blow, thereby determining its ability to resist arising in the process of dynamic effects. The tests began to strike allows you to see the degree of brittleness, processing quality and toughness (ratio of work spent on the destruction of the sample to the area of ??its cross-section at the site of the fracture). Toughness of the steel is very important factor influencing the strength of structures, which are subject to dynamic loads at very low temperatures [4].
Thus, for manufacturing high-strength high-carbon steel wire applied with a carbon content of 0.6-1.0%. It is the structure and properties of the steel in the future provide the necessary range of properties of the finished wire.
2. Types of heat treatment wire
The classic method of heat treating rod - is patenting and annealing to granular perlite. Patenting in the shop is made on broaching units, which are composed of: a furnace for heating; saltpeter bath; washing bath - 2 pieces; a pickling bath; bath for drilling; drying device; coiler [5].
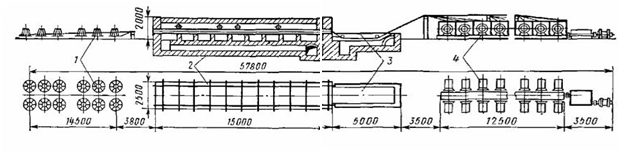
Figure 1 - Apparatus for patenting
Patenting is to heat the preform to a temperature of 950-980°С and cooling it in saltpeter bath at 450-550°С (the temperature depends on the chemical composition of the metal). These salts provide the transformation temperature of the supercooled austenite into pearlite tonkoplastinchaty (sorbitol) plates with thickness of 10-40 nm cementite and ferrite 60-200 nm [5]. Patenting of steel should be carried out taking into account the continuity of the drawing process so the wire on leaving the spinneret is passed through the tubes arranged in a furnace heated to a temperature of hardening of steel; after heating wire is pulled through the salt bath, then removed from it. Cooled and reeled again drawn through the die following. The length of the furnace, away from the bath tub to the drum and the winding speed of the wire is calculated so that the wire is warmed to the desired temperature, resulted in the conversion occurring and the wire had time to cool off in air. The microstructure of the steel patentiruemoy not be martensitic inclusions and excess ferrite. This structure allows the drawing with high degrees of compression and provides after drawing reinforcement steel retaining increased ductility and toughness [6].
There are many publications that describe different methods of heating and cooling a wire rod. Unconditional interest heating wire rod temperature plasma and electrolytes. However, no information on the structure and properties, thus treated steels. Renounce the use of molten salts is possible through the use of low-alloy steels, but it is not profitable, because of the growing shortage of alloying elements.
In recent years, great interest in technology, in which a cooling water is used in the sorbitizing. Com-plex Water Bath Processing - a process in which the austenitizing temperature at the intermediate patenting at 800°С-820°С, and when the final - 820°С-850°С. This is a positive aspect of this technology, t. To. These temperatures are lower than in patenting in lead melt [7].
Another technology bessolevoy sorbitizing - sorbitizing steel is air that moves. In the study sorbitizing stream of moving air, it was found that increasing the austenitizing temperature and duration of exposure of samples leads to a monotonic increase in the microhardness of steel [7]. This is due to the fact that the growing of the austenite grain and its homogeneity, and this increases the stability of the supercooled austenite, its tendency to supercooling and more dispersed structure in the decay of [8].
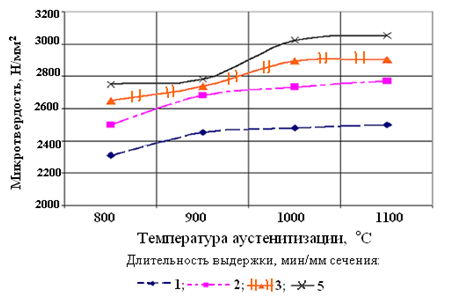
Figure 2 - Effect austenitizing temperature and holding time on microhardness of steel wire rod structure 70 with cooling air flow, which moves at a speed of 4m/s
With the reduction of the cooling rate decreases and hardness rod. Increasing the heating temperature and duration of exposure leads to higher values of microhardness of diffusion decomposition products supercooled austenite [9].
Currently, new technologies are introduced into the process thermtion wire processing. One such technology - is sorbitizing steel granular graphite. It is known that on cooling from the austenitizing temperature of steel in the bulk graphite possible spontaneous structural phase transformation, which allow to obtain the desired level of properties without energy consumption for the cooling process. Knowledge of the phase-structural transformations in metals based on their thermodynamics, mechanism and kinetics. The kinetics of phase-structural transformations characterize parameters kinetic curves and diagrams. It is known that particulate graphite unlike liquid (water, oil, molten salt) and gaseous (air, gas) media is "pseudo solid" pliable cooling medium, it provides more uniform heat transfer from the metal [9].
The research of many scientists have shown that spent in non-isothermal conditions of real samples of wire rod cooling in the medium of powdered graphite indicates that pre-cold plastic deformation processes in subsequent austenitizing and decay of supercooled austenite to accelerate nucleation decay products. The paper [9] studied the effect of conditions of formation of structure in the high-sorbitol wire rod by austenitizing and then cooling-blowing powdered graphite. For this, samples of steel rod 75 ametrom 6.5 mm, steel diameter 6.5 to 70 mm, steel diameter 5.5 mm 75 and 80 became 5.5 mm was heated to 950°C with a specific exposure rate of 1.5 m / mm cross section, after which the samples were removed from the oven and placed for further cooling in a graphite powder at room temperature. Microhardness values obtained confirm the fact that, with the increase of carbon content in steel and the reduction of the diameter of wire rod and with this method of cooling, increasing microhardness.
The structure of steel after sorbitizing graphite in powder consists of sorbitol, whose structure is most desirable during this heat treatment. In the course of such research scientists have obtained the kinetic curves of the transformation of supercooled austenite in the pearlite structure. Kinetic curves provide a basis for the construction of real charts the disintegration of supercooled austenite in a non-isothermal cooling medium graphite. These studies indicate the possibility of non-toxic salt baths in favor of powdered graphite [10].
Another alternative technology of thermal processing of high-strength wire - a wire patenting in a fluidized bed. To eliminate the patenting of toxic lead wire and explosive Saltpeter baths Ural Polytechnic Institute, Giprometizom and Beloretsk Metallurgical Plant has developed a technology and pilot production plant for wire patenting in a fluidized bed.
The unit is a furnace for heating the wire length of 3350 mm and a length of the cooling bath 4640 mm, separated by a partition 250 mm. The temperature of the fluidized bed furnace 950°C, and the bath can be adjusted from 60°C to 500°C [11].
As fluidizing fine material in the bath furnace and white aluminum oxide was used with a particle size of 100um. For patenting wire in a fluidized bed were selected more than 50 tons of wire. The results showed that the tensile strength, elongation and the relative transverse contraction wire satisfy the technical requirements for the 93-67 patentiruemoy wire. The microstructure of the wire after patenting at a fluidized bed installation - sorbitol with the presence of a small amount of ferrite. Also during studies, scientists Ural Polytechnic Institute has been found that the temperature of the furnace with a fluidized bed can be varied over a wide range (from 800 to 1000°C). Changing the heating temperature greatly influences the structure and properties of high carbon steel wire. With increasing temperature the fluidized layer increases the stability of austenite, its transformation during cooling proceeds at lower temperatures, which improves dispersibility of ferrite-carbide mixture and reduces the amount of excess ferrite. These structural changes are accompanied by an increase in the strength properties of the wire. A detailed comparative study showed that the patented wire in a fluidized bed, does not differ from patentiruemoy in lead nitrate and not only in their mechanical properties, but also on a number of physical properties.
Already in 1972, for the production and operation of furnaces with a fluidized bed baths in England was created company «Hudfire Development Limited». It has developed a plant for wire patenting in a fluidized bed consisting of three zones [11].
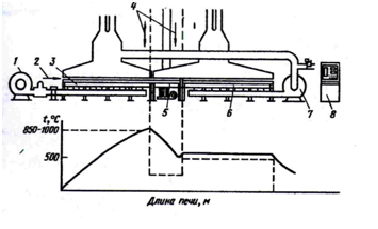
Figure 3 - Driving unit for patenting the wire in a fluidized bed and changing the temperature of the wire during its motion through the unit
It is noted that these furnaces have significant advantages over conventional, as the wire winding is simplified, four times the length of the furnace is reduced, oxidation of the wire is reduced, it is achieved by high temperature uniformity. At the same time, the replacement of a cooling fluid bed saltpeter bath eliminates the deposition of salt on the wire, the oxidation baths and clean environment from the harmful effects of salt vapors [11].
3. Setting goals and objectives of research
As the heat treatment of high-carbon steel wire patenting applied in molten salts, which provides the structure of sorbitol. However, patenting in liquids is a very time-consuming and energy-consuming process. Molten salts are also very explosive and adversely affect the ecology of the surrounding atmosphere.
A compromise solution that reduces trudoem-bones and energy to the process of heat treatment of the wire, as well as improve working conditions in the workplace, is sorbitizing wire bar in granular media.
Therefore, the purpose of this master's work - a study of the conditions of formation of the structure of sorbitol in high-tensile wire of high carbon steel by austenitizing and further cooling in granular media such as graphite powder.
4. Materials, methods and equipment for investigation
The material for this work was the wire rod of high carbon steel cold-85 with varying degrees of compression up to 75% of a diameter of 2 mm. The chemical composition of the steel is given in Table 1 [12].
C | Si | Mn | Ni | S | P | Cr | Cu |
0.82-0.9 | 0.17-0.37 | 0.5-08 | <0.25 | <0.035 | <0.035 | <0.25 | <0.2 |
The experiments studied the patterns of cooling samples of steel 85 in powdered graphite. For the samples diametr 2,0 mm and a length of 30 mm were placed in a high-temperature ceramic crucibles, covered charcoal which served as a protective environment against decarburisation and oxidation of the surface, and electrically charged in the heating furnace MB 2UM preheated to a temperature ± 950 10 °C, and 1000 ± 10 °C; the total time of heating and soaking at this temperature was 10 minutes to complete the perlite-austenite transformation and the formation of single-phase austenitic state.
After the end of exposure patterns by one in order to avoid heat losses quickly transferred into the crucible with silver powdered graphite dispersion of 6-7 microns; shutter speed it 0 - 12; After the samples were quenched in water.
Microsections were prepared by standard methods with subsequent etching of 4% th alcoholic solution of nitric acid. The microstructure of the samples was studied in microscope MIM - 7, followed by photographing; microhardness measurement was carried out on a PMT-3 microhardness under a load of 1 N.Po microstructures of the samples were evaluated proportion of austenite transformed by the method of cross-sections (Standard 5639) and the conversion of kinetic curves built supercooled austenite decomposition products.
5.Research results
Figure 4 and 5 show microstructure of the wire after sorbitizing a graphite powder at a temperature of 950 and 1000, Respectively. By using photomicrographs secant believed volume fractions of the phases. The calculations were obtained kinetic curves in coordinates percentage decay - decay time.
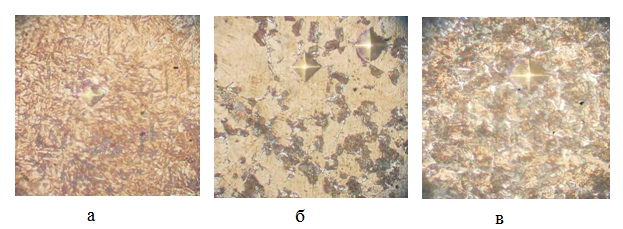
Figure 4 - The microstructure of the wire with a degree of 27% after PHPD sorbitizing in granular graphite, s, 160: a) 1, b), 6 in) 9, 950 °C
It is seen that when exposed for 1 second structure consists of martensite, therefore, the collapse has not yet begun; by exposing the structure 6 consists partly of martensite and degradation products, ie. e. there is a partial decomposition of austenite, and at 9 - entirely of decomposition products, indicating that it was fully decay supercooled austenite.
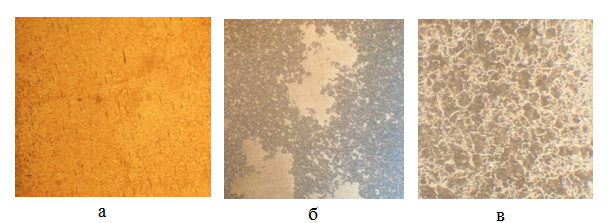
Figure 5 - The microstructure of the wire with a degree of 27% after PHPD sorbitizing in granular graphite, s, 160: a) 1, b), 6 in) 9, 1000°С
By using photomicrographs secant believed volume fractions of the phases. The calculations were obtained kinetic curves in coordinates percentage decay - decay time. Kinetic curves are shown in Figure 6 and 7.
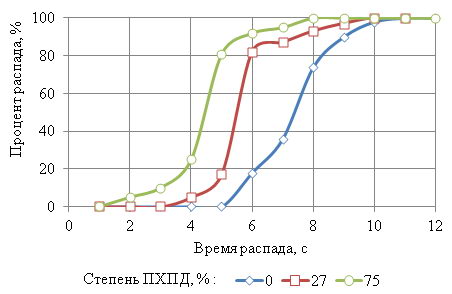
Figure 6 - Kinetic curves of the wire after sorbitizing in the bulk graphite at 950°C
Figure 6 indicates that the wire with PHPD 0% decomposition of austenite to-chalsya to 6c, and finished with 10. The wire with PHPD 27% decay began at 6 and ended on 10. A wire with a 75% PHPD decomposition of austenite started at 2 and ended at 8c. It turns out that the collapse of supercooled austenite wire PHPD 0% lasted for 4, 27% lasted 4 and wire PHPD 75% 6.
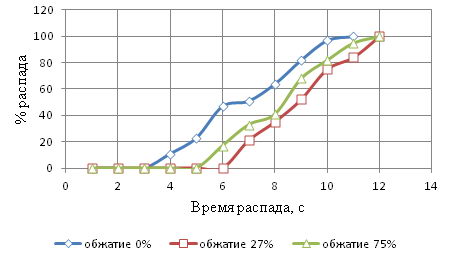
Figure 7 - Kinetic curves of the wire after sorbitizing in the bulk graphite at 1000°С
Figure 7 shows that the wire with PHPD 0% decomposition of austenite to-chalsya to 4c, and finished with 11. The wire with a 27% decay PHPD kept at 7 and at 12 ended. A wire with a 75% PHPD decomposition of austenite began at 6 and ended at 12c. It turns out that the collapse of supercooled austenite wire PHPD 0% lasted 7 to 27% lasted 5 seconds, and wire PHPD 75% 6.
Comparing the results obtained after sorbitizing at 950 ° C with the results at 900 ° C, we can conclude that the decomposition of austenite in the wire with PHPD 0% began after 2 seconds. The wire with PHPD 27% austenite decomposition started later at 4, in the wire with 75% PHPD decomposition began before 1 sec.
ПComparing the results after sorbitizing at 950 ° C and the results after sorbitizing at 1000 ° C, it is seen that the disintegration of the wire with 0% PHPD kept equally to 4c, however, it ended later. The wire PHPD 27% and 75% of decay began and ended later.
Next, using a PMT-3 microhardness under a load of 50 grams was measured microhardness of the decay products of supercooled austenite. Then plot the microhardness of the decay products of the isothermal holding time, which are presented in Figure 8.
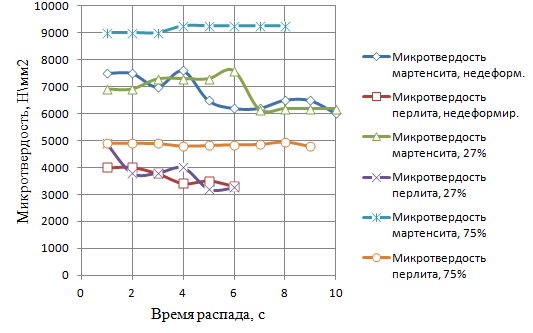
Figure 8 - Microhardness of structural components from the sample holding time in graphite by Stepney PHPD at 950 C
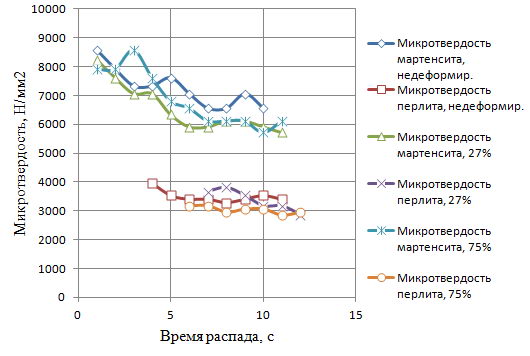
Figure 9 - Microhardness of structural components from the sample holding time in graphite by Stepney PHPD at 1000°C
Thus, the increase in the degree PHPD leads to faster start time decay of supercooled austenite in an environment of powdered graphite, but it increases the duration of this decay. Accelerating the beginning the collapse is likely due to the introduction of crystal defects that increase the number of places for the nucleation of a new phase, thereby reducing the duration of the incubation period.
Comparison of these results with the data for the decay of 900°C indicates that the undeformed and deformed samples with low degrees of compression top collapse at 950°C is decelerated at the same time, highly deformed samples fixed before the beginning of decay. This can be explained as follows. It is known that the growth of the austenitizing temperature increase promotes austenite grain size and speed homogenization, thereby impeding its decomposition at the subsequent cooling, which was obtained for samples with PHPD 0 and 27%. In case of high degree PHPD introduce more defects has not time enough to fall within the specified (10 min) exposure time, and prevents the growth of austenite grains and homogenizing while facilitating nucleation during subsequent cooling. In consequence, the decomposition of austenite for samples with large deformation prior accelerated.
Conclusions
Master's thesis is devoted to actual scientific problem of studying the influence of parameters on the collapse of the austenitizing supercooled austenite high-carbon steel:
- Formation of the structure of sorbitol in high-carbon wire rod by austenitizing and further cooling in salt-free environments is possible in principle and requires a detailed study.
- Based on the analysis of the literature found that powdered graphite is an actual cooling medium for sorbitizing, t. To. Lets get the necessary structure and properties of the wire rod level. Also in the bulk graphite cooling saves energy and improve the ecology of the environment.
- A number of experiments on the use of powdered graphite medium for sorbitizing steel.
- It is advisable to a deeper study of the question to find new and improvement of old modes of heat treatment wire rod, in order to increase and improve the mechanical properties of the wire, as well as extending the life.
Further studies focused on the following aspects:
- Qualitative improvement of the use of the medium of bulk graphite for sorbitizing.
- Adaptation sorbitizing in graphite in a production environment.
List of sources
- Виды и применение проволоки [Электронный реcурc] / Интернет журнал – Режим доcтупа: http://www.sportobzor.ru/poleznye-sovety/vidy-i-primenenie-provoloki.html
- Рынок металлов: прогнозы cтарые и новые [Электронный ресурс] / Информационно-аналитиче°°°°°°°°Ский журнал – Режим доступа: http://www.metalbulletin.ru/analytics/color/341/
- ГОСТ 3282-74. Проволока стальная. Технические условия. – Введ. 1974-17-01. – М.: Изд-во стандартов, 1976. – 17с.
- Циммерман Р. Металлургия и материаловедение / Р. Циммерман, К. Гюнтер; пер. нем. – М.: Металлургия, 1982. – 480с.
- Гуляев А.П. Металловедение. Учебник для вузов / Гуляев А.П. – [6-е изд.]. – М.: Металлургия, 1986. – 544с.
- Жучков С.М. Новая технология и оборудование для повышения качества катанки / С.М. Жучков // Наука та Інновації. – 2007 - № 3. – С. 43 – 49.
- Алимов В.И. Бессолевая сорбитизация проволоки / В.И. Алимов // Металлургия: Сб. науч. трудов. ДВУЗ «ДонНТУ» - Донецк. – 1999. – ВипуСк 8 (141). – С. 129 – 133.
- Алимов В.И. Влияние режима термообработки на структуру и свойства предварительно ускоренно охлажденной с прокатного нагрева катанки / В.И. Алимов, О.В. Олейникова, Т.С. Коржова // Металлургия: Сб. науч. трудов ДонНТУ. – 2011. – Вып. 13 (194). – С. 170-179.
- Алимов, В.И. Фазовые и Структурные превращения при деформационно-термической обработке проволоки / В.И. Алимов, О.В. Пушкина. – Донецк: Донбасс, 2012. – 242 С.
- Пат. на кор. Модель Укр. №65131, МПК С21Д9/52 (2006.01). Спосіб сорбітизації дротяної заготівки для музичних струн в сипучому графіті / Алімов В. І., Туков В. А., Алімова С. В., Максаков А. І., Олейнікова (Пушкіна) О. В., Пономарьова І. В. - № и 2011 06109; заявл. 16.05.2011, Бюл. № 22.
- Башнин Ю.А. Технология термической обработки стали / Башнин Ю.А., Ушаков Б.К., Сеней А.Г. – М.: Металлургия, 1986. – 424 С.
- Сорокин В.Г. Стали и сплавы: Марочник / В.Г. Сорокин, М. А. Гервасьев – М.: «Интермет Инжиниринг», 2001. – 608 С.