Abstract
Ñîäåðæàíèå
- Introduction
- 1. Brass. General characteristics, classification
- 2. General properties of brass
- 2.1 Simple brass
- 2.2 Alloy brass
- 3. Heat treatment of brass
- 4. Materials and methods of research
- 5. These results
- Findings
- List of sources
Introduction
Metals are widely used in modern technology due to both chemical, in particular, and their physical properties. The commonality of physical properties of metals (high electrical conductivity, thermal conductivity, malleability, ductility) is explained by common structure of their crystal lattices.
Currently, the role-based alloys non-ferrous metals is increasing every year. Besides metallurgy, machine building, shipbuilding and other long-established areas of technology metallic materials of this group are used in instrumentation, electronics, nuclear, cryogenic engineering, electrical engineering, aviation, aerospace and medicine. p>
Brass thanks to its qualities are widely used in machine building, chemical industry, in the production of household goods. Advantages brass promote sustainable consumption of its planned growth in all industries. The metal is in demand almost everywhere - from the production of door handles and watch gears to manufacture the most complex heat exchangers in the energy sector [1].
1. Brass. General characteristics, classification
Brass - is a double or multi-component alloy based on copper, wherein the main alloying element is zinc, sometimes with the addition of tin, nickel, lead, manganese, iron and other elements [2]. Brass smelted More BC. e., with the late 18th century. it received from the smelting of copper ore, zinc, mixed with charcoal. Only in the 19th century. This method has been widely supplanted by direct fusion of copper and zinc. Due to good workability pressure in the hot and cold, high mechanical properties, beautiful color and comparative cheapness of brass - the most common copper alloys. Of these, a sheet, ribbon, bar, tube, wire (wrought brasses), and casting (casting brass). With increasing zinc content brass color changes from red to light yellow. Figure 1.1 shows the phase diagram of the alloy Cu - Zn [3].
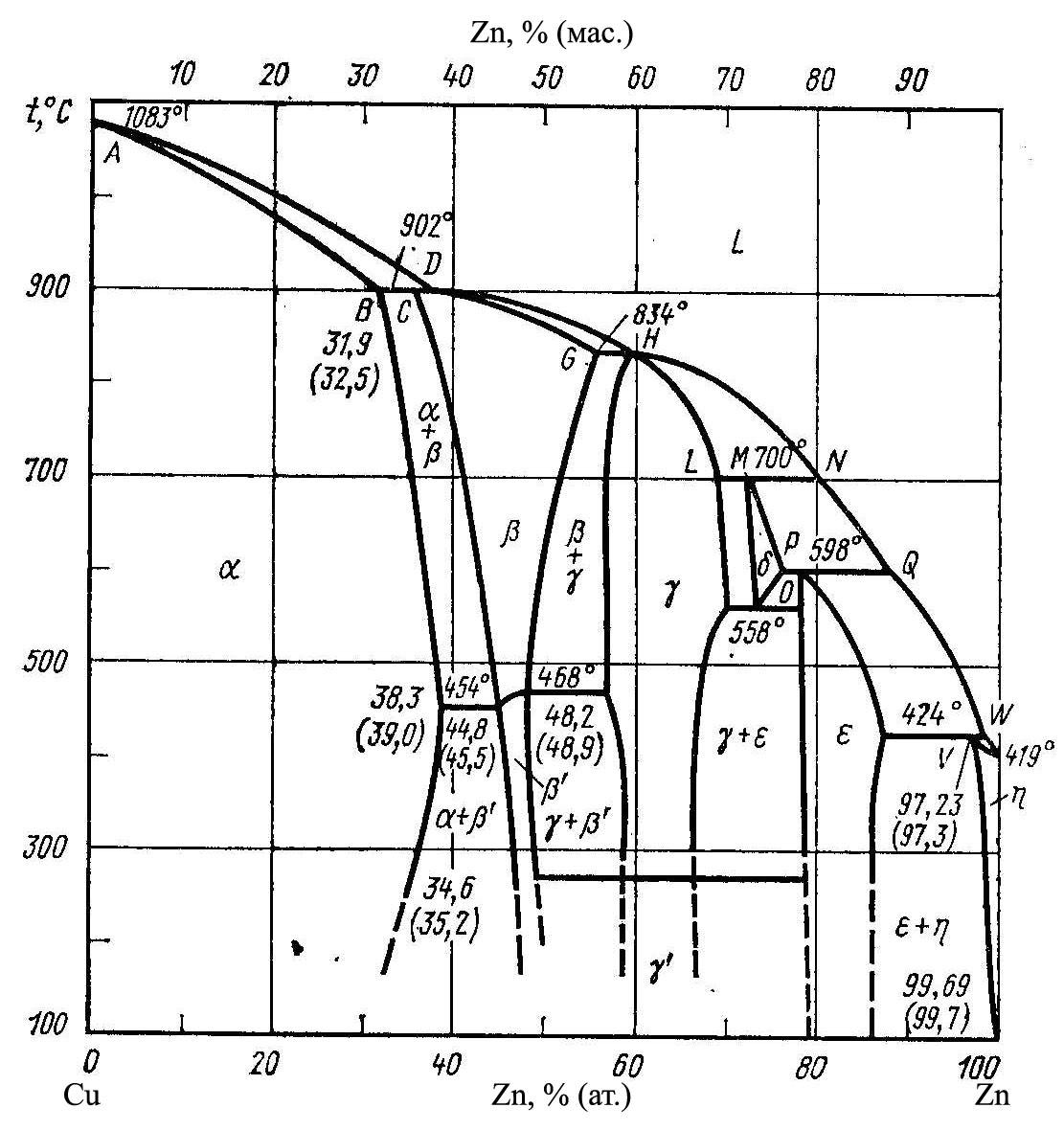
Figure 1.1 - diagram of the system Cu - Zn
Reserve solubility of zinc in the copper is 39%. The temperature is lowered from 902 to 454 °C maximum solubility of zinc in copper increases, while further reducing it, according to some authors, can be reduced to about 30-32%. Therefore brass containing 39% zinc, theoretically have a structure consisting of only a solid solution crystal α. These are called single-phase brass, or α-brass. However, in real conditions even when the zinc content is about 30% of the crystals appear brass second phase (β'-phase). If you exceed the limit of solubility of zinc in copper brass are biphasic, or (β + β')-brass. β'-phase is very strong, but fragile [4].
2. General properties of brass
2.1 Simple brass
Hardness, yield strength, tensile strength and ductility of ordinary brass is higher than that of copper. In general, these parameters increase with increasing zinc content. The best plasticity has L68 (maximum depth for drawing sheets, the largest number of wire bends). The number of L63 β phase slightly and it has little effect on the plasticity of L63 and its ability to pressure treatment at low temperatures, but requires strict adherence cooling [5]. P>
From simple brass can hire all kinds.
All simple brass have good casting properties and can be used to produce castings.
Simple brass anti-friction properties, as well as copper, do not possess. P>
2.2 Alloy brass
Special brass have greater strength, better corrosion resistance to more environments than simple brass. Most special brasses have good anti-friction properties. Many of them are resistant to sea water (tin, aluminum, silica. Manganese), superheated steam (manganese brass), etc. Some of them combine excellent corrosion properties with good sliding properties (LK65-1.5-3, LO90-1, LZhMts59-1-1). The special resistance of certain brasses to specific environments in specific operating conditions determine the scope of their preemptive use. P>
The most common are lead brass. Their main feature - excellent machinability. This manifests itself in the possibility of high-speed machining with low tool wear. This forms a small loose chips, which determines the purity of the treated surface and minimal work hardening during cutting. It defines the use of lead for the production of small-sized brass parts for precision mechanics. Their negative side is the low toughness, low flexural strength in the presence of the notch. The most common of lead brass is LS59-1 [6].
The best workability has LS63-3 brass. With respect thereto evaluate machinability nonferrous metals and carbon steels (in percentage).
Virtually all brass is a good structural material at low temperatures. Also, as they retain the plasticity of copper and do not become brittle when cooled down to liquid helium temperatures.
Due to the higher recrystallization temperature (300-370 °C) brasses creep at high temperatures is smaller than that of copper. In medium temperature zone (200-600 °C) brasses observed phenomenon of brittleness. It is due to the formation of brittle interlayers intercrystalline insoluble at low temperatures impurities (lead, bismuth). With increasing temperature, toughness decreases brass. Electrical and thermal conductivity of brass is markedly lower than that of copper.
Lead brass worse than brass solders are connected, welded and polished. For connection of lead brass is not recommended oxyacetylene welding arc in inert gas and arc with a consumable electrode [7]. P>
The corrosion resistance of lead brass. Lead possess brass: excellent resistance against the effects of net hydrocarbons, freon, fluorinated gidrokarbonatovyh coolers and varnishes; good resistance to the impact of industrial, marine, rural atmosphere, alcohol, diesel fuel and dry carbon dioxide; average resistance to impact crude carbon dioxide and water; poor resistance against the effects of ammonium hydroxide, hydrochloric acid and sulfuric acid [7]. P>
The main alloying elements in multicomponent brasses are aluminum, iron, manganese, lead, silicon, nickel. They have different effects on the properties of brass. P>
Manganese increases strength and resistance to corrosion, especially in combination with aluminum, tin and iron. P>
Tin increases the strength and greatly improves the corrosion resistance in seawater. Brass containing tin, often called naval brass. P>
Nickel improves the strength and corrosion resistance in various media. P>
Lead affects the mechanical properties, but it improves machinability. They were ligated (1-2%) of brass, which are machined on automatic machines. Therefore, these brass called automata. P>
Silicon impairs hardness, strength.
When combined doping of silicon and lead increased frictional properties of brass and it can serve as a substitute for more expensive, such as tin bronzes that are used in bearings.
Table 2.1 presents the physical and technological properties of some grades of special brass. P>
Table 2.1 - Physical and technological properties of special brass [7]
Property | Brand | ||
ËÀÆ 60-1-1 | ËÎ 70-1 | ËÊ 80-3 | |
melting point,°Ñ | 904 | 935 | 900 |
density,ã/ñì3 | 8,2 | 8,5 | 8,6 |
The elastic modulus, kg / mm2 | 10500 | 10600 | 9800 |
Temperature hot processing,°Ñ | 700-800 | 650-750 | 750-850 |
The annealing temperature,°C | 600-700 | 550-650 | 500-600 |
3. Heat treatment of brass
In developing the technology of thermal processing of copper and its alloys have to consider two features: high thermal conductivity of copper and active interaction with gases when heated. When heating thin and semifinished products thermal conductivity is of secondary importance. Upon heating the massive products high thermal conductivity of copper is responsible for more rapid and uniform heating of the entire cross section, as compared, for example with titanium alloys. Due to the high thermal conductivity during the hardening heat treatment of copper alloy is no problem hardenability. When used in practice dimensions of semi-finished products and they are baked through.
Copper and its alloys are actively interact with oxygen and water vapor at elevated temperatures, at least more intensive than aluminum and its alloys. In this regard, during the heat treatment of semi-finished products, and from copper and its alloys are frequently used protective atmosphere [8]. P>
Heat treatment of brass is recrystallization annealing. The temperature of the onset of recrystallization copper intensively raised elements such as Zr, Cd, Sn, Sb, Cr, whereas Ni, Zn, Fe, Co have little effect. At the recrystallization temperature also affects brasses preceding treatment, primarily the degree of cold working and grain size, formed by this processing. For example, the time to onset of recrystallization brass L95 at 440 °C is 30 minutes at a degree of cold deformation of 30% and 1 min at a degree of deformation of 80% [8].
The value of the grain affects the recrystallization process opposite to increase the degree of deformation. For example, the alloy L95 with the initial grain 30 and 15 microns annealing after 50% strain at 440 °C leads to recrystallize at 5 and 1 minute, respectively. At the same time, the value of the grain does not affect the rate of recrystallization, if the annealing temperature exceeds 440 °C. P>
Under the same conditions of deformation and annealing with increasing zinc content of the grain size decreases, reaches a minimum, and then increases. For instance, after annealing at 500 °C for 30 min grain size is: 0.025 mm copper; a brass containing 15% Zn - 0,015 mm and a brass with 35% Zn - 0,035 mm. In α brass grains begin to grow at relatively low temperatures and increases until the solidus temperatures. The two-phase (α + β) - and special brass grain growth usually occurs only at temperatures at which remains one β phase. For example, brass L59 significant increase in grain begins at annealing temperatures above 750 °C [9]. P>
When annealing copper alloys with the content of 32-39% Zn at temperatures above α - (α& + β ) transition stands β phase, which causes non-uniform grain growth. Annealing of these alloys is preferably carried out at temperatures not exceeding line α - (α + β) -equilibrium system Cu-Zn. Therefore brass composition lying near the maximum solubility of zinc in the copper should be annealed in ovens with accurate temperature control and high uniformity of its distribution by volume of the furnace [10] . p>
When you select the recrystallization annealing of brass should be noted that the alloys lying near the phase boundary α / (α + β), due to variable solubility of zinc in the copper can be thermally harden. Tempering brasses containing more than 34% Zn, making them prone to aging, and ability to age hardening increases with increasing zinc content of up to 42%. Practical application of this kind of thermal bonding brass found. However, the cooling rate of the brass type L63 after recrystallization annealing affects their mechanical properties. Possibility of decomposition of supersaturated solutions α brass containing more than 34% Zn, and (α + β )-brass should also be considered when choosing the annealing conditions to reduce stress. A strong cold deformation can accelerate the decay of supersaturated α and 946-solution during annealing [11]. P>
The quality of the annealed material is determined not only by its mechanical properties, but also the size of the recrystallized grains. The grain size in the fully recrystallized structure is quite uniform. If improperly installed modes recrystallization annealing in the structure clearly detected two groups of grains of different sizes. This so-called dual structure is particularly desirable in operations deep drawing, bending, or polishing and etching products. With the increase in grain size to a certain extent improved formability brass, but the surface quality deteriorates. On the surface of the product with the grain size of more than 40 microns observed characteristic roughness - "orange peel" [12].
4.Materials and methods of research
For experimental studies have been sampled with a special brass brand LS59-1 provided TM "Termolayf" whose chemical composition is shown in Table 4.1 [13]. p>
Table 4.1 - Chemical composition of brass LS59-1 [13]
The content of the element, % | ||||||||||
Fe | P | Cu | Pb | Zn | Sb | Bi | Sn | impurities | - | |
äî 0,5 | äî 0,02 | 57-60 | 0,8-1,9 | 37,05-42,2 | äî 0,01 | äî 0,003 | äî 0,3 | âñåãî 0,75 | Si+Sn<0,5 | |
Note: Zn - base; the percentage of Zn is given approximately. |
Samples were selected from the 24 mm width of the hexagon. Sample thickness 10 - 11 mm. P>
In order to study the microstructure of the surface of the sample was subjected to grinding abrasive paper and then polishing. To identify the structure of the ground and polished samples yielded etching solution of nitric acid HNO3 in water at a ratio of 1: 1. P>
During the research the following equipment: light horizontal metallographic microscope «Neophot - 21" hardness TC-2M Micro Durometer PMT-3, chamber furnace SNOL 1,6.2,5.1 / 11 HA thermocouple, digital combined unit ni - 4300 . p>
The samples were subjected to recrystallization annealing at a heating temperature:
- 500 - 520 °C - heating of the two-phase (α + β) - the region; li>
- 800 - 820 °C - heating in single-phase β region. Li> p>
Ol>
The cooling was performed with the furnace in air and in water to accelerate cooling and better separation okaliny.Na selected samples was performed microarray analysis of measured hardness and microhardness.
5.These results
Figure 5.1 shows the microstructure of the original sample and heated to 500 and 800 °C with subsequent cooling in air, x1000 magnification.
Ðèñóíîê 5.1 – The microstructure of the brass brand LS59-1
Figure (a) shows the structure of brass in the original raw state, is a dark matrix of beta-phase (intermetallic ~ CuZn) and formed from her bright isolation alpha solid solution based on copper. Inside some of these particles are not detected in the soluble copper lead which is the last to solidify. These particles serve as nuclei on which the crystals begin to form the alpha phase. P>
The figure (b) shows the structure of brass after heating to 500 °C. Heating to temperatures (500-520 °C) allows to obtain a heated state two-phase structure of ( α + β) with a sufficiently high number of β phase. Also present particles are not soluble in copper lead. P>
After heating to 800 °C, we find ourselves in single phase β region. The structure of a dispersion (drawing in). P>
was measured hardness Rockwell samples before and after heat treatment. The values ??are presented in Table 5.2. P>
Table 5.2 - The hardness of the samples (HRB), depending on the cooling medium p>
The heating temperature, °Ñ cooling condition water air oven 500-520 61 55 58 650-670 59 54 - 800-820 50 43 33 Note: The initial sample hardness HRB 62
The table shows that the greater the cooling capacity of the medium, the samples exhibit greater firmness. This is due to the fact that, upon rapid cooling increases the number of β'-phase, which increases the hardness of brass, and in some cases improves machining. With slow cooling in the structure shown greater plasticity α phase. With increasing processing temperatures the hardness of brass reduced.
Findings
In this paper we analyzed the impact of heat treatment on the structure and properties of brass LS59-1. P>
The structure of a special two-phase brass LS59-1 a dark matrix of beta-phase (intermetallic ~ CuZn) and formed from her bright isolation alpha solid solution based on copper. Inside some of these particles are not detected in the soluble copper lead which is the last to solidify. These particles serve as nuclei on which the crystals begin to form the alpha phase. P>
It was established experimentally that the cooling down of the medium brass structure becomes more coarse. P>
It was also considered the impact of the cooling medium hardness brass. The greater cooling capacity of the medium, the samples exhibit greater firmness. This is due to the fact that, upon rapid cooling increases the number of β'-phase, which increases the hardness of brass, and in some cases improves machining. With slow cooling in the structure shown greater plasticity α phase. With increasing processing temperatures the hardness of brass snizhaetsya.To i.e. by changing the temperature of heat treatment can not only affect the structural characteristics, but also on the characteristics of hardness. P>
The practical use of brass products are rarely carried out in the mode of high temperature, since the alloy during prolonged thermal exposure, especially in the presence of hot steam, it loses its strength and toughness starting deformed, making it difficult to service.
List of sources
- Brass. Alloy steels [electronic resource]: // Technical Reference, 2005 - Access: http://www.bestreferat.ru/referat-31682.html
- Brass. General characteristics. [Electronic resource]: Technical Reference //, 2004 ã. – ðåæèì äîñòóïà: http://melita.com.ua/latun.html
- Warlimont H. martensitic transformations in alloys based on copper, silver and gold / H.Varlimont, L.Diley. - M .: Science, 1980. - 208 ñ.
- Structural and phase transformations in (α+ β )-brass / [Pugacheva NB, Pankratov AA, Frolov NY, Kotliarov IV.] // Metals.- 2006.- ¹3.- ñ. 65-75
- The properties of brass. [Electronic resource]: technical reference // 2013g.-access mode: http://normis.com.ua/index.php?option=com_c ontent&view=article&id=15&Itemid=21
- Presnyakov AA Brass. Transformations in the solid state, technological properties / Presnyakov AA Chervyakova VV Duysemaliev U.K.- M .: Metallurgy, 1969.- 120 ñ.
- Brass: classification, properties and chemical composition. [Electronic resource]: technical reference // 2013g.-access mode: http://www.dpva.info/Guide/GuideMatherials/Metalls/CooperBronsesAndBrasses/Brass/BrassToGostOverview/
- Kolachev BA Metallurgy and heat treatment of non-ferrous metals and alloys / Kolachev BA VI Elagin, Lebanon VI - M .: MISIS, 2005 . -432 ñ.
- G. Merkulov A.Metallovedenie and thermal processing of non-ferrous alloys: Proc. Benefit / - Krasnoyarsk: Sib. Feder. Univ. 2008. – 312 ñ.
- Lahtin YM Metallurgy and heat treatment of metals / Yu.M.Lahtin. - M .: Metallurgy,1983. – 320 ñ.
- Gulyaev AP Metallurgy / A.P.Gulyaev. - M .: Metallurgy, 1986. – 544 ñ.
- ovikov II Theory of heat treatment of metals / Novikov II - M .: Metalurg³ya, 1986. – 480ñ.
- Database of steels and alloys [electronic resource]: // Technical Reference, 2005 - Access: http://www.splav.kharkov.com/choose_type.php