Реферат за темою випускної роботи
Зміст
- Вступ
- 1. Актуальність теми
- 2. Мета і задачі роботи та заплановані результати
- 3. Методологія модернізації та технічного переозброєння ректифікаційних комплексів хімічних підприємств
- 4. Оптимізація одноколонних ректифікаційних апаратів для хімічних технологій і процесів нафтопереробки
- 5. Переробка хімічних продуктів коксування як спосіб мінімізації негативного впливу на навколишнє середовище
- Висновки
- Перелік посилань
Вступ
Природні енергоносії, такі як нафта, природний газ, газовий конденсат, вугілля мають найважливіше значення в розвитку всіх галузей народного господарства. Високий рівень споживання продуктів нафтопереробки в останнє десятиліття призвела до інтенсивного зростання нафтохімічної промисловості. В даний час гостро постає питання про розширення асортименту товарної продукції, поліпшення її якості та зниження енерговитрат.
Для вирішення цих питань необхідно вдосконалити існуючі та розробити більш ефективні схем поділу та утилізації вуглеводневої сировини, діючого технологічного обладнання та промислових технологій.
Крім цього, на підприємствах, що технологічно потребують теплову енергію цілий рік, важливим і актуальним є організація оптимальної схеми енерго- і ресурсозбереження. В даний час для вирішення цих завдань широко використовуються міні-ТЕЦ, де поряд з електроенергією споживач використовує, тобто утилізує і теплову енергію, підвищуючи тим самим загальний ККД установок. Міні-ТЕЦ є сучасне високотехнологічне та енергозберігаюче обладнання, найбільш прийнятне, з позицій «ефективність–вартість».
1. Актуальність теми
При аналізі та оптимізації складних технічних комплексів, таких як об'єкти нафтопереробної промисловості, основним методологічним прийомом є системний підхід, який дозволяє оцінювати вплив різних чинників на ефективність функціонування хіміко-технологічної системи (ХТС). Завдання оптимізації може вирішуватися як для системи в цілому, так і для її окремих елементів з урахуванням внутрішніх зв'язків між окремими складовими ХТС.
Однією з найважливіших складових технологічного циклу сучасних хімічних і нафтохімічних виробництв є процеси розділення. Прикладом може служити комплекс виділення бензолу на установці каталітичного риформінгу, що включає в собі блоки стабілізації каталізата, екстракції ароматичних вуглеводнів і вторинної ректифікації індивідуальних компонентів. Оптимізації окремих процесів розділення у в промисловості, в тому числі при виділенні бензолу, присвячена велика кількість робіт таких авторів, як В. В. Кафаров, С. С. Хачатрян, А .А. Гайле. Однак комплексного аналізу взаємопов'язаних технологічних блоків промислової установки не проводилося.
З огляду на постійно зростаючий попит на бензол на світовому ринку вуглеводнів (200–300 тис. т/рік), одним із важливих завдань, яке може бути вирішено методами системного аналізу при дослідженні ХТС виробництва бензолу, є підвищення продуктивності діючих установок.
2. Мета і задачі роботи та заплановані результати
Мета роботи полягає в аналізі існуючих і новітніх методів оптимізації режимів роботи ректифікаційного обладнання, яке використовуються в різних процесах хімічної технології, а також у складанні власних алгоритмів.
Задачі, які вирішуються для досягнення зазначеної мети:
- Аналіз технологічних систем по виділенню різноманітних хімічних продуктів.
- Обгрунтування конструктивних характеристик обладнання, що використовуються в технологічних схемах.
- Розробка математичної моделі режимів роботи ректифікаційних колон.
- Складання алгоритмів оптимізації ректифікаційних апаратів.
- Техніко-економічне обґрунтування технічних рішень.
Об'єкт дослідження: процеси розділення речовин в ректифікаційних установках.
Предмет дослідження: апаратурне оформлення процесів розділення речовин.
Наукова новизна роботи полягає в розробці алгоритму оптимізації апаратурного оформлення процесів розділення речовин на основі аналізу різних методів по модернізації існуючих ректифікаційних комплексів і аналізу впливу різних чинників на ефективність процесів.
Практичне значення роботи полягає у використанні результатів роботи для зниження енерго-, і матеріалоспоживання при прийнятті проектних рішень і промисловому впровадженні модернізованих установок.
3. Методологія модернізації та технічного переозброєння ректифікаційних комплексів хімічних підприємств
Основна частка в споживанні енергії в хімічних і нафтохімічних технологіях (до 80%) припадає на систему виділення продуктів з реакційної маси і їх очищення методами ректифікації. Ці комплекси багато в чому визначають вихід і якість товарних продуктів. Як правило, всі вхідні в ректифікаційні комплекси апарати пов'язані між собою матеріальними і енергетичними потоками, що утворюють нерідко технологічні рецикли. Структурна варіантність технологій виділення хімічних продуктів (ТВХП) з однієї і тієї ж реакційної суміші, що впливає як на енергетику, так і на апаратурне оформлення, як правило, велика [1].
Зниження енергоємності, збільшення виходу і підвищення якості товарних продуктів, забезпечення технологічної стабільності і безпеки існуючих та новостворених виробництв може істотно підвищити їх конкурентну здатність і експортний потенціал хімічних і нафтохімічних виробництв.
Разом з тим на нафтопереробних заводах часто виникає необхідність підвищення потужності установок і їх ефективності при збереженні існуючих корпусів колон і технологічної обв'язки. Дані завдання можна вирішити за рахунок модернізації існуючих ректифікаційних комплексів.
При обстеженні діючих виробництв проводиться аналіз структури технологічної схеми, покомпонентного матеріального балансу, режимів роботи кожної технологічної стадії, конструктивних характеристик існуючого обладнання та систем управління. Формулюються (спільно з підприємствами) вимоги до оптимізації виробництв: підвищення виходу і якості продуктів, зниження енергоємності, видалення лімітують домішок і т. д. Отримана в результаті обстеження інформація по структурі технологічної схеми, параметрам процесу, конструктивним характеристикам устаткування і системи керування є основою для розробки оптимальної технології [2].
Наступним і основним етапом при розробці нових сучасних технологій і модернізації існуючих являється апаратно-технологічна оптимізація окремих стадій і технології в цілому при стаціонарних умовах роботи. Причому попередній синтез ТВХП або результати комплексного обстеження діючої технології є в даному випадку першим наближенням для оптимізації. Послідовність робіт даного етапу представлена на рис. 3.1 [3].
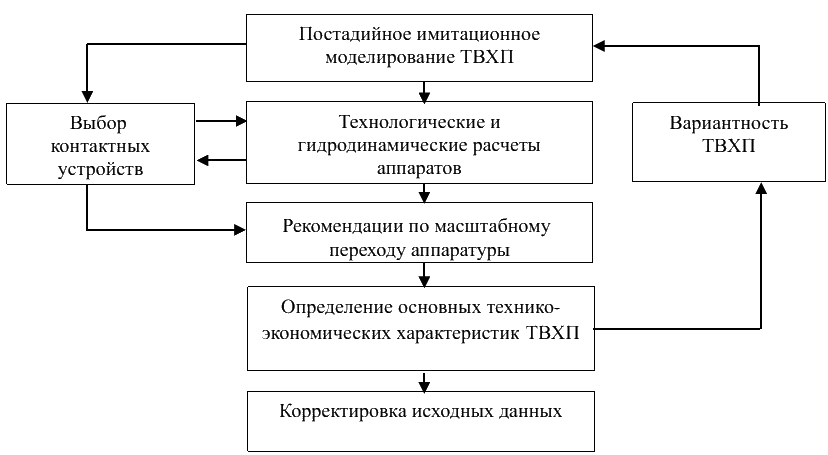
Рисунок 3.1 — Послідовність апаратурно-технічної оптимізації при стаціонарних умовах роботи
4. Оптимізація одноколонних ректифікаційних апаратів для хімічних технологій і процесів нафтопереробки
Оптимізація роботи одноколонного ректифікаційних апаратів безперервної дії — складова частина завдання підвищення ресурсо- та енергозбереження хімічних і нафтохімічних виробництв. У літературі докладно описані методи розрахунку оптимального флегмового числа при заданому ступені розділення [4–8]. Методом сканування при використанні потужної обчислювальної техніки та відомих програмних комплексів (CHEMCAD, ASPEN+ та ін.) Перебравши безліч варіантів, можна вибрати прийнятні для практичної реалізації технологічні режими і ефективність колони.
Використання алгоритмів пошуку оптимуму, з аналізом і експертною оцінкою отриманих результатів на певних етапах, різко скорочує кількість обчислювальних робіт.
Облік ефектів підвищення виходу і чистоти продуктів:
- при їх відборі з ректифікаційних колон у вигляді бічних погонів з формуванням буферної зони певної ефективності між точкою відбору цільового продукту і верхом колони;
- при видаленні проміжних домішок з зон їх концентраційних екстремумів, максимізувати за рахунок оптимізації технологічних режимів і ефективності колони;
- при циклічних відборах домішок при малих величинах відборів (1 ... 5% від подачі живлення), — часто призводить при оптимізації до якісно новим технічним рішенням.
На прикладах розділення метиламінов, ряду фторорганічних продуктів, очищення фурфуролу, отримання метилового, етилового, пропіловий спиртів, поділу продуктів нафтохімії розрахунковими методами встановлено і експериментально підтверджено, що при наявності екстремумів концентрацій домішок по висоті колони їх величина і положення залежать від ефективності колони і технологічних режимів . Підвищення ефективності колони і флегмове чисел призводить до зростання екстремумів концентрацій. Видалення домішок із зони екстремумів у вигляді бічних відборів підвищує чистоту як кубових продуктів, так і дистилятів.
При виділенні хімічних продуктів з реакційних сумішей і їх очищення, коли частка відбору мала (для легколетких і проміжних домішок менше 1%, для висококиплячих домішок, що відбираються у вигляді кубової рідини — менше 5%), використання циклічних відборів при рівних енерговитратах призводить до більш високої ступеня поділу, забезпечує запас технологічної стійкості і більш високу якість продуктів, ніж при постійному відборі [5–7]. Частота і шпаруватість відборів визначаються на основі алгоритмів розрахунку перехідних процесів в ректифікаційних колонах. Типовими прикладами ефективності циклічних відборів є колони виділення легколетких домішок (фурана і ін.) і 1–бутанолу в виробництві ТГФ з фурфуролу, колона відділення легколетких домішок при очищенні ацетону в виробництві ПВ, товарна колона і колона концентрування метанолу у виробництві етилового спирту.
Алгоритм оптимізації одноколонного апаратів, заснований на інтегральному використанні встановлених ефектів, наведено на рис. 3, де R — флегмове число; е — частка відбору дистиляту, кмоль/кмоль; Е — енергія, що витрачається на проведення процесу, кДж; Р — тиск в колоні, МПа; N — ефективність ректифікаційної колони (число теоретичних тарілок); Nf — номер теоретичної тарілки колони (вважаючи знизу), на яку подається живлення.
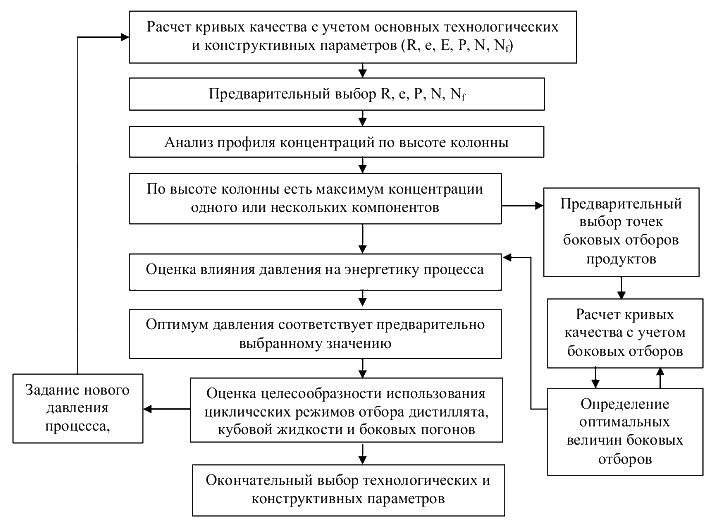
Рисунок 4.1 — Алгоритм оптимізації одноколоних апаратів безперервної дії
Оптимальні характеристики (ефективність колони (Nопт), точки введення харчування (Nf sub>опт), точки і величини бічних відборів продуктів (Nfбо, ебо), флегмовое число (Rопт), частка відбору дистиляту (еопт), тиск процесу (Ропт) визначаються за допомогою побудови і аналізу сімейства «кривих якості». Під «кривими якості» розуміються залежності Еотн = f (N, N/Nf) або N = f (Еотн, N/N f), Еотн = f (Nf), Еотн = f (P), кожна точка яких характеризує сукупність конструктивних і технологічних параметрів, що забезпечують необхідні показники якості товарного продукту, що є постійною величиною для всієї множини точок. Параметр Еотн=(R+1)·e побічно характеризує величину енерговитрат (Е) на ректифікацію [6].
5. Переробка хімічних продуктів коксування як спосіб мінімізації негативного впливу на навколишнє середовище
Коксохімічна промисловість забезпечує ресурсами чорну, кольорову металургію і ряд інших виробництв, де необхідні паливо і відновник, а також є джерелом різноманітної хімічної сировини. Крім коксу, продуктами коксохімії є фракції кам'яновугільної смоли, сирої бензол і ін.
Технології уловлювання хімічних продуктів коксування, їх очищення і переробки вимагають постійного вдосконалення, оскільки далеко не завжди відповідають сучасним вимогам екології і ресурсозбереження.
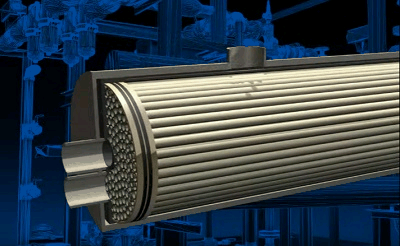
Рисунок 5.1 — Процес розділення коксового газу в ректифікаційній колоні
анімація: 4 кадра, 6 циклів повторення, 143 кілобайт
Для уловлювання сирого бензолу використовується поглинювальна фракція кам'яновугільної смоли. Вона містить безліч компонентів, основними з яких є, нафталін, метилнафталіном, аценафтена. Сорбцію бензолу забезпечує присутність в поглинальному маслі метилнафталіном, а нафталін володіє незначними сорбційними здібностями. Крім того, при адсорбції бензолу відбуваються значні викиди нафталіну в атмосферу. Таким чином, поглотительное масло, що отримується при фракціонуванні смоли, низької якості через високий вміст (до 60% мас.) в ньому нафталіну.
Отримання поліпшеного поглинювального масла на основі поглинювальної фракції кам'яновугільної смоли буде сприяти зниженню викидів нафталіну в атмосферу і отримання його в якості товарного продукту, збільшення абсорбції здатності поглинювального масла. Таким чином, процес «поліпшення» масла передбачає видалення з нього нафталіну.
Нафталін та метилнафталіном мають відносно близькими температурами кипіння (218 °С, 241 °С, 245 °С), тому для виділення нафталіну з поглинальної фракції кам'яновугільної смоли ми пропонуємо азеотропную ректифікацію. Згідно з літературними даними [9], азеотропного агентом може служити капронова кислота, яка утворює азеотропную суміш з нафталіном, а з метилнафталіном суміші зеотропних.
Для створення ректифікаційної схеми виробництва поліпшеного поглинювального масла, перш за все, необхідно було вивчити рівновагу пар–рідина в бінарних системах, утворених компонентами досліджуваної суміші. Це дозволяє вивчити закономірності ректифікованого розділення в обчислювальному експерименті.
Прогнозування рівноваги пар–рідини проводилося за допомогою групової моделі UNIFAC, а опис отриманих псевдоексперіментальних даних здійснювалося з використанням рівняння Вільсона, в результаті чого були визначені параметри бінарного взаємодії речовин в досліджуваній суміші. Залежність пружності пара індивідуальних речовин від їх температур кипіння моделювалася рівнянням Антуана.
Результати математичної обробки — параметри рівняння Вільсона для всіх двокомпонентних систем досліджуваної суміші були покладені в основу розрахунку процесу ректифікації.
Ректифікаційне розділення в обчислювальному експерименті прийнято було проводити на колоні періодичної дії діаметром 1 м. Критерієм параметричної оптимізації режиму роботи колони служив мінімум енерговитрат при заданій якості продуктів розділення. Параметрами оптимізації були: загальна ефективність колони (число теоретичних тарілок) — Nт.т, флегмове число — R, тривалість ректифікаційного розділення — т.
Було поставлено два завдання:
- видалити нафталін з поглинювальної фракції за допомогою азеотропної ректифікації;
- провести регенерацію розділюючого агента;
Регенерація розділюючого агента буде проводитися також шляхом ректифікації при зміні тиску з 760 мм рт. ст. до 20 мм рт. ст.
В ході моделювання нами було виявлено, що азеотропная суміш капронова кислота - нафталін при зниженні тиску збагачується капронової кислотою (рис. 5. 2). При тиску 10 мм рт. ст. відбувається інверсія, суміш стає зеотропних, і нафталін є низко киплячим компонентом. Виходячи з цього, з метою мінімізації витрат розділового агента, було прийнято проводити розділення поглинювальної фракції при тиску 20 мм рт. ст., т. е. тобто суміш ще азеотропна і максимально збагачена нафталіном [10].
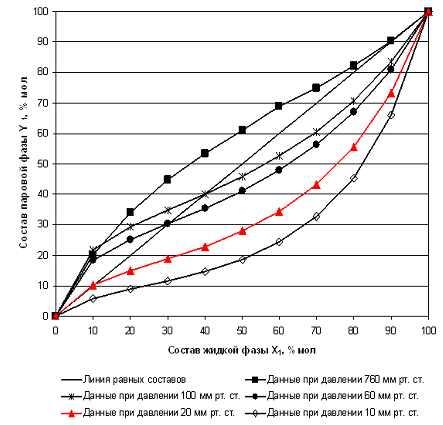
Рисунок 5.2 — Рівновага рідина–пар у системі капронова кислота (1) – нафталін (2)
Пропонується технологічна схема отримання поліпшеного поглинювального масла. Основний розділювальний елемент — колона ректифікації періодичної дії, на якій поперемінно реалізуються процеси відділення нафталіну і регенерації азеотропного агента..
На першій стадії нафталін виділяється у вигляді азеотропної суміші з капронової кислотою в дистилят.
Висновки
При модернізації ректифікаційних комплексів останні необхідно розглядати в нерозривному зв'язку: технологія + апаратура + система автоматичного управління.
Розробка технічних рішень по модернізації ректифікаційних комплексів повинна включати ряд взаємопов'язаних етапів: а) системний аналіз існуючого виробництва; б) аппаратурно-технологічну оптимізацію в умовах стаціонарної роботи з використанням імітаційного моделювання, що включає мінімальний експеримент і оптимізацію чисельними методами; в) забезпечення технологічної стійкості; г) моделювання ситуацій пускового періоду.
Розроблена методологія створення нових і модернізації існуючих ректифікаційних комплексів дозволяє при мінімальних витратах тимчасових і матеріальних ресурсів вирішувати завдання з технічного переозброєння хімічних і нафтохімічних виробництв з вибором економічно оптимальних варіантів.
Під час написання даного реферату магістерська робота ще не завершена. Остаточна дата завершення: червень 2017 року. Повний текст роботи і матеріали по темі можуть бути отримані у автора або його керівника після зазначеної дати.
Перелік посилань
- Леонтьев В. С., Смыкалов П. Ю. Физико-химические и математические основы интенсификации и модернизации технологических процессов и оборудования для технологического перевооружения предприятий химической индустрии // Тезисы докладов V научно-технической конференции «Технохимия — 2003». СПб., 2003. C. 97 – 98.
- Леонтьев В. С., Смыкалов П. Ю. Создание современных экономически оптимальных технологий в химической промышленности и модернизация существующих производств с целью энерго- и ресурсосбережения // Тезисы докладов IV Международной научно-техническая конференции «Технохимия — 2002». СПб., 2002. С. 3 – 4.
- Леонтьев В. С., Шариков Ю. В., Седов В. М. Подход к модернизации и техническому перевооружению ректификационных комплексов в нефтехимической промышленности // Материалы отраслевого совещания главных механиков нефтеперерабатывающих и нефтехимических предприятий России и СНГ. М.: Компрессорная и химическая техника, 2003. С. 110 – 117.
- Анисимов И. В., Бодров В. И., Покровский В. Б. Математическое моделирование и оптимизация ректификационных установок. М.: Химия, 1975, 216 с.
- Бояринов А. И., Кафаров В. В. Методы оптимизации в химической технологии. М.: Химия, 1975. — 575 с.
- Петлюк Ф. Б., Серафимов Л. А. Многокомпонентная ректификация. Теория и расчет. М.: Химия, 1983, 304 с.
- Кафаров В. В. Методы кибернетики в химии и химической технологии. М.: Химия 1985. — 468 с.
- Леонтьев В. С. Разработка оптимальных систем разделения химических продуктов // Тезисы докладов Международной научно-практической конференции «Химия для топливно-энергетического комплекса России». С.-Пб., 2000. С. 92 – 93.
- Огородников С. К., Лестева Т. М., Коган В. Б. Азеотропные смеси. — С-Пб.: Химия, 1971. — 848 с.
- Гарбер Ю. Н., Караваев Н. М., Зыков Д. Д. // Украинский химический журнал, Т. 21, вып. 2, 1955. - С. 177 – 179.