Abstract
Content
- Introduction
- 1. Theme urgency
- 2. Goal and tasks of the research
- 3. Description of the technological equipment and controllers
- 3.1 Description of the pneumatic actuator and compressor
- 3.2 Description of the two–position table
- 3.3 Short description of the programmable logic controller SIMATIC S7–300
- 3.4 Short description of the motion controller SIMOTION C230–2
- Conclusions
- List of sources
Introduction
Control system – this is a set of specialized devices, methods and tools necessary to implement the functions of controlling the movements of working bodies and other technological equipment, as well as changing their sequence and operating mode according to a pre–prepared program.
Automatic control refers to a closed control system when there is a flow of information about the actual behavior of the object that comes from the sensor. At the same time, the control system continuously compares the program signals with the sensor signals about the actual position of the operating device. It is considered that such a system has a full feedback provided that use of this information as a signals, which correct the control process. [1]
1. Theme urgency
At present time, the CAPCS (Computer–Aided Process Control System) is an object of active theoretical research.
Microprocessor is based on the industrial controllers have their own programming languages, which allow to describe a specific process: there are the so called relay languages with Boole operations. Controllers can be programmed with either an Assembler or a high–level language, most often C, followed by compiling and loading control programs into the controller memory. Typical schemes, circuit and software solutions have been worked out, using which the developers do not even emphasize the fact that they create an automated process control system but they are solve simply the current tasks of managing the equipment or process. This indicates that automation has already reached the level of ordinaryity, as, for example, electrification. Nevertheless, new applications or new solutions in this area always attract attention. [2]
2. Goal and tasks of the research
Purpose of the work is a creation the program for control of technological equipment. The technological equipment includes the pneumatic actuator of the manipulator and two–position table.
The development of the control program for the pneumatic actuator of the manipulator will be carried out on the basis of the programmable logic controller (PLC) Simatic S7–300 with the SIMATIC STEP 7 software. A control program for the two–position table will be use the motion controller SIMOTION C230–2 in the SIMOTION SCOUT development environment.
The developed programs will operate synchronously and allow to observe the joint automatic operation of the pneumatic actuator of the manipulator and the two–position table by the example of sorting of technological debris.
3. Description of the technological equipment and controllers
3.1 Description of the pneumatic actuator and compressor
The first object of the technological equipment is the pneumatic actuator of the manipulator, which is shown on Fig. 1.
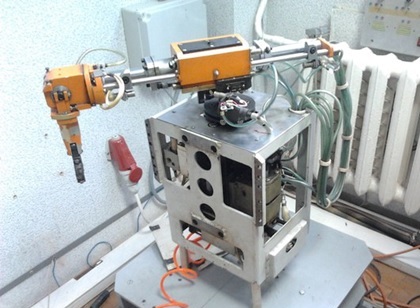
Figure 1 – Pneumatic actuator of the manipulator
This actuator with the help of five on–off pneumatic cylinders performs forward movement of the working bodies. Moving the manipulator forward and backward between the two inductive position sensors, turning the manipulator to the left and right by the distance between the two inductive sensors, raising and lowering the manipulator at a distance between the two inductive sensors, raising the arm of the manipulator and grabbing by it any items.
Compressed air is supplied by an air compressor Rostech
, which is shown on Fig. 2.
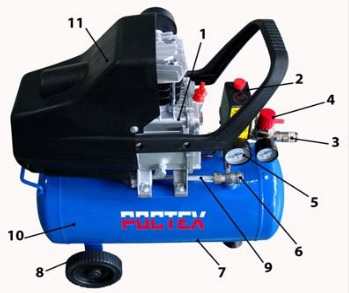
Figure 2 – Air compressor Rostech
;
(1. Compressor; 2. Pressure switch; 3. Outgate; 4. Reducer; 5. Air–gauge of the receiver; 6. Non–return valve; 7. Drain valve; 8. The wheel;
9. Pimping tube; 10. Air receiver; 11. Engine protection cover)
The appearance of the two–position cylinder is shown on Fig. 3
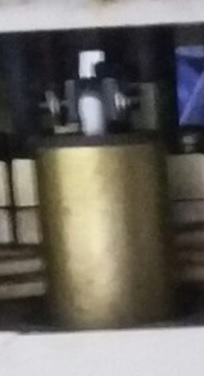
Figure 3 – One of the two–position cylinders of the pneumatic manipulator actuator
Connection of pneumatic cylinders performs, as already mentioned above, between the installation and the module of digital outputs of the controller. Signals coming from the cylinders compel to move the device. There are 2 wires from the cylinders. Blue is the signal wire. White is the Earth
. At the entrance of the digital outputs come blue and white wires. The scheme is shown on Fig. 4.
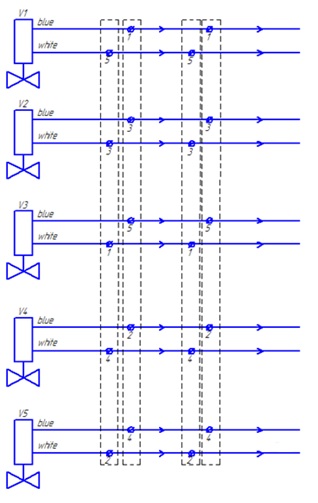
Figure 4 – The electrical connection scheme of pneumocylinders
The figure below shows the appearance of one of the inductive sensors on Fig. 5
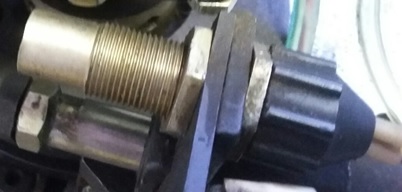
Figure 5 – One of the inductive sensors of the pneumatic manipulator actuator
There are 3 wires from the sensor. Blue – this is a signal wire. Red – this is a power supply wire 24V. White – this is a wire Earth
. At the entrance of the digital inputs comes a blue wire, and the
red and white come to the power supply of controller. The scheme is shown on Fig. 6.
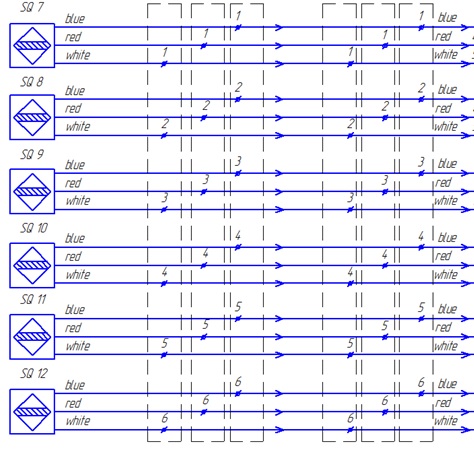
Figure 6 – The electrical connection scheme of inductive sensors of the pneumatic drive
3.2 Description of the two–position table
On Fig. 7 shows the general block diagram of the connection between the two–position table drives, the SIMODRIVE 611 frequency converter, the controller SIMOTION C230–2 and a personal computer. The C230 is connected via the PROFIBUS from the computer with SIMOTION SCOUT. SIMODRIVE is activated by means of an analog value via a cable. The position of the rotor comes from the sensors in analog form to the converter, where it is converted into a sequence of pulses corresponding to the position value and goes to C230 (green cable). Yellow Cables – there are power cables.
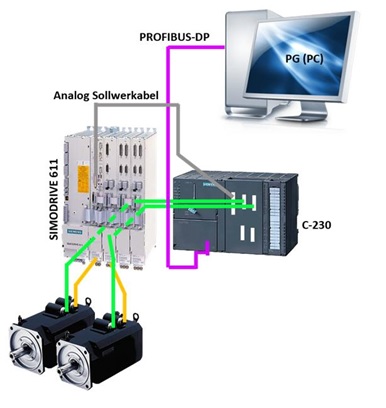
Figure 7 – General structure of the system
The table consists two iron platforms, fixed by two synchronous servomotors on the table top. The drives 1Ft6044 are connected by means of a tap screw on the table top using a special nut. Below on Fig. 8 (left) shows the two–position table and the appearance of the synchronous motor 1Ft6044 on Fig. 8 (right).
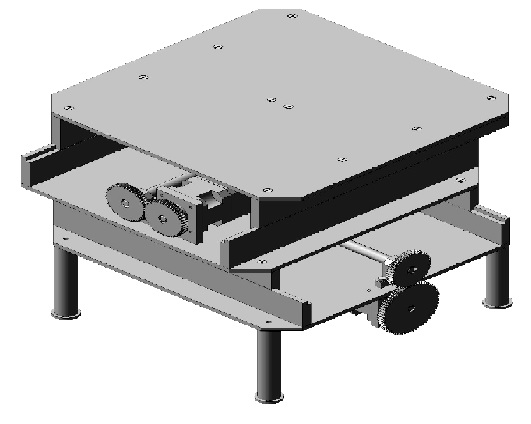
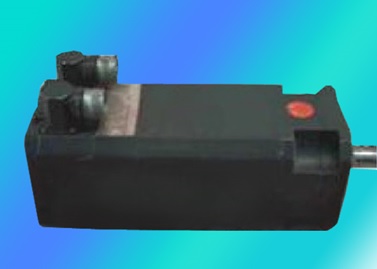
Figure 8 – Two–position table (left) and Synchronous motor1Ft6044 (right)
Like the pneumatic drive of the manipulator, the two–position table has six inductive proximity sensors. A little lower, on Fig. 9 (leftward) presents a photograph of a pair of sensors (photo of the end sensor (leftward) and the reference sensor (rightward)), and the switching plan of the sensor on Fig. 9 (rightward).
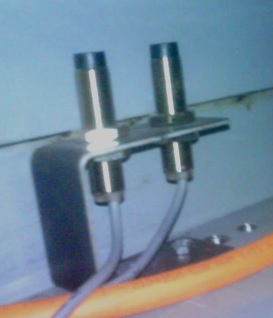
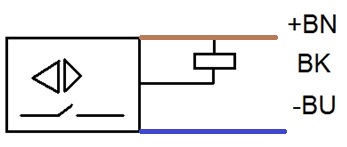
Figure 9 – Photo of a pair of sensors (leftward) and a plan for switching one of the sensors (rightward)
The sensors are connected to the digital inputs of the controller SIMOTION C230–2. BN – this is a brown wire (24V DC power supply is connected to the SIMODRIVE 611
frequency converter), BK – this is a black wire (signal wire, connected to the digital inputs of the controller SIMOTION C230–2), BU – this is a blue wire (Earth
, connects to
the SIMODRIVE 611 frequency inverter and the SIMOTION C230 digital inputs).
On Fig. 10 is shown the electrical connection scheme of inductive table sensors.
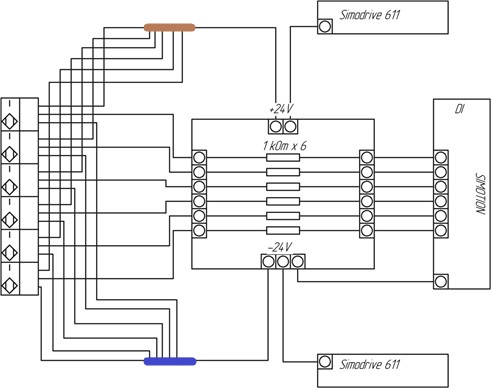
Figure 10 – Electrical connection scheme of inductive sensors
3.3 Short description of the programmable logic controller SIMATIC S7–300
Programmable controller SIMATIC S7–300 has a modular design. The modules from which the required controller configuration is composed can be central (located in the neighborhood of the CPU) or distributed.
The CPU memory is logically divided into areas. The user program is located in the boot memory and in the working memory. Structurally, the boot memory is part of the CPU or a separate embedded memory module. An entering program and the hardware configuration are written to the boot memory.
Working memory is structurally part of the CPU and represents RAM–memory. The RAM contains executable parts of the user program: program code and user data.
The principle of operation of the PLC consists in processing data through the user application program from the input modules (for example, signals from the connected sensors) and then issuing control signals through the output modules and communication modules providing connection of the actuators.
3.4 Short description of the motion controller SIMOTION C230–2
The functions of logic control and motion control are centrally executed in the SIMOTION C controller. The functionality extends from simple positioning to complex motion control.
Motion control with position control:
- Position control with analog reference signal output SIMOTION C The Motion Controller has an analog output for each axis to set the speed and sensor input for the cyclical determination of the true position.
- Pulse position control for stepper drives SIMOTION C The Motion Controller has one pulse output for setting the position of the stepping motor. Stepper drives can be controlled either without a position sensor, or can be adjusted by an external sensor.
- Position control with digital reference output. For this, the PROFIBUS DP interface with the PROFIdrive profile is used. In this case, the set speed value is transmitted via PROFIBUS DP and the current position value is read.
- Position control with mixed method of setting the set point. Actuators with analog reference, step drives and drives on PROFIBUS can be used simultaneously. 4 channels of the integrated interface can be used for step drives or drives with an analog reference.
- Position determination by incremental encoders. Incremental sensors produce counting pulses for the traversed path in accordance with its resolution. As a rule, you need to use the referencing procedure. Can be used: rotating sensors and linear sensors (measuring rulers).
- Determination the position of absolute sensors. Absolute position sensors can be used with serial interface SSI. The use of abstracting is not required. [7]
The SIMOTION concept is part of the global Siemens Totally Integrated Automation (TIA) and is designed to solve the tasks of controlling the movement, rotation, precise positioning and synchronization of several drives.
Conclusions
In this report were considered important aspects of future master's work. Important components and the design of the laboratory bench, which includes the pneumatic drive of the manipulator and the two–position table, were investigated. General information about pneumatic actuators is generalized. The advantages and disadvantages of a pneumatic drive are described. Presented and described the controllers of the family Simatic S7–300 and SIMOTION C230–2. In the future will be developed the system of automatic control of technological equipment using the SIMATIC STEP 7 software and the SIMOTION SCOUT development environment.
During the writing this report, the master's work is not yet complete. Final completion: June 2018. The full text of the work and materials on the topic can be obtained from the author or his supervisor after the specified date.
List of sources
- Основы управления технологическим оборудованием с ЧПУ и подготовки управляющих программ. Электронный ресурс: http://www.nntu.ru
- Автоматизированные системы управления технологическими процессами (АСУ ТП). Электронный ресурс: http://wiki.mvtom.ru
- Энциклопедический словарь. ПНЕВМАТИЧЕСКИЙ ПРИВОД. Электронный ресурс: https://dic.academic.ru
- Пневматический цилиндр. Конструкция пневмоцилиндра. Электронный ресурс: http://www.hydro-pnevmo.ru
- SIMOTION Motion Control System. Электроныый ресурс: http://www1.siemens.cz
- Устройство и принцип работы программируемого логического контролера SIMATIC S7–300. Электронный ресурс: http://studbooks.net
- Контроллер управления движением SIMOTION C230–2 Siemens. Электронный ресурс: http://pzip.ru
- Концепция SIMOTION. Электронный ресурс: http://www.silogic.com.ua
- Методичні вказівки до лабораторного практикуму за курсом
Електромеханічні актуаторні системи
. Мікропроцесорна позиційна система SIMOTION C230–2. Склад.: О.В. Передерій. – Донецьк, ДонНТУ.– 2009.– 100 с.