Зміст
- Вступ
- 1. Актуальність теми
- 2. Обзор роботів – маніпуляторів.
- 2.1.Функціональная схема робота – маніпулятора.
- 2.1.1.Виконавчий механізм.
- 2.1.2. Робочій орган.
- 2.1.2. Приводи.
- 2.2 Опис робота–маніпулятора Manus.
- 3. Мета і задачі роботи, необхідні результати.
- 4. Розробка апаратної частини.
- 5. Опис програмної частини.
- Список джерел
Вступ
На діючих виробничих підприємствах величезними темпами набирає популярність застосування автоматизованих рішень, при яких технологічний процес може здійснюватися без участі людини. При такому рішенні якість виконуваних робіт помітно підвищиться, а також не буде відрізнятися якість виробленої продукції від партії до партії і людський фактор зведеться до мінімуму, так як на всьому виробничому ділянку буде вимагатися лише один оператор, який стежить за справністю роботи виробничих роботів [2].
1. Актуальність теми
Сучасний промисловий робот–маніпулятор застовується для заміни людської праці. Так, робот може використовувати інструментальне захоплення для утримання інструменту і здійснення обробки заготовки, або тримати саму заготовку для подачі її в робочу зону для подальшої обробки.
При застосуванні робота продуктивність зазвичай підвищується, так як робот може виконувати переміщення і позиціонування робочого інструменту значно швидше людини, а також завдяки безперервній роботі робота 24 години на добу без перерв і зупинок, на відміну від людини. При правильному виборі роботизованої системи продуктивність зростає в рази або навіть на порядок, по порівняно з ручним виробництвом.
Замінюючи людину, роботизовані механізми ефективно зменшують витрати виробництва на оплату різного роду фахівців. цей фактор найбільш актуальний в розвинених країнах з високими заробітними платами і необхідністю великих надбавок за переробку. Із застосуванням робота на виробництві необхідно лише наявність оператора, який контролює процес. підвищується якість обробки – промислові роботи мають високу точність позиціонування (0.1 – 0.05 мм) і повторюваність. виключення людського фактора призводить до зменшення різних помилок і збереженню постійної повторюваності на весь період виробництва. Застосування роботів особливо ефективно на шкідливих виробництвах, що роблять негативний вплив на людину, наприклад, в хімічній промисловості. У випадках, коли застосування людської праці обмежується на законодавчому рівні, застосування роботів є найкращим рішенням. Сучасні промислові маніпулятори практично не вимагають обслуговування, за рахунок застосування безколекторних двигунів і передавальних механізмів з високоякісної сталі [2].
2. Обзор роботів – маніпуляторів.
В сучасності промисловий робот & ndash; маніпулятор є механізм, схожий з людською рукою – стандартний антропоморфний робот & ndash; маніпулятор. Даний вид роботу користується найбільшим попитом. Будь–який промисловий робот & ndash; маніпулятор являє собою універсальний механізм, часто, має кілька ступенів свобод (осей рухливості). найбільш поширеними є дистанційно керовані «механічні руки», які встановлюються на нерухомому або рухомому підставі. Однак специфіка різних застосувань промислових роботів змушує виробників розробляти спеціалізованих роботів під конкретні завдання [3].
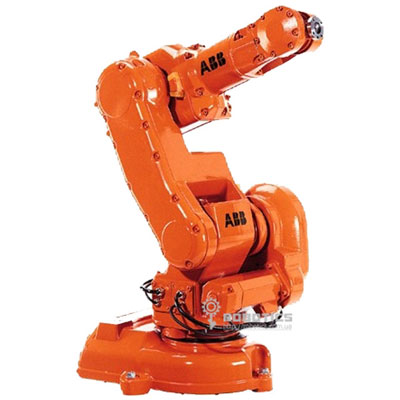
Рисунок 2.1 – Промисловий маніпулятор виробництва ABB
Наприклад, для таких операцій, як укладання матеріалів на палети і транспортери використовуються спеціалізовані роботи & ndash; укладальники. До переваг такого робота можна віднести простоту кінематики, за рахунок чого можливо використовувати одну систему управління для відразу кількох роботів, досить компактні розміри, високу швидкість і енергоефективність. З іншого боку, маючи 4 керовані осі, такі роботи можуть орієнтувати стерпний вантаж всього в 4 & ndash; х горизонтальних площинах [4].
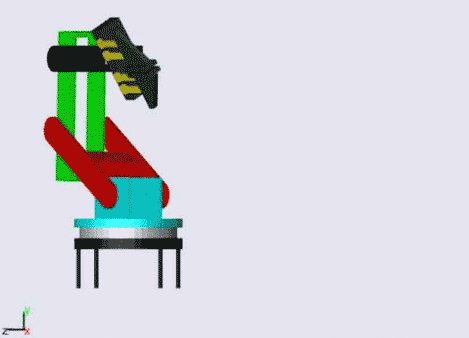
Рисунок 2.1 – Моделювання і візуалізація переміщень маніпулятора в бібліотеці SimMechanics
(анімація: 10 кадрів, 5 циклів, 349 кб)
2.1 Функціональна схема робота & ndash; маніпулятора.
До складу робота & ndash; маніпулятора входить механічна частина (Що включає ланки маніпулятора) і система управління приводами цієї механічної частини. Крім того, на маніпулятор можуть бути додані ограни очувствленія (Формують в сукупності інформаційно & ndash; сенсорну систему), від яких сигнали надходять до системі управління роботом & ndash; маніпулятором.
2.1.1 Виконавчий механізм.
Виконавчий механізм маніпулятора, являє собою відкритий кінематичний ланцюг, ланки якого послідовно з'єднані між собою зчленуваннями різного типу (Обертальні або поступальні). Комбінація і взаємне розташування ланок і зчленувань визначає число ступенів рухливості, а також область дії захоплення робота. найчастіше передбачається, що перші три зчленування у виконавчому механізмі маніпулятора забезпечують транспортні ступеня рухливості (забезпечуючи переміщення робочого органу в необхідне положення), а решта зчленування – реалізують орієнтують ступеня рухливості (орієнтуючи робочий орган відповідно до завдання) [4].
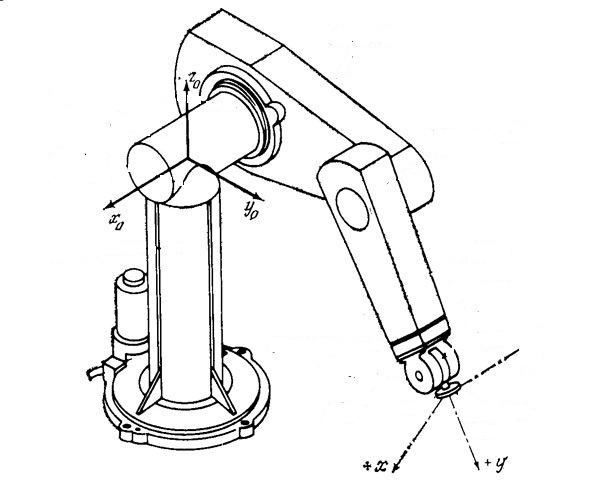
Рисунок 2.2 – Узагальнена схема робота маніпулятора
Залежно від виду перших трьох зчленувань більшість роботів відносять до однієї з чотирьох категорій:
- Роботи, що працюють в декартовій системі координат – роботи, у яких всі три початкових зчленування є прогресивними;
- Роботи, що працюють в циліндричній системі координат – роботи, у яких серед початкових сполучень два поступальних і одне обертальний;
- Роботи, що працюють в сферічній системі координат — роботы, у яких серед початкових сполучень одне поступальне і два обертальних;
- Роботи, що працюють в кутовий, або обертальної, системі координат – роботи, у яких всі три початкових зчленування є обертовими.
Для деяких роботів & ndash; маніпуляторів поділ ступенів рухливості на переносні і орієнтувальні не застосовується. Наприклад маніпулятори з надлишковою кінематикою (З числом ступенів рухливості, більше шести); в таких системах управління переміщенням робочого органу і управління його орієнтацією не розділені за окремими групами зчленувань [4].
2.2.2. Робочий орган.
На крайньому ланці маніпулятора розташовується робочий орган & ndash; пристрій, що виконує спеціальні завдання. У ролі робочого органу можуть бути захватний пристрій або спеціальний інструмент.
Найуніверсальнішим різновидом загарбного пристрою є схват & ndash; пристрій, в якому загарбання об'єкта проводяться за допомогою відносного переміщення частин даного пристрою. Як правило, схват за своєю конструкцією нагадує кисть людської руки: захоплення об'єкта здійснюється з допомогою механічних «пальців». Для захоплення плоских предметів використовуються захватні пристрої з пневматичної присоскою. Застосовують також гаки (для підняття деталей з конвеєрів), черпаки або совки (для рідких, сипучих або гранульованих речовин). Для захоплення ж безлічі однотипних деталей застосовують спеціалізовані конструкції.
За способом управління об'єкта захватні пристрої поділяють:
- схватуючі (механічні тужавіння і пристрої з еластичними робочими камерами, в які нагнітають рідину або стиснене повітря);
- підтримуючі (в них об'єкт не затискають, а застосовують для його утримання нижню поверхню, виступаючі частини об'єкта або наявні в ньому отвори);
- утримуючі (в них на об'єкт надають силовий вплив за рахунок різних фізичних ефектів (вакуумні, магнітні і електростатичні захоплення, адгезія і т. п.).
Число застосувань промислових роботів, в яких схват використовується для утримання робочого інструмента, відносно невелика. У більшості випадків інструмент, потрібний для виконання технологічної операції, кріпиться безпосередньо до зап'ястя робота, стаючи його робочим органом. Це може бути пульверизатор для фарбування розпиленням, зварювальні кліщі для точкового зварювання, зварювальний головка для дугового зварювання, дисковий ніж, дриль, фреза, викрутка, гайковерт і т. д.
2.2.3. Приводи.
Для приведення ланок маніпулятора і пристроїв схвата в рух використовують електричні, гідравлічні або пневматичні приводи. гідравлічні приводи кращі у випадках, коли треба забезпечити значну величину зусиль або високу швидкість; зазвичай такими приводами забезпечуються великі роботи великої вантажопідйомності. Електричні приводи не володіють настільки ж великий силою або швидкодією, але дозволяють домогтися кращих точностних характеристик. Нарешті, пневматичні приводи зазвичай застосовують для невеликих за розмірами роботів, які виконують прості і швидкі циклічні операції. За наявними оцінками, приблизно в 50% сучасних промислових роботах використовується електричний привід, в 30% – гідравлічний і в 20% – пневматичний.
2.3.Опис робота – маніпулятора Manus.
В даному проекті за основу взяті механіка і приводи від робота – маніпулятора Manus. Даний маніпулятор розроблений і виготовлений голландською компанією і призначений для установки на інвалідні коляски.
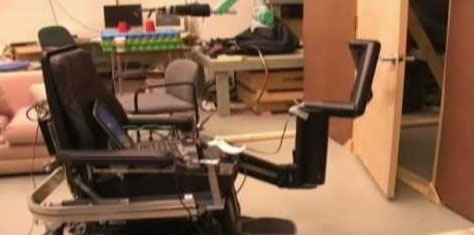
Рисунок 2.3 – Маніпулятор Manus встановлений на інвалідному візку.
Manus може мати власний керуючий комп'ютер і пульт – джойстик для ручного управління, що дозволяє здійснювати дії, не доступні особам з обмеженими можливостями в силу їх фізичних особливостей. Наприклад, цей маніпулятор може подавати різні предмети, віддалені від крісла, в межах зони досяжності маніпулятора. Крім ручного управління з джойстика, комп'ютер (контролер), який обслуговує даний маніпулятор, дозволяє підключати камери і може обробляти отримане зображення за допомогою алгоритмів машинного зору. Дана особливість дозволяє маніпулятору виконувати не тільки задані керуючою особою дії, а й автоматизувати деякі завдання. також керуючий комп'ютер дозволяє поєднувати вищеописані типи управління (в оригінальній документації на Manus даний тип управління називається Collaborative Control). Спільне управління дозволяє домогтися кращих показників в точності позиціювання захоплення маніпулятора за рахунок того, що завдання надходить з джойстика від управляючої особи коригується за певними алгоритмами виходячи їх навколишньої ситуації. Аналіз навколишнього ситуації проводиться за допомогою алгоритмів машинного зору на основі надходженних з камер даних. Такі коригування завдання дозволяють вибрати найбільш оптимальну траєкторію, а також дозволяють автоматично обходити перешкоди [5].
На рисунках 2.4 і 2.5 представлені фотографії нашого екземпляра маніпулятора Manus.
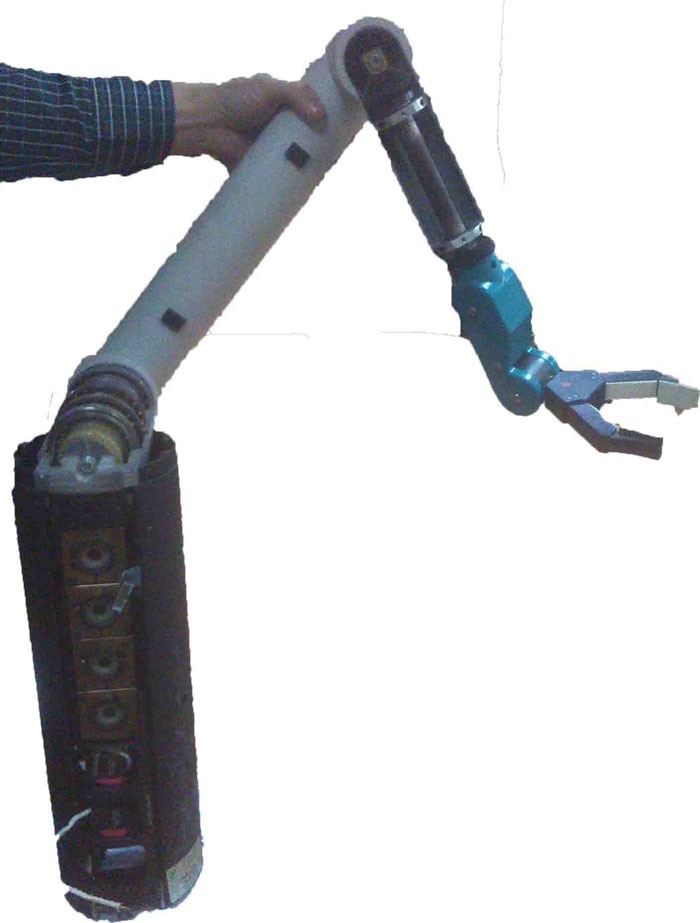
Рисунок 2.5 – Фотографія маніпулятора Manus.
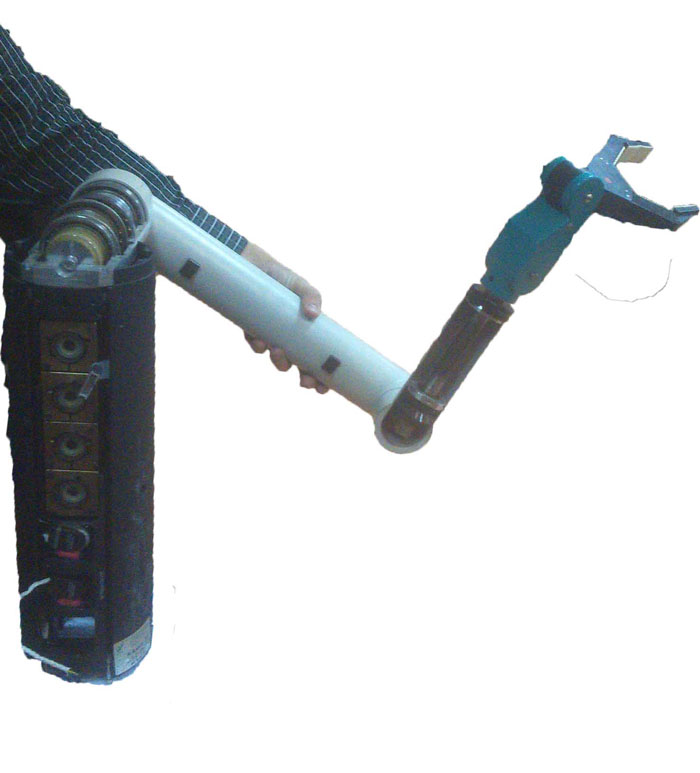
Рисунок 2.5 – Фотографія маніпулятора Manus.
Даний маніпулятор складається з чотирьох рухомих ланок, кожне з яких має свою вісь обертання, а також загарбного пристрої (схвата), закріпленого на кінці останнього з ланок. схват маніпулятора також має вісь обертання. Така конфігурація маніпулятора забезпечує 6 ступенів свободи. Розмір даного маніпулятора можна приблизно оцінити по фотографії, а його вага – близько 15 кг.
Зазвичай, в подібних роботах можуть застосовуватися 2 типу приводів: на базі СДПМ – синхронних двигунів з постійними магнітами, або на основі ДПС – двигунів постійного струму.
У маніпуляторі, розглянутому в даному проекті, застосовуються приводу другого типу – на базі двигунів постійного струму з збудженням від постійних магнітів. Таке рішення має ряд переваг: відносно проста СУЕД в порівнянні з приводами на базі СДПМ, а також значно нижча вартість як самих двигунів, так і силових перетворювачів до них. Крім переваг дана система має недолік & ndash; більш низька динаміка (щодо СДПМ). Однак, у випадку з маніпулятором Manus даний недолік не має ніякого значення, так як робот проектувався для установки на інвалідних візках з метою допомоги обмеженим у рухах людям, а в такому застосуванні висока динаміка системи і не потрібна.
Двигуни всіх зчленувань, застосовані в маніпуляторі Manus – однакові, фірми Maxon серії maxon DC motor. Зовнішній вигляд даного двигуна представлений на рисунку 2.5.
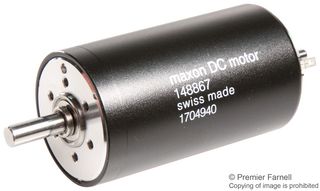
Рисунок 2.5 – Зовнішній вигляд двигунів встановлених в маніпуляторі.
Основні параметри даного двигуна наведені в таблиці 2.1.
Номінальна напруга | 24 В |
Номінальний струм | 0.7 А |
Номінальна швидкість | 8670 об/хв |
Струм холостого ходу | 0.05 А |
Максимальний допустимий струм | 2 А |
Таблиця 2.1 – Параметри двигуна maxon DC motor.
Для передачі обертання від моторів до ланок маніпулятора застосовуються редуктора з планетарною передачею. даний тип редукторів має чимало переваг над іншими, такі як компактність і надійність. Редуктори встановлені на всіх двигунах однакові і мають передавальне число 1: 800.
Крім двигунів і редукторів в вихідну систему електроприводу входять датчики швидкості обертання двигунів, встановлені безпосередньо на валах двигунів. Тип застосовуваних датчиків – інкрементальний енкодер з оптичною комутацією. Роздільна здатність застосовуваних датчиків 100 імп / об, що в цілому є досить маленьким значенням для побудови якісної позиційної системи. Але з огляду на той факт, що датчик встановлений до редуктора, що має передавальне число 1: 800 – такого роздільної здатності буде більш ніж достатньо.
3.Мета і задачі роботи, необхідні результати. .
З урахуванням усього вищевикладеного в дипломному проекті планується розробити систему управління роботом & ndash; маніпулятором, описаним в пункті 2.3.
Задачі магістерського проекту:
- Виконати моделювання електроприводів робота – маніпулятора.
- Виконати моделювання механіки робота – маніпулятора.
- Розробити апаратне рішення (силову частину) для управління приводами робота – маніпулятора.
- Розробити керуючу програму, що дозволяє управляти приводами робота – маніпулятора із забезпеченням підтримки заданого положення для кожного з приводів.
4.Розробка апаратної частини.
Основним елементів апаратної частини є силовий перетворювач – драйвер двигуна. Для управління двигунами постійного струму застосовуються кілька схем, найфункціональніші з яких Н – міст. Узагальнена схема представлена на рис. 4.1.
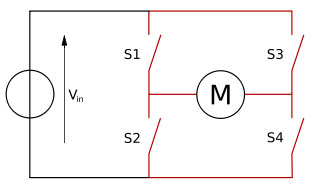
Рисунок 4.1 – Узагальнена схема Н – моста.
Дана схема складається з чотирьох ключів, включених попарно послідовно, між парами включається двигун (Якірний ланцюг). Два верхніх ключа підключаються до позитивної шині джерела живлення, два нижніх ключа – до негативної шині джерела живлення. Для роботи двигуна необхідно, щоб були включені два ключа, наприклад S1 і S4, в такому випадку струм буде протікати від джерела живлення через ключ S1, далі через якір двигуна і через ключ S4. У той же час, два інші ключа повинні бути закриті. Для зміни напрямку струму в якорі двигуна (а, відповідно, і напрямку обертання двигуна) необхідно закрити відкриті ключі S1 і S4, а ключі S2 і S3 відкрити.
Залежно від необхідної швидкості перемикання в якості ключів можуть застосовуватися або реле, або транзистори. У проекті, що розробляється потрібна висока швидкість перемикання (тому що управління двигуном буде здійснюватися з допомогою ШІМ), а, отже, в ролі ключів повинні застосовуватися транзистори.
Необхідну схему можна зібрати з окремих транзисторів. Але це – недоцільно. Тому що на сьогоднішній день набули широкого поширення мікросхеми – драйвери двигунів, які включають в себе необхідну схему Н & ndash; моста, а також обв'язку для силових ключів. Таке рішення спрощує і здешевлює процес розробки СУЕД.
Для розроблювального проекту з наявних на ринку обрана мікросхема драйвера двигуна L298. Структурна схема драйвера l298 показана на рис.4.2.
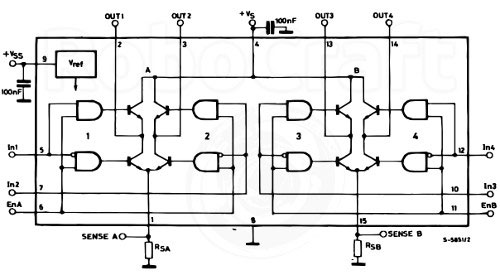
Рисунок 4.2 – Структурна схема драйвера l298.
Виходячи з структурної схеми драйвера видно, що обрана мікросхема містить у собі два мостових драйвера, що дозволяє підключити до одного драйверу два двигуна, що в свою чергу дозволить заощадити місце на друкованій платі драйвера, тому що в проекті, що розробляється використовується 7 двигунів, але мікросхем драйверів досить буде чотирьох. Крім того, дана мікросхема має вивід для підключення датчика струму шунтового типу, що є необхідним в деяких випадках.
У документації зазначено, що для роботи даної мікросхемі потрібно всього кілька зовнішніх елементів, таких як: додаткове джерело живлення 5В (необхідне для живлення логічних ланцюгів всередині мікросхеми), а також 8 зовнішніх діодів, які будуть виконувати функцію захисту драйвера і прийматимуть на себе зворотну ЕРС двигуна. параметри мікросхеми L298 наведені в таблиці 4.1.
Напруга живлення | 5 – 46 В |
Напруга харчування логіки | 5 В |
Струм колектора тривалий | 2 А |
Струм колектора імпульсний | 3 А |
Робоча частота | 25 – 40 кГц |
Вхідна напруга логіки | 3 – 5 В |
Таблиця 4.1 – Параметри драйвера l298.
Критеріями вибору саме цієї мікросхеми служили електричні параметри двигуна, наведені в попередньому розділі, а також той факт, що дана мікросхема найбільш поширена на ринку і, як наслідок, має низьку вартість порівняно з конкурентами.
Для управління даними драйвером потрібно 3 вхідних сигналу, які будуть подаватися від мікроконтролера: 1 – дозвіл роботи, 2 і 3 напрямку обертання двигуна.
Крім силової мікросхеми потрібно також застосування датчика струму, для вимірювання струму якоря. Використання шунтового датчика струму підключеного до спеціального висновку L298 в даному випадку не підходить, так як є два суттєвих нестачі – відсутність розв'язки з силовою схемою і неможливість вимірювання напрямку струму, а тільки його величини.
За перерахованими вище причин вирішено використовувати датчик струму на ефекті Холла. Дані датчики забезпечують гальванічну розв'язку силової частини і вимірюваного виходу, а це означає, що вимірюваний вихід можна підключати до АЦП мікроконтролера без ризику пробою в разі відмови будь & ndash; або компонента.
Из доступних у продажу на момент вибору датчиків струму на ефекті Холла, підходить лише модель ACS758 фірми Allegro Microsystem. Тільки даний датчик має біполярний вхід, що в свою чергу дозволить вимірювати не тільки величину струму, але і його знак. На малюнку 4.3 представлена схема підключення датчика з документації на нього.
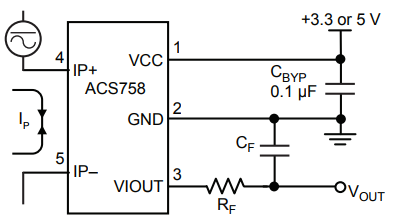
Рисунок 4.3 – Схема підключення датчика ACS758.
Даний датчик працює наступним чином: висновки 4 і 5 включаються в вимірювану ланцюг, на виведення 1 і 2 підключений до джерела живлення, а з виведення 3 знімається напруга, рівень якого пропорційний вимірюваній току. причому, змінюється вихідний сигнал немає від 0 В до напруги живлення, а якось по–особливому закону: нульового вимірюваному току, буде відповідати вихідна напруга рівне половині напруги живлення. А при протіканні струму в вимірювальної ланцюга амплітуда вихідного сигналу буде збільшуватися (Або зменшуватися, залежно від напрямку протікання струму) на значення 40 мВ помножене на 1 А вимірюваного струму. Наприклад: живлення датчика 5 В, при нульовому вимірюваному струмі на виході датчика буде сигнал 2,5 В, а при протіканні струму 10 А в вимірюваної ланцюга, вихідний сигнал датчика буде 2,5 В + 40 мВ.
Ще однією перевагою даного датчика є те, що він може живитися, як від 3.3 В, так і від 5 В, що дозволить застосовувати мікроконтролери різної архітектури.В таблиці 4.2 наведені основні параметри датчика струму.
Максимальний вимірюваний струм | +- 50 А |
Чутливість | 40 мВ/А |
Напруга живлення | 3.3 – 5 В |
Таблиця 4.2 – Основні параметри датчика струму
Так, як максимальний струм використовуваного в проекті двигуна не перевищує 2 А, то можна порахувати, що максимальний діапазон вихідної напруги з датчика струму буде 1.55 – 1.75 В при живленні від джерела 3.3 В. Даний діапазон доцільно буде розширити, тому що АЦП в мікроконтролерах вимірює від нуля до напруги харчування з кінцевим дозволом (наприклад 10 біт), а значить при такому діапазоні точність вимірювання буде низькою, а відповідно і точність регулювання струму також буде низькою.
Для розширення діапазону вихідної напруги застосуємо операційний підсилювач і підключимо його за схемою підсилення зі зміщенням сигналу. Схема представлена на рисунку 4.4 .
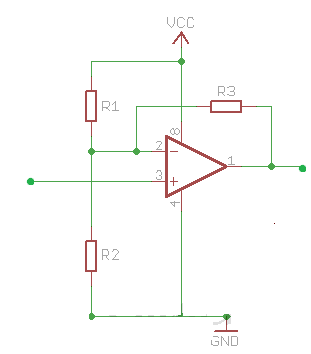
Рисунок 4.4 – Схема включення операційного підсилювача.
Дана схема дозволяє отмасштабовані сигнал з датчика так, що при виході з датчика сигналу 1.55 В на виході операційного підсилювача буде сигнал близький до нуля, а при виході з датчика 1.75 В рівень сигналу з виходу операційного підсилювача буде близький до напруги його живлення, що дозволить підключити його до АЦП мікроконтролера і отримувати більш точні вимірювання. Розрахунок номіналів резисторів в рефераті приводитися не буде. На основі наведених вище висновків і вибору компонентів розроблена загальна схема драйвера двигуна, представлена ??на рис.4.5.
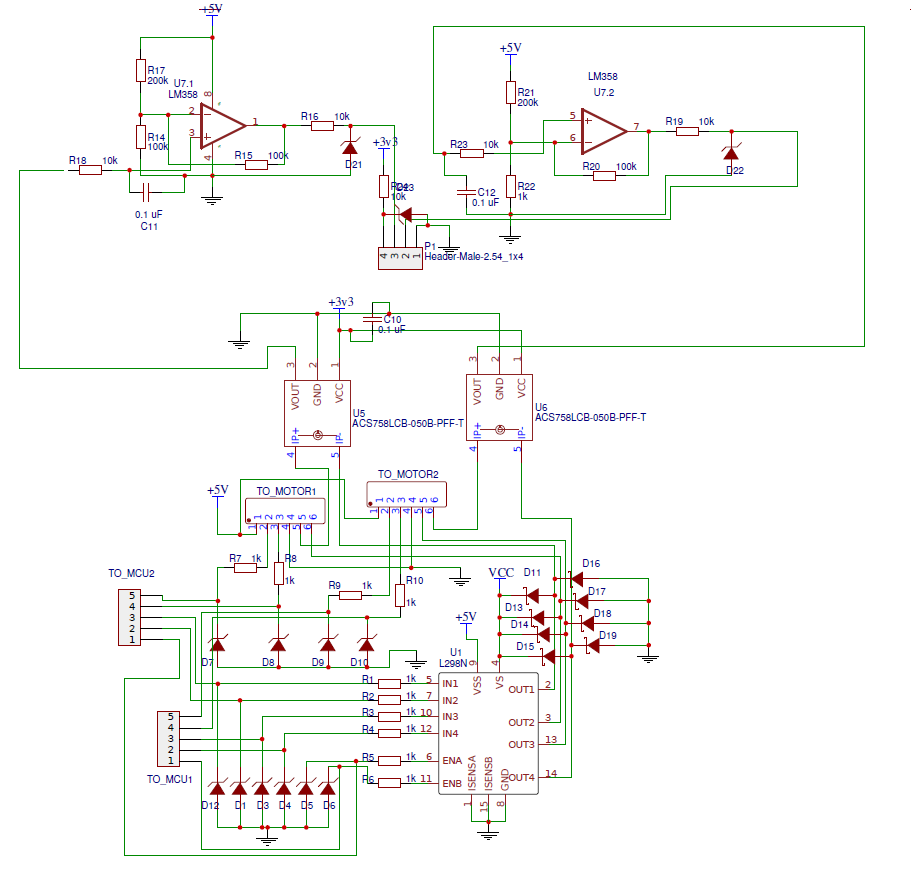
Рисунок 4.4 – Схема драйвера двигуна.
Дана схема включає драйвер для двох двигунів, два датчика струму і два операційних підсилювача. Коннектори TO_MOTOR – роз'єми підключення двигунів і енкодерів, коннектори TO_MCU – роз'єми для підключення до мікроконтролеру, що включають три лінії управління драйвером (описані в попередньому розділі) і дві лінії для сигналів з енкодера. Діоди в обв'язки драйвера – будь–які швидкодіючі діоди на напругу і струм, що перевищують напругу і струм двигуна, стабілітрони по керуючим лініях – захисні стабілітрони з напругою стабілізації, що дорівнює робочій напрузі керуючого мікроконтролера, необхідні для захисту мікроконтролера в разі пробою силового драйвера.
5. Опис програмної частини.
Для управління розробляємим пристроєм необхідно застосування обчислювального пристрою. Таким пристроєм може служити мікроконтролер. Цей мікроконтролер повинен виконувати наступні функції: приймати сигнали зворотних зв'язків за струмом та швидкості двигунів, робити обчислення регуляторів двигунів, управляти двигунами, видаючи керуючі сигнали на драйвери двигунів. Даний мікроконтролер повинен відповідати наступним вимогам:
- В якості датчика швидкості застосований інкрементальний енкодер. Для читання його показань застосовують кілька методів – програмний та апаратний. Програмний метод полягає в ручному опитуванні дискретних входів мікроконтролера і, в залежності від їх стану, відбувається визначення сигналу енкодера. Даний метод не підходить для розробляємої системи, так як потрібно побудувати 7 швидкодіючих САР, а програмний метод сильно витрачає ресурси мікроконтролера і має низьку точність при великому навантаженні на процесор. Тому застосуємо апаратний метод обробки енкодера. Звідси вимога – наявність в контролері НЕ менше 7 зовнішніх переривань або інтерфейсів для енкодера.
- Наявність комунікаційного інтерфейсу для обміну даними з ПК.
- Висока продуктивність.
- Апаратна підтримка обчислень з плаваючою комою.
- Не менш 7 аналогових і 70 дискретних входів.
Найпоширеніші на ринку мікроконтролери – AVR, STM32, TI. Мікроконтролери архітектури AVR не відповідає вимогам 1,4 і 5 тому розглядатися для застосування не будуть.
Мікроконтролери STM32 і TI побудовані на одній архітектурі – Cortex M. Дана архітектура має підтримку всіх ресурсів, необхідних за вимогами. З двох лінійок мікроконтролерів виберемо STM32, так як мікроконтролери TI при тих же характеристиках значно дорожче перше, а також менш поширені в продажу. На сайті виробника мікроконтролерів STM32 можна побачити порівняльну характеристику всіх лінійок і все контролерів серед лінійки. Для розроблюваної системи обрана лінійка контролерів на ядрі Cortex M4, так як лінійки нижче не мають підтримки апаратних обчислень над числами з плаваючою комою, а контролери самої старшої лінійки Cortex M7 коштують значно дорожче і мають надлишкові для розроблюваної СУЕД ресурси.
З лінійки STM32F4 обраний мікроконтролер STM32f407vgt6 так як починаючи з цього контролера є необхідна кількість зовнішніх переривань, а також крім цього є 6 апаратних модулів енкодера, що дозволяє обробляти дані з енкодера, що не задіюючи процесор. Крім того, на базі даного мікроконтролера існує популярна плата для розробників, що включає сам мікроконтролер і необхідний для нього програматор & ndash; відладчик. Застосування такої плати значно спрощує етап розробки мікропроцесорних пристроїв. У таблиці 5.1 наведені основні характеристики обраного мікроконтролера які вплинули на його вибір.
Обсяг пам'яті програм | До 1 Мб |
Об'єм оперативної пам'яті | До 256 Кб |
Напруга живлення | 1.8 – 3.6 В |
Тактова частота | До 168 Мгц |
Вбудований АЦП | 3x12 біт , до 27 каналів |
кількість таймерів | 17 |
Кількість зовнішніх переривань | 16 |
Кількість портів введення виведення | 85 |
Основні інтерфейси передачі даних | UART, USB |
Таблиця 5.1 – Основні характеристики мікроконтролера STM32f407vgt6.
Існують різні методи програмування даного мікроконтролера: мова C і модельно – орієнтований метод. Останній полягає не в написанні коду програми, а в створенні її у вигляді блок схеми (наприклад в середовищі Simulink) і подальшої компіляцією її в виконавчий код для мікроконтролера. Даний метод не доречний при поточному завданні, так як задіє малу частину можливостей мікроконтролера і при цьому код при такій компіляції буде менш оптимальний, тому програмування буде здійснюватися шляхом написання програми на мовою C.
З даними мікро контролером працює безліч IDE, але найпоширенішою є середовище Keil, так так має в своєму складі найбільш потужні інструменти для роботи з МК і має безкоштовну версію.
Крім того, що в даному середовищі можна писати і компілювати код програми, в ній також передбачений Крім того, що в даному середовищі можна писати і компілювати код програми, в ній також передбачений режим налагодження, який дозволяє завантажити програму в контролер і виконувати покроково, зупиняти в будь–якому місці, продовжувати з цього місця, переглядати значення всіх змінних і стан всієї периферії та багато іншого. Даний інструмент значно допомагає в розробці складних систем. Опис процесу програмування в рефераті не наводиться.
Список джерел
- Лекции. Классификации систем координат [Электронный ресурс]. – Режим доступа: http://baumanki.net/lectures/.
- Промышленный робот [Электронный ресурс]. – Режим доступа: https://ru.wikipedia.org/wiki.
- Анализ современного состояния применения роботов в промышленности [Электронный ресурс]. – Режим доступа: https://ru.wikipedia.org/wiki
- А. Г. Схиртладзе, В. И. Выходец, Н. И. Никифоров Классификация и структура промышленных роботов [Электронный ресурс]. – Режим доступа: http://www.metal-working.ru/.
- T. K. Ten. KateF. LiefhebberA. H. G. Versluis J. A. van. Woerden Collaborative Control of the Manus Manipulator [Электронный ресурс]. – Режим доступа: https://link.springer.com/.
- B.J.F. Driessen, ing J.A. van Woerden Enhancing the usability of the MANUS manipulator by using visual servoing [Электронный ресурс]. – Режим доступа: http://citeseerx.ist.psu.edu/.
- D.-J. Kim, R. Hazlett, H. Assistive Robotics [Электронный ресурс]. – Режим доступа: http://eecs.ucf.edu/.
- Анучин А.С. Системы управления электроприводов/ Анучин А.С .: Издательский дом
МЭИ
, 2015. – 43 с. - Манипулятор (механизм) [Электронный ресурс]. – Режим доступа: https://ru.wikipedia.org/wiki/ .
- Fundamentals of robotics / S. Schilling : Издательский дом
Prentice hall
, 2005. – 90 с.