Реферат по теме выпускной работы
Содержание
- ВВЕДЕНИЕ
- 1. АКТУАЛЬНОСТЬ ТЕМЫ
- 2. АНАЛИЗ СУЩЕСТВУЮЩИХ СПОСОБОВ И ОБОСНОВАНИЕ ПРИНЯТЫХ РЕШЕНИЙ
- 2.1. Прессование, как один из способов переработки дискретных материалов.
- 2.2 Прессование сыпучих материалов
- 2.3 Тепловые процессы при холодном прессовании дискретных материалов
- 2.4 Особенности деформирования дискретных материалов
- 3. АНАЛИЗ ПРЕССУЕМОСТИ ДИСКРЕТНЫХ МАТЕРИАЛОВ
- 3.1 Схемы и конструктивный анализ прессового оборудования
- СПИСОК ЛИТЕРАТУРЫ
Цель магистерской работы заключается в исследовании прессования дискретных материалов для усовершенствования прессового оборудования. В промышленности дисперсные системы занимают чрезвычайно важное место в связи с их распространением и разнообразным применением, исключительной ролью в природных явлениях и процессах, в повседневной техногенной деятельности человека и вместе с тем в связи с весьма специфическими физико-механическими свойствами.
С появлением новых инновационных идей, прогрессивных ресурсосберегающих технологий и новой техники важным аспектом научно-технического прогресса является появление новых способов получения материалов и изделий с заданными или принципиально новыми свойствами, параметрами и качеством.
Прессование часто является основным процессом при получении дисперсных материалов, таких, как бетоны, лакокрасочные материалы, высоконаполненные резины и пластики, гетерогенные твердые ракетные топлива, керамические и металлокерамические материалы, бумага и картон, искусственные кожи и множество других материалов [3]. Актуальным также является прессование угольных шламов и мелких классов угля. Полученные брикеты могут быть использованы в качестве топлива для сжигания в бытовых и промышленных топках. Прессование угольной пыли и измельченной угольной фракции выполняется на двух-валковых прессах.
В зависимости от вида угля и связующего в технологии бывает необходимо специальным образом охлаждать и выдерживать готовый брикет некоторое время в специальных бункерах, в течение которого брикет приобретает прочность. Время выдерживания индивидуально и определяется на этапе тестирования. Топливный брикет обладает высокими потребительскими свойствами, повышает экономическую эффективность работы предприятия при рациональном использовании его вторичных угольных ресурсов. В большинстве случаев процесс брикетирования угля происходит с добавлением связующего (угольный пек, нефтяной битум, смола, меласса и известь, лигносульфонат, крахмал, полимеры.) что делает брикет более высокого качества . В отдельных случаях брикетирование возможно также и без связующего, но при этом значительно повышаются энергозатраты. Основными достоинствами являются высокая производительность, низкое удельное энергопотребление, высокая надёжность, долгое горение, постоянство температуры при сгорании. Рассмотрим процесс прессования на примере получения угольных брикетов (Рис 1.).
Из обезвоженного угольного шлама и/или угольной мелочи с содержанием воды с добавлением лигносульфоната (сухого или жидкого), в результате чего получают бездымное, прочное и водостойкое топливо. Предложенный способ обеспечивает снижение первоначальных капитальных затрат, уменьшение потребляемой при производстве энергии, повышение производительности, улучшение потребительских свойств топливного брикета за счет повышения его прочности, водостойкости и полноту выгорания угля в брикете.
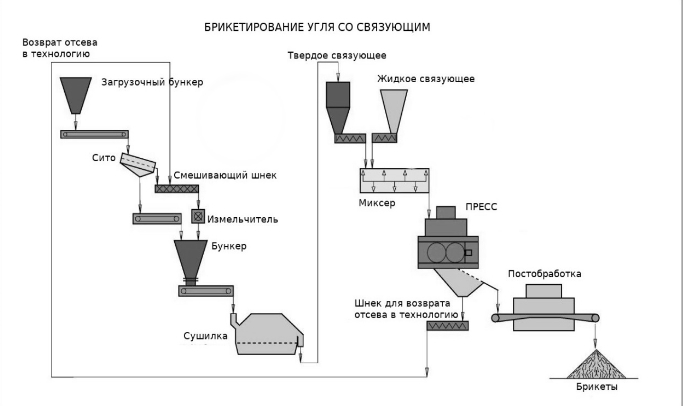
Способ получения угольных брикетов [2]включает обезвоживание угольного шлама, перемешивание угольных частиц и минеральной составляющей исходного шлама, последующее формование обезвоженной указанной массы с гранулометрическим составом; дополнительно угольный шлам содержит не менее 25% спекающихся углей. При этом получают угольный брикет прочный, пористый, водостойкий, с малым содержанием влажности, органических и летучих веществ, который имеет рациональную формообразующую поверхность. Высокая механическая прочность, водостойкость брикета из угольного шлама обеспечивают его хорошую сохранность при транспортировке и при неблагоприятных атмосферных воздействиях. Кроме того, брикет имеет теплотворную способность выше, чем у исходного шлама, что связано с пониженным содержанием в нем влажности, органических и летучих веществ при термообработке. Пористость брикетов обеспечивает полное выгорание угля при сжигании брикетов. При сгорании брикета обеспечивает пониженное содержание выбрасываемых в атмосферу вредных веществ. Брикеты могут использоваться в энергетических целях и в комунально-бытовом секторе, а зольный остаток в строительстве и других отраслях. Угольный брикет содержит минимальное количество вредных веществ, и обеспечивает исключительную экологическую безопасность при использовании. Угольный топливный брикет - экологически чистый продукт и горит практически бездымно, он является хорошим топливом для использования в жилых помещениях. Добавки в брикеты предназначены для повышения их экологичности (связывая соединение серы в зольном остатке) и улучшения потребительских качеств (цвет горения, запах).
Прессование сыпучих материалов — физико-механический процесс, основанный на свойстве сыпучих тел уплотняться под действием внешней нагрузки. Сыпучий материал состоит из двух фаз: твердой, содержащей некоторое количество влаги; газообразной, заполняющей пространство между частицами. Количественное соотношение этих фаз до прессования и после связано с получением продуктов прессования (гранулы, брикеты) необходимой прочности. В зерноперерабатывающей промышленности прессованию подвергают отруби, лузгу и комбикорма. Процесс получения крупных прессованных брикетов носит название брикетирования, более мелких-гранулирования.
Существует ряд гипотез, объясняющих процесс прессования сыпучих материалов (капиллярная, коллоидная, молекулярная и др.). Наибольший интерес представляет молекулярная гипотеза, основанная на термодинамической теории аутогезии, согласно которой объединение частиц происходит под действием молекулярных сил. Величина сил молекулярного притяжения зависит от природы контактирующих поверхностей и их геометрической характеристики. Действие сил молекулярного притяжения при сближении частиц проявляется практически мгновенно. Давление прессования необходимо для сближения частиц и создания достаточного числа контактов между ними.
Число контактов зависит от дисперсности прессуемого материала. Поэтому при прочих равных условиях тонкое измельчение исходных материалов позволяет получать более прочные гранулы. На прочность гранул и удельные энергозатраты влияет длина пути основного этапа — прессования (цилиндрическая часть фильеры). Чем больше длина фильеры, тем прочнее получаются гранулы и менее проявляются их релаксионные свойства. На характер процесса оказывают большое влияние влажность прессуемого материала и величина зазора между матрицей и роликами. Биохимические изменения при пропаривании и прессовании сводятся к некоторому изменению соотношения крахмала, белков, активности ферментов и витаминов.
В начальный период прессования до толщины брикета [4], продукт сжимается без особых усилий (первая стадия прессования). Затем увеличение давления хотя и приводит к дальнейшему уменьшению высоты брикета, но этот процесс идет с медленней (вторая стадия). Наконец, даже значительное повышение давления уже не приводит к сколько-нибудь заметному изменению высоты брикета. Высота брикета при снятии давления увеличивается и продолжает увеличиваться с течением времени, в результате появления упругих деформаций и расширения запрессованного в продукте воздуха. В процессе прессования необходимо стремиться к увеличению показателя В и снижению Е. На показатели В и Е оказывают влияние как условия процесса, так.и физико-химические свойства продуктов.
К числу первых относят давление прессования, продолжительность выдерживания продукта под давлением, кратность нагружения, температуру рабочих органов и материала, конструктивные особенности и техническое состояние рабочих органов. Среди второй группы факторов можно выделить химический состав продуктов, их дисперсность, коэффициенты внутреннего и внешнего трения, гигроскопические свойства, количество и свойства связующих веществ. С увеличением давления прессования повышается плотность и прочность прессованных продуктов, большая продолжительность выдерживания продукта под давлением вызывает релаксацию напряжений в нем, снижение коэффициента упругого расширения брикета. Важным фактором, влияющим на протекание процесса прессования, является температура продукта. Повышение температуры способствует миграции влаги, пластифицирует продукт, снижая величину Е, химический состав продуктов также влияет на прочность брикетов. Продукты, содержащие много клетчатки, образуют менее прочные брикеты или гранулы. Более прочные гранулы образуют материалы с высоким содержанием белка и крахмала.
Операция формования является одной из важнейших в технологическом цикле. Под прессованием (формованием) металлических порошков подразумевается операция, в результате которой под действием приложенных сил из бесформенного сыпучего порошка получается относительно прочное тело – прессовка, которая по форме и размерам близка к форме и размерам готового изделия с учетом допусков на усадку и калибровку, а если необходимо, то и на механическую обработку. Различают холодное (при комнатной температуре) и горячее (при повышенных температурах) прессование. Холодное прессование в закрытых пресс-формах – наиболее распространенный прием. При засыпке порошка в пресс-форму его частицы располагаются хаотически, образуя при этом так называемые мостики или арки. Плотность засыпанного порошка в этом случае не увеличивается. Приложение внешнего давления незначительной величины к такому свободно насыпному порошку приводит к резкому повышению его плотности. Это объясняется тем, что в начале формования частицы заполняют пустоты и поры. По мере увеличения прилагаемого давления мостики и арки разрушаются и частицы проникают в мелкие поры. На дальнейших этапах формования происходит качественное и количественное изменение границ между частицами: от трения частиц при перемещении друг относительно друга удаляются окисные пленки, контакты между частицами в этих местах из неметаллических переходят в металлические. В результате чего повышается прочность заготовки, затем происходит хрупкое разрушение частиц порошков из твердых металлов и пластическая деформация частиц из мягких металлов.
Перспективно применение гидростатического прессования. Сущность такого прессования состоит в том, что порошковая шихта, засыпанная в эластичные оболочки, всесторонне обжимается жидкостью (водой, маслом) при давлении выше 1000–2000 атм. После холодного прессования металлокерамические заготовки обладают чрезвычайно низкими механическими свойствами и в некоторых случаях могут снова рассыпаться в порошок при самом незначительном усилии нажатия.
Для повышения механической прочности и придания изделиям необходимых физико-химических свойств спрессованные заготовки подвергаются термической обработке – спеканию. При спекании в порошковом изделии происходит:
1) изменение формы и размеров частиц и увеличение их контактной поверхности; контакт между частицами из окисного превращается в металлический;
2) снятие остаточных напряжений, возникающих при прессовании за счет упругих свойств частиц порошка;
3) объединение частиц порошка и изменение соотношения объема между порами и компактным металлом частиц.
Последний процесс чувствителен к состоянию поверхности частиц порошка. Окисная пленка препятствует их коагуляции. Поэтому спекание проводят в вакууме или в защитной атмосфере (инертные газы, окись углерода, азот). Горячее прессование – это разновидность формования порошков, когда процессы прессования и спекания совмещены во времени. При сравнительно малых давлениях прессования имеется возможность получать почти беспористые изделия с плотностью, недостижимой при раздельном ведении процессов прессования и спекания.
-Температурно-скоростные режимы:
Горячее прессование чаще всего осуществляется в закрытых пресс- формах в области температур, составляющих 0,5–0,8 от абсолютной температуры плавления основного порошка.
-Силовые условия прессования:
При выборе оборудования, расчете и конструировании пресс-форм необходимо учитывать вид порошка и способ подготовки шихты к формованию. Химический состав, физические и технологические свойства порошков оказывают влияние на процесс формования, следовательно и на выбор оборудования.
-Прессовый инструмент:
Инструмент для прессования изделий должен обеспечивать точность размеров изделий, обладать высокой прочностью, чтобы противостоять весьма большим напряжениям, возникающим при прессовании, обладать высокой жесткостью во избежание деформаций, приводящих к трещинообразованию в прессовках и повышенному износу инструмента, иметь высокую поверхностную твердость, чтобы противостоять износу, иметь минимальные допуски на формообразующие размеры, иметь высокую чистоту поверхности, обеспечивать высокую производительность, быть долговечным в работе. К инструменту относятся детали пресс-форм технологического назначения: матрицы, пуансоны, стержни. Рассмотрим принципы конструирования этих наиболее ответственных деталей пресс-форм. Матрицы в пресс-формах применяются трех видов: сплошные, составные и сборные. Составные и сборные матрицы могут быть как цельные, так и разрезные. Разрезные матрицы, в свою очередь, бывают разъемными и неразъемными. При конструировании разрезных матриц необходимо правильно выбрать число разрезов и их места. При проектировании калибровочных матриц большое значение имеют форма, длина и угол заходного и выходного конусов. Вкладыши – это детали (или деталь) матрицы, пуансона или стержня, образующие либо формующую полость (вкладыши матрицы или пуансона), либо формующий элемент пуансона, матрицы или стержня, создающий углубления в прессуемом изделии. Основные требования, предъявляемые к прессовому инструменту, в полной мере относятся и к калибрующему (точность размеров, чистота поверхности, необходимые твердость, прочность и жесткость)
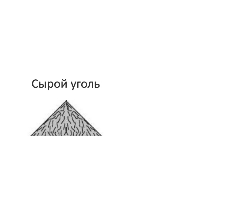
Способы прессования, применяемые в промышленности, отличаются способами на-грева материала, его ввода в форму и после¬дующего формования: прямое (компрессион-ное), литьевое (трансферное) и непрерывное профильное (штранг-прессование). В процессе прямого (компрессионного) прессования (рис.1a) подготовленный к прессованию материал 2 (пресс-порошок) до¬зируется и поступает в матрицу пресс-формы З, в которой осуществляется процесс формова¬ния изделия 5, после чего изделие удаляется из матрицы выталкивателем 4. Литьевое (транс¬ферное) прессование (рис. 1, 6) отличается от прямого тем, что расплавленный в загрузоч¬ной камере пресс-материал 1 под действием давления, передаваемого пуансоном 2, через литниковые каналы 3 поступает в предвари-тельно сомкнутую форму, где он отверждается в изделие 4. Непрерывное профильное прессование, или штранг-прессование, применяется для получения профильных погонажных изделий.
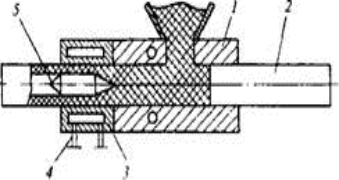
Постоянного сечения выдавливанием расплава пресс-материала плунжером 2 через формующий инструмент, образованный мундштуком 3 и торпедой 5 (рис 2). Привод плунжера 2 обеспечивает его возвратно-поступательное движение. Прогрев материала происходит при помощи системы обогрева 4 и за счет сдвиго¬вых деформаций при его выдавливании. Прессование слоистых пластиков, пред¬ставляющих собой композиционные материа-лы и состоящих из наполнителя и связующего, чаще всего термореактивных смол, осуществ¬ляется на многоэтажных гидравлических прес¬сах. В результате получают пластики различ¬ные по толщине: текстолит, стеклотекстолит, асботекстолит, гетинакс, декоративный слои¬стый пластик, древесный слоистый пластик. Конструкции прессового оборудования. Прессы - машины статического действия, предназначенные для формования изделий из пресс-материалов путем приложения давления. Разнообразные современные конструкции прессового оборудования могут быть клас¬сифицированы по ряду признаков.
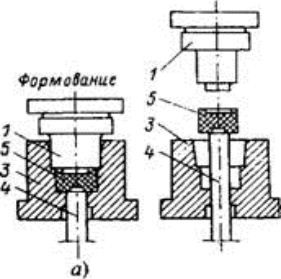
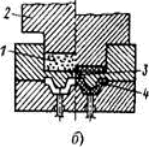
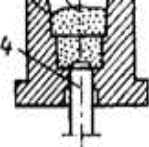
Наиболее распространенным прессовым оборудованием являются прессы с гидравлическим приводом, которые обладают значитель¬ными преимуществами перед другими пресса.
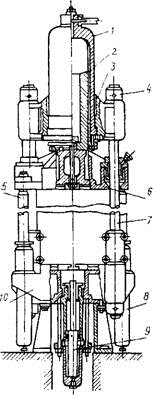
В гидравлическом колонном прессе с верхним расположением рабочего цилиндра (рис. 4) рабочая жидкость (эмульсия или масло) Сила прессования - один из основных параметров пресса. Гидравлический пресс, как правило, включает следующие основные механизмы и детали: станину, систему цилиндров (рабочий, возвратный, выталкивающий) с плунжерами или поршнями, подвижные и неподвижные поперечины, гидроагрегат, состоящий из насо¬сов, трубопроводов и распределителей потока жидкости. По направлению действующей силы прессования гидравлические прессы подразде-ляют на вертикальные, горизонтальные и угло¬вые. В зависимости от конструкции станины прессы бывают колонные, рамные и челюстные. Колонные прессы обеспечивают хороший доступ к пресс-форме, однако имеют значи¬тельные габаритные размеры и металлоем¬кость.а также малую жесткость. Эти недостат¬ки отсутствуют в прессах рамной конструкции (рис. 5). В верхней части рамы 1 жестко закреплен рабочий гидроцилиндр 9 с диффе¬ренциальным поршнем 8 двойного действия. Плита 7 движется по направляющим 5 под действием соединенного с ним поршня 8. В нижней части рамы расположен стол 4 и вытал¬киватель 2. Для ограничения хода ползуна б и штока выталкивателя 2 служат выключатели 3. Достоинством пресса с нижним располо¬жением рабочего цилиндра является его устой¬чивость (так как центр тяжести расположен достаточно низко), небольшие габаритные раз¬меры, возможность применения съемных форм с большой силой прессования. Прессование слоистых пластиков проводят на этажных прессах колонной конструкции с нижним рас¬положением рабочего гидроцилиндра 1 (рис. 5).
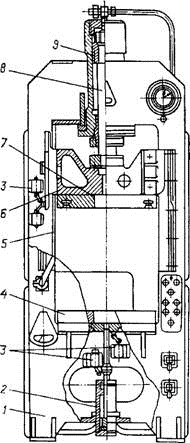
Станина пресса должна быть достаточно прочной и жесткой, чтобы обеспечить требуе¬мую точность взаимного расположения меха¬низмов пресса и относительного положения инструмента и обрабатываемого объекта при динамических нагрузках.
Участок колонны между нижней и верхней плитами в связи с деформацией плит и эксцентричным их нагружением работает не только на растяжение, но и на изгиб. Кроме того, на колонны действуют пульсирующие нагрузки, поэтому выполняется расчет и на их усталость . Колонны обычно изготовляют из стали Ст5 или низколегированных сталей. При этом коэффициент запаса прочности принимают равным 2,0...2,2
При написании данного реферата магистерская работа еще не завершена. Окончательное завершение: июнь 2018 года. Полный текст работы и материалы по теме могут быть получены у автора или его руководителя после указанной даты.
- Металлические порошки и порошковые материалы: справочник /Б.Н. Бабич, Е.В.Вершинина, В.А. Глебов и др.; под ред. Ю.В. Левинского. –М.: ЭКОМЕТ, 2005. – 520с.: ил.
- Оборудование и оснастка для формования порошковых материалов.Клячко Л.И., Уманский А.М., Бобронов В.Н. М.: Металлургия, 1986, 336 с.
- Барков, Н.А. Технология прессования: Метод.указания к лабораторным занятиям покурсу «Технология прессования» для студентов специальности 110600 «Обработка металлов давлением» / Сост. Н.А. Барков, С.Б.Сидельников, С.В. Беляев и др.– Красноярск: ГУЦМиЗ, 2004. – 36 с.
- Носков В.А., Ващенко С. В. Об использовании принципа многоступенчатого уплотнения при брикетировании мелкофракционных шихт // Фундаментальные и прикладные проблемы черной металлургии: сб. научн. тр. Выпуск 4. К.: Наукова думка. – 1999. – С. 285.
- А. с. №1473246 (СССР) / В.А. Генетов, М.Г. Скляр, Э.И. Торяник, А.А.Тараканов, В.Н.Шмадченко, Ф.С. Щелкунов Опубл. в Б. И., 1991, №22.
- А. с. №1189686 (СССР) / Л.С. Грешнов, И.И. Фетисов, В.Ф. Брыкалин, В.В. Борисейко, Н.П. МарукОпубл. в Б. И., 1988, №40.
- А. с. №2190877/27 (СССР) / М.Д. Петров Опубл. в Б.И., 1977, №9. .