Реферат по теме выпускной работы
Содержание
- Введение
- 1. Цели и задачи исследования
- 2. Анализ конструктивных особенностей систем для быстрой смены дозирующих и погружных стаканов
- 3. Разработка усовершенствованного устройства дозирующих и погружных стаканов
- 3.1 Исследование энергосиловых параметров системы быстрой смены дозирующих и погружных стаканов
- 3.2 Математическое моделирование термических напряжений в огнеупорных элементах устройства для быстрой замены стаканов - дозаторов промковшей МНЛЗ
- 4. Заключение
- Список источников
Введение
Современное металлургическое производство требует постоянного повышения эффективности систем для быстрой смены дозирующих и погружных стаканов в процессе непрерывной разливки длинными и сверх-длинными сериями на МНЛЗ. Основными требованиями к таким системам являются: надежность работы в условиях длительного воздействия высоких температур; способность конструкции противостоять значительным нагрузкам, при выполнении технологических операций; простота в обслуживании и эксплуатации.
1. Цели и задачи исследования
Целью настоящего исследования является разработка и обоснование конструктивных и энергосиловых параметров системы быстрой смены дозирующих и погружных стаканов, при функционировании которой исключался бы тяжелый физический труд обслуживающего персонала МНЛЗ, сокращалось время проводимой технологической операции, минимизировались энергетические затраты на ее выполнение и рационально использовалось, свободное место на рабочей площадке.
Для достижения поставленной цели необходимо решить следующие задачи:
2. Анализ конструктивных особенностей систем для быстрой смены дозирующих и погружных стаканов
Наиболее широко используемыми на металлургических предприятиях являются устройства фирм: INTERSTOP, VESUVIUS и IFGL, конструктивные схемы которых показаны на рис. 1 – 3.
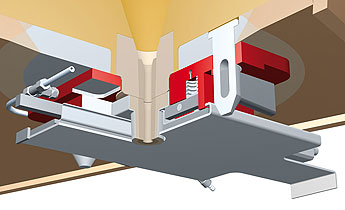
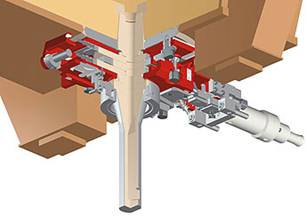
Рисунок 1 – Система компании INTERSTOP
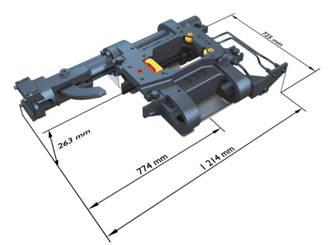
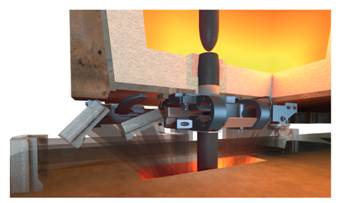
Рисунок 2 – Система компании VESUVIUS
Одними из главных недостатков в указанных системах являются сложность конструктивных решений при разработке и обслуживании узла прижатия стакана-дозатора к верхнему базовому огнеупорному блоку. Конструкция требует тщательного подбора всех устанавливаемых пружин для обеспечения одинаковых упругих характеристик, а также проведения их регулярного контроля.
Анализ возможности выполнения операций по настройке и обслуживании, что у систем, разработанных фирмами INTERSTOP и VESUVIUS (рис.1, рис. 2), осуществление контроля силы упругости, развиваемой каждой пружиной, и ее замена при выходе из строя возможны только после снятия всего устройства с ковша и полной его разборки на стенде в мастерской.
Система, предложенная фирмой IFGL (рис.3), позволяет выполнить контроль упругих характеристик пружин непосредственно на ковше, одна-ко для их замены требуется частичная разборка узла прижатия сменного огнеупорного элемента.
Опыт эксплуатации таких устройств показал, что показатели эффек-тивности их применения существенно отличаются. Главной причиной это-го является отсутствие в технической литературе методик для расчетов и оптимизации рабочих параметров разливочных систем данного класса, что в свою очередь приводит к разрушению сменного дозирующего элемента.
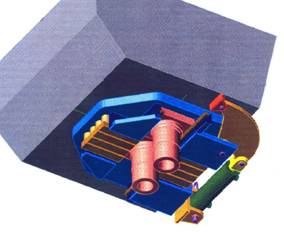
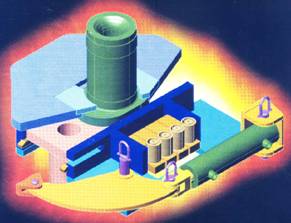
Рисунок 3 – Система компании IFGL
3. Разработка усовершенствованного устройства дозирующих и погружных стаканов
В результате анализа достоинств и недостатков существующих уст-ройств, а также на основании результатов лабораторных исследований и математического моделирования напряженно-деформированного состояния элементов конструкции сотрудниками кафедры «Механическое оборудование заводов черной металлургии имени профессора Седуша В.Я.» ДонНТУ была предложена новая конструкция устройства для быстрой замены стаканов-дозаторов рис.4 [1].
Устройство состоит из металлического корпуса 3, который винтами 4 крепится к наружной поверхности днища промежуточного ковша 2. В корпусе 3 размещен огнеупорный гнездовой блок со сталевыпускным стаканом 1 промежуточного ковша. В корпусе 3 размещен сменный огнеупорный стакан-дозатор 12, который имеет возможность перемещения съемным силовым гидроцилиндром 5. Прижатие стакана-дозатора к гнездовому блоку осуществляется механизмом, включающим поворотные элементы 11, установленные на осях 10 по обеим сторонам стакана-дозатора 12. Для передачи силы прижатия к стакану-дозатору 12 поворотные элементы 11 кинематически взаимосвязаны с пружинами 8, размещенными на направляющих стержнях 9 в горизонтальных цилиндрических каналах, выполненных в металлическом корпусе блока 6. На внутренних поверхностях этих каналов нарезана резьба для ввинчивания пробок 7. Для вращения пробки на выходящей наружу тор-цевой части предусмотрен либо шлиц под отвертку, либо головка под ключ.
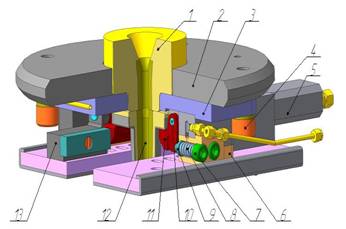
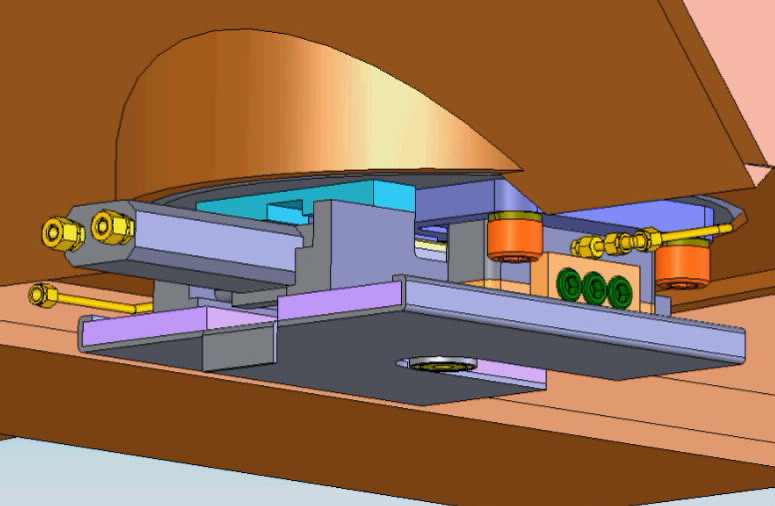
Рисунок 4 – Система ДонНТУ
Во время дозированного перелива стали из промежуточного ковша в кристаллизаторы МНЛЗ при необходимости замены вышедшего из строя стакана-дозатора резервным, осуществляют запуск гидропривода, силовой цилиндр которого проталкивает дозирующие элементы на расчетное рас-стояние, в результате чего новое огнеупорное изделие занимает место отработанного.
Благодаря усовершенствованию конструкции опорного узла разливочной системы, отпала необходимость в ее полной разборке при осуществлении контроля силы, развиваемой каждой из пружин, или в случае их замены. Кроме этого, удалось расширить допустимые пределы отклонения жесткости упругих элементов от заданного значения, так как предлагаемая конструкция позволяет выполнять индивидуальное регулирование силы воздействия пружины на дозирующий стакан, не снимая разливочное уст-ройство с ковша.
При обслуживании разливочной системы для контроля жесткости пружин в отверстие каждого из поворотных элементов поочередно вводят хвостовик динамометрического ключа и, поворачивая элемент на оси на небольшой угол, определяют обеспечиваемую пружиной упругую силу как показано на рис. 5. В случае отклонения этой силы от заданного значения, необходимо повернуть в нужном направлении пробку, сжимая или ослабляя пружину. Если после такой регулировки все же не удается достичь желаемого результата, пришедшую в негодность пружину заменяют новой, вывинтив полностью из резьбового гнезда пробку [2].
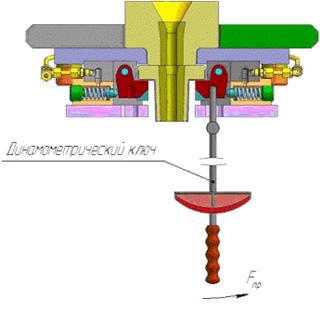
Рисунок 5 – Схема контроля упругой силы, развиваемой пружиной узла прижатия стакана-дозатора
Благодаря своим конструктивным особенностям предлагаемое устройство значительно проще в обслуживании и эксплуатации в сравнении с известными зарубежными аналогами, так как позволяет осуществлять контроль и регулирование силы, развиваемой каждой из пружин, производить при необходимости их замену без снятия разливочной системы с ковша и проведения ее полной или частичной разборки. Кроме того, данное устройство обладает универсальной конструкцией и может быть трансформировано для обеспечения быстрой замены погружных стаканов, применяемых для защиты стали от вторичного окисления на участке промежуточный ковш – кристаллизатор слябовых МНЛЗ.
3.1 Исследование энергосиловых параметров системы быстрой смены дозирующих и погружных стаканов.
Данные устройства в конструктивном исполнении идентичны двух-плитному скользящему затвору, однако использование для расчета сило-вых характеристик их приводов зависимостей, полученных для затворов шиберного типа [3], не представляется возможным, так как скоростные режимы работы упомянутых разливочных систем практически несопоставимы. При одинаковом рабочем ходе подвижных частей у обеих систем, составляющем 120-130 мм, продолжительности их перемещения из одного крайнего положения в другое отличаются на порядок, так как плита затвора совершает полный ход за 3-7 с, а стакан-дозатор – за 0,3 - 0,5 с.
Резкое нарастание скорости движения отработанного и резервного стаканов-дозаторов в начальной стадии процесса их смены, обеспечиваемой гидравлическим приводом, влечет за собой развитие динамических нагрузок, действующих на элементы конструкции разливочного устройства. Установление и учет характера изменения статических и инерционных сил, преодолеваемых приводом, позволит обосновать и оптимизировать значения его энергосиловых параметров, что в конечном счете будет способствовать повышению надежности и экономичности всей двигательной системы, а также развитию теоретических основ ее расчета [4]. Достичь поставленной цели можно лишь, основываясь на известных методах решения задач динамики привода гидромеханических систем, применяемых в металлургии [5, 6], и дополнив их новыми положениями, разработанными с учетом специфики функционирования устройств дозированного перелива стали из промежуточных ковшей МНЛЗ. Учитывая экстремальные условия эксплуатации сталеразливочного оборудования и связанные с ними трудности использования контрольно-измерительных средств для получения данных о силовом нагружении натурного образца во время выполнения операции по замене вышедшего из строя огнеупорного элемента, требуемую информацию о значении и характере нарастания сил технологического сопротивления установили по результатам поставленных специальных экспериментальных исследований. Для их проведения спроектировали и изготовили физический аналог системы быстрой смены стакана-дозатора промежуточного ковша сортовой МНЛЗ (рис. 6), который в конструктивном отношении и по масштабу в точности соответствовал реальному образцу и отличался лишь способом обеспечения силы прижатия сменного огнеупорного элемента. Контролируемую силу воздействия на опорную поверхность его металлической обоймы развивали с помощью набора грузов, навешиваемых на два рычага. За счет изменения массы грузов и длины рычагов достигали строгой фиксации в широком диапазоне значений силы прижатия стакана-дозатора, что позволяло повысить точность проводимых измерений.
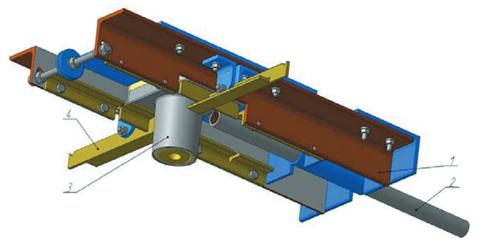
Рисунок 6 – Физический аналог промышленного устройства для быстрой замены стаканов-дозаторов
3.2 Математическое моделирование термических напряжений в огнеупорных элементах устройства для быстрой замены стаканов - дозаторов промковшей МНЛЗ
Наиболее термически нагруженным элементом конструкции являет¬ся стакан-дозатор, поэтому на первом этапе исследований было принято решение рассмотреть распределение температур в нем. Стакан-дозатор представляет собой элемент, состоящий из металлического кожуха, сред-ней огнеупорной части и циркониевой вставки, материалы которых имеют разные теплофизические свойства. Учитывая длительность процесса раз-ливки длинной серией, в ходе моделирования рассматривалась стационар-ная задача теплопроводности. При этом температурное поле стакана опи-сывается уравнением теплопроводности:
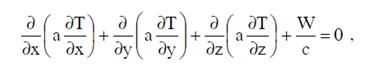
где а - коэффициент температуропроводности, отражающий теплоинерционные свойства в рассматриваемой точке стакана-дозатора; а = л/с;
с, л - объемная теплоемкость и коэффициент теплопроводности материалов стакана;
Т - температура в рассматриваемой точке стакана-дозатора;
х, у, г - координаты рассматриваемой точки;
W - мощность источника тепла.
Температурное воздействие на стакан оказывается струей жидкой стали, проходящей через канал, а также излучением зеркала металла, нахо-дящегося в кристаллизаторе.
В виду сложной пространственной конструкции стакана, решение задачи выполнялось с помощью прикладного пакета ANSYS, реализующе¬го метод конечных элементов [7]. Так как стакан-дозатор является осесим¬метричным элементом, то для расчета была создана геометрическая мо¬дель, соответствующая четверти стакана (рис.7 а). В качестве граничных условий использовались следующие: на поверхности сталеразливочного канала - конвективная теплоотдача от жидкой стали с температурой 1600°С (коэффициент теплоотдачи 0,27 МВт/(м2•К) [8]); на нижней поверхности цилиндрической части - теплоотдача излучением с плотностью теплового потока 20 кВт/м2 [8]; на внешней поверхности кожуха стакана - конвек¬тивная теплоотдача в окружающую среду (температура воздуха принята 30 0С). В ходе моделирования рассматривались два варианта (№»1 и №2) кон¬струкции стакана-дозатора, отличающиеся высотой борта кожуха. При этом конечно-элементные модели (рис.7 б) состояли из 33775 и 33499 эле¬ментов соответственно.
В результате выполненных расчетов получено распределение темпе-ратурных полей в конструкции стакана-дозатора (рис.8).
Как можно увидеть, наибольшую температуру имеет циркониевая вставка, далее в средней части происходит интенсивное падение температуры. Температура кожуха находится в диапазоне 60 ... 250 °С.
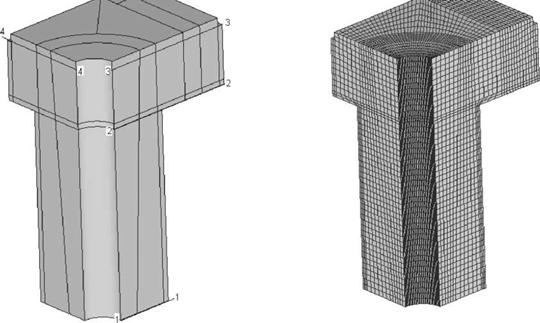
Рисунок 7 – Геометрическая модель (а) и конечно-элементная модель (б) стакана-дозатора (1, 2, 3, 4 характерные сечения)
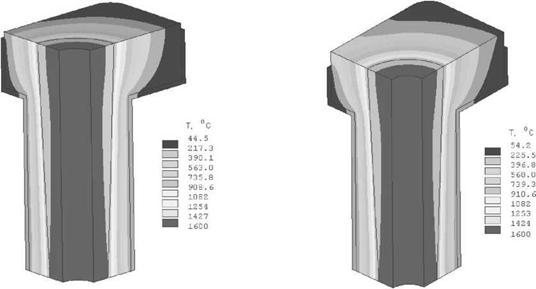
Рисунок 8 – Картины распределения температурных полей в стакане-дозаторе: а) вариант № 1; б) вариант № 2
Графики изменения температур вдоль отдельных сечений показаны на рис.9. Следует отметить, что в целом распределение температурных полей подобно для обоих вариантов конструкции стакана, но для варианта №2 (с коротким бортом кожуха) температура кожуха на 10-17 0С выше.
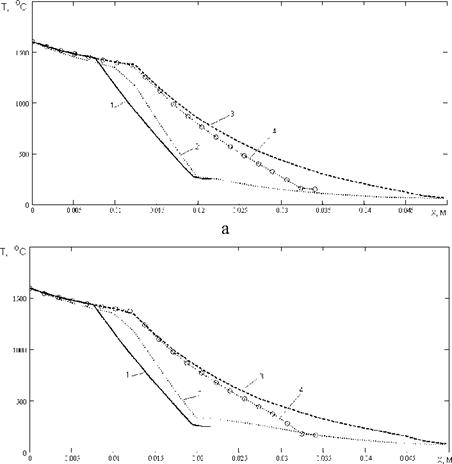
Рисунок 9 – Изменение температуры в характерных сечениях стакана дозатора (1, 2, 3, 4 - характерные сечения): а) вариант №1; б) вариант №2
Под действием температурных полей в конструкции стакана-дозатора возникают термические напряжения, которые описываются соот-ношениями Дюгамеля-Неймана [9]:
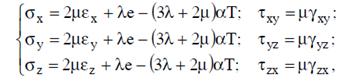
где Єх, Єу, Єz - нормальные напряжения вдоль оси х, у z соответственно;
Тху, Туz, Тzх - касательные напряжения;
Ех, Еу, Еz - относительные линейные деформации по оси х, у z соот-ветственно;
Уху, Ууz, Уzх - относительные угловые деформации;
л, у - коэффициенты Ляме, зависящие от коэффицента Пуассона у и модуля упругости Е материалов стакана-дозатора:
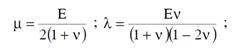
е - объемная деформация: е = Ех + Еу + Еz;
с - коэффициент линейного расширения материалов стакана- дозатора;
Т - температура в рассматриваемой точке конструкции.
Задача о напряженно-деформированном состоянии стакана-дозатора, вызванного температурными воздействиями, также решалась с помощью пакета ANSYS. При этом в качестве нагрузки использовались температу-ры, полученные для каждого узла конечно-элементных моделей, а ограни-чения на перемещение были заданы на верхней поверхности стакана-дозатора, являющейся местом контакта с базовой огнеупорной плитой, размещенной во фланце днища промежуточного ковша.
В результате расчета получено распределение напряжений в теле стакана-дозатора (рис.10).
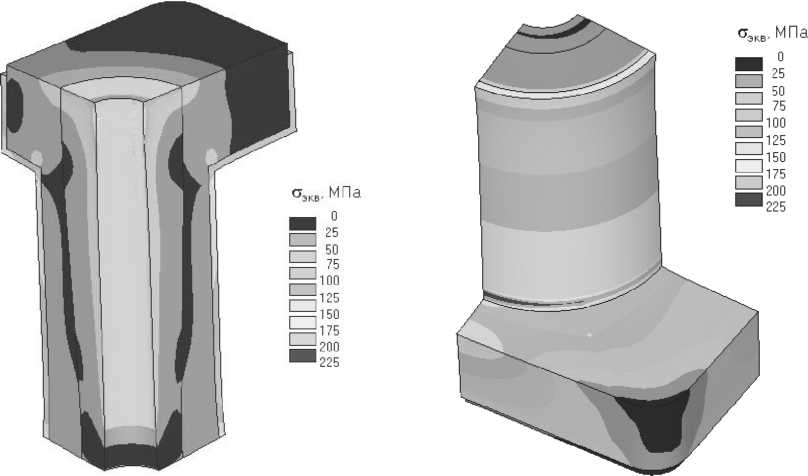
Рисунок 10. Картины распределения эквивалентных напряжений
в стакане-дозаторе
Установлено, что максимальные эквивалентные напряжения в огне-упорных частях стакана не превышают 37 МПа, а в металлическом кожухе - 210 МПа, что ниже допускаемых значений - 52 МПа и 240 МПа. Для конструкции стакана с коротким бортом (вариант № 2) напряжения в це-лом на 5..10 % выше. Максимальные напряжения возникают на поверхно-сти стакана-дозатора, обращенной к зеркалу металла в кристаллизаторе, а также на кожухе в месте соединения цилиндрической и плоской частей. Максимальные линейные деформации в направлении осей x и у (расшире-ние конструкции) достигают 1 мм, а в направлении оси z (удлинение кон-струкции) не превышают 2 мм. Полученные расчетные значения деформа-ций огнеупорного элемента учитывали при назначении конструктивных размеров и гарантированных зазоров в опорных и направляющих узлах механической системы опытно-промышленного образца разработанного разливочного устройства [9].
4.Заключение
В результате проведенного анализа достоинств и недостатков сущест-вующих систем быстрой смены стаканов, а также на основе результатов практических и лабораторных испытаний, разработан новый вариант системы быстрой смены стаканов-дозаторов. Применение предлагаемого устройства позволит упростить его обслуживание и эксплуатацию в сравнении с известными зарубежными аналогами.
При написании данного реферата магистерская работа еще не завершена. Окончательное завершение: июнь 2018 года. Полный текст работы и материалы по теме могут быть получены у автора или руководителя после указанной даты.
Список источников
- Пат. 74507 Украины, В 22 В 41/56. Устройство для смены стаканов-дозаторов промежуточного ковша машины непрерывного литья заготовок. Опубл. 15.12.2005. Бюл. № 12.
- Совершенствование конструкции устройства для быстрой смены стаканов-дозаторов промковша МНЛЗ / С.П. Еронько, А.Н. Смирнов, Д.А. Яковлев и др. // Металлургическая и горнорудная промышленность.— 2006.м №8.— С. 107-109.
- Еронько С. П. Расчет энергосиловых параметров ковшовых затворов // Металлургическая и горнорудная промышленность. – 2007. – No 3. – С. 104-108.
- Большаков В. И. Исследование динамических нагрузок металлургических машин // Захист металургійних машин від поломок. Межвузівський тематичний збірник наукових праць. – Маріуполь: ПДТУ, 1999. – С. 6-14.
- Кожевников С. Н., Пешат В. Ф. Гидравлический и пневматический приводы металлургических машин. - М.: Машиностроение, 1977. – 310 с.
- Праздников А. В. Гидропривод в металлургии. – М.: Металлургия, 1973. – 336 с.
- Каплун А.Б., Морозов Е.М., Олферьева М.А. ANSYS в руках инженера. - М.: Едиториал УРСС, 2003. - 272 с.
- Огурцов А.П., Жульковская И.И., Кулик А.Д. Расчет температурного состояния ковшового шиберного затвора при различных способах разливки стали // Изв. ву¬зов. Черная металлургия. - 2001. - №4. - С.11- 15.
- Устройство для быстрой замены стаканов-дозаторов промежуточного ковша сортовой МНЛЗ/ С.П. Еронько, А.Н Смирнов, Д.А. Яковлев и др. // «Черметинформация». Бюлл. « Черная металлургия». – 2007. – №2 – С. 70-73.