Тема: Методы контроля металлопроката
Цель испытания материалов состоит в том, чтобы оценить качество материала, определить его механические и эксплуатационные характеристики и выявить причины потери прочности. Механические свойства характеризуют способность материала сопротивляться деформации и разрушению под действием приложенных нагрузок.По характеру изменения во времени действующей нагрузки механические испытания могут быть статическими (на растяжение, сжатие, изгиб), динамическими (на ударный изгиб). По воздействию температуры на процесс их делят на испытания при комнатной температуре, низкотемпературные и высокотемпературные (на длительную прочность, ползучесть)Статические испытания проводятся при воздействии на образец с определенной скоростью постоянно действующей нагрузки. Скорость деформации составляет от 10-4 до 10-1 с-1. Статические испытания на растяжение относятся к наиболее распространенным. Свойства, определяемые при этих испытаниях, приведены в многочисленных стандартах по техническим условиям на материалы. К статическим относятся испытания на растяжение, сжатие, изгиб.Динамические испытания характеризуются приложением к образцу ударной нагрузки и значительной скоростью деформации. Длительность испытания не превышает сотен долей секунды. Скорость деформации составляет около 102 с-1. Динамические испытания чаще всего проводят по схеме ударного изгиба образцов с надрезом.Испытания на твердость.Простейшим механическим свойством является твердость. Методы определения твердости в зависимости от скорости приложения нагрузки делятся на статические и динамические, а по способу ее приложения - на методы вдавливания и царапания. Методы определения твердости по Бринеллю, относятся к статическим методам испытания.Твердость - это способность материала сопротивляться вдавливанию в него более твердого тела (индентора) под действием внешних сил.При испытании на твердость в поверхность материалов вдавливают шарик (индентор), в связи с чем различают методы испытаний, соответственно, по Бринеллю. При испытании материалов на твердость не изготавливают стандартных специальных образцов, однако к размерам и поверхности образцов и изделий предъявляются определенные требования.
Испытание на растяжение материалов проводят в соответствии с ГОСТ 1497-84 «Методы испытаний на растяжение». Стандарт устанавливает методы статических испытаний на растяжение черных и цветных металлов для определения при температуре 20 °С пределов пропорциональности, упругости, текучести, временного сопротивления разрыву, относительного удлинения и относительного сужения, модуля упругости.Для испытаний применяют плоские и цилиндрические образцы, выре-занные из детали или специально изготовленные. Размеры образцов регламентированы указанным стандартом, они подчиняются геометрическому подобию и могут быть короткими и длинными. Цилиндрические образцы на нашем предприятии вытачивают из круга образца берется соотношение начальной рабочей длины l0 и исходного диаметра d0: l0= 5d0- короткий образец, l0= 10d0 - длинный образец. Для плоского образца берется соотношение рабочей длины l0 и площади поперечного сечения F0:l0= 5,65vF0 - короткий образец, l0= 11,3vF0 - длинный образец. Цилиндрические образцы изготавливаются диаметром 3 мм и более. Образцы состоят из рабочей части длиной l0 и головок, форма и размер которых соответствуют захватам машины (рис. 2).
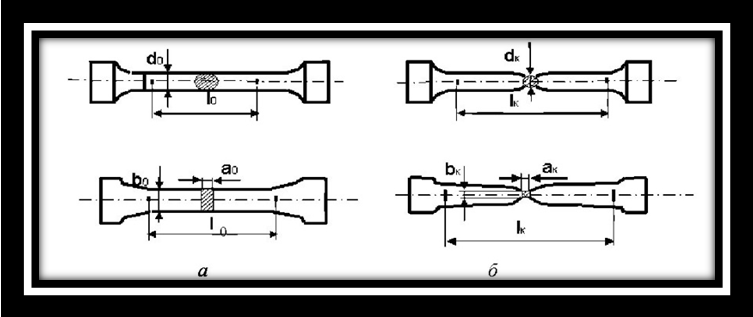
Рисунок 1 – Цилиндрические и плоские образцы до (а) и после (б) испытания на растяжение
Растяжение образца проводят на специальных машинах, позволяющих фиксировать величину прилагаемой нагрузки и изменение длины образца при растяжении. Эти же машины дают возможность записывать изменение длины образца при увеличении нагрузки (рис. 3), т.е. первичную диаграмму испытания на растяжение в координатах: нагрузка Р, Н, кН; и абсолютное удлинение образца А, мм.
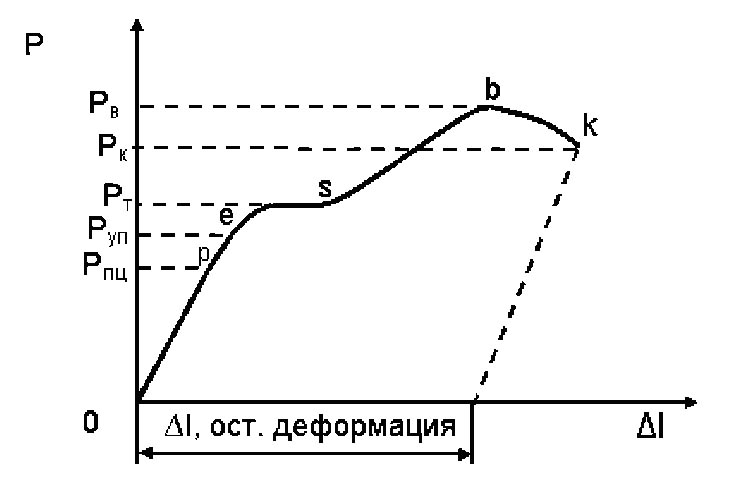
Рисунок 2 – Первичная диаграмма растяжения
Измеряя величину нагрузки в характерных точках диаграммы испытаний на растяжение (рис.2), определяют следующие параметры механических свойств материалов:
Єпц- предел пропорциональности, точка р;
Є0,05 - предел упругости, точка е;
Єт - предел текучести физический, точка s;
Є0,2- предел текучести условный;
Єв - временное сопротивление разрыву, или предел прочности, точка b.
Значения 0,05 и 0,2 в записи предела упругости и текучести соответствуют величине остаточной деформации ?l в процентах от l0 при растяжении образца. Напряжения при испытании на растяжение вычисляют путем деления нагрузки Р, соответствующей характерной точке на диаграмме, на площадь первоначального поперечного сечения F0рабочей части испытуемого образца:Єпц=Pпц/F0;Є0,05=P0,05/F0;Єт=Pт/F0 или Єв=P max/F0;Площадь поперечного сечение F0 определяется по следующим формулам:для цилиндрического образца F0 = ?d02/ 4.
Испытания на изгиб
Применение испытаний на изгиб обусловлено широкой распространенностью этой схемы нагружения в реальных условиях эксплуатации и большей ее мягкостью по сравнению с растяжением, что дает возможность оценивать свойства материалов, хрупко разрушающихся при растяжении. Испытания на изгиб удобны для оценки температур перехода из хрупкого состояния в пластичное. При испытаниях на изгиб применяют две схемы нагружения образца, лежащего на неподвижных опорах:
1.нагрузка прикладывается сосредоточенной силой на середине расстояния между опорами;2.нагрузка прикладывается в двух точках на одинаковом расстоянии от опор.
В изгибаемом образце создается неоднородное напряженное состояние, зависящее от геометрии образца и способа нагружения. При чистом изгибе узких образцов с прямоугольным сечением напряженное состояние в каждой точке можно считать линейным. В широких образцах (с отношением ширины к высоте сечения более трех) при обеих схемах изгиба создается двухосное напряженное состояние из-за затруднения поперечной деформации. Нижняя часть образца оказывается растянутой, верхняя — сжатой. К тому же напряжения, связанные с величиной изгибающего момента, различны по длине и сечению образца. Максимальные напряжения возникают вблизи поверхности. Все это затрудняет оценку средних истинных напряжений и деформаций, строго характеризующих механические свойства при изгибе.
Испытания на изгиб можно проводить на любой универсальной испытательной машине, используемой для испытаний на растяжение. Образец устанавливают на опорную плиту в нижнем захвате и деформируют изгибающим ножом (пуансоном), крепящимся в верхнем захвате машины. Для уменьшения трения опоры, на которых лежит образец, часто делают из роликоподшипников. Образец изгибается при опускании верхнего или подъеме нижнего захвата.
Простота испытания на изгиб и наглядность получаемых при этом характеристик пластичности привели к разработке ряда технологических проб, которые применяются в заводских условиях. Задача всех этих проб — оценить пластичность деформированных полуфабрикатов, отливок и изделий (листов, труб, проволоки и др.). ГОСТ 14019— 80 «Методы испытаний на изгиб» предусматривает изгиб сосредоточенной силой плоских образцов из проката, поковок и отливок, помещаемых на две опоры. Критерием годности продукции может быть: а) заданный угол загиба образцов (см. рис. 5, б) появление первой трещины после загиба на угол, равный или больший заданного; в) возможность загиба пластины до параллельности (см. рис. 5, в) или соприкосновения сторон (см. рис. 5, г). Существуют также пробы на перегиб листа, ленты и проволоки, в которых фиксируют заданное число перегибов либо количество перегибов, после которых появились трещины или образец разрушился.
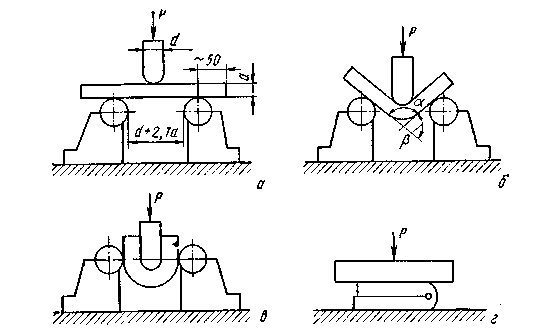
Рисунок 3 – Технологическая проба на изгиб
Макроанализ заключается в определении строения металла путем просмотра его излома или специально подготовленной поверхности невооруженным глазом или через лупу при небольших увеличениях — до 30 раз. Это позволяет наблюдать одновременно большую поверхность и получить представление об общем строении металла и о наличии в нем определенных дефектов. Поверхность, подлежащую макроанализу, изучают непосредственно (по виду излома) или шлифуют и подвергают травлению специально подготовленными реактивами. На шлифованной поверхности не должно быть загрязнений, следов масла и т. п., поэтому ее перед травлением протирают ватой, смоченной в спирте. Подготовленный образец называют макрошлифом.Травление производят в вытяжном шкафу; макрошлифы вынимают из реактива щипцами или рукой, защищенной резиновой перчаткой.При погружении макрошлифа в реактив (на 25-30 мин. в растворе соляной кислоты) происходит обменная реакция: железо вытесняет медь из водного раствора, и она оседает на поверхности шлифа; на участках, недостаточно защищенных медью (поры, трещины, неметаллические включения), происходит травление. Затем макрошлиф вынимают, слой осевшей меди снимают ватой под струей воды и протирают макрошлиф досуха, чтобы предохранить его от быстрого окисления на воздухе.
Микроскопический анализ металлов заключается в исследовании их структуры с помощью оптического микроскопа (использующего обычное белое или ультрафиолетовое излучение) и электронного микроскопа.При использовании оптического микроскопа структуру металла можно изучать при общем увеличении от нескольких десятков до 2 000–3 000 раз. Микроанализ позволяет характеризовать размеры и расположение различных фаз, присутствующих в сплавах, если размеры частиц этих фаз не менее 0,2 мкм. Многие фазы в металлических сплавах имеют размеры 10–4–10–2 см и поэтому могут быть различимы в микроскопе.С помощью микроанализа можно определить структуру сплава не только в равновесном, но и в неравновесном состоянии, что в ряде случаев позволяет установить предшествующую обработку сплава.Изменение структуры от поверхностного слоя к середине изделий указывает на характер нагрева (наличие окисления или обезуглероживания стали) или на применение химико-термической обработки (цементации, азотирования и т. д.).Приготовление микрошлифовВ оптическом микроскопе рассматриваются микрошлифы — специальные образцы металла, имеющие шлифованную и полированную гладкую поверхность, отражающую световые лучи.Шлифование плоскости образца. После получения приблизительно плоской поверхности образец шлифуют наждачной бумагой, помещенной для этого на плоском основании (обычно на стекле), или закрепленной с помощью зажимных колец, или наклеенной на вращающийся круг.Шлифование производят последовательно наждачной бумагой различного сорта, сначала с более крупным зерном абразива, а затем с более мелким. Направление движения образца по наждачной бумаге или положение образца относительно направления круга при смене сорта бумаги изменяют на 90° для лучшего удаления гребешков и рисок, созданных предыдущим шлифованием.Остающиеся на поверхности образца после шлифования частицы абразивного материала удаляют обдуванием воздухом или промывкой водой.Полирование считается законченным, когда поверхность образца приобретает зеркальный блеск и даже под микроскопом не видны риски или царапины.
Изучение механических свойств металлических материалов необходимо для обеспечения требуемого качества продукции. Вопрос качества продукции стал очень актуальным в настоящее время. Наше предприятие занимается постоянным изучением требований мировых потребителей, для удовлетворения их потребностей и их предвосхищения. Проведение испытаний, имитирующих условия эксплуатации, с помощью современного оборудования позволяет с необходимой точностью определять механические свойства материалов. Результаты испытаний используются для дальнейшего применения в производстве, других испытаниях...