Abstract
The contents
- Introduction
- 1. Actuality of the problem
- 2. The purpose and research problems, the planned results
- 3. Main part
- Conclusion
- References
Introduction
Diamond grinding of large-sized complex-profile thin-walled shells from brittle nonmetallic materials is an integral part of the technological process of creating elements for the construction of aviation and missile equipment, the effectiveness of which determines labor intensity, cost and quality of products.
The quality requirements for the parts in question are determined by the conditions of their operation. The main requirements are to ensure aerodynamic design, high mechanical strength, able to maintain at operating temperatures, as well as selective transmission of electricity in a given frequency range and a relatively small mass of the product.
The strength of the product is mainly ensured by the absence of defects in the near-surface layer [1].
Sitallas are inorganic materials obtained by directional crystallization of different glasses during their heat treatment [2].
1. Actuality of the problem
The theme of the master's
thesis is: Develop and
research the accuracy control system for machining of thin-walled parts
from sitalls
.
2. The purpose and research problems, the planned results
The main objectives of the study:
- Analysis of factors affecting the formation of accuracy of machining the product.
- Analysis of options and selection of a method for controlling the precision of processing of the sitae fairing.
- Selection of the parameters of the automatic control system.
- Development of the control program in parametric form.
The object of the study: The process of diamond grinding of the sitae fairing.
The subject of the study: The process of forming the accuracy of the outer contour in diamond grinding.
3. Main part
Analysis of the process of formation of the error of contour processing on CNC machines and its components shows that automatic control can be carried out by correcting the equidistant or by controlling the cutting regimes in order to stabilize or compensate for the disturbances. Combined methods are also used that combine control of treatment regimes with equidistant correction. By the nature of the information used, automatic control methods can be divided into methods using a priori, current and a posteriori information.
Control of cutting modes for a priori information. This method is expedient for applying at essential influence of instability of modes of cutting on quality of the processed surface, for example, at grinding.
The method is based on the established relationship between perturbations, control actions and processing quality parameters.
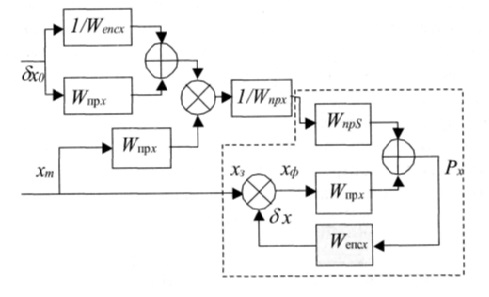
Figure 1 – Control scheme for stabilizing processing conditions
Control cutting modes for
current information. The method provides for the creation of an
automated control system, closed through a cutting process and working
on the principle of balancing
,
that is, an error. Despite the general principle of control, this
method differs from the above method of controlling the trajectory of
the form–building movement on the current information.
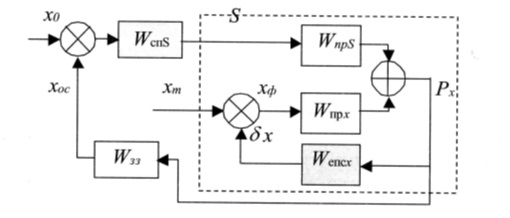
Figure 2 – Control scheme for processing modes according to current information
The method is expedient for applying not only for stabilization, but also for program control of any process parameters in the processing cycle. For example, with different grinding, the system can provide an algorithm for controlling the transverse infeed, as required, in the coordinate function of the remaining allowance. For this purpose, a continuous measurement of the actual coordinate in the direction of the frame must be ensured in the automatic control system and an additional program block to which the specified control algorithm is applied.
According to one of the presented methods, a precision control system for the processing of thin-walled details from steel plates is developed and studied.
Conclusion
Master's work is develop and research the accuracy control system for machining of thin-walled parts from sitalls.
When writing this paper the master's thesis isn't completed yet. Final end: June, 2018. The full text of work and materials on a subject can be received from the author or his scientific supervisor after the specified date.
References
- Гусев В.В., Калафатова Л.П. Повышение виброустойчивости технологической системы во время алмазного шлифования тонкостенных оболочек вращения из ситаллов //ISSN 2078–7405. Резание и инструмент в технологических системах, 2013, выпуск 83. Харьков: КПИ..
- ХИМИК. Сайт о химии. Ситаллы // [Электронный ресурс] – Режим доступа: http://www.xumuk.ru/encyklopedia/2/4086.html
- Калафатова
Л.П. Прогнозирование качества поверхностного слоя при обработке изделий
из технических ситаллов // Приложение №9 к журналу
Инженерный журнал. Справочник
Инженерия поверхности. – М.: Машиностроение. – 2002. – №9. – С.5–8. - Калафатова Л.П., Гусев В.В., Олейник С.Ю. Исследование динамического состояния технологической системы алмазно–абразивной обработки тонкостенных оболочек из ситаллов // Вісник СевНТУ: зб. наук. пр. Вип. 128/2012. Серія: Машиноприладобудування та транспорт. – Севастополь, 2012 с.60–67
- Гусев В.В. Исследование динамических характеристик элементов системы СПИД при шлифовании деталей сложной пространственной формы из ситаллов / В.В. Гусев, Л.П. Калафатова, И.С. Каракуц // Надійність інструменту та оптимізація технологічних систем. Збірник наукових праць. – Краматорск, 2007. – Вип. №21. – С. 148 – 155.
- Якушев Н.З. Коническая оболочка под действием подвижных нагрузок / Якушев Н. З., Якушев Р. С. // Исследования по теории пластин и оболочек. – Казань: Изд–во Казанского ун–та, 1975. – С. 303 – 316
- Гусев В.В. Повышение качества алмазного шлифования тонкостенных оболочек из ситалла путем снижения вибраций в технологической системе / Гусев В.В., Калафатова Л.П., Олейник С.Ю. // Наукові праці ДонНТУ– Донецк, 2010. – Вип. № 7(166).– С. 156–167.
- Петраков Ю.В.Драчев О.И. Теория автоматического управления технологическими системами / М.: Машиностроение, 2008. – C. 158 – 162